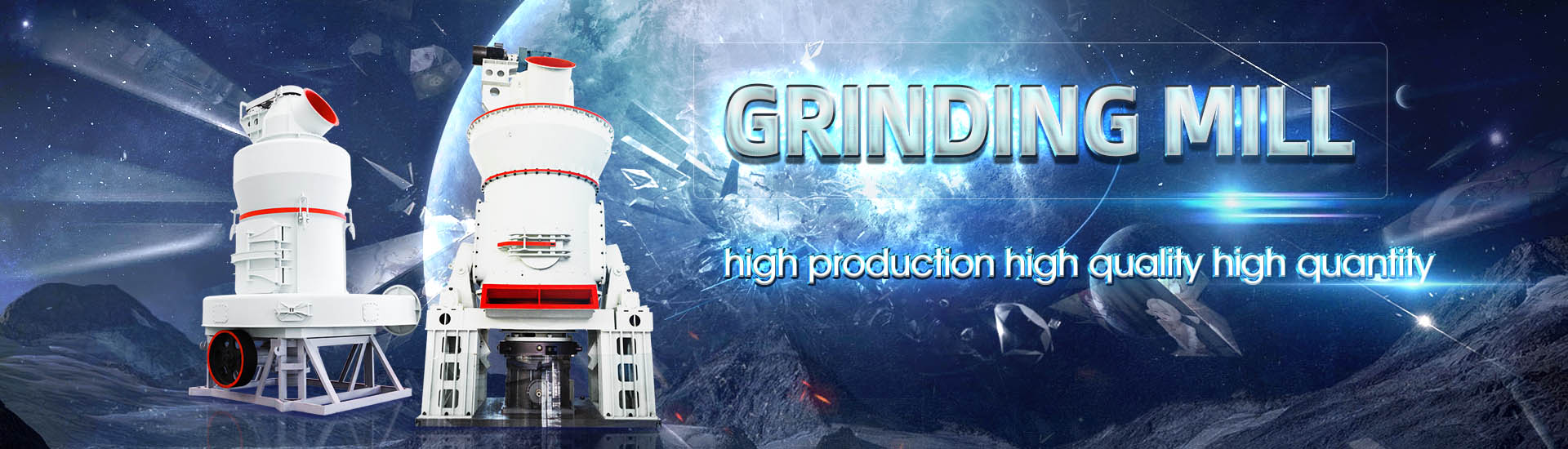
How to design a singlelayer highfine vertical mill for mining
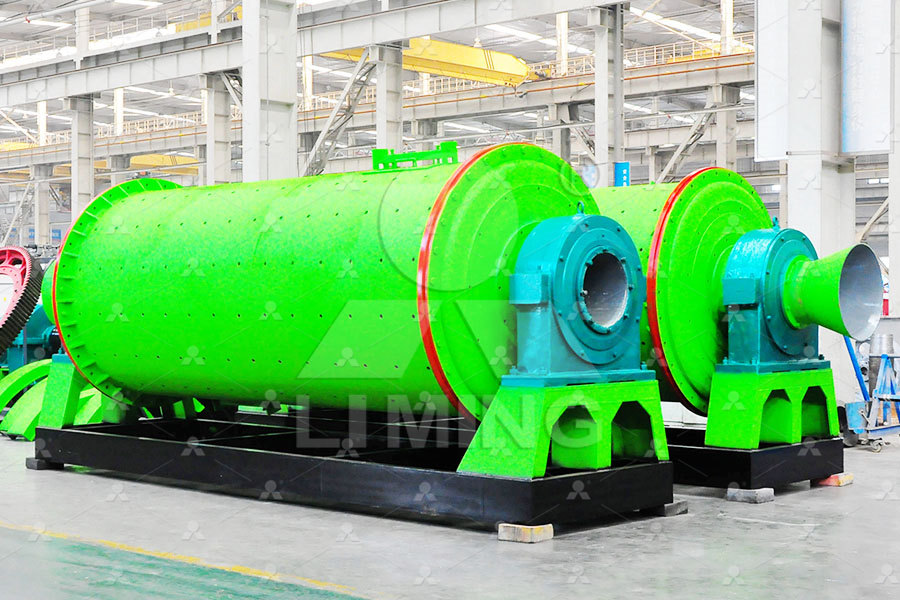
Operational parameters affecting the vertical roller mill
2017年4月1日 In the airswept mode, the verticalrollermill and a high efficiency dynamic classifier are suited above each other as a single unit (Fig 1) Material is fed to the grinding 2023年6月1日 For the optimization of operating parameters of large vertical mills, this paper determines the optimization design variables and multiple optimization objectives according to Operation parameters multiobjective optimization method 2022年5月31日 The vertical roller mill (VRM) is commonly used for secondary and tertiary crushing processes in numerous industries In this study, the discrete element method (DEM) Analysis of vertical roller mill performance with changes in 2020年3月19日 Abstract—It is difficult to effectively control the vertical grinding process of raw materials due to its characteristics of strong coupling, nonlinearity and large hysteresis This Intelligent Control System Design for Vertical Mill Based
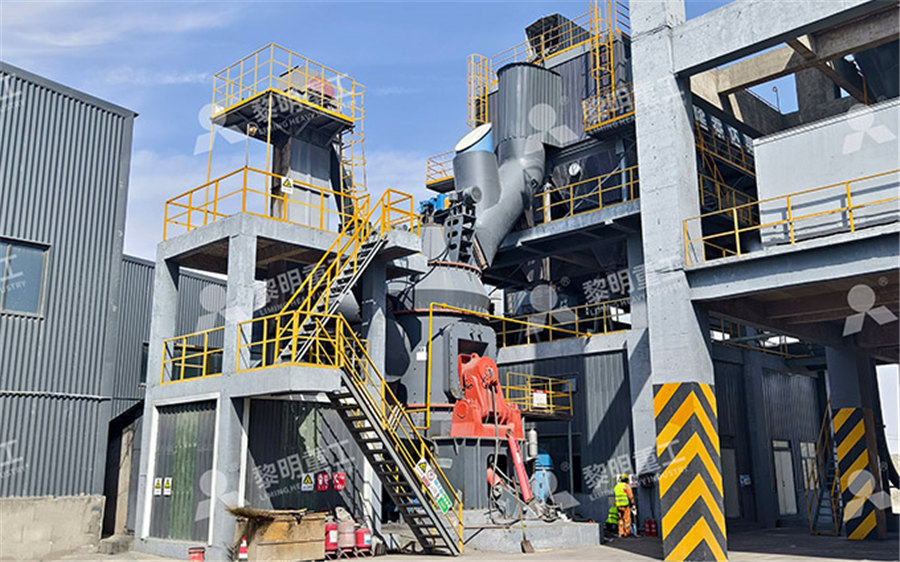
RECENT DEVELOPMENTS IN COARSE GRINDING USING
2023年9月21日 Vertical stirred milling is a wellrecognized technology for the secondary, regrind and fine grinding applications and are increasingly replacing coarser ball mill applications in 2019年1月17日 Through the analysis of the main structure of the vertical mill, we use the assembly function of the solid edge threedimensional solid software to implement the Solid Edge’s Application in Vertical Mill Design2018年2月20日 solution for fine and ultra fine grinding Outotec HIGmills™ offer the unique possibility for online control and optimization of regrind product particle size This paper Outotec HIGmills; A Fine Grinding Technology2023年12月4日 Slope stability is a prominent problem for the eficient application and promotion of highwall mining technology, especially when mining residual coal under high and steep Slope stability calculation method for highwall mining
.jpg)
Study on the law of surface subsidence in layered mining of
2023年9月7日 In this paper, taking the Barapukuli coal mine (referred to as Mengba mine) in Bangladesh as an example, a model was constructed by combining the measured subsidence 2017年4月1日 A grinding power model has been developed to predict the power draw of Outotec’s vertical fine grinding mill (HIGmill) The model is based on a combination of A power model for fine grinding HIGmills with castellated 2014年5月1日 The specific energy consumptions of the grinding equipment and the standard bond work indexes, used 100μm screen, of raw materials are given belowCircuitBond work index (kWh/t)Specific energy (PDF) Matrix Model Simulation of a Vertical 2016年9月1日 The Loesche vertical roller mill is one such high compression grinding device which has undergone test studies in a minerals processing context (Altun et al, 2017 (Altun et al, , 2015van Drunick Operational parameters affecting the vertical roller mill
%3C1PGHL[2}HK_]YT.jpg)
Ultrafine Vertical Mill
Ultrafine vertical mill is a highefficient industrial grinding mill, be used to grind hard stones into ultrafine powder, like talc, mica, etc CLUM series ultrafine vertical mills are equipped with specially designed roller sleeves and liner 2024年8月29日 Product introduction:LUM ultrafine vertical mill is a largescale highfine vertical mill on the basis of LM vertical mill that developed by our company for reference to advanced technology at home and abroad, and suitable for nonmetallic minerals with a largescale ultrafine processingLUM Ultrafine Vertical Mill vanguardtec2019年10月11日 Gold mining practices have stagnated in the face of continuously changing technology Companies face a new battery of challenges to recover minerals The VRM, depending on the roller size, has a high reduction ratio; feed from 80 mm to 140 mm to a product of P80 at 75 µm in one pass, the mill is a closed circuit on its own having the Vertical roller mills: The new leader in grinding technology2014年10月20日 Rio Paracatu regrind circuit Santos Júnior et al (2011) presented some data on the Paracatu Vertical Mill circuit process, as well as its comparison to the plant's conventional ball millRegrind of metallic ores with vertical mills: An overview of
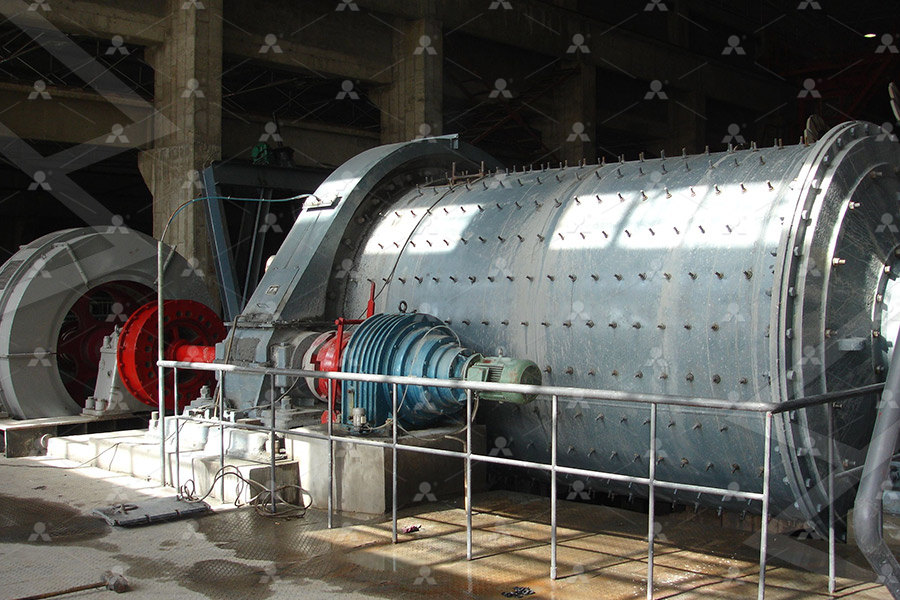
Full article: Methodology for a dump design optimization in largescale
2017年10月13日 1 Introduction Three major destination groups, characterized by a cutoff grade criteria and ore type, represent the places in the mine where the material receives specific treatment after its delivery from the pit: leach dumps, waste dumps and mill (Hustrulid, Kuchta, Martin, Citation 2013)Dump leaching facilities are built to receive and treat lowgrade ore by 1 What is a Vertical Grinding Mill? The Vertical Grinding Mill (VGM) is an upright steel vessel with an inlet, an outlet and a central portion of the inlet It is used for fine size reduction when output to input reduction required is large These mill crushers consist of a reducing rotating mill for size reduction The whole closed circuit is Vertical Grinding Mill: How it Works, Application And 2023年2月15日 Compared with single layer mining, the vertical stress on the web pillar in the lowest panel is reduced by 1483~1825%, and the safety factor of the web pillar is increased to 027Stability Analysis of MultiLayer Highwall Mining: A 2018年9月17日 The use of vertical stirred mills in the mining industry has increased remarkably over the past few decades, as a result of growing requirement for finer ore grindingDEVELOPMENT OF A LABORATORY TEST TO DESIGN VERTICAL STIRRED MILLS
.jpg)
The Selection and Design of Mill Liners 911 Metallurgist
2024年9月24日 Figure 5 High–low wave ball mill liner Materials The selection of the material of construction is a function of the application, abrasivity of ore, size of mill, corrosion environment, size of balls, mill speed, etc liner design and material of construction are integral and cannot be chosen in isolation2024年6月2日 Beef (high mineral) 12981471 Single ingredient (alfalfa, beet pulp, gluten) 12111471 The above recommended values may vary due to feed ingredient variation or desired pellet quality Chapter 3: Pellet Mill Design electricity being present and the possible generation of sparks occurring Geardriven pellet mills do notPellet mill design Feed StrategyThe process comprises just a scalping cyclone with no circulating load, feed tank and pump, and the mill itself The benefit of high power intensity and vertical installation is a very small footprint The head room over the mill is small and HIGmill high intensity grinding mill Metso2015年11月5日 It is evident that grinding in a vertical stirred mill with a double helical screw is more efficient than that using a pin type stirrer in terms of the product size distribution and the specific energy consumption It is concluded that the double helical screw design provides better energy efficiency compared to the pin type stirrer designA Comparative Study on a Vertical Stirred Mill Agitator Design for Fine
.jpg)
A Review: Textile Technologies for Single and Multi‐Layer
Engineering fibrous architectures entail fiber fabrication and manufacturing textile structures that will mimic the native ECM and provide a favorable environment for cell growth and differentiation [] Recent studies used textile technologies, such as electrospinning, [1115] braiding, [16, 17] knitting, [18, 19] weaving, [20, 21] or a combination [2226] to fabricate scaffolds of tubular 2022年1月12日 Advantages of CLUM Ultrafine Vertical Mill: ① High grinding efficiency and excellent quality of finished products Special structure design and working principle, the equipment has low vibration and low noise ultrafine ball mill can produce 10um powder; ceramic ball mill has high whiteness and the lowest iron content Good grain What is the difference between vertical mill and ball mill?2023年9月21日 Pilot test work was carried out by Mazzinghy et al (2015) on a batch ball mill and pilot scale vertical mill to assess the energy efficiency factor The results shows that the scaling factor of 135 was required to adjust the ball mill energyspecific breakage rates to match the breakage rates in a vertical mill The vertical millRECENT DEVELOPMENTS IN COARSE GRINDING USING 2017年8月12日 vertical roller grinding mills for grinding: • Coal • Cement raw material • Clinker / granulated slag • Industrial minerals, and • Ores The core elements of these plants are the Loesche vertical mills for drygrinding the abovementioned grinding stock Loesche has developed and built the largest and mostPROCESS OPTIMISATION FOR LOESCHE GRINDING
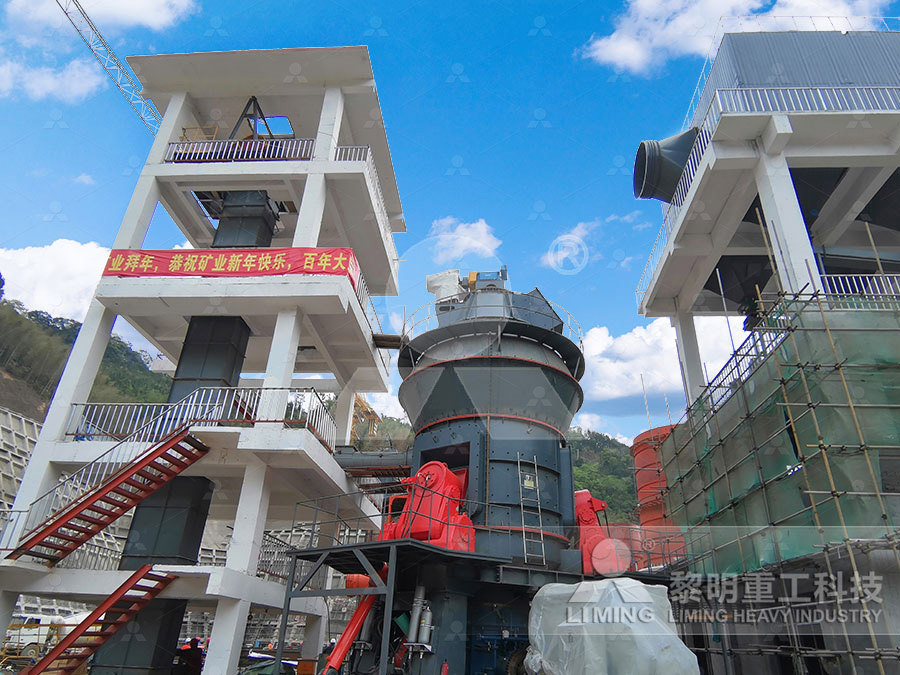
How to operate an air classifier mill to meet your fine
2021年7月11日 vertical mill Combined drive In this classifier mill, as shown in Figure 2b, the classifier wheel and rotor disc are mounted on one shaft and rotate at the same speed As a result, the mill is smaller, has a lower purchase cost, and requires less installed horsepower than the vertical mill However, the apFigure 1 Vertical air classifier 2022年4月14日 construction, mining industry and developments LUMSeries Ultra fine vertical grinding mill is an advanced mill which combining our company’ several years of millproducing experiences, It is designed and researched based on vertical mill technology, absorbing the worldwide ultrafine grinding theories ThisLUM SERIES ULTRAFINE GRINDING MILL Kefid2006年1月1日 The appropriate design of liners continues to be an issue on many mills worldwide Loss of milling capacity especially at liner change, uneven wear lives along the mill, substantial scrap on worn (PDF) Selection and design of mill liners2016年3月11日 The advantages of producing a fine mill feed have been recognized for many years equipment design and operation Where fine crushing should stop and grinding begin is controversial and is influenced Crushing Plant Flowsheet DesignLayout
.jpg)
(PDF) Grinding in Ball Mills: Modeling and Process Control
2012年6月1日 As the cylinder starts to rotate, the grinding balls inside the cylinder crush and grind the feed material, generating mechanical energy that aids in breaking bonds, activating the catalyst, and 2020年8月12日 This study shows the performance of a currently running vertical roller coal mill (VRM) in an existing coalfired power plant In a power plant, the coal mill is the critical equipment, whose An investigation of performance characteristics and 2022年7月20日 The smallest dualpolarization coupler compatible with MCFs reported to date has an area of 200 µm 2 and an efficiency of −43 dB with a fiber tilted at 10 • [7]Multilayer inverse design of vertical grating couplers for high 2019年1月16日 vertical mill design involves different product specifications, due to technical limitations, it is impossible to form a standardized design Obviously, 2D design cannot meet the requirements of individual product design and product performance However, Solid Edge 3D design can solve these problems 3 Solid Edge 3D Design in Vertical Mill DesignSolid Edge’s Application in Vertical Mill Design Springer
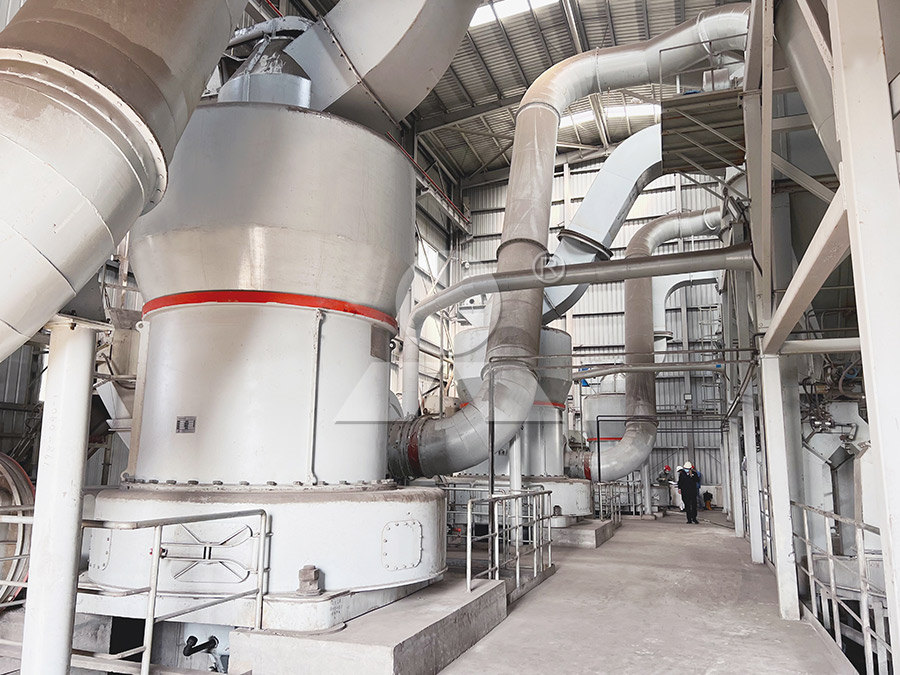
Vertical Roller Mill Operation in Cement Plant
The vertical roller mill (VRM) is a type of grinding machine for raw material processing and cement grinding in the cement manufacturing processIn recent years, the VRM cement mill has been equipped in more and more cement plants around the world because of its features like high energy efficiency, low pollutant generation, small floor area, etc The VRM cement mill has a 2015年6月19日 The basic parameters used in ball mill design (power calculations), rod mill or any tumbling mill sizing are; material to be ground, characteristics, Bond Work Index, bulk density, specific density, desired mill tonnage capacity DTPH, operating % solids or pulp density, feed size as F80 and maximum ‘chunk size’, product size as P80 and maximum and finally the type of Ball Mill Design/Power Calculation 911Metallurgist2021年1月29日 VRM Production Rate and Specific Power It can be clearly seen in Figure 3 that last 6 months average breakdown frequency Rate was 6016 tripping per month means per day more than 2 trippingIncrease productivity of vertical roller mill using seven QC tools2023年11月8日 This sturdy design, compared to vertical mills, results in less vibration, reduced deflection, and a more stable operation, enhancing overall machine performance and durability Cons Costly: Horizontal milling setups are notably more expensive than vertical machines, involving substantial initial capital and maintenance C Milling: Horizontal vs Vertical Guide Zintilon

(PDF) Matrix Model Simulation of a Vertical
2014年5月1日 The specific energy consumptions of the grinding equipment and the standard bond work indexes, used 100μm screen, of raw materials are given belowCircuitBond work index (kWh/t)Specific energy 2016年9月1日 The Loesche vertical roller mill is one such high compression grinding device which has undergone test studies in a minerals processing context (Altun et al, 2017 (Altun et al, , 2015van Drunick Operational parameters affecting the vertical roller mill Ultrafine vertical mill is a highefficient industrial grinding mill, be used to grind hard stones into ultrafine powder, like talc, mica, etc CLUM series ultrafine vertical mills are equipped with specially designed roller sleeves and liner Ultrafine Vertical Mill2024年8月29日 Product introduction:LUM ultrafine vertical mill is a largescale highfine vertical mill on the basis of LM vertical mill that developed by our company for reference to advanced technology at home and abroad, and suitable for nonmetallic minerals with a largescale ultrafine processingLUM Ultrafine Vertical Mill vanguardtec
.jpg)
Vertical roller mills: The new leader in grinding technology
2019年10月11日 Gold mining practices have stagnated in the face of continuously changing technology Companies face a new battery of challenges to recover minerals The VRM, depending on the roller size, has a high reduction ratio; feed from 80 mm to 140 mm to a product of P80 at 75 µm in one pass, the mill is a closed circuit on its own having the 2014年10月20日 Rio Paracatu regrind circuit Santos Júnior et al (2011) presented some data on the Paracatu Vertical Mill circuit process, as well as its comparison to the plant's conventional ball millRegrind of metallic ores with vertical mills: An overview of 2017年10月13日 1 Introduction Three major destination groups, characterized by a cutoff grade criteria and ore type, represent the places in the mine where the material receives specific treatment after its delivery from the pit: leach dumps, waste dumps and mill (Hustrulid, Kuchta, Martin, Citation 2013)Dump leaching facilities are built to receive and treat lowgrade ore by Full article: Methodology for a dump design optimization in largescale 1 What is a Vertical Grinding Mill? The Vertical Grinding Mill (VGM) is an upright steel vessel with an inlet, an outlet and a central portion of the inlet It is used for fine size reduction when output to input reduction required is large These mill crushers consist of a reducing rotating mill for size reduction The whole closed circuit is Vertical Grinding Mill: How it Works, Application And
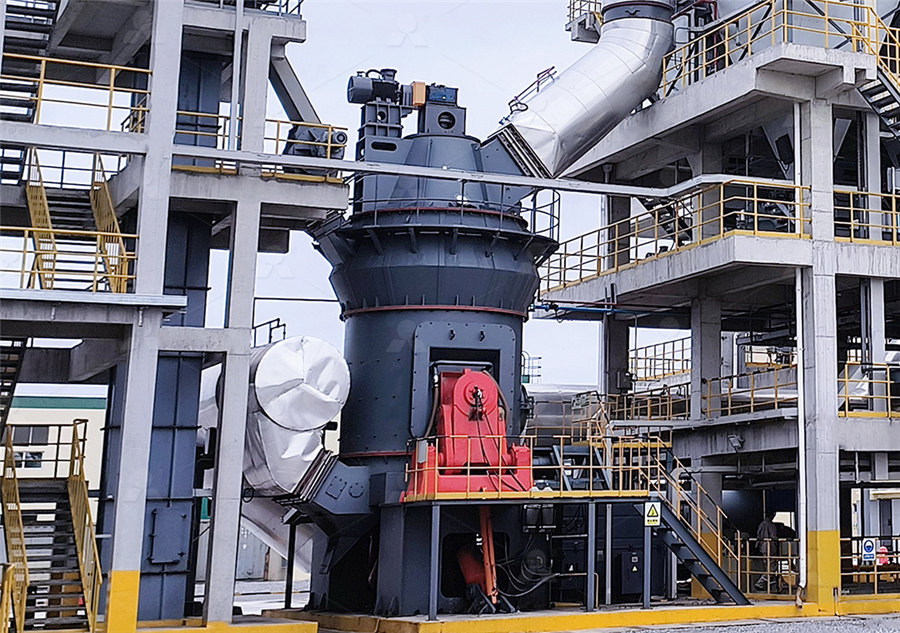
Stability Analysis of MultiLayer Highwall Mining: A
2023年2月15日 Compared with single layer mining, the vertical stress on the web pillar in the lowest panel is reduced by 1483~1825%, and the safety factor of the web pillar is increased to 0272018年9月17日 The use of vertical stirred mills in the mining industry has increased remarkably over the past few decades, as a result of growing requirement for finer ore grindingDEVELOPMENT OF A LABORATORY TEST TO DESIGN VERTICAL STIRRED MILLS