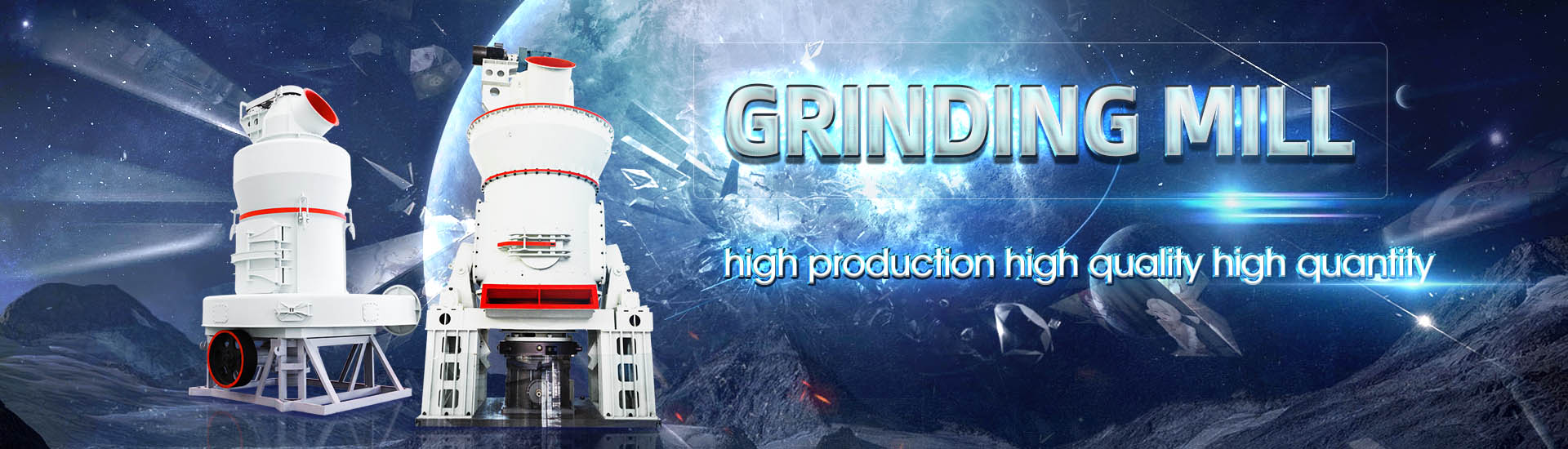
Sintering fourroller operation and maintenance method

Efficient and Clean Production Practice of LargeScale Sintering
Four curve fitting methods are adopted to analyze the temperature of wind box exhaust gas, developing the advanced judgment criterion of sinter temperature and sinter end, which can provide a scientific basis for controlling BTP (Burning Through Point) precisely How to realize 2022年1月1日 The known designs of pallet cars roller assemblies for the manufacturing of sinter and pellets on conveyor lines are analyzed in the paper The advantages and disadvantages Design and Durability of Roller Assemblies in Sintering 2012年9月14日 This technique has been applied to four sintering machines at Kimitsu and Oita Works, Nippon steel Corp since 1996 and contributed to their high productivity operation Highproductivity Operation of Commercial Sintering 2021年7月1日 Sintering is a thermal process used to agglomerate a base mix, which consists of iron ore fines, coke fines (which act as the sintering fuel) fluxes (usually limestone and Study of Frequent Failures of the Pressure Roller at
.jpg)
PhaseField Simulation of Sintering Process: A Review
Sintering, a wellestablished technique in powder metallurgy, plays a critical role in the processing of high melting point materials A comprehensive understanding of structural changes during 2020年4月2日 existing sintering capacity deficiency The Mosaic Embedding Iron Ore Sintering process (MEBIOS) was employed as a new major technology to cope with the possible future Introduction of New Technologies in Sintering Machine Combined with the sintering FGD projects have been implemented, according to the characteristics of sintering plant condition and flue gas conditions, from the aspects of Design, operation and maintenance of wet desulfurization 2021年1月1日 There are two methods for processing metals and ceramics using laser power: indirect method and direct method However, the indirect method cannot be “strictly” called Overview of conventional and unconventional sintering methods
.jpg)
Data‐driven modelling methods in sintering
2022年11月30日 First, the mechanism and characteristics of the sintering process are introduced and analyzed elaborately Second, the detailed research status of the sintering process is illustrated from four aspects: key parameters 2012年4月6日 Juarez, Chih, Mexico Summary This chapter contains sections titled: Introductory Overview Physical Description Viscous Sintering SolidState Sintering LPS Sintering: Fundamentals and Practice Wiley Online Library2024年3月16日 The sintering process is an intricate system with a protracted process flow The steps in the manufacturing line are primarily composed of the ingredients and mixing process, the sintering operation process, and the treatment of the sintered ore [39, 40]22 Important parameters and characteristics of sintering process As shown in Fig 2, all variables affecting Application of deep learning in iron ore sintering process: a 2022年11月30日 The division of roller bearings can be done in several different ways: According to the direction of force, they are divided into: radial (transmitting force in the radial direction); axial (transmitting force in the axial direction) and radialaxial (transmitting force in the radial and axial directions) []Depending on the mounting method, they can be: fixed, which transmit radial and Selection, Dimensioning and Maintenance of Roller Bearings
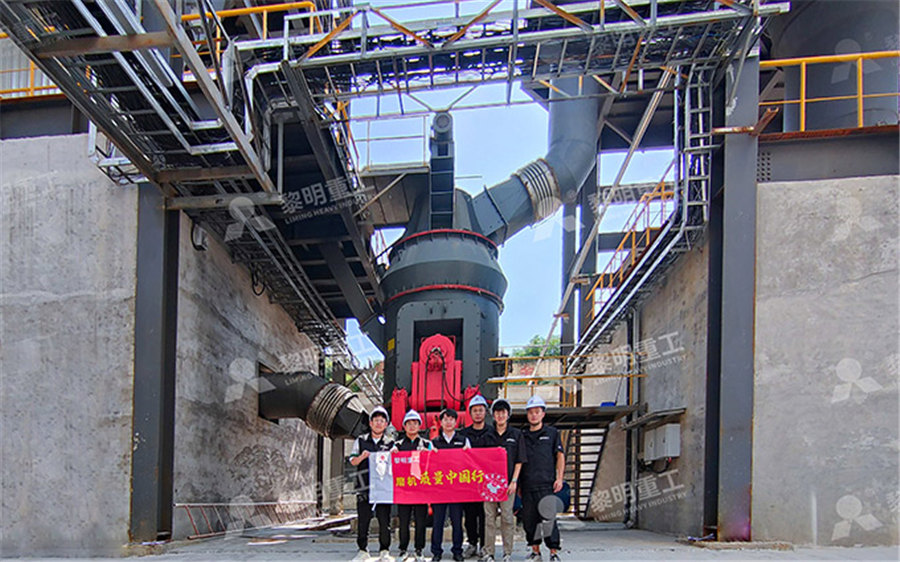
Overview of conventional and unconventional sintering methods
2021年1月1日 Roughly, sintering can be classified into three major processes: (1) solidphase, (2) liquidphase, and (3) vaporphase sintering methods [1], [4] In the first case, all components of the system are solid through the whole process This is the case when sintering crystalline and amorphous solids2012年9月14日 the principle of the method and its effects of improving the commercial operation of sintering machines 2 Principle of Standsupport Sintering Method In a typical sintering machine, blended fine iron ore mixed with coke breeze, which serves as the fuel, is loaded onto grate pallets to form a thick bed, ignited at the upper surface of the bed Highproductivity Operation of Commercial Sintering 2016年10月28日 Sintering is an agglomeration process that fuses iron ore fines, fluxes, recycled products, slagforming elements and coke The purpose of sintering is to obtain a product with suitable (PDF) Iron Ore Sintering: Raw Materials and Granulation2003年10月1日 Both sintering methods ensure obtaining the material with appropriate dielectric and ferroelectric parameters, and the tests carried out verified that the ceramic materials have a diverse range of Selective Laser Sintering: A Qualitative and Objective Approach
.jpg)
Numerical Investigation of Vertical Roller Mill Operation
2023年12月4日 21 Vertical Roller Mill The VRM shall have three or four rollers and a table The rollers were pressed against the ore and table using hydraulic cylinders during operation The table is rotated by an external drive train, and rollers are counterrotated due to the friction between the roller and materialThe spark plasma sintering (SPS) method is of great interest to the powder and powder metallurgy industry and material researchers of academia for both product manufacturing and advanced material research and development Today in Japan, a number of SPS products for different industries have already been realized Today’s fifthgeneration SPS systems are Progress of Spark Plasma Sintering (SPS) Method, Systems2022年9月1日 Iron ore sintering is a pretreatment step of smelting that agglomerates the iron ore using surface melting of green pellets to improve the quality of the steel product The sintering process not only improves the quality of steel products, but also releases CO and CO2 gases, evaporates moisture, and improves the reducibility of iron ore to ensure smooth operation of Review of computational fluid dynamics modeling of iron sintering 2019年10月17日 main causes for bad quality in the final part Shifts can be caused by nonuniform sintering of layers, collision of roller with a sintered layer due to inadequate distance from the layer, high friction between roller and surface of powder in build platform, previous layer’s warped edge which is easily hit by the roller, software failure, andA Comparative Investigation of Sintering Methods for

Study of Frequent Failures of the Pressure Roller at
2021年7月1日 roller sets and sealing elements are designed for reliable operation and low maintenance [1] The sidewall design allows temperatures up to 1350 C The pallet car assembly is shown in Fig 1b–c Pressure rollers are used in pellet cars for gripping the track as shown in Fig 1d Pallet cars include a rail track assembly with four sets of SINTERING PRODUCTION is one of important operation during iron and steel is produced, existing sintering processing uses a kind of continuous pallettype sintering machine, sintering machine as shown in Figure 4 includes the sintering pallet group 12 be linked in sequence by multiple sintering pallet on the surperficial slideway 13 of the upper side band being arranged The Inspection and maintenance method of sintering machineThis article provides a comprehensive overview of the latest research advancements in phasefield sintering models, as shown in Fig 1In Section 2, a summary of energybased phasefield sintering models is mencing with the introduction of the fundamental phasefield sintering model, subsequent discussions address models that incorporate considerations for PhaseField Simulation of Sintering Process: A Review2023年12月15日 A new disposal method for white mud: Replacing limestone in iron ore sintering all of the obtained sinter was dropped from a height of 2 m onto the steel plate four times and screened The proportion of sinter larger than 5 mm among the total weight of the sinter is the yield High temperature mineralization behavior of mixtures during A new disposal method for white mud: Replacing
.jpg)
Optimization of Selective Laser Sintering Process Parameters
2018年6月5日 Selective laser sintering (SLS) empowers the fast, flexible, costefficient, and easy manufacture of prototypes for various application of required shape and size by using powder based material to the Taguchi parametric strategy L9 at various combinations of process parameters and arithmetical optimization method ANOVA was used to decide 2023年12月2日 Protonic ceramic fuel cells with high efficiency and low emissions exhibit high potential as nextgeneration sustainable energy systems However, the practical proton conductivity of protonic Sinteringinduced cation displacement in protonic ceramics 2021年8月15日 The sintering process is an important part of iron and steel production (Cheng et al, 2016)The gaseous pollutants emitted from this process accounting for 40% of the total emissions from steel production (Zhang et al, 2020c)The sintering flue gas has the characteristics of complex composition, wide temperature range, high oxygen content, and Environmental and economic impact assessment of three sintering 2024年9月13日 Selective laser sintering (SLS) is a bed fusion additive manufacturing technology that facilitates rapid, versatile, intricate, and costeffective prototype production across various applications It supports a wide array of thermoplastics, such as polyamides, ABS, polycarbonates, and nylons However, manufacturing plastic components using SLS poses Selective Laser Sintering of Polymers: Process Parameters
.jpg)
Design and subsystem development of a high temperature
2015年1月1日 Early models of polymers selective laser sintering are found in [8], [9], [10] A recent review of thermal models and methods for laser sintering and selective laser melting has been published by Zeng et al, reinforcing the importance of managing the material temperature prior to and during the laser energy deposition and melting process [11]2021年5月5日 center and end castings, where the roller sets and the side walls are mounted, are joined with bolts The center casting is symmetrical and can be reversed for extended use The roller sets and sealing elements are designed for reliable operation and low maintenance The split sidewall design allows for an exchange of theSintering and pelletizing services Pallet cars for sintering 2021年7月19日 Realtime monitoring systems are being used to record information for both quality control and preventative maintenance Information about power draw can be automatically sent to the furnace manufacturer on a Advances In Powder Metal Sintering Technology 2020年9月2日 Models Standard Carrier Dimensions* Max Operating Temp Max Throughput Total Dimensi Width Length Length PILOT PRS© 300 mm 420 mm 1,400 °C 120 kg/hr 178 m PILOT PRL© 300 mm 420 mm 1,400 °C 180 kg/hr 188 m SERIES RCS© 700 mm 460 mm 1,190 °C 450 kg/hr 215 m SERIES RCL© 700 mm 460 mm 1,190 °C 680 kg/hr 255 m ROLLER HEARTH SINTERING FURNACE ONE SOLUTION
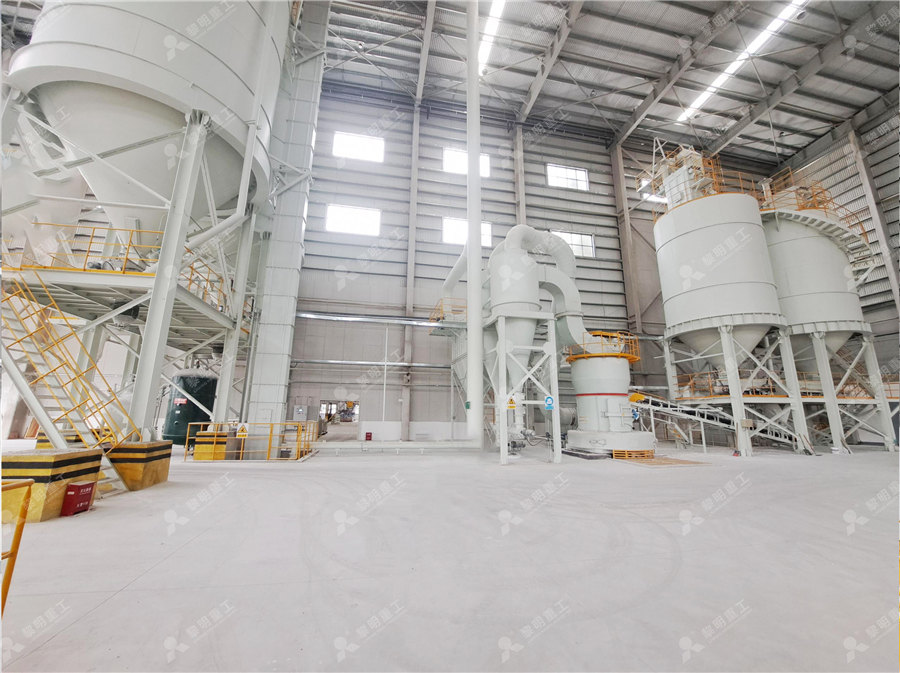
Study of Frequent Failures of the Pressure Roller at Sinter Plant
2021年3月22日 Pressure rollers are used for gripping pellet cars as they travel through the track Of 776 pressure rollers, four were found broken after three years of service in a pellet plant of an integrated steel plant Fatigue cracks had initiated from heavy dent marks at outer surface in all the failed roller Microstructural analysis revealed dents with some foreign particles embedded 2015年3月15日 Sintering plant operations Coke breeze is need to be crushed (normally in four roll crusher) to obtain the correct particle size (025 mm to minus 3 mm) for enhancing sinter productivity and reducibility Less than 025 mm coke size has a negative effect on the productivity, while size fractions of – 315 mm to + 100 mm shows better Understanding Sinter and Sinter Plant Operations IspatGuru2016年7月13日 Our research team proposes a colored manufacturing technology with a layerbylayer printing process Using digital inkjet printing in layerbylayer printing color graphics, a further lowcost color 3D Printing (3DP) technology can be developed It can provide an integrated way to prototype and reproduce 3D objects, from concept to design and manufacturing Color 3D Printing: Theory, Method, and Application2023年12月6日 four rows of rollers Fourrow cylindrical roller bearings are also available with a variety of heattreatment options to suit different operating conditions It is important that any replacement bearings, or parts of bearings, are of the same specification as originals Fourrow cylindrical roller bearing component designationsMounting and maintenance instructions Fourrow
.jpg)
Numerical Modeling of the SolidState Sintering Process by
So the use of sintering techniques for processing materials (ceramic or hard metal) to manufacture parts with structural and functional applications will continue to be a challenge in the coming years [2, 4] Solidstate sintering is the bonding and densification of particles by the application of heat below the melting point of a material [5, 6]2023年11月25日 InSitu Resource Utilisation (ISRU) is increasingly being seen as a viable and essential approach to constructing infrastructure for human habitation on the moon Transporting materials and resources, from Earth to the Moon, is prohibitively expensive and not sustainable for longterm, largescale development Various fabrication technologies have been Regolith sintering and 3D printing for lunar construction4 天之前 FourRoller Plate Rolling Machine is one curved, calibration equipment, which specialized in sheet metal bending work and can roll a variety of specifications of cylindrical, and curved workpieces The sheet metal can be shaped and flattened on the 4roll bending machine In addition, appropriately adjusting the relative position between the side roll and the top roll, 4 Roll Plate Roller Operation Manual 2022 ultimate2017年9月10日 Powder Sintering Powder sintering involves raising the temperature of the green compact, (pressed powder part), to a certain level and keeping it at that temperature for a certain amount of time The sintering temperature is usually between 70% and 90% of the melting point of the powder metal This will cause bonding mechanisms to occur between powder Pressing And Sintering Of Powder Parts
.jpg)
Application of deep learning in iron ore sintering process: a
2024年3月16日 The sintering process is an intricate system with a protracted process flow The steps in the manufacturing line are primarily composed of the ingredients and mixing process, the sintering operation process, and the treatment of the sintered ore [39, 40]22 Important parameters and characteristics of sintering process As shown in Fig 2, all variables affecting 2022年11月30日 The division of roller bearings can be done in several different ways: According to the direction of force, they are divided into: radial (transmitting force in the radial direction); axial (transmitting force in the axial direction) and radialaxial (transmitting force in the radial and axial directions) []Depending on the mounting method, they can be: fixed, which transmit radial and Selection, Dimensioning and Maintenance of Roller Bearings2021年1月1日 Roughly, sintering can be classified into three major processes: (1) solidphase, (2) liquidphase, and (3) vaporphase sintering methods [1], [4] In the first case, all components of the system are solid through the whole process This is the case when sintering crystalline and amorphous solidsOverview of conventional and unconventional sintering methods2012年9月14日 the principle of the method and its effects of improving the commercial operation of sintering machines 2 Principle of Standsupport Sintering Method In a typical sintering machine, blended fine iron ore mixed with coke breeze, which serves as the fuel, is loaded onto grate pallets to form a thick bed, ignited at the upper surface of the bed Highproductivity Operation of Commercial Sintering
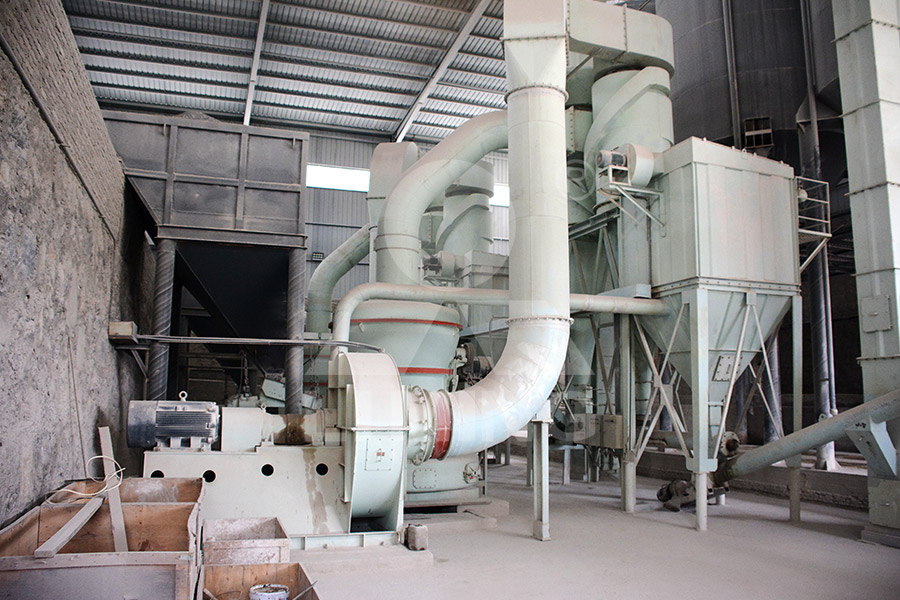
(PDF) Iron Ore Sintering: Raw Materials and Granulation
2016年10月28日 Sintering is an agglomeration process that fuses iron ore fines, fluxes, recycled products, slagforming elements and coke The purpose of sintering is to obtain a product with suitable 2003年10月1日 Both sintering methods ensure obtaining the material with appropriate dielectric and ferroelectric parameters, and the tests carried out verified that the ceramic materials have a diverse range of Selective Laser Sintering: A Qualitative and Objective Approach2023年12月4日 21 Vertical Roller Mill The VRM shall have three or four rollers and a table The rollers were pressed against the ore and table using hydraulic cylinders during operation The table is rotated by an external drive train, and rollers are counterrotated due to the friction between the roller and materialNumerical Investigation of Vertical Roller Mill Operation The spark plasma sintering (SPS) method is of great interest to the powder and powder metallurgy industry and material researchers of academia for both product manufacturing and advanced material research and development Today in Japan, a number of SPS products for different industries have already been realized Today’s fifthgeneration SPS systems are Progress of Spark Plasma Sintering (SPS) Method, Systems
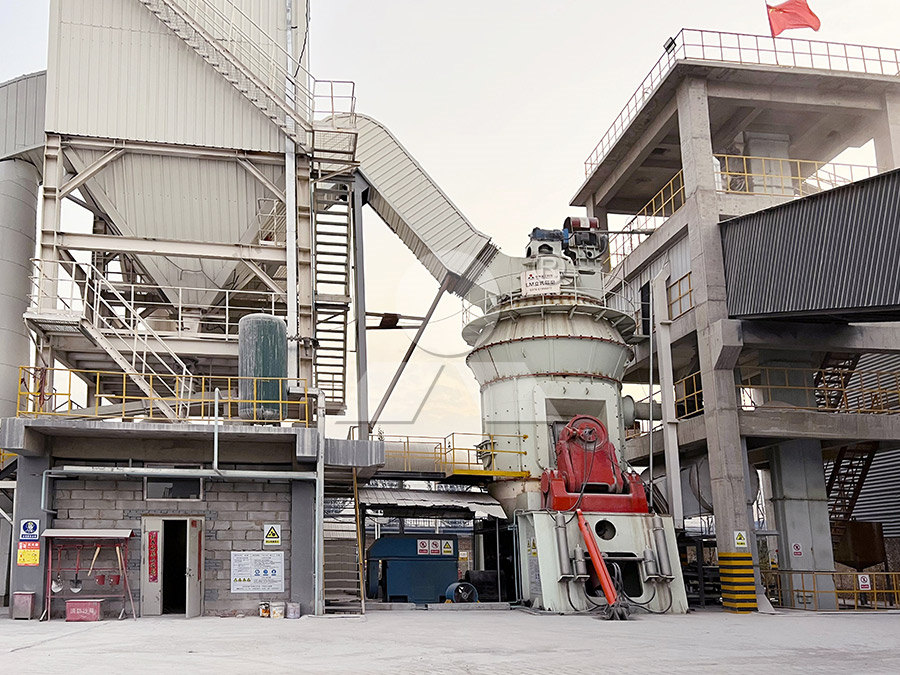
Review of computational fluid dynamics modeling of iron sintering
2022年9月1日 Iron ore sintering is a pretreatment step of smelting that agglomerates the iron ore using surface melting of green pellets to improve the quality of the steel product The sintering process not only improves the quality of steel products, but also releases CO and CO2 gases, evaporates moisture, and improves the reducibility of iron ore to ensure smooth operation of 2019年10月17日 main causes for bad quality in the final part Shifts can be caused by nonuniform sintering of layers, collision of roller with a sintered layer due to inadequate distance from the layer, high friction between roller and surface of powder in build platform, previous layer’s warped edge which is easily hit by the roller, software failure, andA Comparative Investigation of Sintering Methods for