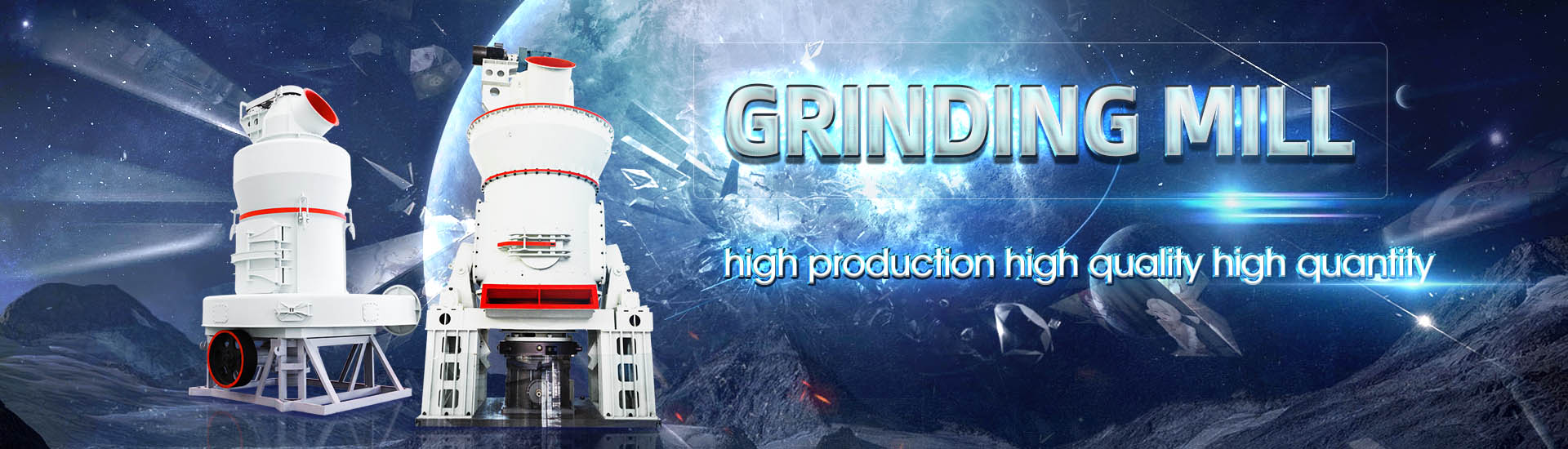
Calculation of blast furnace slag flushing water consumption
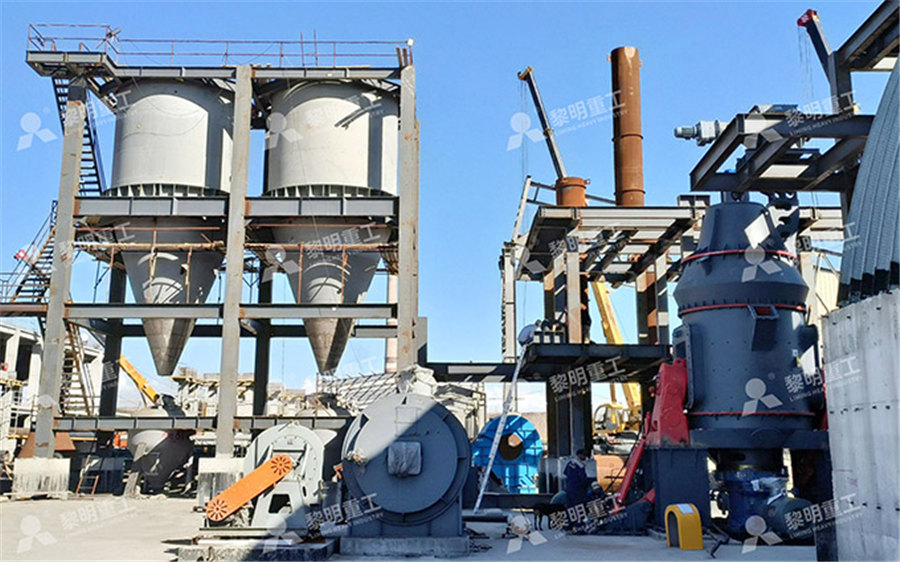
Full article: Comprehensive utilisation of blast furnace slag
2023年7月21日 The principle of the RASA method is that after the blast furnace slag has been water quenched in front of the furnace, the slagwater mixture is concentrated, filtered and 2024年7月1日 Physical recovery of waste heat from blast furnace slag (BFS) by a moving bed is a promising solution The heat recovery of BFS is mainly achieved through gas–solid heat Waste heat recovery of blast furnace slag in moving bed: 2014年3月1日 The results showed that for blast furnace slag flushing water at 100 °C, water temperature drops 15 °C per meter, about 093 kW electrical energy can be produced per Thermoelectric power generation driven by blast furnace slag This paper presents a method of utilizing waste heat of blast furnace slag flushing water for seawater desalination After the flash process, heat exchange process and heat repair RESEARCH ON APPLICATION OF HEAT OF BLAST FURNACE SLAG WATER
.jpg)
Development of Slag Flowability Prediction Formula for
In this study, the effects of MgO content, Al2O3 content, TiO2 content and C/S (=CaO/SiO2) on slag flowability are investigated for blast furnace (BF) operation The liquidus temperature and 2014年3月1日 The blast furnace (BF) slag waste heat was recovered by an integrated system stage by stage, which combined a physical and chemical method The water and coal Thermoelectric power generation driven by blast furnace slag flushing water2021年12月4日 On this basis, the BF slag is up to 247 million tons in 2014, corresponding to 11 million tons standard coal, approximating 140% of consumption in the BF process Generally, A Review of Granulation Process for Blast Furnace Slag2014年3月1日 The results showed that for blast furnace slag flushing water at 100 °C, water temperature drops 15 °C per meter, about 093 kW electrical energy can be produced per Thermoelectric power generation driven by blast furnace slag flushing water
.jpg)
Overall Utilization of TiExtraction Blast Furnace Slag as a
2021年7月26日 Tiextraction blast furnace slag (TEBFS) is the metallurgical solid waste generated during titanium extraction by hightemperature carbonization and lowtemperature 2016年6月1日 Slag mudtocement (MTC) technology was originally developed with slag as the cementing material is refers to the process where the blast furnace water quench slag is replaced by traditional Energy–environment–economy evaluations of commercial2020年3月29日 The ACBF slag collected from the blast furnace slag yard have coarser particle size with 16% of +65 mm, 18% of −65 + 40 mm, 40% of −40 + 20 mm, 12% of −20 + 10 mm and 13% of below 10 mm The received samples were reduced to particle size below 10 mm and the representative samples were taken for characterisation studiesUtilisation perspective on water quenched and aircooled blast furnace 2023年1月17日 The main trough of a blast furnace (BF) is a main passage for hot metal and molten slag transportation from the taphole to the torpedo and the slag handlingProlonging Campaign Life of Blast Furnace
.jpg)
Typical chemical composition of blast furnace slags
The low recycling for reuse of LS slag was mainly attributed to its volume instability ie disintegration of slag during cooling due to phase transformation and wideranging slag composition [20 2013年12月12日 Several numerical approaches have been proposed in the literature to simulate the behavior of modern blast furnaces: finite volume methods, datamining models, heat and mass balance models, and classical thermodynamic simulations Despite this, there is actually no efficient method for evaluating quickly optimal operating parameters of a blast furnace as a Process Simulation and Control Optimization of a Blast Furnace 2023年6月1日 Keywords: Slag flushing water, Water flashed, Heat exchange 1 INTRODUCTION The blast furnace produces iron melt and blast furnace slag at about 1500 °C At present, the main method to deal with the slag is the water quenching method This process produces a large amount of blast furnace slag flushing water with lowgrade heat energyJournals PDF Frontiers in Heat and Mass Transfer 2023年10月24日 42 Air blast method High speed and high pressure air plays a pivotal role to discharge the molten slag with a rapid cooling in this process, along with absorbing the sensible heat [4]A Review of Granulation Process for Blast Furnace Slag
.jpg)
Waste Heat Recovery from Blast Furnace Slag by
2012年7月31日 such as excess water consumption and pollution of air and water2 Additionally, extra energy is necessary to dry the slag to produce cement To recover the sensible heat of BF slag, three key problems should be considered: (I) the dry granulation of BF slag without consuming water, (II) increasing the recovery rate of the waste heat effi2022年8月1日 The annual production of titaniumbearing BFS is estimated to be around 3 million tons [10]The accumulative amount of titaniumbearing BFS in the Panzhihua area of China is up to an astonishing 70 million tons [11]BFS is classified into two types based on the slag cooling method: aircooled BFS and waterquenched BFS [12]The aircooled BFS is black with a An approach towards utilization of waterquenched blast furnace slag 2022年7月18日 When the slag from the blast furnace is molten, it is swiftly cooled with strong water jets, which transform it into GGBS, a fine, granular and glassy substance Figure 2 depictsA Comprehensive Review on the Ground Granulated Blast Furnace Slag 2012年7月31日 Blast furnace (BF) slag, which is the main byproduct in the ironmaking process, contains large amounts of sensible heat To recover the heat, a new waste heatrecovery system—granulating molten BF slag by rotary multinozzles cup atomizer and pyrolyzing printed circuited board with obtained hot BF slag particle—was proposed in this study The feasibility Waste Heat Recovery from Blast Furnace Slag by Chemical
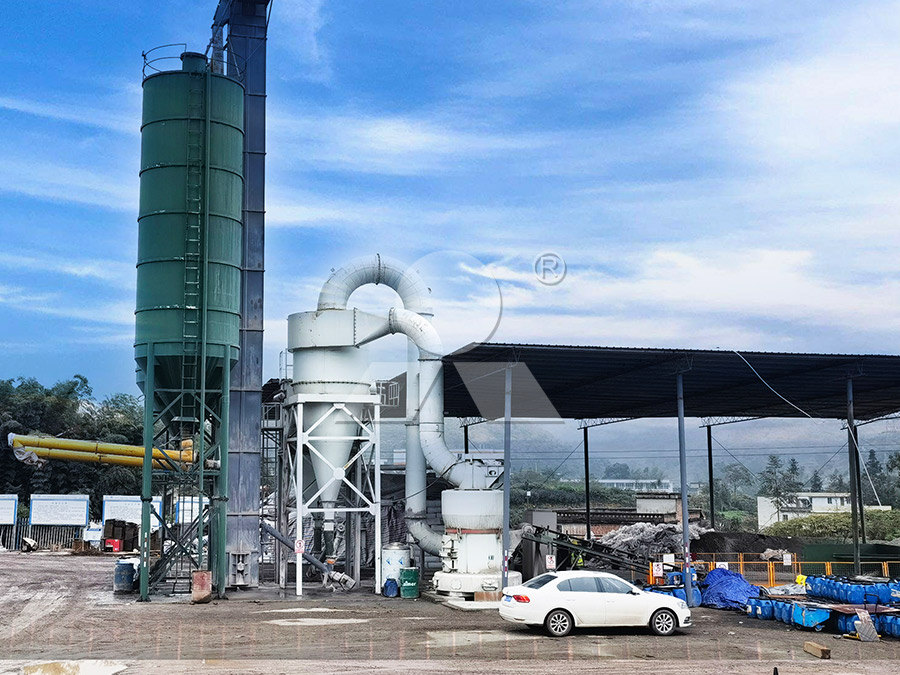
How blast rate variation affects dynamic infurnace
The blast furnace (BF) is the most energyconsuming and important reactor in ironmaking industries at present (ie, conventional BFs) and in the near term (ie, novel BFs) [1]In the BF process, iron ore and coke are loaded alternately at the furnace top, and hot blast is introduced into the lower part of the furnace along the circumference through the tuyeres, generating the 2023年12月20日 BF slag waste heat Abbreviations BF slag Blast furnace slag EXL Exergy loss RCA Rotary cup atomizer List of Symbols T Temperature of object (K) T 0 Temperature of ambient (K) DS Entropy change of Thermodynamic Analysis of Blast Furnace Slag Waste 2024年6月26日 isation of blast furnace slag and improve the economic benefits of the steel industry, this paper will introduce the current status quo of comprehensive utilisation of blast furnace slag from the current blast furnace slag sensible heat recovery of molten steel 1 Overview of blast furnace slag treatment process in ChinaComprehensive utilisation of blast furnace slag Taylor 2016年8月15日 The heat of the flushing water and its dosage can be, respectively, expressed as (34) Q fw = λ fw m slag h slag (35) m fw = λ fw m slag h slag c fw (T fw,out − T fw,in) where T fw,in and T fw,out represent the temperatures of flushing water before and after the flushing process, c fw represent the specific heat capacity of Constructal design of a blast furnace ironmaking process
.jpg)
Life cycle and economic assessment of multistage blast furnace slag
2018年1月1日 As we all know, as a main kind of byproduct, BF slag was exhausted at extremely 1773 K–1873 K and thus, the energy about 1700 MJ/t slag, corresponded to 130% of consumption in the blast furnace process was carried by the slag [7] Now the major BF slag waste heat recovery method was water quenching method (including OCP, INBA, TYNA and 2016年5月6日 The Sierraleone ore has high alumina content (about 70 mass pct) and low silica content (about 17 mass pct) Figure 1 clearly shows that the slag composition and volume have undergone drastic modifications compared with the other raw materials If the high Al 2 O 3 ore is extensively used in a blast furnace (BF), great deviation will form from the usual slag system to Transition of Blast Furnace Slag from SilicatesBased to Aluminates 2017年8月12日 Results are provided for calculation of the predicted blast furnace operating regime using converter slag in the ironore part of the charge without implementing additional measures with the aim of evaluating its effect on process indices Introduction into a blast furnace charge of fractionated converter slag may be performed in order to increase slag magnesia Effect of Converter Slag Consumption on Blast Furnace2021年7月26日 Tiextraction blast furnace slag (TEBFS) is the metallurgical solid waste generated during titanium extraction by hightemperature carbonization and lowtemperature selective chlorination process in China The high chlorine content in slag restricts its largescale utilization in engineering materials To solve this problem, this study comprehensively Overall Utilization of TiExtraction Blast Furnace Slag as a
.jpg)
Vapor recovery blast furnace slag flushing water system
The invention provides a vapor recovery blast furnace slag flushing water system A gas collecting hood with a spraying system is arranged at the upper part of a slag producing tank in the system; and an external sucking hood with an emptying pipe is arranged at an opening of the gas collecting hood By adopting the system, a micro positive pressure state inside a granulation DOI: 101016/JENERGY201402018 Corpus ID: ; Thermoelectric power generation driven by blast furnace slag flushing water @article{Meng2014ThermoelectricPG, title={Thermoelectric power generation driven by blast furnace slag flushing water}, author={Fankai Meng and Lingen Chen and Fengrui Sun and Bo Yang}, journal={Energy}, Thermoelectric power generation driven by blast furnace slag flushing water2016年8月15日 Based on Ref [11], Xiong et al [12] performed numerical calculation for a twostage thermoelectric energy recovering system driven by the waste heat of BF slag flushing water, and analyzed the effects of the main parameters on Constructal design of a blast furnace ironmaking process based 2016年1月1日 Molten slags of blast furnace is a second resources with great value of 1600~1 800 MJ sensible heat per ton At present, waterquenching process plays a leading role in recovering waste heat of (PDF) A Review of Granulation Process for Blast
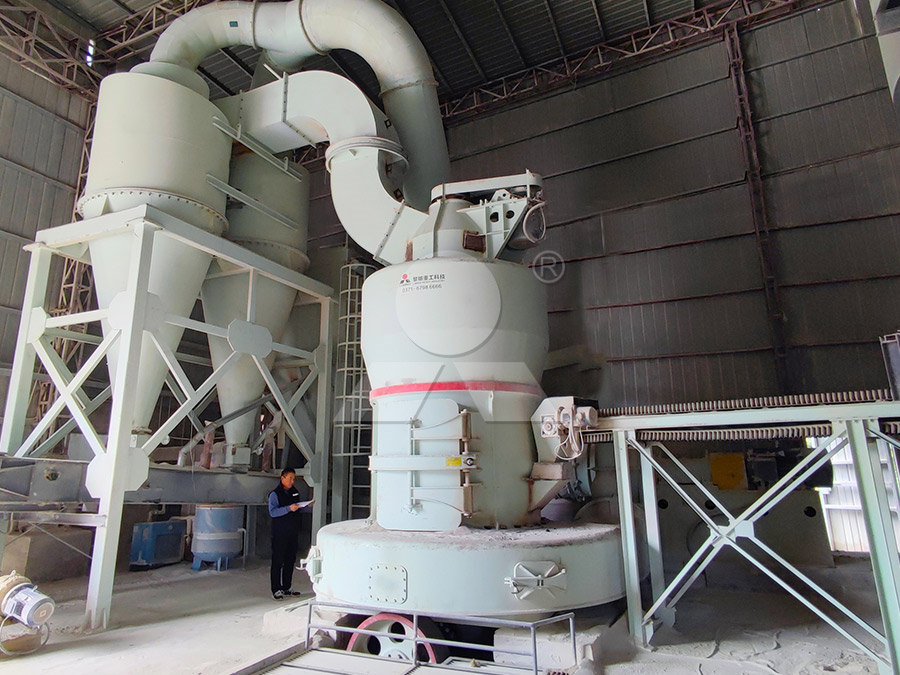
What is Blast Furnace Slag and How to Process It?
2022年2月26日 Blast furnace slag can be processed into the following materials by various processes In China, blast furnace slag is usually processed into water slag, slag gravel, expanded slag and slag beadsWater slag is the process of putting the hotmelt blast furnace slag into water for rapid cooling, which mainly includes slag pool water quenching or furnace front 2024年4月15日 Raw material with a high Al2O3 content has led to an increase in the Al2O3 content in blast furnace slag, which has affected the normal operation of a blast furnace The exergy analysis method is an important method for studying the energy utilization of highalumina blast furnace smelting In this paper, to investigate the impact of slag composition on exergy Optimization of HighAlumina Blast Furnace Slag Based on 2023年8月26日 The large amount of heat absorbed by direct reduction in the belly means that higher tuyere combustion temperature is needed to maintain sufficient heat supply When copper slag is reduced by blast furnace process, there are differences between blast furnace design, charge layer structure and temperature distribution and traditional blast furnaceCase Analysis of Blast Furnace Consumption Technology and 2014年12月1日 Calculation results show that the maximum power output and maximum efficiency of the system can, respectively, reach to 114 kW and 420% for inlet temperature of blast furnace slag water at 150 °C, they are respectively 162% and 578% improvements than those of the system with inlet temperature of blast furnace slag water at 100 °CModeling and performance analysis of a twostage
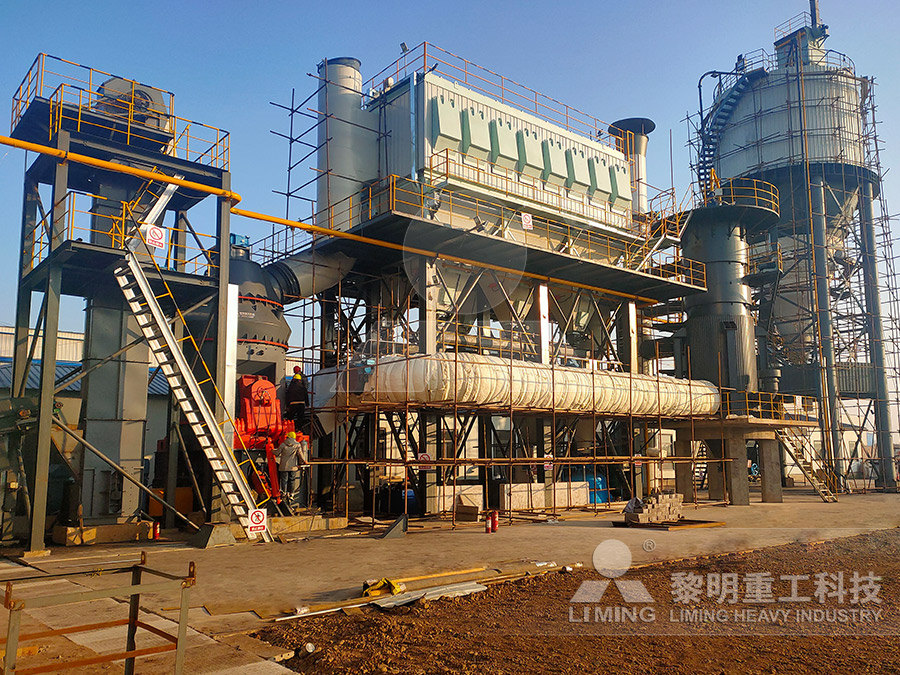
Calculation and Analysis of the Relationship Between the
2019年7月13日 The arc efficiency and specific power consumption were calculated and analyzed for the small (15 to 20 tons) and large (100 to 120 tons) capacity electric arc furnaces In the smallcapacity furnaces, the increased specific power consumption for melting the furnace charge (475 to 500 kW h/t) is associated with low arc efficiency (055 to 057) In the large 2023年10月6日 The smelting process of blast furnace is carried out in the shaft furnace of a closed countercurrent reactor and heat exchanger The complex physical changes and chemical reactions are completed in the process of the countercurrent movement of the charge and gas in which the raw materials containing iron oxide (sinter, pellets, etc), coke, slag flux (limestone) Blast Furnace Ironmaking SpringerLink2015年4月14日 The blast furnace (BF) slag waste heat was recovered by an integrated system stage by stage, which combined a physical and chemical method The water and coal gasification reactions were used to recover the heat in the system Based on the first and second law of thermodynamics, the thermodynamic analysis of the system was carried out by the Thermodynamic Analysis of Blast Furnace Slag Waste Heat2016年6月1日 Slag mudtocement (MTC) technology was originally developed with slag as the cementing material is refers to the process where the blast furnace water quench slag is replaced by traditional Energy–environment–economy evaluations of commercial
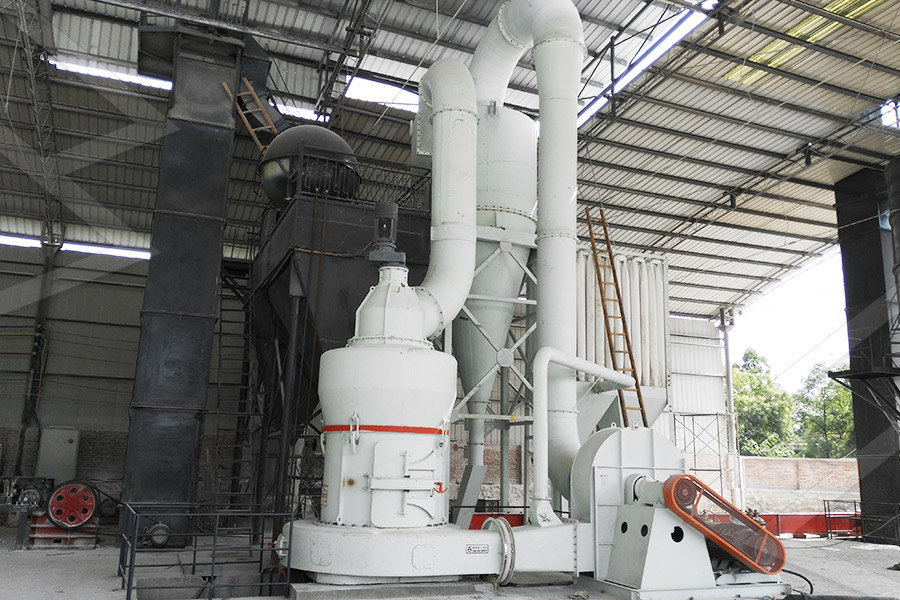
Utilisation perspective on water quenched and aircooled blast furnace
2020年3月29日 The ACBF slag collected from the blast furnace slag yard have coarser particle size with 16% of +65 mm, 18% of −65 + 40 mm, 40% of −40 + 20 mm, 12% of −20 + 10 mm and 13% of below 10 mm The received samples were reduced to particle size below 10 mm and the representative samples were taken for characterisation studies2023年1月17日 The main trough of a blast furnace (BF) is a main passage for hot metal and molten slag transportation from the taphole to the torpedo and the slag handlingProlonging Campaign Life of Blast Furnace The low recycling for reuse of LS slag was mainly attributed to its volume instability ie disintegration of slag during cooling due to phase transformation and wideranging slag composition [20 Typical chemical composition of blast furnace slags2013年12月12日 Several numerical approaches have been proposed in the literature to simulate the behavior of modern blast furnaces: finite volume methods, datamining models, heat and mass balance models, and classical thermodynamic simulations Despite this, there is actually no efficient method for evaluating quickly optimal operating parameters of a blast furnace as a Process Simulation and Control Optimization of a Blast Furnace
.jpg)
Journals PDF Frontiers in Heat and Mass Transfer
2023年6月1日 Keywords: Slag flushing water, Water flashed, Heat exchange 1 INTRODUCTION The blast furnace produces iron melt and blast furnace slag at about 1500 °C At present, the main method to deal with the slag is the water quenching method This process produces a large amount of blast furnace slag flushing water with lowgrade heat energy2023年10月24日 42 Air blast method High speed and high pressure air plays a pivotal role to discharge the molten slag with a rapid cooling in this process, along with absorbing the sensible heat [4]A Review of Granulation Process for Blast Furnace Slag2012年7月31日 such as excess water consumption and pollution of air and water2 Additionally, extra energy is necessary to dry the slag to produce cement To recover the sensible heat of BF slag, three key problems should be considered: (I) the dry granulation of BF slag without consuming water, (II) increasing the recovery rate of the waste heat effiWaste Heat Recovery from Blast Furnace Slag by 2022年8月1日 The annual production of titaniumbearing BFS is estimated to be around 3 million tons [10]The accumulative amount of titaniumbearing BFS in the Panzhihua area of China is up to an astonishing 70 million tons [11]BFS is classified into two types based on the slag cooling method: aircooled BFS and waterquenched BFS [12]The aircooled BFS is black with a An approach towards utilization of waterquenched blast furnace slag
.jpg)
A Comprehensive Review on the Ground Granulated Blast Furnace Slag
2022年7月18日 When the slag from the blast furnace is molten, it is swiftly cooled with strong water jets, which transform it into GGBS, a fine, granular and glassy substance Figure 2 depicts