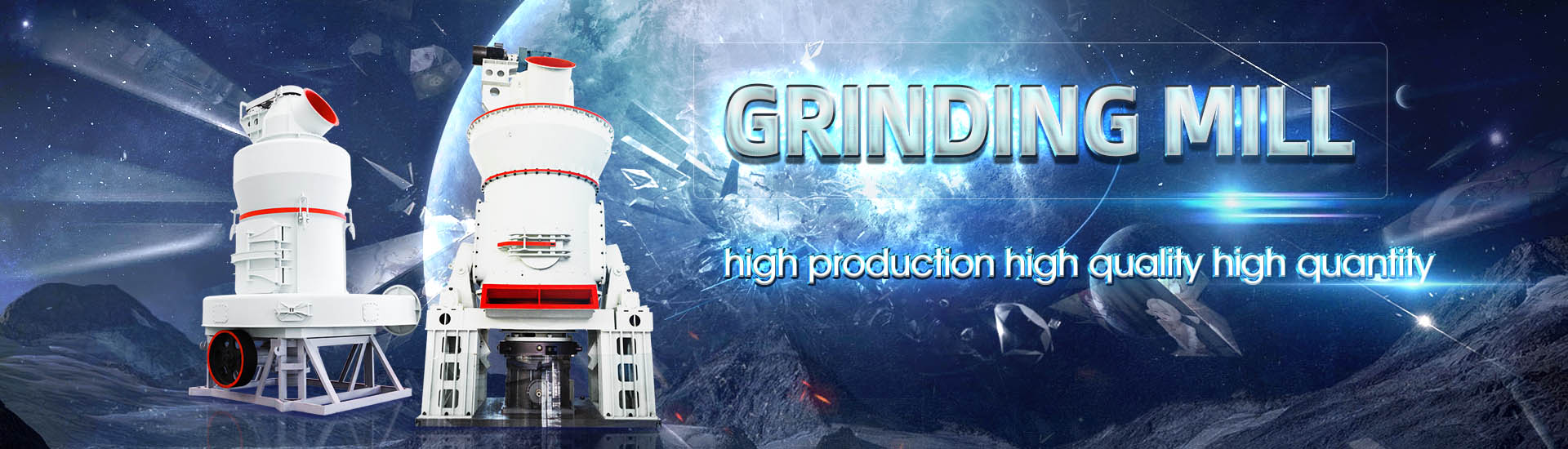
What are the raw materials of dry limestone
.jpg)
Limestone Characteristics, Formation, Texture, Uses, Facts
2024年10月30日 Limestones enriched in phosphate by the chemical action of ocean waters constitute a principal source of raw materials for the fertilizer industry When heated to temperatures of 900 to 1,000 °C (1,650 to 1,800 °F), limestones will dissociate calcium Limestone is used as the raw material for the manufacture of quicklime (calcium oxide), slaked lime (calcium hydroxide), cement, and mortar 9 Filter Limestone has great neutralizing power against toxins and hazardous chemicals For this reason, Limestone aggregates and crushed particles of varying sizes are used to create sewage and other Limestone Formation, Composition, Types and Uses Earth Eclipse2021年3月3日 The raw material for lime production is limestone ( Fig 74) or, to a lesser extent, dolostone and dolomitic limestone Limestone and dolostone deposits are relatively common in many countriesLime SpringerLinkLime is an inorganic material composed primarily of calcium oxides and hydroxides It is also the name for calcium oxide which occurs as a product of coalseam fires and in altered limestone xenoliths in volcanic ejecta [1] The Lime (material) Wikipedia
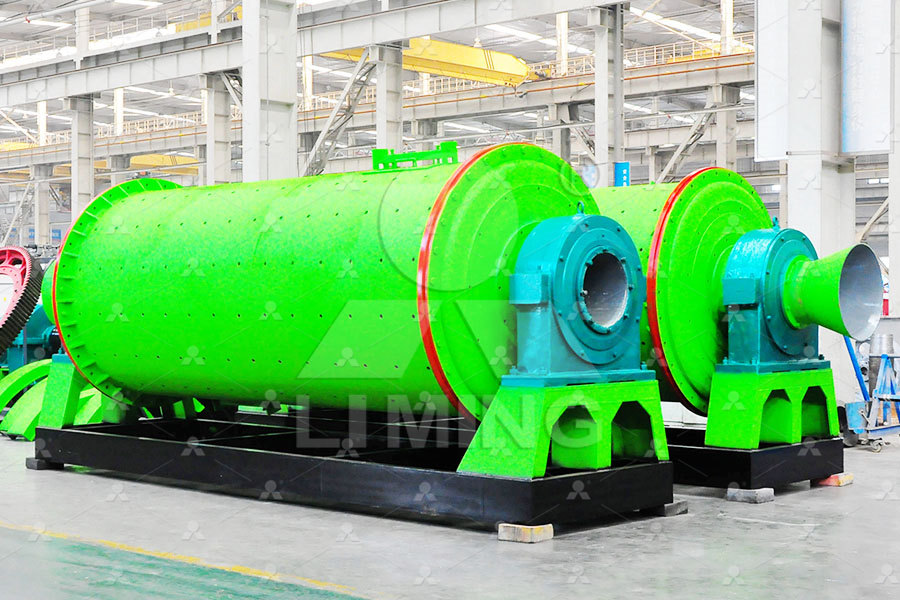
Limestone: The Calcium Carbonate Chemical
Limestone is used as a filler in a variety of products, including paper, plastic, and paint The purest limestone is even used in foods and medicines such as breakfast cereals and calcium pills Limestone is also the raw material for The raw material for hydraulic lime is limestone which is impure, that contains calcium carbonate and impurities of clay These are also calcinated at 900 to 1000 degree Celsius The reaction is as follows Calcium carbonate + clay Building Lime – Properties of Lime, Advantages and 2024年1月7日 Its role extends to the chemical industry where it serves as a raw material for producing various chemicals like slaked lime, quicklime, and hydrated lime, integral in many industrial processesLimestone: characteristics, formation, uses ZME Science2023年6月13日 Limestone, composed primarily of calcium carbonate (CaCO3), is a carbonate sedimentary rock and serves as the primary source material for lime production The accumulation of marine fossils, minerals, and other Limestone: Formation, Composition, Types Uses
.jpg)
An overview of dry mix mortar – materials, products
2022年6月7日 Raw Materials for DryMix Mortar Most of the drymix mortar products require only the addition of potable water and mixed with a simple mixer to produce highquality fresh mortars Although the dry mortars are relatively 2023年2月1日 Raw material blending is an important process affecting cement quality The aim of this process is to mix a variety of materials such as limestone, shale (clay), sandstone and iron to produce CEMENT RAW MATERIALS BLENDING PROCESS BY Raw materials for clinker production are for good reasons primarily based on limestone, The basic stage of clinker production is the extraction of raw materials They are mainly limestone, clay, slate, chalk, The hot gases from the preheater tower can be used as a heat source to dry the raw meal for clinker productionClinker Production an overview ScienceDirect TopicsWhile each cement plant may differ in layout, equipment, and appearance, the general process of manufacturing portland cement is the same: crushed limestone and sand are mixed with ground clay, shale, iron ore, fly ash and alternative raw materials Some manufacturers grind the raw materials dry, while others use a wetgrinding process How Cement is Made Portland Cement Association
.jpg)
Cement Manufacturing Process and Its Environmental Impact
2023年7月10日 Cement is produce d from raw materials such as limestone, chalk, shale, clay, and sand [1] Table 1 indicates the raw ingredients used to provide each of the main cement elements Table 1Hence, the raw materials (limestone, sandstone and gypsum) are needed to be transported by cross country conveyer belt which has a transportation capacity of 1000 ton/hr For example more energy is needed to produce enough hot air in Cement Manufacturing Process INFINITY FOR CEMENT EQUIPMENT2023年12月20日 From the limestone mine, to crushing, blending, the raw mill, kiln and beyond, elemental analysis is a critical component to driving process control, efficiencies, and higher quality end products Powerful analyzers can help you better understand the composition of your raw materials, and give you more control over downstream production processesThe Cement Manufacturing Process Thermo Fisher Scientific1971年8月17日 Typically, these raw materials are obtained from openface quarries, but underground mines or dredging operations are also used Raw materials vary from facility to facility Some quarries produce relatively pure limestone that requires the use of additional raw materials to provide the correct chemical blend in the raw mix116 Portland Cement Manufacturing US EPA
.jpg)
Manufacturing of Portland Cement – Process and Materials
14 小时之前 The manufacture of Portland cement is a complex process and done in the following steps: grinding the raw materials, mixing them in certain proportions depending upon their purity and composition, and burning them to sintering in a kiln at a temperature of about 1350 to 1500 ⁰C During this process, these materials partially fuse to form nodular shaped clinker The raw materials such as limestone, clay, and iron ore are crushed and then ground into a fine powder in ball mills or tube mills Dry raw materials are used in this process, and after being ground into a fine powder, they are put into a kiln The following are the main steps of the dry process of cement manufacturing:2 Types of Manufacturing of Cement Wet and Dry ProcessSince a form of calcium carbonate, usually limestone, is the predominant raw material, most plants are situated near a limestone quarry or receive this material from a source via inexpensive transportation Cement manufacturing begins with quarrying operations in which limestone in mines is quarried and brought to crusher for crushingLimestone quarry, quarrying, cement raw materialsThe properties of limestone make it a valuable natural resource for a wide range of industries Limestone is a sedimentary rock, composed mainly of skeletal fragments of marine organisms such as coral, forams and molluscs Its major materials are the minerals calcite and aragonite, which are different crystal forms of calcium carbonateLimestone: Definition, Usage and History DDL
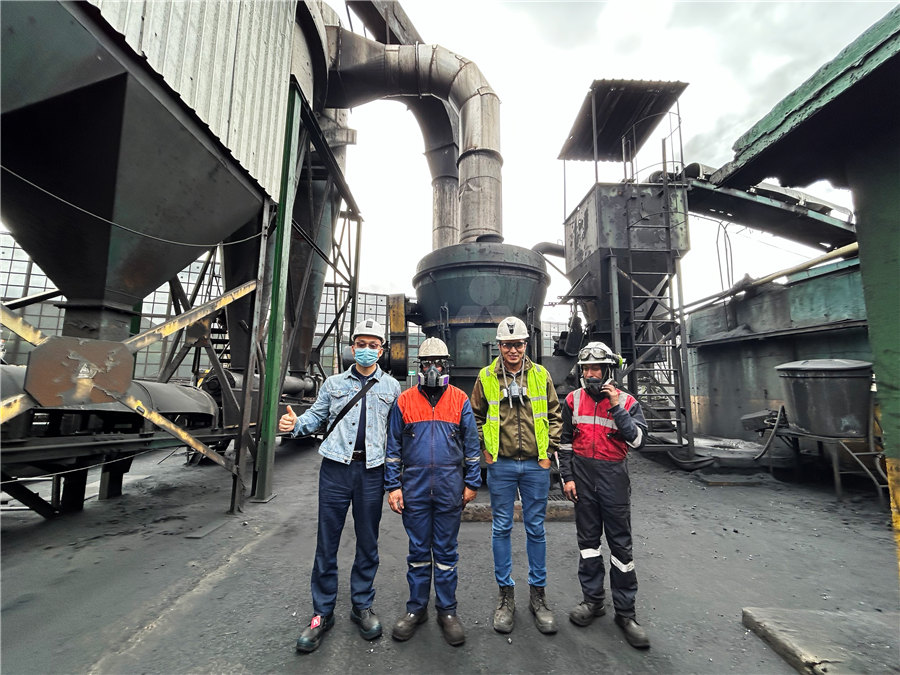
Manufacture of Cement Materials and Manufacturing
Table shows the raw materials for Portland cement manufacture The mixing procedure of the manufacture of cement is done in 2 methods, Dry process; Wet process; a) Dry Process The both calcareous and argillaceous raw materials Cement is a finely milled mineral powder, usually grey in colour The most important raw materials for the production of cement are limestone, clay, and marl Mixed with water, cement serves as an adhesive to bind sand, gravel, and hard rock in concrete Cement hardens both in the air and under water, and remains in its hardened state once reachedCement, its nature and origin Heidelberg MaterialsThe second raw material (materials in the rawmix other than limestone) depend on the purity of the limestone Some of the second raw materials used are: clay, shale, sand, iron ore, bauxite, fly ash and slag Portland cement clinker is made by heating a homogeneous mixture of raw materials in a rotary kiln at high temperatureCement clinker WikipediaRaw Materials Crushing, Storing and Grinding Clinker calcination is the most crucial part of the whole process of cement manufacturing At this stage, ground raw materials will be sent into the cement kiln and be heated at a high temperature to produce chemical reactions with each other, eventually forming clinker In addition, clinkers that just complete the calcination will have a Cement Clinker Calcination in Cement Production Process AGICO
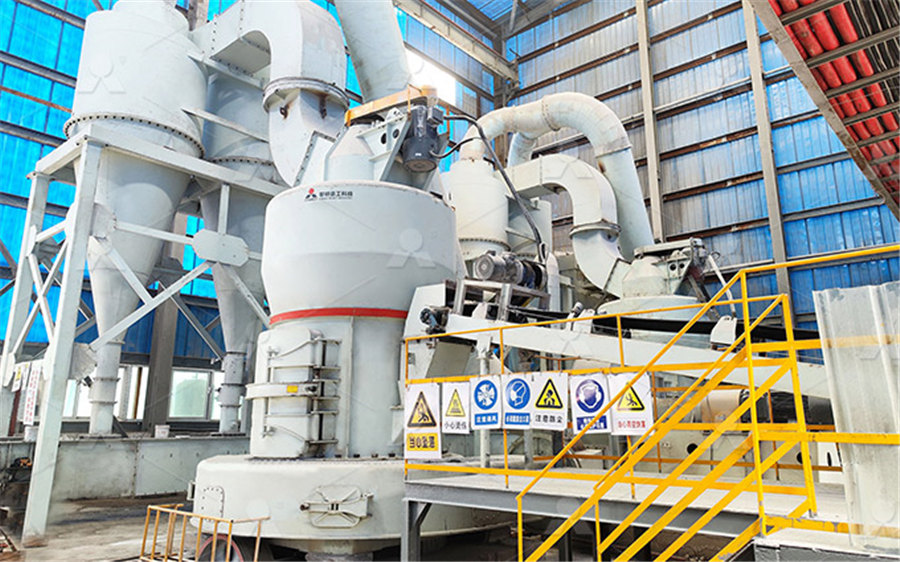
116 Portland Cement Manufacturing US Environmental
"natural cement rock" Typically, these raw materials are obtained from openface quarries, but underground mines or dredging operations are also used Raw materials vary from facility to facility Some quarries produce relatively pure limestone that requires the use of additional raw materials to provide the correct chemical blend in the raw mixThe raw material used for the production of pcc is limestone 21st century – 5000 million tonnes worldwide Annual usage of limestone is 5000 million tonnes in building and construction, cement manufacture, agriculture and steel production Many uses for calcium carbonate, directly sourced from limestone, have been foundHistory of limestone uses – timeline — Science Learning HubRAW MATERIALS Natural by Nature Why renewable raw materials? is left to ‘dry’ and harden in a 20meter tall drying room The natural curing process takes around three weeks Linseed oil Gum Rosin Tall oil Wood flour Limestone Jute Recycled Marmoleum Natural 97% Renewable 62% Rapidly renewable (1 year) 29% Recycled 44%RAW MATERIALSmainly limestone and clay, which are used in cement manufacturing In most of the cases, the limestone and clay are excavated from open cast mines by drilling and blasting and other appropriate processes in mines Subsequently, the limestone and clay are loaded onto dumpers which transport the materials Limestone is unloadedCement Manufacturing—Technology, Practice, and Development
.jpg)
I03 cement June 2010 GSgct IEAETSAP
between wet and dry process is the mix preparation method prior to burning clinker in the kiln In the wet process water is added to the raw materials to form a raw thick slurry whereas the dry process is based on the preparation of a fine powdered raw meal by raw materials grinding and drying [1, 5] The choice of theWe also source raw materials, including limestone, clay, pozzolans and gypsum, from third parties both in the Philippines and from abroad There are two primary processes used to manufacture clinker: the dry process and the wet process Our plants use the dry process, which is more energy efficientProduction Process CEMEX Philippines2015年12月9日 Raw materials are used to produce the main cement elements (Mohsen, 2015) • Quarry The process of obtaining raw materials for cement manufacturing involves mining and quarrying natural materials (PDF) Cement Manufacturing ResearchGate2024年2月6日 Aggregates are raw materials that are produced from natural sources and extracted from pits and quarries, including gravel, crushed stone, and sand When used with a binding medium, like water, cement, and asphalt, they are used to form compound materials, such as asphalt concrete and Portland cement concreteConstruction Aggregates 101: What They Are (and Why They
.jpg)
Limestone – Its Processing and Application in Iron and
2017年7月7日 Limestone is also a very important industrial mineral Its chemical properties make it a valuable mineral for a wide range of industrial/manufacturing uses Limestone is also one of the vital raw materials used in production of iron and steel Limestone, by definition, is a rock that contains at least 50 % of CaCO3 in the form of calcite by weightIn cases where raw materials with a higher phosphorus content are used (e g limestone with a high P205content, or industrial wastes from phosphorus production), an admissible limit of about 25% P205 in the clinker is quoted [12b]Raw materials used for Cement ProductionFollowing that, we delve into the dry process, which involves grinding raw materials into a fine powder before being fed into a kiln for firing Students will grasp the key stages of dry cement production and the specific techniques employed in this methodFrom Raw Materials to Concrete: The Science of Portland Cement Stage 2: Grinding, Proportioning, and Blending The crushed raw ingredients are made ready for the cementmaking process in the kiln by combining them with additives and grinding them to ensure a fine homogenous mixture The composition of cement is proportioned here depending on the desired properties of the cement Generally, limestone is 80%, and the remaining 20% How Cement is Made Cement Manufacturing Process
.jpg)
How concrete is made material, manufacture, making, how to
Raw Materials Structural concrete 1 The limestone, silica, and alumina that make up Portland cement are dry ground into a very fine powder, mixed together in predetermined proportions, preheated, and calcined (heated to a high temperature that will burn off impurities without fusing the ingredients) Next the raw materials required for the cement are easily available A typical LC3 blend would contain between 40% to 50% clinker, 15% to 20% crushed impure limestone, 30% to 40% of calcined clay and up to 5% of gypsum It has been seen that clays with around 50% kaolinite content and limestone with as low as 30% CaO content can be used in LC3An economic analysis of the production of limestone calcined clay 2022年6月7日 Raw Materials for DryMix Mortar Most of the drymix mortar products require only the addition of potable water and mixed with a simple mixer to produce highquality fresh mortars Although the dry mortars are relatively An overview of dry mix mortar – materials, products 2023年2月1日 Raw material blending is an important process affecting cement quality The aim of this process is to mix a variety of materials such as limestone, shale (clay), sandstone and iron to produce CEMENT RAW MATERIALS BLENDING PROCESS BY
.jpg)
Clinker Production an overview ScienceDirect Topics
Raw materials for clinker production are for good reasons primarily based on limestone, The basic stage of clinker production is the extraction of raw materials They are mainly limestone, clay, slate, chalk, The hot gases from the preheater tower can be used as a heat source to dry the raw meal for clinker productionWhile each cement plant may differ in layout, equipment, and appearance, the general process of manufacturing portland cement is the same: crushed limestone and sand are mixed with ground clay, shale, iron ore, fly ash and alternative raw materials Some manufacturers grind the raw materials dry, while others use a wetgrinding process How Cement is Made Portland Cement Association2023年7月10日 Cement is produce d from raw materials such as limestone, chalk, shale, clay, and sand [1] Table 1 indicates the raw ingredients used to provide each of the main cement elements Table 1Cement Manufacturing Process and Its Environmental ImpactHence, the raw materials (limestone, sandstone and gypsum) are needed to be transported by cross country conveyer belt which has a transportation capacity of 1000 ton/hr For example more energy is needed to produce enough hot air in Cement Manufacturing Process INFINITY FOR CEMENT EQUIPMENT
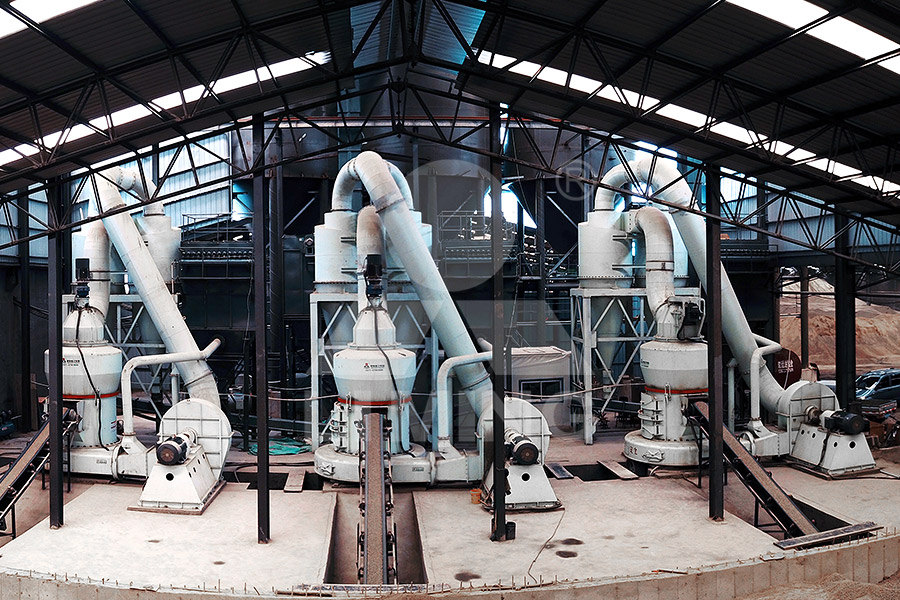
The Cement Manufacturing Process Thermo Fisher Scientific
2023年12月20日 From the limestone mine, to crushing, blending, the raw mill, kiln and beyond, elemental analysis is a critical component to driving process control, efficiencies, and higher quality end products Powerful analyzers can help you better understand the composition of your raw materials, and give you more control over downstream production processes1971年8月17日 Typically, these raw materials are obtained from openface quarries, but underground mines or dredging operations are also used Raw materials vary from facility to facility Some quarries produce relatively pure limestone that requires the use of additional raw materials to provide the correct chemical blend in the raw mix116 Portland Cement Manufacturing US EPA14 小时之前 The manufacture of Portland cement is a complex process and done in the following steps: grinding the raw materials, mixing them in certain proportions depending upon their purity and composition, and burning them to sintering in a kiln at a temperature of about 1350 to 1500 ⁰C During this process, these materials partially fuse to form nodular shaped clinker Manufacturing of Portland Cement – Process and MaterialsThe raw materials such as limestone, clay, and iron ore are crushed and then ground into a fine powder in ball mills or tube mills Dry raw materials are used in this process, and after being ground into a fine powder, they are put into a kiln The following are the main steps of the dry process of cement manufacturing:2 Types of Manufacturing of Cement Wet and Dry Process