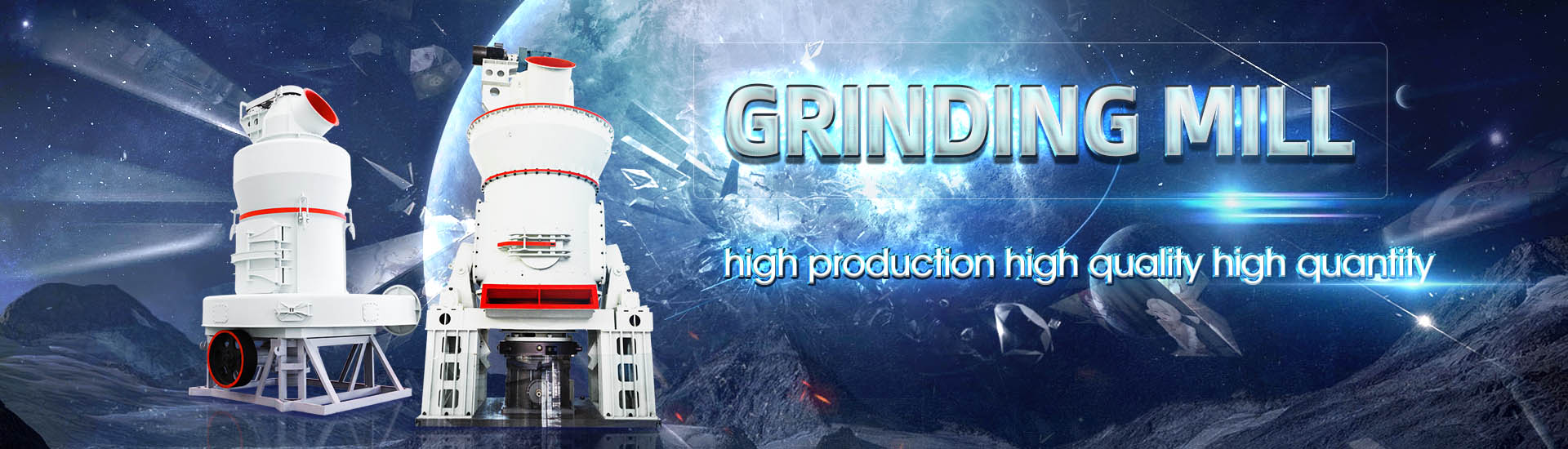
How to determine the model of ore mill
.jpg)
All About Particles: Modelling Ore Behaviour in Mineral Elements
liberate the valuable minerals in an ore by comminution, and then separate the resulting particles by means of their geometric, compo sitional, and physical properties From a 2012年6月1日 The paper presents an overview of the current methodology and practice in modeling and control of the grinding process in industrial ball mills Basic kinetic and energy Grinding in Ball Mills: Modeling and Process Control ResearchGateGrinding in ball mills is an important technological process applied to reduce the size of particles which may have different nature and a wide diversity of physical, mechanical and chemical Grinding in Ball Mills: Modeling and Process Control Sciendo2013年4月1日 A simple and novel nonlinear model of a runofmine ore grinding mill circuit, developed for process control and estimation purposes, is validated The model makes use of Analysis and validation of a runofmine ore grinding mill circuit
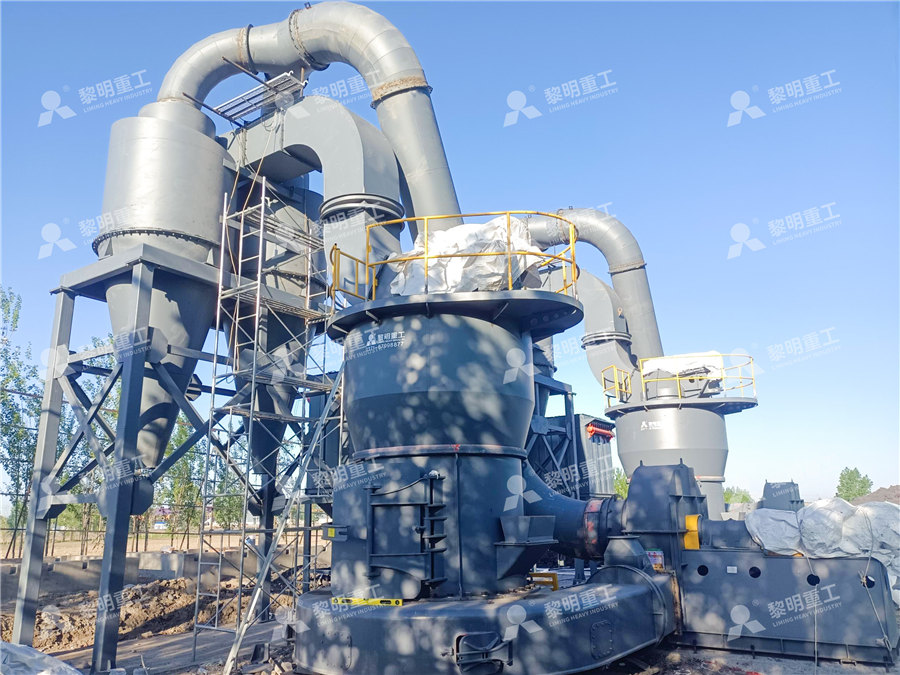
Analysis and validation of a runofmine ore grinding mill circuit
2013年4月1日 A simple, novel and nonlinear model of runofmine ore grinding mill circuit is validated The model is developed for process control and estimation purposes The model Abstract: A nonlinear phenomenological model of a grinding mill is used to determine five runofmine (ROM) grinding milling circuit parameters The five parameters are fraction of fines and Identifiability of runofmine ore grinding mill circuit parameters 2021年9月5日 The present study through batch laboratory experiments aims to model grinding of bauxite ore and identify the optimum material filling volume in a ball mill Modeling involves Modeling of Bauxite Ore Wet Milling for the Improvement of More reliable models for the prediction of the power drawn by ball, semiautogenous and fully autogenous mills have been developed by Morrell and by Austin (Morrell, S Power draw of TECHNICAL NOTES 8 GRINDING R P King
.jpg)
(PDF) Determining optimum wet milling and leaching
2017年10月1日 In this article, we present laboratory scale batch grinding and leaching profiles of a monosized gold ore sample (1700 + 850 μm) The sample was obtained from a runofmine (ROM) ore of one2023年7月31日 Gold Ore Ball Mill Models: Gold ore ball mill models have complete specifications and are suitable for different sizes of gold processing plants The cylinder diameter of gold ore ball mills ranges from 06m to 45m, with production capacities ranging from 065t/h to Gold ore ball mill common model and price, how to match the 2019年12月15日 To properly and precisely determine the deportment of gold in an ore or mill product, collected from different blocks of the deposit to determine gravity recoverable gold and/or T, et al 2018 Realtime reconciliation of a geometallurgical model based on ball mill performance measurements—a pilot study at the Tropicana Ore Body Knowledge SpringerLink2023年10月17日 Factors for choosing a suitable ore powder grinding mill 1 Raw material characteristics: Different raw materials have different hardness, humidity and grinding and crushing properties, and the corresponding ore How to choose a suitable ore powder grinding mill?
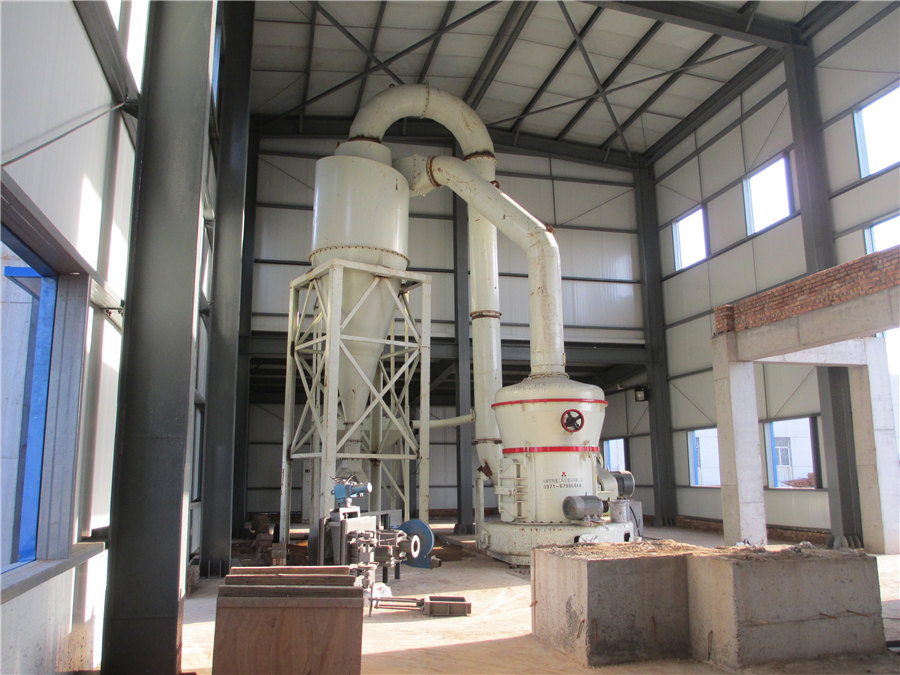
(PDF) TheMorrellMethodtoDeterminetheEfficiencyof
2022年1月30日 When the SMC Test ® is used to estimate values of A and b (used in the JK AG/SAG mill model), a size scaling factor might be required Since the average particle size used when testing with a JK 2014年12月22日 For design purposes, you need an estimation or prediction of your SAG Mill’s tonnage; well, there are 3 ways to generate good rock “ore” hardness testing data for SAG and ball mill circuit grindability from half drill core We can abbreviate the discussion by saying there are three “faiths” of grinding, and there are smallscale tests suitable for all three of the major Ore Hardness Testing SAG Mill Tonnage Estimation Method2016年3月21日 Concentration and Recovery Formulas These are used to compute the production of concentrate in a mill or in a particular circuit The formulas are based on assays of samples, and the results of the calculations are generally accurate— as accurate as the sampling, assaying, and crude ore (or other) tonnage on which they mon Basic Formulas for Mineral Processing Calculationsmill grinds the largesized ore and then a secondary mill grinds the ore from a small size to the desired size The breakage mechanisms that mills use are impact (for coarse grinding), and attrition and abrasion (for finer sizes) These forces not only grind the rock, but they also subject the mill to substantial wear and tear Applying theseThree factors that determine the wear life and performance of mill
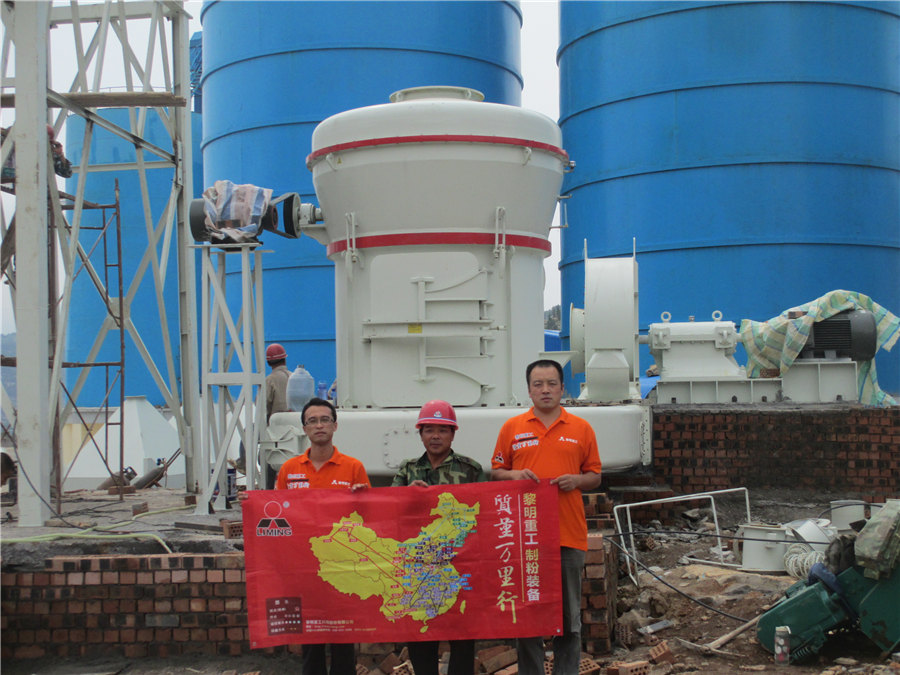
Dilution and ore loss – A short practical guide Cube Consulting
GM comes into the office asking why the grade is not appearing at the mill! Interestingly, in the authors’ experience , the term ‘ore loss’ is used far less frequently or not mentioned at all This is a little perplexing , as the potential economic impact of ore loss is far greater than dilution2004年11月1日 Semantic Scholar extracted view of "Using DEM to model ore breakage within a pilot scale SAG mill" by R Morrison et al Semantic Scholar extracted view of "Using DEM to model ore breakage within a pilot scale SAG mill" by R in normal operating conditions is performed The purpose is to determine how the geometry of the ExpandUsing DEM to model ore breakage within a pilot scale SAG millThe calculations below mainly apply to ore mills 1 Workindex What is the workindex of a mill ? The workindex is a parameter used in ore milling processes It is defined as the energy needed to reduce ore from infinite size to the state where 80% of the milled ore will pass through a Grinding power : step by step calculation PowderProcess2016年6月6日 Mill operating conditions including mill speed (for circuits with variablespeed drives), density, and total mill load; The effect of feed hardness is the most significant driver for AG/SAG performance: with variations in ore SAG Mill Grinding Circuit Design 911Metallurgist
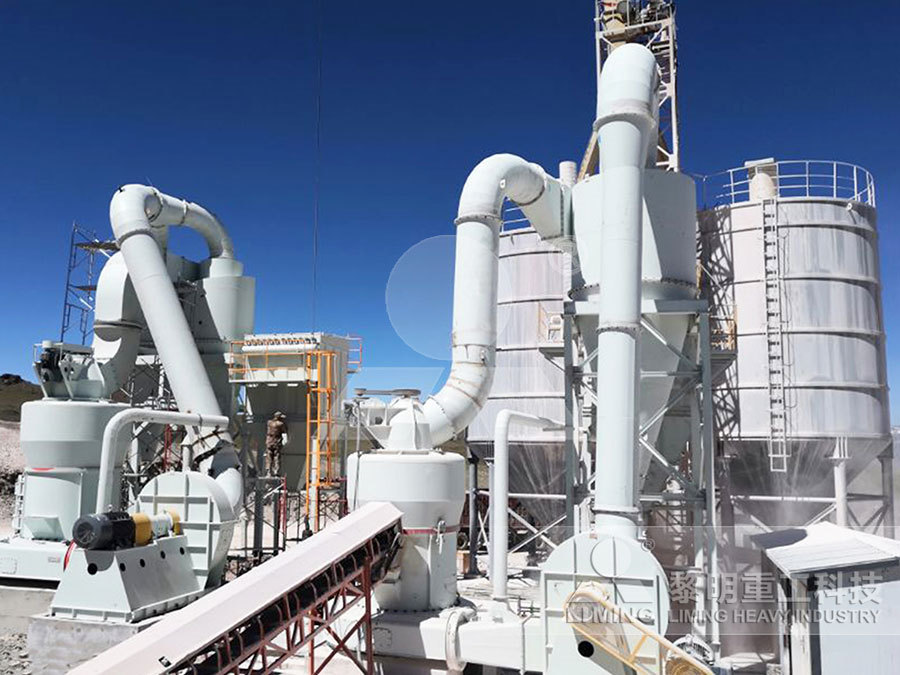
On the Optimization Procedure of Rolling Mill
2012年9月27日 This article proposes URC Technology to optimize the mill design from model software calculation, to mill window layout, and even to level2 optimal set up It is a combination of software and Understanding Mine to Mill is presented in five parts Part A – Setting the Scene provides some definitions of Mine to Mill (M2M) and the historical background A chronology of Mine to Mill developments is followed by brief descriptions of the very wide range of Mine to Mill applications which have been implemented over the last 15 yearsUNDErsTaNDINg MINE TO MILL 911 Metallurgist4 Classification in the chamber of the crusher is controlled by the open and closed side setting If the rock is larger than the open side settingModelling and Simulation Techniques Applied for Optimisation of distribution entering the mill This multiplication yields the mill product matrix which describes the size distribution of the particles exiting the mill Inpractice one creates the mill matrix by measuring the size distribution of the feed and product, then calculating the mill matrix by various methods This is referred to as solving Assessment of the Functionality of Selection and Breakage Rate
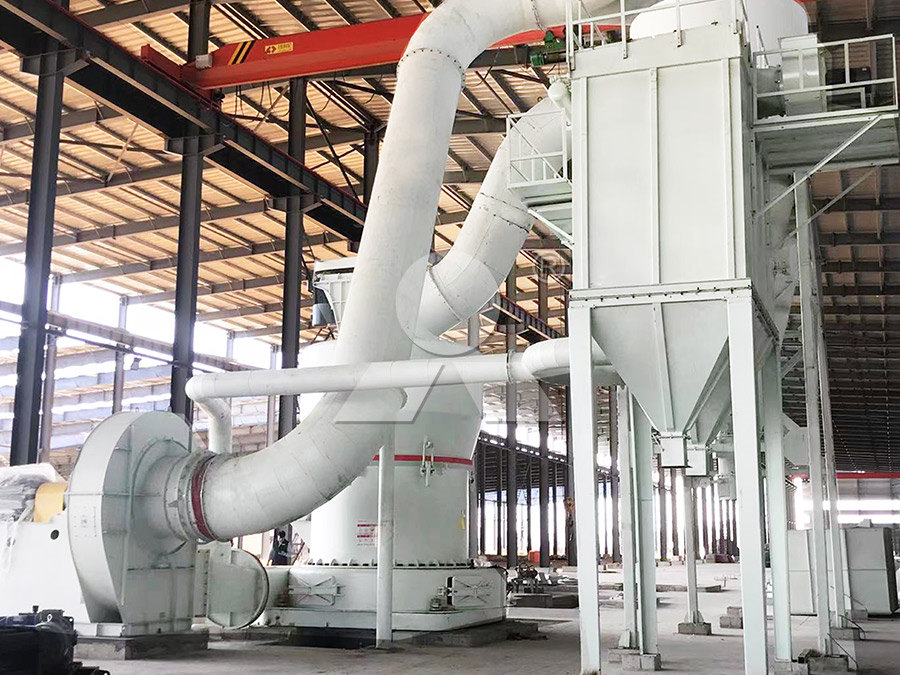
Introducing The Next Generation of Mill
SAN BRUNO, Calif, Feb 29, 2024 — The next generation of Mill is here, and it promises to help you waste less while you sleep In less than a year, Mill (the food wasterecycling system that turns household food scraps into dry grounds to feed farms or gardens) has helped people keep over one million pounds of food out of the landfill2011年1月1日 This paper describes the use of the Marx value in use (VIU) model to quantify the downstream value of iron ores The Marx model consists of heat and mass balance modules for sintering, pelletising Calculating the value of iron ores in ironmaking and steelmaking2023年10月2日 The Morrell Cmodel is generally regarded as one of the most accurate tumbling mill powerdraw models and is ideally suited for this application of estimating fill levels of the SAG mill in real time(PDF) RealTime Estimation of SAG Mill Charge Characteristics for 2022年10月1日 The presented model is valid only for ores with a typical Hukki exponent South American metasedimentary copper mine, and copper porphyry ore from Canada, of different feed sizes, were used to determine the Bond ball mill work index according to the standard procedureA new methodology to obtain a corrected Bond ball mill work
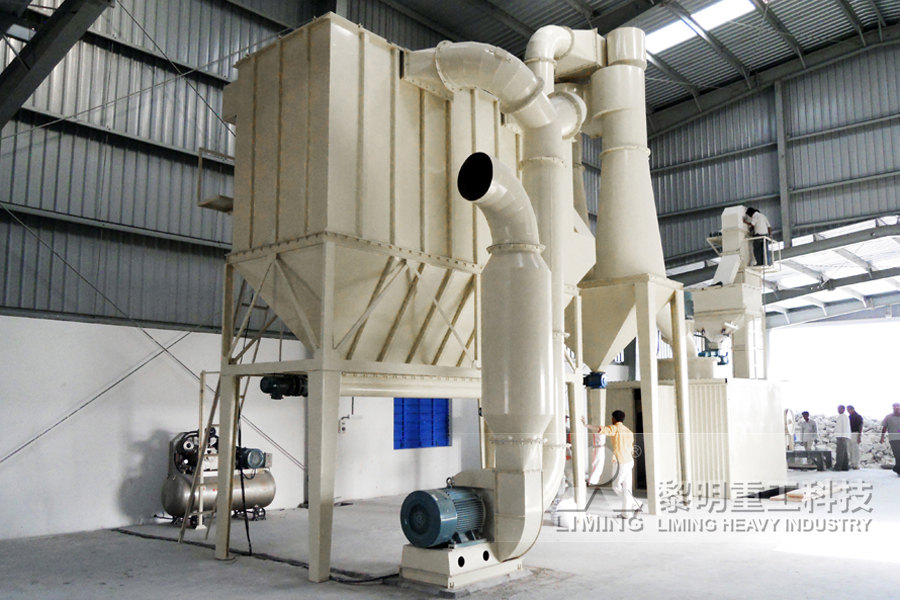
(PDF) Mine schedule optimization and mine operational realities
2019年5月22日 Such a schedule would be infeasible from an operational standpoint and would create discord with the neighboring mines To meet the annual ore production target, to preclude lost opportunity, and 2019年11月14日 With the modern manufacturing industry evolving and advancing and amid a more energy conscious society, high energy demand in manufacturing—particularly in machining—has drawn more and more attention Accurate energy consumption modelling is critical to the improvement of energy efficiency in machining In the existing energy models of Energy consumption model for milling processes considering TONS PER DAY MILl D 10,0 11,{)OO Fig 633 Mill crew vs mill process and size The number of mill personnel Nm l required to operate mills treating Ttons aflawgrade ore mined by open pit methods may be estimated from the following formulas: Nml = 590 TO3 for cyanidation of precious metal ores = 570 To3 for flotation of lowgrade baseCOSTS AND COST ESTIMATION Chapter NUBE MINERA2018年4月17日 Mill Sizing: After laboratory and pilot plant testing confirm the feasibility of autogenous or semiautogenous grinding, it can be used to establish the exact grinding circuit and mill sizeIn the pilot plant tests, the tare power of the pilot plant mills should be determined before and after each test run The tare power should be for the empty millAutogenous and SAG SemiAutogenous Mill Design Calculations
.jpg)
Grinding in Ball Mills: Modeling and Process Control Sciendo
55 known as the distribution function [45, 46]) describes the distribution of fragment sizes obtained after a breakage of particles of size xjThus, b1j, b2j, , bnj are the mass fractions of particles in size classes 1, 2, , n after a breakage of particles in size class j The mechanism of breakage is illustrated in [23] by a diagram shown in Fig 32018年3月12日 In addition, the variance of results generated from the four modern models is about 014%, indicating that these models are all appropriate for optimising cutoff grades Discover the world's research(PDF) Comparison of cutoff grade models in mine ResearchGateinside the mill and it is composed of balls, ore and water The ball charge is a function of the bulk fraction of the SAG mill volume (Jb) occupied by balls; the ore retained in the mill is the result of the volumetric filling which depends on the ore size distribution (specially the % +600 and the % 600 +100), on the rotational speed (N/Nc)Modelling SAG milling power and specific energy consumption 2015年1月1日 "A New Model to Improve Ore Grade Reconciliation between the Exploration Model and the Mine", Proceedings of Mine Planning and Equipment Selection (MPES) Conference, Fremantle, Western Australia Ore Grade Reconciliation Techniques A Review ResearchGate
.jpg)
METALLURGICAL TESTING METHODS (RENISON, TASMANIA
complexes and full Model Analysis; and x Comparison of metallurgical response of ore to a standard mill circuit recovery (through flotation or other associated ore concentration processes) to determine the maximum liberation point for the unknown ore2012年6月1日 model can also be very useful with regard to mill scaleup and the analysis of other types of comminution systems such as roll mills Except for the linear models, itGrinding in Ball Mills: Modeling and Process Control2016年3月11日 It was felt by some that crushing to this fine size is only possible if the ore is friable and is relatively soft in comparison to the harder ores Our results show that some of the copper ores are as hard as taconite and are crushed to ball mill feed all passing 13MM (½”)Crushing Plant Flowsheet DesignLayout 911Metallurgist2023年7月31日 Gold Ore Ball Mill Models: Gold ore ball mill models have complete specifications and are suitable for different sizes of gold processing plants The cylinder diameter of gold ore ball mills ranges from 06m to 45m, with production capacities ranging from 065t/h to Gold ore ball mill common model and price, how to match the
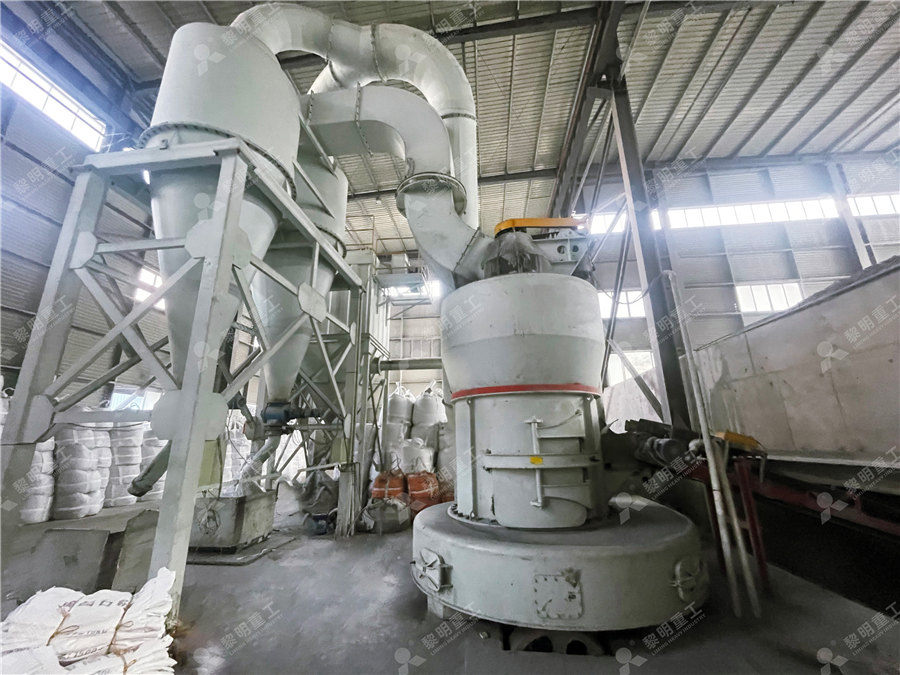
Ore Body Knowledge SpringerLink
2019年12月15日 To properly and precisely determine the deportment of gold in an ore or mill product, collected from different blocks of the deposit to determine gravity recoverable gold and/or T, et al 2018 Realtime reconciliation of a geometallurgical model based on ball mill performance measurements—a pilot study at the Tropicana 2023年10月17日 Factors for choosing a suitable ore powder grinding mill 1 Raw material characteristics: Different raw materials have different hardness, humidity and grinding and crushing properties, and the corresponding ore How to choose a suitable ore powder grinding mill?2022年1月30日 When the SMC Test ® is used to estimate values of A and b (used in the JK AG/SAG mill model), a size scaling factor might be required Since the average particle size used when testing with a JK (PDF) TheMorrellMethodtoDeterminetheEfficiencyof 2014年12月22日 For design purposes, you need an estimation or prediction of your SAG Mill’s tonnage; well, there are 3 ways to generate good rock “ore” hardness testing data for SAG and ball mill circuit grindability from half drill core We can abbreviate the discussion by saying there are three “faiths” of grinding, and there are smallscale tests suitable for all three of the major Ore Hardness Testing SAG Mill Tonnage Estimation Method
.jpg)
Common Basic Formulas for Mineral Processing Calculations
2016年3月21日 Concentration and Recovery Formulas These are used to compute the production of concentrate in a mill or in a particular circuit The formulas are based on assays of samples, and the results of the calculations are generally accurate— as accurate as the sampling, assaying, and crude ore (or other) tonnage on which they dependmill grinds the largesized ore and then a secondary mill grinds the ore from a small size to the desired size The breakage mechanisms that mills use are impact (for coarse grinding), and attrition and abrasion (for finer sizes) These forces not only grind the rock, but they also subject the mill to substantial wear and tear Applying theseThree factors that determine the wear life and performance of mill GM comes into the office asking why the grade is not appearing at the mill! Interestingly, in the authors’ experience , the term ‘ore loss’ is used far less frequently or not mentioned at all This is a little perplexing , as the potential economic impact of ore loss is far greater than dilutionDilution and ore loss – A short practical guide Cube Consulting2004年11月1日 Semantic Scholar extracted view of "Using DEM to model ore breakage within a pilot scale SAG mill" by R Morrison et al Semantic Scholar extracted view of "Using DEM to model ore breakage within a pilot scale SAG mill" by R in normal operating conditions is performed The purpose is to determine how the geometry of the ExpandUsing DEM to model ore breakage within a pilot scale SAG mill
.jpg)
Grinding power : step by step calculation PowderProcess
The calculations below mainly apply to ore mills 1 Workindex What is the workindex of a mill ? The workindex is a parameter used in ore milling processes It is defined as the energy needed to reduce ore from infinite size to the state where 80% of the milled ore will pass through a