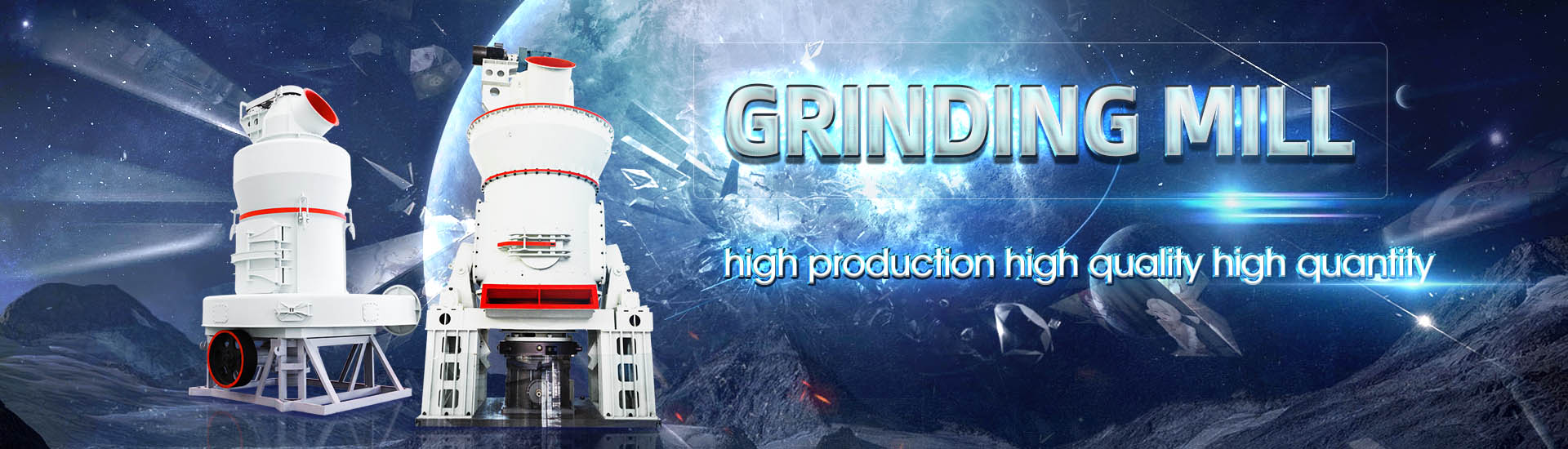
Calculation method of feed particle size of grinding system type 3 roller ore mill
.jpg)
Analysis of vertical roller mill performance with changes in
2022年5月31日 In this study, the discrete element method (DEM) was employed to explore the crushing in an overflow VRM without air involved via the bondedparticle model (BPM) 2020年3月1日 The way the size of particles is measured and expressed, however, is limited in explaining pig growth performance differences This review explores new possibilities to Size reduction in feed technology and methods for 2021年9月1日 Feed size, product size and energy data from pilot scale grinding tests were evaluated with material characterization tests Based on energysize reduction models Predicting the grinding energy of vrm depending on material 2020年11月11日 The roller mill minimizes such costs by precisely reducing feed materials with an average particle size up to 3⁄ 4 inch to a uniform average size typically between 100 and Roller mills: Precisely reducing particle size with greater
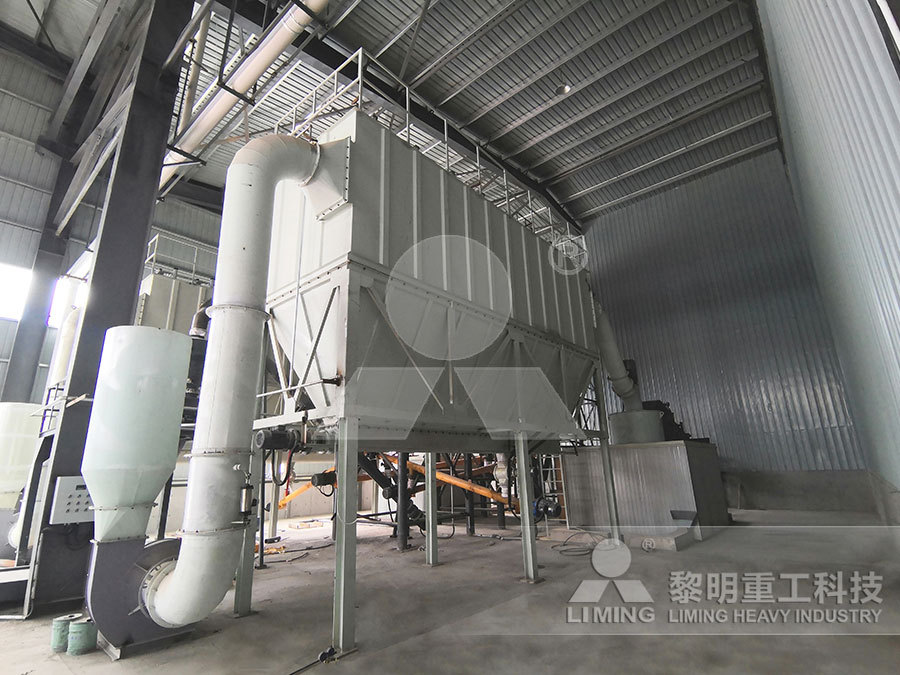
(PDF) Performance Evaluation of Vertical Roller
2017年9月11日 Particle size distributions of collected samples were determined by the combination of dry sieving and laser scattering method down to 500 µm Data obtained from two surveys were used to2024年5月29日 To achieve a finer grind (smaller finished particle size), energy and maintenance costs increase and, everything else being equal, the capacity of the grinding system will be Grinding considerations when pelleting livestock feeds2019年11月1日 This review explores new possibilities to determine, express and predict particle size Different grinding methods, including the use of roller mills, hammer mills, multicracker andSize reduction in feed technology and methods 2023年7月4日 Roller mill is a type of grinding equipment for crushing materials by pressure between two or more rolling surfaces or between rolling grinding bodies (balls, rollers) and a Roller Mill Springer
.jpg)
Numerical Investigation of Vertical Roller Mill Operation
2023年12月4日 This study investigated the effect of table speed (mill speed), roller and table gap, dam ring height, and rolling resistance of material using the discrete element method in 2024年9月27日 Particle size should be evaluated daily for roller mills and weekly for hammermills with at least the 3sieve short stack and monthly using the full 13sieve stack Particle Size Reduction Kansas State University2021年3月27日 Effect of ball and feed particle size distribution on the milling efficiency of a ball mill: An attainable region approach N Hlabangana a, G Danha b, *, E Muzenda b a Department of Chemical Engineering, National University of Science and Technology, P O Box AC 939, Ascot Bulawayo, Zimbabwe b Department of Chemical, Materials and Metallurgical Engineering, Effect of ball and feed particle size distribution on the 2022年3月9日 Therefore the feed miller needs to be able to control and adjust the particle size depending on the type of feed or maybe even depending on the produced formulation due to the prebreaking action of the Roller Mill If in Importance and optimization of particle size in
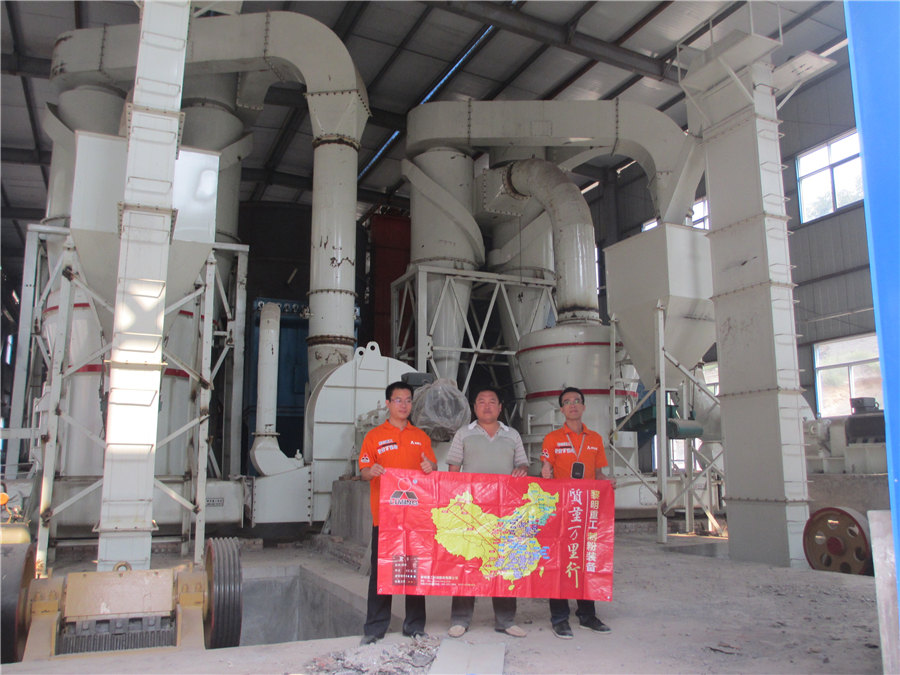
Investigating the Influence of Medium Size and
2024年8月27日 This study explores the effect of steel ball size and proportion on mineral grinding characteristics using Discrete Element Method (DEM) simulations Based on batch grinding kinetics, this paper analyzes the contact 2023年2月14日 finished particle size is the screen Any material that enters the grinding chamber must be reduced to a size small enough to pass through the screen that covers the mill's discharge opening Because of this the screen size generally provides 70% or more of the control over the finished particle sizeIntro to Size Reduction Schutte Hammermill2024年11月7日 The particle shape is determined by the properties of the feed material and the sizereduction mechanism of the mill However, because the feed material typically cannot be modified, particle shape is strongly influenced by the type of grinding mill selected Characterize the feed material To determine the type of mill you will need for your Hammer Milling and Jet Milling Fundamentals AIChE2016年7月8日 The Work Index values listed in Table I and II apply directly to a wet grinding overflow type rod mill 75 feet in diameter in open circuit; and to a wet grinding overflow type ball mill 75 feet in diameter in closed circuit with a rake classifier at 250% circulating load, and with 80% or more of the feed passing 4 meshEquipment Sizing: Crusher or Grinding Mill 911Metallurgist
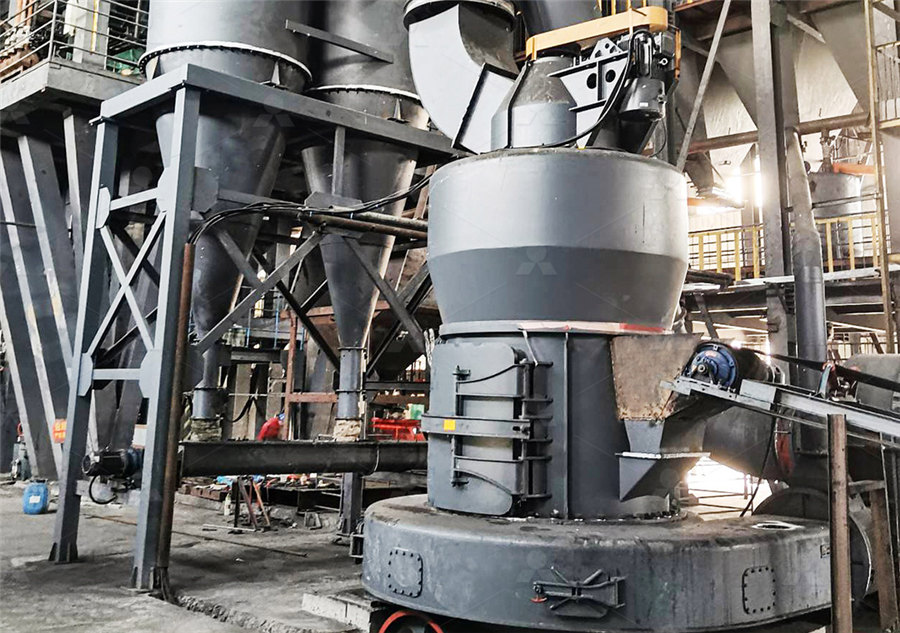
Operation Analysis of a SAG Mill under Different Conditions Based on
2020年10月9日 This method simulates the particles size, mill power, and qualified particles quality of crushed particle, which reveal the grinding strength and energy consumption of the SAG mill2017年3月20日 An effect of a grinding method, that is ball mill and high pressure grinding rolls (HPGR), on the particle size, specific surface area and particle shape of an iron ore concentrate was studiedPhysicochemical Problems of Mineral Processing Investigation 2024年5月29日 Roller mill: Particle size = 841 µm; std deviation (sgw) = 2134 841 µm ÷ 2134 = 394 µm 841 µm × 2134 = 1,792 µm Thus, 67% of the material would be between 394 and 1,792 µm Grinding equipment Both roller mills and hammermills have been applied to the task of particle size reduction or grinding in feed milling applicationsGrinding considerations when pelleting livestock feeds2024年8月8日 Different materials, sizes, and densities of grinding media can significantly affect the energy transfer during milling, impacting the rate and uniformity of particle size reduction Consequently, this choice directly influences product quality, affecting characteristics such as purity, particle size distribution, and surface areaBall Mill Success: A StepbyStep Guide to Choosing the Right Grinding
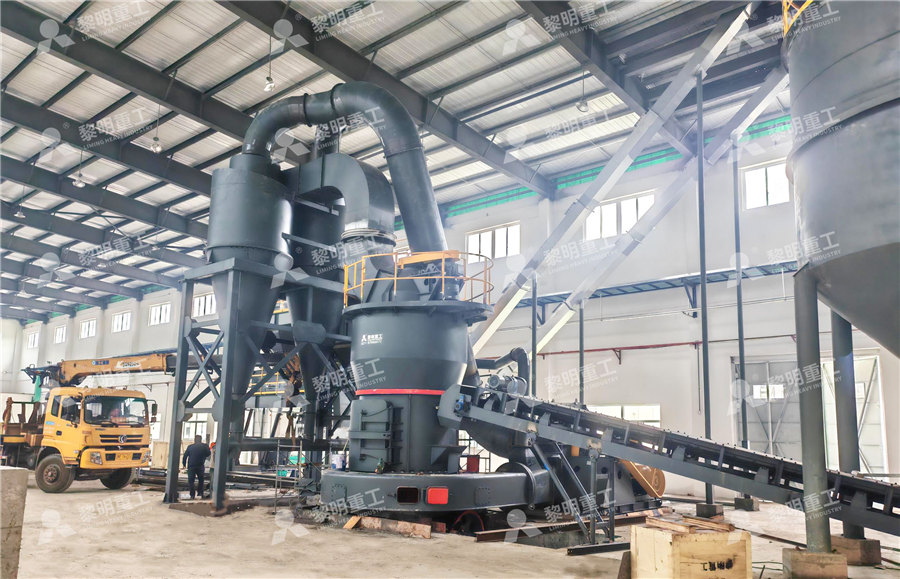
Ore Grinding SpringerLink
2023年7月20日 According to the different grinding medium, the grinding mill is divided into three types: (1) ball mill – it is used widely, and almost all materials can be triturated by ball mill; (2) rod mill – its efficiency is relatively high with the feeding particle size less than 30 mm and the product particle size around 3 mm, and the produced 2024年1月3日 Particle size distributions of collected samples were determined by the combination of dry sieving and laser scattering method down to 500 µm Data obtained from two surveys were used to obtain Performance Evaluation of Vertical Roller Mill in Cement 2022年1月23日 mill, coal mill, Clinker Mill and cement mill, and the vertical mill occupies a large energy consumption unit Therefore, it is necessary to optimize the multiobjective parameters ofAnalysis and Optimization of Grinding 2023年4月23日 observed that 30mm diameter balls were better than 10 and 20mm diameter balls in grinding a quartzite ore of feed size 8 to +56mm However, there was an increa se in efficiency when the feed (PDF) Grinding Media in Ball MillsA Review ResearchGate
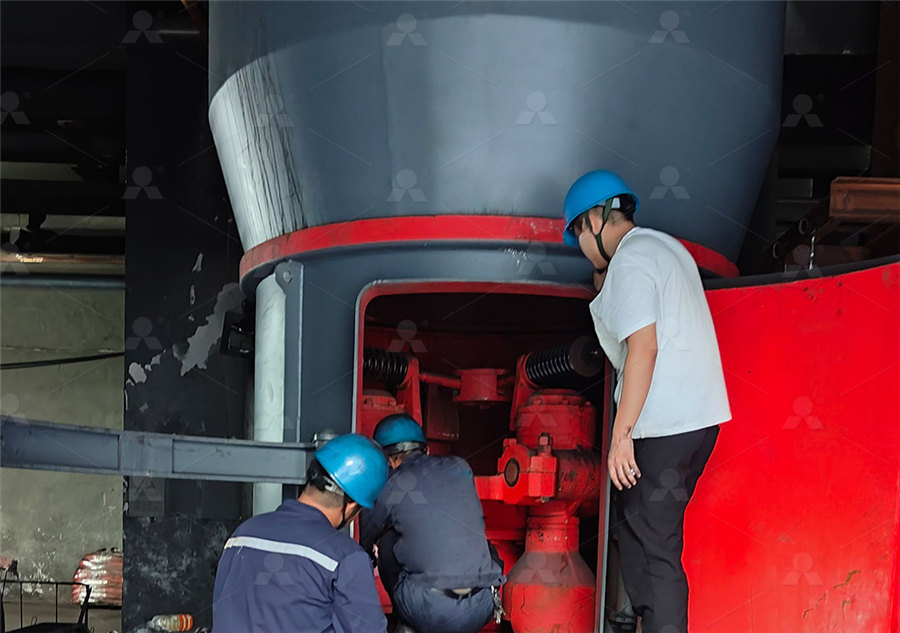
EnergyEfficient Advanced Ultrafine Grinding of Particles
2023年7月10日 The present literature review explores the energyefficient ultrafine grinding of particles using stirred mills The review provides an overview of the different techniques for size reduction and the impact of energy requirements on the choice of stirred mills It also discusses the factors, including the design, operating parameters, and feed material properties, 2022年5月31日 The size of each type metaparticle is defined by length, width, and height Table 3 gives the shape parameters of three metaparticles The size of type1 is 260 × 197 × 159 mm and the sphericity is 084 The size of type2 is 293 × 262 × 210 mm and the sphericity is 0837Analysis of vertical roller mill performance with changes in 2014年4月9日 Abstract Background: Mechanical preprocessing, which includes particlesize reduction and mechanical separation, is one of the primary operations in the feedstock supply system for a lignocellulosic biorefinery It is the means by which raw biomass from the field or forest is mechanically transformed into an onspec feedstock with characteristics better suited Full article: Optimizing hammer mill performance through 2021年1月1日 Big feed size The vertical roller mill can grind the material of particle size of 5% of the grinding roller diameter The feed size is generally 40 to 100 mm and can reach 120 mm in case of large VRM In turn it simplifies the grinding system [15], [16] •Review on vertical roller mill in cement industry its
.jpg)
Estimation of Grinding Time for Desired Particle Size
2020年1月3日 22 Grinding Studies Two kinds of mills, BBM and LBM, were used to achieve the desired P 80 passing percentage of 150 μm with an acceptable range of hematite liberation (> 75%) at optimum grinding time The BBM is a standard ball mill having a length and diameter of 300 mm × 300 mm with smooth liner as shown in Fig 2A rotating drum is attached to a 2020年3月1日 The way the size of particles is measured and expressed, however, is limited in explaining pig growth performance differences This review explores new possibilities to determine, express and predict particle size Different grinding methods, including the use of roller mills, hammer mills, multicracker and multistage grinding were reviewedSize reduction in feed technology and methods for 2024年1月3日 Investigation on the particle size and shape of iron ore pellet feed using ball mill and HPGR 909 areas of 500–1600 cm 2 g 1 The concentrate must therefore be reground in order toInvestigation on the particle size and shape of iron ore 2017年11月1日 Optimal particle size could be designed in the grinding process, and it was shown that the most convenient grinding method is to combine roller mill and hammer mill Concerning that nowadays pigs are mainly fed pelleted feed, and that pelleting causes strong additional grinding of feed particles, particle size distribution (PSD) obtained within Importance of feed structure (particle size) and feed form
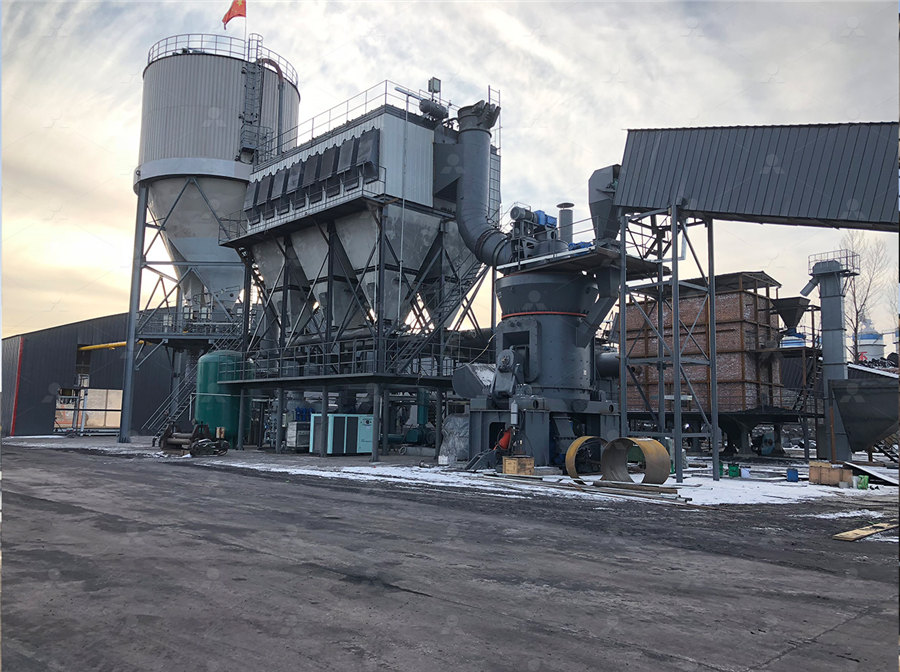
Effect of Corn Grinding Methods and Particle Size on the
2023年7月30日 the meat Therefore, this research aims to evaluate the effect of different grinding methods (roller mill, hammer mill, and twostage grinding) on the particle size distribution of corn, and the impact of varying coarseness of corn on dry matter (DM), crude protein (CP), amino acid (AA) digestibility, and apparent metabolizable energy (AME) in 2023年10月27日 The ball mill is a rotating cylindrical vessel with grinding media inside, which is responsible for breaking the ore particles Grinding media play an important role in the comminution of mineral ores in these mills This work reviews the application of balls in mineral processing as a function of the materials used to manufacture them and the mass loss, as A Review of the Grinding Media in Ball Mills for Mineral 2017年8月1日 A relatively simple backcalculation method was employed to determine above breakage parameters of FA also using timevariant milling data that were obtained after the grinding of distributed (PDF) Grinding of ClassF fly ash using planetary ball mill: A The grinding material is comminuted in the Loesche roller grinding mill between the rotating In the industrial grinding processes, the output particle size strongly depends on the mill residence The clinkers and gypsum with a ratio of 97 to 3% are interred to a vertical roller mill (LOESCHE mill) The feed rate of the clinker VRM is Modeling and simulation of vertical roller mill using
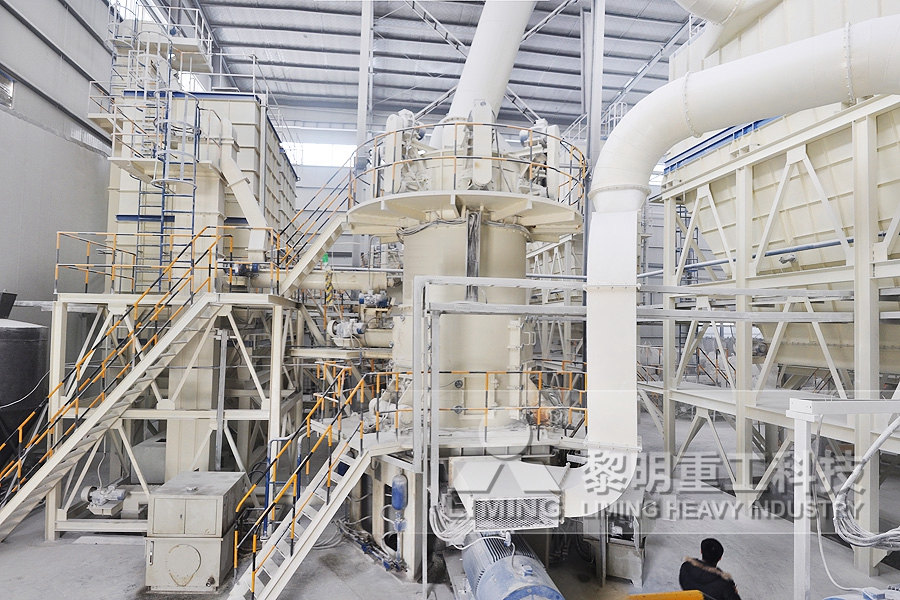
Articles A Method for Determining and Expressing the Size of Feed
1970年1月1日 Section 1Purpose and Scope 11 The purpose of this standard is to define a test procedure to determine the fineness of feed ingredients and to define a method of expressing the particle size of the material The particle size determined can be used to calculate surface area and number of particles per unit weight 12 This standard shall be 2024年9月24日 2 Feed solids – spherical particles of 265 sp gr 3 Feed concentration – less than 1% solids by volume 4 Pressure drop – 69 kPa (10psi) 5 Cyclone geometry – “standard cyclone” as described above CLASSIFICATION Historically, classification has been defined as the particle size of which 1% to 3% reports to the cyclone overflow withThe Sizing Selection of Hydrocyclones 911 Metallurgist2021年3月27日 Effect of ball and feed particle size distribution on the milling efficiency of a ball mill: An attainable region approach N Hlabangana a, G Danha b, *, E Muzenda b a Department of Chemical Engineering, National University of Science and Technology, P O Box AC 939, Ascot Bulawayo, Zimbabwe b Department of Chemical, Materials and Metallurgical Engineering, Effect of ball and feed particle size distribution on the 2022年3月9日 Therefore the feed miller needs to be able to control and adjust the particle size depending on the type of feed or maybe even depending on the produced formulation due to the prebreaking action of the Roller Mill If in Importance and optimization of particle size in
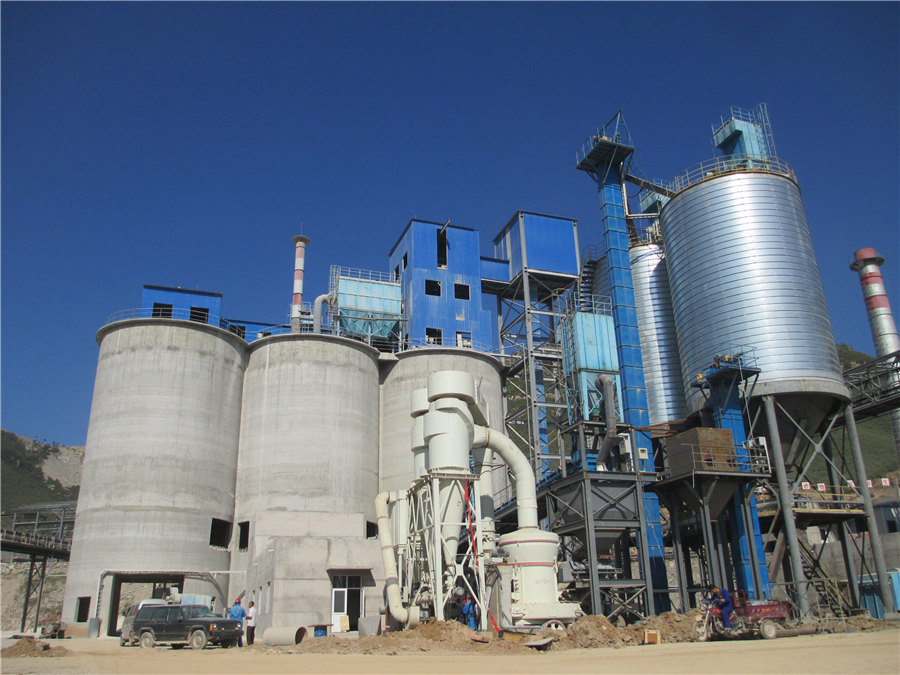
Investigating the Influence of Medium Size and
2024年8月27日 This study explores the effect of steel ball size and proportion on mineral grinding characteristics using Discrete Element Method (DEM) simulations Based on batch grinding kinetics, this paper analyzes the contact 2023年2月14日 finished particle size is the screen Any material that enters the grinding chamber must be reduced to a size small enough to pass through the screen that covers the mill's discharge opening Because of this the screen size generally provides 70% or more of the control over the finished particle sizeIntro to Size Reduction Schutte Hammermill2024年11月7日 The particle shape is determined by the properties of the feed material and the sizereduction mechanism of the mill However, because the feed material typically cannot be modified, particle shape is strongly influenced by the type of grinding mill selected Characterize the feed material To determine the type of mill you will need for your Hammer Milling and Jet Milling Fundamentals AIChE2016年7月8日 The Work Index values listed in Table I and II apply directly to a wet grinding overflow type rod mill 75 feet in diameter in open circuit; and to a wet grinding overflow type ball mill 75 feet in diameter in closed circuit with a rake classifier at 250% circulating load, and with 80% or more of the feed passing 4 meshEquipment Sizing: Crusher or Grinding Mill 911Metallurgist
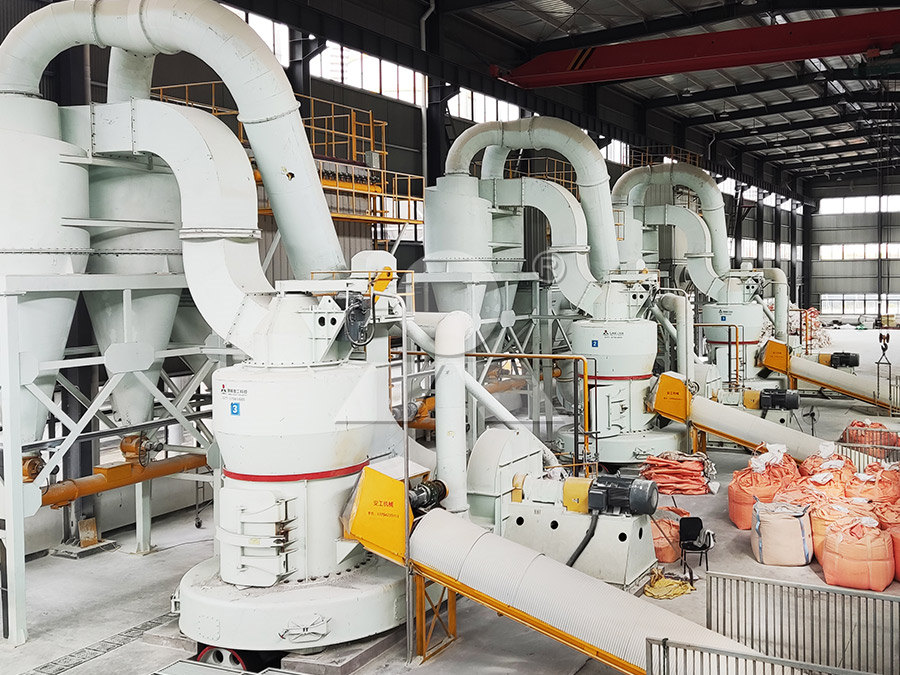
Operation Analysis of a SAG Mill under Different Conditions Based on
2020年10月9日 This method simulates the particles size, mill power, and qualified particles quality of crushed particle, which reveal the grinding strength and energy consumption of the SAG mill2017年3月20日 An effect of a grinding method, that is ball mill and high pressure grinding rolls (HPGR), on the particle size, specific surface area and particle shape of an iron ore concentrate was studiedPhysicochemical Problems of Mineral Processing Investigation 2024年5月29日 Roller mill: Particle size = 841 µm; std deviation (sgw) = 2134 841 µm ÷ 2134 = 394 µm 841 µm × 2134 = 1,792 µm Thus, 67% of the material would be between 394 and 1,792 µm Grinding equipment Both roller mills and hammermills have been applied to the task of particle size reduction or grinding in feed milling applicationsGrinding considerations when pelleting livestock feeds2024年8月8日 Different materials, sizes, and densities of grinding media can significantly affect the energy transfer during milling, impacting the rate and uniformity of particle size reduction Consequently, this choice directly influences product quality, affecting characteristics such as purity, particle size distribution, and surface areaBall Mill Success: A StepbyStep Guide to Choosing the Right Grinding