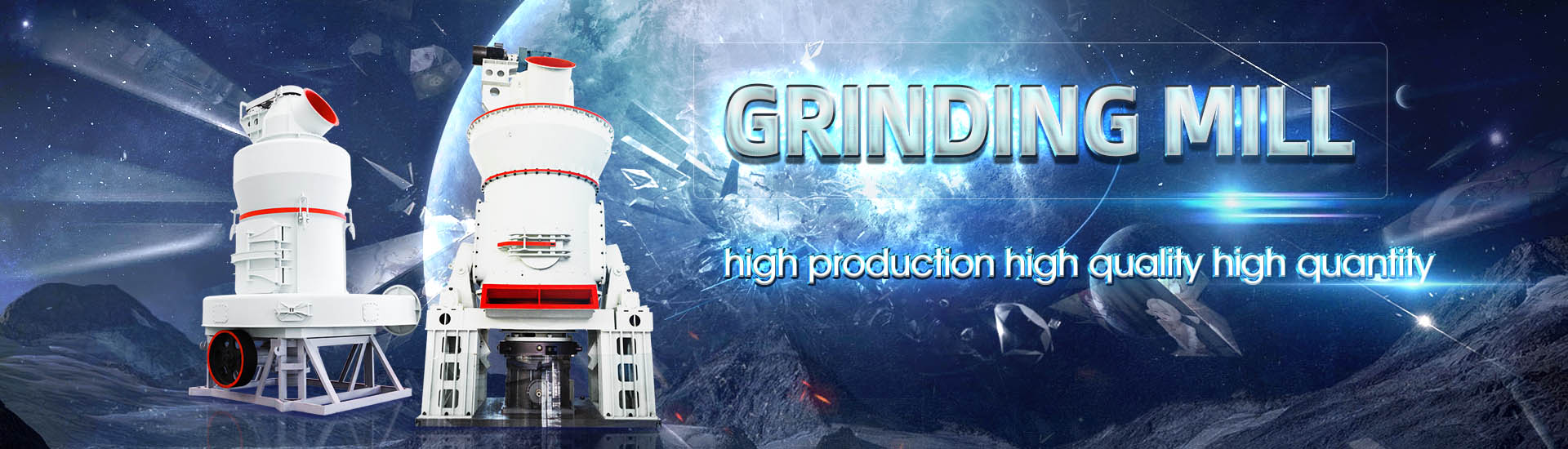
Ore mill is mainly used for where
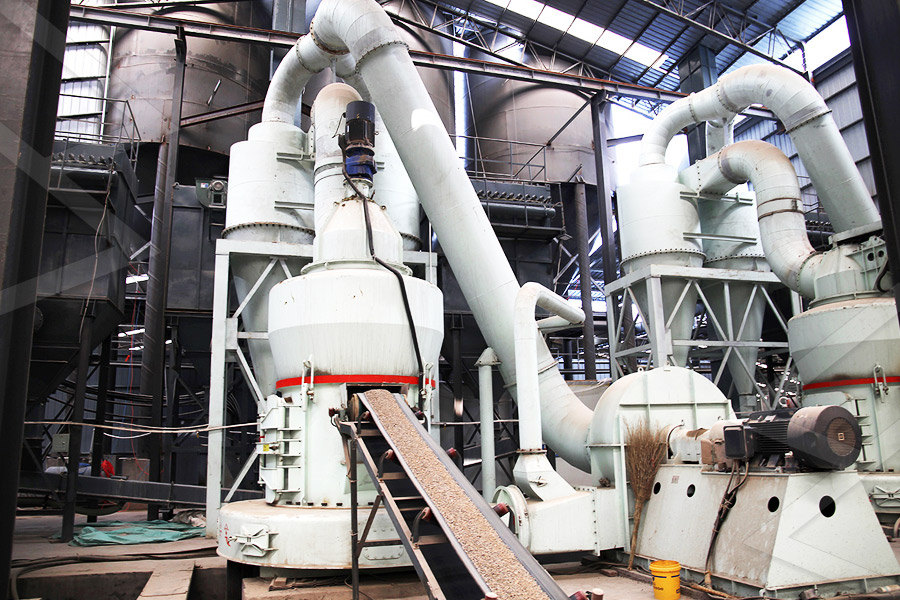
Iron Ore Processing: From Extraction to
2024年4月26日 AG/SAG mills are typically used for coarse grinding, where large pieces of ore are efficiently broken down The grinding process reduces the ore size, which enhances the efficiency of subsequent beneficiation processes by 2023年7月20日 Moist grinding, a special grinding method, is used to prepare pellets for smelting According to the grinding medium features, ore grinding is mainly classified into ball grinding Ore Grinding SpringerLink2023年5月3日 The rod mill is mainly used for gravity or magnetic separation of tungstentin ore and other rare metal ores In some cases, the rod mill can replace the shorthead cone Rod Mill SpringerLink2023年11月8日 When a block is blasted and excavated, its ore type is used to route it to waste, to the crusher, to leaching, or to the appropriate stockpile If the operation requires blending, Ore Types: What They Are, How They’re Made, and Their
.jpg)
Iron Ore Supply Chain: From Mining to Steel
2023年10月25日 The iron ore supply chain begins with the mining of iron ore, which is then transported to processing plants for beneficiation and further refinement The refined iron ore is then transported to steel mills for use in the The most widely distributed ironbearing minerals are oxides, and iron ores consist mainly of hematite (Fe2O3), which is red; magnetite (Fe3O4), which is black; limonite or bogiron ore (2Fe2O33H2O), which is brown; and siderite Iron processing Ores, Smelting, Refining2022年1月1日 Hematite and magnetite iron ores are the most prominent raw materials for iron and steel production Most of the highgrade hematite iron ores are typically subjected to Comminution and classification technologies of iron ore2022年9月1日 This method is called ore blending and it is used in many mines (McKee, 2013, Liu et al, 2021) The purpose of ore blending is simply to provide uniform mill feed which aids Towards waterless operations from mine to mill ScienceDirect
.jpg)
A Review of the Grinding Media in Ball Mills for Mineral
2023年10月27日 The ball mill is a rotating cylindrical vessel with grinding media inside, which is responsible for breaking the ore particles Grinding media play an important role in the 2019年12月15日 Electrostatic separation (ESS) is mainly used for mineral sands application, though earlier patents suggest applications in iron ore and phosphate separations The relative Beneficiation of Gold and Silver Ores SpringerLinkThe wet pan mill is mainly used for the beneficiation of gold, silver, lead, zinc, iron, molybdenum, copper, antimony, and other ore It is also called a gold round mill Because of the small investment, quick results, and high benefits of using Gold Round Mill/Wet Pan Mill / Wet Pan Mill2017年8月29日 addresses all issues related to gold ore processing by the detailed study of an ore or a mill product The methodology is widely used as a predictive tool in feasibility studies and during the process development stage, and as a troubleshooting tool for mineral processing and hydrometallurgical operations INTRODUCTION Based on the gold Gold process mineralogy: Objectives, techniques, and
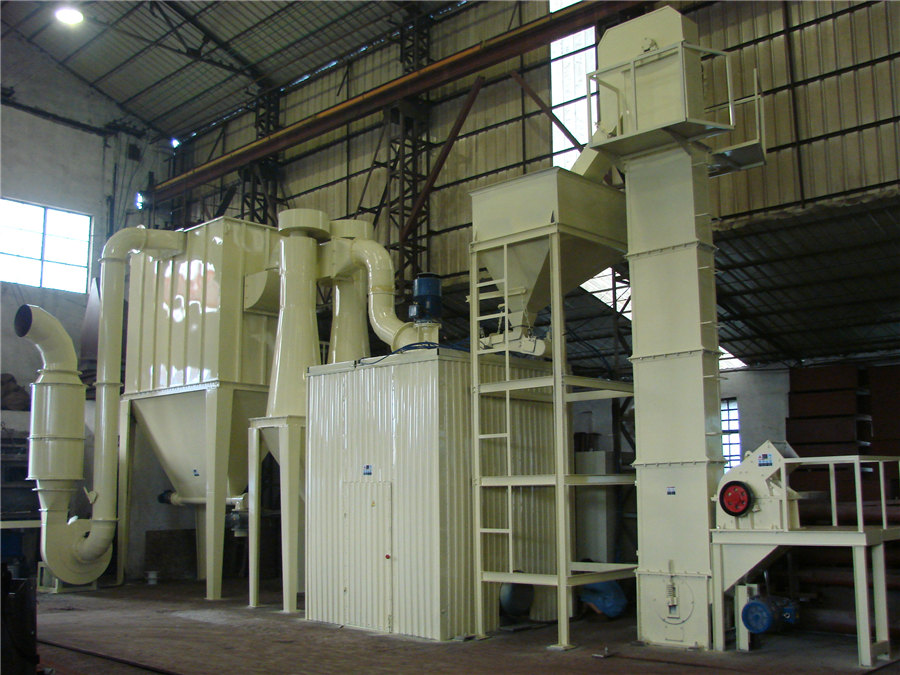
What Is a Ball Mill and How Does It Work?
2024年7月12日 A ball mill and a tumbling mill are both types of grinding mills used to reduce material size We mainly use a ball mill for mixing and grinding processes In contrast, we generally use a tumbling mill for finer material 2023年9月1日 Iron ore is mainly divided into three types: magnetite, hematite, and limonite, all of which are iron oxides, differing in their oxidation methods The higher the iron content in the iron ore, the better Theoretically, the highest iron content in iron ore is around 72%, and iron ore with an iron content above 60% is called rich iron oreIron Ore: The Steel Raw Materials Journey MachineMFG2022年1月1日 The runofmine ore is mainly composed of specularite and quartz The ore is first ground down to about 85% −75 micron particle size using ball mills SLon magnetic separators are then used for roughing and cleaning to extract the specularite particles The magnetic component of the SLon cleaning unit is collected as the final iron ore Physical separation of iron ore: magnetic separation2022年5月19日 The gold flotation process mainly includes four stages: dosing, agitation, aeration, and foam scraping Gold flotation process is suitable for processing gold bearing sulfide ore with fine particle size and good floatability During flotation, sulfide ore is enriched into sulfide concentrate as a carrier for goldHow to Process Gold Ore? 4 Gold Processing Steps Mining
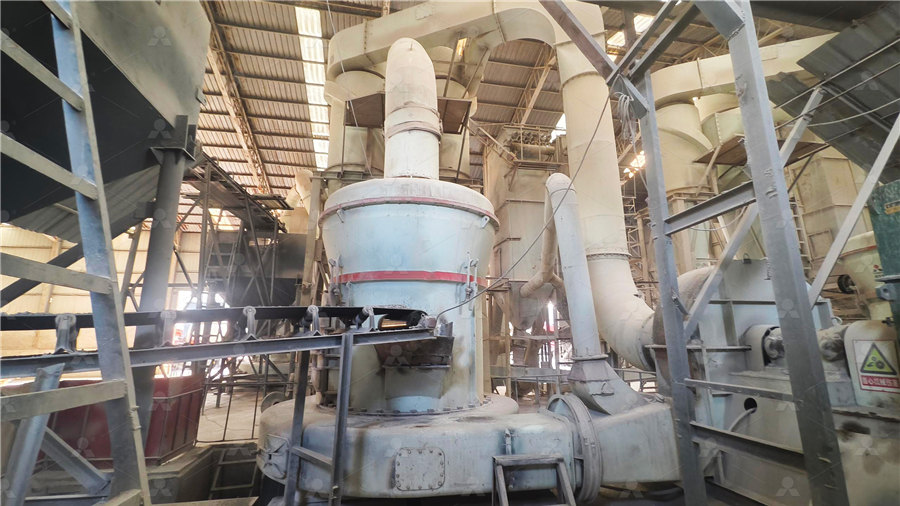
A Review of the Grinding Media in Ball Mills for Mineral
2023年10月27日 The ball mill is a rotating cylindrical vessel with grinding media inside, which is responsible for breaking the ore particles Grinding media play an important role in the comminution of mineral ores in these mills This work reviews the application of balls in mineral processing as a function of the materials used to manufacture them and the mass loss, as 2023年4月23日 One of the most used tumbling mills is the ball mill This paper reviews different types of grinding media that have been developed and improved over the years and their properties(PDF) Grinding Media in Ball MillsA Review ResearchGateEnd peripheral discharge type: It is generally used for dry ore mill His products are coarsegrained Rod mills can also be used for wet grinding A high gradient and better flow rate can be obtained by using the peripheral rod mill His product size is about 25 mm Central peripheral discharge type: It can be used for wet and dry grindingRod Mill Ore MillForui Machinery Henan Forui Machinery 2010年1月1日 Here we use measured data from a well characterised ore in a well instrumented, 12 m diameter pilot scale mill to validate direct DEM prediction of particle size reductionExperimental study of ore characterisation methods for AG/SAG mills
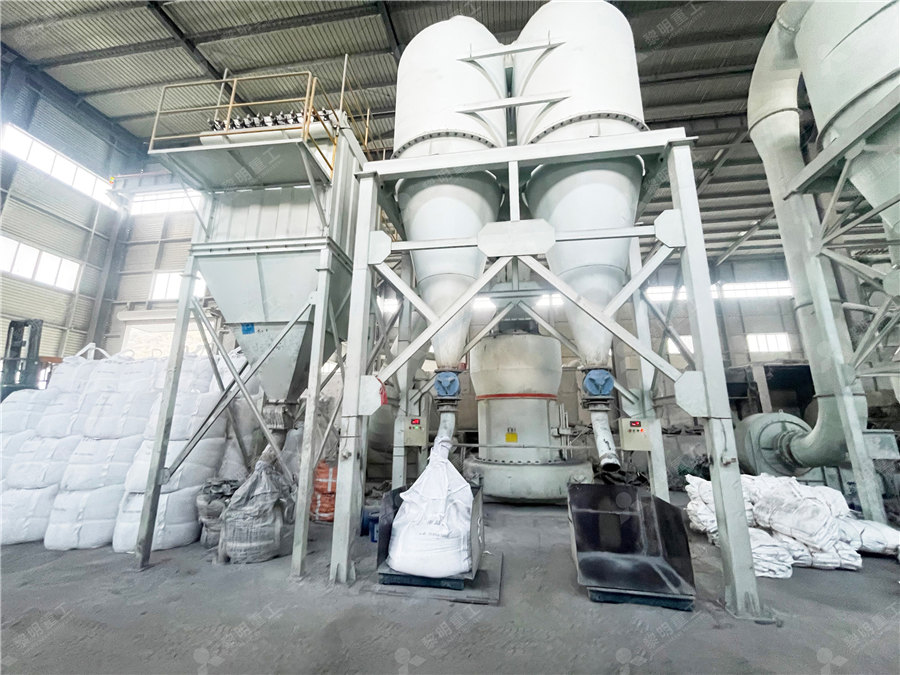
Experimental Study of Ore Characterisation Methods for AG/SAG Mills
Experimental Study of Ore Characterisation Methods for AG/SAG Mills Mining companies have long recognised the importance of ore breakage characterisation in design and optimisation of their crushing and grinding circuits In one of the industry standard methods relevant to AG/SAG milling, ore is characterised using mainly high energy single impact testsx000D However 2022年1月1日 The unique feature of this type of devices is that the coarse ore particles themselves are used as the grinding media, not unlike a pebble mill in which the pebbles are generated naturally from the ore body AG and SAG mills are coarse grinding devices; they consist of a tumbling drum with 25–40% of its volume filled with minution and classification technologies of iron ore2019年6月11日 World resources are estimated to be greater than 800 billion tons of crude ore containing more than 230 billion tons of iron The only source of primary iron is iron ore, but before all that iron ore can be turned into steel, it Sintering: A Step Between Mining Iron Ore and 2015年4月15日 The samples can be taken from adits, pits, trenches, etc, in the ore body or they can be crushed drill cores While it is helpful in anticipating variations in feed rates to know the grindability of the various ore types in a deposit, for mill selection grindability tests should be run on composite samples representative of the blended mill feedWhat Ore Testing is Required For Mill Selection
CFB石灰石脱硫剂制备64.jpg)
Grinding Media in Ball MillsA Review ResearchGate
2024年1月13日 Table 1 Chemical composition of typical grinding media (% wt) Adapted from [24] 211 Cast Iron Cast iron can be grey cast iron or white cast iron, but white cast irons are commonly used in 2017年12月20日 Until the 1950s of the last century, the oxidized iron ores that were loaded into the blast furnace had granulometries within 10 and 120 mm However, the depletion of highgrade iron ore sources has made necessary the utilization of concentration processes with the purpose of enriching the iron ore Because of these processes, a fine granulometry is produced, and Iron Ore Agglomeration Technologies IntechOpen2023年1月1日 The quality of Indian iron ore resources is generally good with high iron content and high percentage of lumpy ore More than 85% of the hematite ore reserves are of medium to highgrade (+62% Fe) and are directly used in blast furnace and in directreduced iron (DRI) plants in the form of sized lump ore, agglomerated sinter, and agglomerated pellets (Iron and Iron ore beneficiation: an overview ScienceDirect2023年5月27日 In which industry is limestone mainly used? The answer is the cement industry and then the homogenized raw materials are sent to a ball mill for fine grinding according to a certain feeding amount to obtain raw meals Step 4: Clinker calcination Fe 2 O 3: from clay, iron ore, scrap iron and fly ash; Gypsum, CaSO 42H 2 0: found 2 Major Roles of Limestone in Cement Manufacturing
.jpg)
Iron Geoscience Australia
2018年5月17日 Properties In the Earth's crust iron is found mainly as minerals of iron oxide such as hematite, magnetite, goethite and limonite The minerals that are mostly used as ore for making iron are hematite (Fe 2 O 3) and magnetite (Fe 3 O 4)Iron is quite soft and easily worked, but it has a very high melting point of 1538°CLead processing, preparation of the ore for use in various products Lead (Pb) is one of the oldest metals known, being one of seven metals used in the ancient world (the others are gold, silver, copper, iron, tin, and mercury) Its low melting point of 327 °C (621 °F), coupled with its easyLead processing Smelting, Refining Uses Britannica2022年9月1日 Waste rocks occupy space from ore in the grinding mill, thus lowering the mill’s ore grinding capacity and mineral concentrator’s concentrate production Moreover, in most cases, waste rock is harder and, consequently, more difficult to grind than the ore which is often found in the weaker areas of the rockTowards waterless operations from mine to mill ScienceDirect2017年8月26日 comminution stage uses a rod mill Here and at one other conventional plant, dense media separation is used to separate the barren norite stringers from the heavier chromite reef before milling and flotation In one of the older converted plants, mills as small as 245 m ¥ 245 m (350 HP) are still in regular use, but theThe Extractive Metallurgy of South Africa’s Platinum Ores
.jpg)
Winning the Metal: Ore Mills of the West
2024年11月19日 It is almost impossible to describe, let alone do justice to, the variety of processes that have been used to mill ore The importance of mills cannot be understated since no money was made until the minerals were 2023年12月21日 A “best” ore type is designated that (in theory) best describes how the rock will behave in processing Codes representing this ore type are entered into the drill hole database, then interpreted on cross sections and level plans, and nally added to the block model Ore types are iteratively reexamined and adjusted over the life of a projectOre Types: What They Are, How They Are Made, and 2023年5月12日 Reverse flotation is a commonly used method for separating magnesite and coexisting quartz The processing flow is as follows 1 Crushing: Crush the raw ore to 100mm with a jaw crusher and a roll crusher 2 Washing: Set a trommel screen to remove the muddy impurities in the ore 3 Grinding: Use a ball mill to grind the raw ore to 95%0074mmMagnesite Ore Processing: Separation and Calcination2023年10月10日 The rod mill is another type of grinding mill used in the copper ore mining process This machine uses steel rods as the grinding media instead of balls, which are commonly used in ball mills The rods grind the ore by tumbling within the mill, similar to the action of a rotating drumUnderstanding the SAG Mill in Copper Ore Mining Process
.jpg)
Monitoring ore loss and dilution for minetomill integration
However, ore below the pay limit adds variation to the mill grade as increased mill throughput will be required to make up for the loss of gold, and that impacts on the recovery in the plant It is against these perspectives and findings of this study that the MCF should be seen as a method that identify the real problems underground and when 2019年1月1日 Metallurgical coke is produced in coke ovens and is mainly used for the iron ore reduction in blast furnaces (BFs) It is also consumed in blast and electric furnaces for ferroalloy production and for the reduction of other metal oxides, chlorides, phosphates, sulfates, as well as for the reduction of carbonates to carbidesCoke in the iron and steel industry ScienceDirect2016年6月20日 AZ Guide to Screening Ore, Rock Aggregate A simple definition of a “screen” is a machine with surface(s) used to classify materials by size Screening is defined as “The mechanical process which accomplishes a division of particles on the basis of size and their acceptance or rejection by a screening surface”Ore, Rock Aggregate Screening (Complete Guide)The wet pan mill is mainly used for the beneficiation of gold, silver, lead, zinc, iron, molybdenum, copper, antimony, and other ore It is also called a gold round mill Because of the small investment, quick results, and high benefits of using Gold Round Mill/Wet Pan Mill / Wet Pan Mill
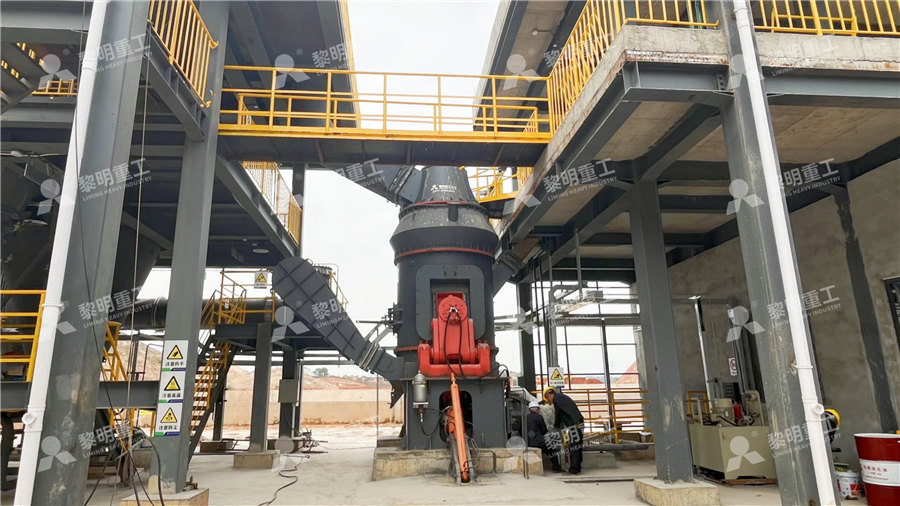
Gold process mineralogy: Objectives, techniques, and
2017年8月29日 addresses all issues related to gold ore processing by the detailed study of an ore or a mill product The methodology is widely used as a predictive tool in feasibility studies and during the process development stage, and as a troubleshooting tool for mineral processing and hydrometallurgical operations INTRODUCTION Based on the gold 2024年7月12日 A ball mill and a tumbling mill are both types of grinding mills used to reduce material size We mainly use a ball mill for mixing and grinding processes In contrast, we generally use a tumbling mill for finer material What Is a Ball Mill and How Does It Work?2023年9月1日 Iron ore is mainly divided into three types: magnetite, hematite, and limonite, all of which are iron oxides, differing in their oxidation methods The higher the iron content in the iron ore, the better Theoretically, the highest iron content in iron ore is around 72%, and iron ore with an iron content above 60% is called rich iron oreIron Ore: The Steel Raw Materials Journey MachineMFG2022年1月1日 The runofmine ore is mainly composed of specularite and quartz The ore is first ground down to about 85% −75 micron particle size using ball mills SLon magnetic separators are then used for roughing and cleaning to extract the specularite particles The magnetic component of the SLon cleaning unit is collected as the final iron ore Physical separation of iron ore: magnetic separation
.jpg)
How to Process Gold Ore? 4 Gold Processing Steps Mining
2022年5月19日 The gold flotation process mainly includes four stages: dosing, agitation, aeration, and foam scraping Gold flotation process is suitable for processing gold bearing sulfide ore with fine particle size and good floatability During flotation, sulfide ore is enriched into sulfide concentrate as a carrier for gold2023年10月27日 The ball mill is a rotating cylindrical vessel with grinding media inside, which is responsible for breaking the ore particles Grinding media play an important role in the comminution of mineral ores in these mills This work reviews the application of balls in mineral processing as a function of the materials used to manufacture them and the mass loss, as A Review of the Grinding Media in Ball Mills for Mineral 2023年4月23日 One of the most used tumbling mills is the ball mill This paper reviews different types of grinding media that have been developed and improved over the years and their properties(PDF) Grinding Media in Ball MillsA Review ResearchGateEnd peripheral discharge type: It is generally used for dry ore mill His products are coarsegrained Rod mills can also be used for wet grinding A high gradient and better flow rate can be obtained by using the peripheral rod mill His product size is about 25 mm Central peripheral discharge type: It can be used for wet and dry grindingRod Mill Ore MillForui Machinery Henan Forui Machinery
.jpg)
Experimental study of ore characterisation methods for AG/SAG mills
2010年1月1日 Here we use measured data from a well characterised ore in a well instrumented, 12 m diameter pilot scale mill to validate direct DEM prediction of particle size reduction