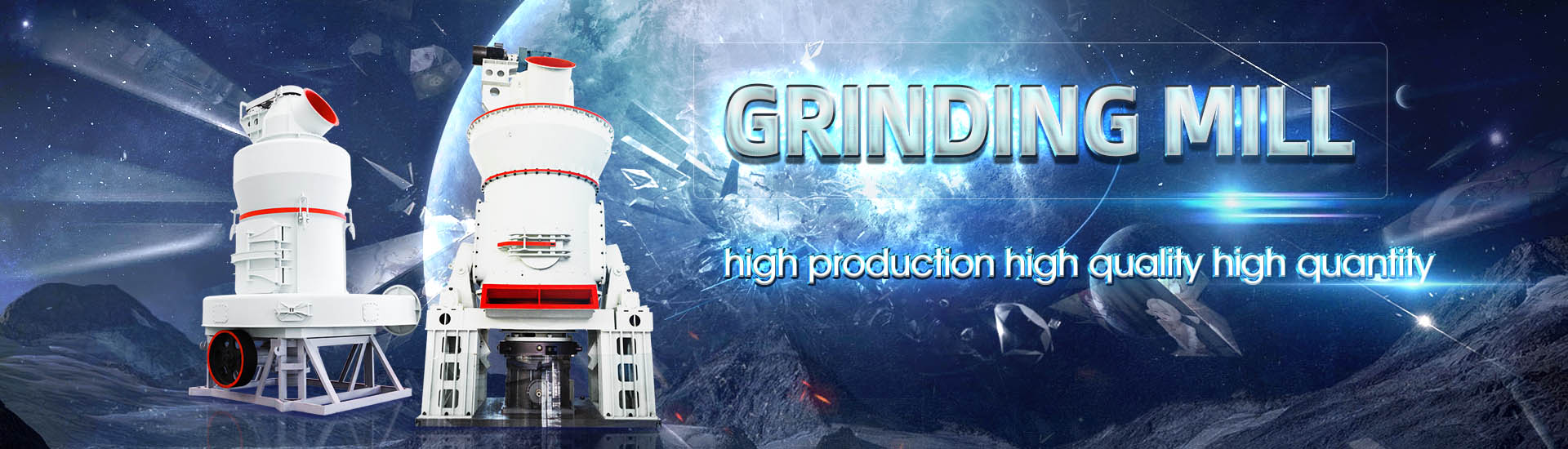
Coal mill bearing maintenance
.jpg)
MAINTENANCE MAINTENANCE OF OF BEARI BEARINGS USED IN
This work presents a technique for bearing maintenance using monitoring by vibration analysis The goal is to apply the method of repowering on cylindrical roller bearings and conical roller bearings used in a coal mill of a Cement industry, through dimensional analysis, predictive The document discusses maintenance of coal mills, including general maintenance activities, preventive maintenance programs, and performance indicators It provides details on 04 Coal Mill Maintenance R2 PDF Bearing Scribd2011年1月1日 Analyze technical characteristics of coal handling system and operating characteristics of the relevant machinery and equipment Then, the safe operation of coal Operation and Maintenance of Coal Handling System in Thermal Regular Maintenance: Routine maintenance of coal mills and associated equipment is vital for preventing mechanical failures This includes inspecting and replacing worn parts, checking Coal Mill Safety: A Critical Aspect of Power Plant Operations Coal
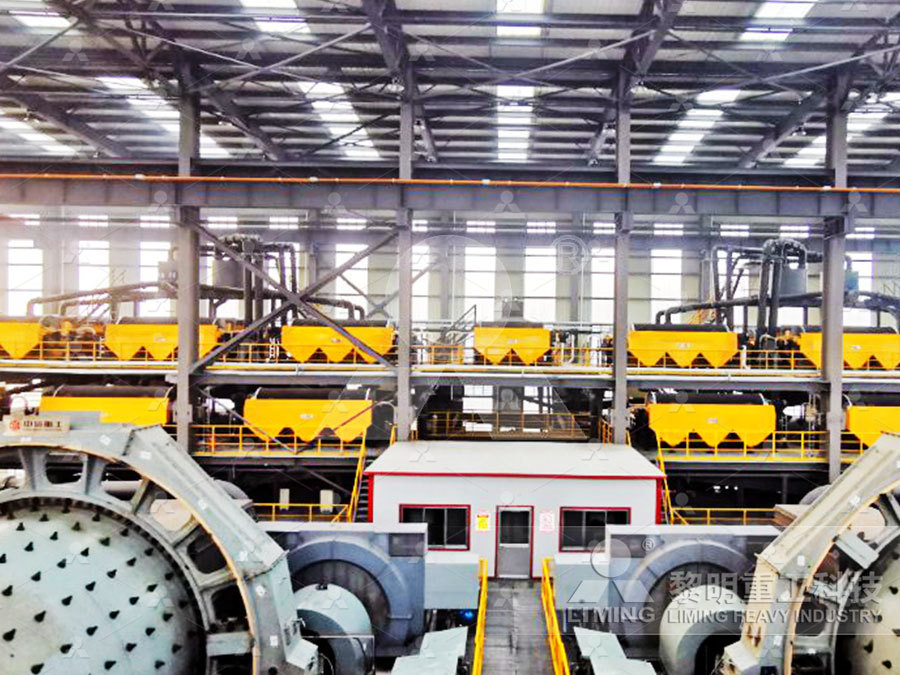
OPERATION AND MAINTENANCE OF CRUSHER HOUSE FOR COAL
To maintain an efficiently operating unit and avoid failure of critical equipment, it is necessary to maintain the critical parts of that equipment There are varieties of critical equipments 2011年12月31日 Defects such as fastener oxidation and corrosion and liner edge warping are recurrent in coal bunkers, requiring maintenance and repair in order to avoid inner wall damages, compromising the(PDF) Operation and Maintenance of Coal Handling Routine Maintenance and Breakdown Maintenance of Milling Plant Overhauling of Milling Plant Preventive measures for stopping erosion of Pulverized Coal lines bends and their proper Operation Maintenance of Coal Mills Feeders National the following process The screening and broken coal machinery as the key equipment of coal conveying system and responsible for the normal operation of the power plant to continually Operation and Maintenance of Coal Conveying System Screening
.jpg)
Predictive Maintenance of Coal Pulverizing Mill Using
This paper proposes a predictive maintenance policy for a coal pulverizing mill by integrating the Failure Mode Effect and Criticality Analysis (FMECA) and output measurement FMECA is used2024年11月19日 Covers premaintenance history to work execution through analysis and having the results with postcondition monitoring data Uses actual machine maintenance photos for Condition Monitoring in Thermal Power Stations2021年5月12日 Babcock is helping to keep South Africa’s power going, following the award of a mill maintenance contract at a major power station Babcock’s diverse scope of work for the fiveyear contract covers the dayto Mill maintenance contract at power station awardedBowl Mill has long been recognized as the most advantageous design of the coal pulverisers and include low initial cost, low maintenance cost, removal of tramp iron, low power consumption, easy maintenance, wide range output, quiet operation The basic features of Bowl Mill (Puveriser) supplied by BHEL are:BHARAT HEAVY ELECTRICALS LIMITED
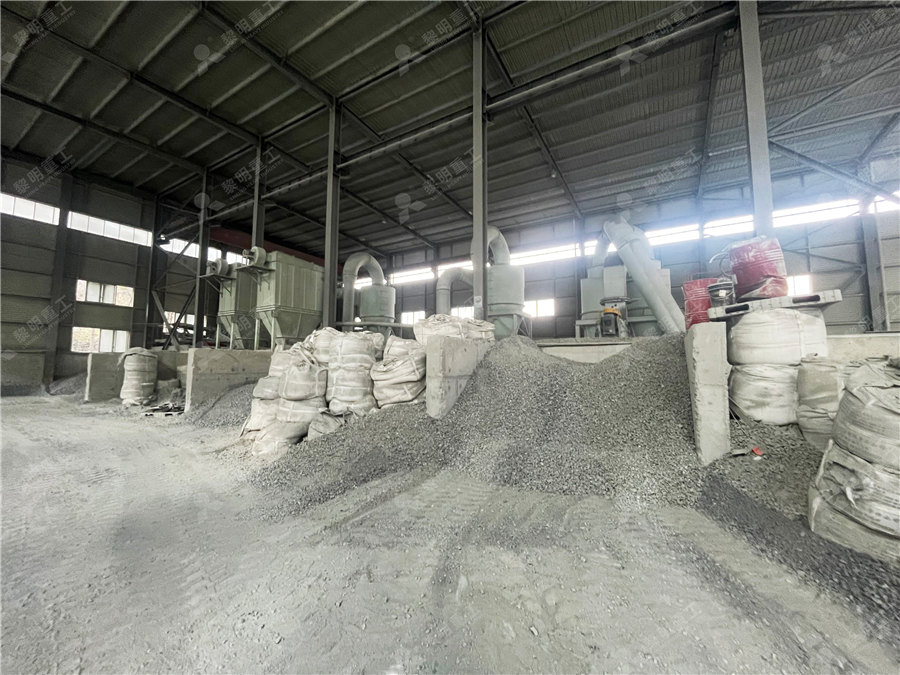
LOESCHEMILLS
1927 First Loesche coal mill delivered for the Klingenberg power station in Berlin 1953 500th coal mill plant sold worldwide 1961 Introduction of hydraulic spring assembly system 1965 Construction of first pressure mill (LM 122 D) 1980 Delivery of first modular coal mill (LM 263 D) 1985 Delivery of first selfinerting coal grinding plant (LM 212 D) for the steel industry (PCI As a result maintenance downtime is reduced and work is easy and safe Our MPS vertical mills MPS 4750 BC cement mill, MPS 200 BK coal mill, Krimzement Bakhchisarayski, Ukraine MPS 3070 BK coal mill, Jaypee Cement Balaji, India MPS 180 GC vertical roller mill for the grinding, drying and calcining of gypsum, Knauf Knin, CroatiaCoal mill, gypsum mill, clay mill, etc Pfeiffer MPS mills2023年5月25日 Proper mill trunnion seals help maintain bearing integrity and extend life Mill trunnion seals must be designed to withstand operating conditions and effectively keep out dust, moisture and other contaminants that can affect mill trunnion bearing performance 6 Proper lubrication is vital for trunnion longevity and performanceHow to Choose Ball Mill Trunnion for Cement Mill, Autogenous Mill, Coal Low installation costs Easy maintenance Nozzle ring 100% 100% 200 300% 1500 3000% 100 200% 45 60 m/s ATOX coal mill will grind any type of coal to the required fineness An oil circulation system effectively lubricates the bearings of the grinding rollersATOX COAL MILL
.jpg)
A Study on 500 MW Coal Fired Boiler Unit’s Bowl Mill
Section of coal bowl mill Table 1 Guaranteed coal conditions for mill performance evaluation Coal Moisture % 20 Coal HGI 55 Mill Outlet Temperarure °C 80 Mill Air Flow T/hr 102 Coal Fineness (% passing trough 200 mesh) 70% passing through 200 mesh and 90% passing through 50 mesh Differental Pressure 300 mmwc Coal Output from Mill 609 t/hr2012年11月17日 20 131Fineness Fineness is an indicator of the quality of the pulverizer action Specifically, fineness is a measurement of the percentage of a coal sample that passes through a set of test sieves usually designated at 50, 100, and 200 mesh A 70% coal sample passing through a 200 mesh screen indicates optimum mill performance The mill wear and Coal mill pulverizer in thermal power plants PPT SlideShareThe document discusses maintenance and repair of an ATOX Vertical Mill It describes systematic and conditionbased maintenance approaches Systematic maintenance consists of regular cleaning, lubrication and visual inspections Conditionbased maintenance monitors factors like vibration levels and temperatures during operation and performs more thorough inspections Atox Vertical Roller Mill, Maintenance and Repair PDF Bearing Maintenance of bearings used in a coal mill Figure 2 Conical bearing after repowering After repowering, the bearing was placed in operation, and a fourth measurement (C4) was performed, obtaining an acceleration of 177 g This value is below the alarm 1, which characterizes normal operating levelsMAINTENANCE MAINTENANCE OF OF BEARI BEARINGS USED IN A COAL MILL
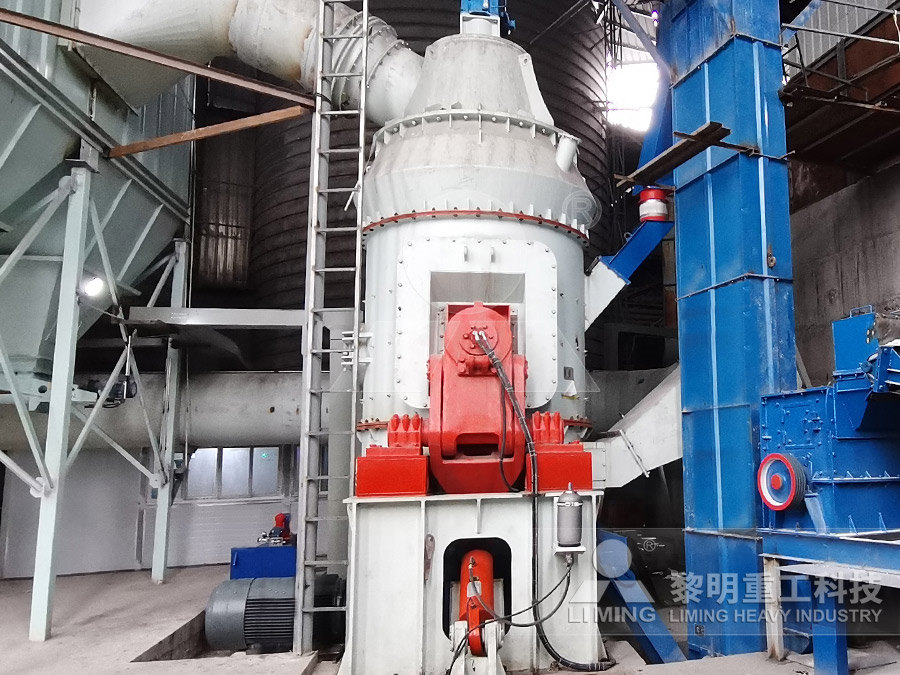
Scheduled Maintenance Reduces Plant Downtime
2020年5月27日 Visual inspections and planned maintenance can extend the life of equipment in the prep plant by steve fiscor, editorinchief Compared to working sections in an underground mine, preparation plants are much more A ball mill maintenance procedure is a crucial process in ensuring the longevity and efficient operation of your mill A poorly maintained ball mill can cause significant downtime, leading to costly repairs and lost production In this article, we will discuss the importance of regular maintenance, premaintenance steps, the ball mill maintenance procedure, postmaintenance Ball Mill Maintenance Procedure: Tips for Maintaining Your Mill2024年8月6日 In an integrated steel plant, the pulverized coal injection (PCI) mill plays an important role in providing pulverized coal to the blast furnace The main purpose of using PCI coal is to reduce the hot metal production cost through the utilization of noncoking coal and to extend the available coke oven life Any unplanned outage of the PCI mill leads to increase in Failure Analysis of Pulverized Coal Injection (PCI) Mill Grinding Introduction This article concerns itself with vertical grinding mills used for coal pulverization only (coal pulverizers), although vertical grinding mills can and are used for other purposes The 3D model in the saVRee database represents a vertical grinding bowl millOther grinding mill types include the ball tube mill, hammer mill, ball and race mill, and , roll and ring millVertical Grinding Mill (Coal Pulverizer) Explained saVRee
.jpg)
Ball Mill Maintenance Installation Procedure 911Metallurgist
2016年10月20日 General Ball Mill Maintenance After the mill is erected, in order to avoid overlooking both obvious and obscure installation details, we recommend the use of a check list This is particularly recommended for multiple mill installations where it is difficult to control the different phases of installation for each and every mill2024年11月19日 Covers premaintenance history to work execution through analysis and having the results with postcondition monitoring data Coal Mill 1EF: Gearbox Input NDE Bearing Damage – September 2019 Abstract chapter 6 7 pages Case Study 5 Coal Mill 2CD: Output Gear Shaft Crack Detection – July 2019Condition Monitoring in Thermal Power Stationsreliability of the mills and their rolling bearings Bearings supporting the grinding rollers in the vertical mill Floating bearing end: Doublerow cylindrical roller bearing (series NNU41) Locating bearing end: spherical roller bearing (series 231) Fine product Feed material SLS high efficiency classifier for accurate classification Entirely Rolling Bearings in Vertical Mills Built by Gebr Pfeiffer AG, Germany2011年1月1日 b9 lubrication of coal crusher Bearing lubrication is an important part of coal crusher, the oil should be 1 / 2 to 2 / 3 is appropriate of the oil chamber :4648 [4] lihua Zhao Operation and Maintenance of Coal Handling System in Thermal Power Plant [J]Colliery Machine;2011, 32(2):201204 ss door, not attached to the Operation and Maintenance of Coal Handling System in Thermal Power
.jpg)
Coal Mill Installation PDF Bearing (Mechanical) Gear
coal mill installation Free download as Word Doc (doc), PDF File (pdf), Text File (txt) or read online for free This document provides installation instructions for a tube ball mill It describes the working principle and structure of the mill, including the feeding part, main bearing, rotary part, and discharge part It also covers installation requirements, commissioning, operation 5 Construction, Working and Maintenance of Crushers for Crushing Bulk Materials practicalmaintenance In a nonreversible hammer mill with screen bars, shown in above figure, material is broken first by impact between hammers and breaker plates and then by a scrubbing action (shearConstruction, Working and Maintenance of Crushers for Crushing 2020年8月12日 This study shows the performance of a currently running vertical roller coal mill (VRM) in an existing coalfired power plant In a power plant, the coal mill is the critical equipment, whose An investigation of performance characteristics and Fine coal particles and wear metals from grinding surfaces enter the lube oil through worn bearing and shaft seals, as well as being “inhaled” through reservoir vents Historically, the design of coal pulverizers has been based on the expectation of few drive system problems under prescribed operation and maintenanceCoal Pulverizer – Power Plant Pall Corporation
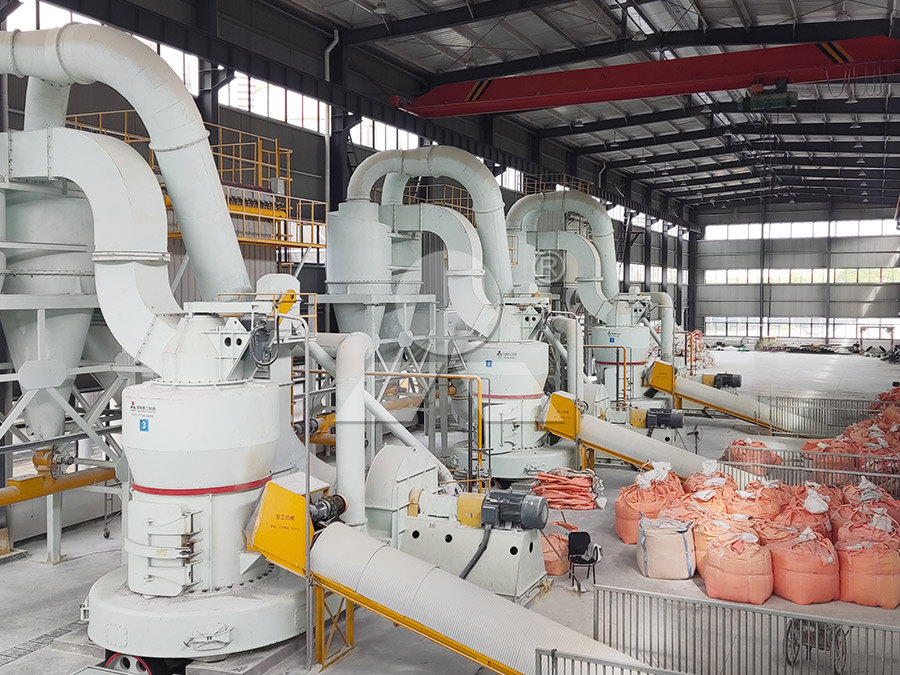
(PDF) Operation and Maintenance of Coal Handling System in
2011年12月31日 Operation and Maintenance of Coal Handling System in Thermal Power Plant December 2011; Procedia Engineering 26(1) from the bearing located at the non driving end of the crusher rotorHammermill Maintenance Mark Heimann Roskamp Champion 2975 Airline Circle Waterloo, Iowa USA 50703 Tel 319 232 8444 Fax 319 236 0481 cpmroskamp Hammermill bearings require good maintenance in order to provide long term Hammermill Maintenance CPM• Coal characteristics profoundly influence risk – Lower rank coals are generally more easily ignited inside the coal mill – High volatile matter and highly reactive coals encourage preignition inside the mill – Higher moisture content requires temperature extremes inside the millMill Inerting and Pulverizer/Mill Explosion Mitigation2020年4月7日 Monitoring and diagnosis of coal mill systems are critical to the security operation of power plants The traditional datadriven fault diagnosis methods often result in low fault recognition rate or even misjudgment due to the imbalance between fault data samples and normal data samples In order to obtain massive fault sample data effectively, based on the Modeling of Coal Mill System Used for Fault Simulation MDPI
.jpg)
Wafangdian Universal Rolling Mill Bearing Manufacture
Wafangdian Universal Rolling Mill Bearing Manufacture Co, Ltd (original name: Wafangdian general Rolling Mill Bearing Factory) is located in Wafangdian which is named as the headstream of China's bearing and has pleasant scenery, beautiful environment, convenient transportation and excellent geographical location Our company was founded in 19942020年4月15日 Nowadays, the evergrowing demand of alternative energy leads also to an important upgrade of traditional energy In a coal power plants, a coal pulverizer assumes a paramount importance in order to increase boiler efficiency by providing pulverized coal with a specific granulometry In a coal pulverizer, rolling bearings are fundamentalRolling bearings for coal pulverizer BEARING NEWS• Mill motor speed • Mill air flow/mill differential pressure • Temperature after the mill • Pressure before the mill • Grinding stock feed • Classifier speed • Mill fan speed • Water spraying • Hot gas • Fresh air Manipulated variables Disturbance variable Process measured value RelauchLMmaster 6 250814 11:47PROCESS OPTIMISATION FOR LOESCHE GRINDING PLANTSFailure of PCI mill roller bearing has been analyzed with the help of whywhy tree analysis (Figs 5, 6, 7, M/s GEBR PFEIFFER Mill Operation and Maintenance Manual, Document number: 240171A5016600000 Rev 00 Date 17042013 Failure Analysis of Pulverized Coal Injection (PCI) Mill Grinding Roller Bearing at Blast Furnace Author Failure Analysis of Pulverized Coal Injection (PCI) Mill Grinding
.jpg)
Boiler Mill and Coal Pulverizer Performance GE Steam
Can GE service my boiler mills? YES Our boiler mills and coal pulverizers span the globe and are built in a variety of sizes and capacitiesWe provide customized maintenance solutions, and offer a full spectrum of highquality solutions for The document outlines the steps for an overhaul procedure of a coal mill It involves 21 steps to remove, inspect, replace, and reinstall components Key steps include removing the mill cover, inspecting and replacing grinding roller Overhaul Procedure For Coal Mill PDF Scribdair system Existing coal piping and coal/gas burners were not changed Figure 5 shows the general arrangement of the fuel system MPS 170 Mill Supply Each of the three MPS 170 mills is equipped with a 400 HP directcoupled drive motor; a removable planetary gear reducer containing a hydrodynamically lubricated, tiltingpad type thrust bearing;WorldProven Coal Pulverizer Technology Debuts in the USSteel Mill Slewing Bearings and provides trended data back to the customer that can be used to more accurately predict the ideal time for a bearing changeout Predictive Maintenance > Aggregates Mining > Rock Crushing > Machine Tool > Crane Bearings > Pulp Paper > Steel Making > Coal Pulverizing > Tunnel Boring > Beverage Bottling Steel Mill Bearings for Rolling Mill Turrets Messinger
.jpg)
coal grinding machine CHAENG
Process introduction Vertical coal mill, also known as vertical roller coal mill or vertical coal grinding mill, is a mechanical equipment for crushing and grinding coal into coal powerMainly used for grinding raw coal, bituminous coal, and other fuels into coal powder, which is supplied to rotary kiln and other kilns in the cement plant and thermal power plantTo ensure smooth and efficient operation, highquality ball mill bearings can withstand heavy loads and reduce friction during the process Common ball mill bearings mainly include ball mill trunnion bearings and sliding shoe bearings Each ball mill bearing has unique features and benefits to suit different ball mill sizes and operating HighQuality Ball Mill Bearing SupplierChoose Reliable Bearings 2023年3月22日 The maintenance of the ball mill is very important to ensure the production and prolong the service life The following are some basic steps and methods for ball mill maintenance: Regularly check the parts of the ball mill, including bearings, gears, belts, tires, etc, to ensure they are in good working conditionBall Mill Maintenance Ball Mill For SaleNomenclatureBowl Mills 583 XRS / 803 XRP Bowl mills 58,80 stands for bowl diameter in inches If the number is even then its shallow bowl mill If the number is odd then its deep bowl mill 3 number of rollers three nos X frequency of power supply 50 cyclesIn USA ’x’ means 60 cycles R Raymond, name of the inventorPulverizer Plant OM Aspects