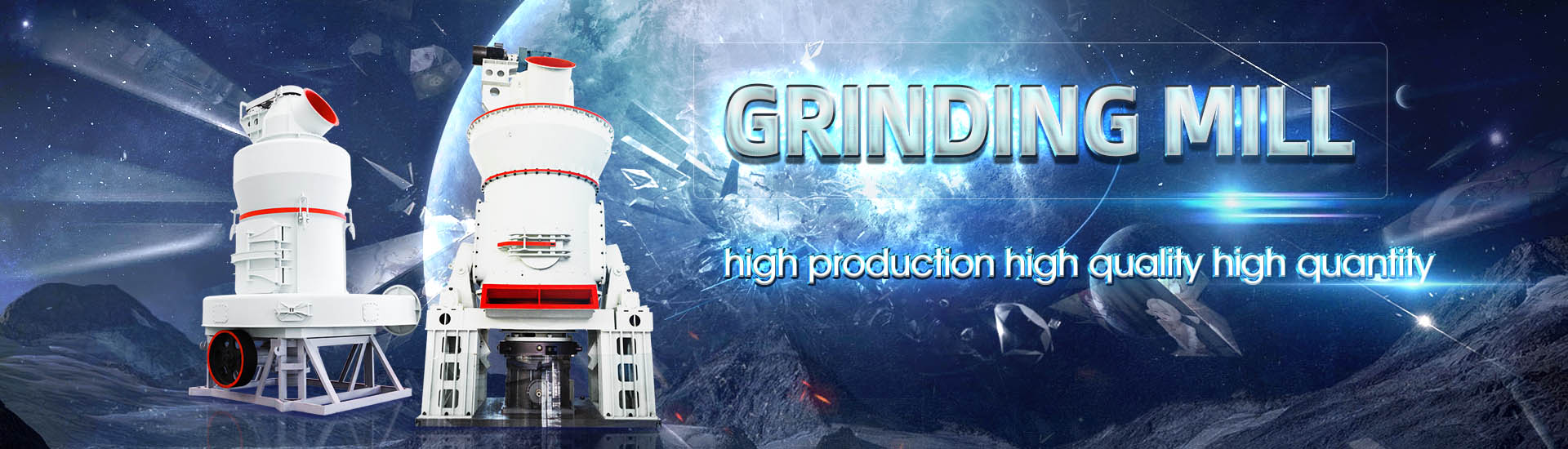
Cement energysaving equipment investment and franchise information
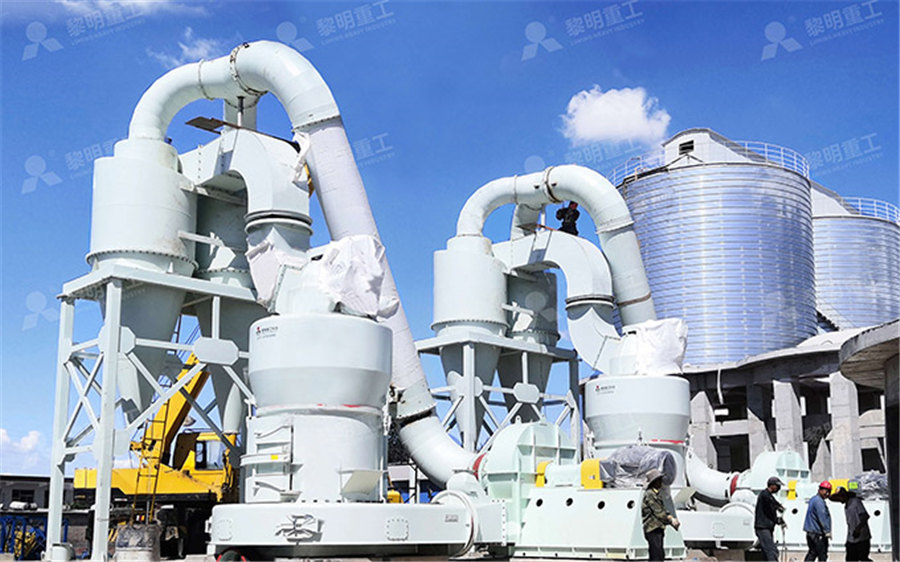
A critical review on energy use and savings in the cement industries
2011年5月1日 In this paper energy use at different sections of cement industries, specific energy consumption, types of energy use, details of cement manufacturing processes, various energy savings measures were reviewed and presented2013年3月1日 In this paper, energy saving measures in the cement industry, such as energyefficiency measures for the preparation of raw materials, production of clinker, and the An overview of energy savings measures for cement industriesWith a cumulative investment portfolio in cement of over $42 billion, IFC has accumulated a vast experience in the industry, including in sustainable energy projects To share its knowledge IMPROVING THERMAL AND ELECTRIC ENERGY EFFICIENCY AT This guide reports on research conducted to support ENERGY STAR and its work with the cement industry Research provides information on potential energy efficiency opportunities for Energy Efficiency Improvement and Cost Saving Opportunities for
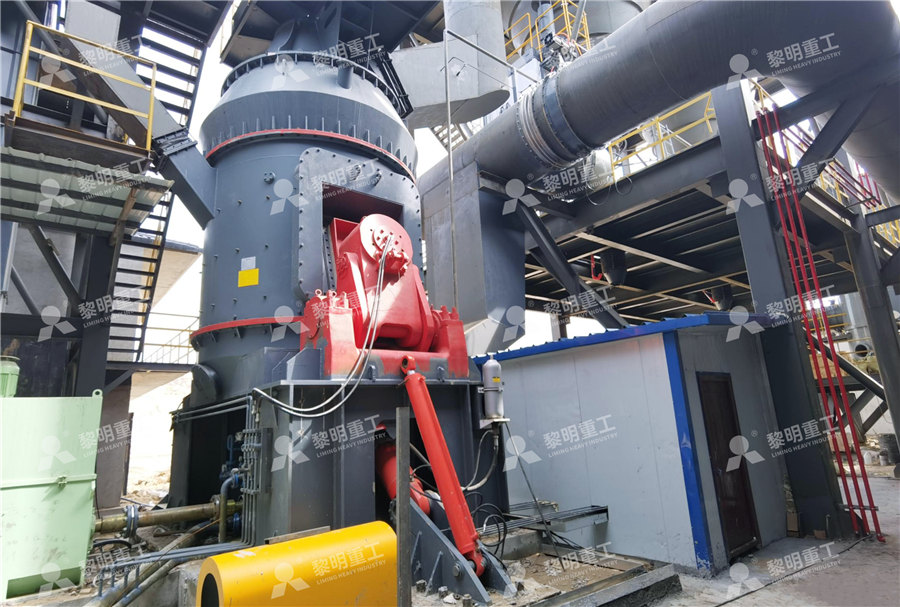
A decision support tool for cement industry to select energy
2020年3月1日 Cement accounts for 83% of total energy use in the production of nonmetallic minerals and 94% of CO2 emissions Both financial and technical aspects need to be taken This report provides a summary of international best practice experience in the cement sector and focuses on specific technical measures that could be implemented by cement plants to reduce Improving thermal and electric energy efficiency at cement plants 2008年1月1日 This report provides information on the energy savings, costs, and carbon dioxide emissions reductions associated with implementation of a number of technologies and measuresEnergy Efficiency Improvement Opportunities for the 2016年11月8日 Despite the historic progress, there is considerable potential for energy efficiency improvement, when compared to other industrialized countries This guide examines Energy Efficiency Improvement and Cost Saving Opportunities for
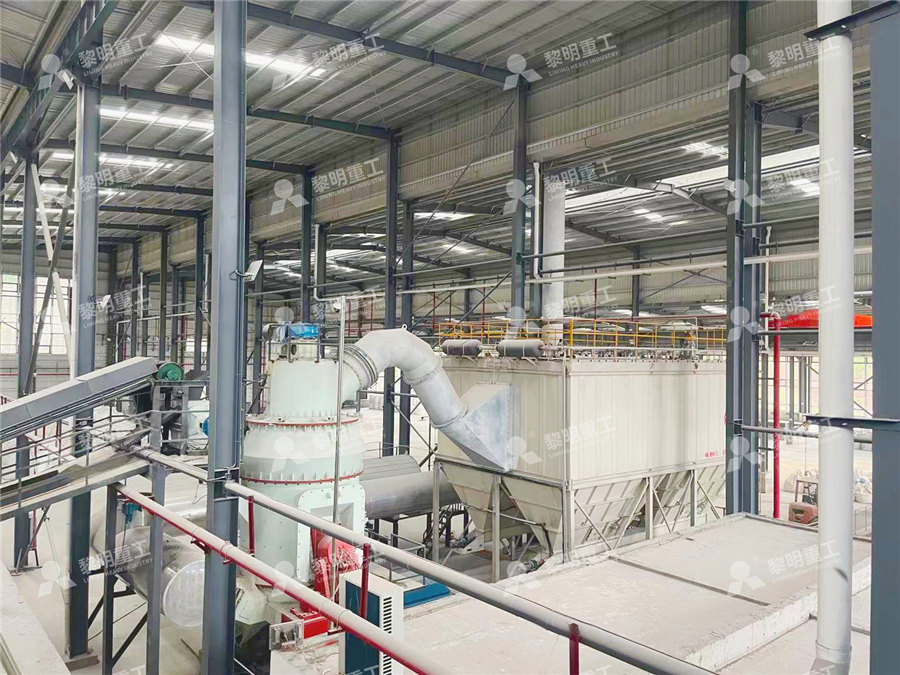
Full article: Energy conservation and waste utilization in the
2014年12月22日 Energy consumption involves 50–60% of the direct production cost of cement (Engin and Ari Citation 2005) Calcination and drying processes plus the kiln requires large 2016年3月1日 Manufacturing of cement is identified as one of the most energy intensive industries in the world Therefore, there is a need for its effective and efficient utilization and hence conservation(PDF) ENERGY UTILIZATION, CONSERVATION AND each technology or measure, costs and energy savings per tonne of cement produced are estimated and then carbon dioxide emissions reductions are calculated based on the fuels used at the process step to which the technology or measure is applied The analysis of cement kiln energyefficiency opportunities is divided into technologies and measuresEnergy Efficiency Improvement Opportunities for the Cement 2021年3月30日 ing cement production equipment, excluding managerial energy ‐ saving measures and measures related, for example, to the us e of waste fuels Moreover, the discussion excludesTechnological Energy Efficiency Improvements in Cement Industries
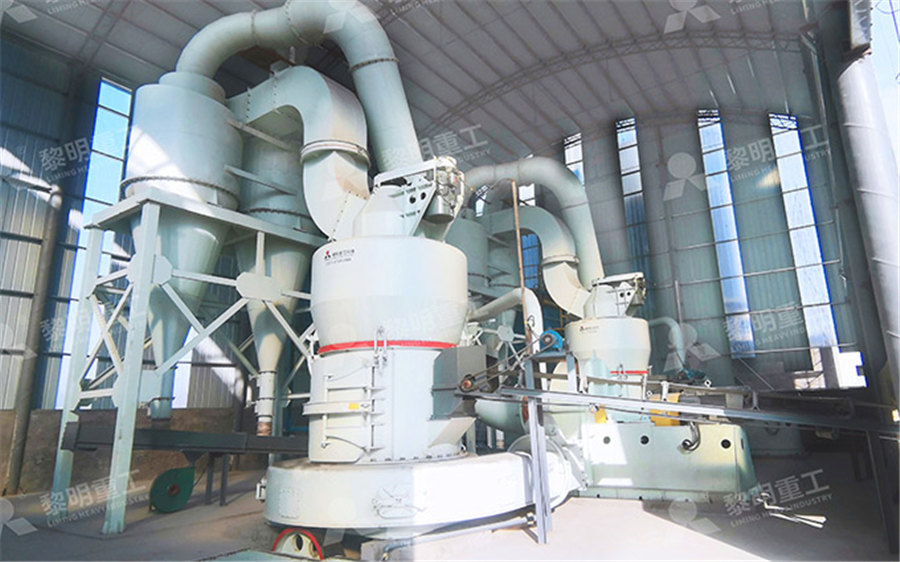
Investigating energy saving and climate mitigation potentials in cement
2023年7月1日 The cement industry is one of the most energy and emissionintensive sectors, accounting for approximately 7% of totalindustrial energy use and 7% of global CO 2 emissions This study investigates the potential energy savings and CO 2 abatement in the cement plants of Ethiopia A Benchmarking and Energy Saving Tool for Cement is used to compare the energy 2021年12月31日 The cement industry is an industrial subsector with high energy intensity It represents nearly 15% of the total energy used by industries Many energysaving programs and strategies have been Investigation of Energy Saving Potential In A South African Cement PDF On Aug 1, 2013, Ernst Worrell and others published Energy Efficiency Improvement and Cost Saving Opportunities for Cement Making An ENERGY STAR® Guide for Energy and Plant Managers Find Energy Efficiency Improvement and Cost Saving Opportunities for Cement 2016年10月5日 In this chapter an introduction of widely applied energyefficient grinding technologies in cement grinding and description of the operating principles of the related equipments and comparisons over each other in terms of grinding efficiency, specific energy consumption, production capacity and cement quality are given A case study performed on a EnergyEfficient Technologies in Cement Grinding IntechOpen
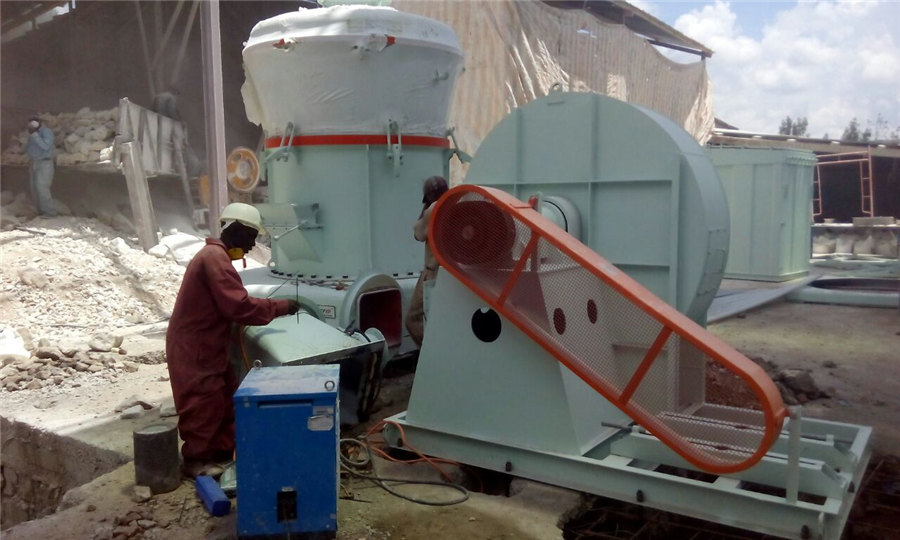
An overview of energy savings measures for cement industries
Bhatty, J, Miller, F and Kosmatka, S 2004 Innovations in Portland cement manufacturing [81] Buzzi, S, Sassone, G, 1993 Optimization of clinker cooler operation [82] Birch E Energy savings in cement kiln systems energy efficiency in the cement industry Elsevier Applied Science; 1990 118–128 [83] Cowi, C 1993Schuer et al [1] gave energy consumption values and described the energy saving methods and potentials for German Cement Industry The study consisted of two parts, namely electrical energy saving methods and thermal energy saving methods The results were presented in the form of energy flow diagrams that made the results easy to understand(PDF) Assessment of energysaving opportunities of cement Technology Compendium on Energy Saving Opportunities Cement Sector An initiative supported by CONTENTS Annexure 3 : List of Equipment/Technology Suppliers 67 Abbreviations 69 ¾ Investment required ¾ Payback period ¾ Technology providersTechnology Compendium on Energy Saving Opportunities Cement 2017年4月22日 China, as the world’s largest cement producer, accounts for more than 60% of global cement production With the continuous development of the Chinese economy, resource and environmental constraints are becoming Energy Conservation in China’s Cement Industry
.jpg)
TIPS TO SAVE ENERGY IN CEMENT
(Worrell and Galitsky, 2004), evaluated the energysaving potential of about 30 energyefficiency technologies and practices that could be applied to both wet and dry process cement production For this analysis, we compare current 2013年10月17日 The old adage, “You can’t control what you can’t measure,” can truly be applied to energy management In the Rohrdorf cement works, energy consumption is measured by the Simatic S7 automation system, and stored in an SQL database This can then be evaluated, and displayed in Excel in either graphic or tabular formSaving Energy in a Cement Plant2024年9月2日 This includes the modernization of cement kilns, the introduction of vertical cement mills, as well as the design and installation of renewable energy equipmentEnhancing Energy Efficiency in the Cement Industry ResearchGate2020年3月1日 PDF Cement industry is one of the most energy intensive industrial subsectors It accounts for almost 15% of the total energy consumed by Find, read and cite all the research you need on (PDF) A decision support tool for cement industry to select energy
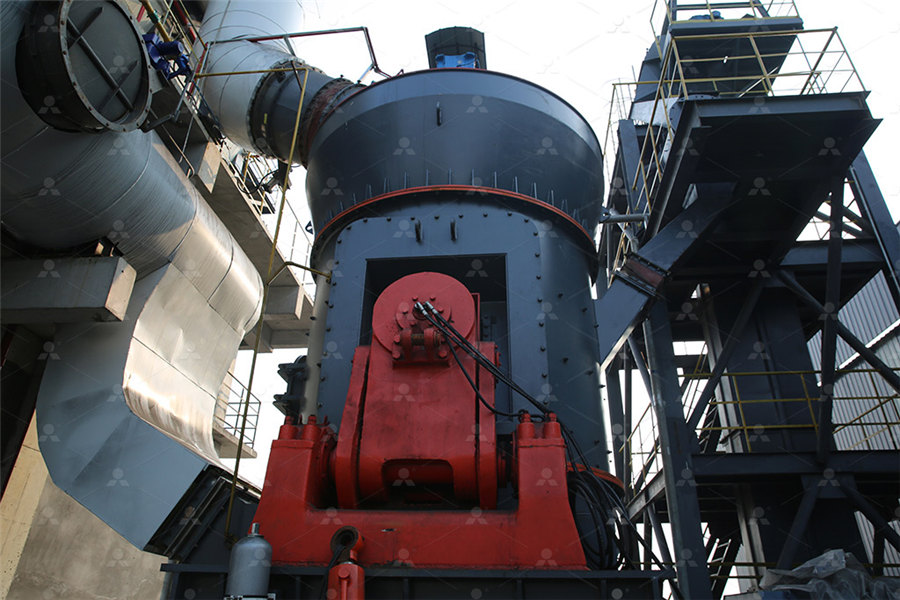
Concrete energy savings – onsite power for the world’s cement
2007年5月1日 null THE ENVIRONMENTAL IMPERATIVE Given the energyintensive nature of the cementmanufacturing process, it is perhaps not surprising that a twentieth of the world’s manmade CO 2 emissions can be traced to a single industry: cement About half of these emissions are a necessary byproduct of the chemical reaction essential in transforming the raw material Revolutionary lowNOx highefficiency gas burner International Energy Agency 1997 [95] Videgar R, Rapson D, Dhanjal S Gyrotherm technology boosts cement kiln output, efficiency and cuts NOx emissions In: Cement Industry Technical Conference 1997 [96] Birch E Energy savings in cement kiln systems energy efficiency in the cement industry(PDF) A critical review on energy use and savings in the cement a cement industry to design the Heat Exchanger Network with the help of Aspen Energy Analyser in order to explore the energy and cost saving opportunities available to the plant 2 Methodology The adopted methodology for this study is based on the study done by Boldyryev et al, 2016 and Verma and Kumar, 2017Energy Savings in Cement Industry: Use of Heat Integration2023年5月3日 Türkiye is the largest cement producer of Europe and the second biggest cement exporter in the world The industry is responsible for more than 8% of global carbon dioxide (CO2) emissions and around 15% of the primary energy consumed worldwide In this paper, the specific energy consumption (SEC) and related emissions of a real scale cement factory currently A comprehensive investigation of a grinding unit to reduce energy
.jpg)
Making Your Cement Grinding Plant Energy Saving Cement
If you want to upgrade your current cement grinding plant to achieve the purpose of energysaving and profit increase, the most direct way is to carry out a technical transformation on traditional cement mills or replace a batch of new energysaving grinding equipment, such as the cement vertical mill grinding system, new type cement ball mill grinding system, cement roller press, Abstract: Cement Industry is one of the major energy consuming industries and optimum use of energy is at present important for our national economy The energy cost is the highest component of cost structure of cement manufacture Energy cost in Indian cement Industry account for over 40 50 % of the manufacturing cost of cement Out of this Optimizing Energy Utilization in the Cement Industry: An Energy Using data taken from Table 4 and Eqs (2)e(5), energy savings and bill savings for all HT motors were estimated and presented in Table 8 The estimated energy savings by HT motors found to be 4,600,386 MWh/year for 60% speed reductions This amount will save about 429,768,060 US$/year as electricity bill for 60% speed reductionAnalysis of electrical motors load factors and energy savings in an This guide reports on research conducted to support ENERGY STAR and its work with the cement industry Research provides information on potential energy efficiency opportunities for cement plants Besides technical information, ENERGY STAR has tools to facilitate stronger corporate energy management practices in US industry, including plant Energy Efficiency Improvement and Cost Saving Opportunities for Cement
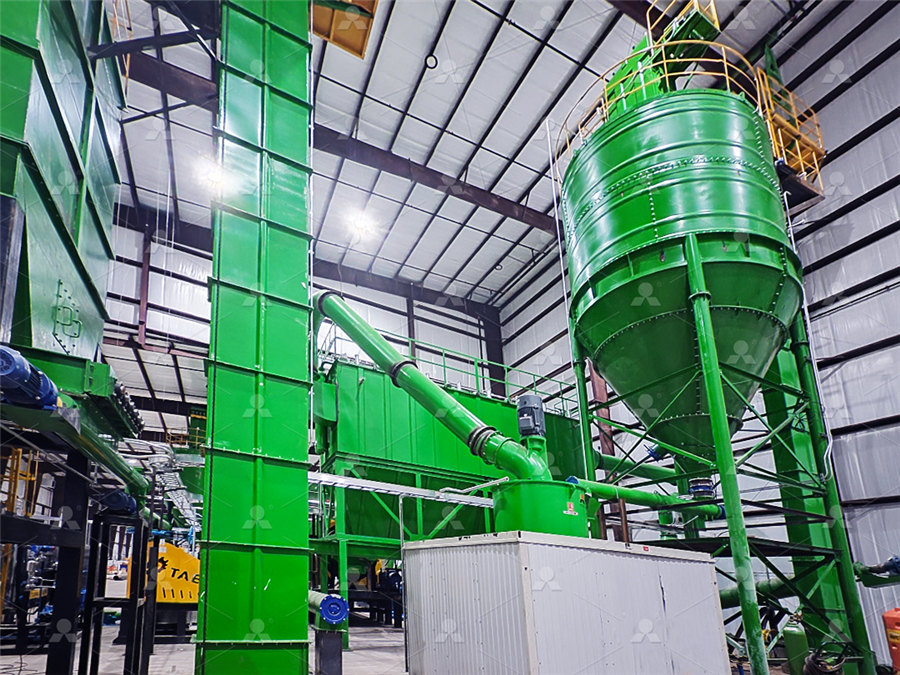
A decision support tool for cement industry to select energy
2020年3月1日 Manufacturing cement requires energy intensive processes; and consumes almost 15% of the total demand for energy in industry [3]On average, to produce one ton of cement, 34 GJ of thermal energy (in dry process) and 110 kWh of electrical energy are needed [4, 5]Furthermore, manufacturing a ton of cement releases 073–099 tons of CO2 [6] which 2023年9月28日 China Energy International Group Samarkand Cement launched another major investment project on cement production in Kattakurgan district of Samarkand region The production capacity of the plant is 75 thousand tonnes of cement clinker per day The plant is equipped with modern, energysaving equipmentOfficial opening of the cement plant in Samarkand (Uzbekistan)422 Shared Savings Energy Performance Contract Improving Thermal and Electric Energy Efficiency at Cement Plants: International Best Practice iii LIST OF FIGURES With a cumulative investment portfolio in cement of over $42 billion, IFC has accumulated a vast experience in theIMPROVING THERMAL AND ELECTRIC ENERGY EFFICIENCY AT CEMENT 2008年1月1日 Tables 2 through 8 provide the following information for each technology: fuel and electricity savings per tonne of cement; annual operating and capital costs per tonne of cement or estimated Energy Efficiency Improvement Opportunities for the Cement
.jpg)
A critical review on energy use and savings in the cement industries
2011年5月1日 Cement manufacturing is an energy intensive process consuming about 12–15% of total energy consumption Therefore opportunities exist to identify areas where energy savings measures can be applied so that energy can be saved along with the reduction of emission pollution Table 15 presents list of energy savings measures for cement industries2016年11月8日 In the cement industry, from 1970 to 1999, carbon dioxide intensity due to fuel consumption and raw material calcination dropped 16 percent Despite the historic progress, there is considerable potential for energy efficiency improvement, when compared to other industrialized countries This guide examines more than 40 energy efficient technologies and Energy Efficiency Improvement and Cost Saving Opportunities for Cement 2008年1月1日 We examined over 40 energy efficient technologies and measures and estimated energy savings, carbon dioxide savings, investment costs, and operation and maintenance costs for each of the measures The report describes the measures and experiences of cement plants around the wold with these practices and technologiesEnergy Efficiency Improvement and Cost Saving Opportunities for Cement The cement industry has a very high energy consumption, which depends on the process and equipment used The main types of energy for cement production are heat and electricity In the context of rising prices for natural resources, Cement plant modernization ESFC Investment Group
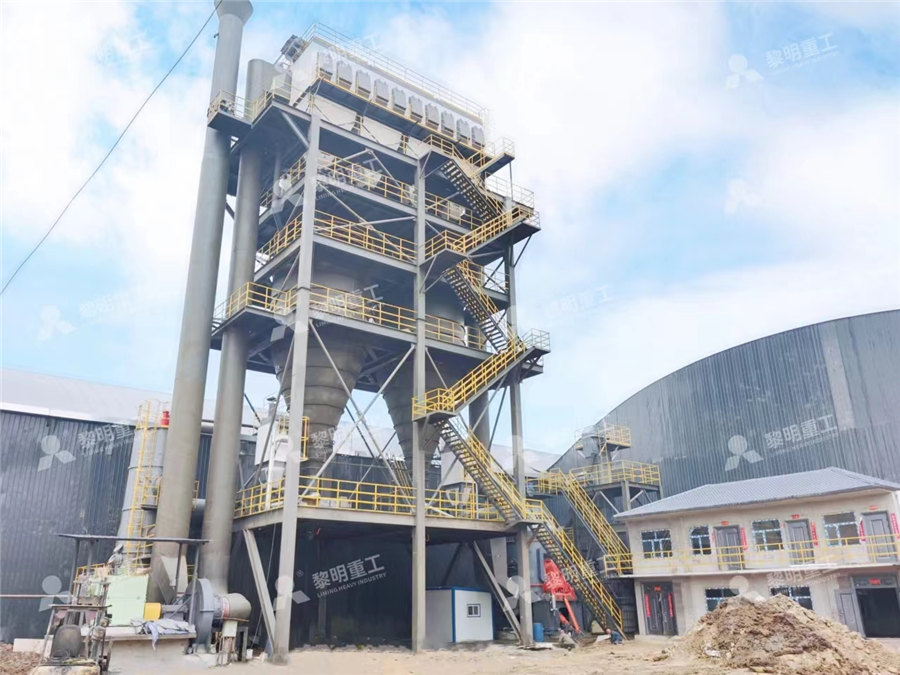
Energysaving investment credit (EIA): Tax Reduction for
Energysaving investment credit (EIA): Tax Reduction for Investments in Energy Saving Equipment and Sustainable Energy policy from the IEA Policies Database2021年11月30日 In this select cement industry, energy performance is checked, there is a continuous improvement is identified by reporting green rating project, and life cycle energy assessment, energy performance (5%) over an improvement period, the total energy cost saving over an improvement in year 20 lakh USD, and the cost implement for energy management is A Case Study on Evaluation of Energy Management System by2015年3月1日 LC3 cement not only produces cement at a lower cost by reducing energy usage but decreases the capital investment required to increase production capacity The use of clinker the energyintensive and relatively expensive component of cement is lower than conventional cement, reducing material costsEnergySaving Cement Construction World2010年10月1日 Download Citation Applications of Efficient EnergySaving Cement Grinding Technology and Equipment Joint grinding system is the preferred cement grinding system of current cement process Applications of Efficient EnergySaving Cement Grinding
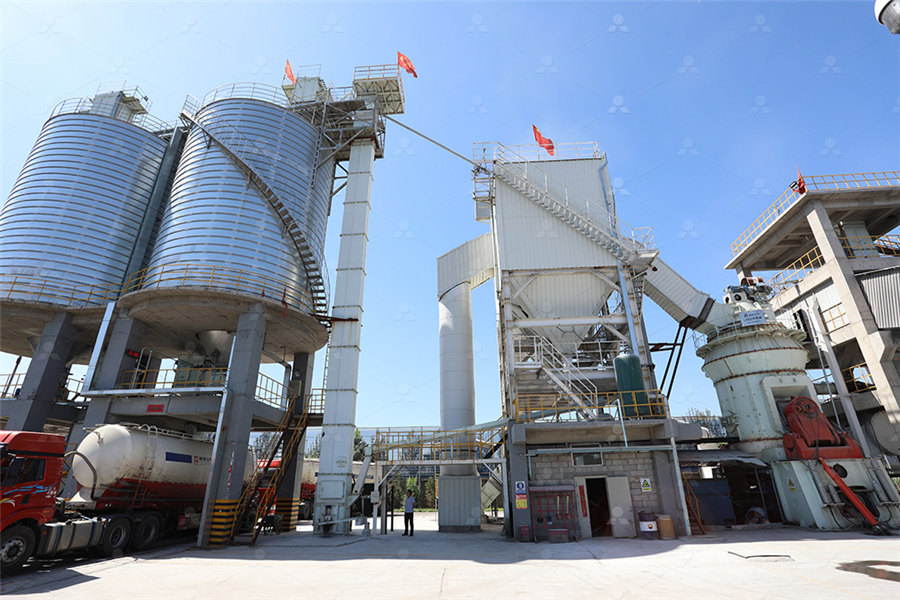
Energy Efficiency Improvement Opportunities for the Cement
electricity savings per tonne of cement; annual operating and capital costs per tonne of cement or estimated payback period; and, carbon dioxide emissions reductions for each measure applied to the production of cement This information was originally collected for a technology investment Results and discussion Energy demand and energy saving potentials: In the next two decades, the gradual transformation of Uganda's economy and the associated urbanisation will result in a growing demand for cement and a steady increase in energy consumption and associated GHG emissions Based on ourPolicy Brief: Prospects for Energy Efficiency in Uganda Cement It has been proven that a thermal energy saving potential of 025–0345 GJ/t, an electrical energy saving potential of 20–35 *Corresponding author: Energy Department, Institute of Science, High Technology Environmental sciences, Graduate University Energy Auditing in Cement Industry: A Case study AcademiaIn this way, cement manufacturers can not only reduce electricity consumption but also realize energy saving and emission reduction At present, this method is mostly applied in large dry process cement plants Conclusion Through the above 5 tips, Portland cement manufacturers can achieve cost savings from each stage of the cement production 5 Costsaving Tips for Portland Cement Manufacturers
.jpg)
Benchmarking and EnergySaving Tool (BEST) for China’s Cement
Benchmarking and EnergySaving Tool for Cement (BESTCement) for China Benchmarking Benchmarking is a commonlyused term that generally means comparing a defined characteristic of one facility to