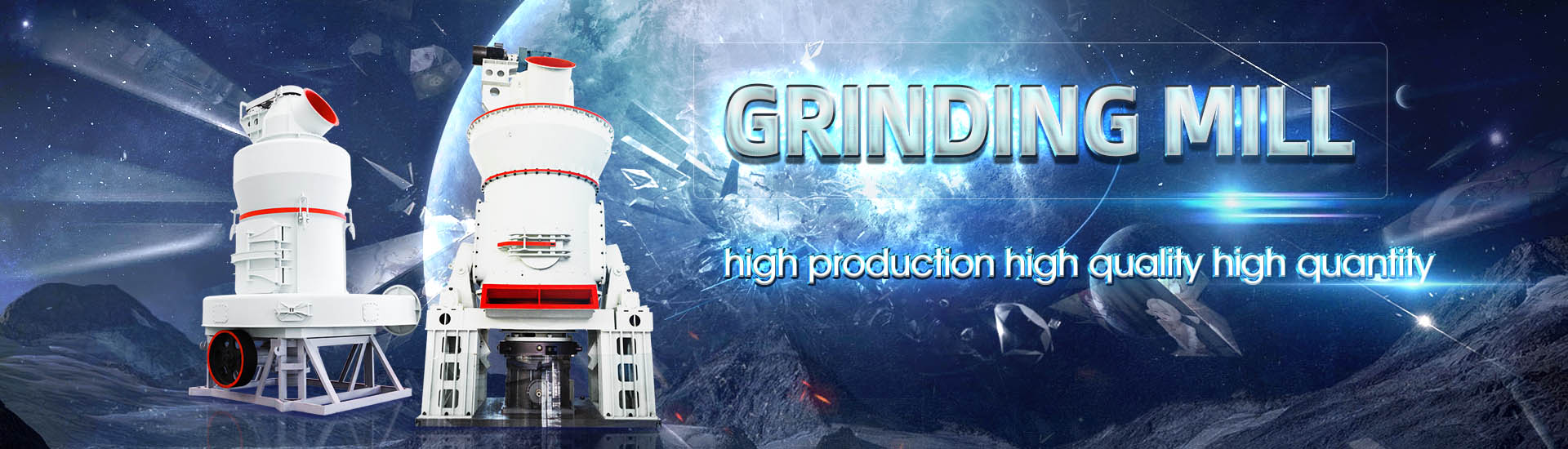
Cement grinding Equipment is new for a few years
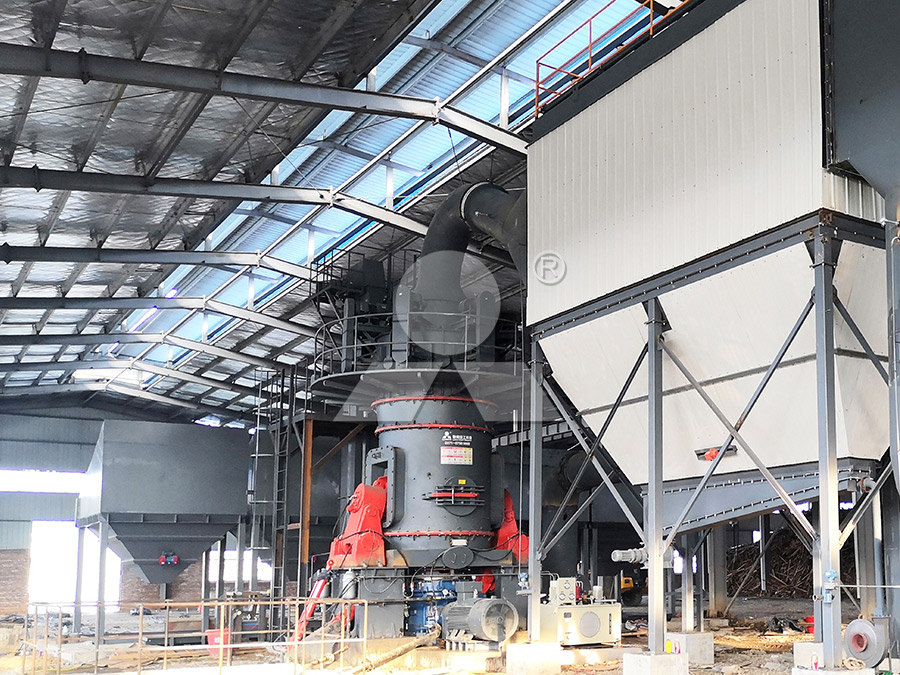
Back To The Grind: World Cement Grinding QA with Fives
2021年4月15日 The FCB Horomill ® grinding system can help provide a solution to these challenges, offering low energy consumption and high flexibility and endproduct quality for an optimised cement/clinker ratioAs part of its green cement plant project, thyssenkrupp has expanded its product range with the polysius® booster mill While one cement manufacturer has already integrated the mill into his Let’s talk: polysius® booster mill – the next level in cement ECRA’s Future Grinding Technologies Project is based on two pillars: The first is a systematical approach towards new technologies for grinding in the cement industry The second is the Future Grinding Technologies Kickstarter Q3i Typo3 11 HeadlessFrom online monitoring to gearless kiln advancements, the future will still rely on developments in equipment designs to augment and/or replace existing systemsEverything you need to know about Future Trends In Cement

CuttingEdge Grinding Solutions Indian Cement Review
2023年8月21日 In a cement plant, the key grinding equipment plays a vital role in transforming raw materials into finely ground cement powder The most common and widely used grinding 2022年11月17日 We find that novel suspension preheater rotary kilns account for approximately 99% of cement production in China in 2021 Climate change and fossil depletion are identified Modernizing cement manufacturing in China leads to substantial Pfeifer was founded by the brothers Karl and Jacob Pfeifer as a small machine factory in Kaiserslautern, Germany, in 1864 Its first products were steam engines and, early on, various GLOBAL CEMENT: GRINDING Gebr Pfeiffer2022年2月18日 World Cement invited industry leaders to share their thoughts on a range of grinding and millingrelated topics Contributions come from: FIVES FCB, Gebr Pfeiffer, and World Cement Grinding Milling QA
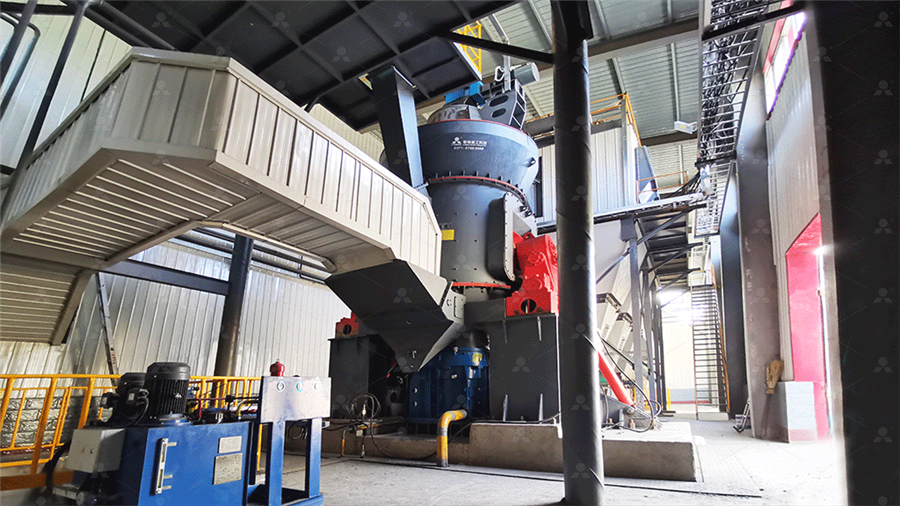
Process technology for efficient and sustainable cement production
2015年12月1日 Over the years technology in the cement industry has developed with a growing focus on sustainable and also cost and energy efficient production While significant steps may Process and equipment has been developed and improved with the aim of performing these steps economically Cement Grinding; × Cement Grinding More than 60% of total cement plant electrical energy consumption is utilised in grinding systems Higher AFR utilisation and new cement types also make it necessary to adjust and adapt cement mills Holzinger Consulting Grinding and Kiln Process Consulting Cement CEMENGAL has been awarded with a new contract for the supply of 2 nd Cement grinding station to ACICO Cement consisting of a complete cement mill workshop; Main equipment to be included within this new contract is related to a 5,200 Kws ball mill fully engineered by CEMENGAL with all the peripheral equipment and a 4 th generation classifier from Magotteaux XP4i130 for high Cemengal is a EPC contractor specialized in the Cement Industry Grinding aids are materials which facilitate grinding in ball or tube mills, by eliminating ball coating or by dispersing the ground material When grinding cement, the additive must also have been shown not to be harmful to the Finish grinding INFINITY FOR CEMENT EQUIPMENT
.jpg)
Grinding: Smarter Solutions Indian Cement Review
2022年8月10日 The newage cement grinding units adopt pregrinding technology The year 1885 saw the development of specialised steel that led to the development of new forms of grinding equipment Cement Grinding Machines Equipment required for the cement grinding plant include cement roller press, Concrete grinding has a few variables like the composition of the cement that determine the process of grinding it down We'll cover all the details about concrete grinding If a contractor is installing wood or tile floors over a concrete floor, it helps for it to be smooth Also, the new flooring won’t need constant repairs as gapping The Ins And Outs if Concrete Grinding ACore ConcreteIn the cement industry there are few demands on the crushed raw material as regards grain shape The crushed product should have the largest possible fine fraction and few oversized grains Thus, when selecting a type of crusher, usually only the maximum grain size tolerated for the following comminution equipment is importantEverything you need to know about Crushers in Cement industry2015年10月23日 In this chapter an introduction of widely applied energyefficient grinding technologies in cement grinding and description of the operating principles of the related equipments and comparisons over each other in terms of grinding efficiency, specific energy consumption, production capacity and cement quality are given A case study performed on a EnergyEfficient Technologies in Cement Grinding IntechOpen
.jpg)
Process Training Ball Mill INFINITY FOR CEMENT EQUIPMENT
To Download this post + all manuals and books and Excel sheets and all notes I collected over my 23 years of experience in Cement industry click here now INTRODUCTION Comminution is a major unit operation in a cement plant, accounting for about 50 75 % of the total plant energy consumption Fine grinding in general is extremely inefficientCement grinding Vertical mill operating in a closed circuit with a high efficiency separator is thus still the most preferred arrangement for new cement grinding installations although the vertical roller mill now the corresponding figure will be 010015 EUR per ton of cement Costs of equipment and civil works The total specific Cement grinding Vertical roller mills VS ball mills2019年1月3日 Clinker grinding technology is the most energyintensive process in cement manufacturing Traditionally, it was treated as "low on technology" and "high on energy" as grinding circuits use more than 60 per cent of total energy consumed and account for most of the manufacturing cost Since the increasing energy cost started burning the benefits significantly, Clinker grinding technology in cement manufacturing2017年5月19日 Grinding is an essential operation in cement production given that it permits to obtain fine powder which reacts quickly with water, sets in few hours and hardens over a period of weeks i Overview of cement grinding: fundamentals,
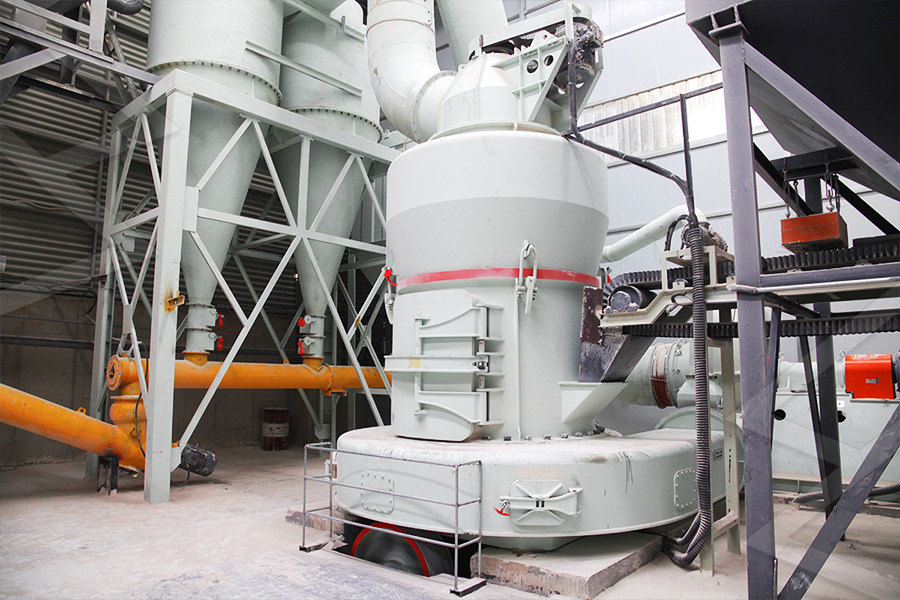
Latest trends in modular cement grinding plants
In the last few years, investments in new clinker capacity have become rare However, the capacity expansion of standalone grinding plants has never paused Especially the demand for compact and modular cement grinding Based on customer needs and years of experience in cement equipment manufacturing, AGICO Cement develops a lowcost and highly efficient EPC solution for cement grinding unit – modular mobile (MMG) cement grinding Modular Mobile Cement Grinding Plant For SaleThe cement production would be dictated by local and foreign demands, and, by the targeted 10 MTPA Grinding operations would therefore necessarily be carried out 24 hours a day through three eight hour shifts for 365 days a year The packing plant is planned to operate 24 hours a day through three 8hour shifts, 365 days a yearEVERYTHING YOU NEED TO KNOW ABOUT ESTABLISHING CEMENT GRINDING PLANT 2018年4月24日 A ccording to CW Research’s recently published “World Cement Equipment Market and Forecast Report,” the market for cement manufacturing related equipment and services is projected to reach $9 billion by 2022 However, as greenfield cement plant projects remain scarce, upgrades to existing cement plants will become relatively more important; Cement Plant Equipment Market To Reach $9 Billion By 2022
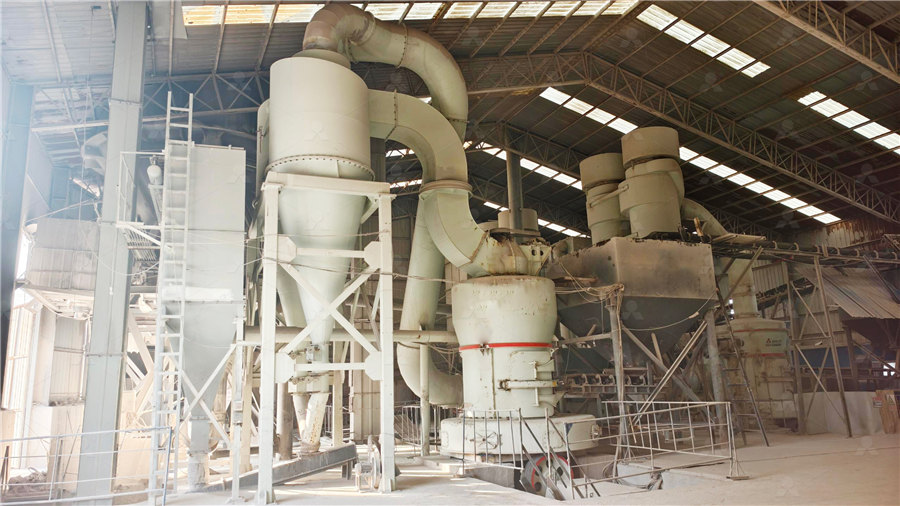
UPGRADATION OF EXISTING CEMENT GRINDING SYSTEMS WITH
The revised grinding media pattern before upgradation and after upgradation is shown in the table 41 (b) below; Cement Mill Grinding Media (Before Up gradation) , CM – 4 / 5 Cement Mill Grinding Media (After Up gradation), CM – 4 Ball Size, mm 1st Chamber 2nd Chamber Ball Size, mm 1st Chamber 2nd Chamber 90 mm 15 2023年9月26日 Maintenance Performance Optimization for Critical Subsystems in Cement PreGrinding Section: A Case Study ApproachMaintenance Performance Optimization for Critical Subsystems in Cement 2023年8月21日 Tushar Khandhadia, General Manager – Production, Udaipur Cement Works, discusses the role of grinding in ensuring optimised cement production and a high quality end product How does the grinding process contribute to the production of highquality cement?The quality of cement depends on its reactive properties and particle size grinding helps to reduce Grinding process is a critical stage in cement productionVertical roller mill vs ball mill for cement grinding: Comparison the advantages and disadvantages of these two types of mills TO Download this post and all the books and excel sheets and my personal notes and presentations I collected about cement industry in the last 30 years click the below paypal linkVertical roller mill vs ball mill for cement grinding: Comparison
FYEFEPS2HDZ49G5Z0[B.jpg)
HighCapacity Cement Grinding Solutions: Enhancing Efficiency
An Asian cement manufacturer integrated highpressure grinding rolls (HPGRs) into its existing grinding circuit, resulting in a 30% increase in grinding capacity The addition of HPGRs allowed the plant to process harder materials while improving energy efficiency and MECHANICAL ELEMENTS OF TUBE MILLS this is a part of ASEC Academy training Courses SUMMARY the mechanical elements of a tube mill could be separated into elements which have a direct function with the grinding process (ie grinding media, liners, diaphragms) and into elements which can be considered as individual units which are connected to each other to a MECHANICAL ELEMENTS INFINITY FOR CEMENT EQUIPMENT2024年6月26日 JK Cement, a leading Indian manufacturer of grey cement and prominent global white cement producer, today announced the commissioning of a new grinding unit at its Prayagraj Plant in Uttar Pradesh This significant JK Cement adds new grinding unit at Prayagraj2020年1月3日 The cement manufacturing process starts with mining of limestone followed by grinding it with other raw materials like clay, shale, bauxite, iron ore, etc to prepare a raw meal, which is heated at a sintering temperature Key factors in setting up a cement plant Indian
.jpg)
Reprint Sonderdruck aus Cement International 62021 Gebr
The first MPS vertical roller mill for cement grinding was commissioned in 1980 and remains in operation 40 years later in 2021 MPS mills are well suited for many materials in different industries such as eg cement, gypsum, limestone, industrial minerals Market demands for very high production capacities asked for bigger equipment Due to2014年6月24日 KUCHING: Cahya Mata Sarawak Bhd’s (CMS) cement division yesterday signed the Engineering, Procurement and Construction (EPC) Agreement with Christian Pfeiffer Maschinenfabrik GmbH (CPB) as its CMS Cement signs EPC agreement for new cement grinding Vertical roller mills Vs ball mills has long been a raging debate in the cement industry In spite of the fact that vertical roller mills have been around for over ten years now and have gradually become the standard as far as cement manufacturing goes, several cement manufacturers still prefer ball mills for cement production when they want to design new grinding plants or a new Ball Mills Or Vertical Roller Mills: Which Is Better For Cement Grinding?2011年5月1日 New technologies can be developed to reduce its energy consumption as sizeable energy is consumed in grinding operation of a cement manufacturing process In another study [16] , it was found that cement mill, raw mill, crusher and heater consume approximately 38%, 35%, 3% and 24% of total energy, respectivelyA critical review on energy use and savings in the cement industries
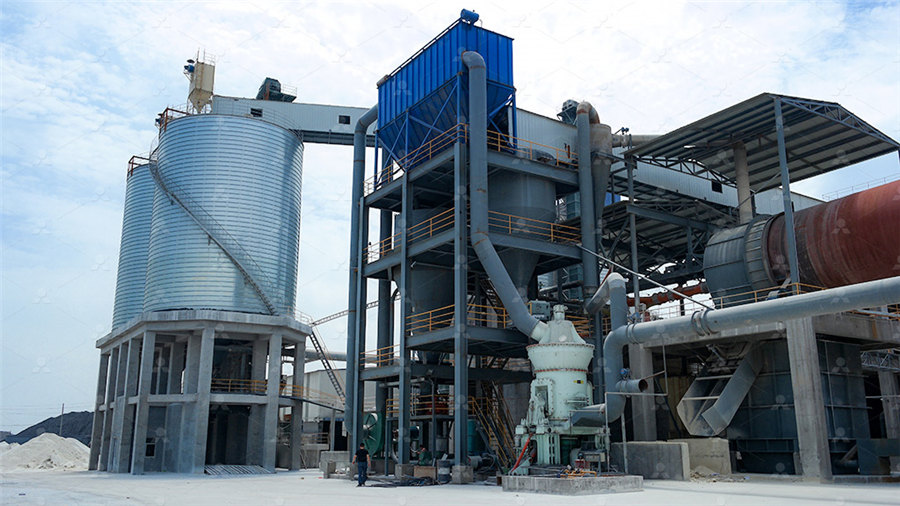
Everything you need to know about Automation and Optimization
The configuration of lab equipment (grinding mills, presses, fusion machines, Xray analyzers, etc) also depends on the type and quantity of samples taken per hour for analysis In some plants up to 500 samples per day are taken, although capacity restrictions for the specific lab may require queuing for sequencing of analysis25 years in the cement industry supplying engineering and equipment for assembly and commissioning of clinker and slag Grinding Station, cement plants, metallic and Main equipment to be included within this new contract is related to a 5,200 Kws ball mill fully engineered by CEMENGAL with all the peripheral equipment and a 4 th generation Cemengal is a EPC contractor specialized in the Cement Industry minor role in new installations Cement grinding In Table 1, three common cement grinding systems are compared on their electrical consumption for a typical 3500 Blaine ordinary portland cement (OPC) Roller press finish‑grinding systems, due to lower fan power demand compared to a VRM, exhibit a lower specific energy consumptionThomas Holzinger, Holzinger Consulting, grinding system Process and equipment has been developed and improved with the aim of performing these steps economically Cement Grinding; × Cement Grinding More than 60% of total cement plant electrical energy consumption is utilised in grinding systems Higher AFR utilisation and new cement types also make it necessary to adjust and adapt cement mills Holzinger Consulting Grinding and Kiln Process Consulting Cement
.jpg)
Cemengal is a EPC contractor specialized in the Cement Industry
CEMENGAL has been awarded with a new contract for the supply of 2 nd Cement grinding station to ACICO Cement consisting of a complete cement mill workshop; Main equipment to be included within this new contract is related to a 5,200 Kws ball mill fully engineered by CEMENGAL with all the peripheral equipment and a 4 th generation classifier from Magotteaux XP4i130 for high Grinding aids are materials which facilitate grinding in ball or tube mills, by eliminating ball coating or by dispersing the ground material When grinding cement, the additive must also have been shown not to be harmful to the Finish grinding INFINITY FOR CEMENT EQUIPMENT2022年8月10日 The newage cement grinding units adopt pregrinding technology The year 1885 saw the development of specialised steel that led to the development of new forms of grinding equipment Cement Grinding Machines Equipment required for the cement grinding plant include cement roller press, Grinding: Smarter Solutions Indian Cement ReviewConcrete grinding has a few variables like the composition of the cement that determine the process of grinding it down We'll cover all the details about concrete grinding If a contractor is installing wood or tile floors over a concrete floor, it helps for it to be smooth Also, the new flooring won’t need constant repairs as gapping The Ins And Outs if Concrete Grinding ACore Concrete
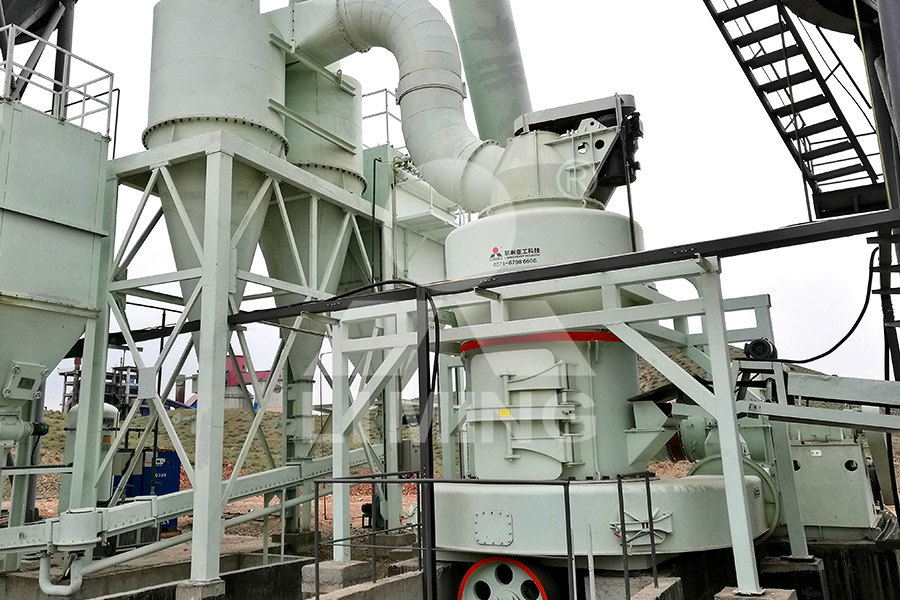
Everything you need to know about Crushers in Cement industry
In the cement industry there are few demands on the crushed raw material as regards grain shape The crushed product should have the largest possible fine fraction and few oversized grains Thus, when selecting a type of crusher, usually only the maximum grain size tolerated for the following comminution equipment is important2015年10月23日 In this chapter an introduction of widely applied energyefficient grinding technologies in cement grinding and description of the operating principles of the related equipments and comparisons over each other in terms of grinding efficiency, specific energy consumption, production capacity and cement quality are given A case study performed on a EnergyEfficient Technologies in Cement Grinding IntechOpenTo Download this post + all manuals and books and Excel sheets and all notes I collected over my 23 years of experience in Cement industry click here now INTRODUCTION Comminution is a major unit operation in a cement plant, accounting for about 50 75 % of the total plant energy consumption Fine grinding in general is extremely inefficientProcess Training Ball Mill INFINITY FOR CEMENT EQUIPMENTCement grinding Vertical mill operating in a closed circuit with a high efficiency separator is thus still the most preferred arrangement for new cement grinding installations although the vertical roller mill now the corresponding figure will be 010015 EUR per ton of cement Costs of equipment and civil works The total specific Cement grinding Vertical roller mills VS ball mills
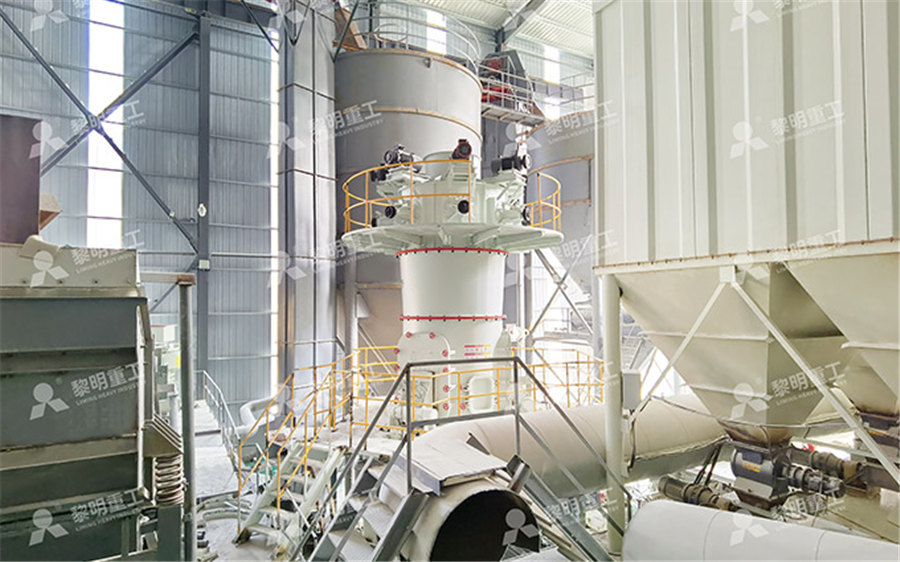
Clinker grinding technology in cement manufacturing
2019年1月3日 Clinker grinding technology is the most energyintensive process in cement manufacturing Traditionally, it was treated as "low on technology" and "high on energy" as grinding circuits use more than 60 per cent of total energy consumed and account for most of the manufacturing cost Since the increasing energy cost started burning the benefits significantly,