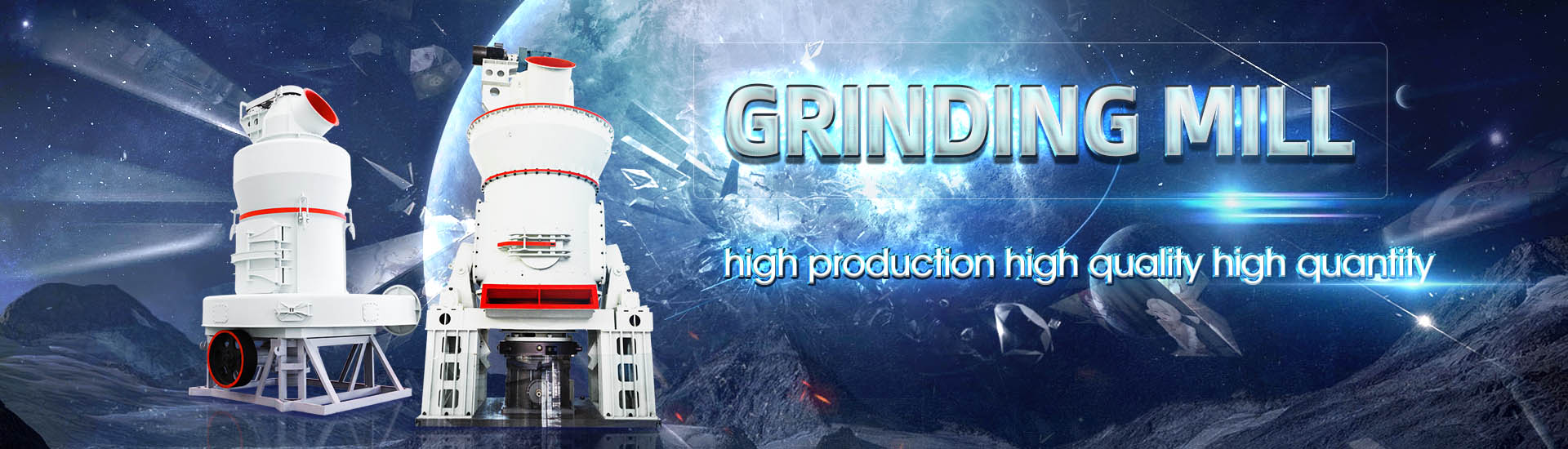
Furnace processing and iron selection process
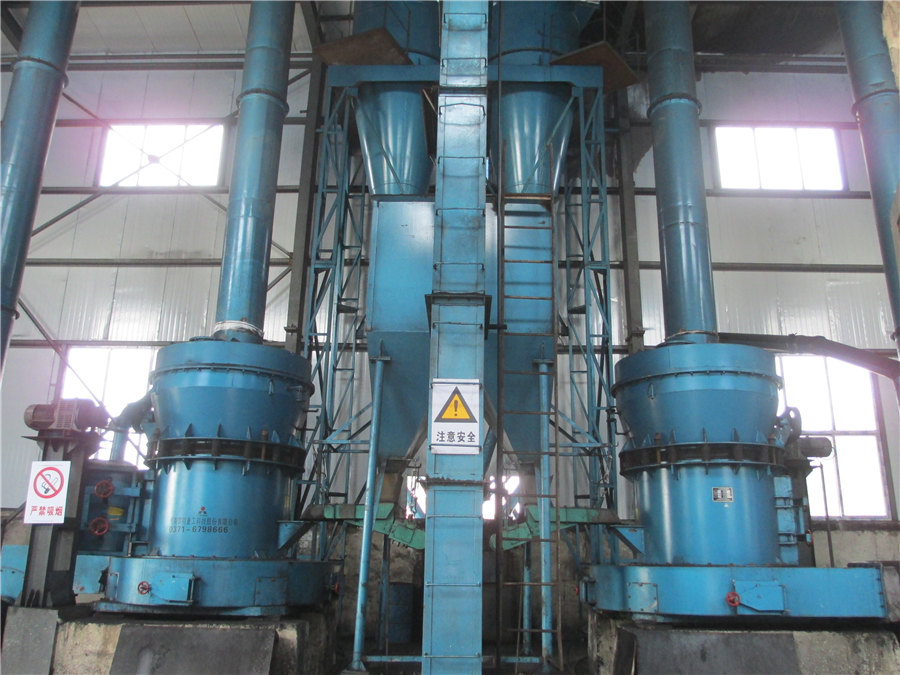
An Analysis of LongProcess Ironmaking in a
2023年10月16日 The three new ironmaking processes in the project are the top gas circulating oxygen blast furnace (OBF) process, the new smelting reduction process (HIsarna), and the iron ore electrolysis process (ULCOWIN) 2016年5月24日 From this angle, an evaluation of the technical alternatives for melting, holding, transferring and pouring the molten iron is presented, chiefly with regard to the use of The Melting, Holding and Pouring Process Energy and 2024年5月27日 The data on raw and fuel materials, process operation, smelting state, and slag and iron discharge during the whole BF process comprised 171 variables with 9223 groups of Process metallurgy and datadriven prediction and feedback Most blast furnace iron is the raw material for oxygen steelmaking, where the molten iron is refined to produce the world’s most popular metal for engineering applications—rolled steel In Blast Furnace Ironmaking ScienceDirect
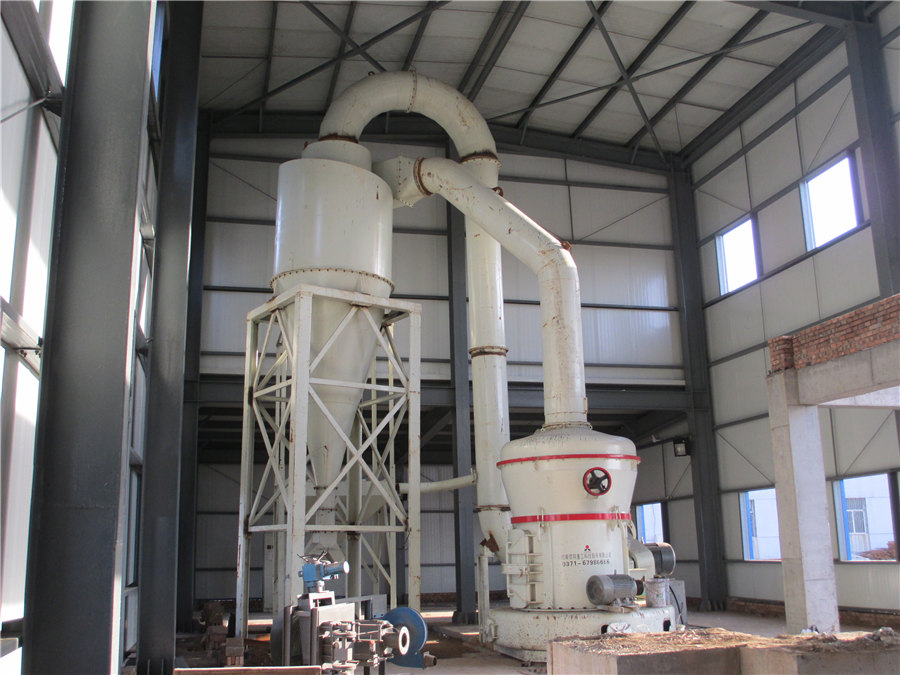
A review of ironmaking by direct reduction processes:
2019年1月1日 DR processes reduce iron ore in its solid state by the use of either natural gas or coal as reducing agents, and they have a comparative advantage of low capital costs, low 2020年8月19日 From that moment, the technologies to produce iron/steel have been significantly developed This way, nowadays, there are three routes: the utilization of Direct Production of Iron in the Blast Furnace SpringerLink2016年4月8日 The blast furnace is a widely used process in the iron and steelmaking industry for converting iron ore to liquid iron, and it represents the predominant ironproducing process in North America Recently, the driving Comprehensive Numerical Modeling of the Blast 2023年9月8日 These actions targeted blast furnace process enhancement, leading to heightened production rates, reduced fuel consumption, and diminished greenhouse gas emissions This work epitomizes theBlast Furnace process optimization for
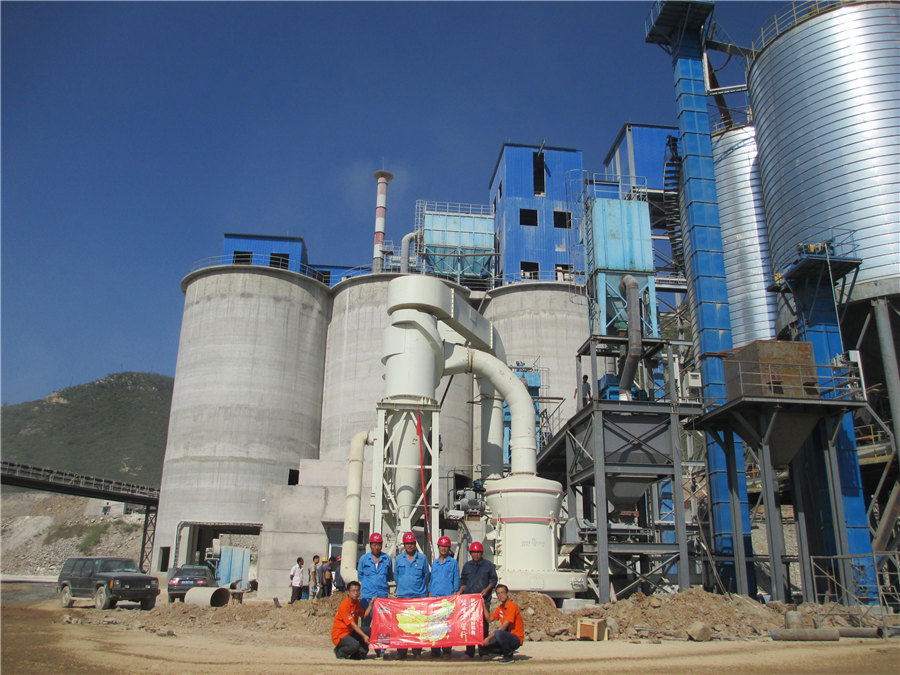
Recent Trends in the Technologies of the Direct
2023年4月5日 The blast furnace and direct reduction processes have been the major iron production routes for various iron ores (ie goethite, hematite, magnetite, maghemite, siderite, etc) in the past few decades, but the 2022年8月23日 The blast furnace and direct reduction processes have been the major iron production routes for various iron ores (ie goethite, hematite, magnetite, maghemite, siderite, etc) in the past few (PDF) An Overview of the ReductionSmelting 2022年1月14日 Dumping of electric arc furnace dust is an environmental concern, and recovery of valuable metals like iron, zinc, lead from EAFD and safe disposal of residue has got enough attention(PDF) A Review on Processing of Electric Arc 2023年9月20日 The basic oxygen furnace (BOF) process is the most widely used steelmaking process in the world, accounting for more than 70% of global steel production such as raw material selection, process control, His research focuses on Physicsbased and data driven modeling of metal processing, the application of AI and ML for manufacturing Toward learning steelmaking—A review on machine learning

Process metallurgy and datadriven prediction and feedback
2024年5月27日 The prediction and control of furnace heat indicators are of great importance for improving the heat levels and conditions of the complex and difficulttooperate hourclass delay blast furnace (BF) system In this work, a prediction and feedback model of furnace heat indicators based on the fusion of datadriven and BF ironmaking processes was proposed Iron processing Smelting, Refining, Alloying: The primary objective of iron making is to release iron from chemical combination with oxygen, and, since the blast furnace is much the most efficient process, it receives the most attention here Alternative methods known as direct reduction are used in over a score of countries, but less than 5 percent of iron is made this Iron processing Smelting, Refining, Alloying Britannica2024年8月28日 The conventional iron and steel industry (ISI), driven by coal utilization as its predominant feedstock, constitutes a substantial source of greenhouse gas emissions Hydrogen metallurgy presents the opportunity to mitigate carbon emissions in ISI from the origin Among hydrogen metallurgical approaches, the hydrogenbased direct reduction iron (HDRI) process Development and Application of HydrogenBased Direct Reduction Iron ProcessThis process is crucial in the production of iron and steel, where raw iron ore is transformed into molten iron through hightemperature heating, and impurities, known as slag, are separated Metallurgical furnaces play a pivotal role in the extraction of metals from ores, providing the basic materials for subsequent metal processingMetallurgical Industrial Furnaces: Types and Functions
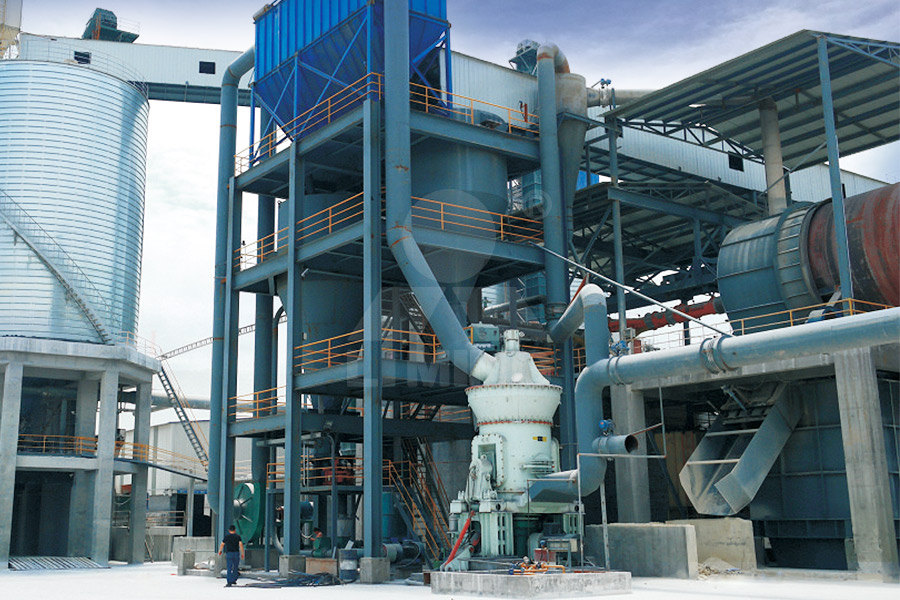
Blast Furnace Process Steel Museum
A blast furnace is a steel cylinder lined with refractory It operates continuously until the lining wears out, which takes many years to occur The term blast furnace comes from the blast of hot air that is blown into the lower part of the furnace at between 1400º to 2100ºF Molten iron is produced in a blast furnace by the following steps: 12019年9月3日 Industrially, the pyrometallurgical treatment of laterites is mostly accomplished with a wellestablished method, namely, the rotary kiln–electric arc furnace (RKEF) process, which includes (PDF) Nickel Laterite Smelting Processes and SomeFor general information about merchant pig iron, please visit the pig iron page Modern blast furnaces produce more than 10,000 tonnes per day Blast Furnace Process The blast furnace is a countercurrent gas/solids reactor in which the Pig iron blast furnace route International Iron 2020年7月15日 30th European Symposium on Computer Aided Process Engineering Pourya Azadi, Sebastian Engell, in Computer Aided Chemical Engineering, 2020 1 Introduction The ironmaking blast furnace (BF) is a very energyintensive metallurgical process and the prime route for steel production, from which about 70% of the world’s steel consumption is produced Blast Furnace Ironmaking an overview ScienceDirect Topics
.jpg)
Judgment of blast furnace irontapping status based on data
2023年8月1日 The selection of rate thresholds should accommodate most irontapping scenarios to ensure the universality and accuracy of the algorithm In the actual irontapping process, the irontapping rate often fluctuates within a certain range, and as long as v start meets the minimum value of this range, the start of irontapping can be accurately judged2023年3月27日 The prediction and control of furnace heat indicators are of great importance for improving the heat levels and conditions of the complex and difficulttooperate hourclass delay blast furnace (BF) system In this work, a prediction and feedback model of furnace heat indicators based on the fusion of datadriven and BF ironmaking processes was proposed Process metallurgy and datadriven prediction and feedback 2022年1月14日 In recent years, the recovery of the valuable metals from ironbearing solid waste from steel plant has been one of the most intensive research areas Dumping of electric arc furnace dust is an environmental concern, and recovery of valuable metals like iron, zinc, lead from EAFD and safe disposal of residue has got enough attention Evolution of improved and A Review on Processing of Electric Arc Furnace Dust (EAFD2023年11月15日 With the increasing demand for energy conservation and emission reduction, more attentions have been paid to the intelligentization, greenization and low carbonization during the transformation and upgrading of steelmaking plants Ladle furnace (LF) refining is one of the key procedures in steelmaking process and has been widely used in steelmaking plants for its Modeling of LF refining process: a review Journal of Iron
.jpg)
Mathematical Modeling of the Blast Furnace Process
2024年11月19日 furnace process, Doctor of Technical Sciences Zakharov Ivan Nikitich, in the laboratory of “Complex Processing of Mineral Raw Materials”, the processing complex iron ore This is because the experimental study of operating units and the development of new ones are associated with great financial, technological, and technical 2023年10月6日 The smelting process of blast furnace is carried out in the shaft furnace of a closed countercurrent reactor and heat exchanger The complex physical changes and chemical reactions are completed in the process of the countercurrent movement of the charge and gas in which the raw materials containing iron oxide (sinter, pellets, etc), coke, slag flux (limestone) Blast Furnace Ironmaking SpringerLink2023年8月31日 10 2 Direct Reduction Iron Process Fig 24 Rotary hearth furnace test and distribution diagram according to 3 h circle 3 h after the first tray is placed and 3 h before the last tray is taken out, the pellets are not magnetically separated The pellets in the middle timeDirect Reduction Iron Process Springer2022年9月28日 A behavior of zinc, lead, and iron during the processing of EAFD (electric arc furnace dust from steelmaking) by the promising method based on its calcination with lime was studied The chemical and mineralogical composition of the EAFD were analyzed in detail by Xray fluorescence, Xray diffraction, and Mössbauer analyses, as well as using methods of Characterization of Calcination Process of Electric Arc Furnace
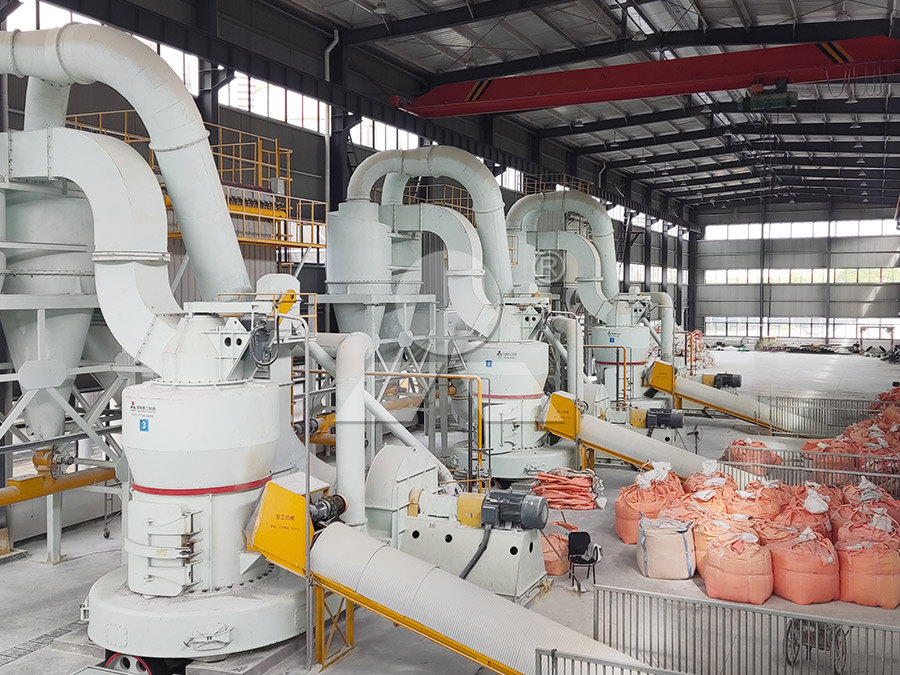
The Melting, Holding and Pouring Process Energy and
2016年5月24日 variety of paths of the molten iron from the melting furnace to the pouring location (Fig 1) Fig 1 Overview of cast iron melting and pouring processes As a matter of fact, cast iron materials are melted chiefly in cupola or inductiontype furnaces today while rotary furnaces are rarely used in this context any moreThe possibilities of conducting industrial experiments in furnaces for processing metallurgical slags are severely limited due to high process costs and measurement constraints of particular parameters during the operation of an EAF in the ferronickel processing process Equations for electric potential, momentum, and heat transfer were Process of Copper Slag Reduction in an Electric Furnace and 2016年9月16日 Although carburizing is a complicated process, it can be broken down into two main steps: carbon generation in the furnace and carbon diffusion into the workpiece The first step provides the source (carbon atoms) while the Carbon Diffusion and Carburizing Parameter 2023年9月12日 Today, no one process is solely used to process steel A blast furnace processes most iron ore, creating pig iron The basic oxygen process is used to create steel using the pig iron and electric arc is used to produce steel from plentiful scrap, although either method can process pig iron or scrap ironHistory of Steel Processing Materials Education (MatEdU)
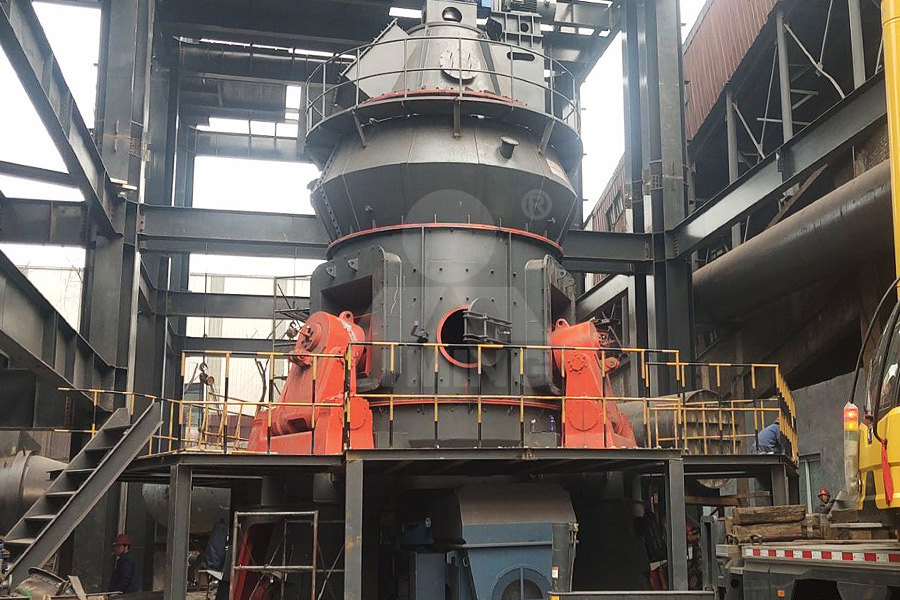
The six main steps of iron ore processing Multotec
When iron ore is extracted from a mine, it must undergo several processing stages Six steps to process iron ore 1 Screening We recommend that you begin by screening the iron ore to separate fine particles below the crusher’s CSS before the crushing stage A static screen is used to divert the fine particles for crushing Select Month 2016年4月8日 Blast furnaces are countercurrent chemical reactors, widely utilized in the ironmaking industry Hot reduction gases injected from lower regions of the furnace ascend, reacting with the descending burden Through this reaction process, iron ore is reduced into liquid iron that is tapped from the furnace hearth Due to the extremely harsh environment inside the Comprehensive Numerical Modeling of the Blast Furnace Ironmaking Process2017年3月24日 The present article reviews the sintering process that the mixture follows, once granulated, when it is loaded onto the sinter strand There, the sinter mixture is partially melted at a temperature between 13001480°C and undergoes a series of reactions that forms the sinter cake to be loaded into the blast furnace to produce pig ironIron Ore Sintering: Process: Mineral Processing and Extractive 2019年8月19日 The blast furnace and direct reduction processes have been the major iron production routes for various iron ores (ie goethite, hematite, magnetite, maghemite, siderite, etc) in the past few A review of ironmaking by direct reduction processes:
.jpg)
(PDF) Iron Ore Sintering: Raw Materials and Granulation
2016年10月28日 Sintering is an agglomeration process that fuses iron ore fines, fluxes, recycled products, slagforming elements and coke The purpose of sintering is to obtain a product with suitable 2010年5月1日 Furnace firing provides a large part of the heat for the process The heat for the process comes from the combustion of fuels The choice of furnace style and design is crucial for the best FURNACE SELECTION, SIZING AND TROUBLESHOOTING, Kolmetz Handbook 2023年4月5日 The blast furnace and direct reduction processes have been the major iron production routes for various iron ores (ie goethite, hematite, magnetite, maghemite, siderite, etc) in the past few decades, but the Recent Trends in the Technologies of the Direct 2022年8月23日 The blast furnace and direct reduction processes have been the major iron production routes for various iron ores (ie goethite, hematite, magnetite, maghemite, siderite, etc) in the past few (PDF) An Overview of the ReductionSmelting
.jpg)
(PDF) A Review on Processing of Electric Arc
2022年1月14日 Dumping of electric arc furnace dust is an environmental concern, and recovery of valuable metals like iron, zinc, lead from EAFD and safe disposal of residue has got enough attention2023年9月20日 The basic oxygen furnace (BOF) process is the most widely used steelmaking process in the world, accounting for more than 70% of global steel production such as raw material selection, process control, His research focuses on Physicsbased and data driven modeling of metal processing, the application of AI and ML for manufacturing Toward learning steelmaking—A review on machine learning 2024年5月27日 The prediction and control of furnace heat indicators are of great importance for improving the heat levels and conditions of the complex and difficulttooperate hourclass delay blast furnace (BF) system In this work, a prediction and feedback model of furnace heat indicators based on the fusion of datadriven and BF ironmaking processes was proposed Process metallurgy and datadriven prediction and feedback Iron processing Smelting, Refining, Alloying: The primary objective of iron making is to release iron from chemical combination with oxygen, and, since the blast furnace is much the most efficient process, it receives the most attention here Alternative methods known as direct reduction are used in over a score of countries, but less than 5 percent of iron is made this Iron processing Smelting, Refining, Alloying Britannica
.jpg)
Development and Application of HydrogenBased Direct Reduction Iron Process
2024年8月28日 The conventional iron and steel industry (ISI), driven by coal utilization as its predominant feedstock, constitutes a substantial source of greenhouse gas emissions Hydrogen metallurgy presents the opportunity to mitigate carbon emissions in ISI from the origin Among hydrogen metallurgical approaches, the hydrogenbased direct reduction iron (HDRI) process This process is crucial in the production of iron and steel, where raw iron ore is transformed into molten iron through hightemperature heating, and impurities, known as slag, are separated Metallurgical furnaces play a pivotal role in the extraction of metals from ores, providing the basic materials for subsequent metal processingMetallurgical Industrial Furnaces: Types and Functions A blast furnace is a steel cylinder lined with refractory It operates continuously until the lining wears out, which takes many years to occur The term blast furnace comes from the blast of hot air that is blown into the lower part of the furnace at between 1400º to 2100ºF Molten iron is produced in a blast furnace by the following steps: 1Blast Furnace Process Steel Museum2019年9月3日 Industrially, the pyrometallurgical treatment of laterites is mostly accomplished with a wellestablished method, namely, the rotary kiln–electric arc furnace (RKEF) process, which includes (PDF) Nickel Laterite Smelting Processes and Some