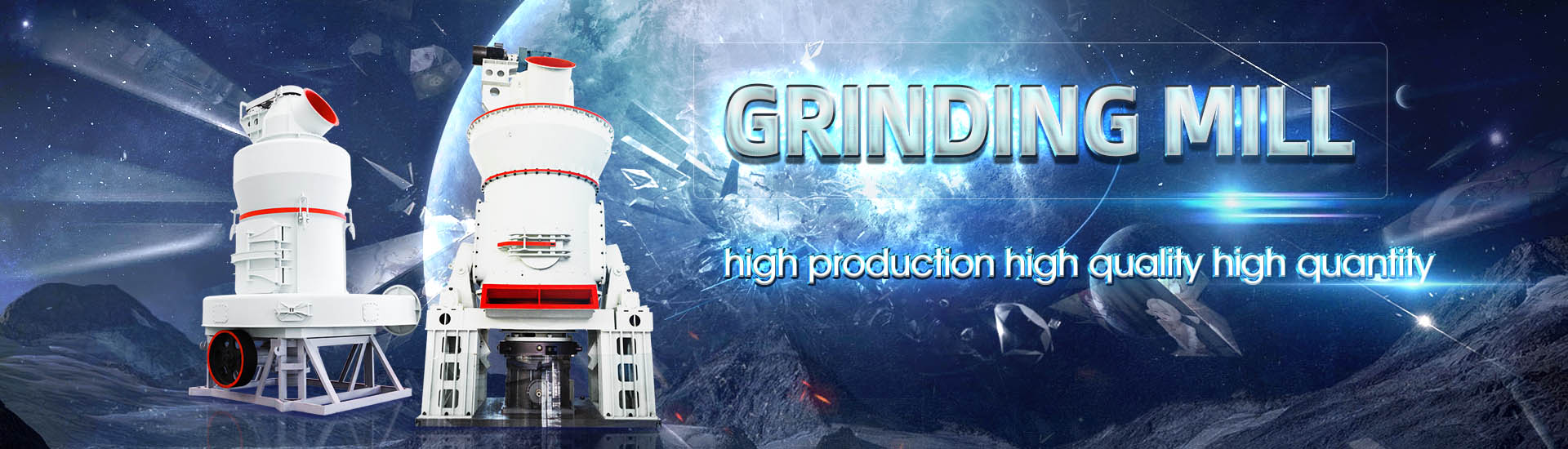
HOME→Information on the purchase of ore grinding mills required for proposed projects in Sichuan and Chongqing areas in 2013
Information on the purchase of ore grinding mills required for proposed projects in Sichuan and Chongqing areas in 2013
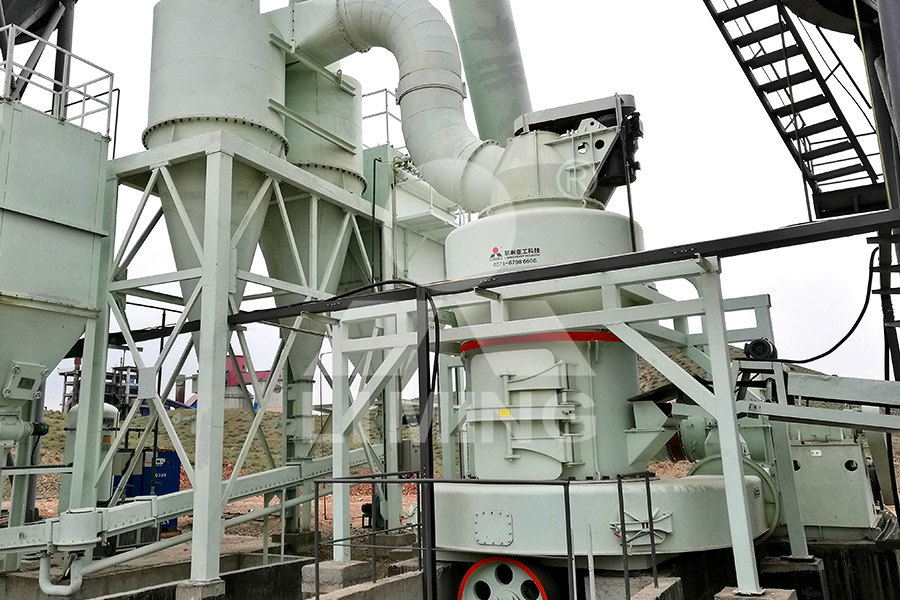
Ore characterization, process mineralogy and lab
2014年6月1日 Automated mineralogical analyses enable mining operations to perform daily process support Process mineralogy also should be used in the development phases of new 2024年11月25日 We have supplied numberless of wet grinding rod mills for customer in coal chemical industry, to deal with the coal and petroleum coke material and prepare for the coal Ore Grinding MillSBM Industrial Technology Group2023年7月20日 Ore grinding is a process to further reduce and disperse the ore particle size In the mineral processing industry, ore grinding is the particle size preparation before the Ore Grinding SpringerLink2019年4月12日 结合当前研究成果及工业现场数据,本文对比了高压辊磨机在金属矿山和球团预处理行业中的工艺流程,以及辊面比压力、辊面线速度、辊缝几个工艺参数,为高压辊磨机在金属矿山和球团预处理应用中工艺参数的选择提供 高压辊磨机在金属矿选矿与球团预处理领域的工艺和
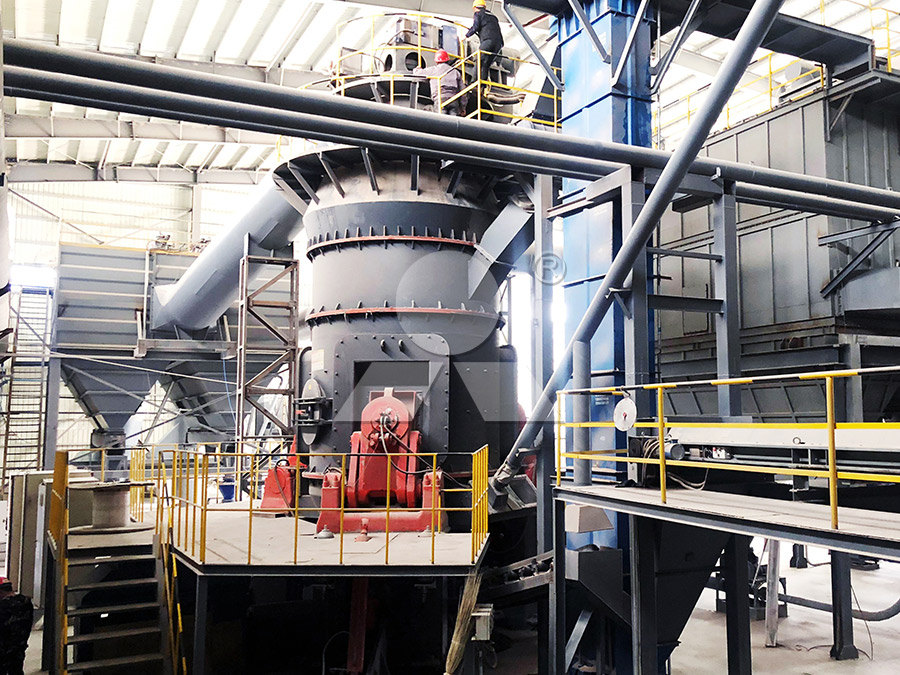
A Review of the Grinding Media in Ball Mills for Mineral
2023年10月27日 Grinding media play an important role in the comminution of mineral ores in these mills This work reviews the application of balls in mineral processing as a function of the 2023年7月31日 Ore grinding is a process to further reduce and disperse the ore particle size In the mineral processing industry, ore grinding is the particle size preparation before the Ore Grinding Methods and Process of Ore GrindingIn the present state of technological development for primary grinding mills, there is a wide choice of acceptable options with respect to type and size, grinding flowsheet and grinding mediaPrimary Grinding Mills: Selection, Sizing And Current Practices2023年10月27日 Grinding media play an important role in the comminution of mineral ores in these mills This work reviews the application of balls in mineral processing as a function of the materialsA Review of the Grinding Media in Ball Mills for
.jpg)
Fine grinding: How mill type affects particle shape characteristics
2017年9月1日 The objective of this work is to assess the influence of fine grinding in ball mills and stirred mills on valuable mineral liberation and particle shape characteristics of UG2 ore, a 2022年1月1日 To operate viably and sustainably, there is a need to reduce costs and energy consumption, particularly of the energyintensive grinding required for lowgrade magnetite Comminution and classification technologies of iron ore2021年1月18日 measure the required design information on every sample The calculation method was set up to use these measurements in a mathematically correct way to size the grinding mills required to grind the ore This method does not require a computer program or a data base It is based only results derived from testingImpact on Grinding Mill Design of Recent New DiscoveriesTechnology and technics of ore preparation processes UDC 622732 O I SKARIN (RIVS Science and Production Association) N O TIKHONOV (JV “IVS”) CALCULATION OF THE REQUIRED SEMIAUTOGENOUS MILL POWER BASED ON THE BOND WORK INDEXES O I SKARIN, Senior Researcher, Candidate of Engineering Sciences N O TIKHONOV, Head of (PDF) Technology and technics of ore preparation processes
.jpg)
Factors affecting ores grinding performance in ball mills
2024年10月13日 Effects of grinding media on ore particles Grinding media affects ore particles in ball mills The type of media and the grinding conditions determine how well the ore is ground, which in turn affects the final product Ball mills are typically used to grind ores that are either small or irregularly shapedThe performance of grinding mills depends on many operating factors among which are the time of grinding, mill speed, grinding media–toore ratio, and filling The aim of grinding is to bring the ore to the meshofgrind (product size) required to obtain optimum liberation size in which the valuable mineral is just released from the ore THE EFFECTS OF PROCESS VARIABLES ON THE GRINDING OF IRON ORESBM Ore Ultrafine Grinding Mill Discharge fineness: 1503000 mesh Feed size: 20 mm Output: 120 T/HSBM Ore Ultrafine Grinding Mill2023年10月17日 Factors for choosing a suitable ore powder grinding mill 1 Raw material characteristics: Different raw materials have different hardness, humidity and grinding and crushing properties, and the corresponding ore powder grinding mill needs to be selected to meet the processing requirements 2 Production capacity: Determine the required processing How to choose a suitable ore powder grinding mill?
.jpg)
CALCULATION OF THE REQUIRED SEMIAUTOGENOUS
2016年1月10日 ore pretreatment laboratory equipped for fullfledged implementation of the first two methods in the list above All of the said methods aim to find specific energy for the required SAG comminution of test ore material Specific energy consumption (SEC) measured in kWh/t is a ratio of the mill drive power to the milling circuit output,2023年10月10日 Types of Grinding Mills Grinding mills play a crucial role in the mining process, as they are responsible for reducing large chunks of ore into smaller particles that can be further processed There are various types of grinding mills available, each designed to meet specific requirements based on the material being ground and the desired outputUnderstanding the SAG Mill in Copper Ore Mining Process2024年9月26日 Energy savings and consumption reduction of ball mills are crucial for industrial production The grinding medium is an important component of a ball mill In theory, using higherdensity grinding media can yield better grinding results However, for materials with varying grindability, employing grinding media of different densities can reduce energy consumption Optimization and Experimental Study of Iron Ore Grinding INTRODUCTION Primary grinding mills as defined in this paper, are autogenous or semiautogenous rotating, tumbling mills having a coarse feed with a top size usually varying from 150 to 300 mm (6 to 12 inches) Most frequently, the feed to these mills is the product of primary crushing plants but in some cases run of mine ore is used as feed such as at Benguet, Primary Grinding Mills: Selection, Sizing And Current Practices
.jpg)
The effects of iron ore concentrate grinding methods (HPGR
2020年10月18日 An iron ore concentrate sample was ground separately in a pilotscale HPGR mill in multiple passes and a dry opencircuit ball mill to increase the specific surface area of particles2019年4月19日 Ore grinding mills are really just slowly rotating barrels, but barrels that are growing in size so fast that the application of electric drives for them is A utility often limits that dip at the point of purchase to 3% or less A dip at the motor in excess of 20% will cause excessive loss of starting torque and exposes plant contactors and Electric Drives for Large Ore Grinding Mills 911MetallurgistFind your ore mill easily amongst the 42 products from the leading brands (Fritsch GmbH, Retsch, Eriez, ) on DirectIndustry, the industry specialist for your professional purchases in Catalogues {0} in Projects {0} in News Trends Brands containing {0} {{>productsMenu}} Products; Catalogs; RFQ ® Grinding Mills are Ore mill, Ore grinding mill All industrial manufacturers2023年7月31日 operation (1) Structure parameters of grinding mill, including its specifications, model, aspect ratio, ore discharging method, and liner form (2) Various working parameters of grinding mill, including fraction of critical speed for grinding mill, filling rate for grinding mill, grinding concentration,grindingcycleload,etc(3)AndgrindOre Grinding Methods and Process of Ore Grinding
.jpg)
A developed approach based on grinding time to determine ore
2013年12月31日 Some authors have proposed new smaller mills that can be used to determine the BWI 1983;Nematollahi, 1994;MenéndezAguado et al, 2005; Saeidi et al, 2013; Mwanga et al, 2017) A group of 2023年4月23日 grinding media in a grinding mill with about 2630 wt% chrome by Chen et al [37] using a phosphate ore in a modified ball laboratory ball mill whose electrochemical potential could be controlled(PDF) Grinding Media in Ball MillsA Review ResearchGate2023年7月10日 The review concludes that stirred mills have significant potential for achieving the energyefficient ultrafine grinding of particles Stirred mills have unique designs and operations, which (PDF) EnergyEfficient Advanced Ultrafine Grinding of The review of ore crushing and grinding processes at the miningandprocessing enterprise is presented An alternative to the standard technology of crushing ore in cone crushers is proposed after a comparative analysis of ore grinding processes The modern branch of industry is characterized by high costs for the implementation ofReengineering of the ore preparation production
.jpg)
Calculation method and its application for energy
2020年2月26日 Measurement results of two ball mills in a real ceramic manufacturing plant showed that the proposed calculation models could achieve an accuracy of more than 96% for predicting the ball mill 4 天之前 A wet grinding 4 x 10 center peripheral discharge rod mill used for producing fine aggregates Twelve 7 x 24 Compeb mills grinding cement clinker to a product of 1750 surface area, 90% passing a 200 mesh screen An 8 x 7 diaphragm type ball mill grinding 05″ copper ore to 96% passing 65 meshGrinding Mills 911Metallurgist2024年7月19日 This automated grinding media feeder is designed to maintain the optimal grinding media load in the mill, ensuring consistent power draw and efficient operation The PLC (Programmable Logic Controllers) is programmed to monitor the grinding mill’s power draw, automatically dispensing grinding media when needed to maintain the desired load and Grinding Mills in the Mineral Processing Industry2023年12月12日 Mathematical models of single and multiloop magnetic circuits of electromagnetic flow transducers with an annular channel are designed taking into account the parameters of the magnetic circuit(PDF) Control of ball mill operation depending
.jpg)
Modeling of Bauxite Ore Wet Milling for the
2022年6月22日 the grinding products are better described by the RR model [24, 27, 28] Over the past decades, the most popular mathematical models used for the optimization of energy consumption in grinding mills are phenomenological grinding kinetics models based on population balance considerations [22] Population balance modeling which is based on4 mechanistic approach, such as energy loss, type and size of the elements involved Previous developments give rise to a model that is able to predict the amount of fine particles captured in aA mechanistic model of SAG mills ResearchGate2018年12月24日 ABSTRACT In this study, simulation aided design of grinding circuit for a gold mine in Iran is presented The main parameters for the design of the grinding circuit are the ore specifications and EVALUATION OF THE ALTERNATIVES FOR GOLD ORE GRINDING 2017年3月20日 An effect of a grinding method, that is ball mill and high pressure grinding rolls (HPGR), on the particle size, specific surface area and particle shape of an iron ore concentrate was studiedPhysicochemical Problems of Mineral Processing Investigation
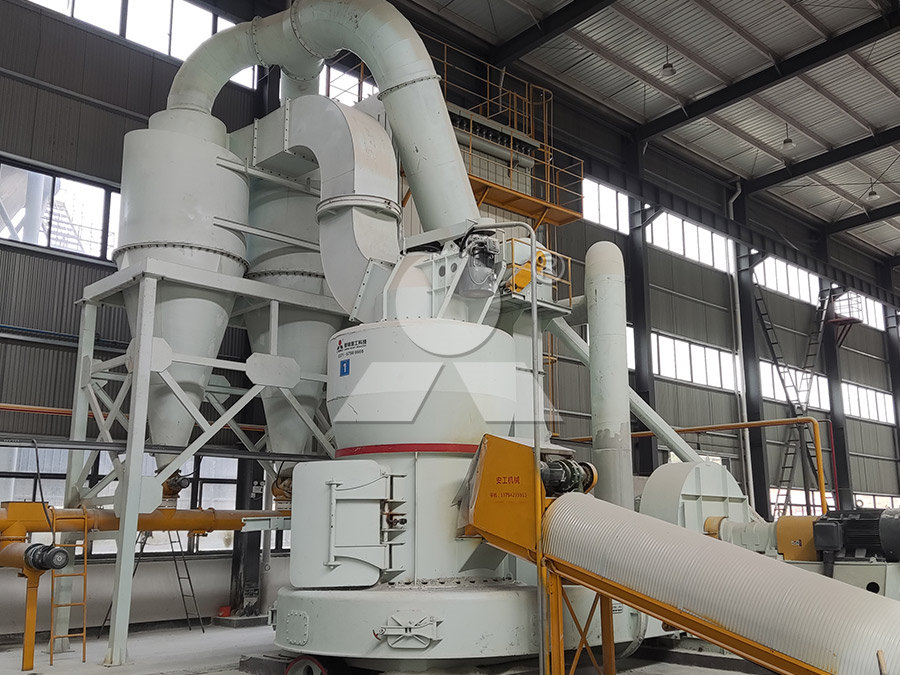
Grind Optimization of Konkola Blended Copper Ore
2020年8月1日 The ore samples studied represented a high quality (HQ) ore dominated by sulphide minerals and low quality (LQ) ore dominated by oxide minerals The project was initiated on the 18th of August, 2015 The experimental results showed that optimization of grind for the blended copper at different grinding times was successfully2017年1月1日 An increase of over 10% in mill throughput was achieved by removing the ball scats from a single stage SAG mill These scats are non spherical ball fragments resulting from uneven wear of balls (PDF) Performance optimization of an industrial ball mill for grinding tests were conducted in a smooth surface cylindrical steel mill of 215 mm diameter and 190 mm long The grinding media consisted of three differentsized steel balls having a density of 768 g/cm3 and diameters of 195, 38, and 50 mm The Bond work index (Wi) of the quartz sample was determined based on two grinding testsEffect of grinding media on the milling efficiency of a Lining is a special finish on the inner surface of the ore grinding mill protecting it from mechanical and physical damage The need for lining is due to the fact that when grinding ore, the walls of the mill drum are subjected to continuous exposure to different fractions of ore Used for cladding large areas of the mill They can also be Rubber Lining for Ore Grinding Mills and Mining and Processing
.jpg)
Impact on Grinding Mill Design of Recent New Discoveries
2021年1月18日 measure the required design information on every sample The calculation method was set up to use these measurements in a mathematically correct way to size the grinding mills required to grind the ore This method does not require a computer program or a data base It is based only results derived from testingTechnology and technics of ore preparation processes UDC 622732 O I SKARIN (RIVS Science and Production Association) N O TIKHONOV (JV “IVS”) CALCULATION OF THE REQUIRED SEMIAUTOGENOUS MILL POWER BASED ON THE BOND WORK INDEXES O I SKARIN, Senior Researcher, Candidate of Engineering Sciences N O TIKHONOV, Head of (PDF) Technology and technics of ore preparation processes 2024年10月13日 Effects of grinding media on ore particles Grinding media affects ore particles in ball mills The type of media and the grinding conditions determine how well the ore is ground, which in turn affects the final product Ball mills are typically used to grind ores that are either small or irregularly shapedFactors affecting ores grinding performance in ball millsThe performance of grinding mills depends on many operating factors among which are the time of grinding, mill speed, grinding media–toore ratio, and filling The aim of grinding is to bring the ore to the meshofgrind (product size) required to obtain optimum liberation size in which the valuable mineral is just released from the ore THE EFFECTS OF PROCESS VARIABLES ON THE GRINDING OF IRON ORE
.jpg)
SBM Ore Ultrafine Grinding Mill
SBM Ore Ultrafine Grinding Mill Discharge fineness: 1503000 mesh Feed size: 20 mm Output: 120 T/H2023年10月17日 Factors for choosing a suitable ore powder grinding mill 1 Raw material characteristics: Different raw materials have different hardness, humidity and grinding and crushing properties, and the corresponding ore powder grinding mill needs to be selected to meet the processing requirements 2 Production capacity: Determine the required processing How to choose a suitable ore powder grinding mill?2016年1月10日 ore pretreatment laboratory equipped for fullfledged implementation of the first two methods in the list above All of the said methods aim to find specific energy for the required SAG comminution of test ore material Specific energy consumption (SEC) measured in kWh/t is a ratio of the mill drive power to the milling circuit output,CALCULATION OF THE REQUIRED SEMIAUTOGENOUS 2023年10月10日 Types of Grinding Mills Grinding mills play a crucial role in the mining process, as they are responsible for reducing large chunks of ore into smaller particles that can be further processed There are various types of grinding mills available, each designed to meet specific requirements based on the material being ground and the desired outputUnderstanding the SAG Mill in Copper Ore Mining Process
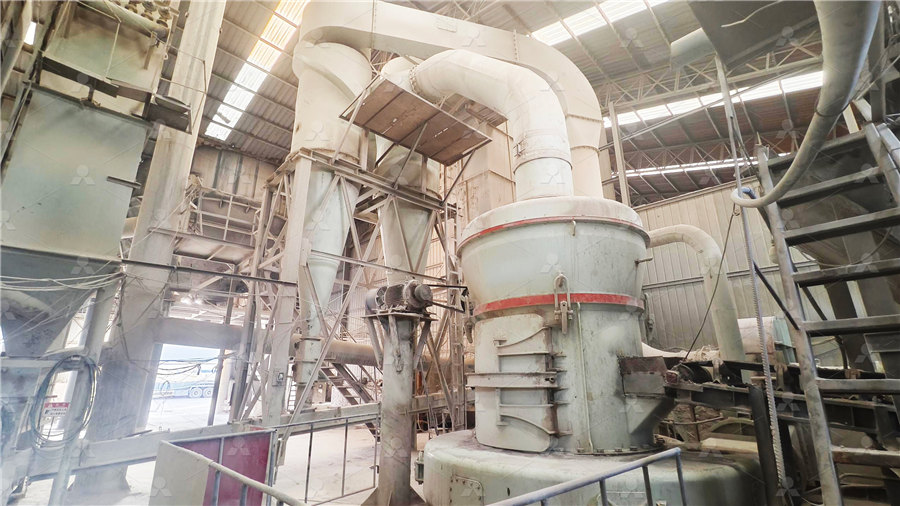
Optimization and Experimental Study of Iron Ore Grinding
2024年9月26日 Energy savings and consumption reduction of ball mills are crucial for industrial production The grinding medium is an important component of a ball mill In theory, using higherdensity grinding media can yield better grinding results However, for materials with varying grindability, employing grinding media of different densities can reduce energy consumption INTRODUCTION Primary grinding mills as defined in this paper, are autogenous or semiautogenous rotating, tumbling mills having a coarse feed with a top size usually varying from 150 to 300 mm (6 to 12 inches) Most frequently, the feed to these mills is the product of primary crushing plants but in some cases run of mine ore is used as feed such as at Benguet, Primary Grinding Mills: Selection, Sizing And Current Practices