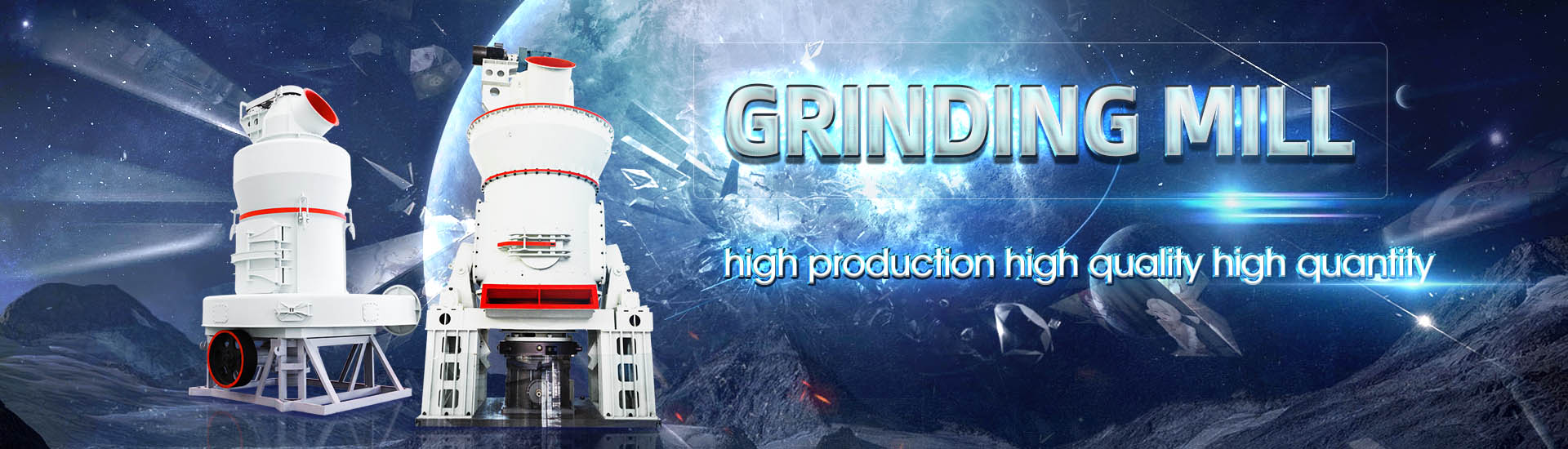
Processing cement clinker
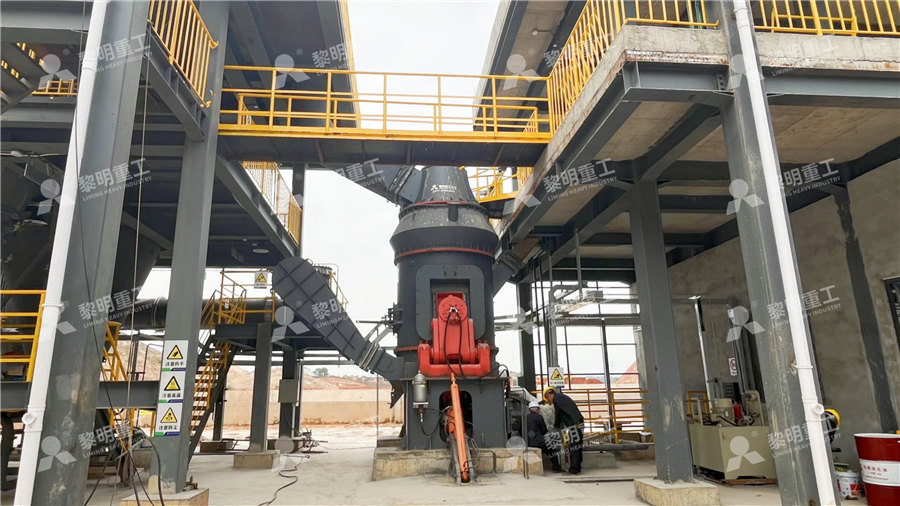
Clinker Production an overview ScienceDirect Topics
Clinker production is the most energyintensive stage in cement production, accounting for more than 90% of total industry energy use and virtually all the fuel use The main kiln type used 2022年4月12日 Only a few studies have recently used the clinker production method to estimate China’s provincial carbon emissions of the cement production process 21 For example, China’s provincial process CO2 emissions from cementLowtemperature electrochemical cement clinker (eclinker) production is a promising technology for reducing carbon dioxide (CO2) emissions in the cement industry This Perspective provides an overLowTemperature Electrochemical Cement 2023年10月16日 This study proposes a raw meal proportioning methodology for optimising coprocessing of natural feedstocks with alternative raw materials in clinker production, intending Thermodynamic modelling of cements clinkering process as
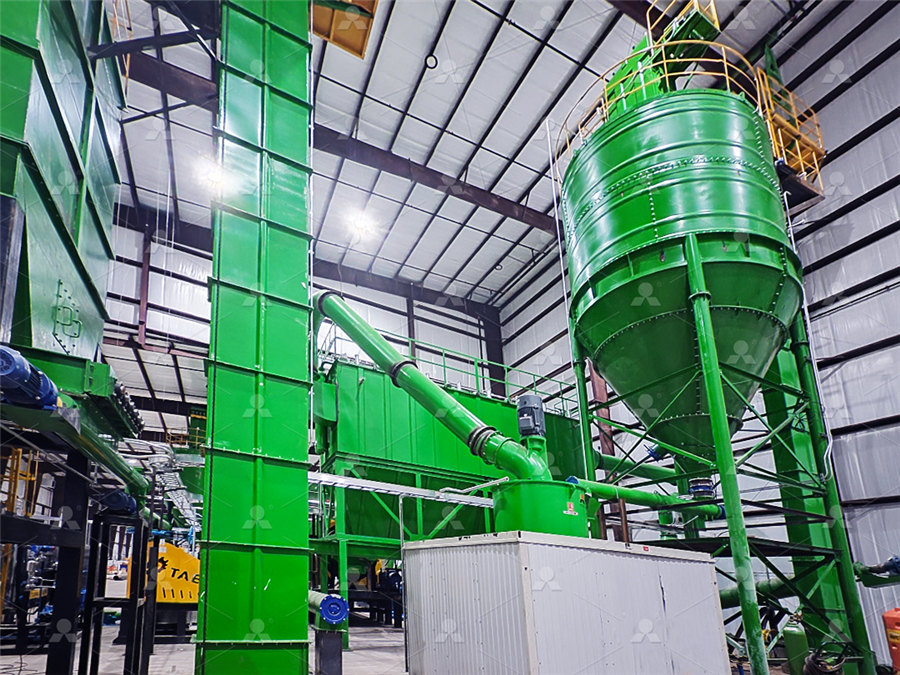
Process characteristics of clinker and cement production
2018年11月30日 New ratebased model was developed and used to validate fullscale CAP simulations for cement plants Upcoming work: CAP optimization CEMCAP framework The cement clinker manufacturing process traditionally involves intimate mixing and the subsequent heat treatment of a blend of calcareous rock, such as chalk or limestone, and Cement Clinker Production an overview ScienceDirect Topics2022年9月30日 Maximal substitution of Portland cement clinker with these materials could have avoided up to 13 Gt CO 2 eq emissions (~44% of cement production and ~28% of Cement substitution with secondary materials can reduce 2024年1月20日 With a simple reduction in the Portland clinker content in cement, whose carbon footprint is estimated at 098 kg CO 2 /kg clinker (the sum of process, fuel and electricityrelated emissions), Gawlicki allows for a Novel Processing Methods of LowClinker Multi

Modelling the cement process and cement clinker quality
2015年9月24日 Models for the simulation of cement clinker manufacturing have been developed Many of the works in the literature describe physical models that focus on flame 2023年12月20日 Excess free lime, for example, results in undesirable effects such as volume expansion, increased setting time or reduced strength Several laboratory and online systems can be employed to ensure process control in The Cement Manufacturing Process Thermo 2023年1月16日 Dr SB Hegde, Professor, Jain University, Bangalore, talks about pyroprocessing and the role of preheater, rotary kiln and clinker cooler in the cement manufacturing process In the concluding part of the twopart series, Pyroprocessing and Kiln Operation Indian 2019年8月27日 The major raw materials used as a source of CaO for cement manufacturing are limestone, chalk, marl, etc These raw materials by virtue of their natural occurrence contains other mineral impurities eg, MgO, SiO 2, Al 2 O 3, Fe 2 O 3, alkali compounds, and sulfidesThese impurities play an important role to influence the cement manufacturing Cement Manufacturing and Process Control SpringerLink
.jpg)
Comparison of energy consumption and carbon emissions from clinker
2021年7月15日 This poses a significant challenge to the cement industry directly, and to the sector using it (namely construction) indirectly The main approaches to reduce CO 2 emissions in the production of Portland cement are (Barcelo et al, 2014; Carriço et al, 2020): i) increasing energy efficiency in the production process; ii) use of alternative fuels and/or biomass; iii) Global cement production has reached 39 billion tons However, the clinkerization process, which is the basis of cement production, is responsible for an approximate annual global CO2 emission of 2 billion tons As part of CEMBUREAU’s 5C strategy, the European cement industry aims to achieve carbon neutrality throughout the cementconcrete value chain by 2050 This article is Cement and Clinker Production by Indirect Mechanosynthesis Process 2021年2月8日 Process heat overview Clinker, and clinker substitutes, are the active components that confer cement its binding properties Producing traditional cement clinker is an extremely energy and CO 2 intensive process In the EU, 90% of clinker is now made via the more energy efficient dry clinkermaking process (2) Older, less efficient wetDeep decarbonisation of industry: The cement sectorEach step of the cement production process is carefully monitored to ensure efficiency and quality Grinding, Mixing, and Blending The clinker comes out of the kiln redhot with a consistency like a lava flow It is quickly cooled down to a handling temperature in a clinker cooler where heated air from the coolers is recovered and returned How Cement is Made Portland Cement Association
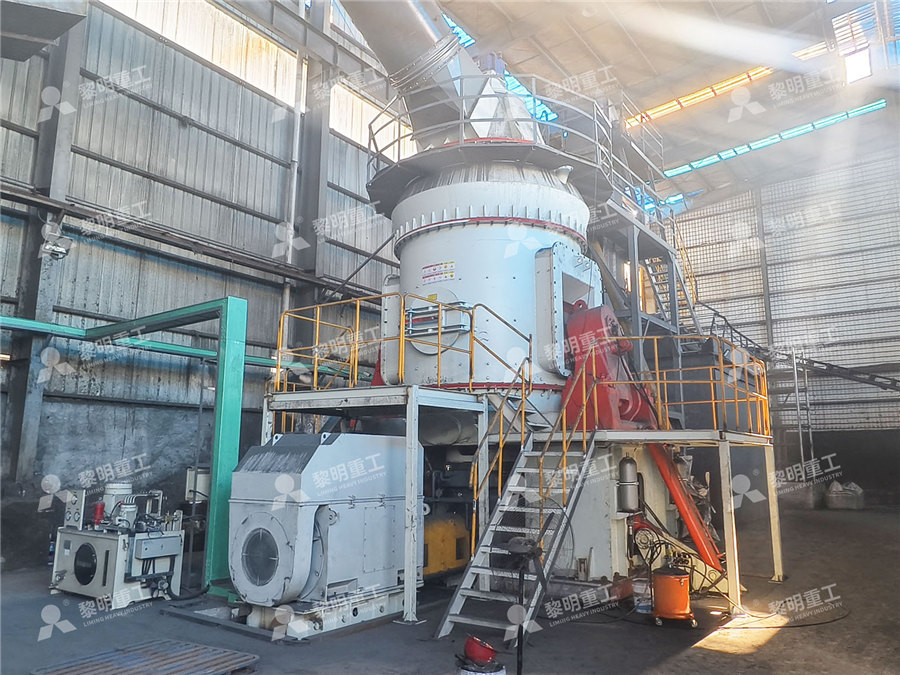
Modelling the cement process and cement clinker quality
2015年5月5日 A simplified illustration of oxygenenriched air combustion is shown in Figure 1The idea is to add highly concentrated oxygen to the process, with the aim of increasing the production of cement clinker for sustainability purposes such as enhancing the combustion of lowgrade fuels or improving energy efficiency (Damtoft et al, 2008)Higher raw meal feed is Clinker: reactions in the kiln However, reading an article or two is perhaps not the best way to get a clear picture of a complex process like cement production To get a more complete and integrated understanding of how cement is made, do have a look at the Understanding Cement book or ebook This easytoread and concise book also Reactions in the cement kiln clinkering Understanding CementA dry process kiln might be only 70m long and 6m wide but produce a similar quantity of clinker (usually measured in tonnes per day) as a wet process kiln of the same diameter but 200m in length For the same output, a dry process kiln The cement kiln Understanding CementThe overall process of conversion from raw meal to clinker being endothermic demands a theoretical heat of about 380420 kcal/kgclinker However, the rest of the specific heat consumption as tabulated above constitutes heat losses from Clinkerization Cement Plant Optimization
.jpg)
Cement Production Process Cement
2020年8月25日 A full cement production process includes the cement crushing process, raw mill process, clinker process, and cement grinding process, cement packing process, and related process Find more! Skip to content +86 2020年9月22日 The use of cement and concrete, among the most widely used manmade materials, is under scrutiny Owing to their largescale use, production of cement and concrete results in substantial emission Environmental impacts and decarbonization strategies in the cement 2023年10月19日 Clinker is a critical component in the production of cement and forms the intermediate product during the cement manufacturing process It can be best described as a nodular material, usually grayish in color, which is produced by sintering limestone and aluminosilicate materials such as clay at high temperatures in a cement kilnUnderstanding the Role of Clinker Grinding in Cement Lowtemperature electrochemical cement clinker (eclinker) production is a promising technology for reducing carbon dioxide (CO 2) emissions in the cement industryThis Perspective provides an overview of the process and the development of the electrochemical reactors for cement production (ie, “cement electrolyzers”), highlighting the potential to revolutionize cement LowTemperature Electrochemical Cement Clinker Production
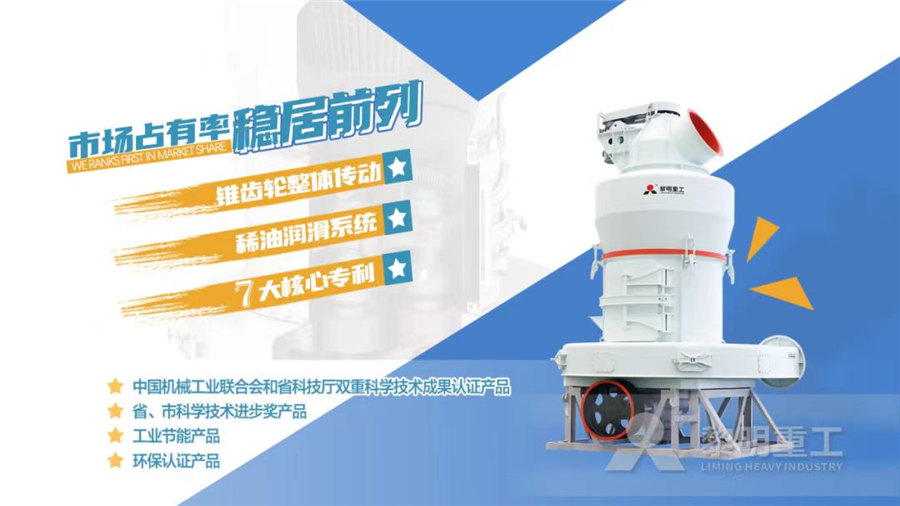
Modelling the cement process and cement clinker quality
2015年9月24日 Modelling the cement process and cement clinker quality Ho¨kfors, Eriksson and Viggh iteration procedure continues until it reaches a mass and energy balance The calculation blocks are placed in the process scheme with Chemapp 2022年9月21日 Global cement production has reached 39 billion tons However, the clinkerization process, which is the basis of cement production, is responsible for an approximate annual global CO2 emission of Cement and Clinker Production by Indirect Mechanosynthesis Process2013年1月1日 Studies on cement production optimisation have been carried out on clinker simulation using AspenTech [36], cement raw materials blending using a general nonlinear timevarying model [37], cement Modelling the cement process and cement clinker qualityThe process that cement raw materials is sintered in a kiln is the key to the quality of cement clinker In the sintering process of cement raw material, the useful components decomposed by various raw materials at 1000 °C are mainly: calcium oxide (CaO), silicon dioxide (SiO 2), aluminum oxide (Al 2 O 3), and ferric oxide (Fe 2 O 3)Cement Clinker an overview ScienceDirect Topics
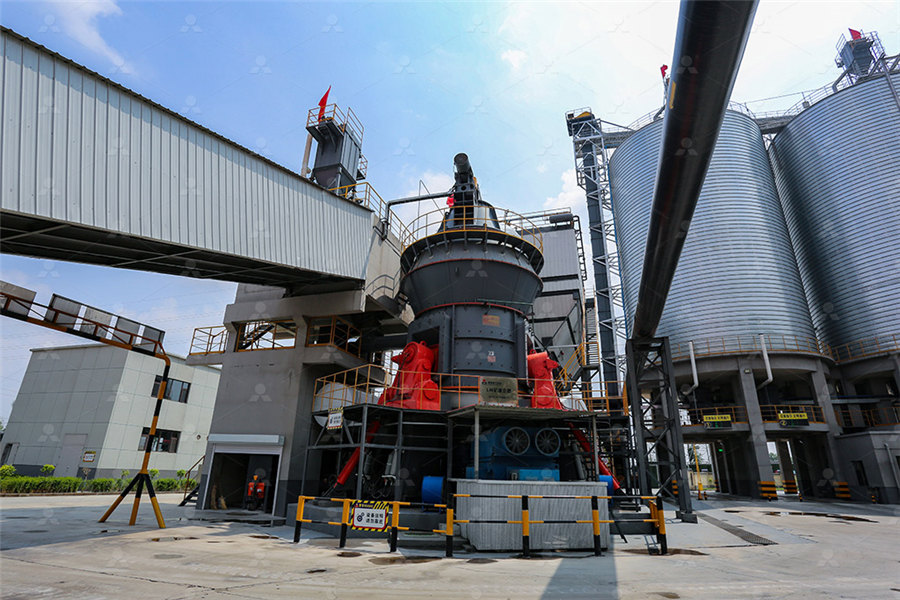
Effects of Fineness and Morphology of Quartz in
2024年7月21日 With the increasing depletion of highquality raw materials, siliceous limestone, sandstone and other hardtoburn raw materials containing crystalline SiO2 are gradually being used to produce clinker This study The clinker nodules are then cooled and stored for further processing Cement Production 1 Clinker Grinding: The clinker nodules are ground into a fine powder using a ball mill or vertical roller mill This process enhances the reactivity of clinker and allows it to be mixed with other materials 2 Addition of Gypsum: Gypsum, a mineral Cement vs Clinker What's the Difference? This vs That2015年12月1日 Aside from the development of cement composition also the production conditions of Portland cement clinker have changed significantly Following the rising social demand for CO 2 reduction and sustainability an increasing amount of secondary fuels and raw materials are used in the cement production process Who would have thought two decades Research review of cement clinker chemistry ScienceDirect4 天之前 Cement clinker is a type of substance formed during the cementmaking process It is created by heating a mixture of limestone and clay at extremely high temperatures in a kiln This pebblesized dark grey clinker, when ground into a fine powder, becomes cement and combined with other ingredients to form cement variantsCement Clinker: Types and Uses of Cement Clinker JK Cement
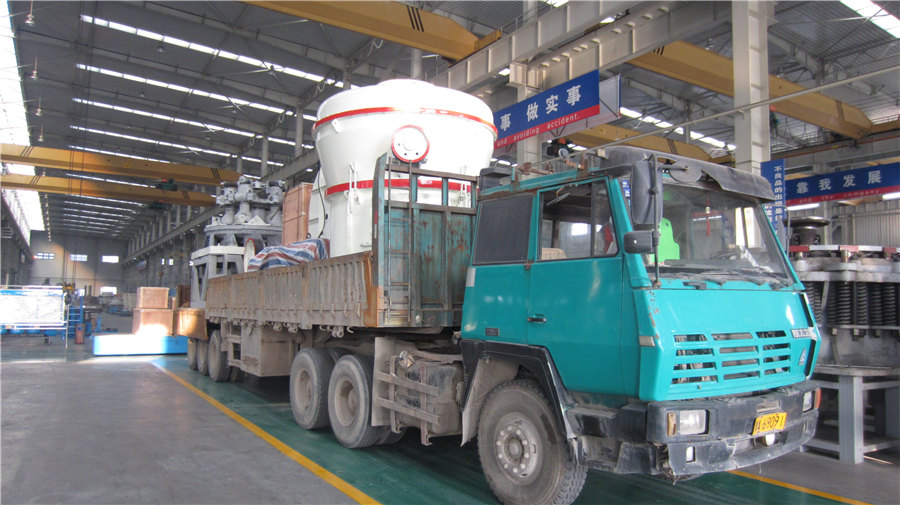
2500TPD new type dry process cement clinker production
2024年7月18日 Description: The 2500t / d cement clinker production line adopts a new dry process, with an annual output of 775,000 tons of cement clinker and a total cement output of 105 million tons / yearA cement production line and auxiliary facilities from limestone crushing to cement packaging are constructed Specialties include raw materials, production technology, 2022年9月30日 Maximal substitution of Portland cement clinker with these materials could have avoided up to 13 Gt CO2eq emissions (~44% of cement production and ~28% of anthropogenic CO2eq emissions) in Cement substitution with secondary materials can reduce 2024年9月5日 The Manufacturing Process of Cement Now, let’s explore the steps involved in the cement production process in more detail: 1 Mining and Crushing It is stored in silos until the next process 7 Clinker Grinding The next step will be to grind the clinker because now it has lowered in temperature This is done inside a ball mill where it A Comprehensive Guide to the Cement Manufacturing Process2021年3月3日 Cement is produced by a hightemperature (about 1500 °C) reaction in a rotary kiln of carefully proportioned and blended ratios of lime (CaO), silica (SiO 2), alumina (Al 2 O 3), and iron oxide (Fe 2 O 3)The production of cement is a chemical process requiring an accurate blend of the previously cited four key organic oxides and the limitation of several undesirable Cement SpringerLink
.jpg)
Efficiency of grinding stabilizers in cement clinker processing
2013年4月1日 The Portland cement clinker was obtained from the Mokra cement plant of the Heidelberg Cement Group (CMC Stock Holding Co) Clinker in the size range 016–5 mm, d 50 = 28 mm, was employed Its chemical analysis is summarized in Table 12023年12月20日 Excess free lime, for example, results in undesirable effects such as volume expansion, increased setting time or reduced strength Several laboratory and online systems can be employed to ensure process control in The Cement Manufacturing Process Thermo 2023年1月16日 Dr SB Hegde, Professor, Jain University, Bangalore, talks about pyroprocessing and the role of preheater, rotary kiln and clinker cooler in the cement manufacturing process In the concluding part of the twopart series, Pyroprocessing and Kiln Operation Indian 2019年8月27日 The major raw materials used as a source of CaO for cement manufacturing are limestone, chalk, marl, etc These raw materials by virtue of their natural occurrence contains other mineral impurities eg, MgO, SiO 2, Al 2 O 3, Fe 2 O 3, alkali compounds, and sulfidesThese impurities play an important role to influence the cement manufacturing Cement Manufacturing and Process Control SpringerLink
.jpg)
Comparison of energy consumption and carbon emissions from clinker
2021年7月15日 This poses a significant challenge to the cement industry directly, and to the sector using it (namely construction) indirectly The main approaches to reduce CO 2 emissions in the production of Portland cement are (Barcelo et al, 2014; Carriço et al, 2020): i) increasing energy efficiency in the production process; ii) use of alternative fuels and/or biomass; iii) Global cement production has reached 39 billion tons However, the clinkerization process, which is the basis of cement production, is responsible for an approximate annual global CO2 emission of 2 billion tons As part of CEMBUREAU’s 5C strategy, the European cement industry aims to achieve carbon neutrality throughout the cementconcrete value chain by 2050 This article is Cement and Clinker Production by Indirect Mechanosynthesis Process 2021年2月8日 Process heat overview Clinker, and clinker substitutes, are the active components that confer cement its binding properties Producing traditional cement clinker is an extremely energy and CO 2 intensive process In the EU, 90% of clinker is now made via the more energy efficient dry clinkermaking process (2) Older, less efficient wetDeep decarbonisation of industry: The cement sectorEach step of the cement production process is carefully monitored to ensure efficiency and quality Grinding, Mixing, and Blending The clinker comes out of the kiln redhot with a consistency like a lava flow It is quickly cooled down to a handling temperature in a clinker cooler where heated air from the coolers is recovered and returned How Cement is Made Portland Cement Association
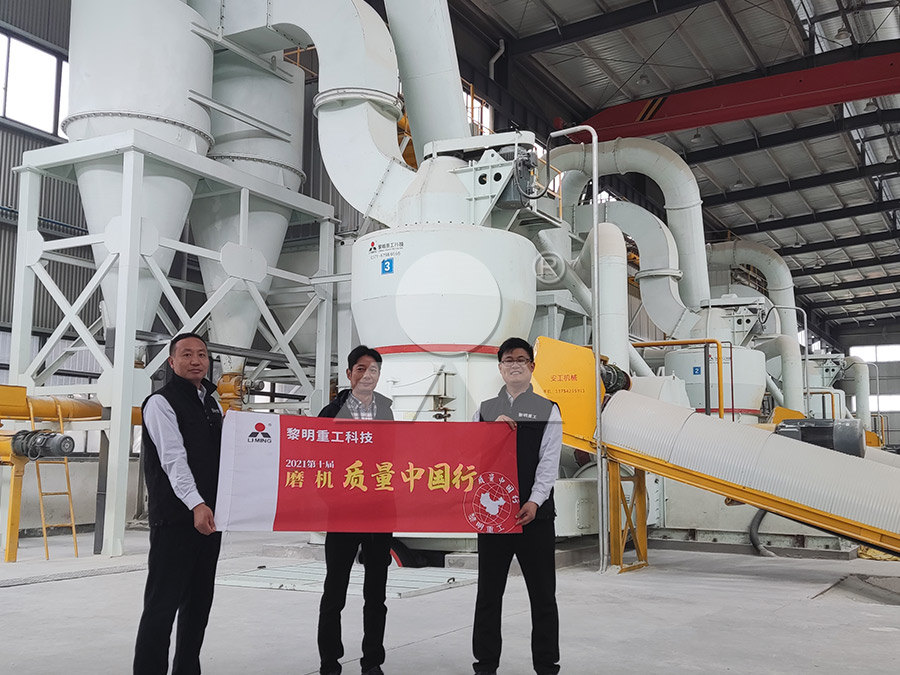
Modelling the cement process and cement clinker quality
2015年5月5日 A simplified illustration of oxygenenriched air combustion is shown in Figure 1The idea is to add highly concentrated oxygen to the process, with the aim of increasing the production of cement clinker for sustainability purposes such as enhancing the combustion of lowgrade fuels or improving energy efficiency (Damtoft et al, 2008)Higher raw meal feed is Clinker: reactions in the kiln However, reading an article or two is perhaps not the best way to get a clear picture of a complex process like cement production To get a more complete and integrated understanding of how cement is made, do have a look at the Understanding Cement book or ebook This easytoread and concise book also Reactions in the cement kiln clinkering Understanding Cement