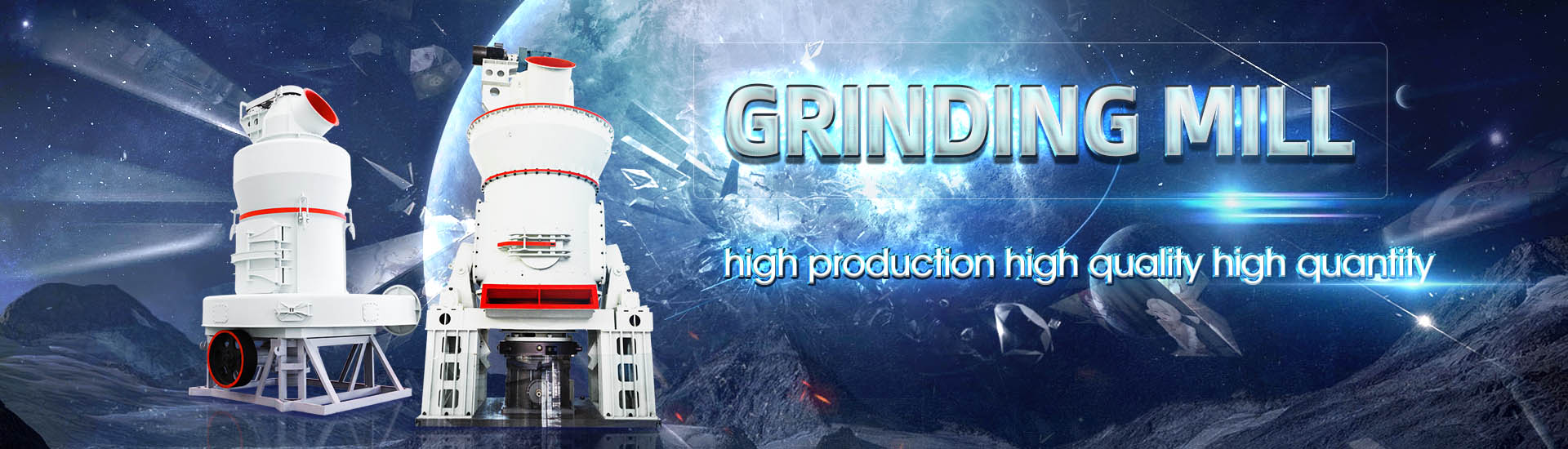
Desulfurization double circuit process
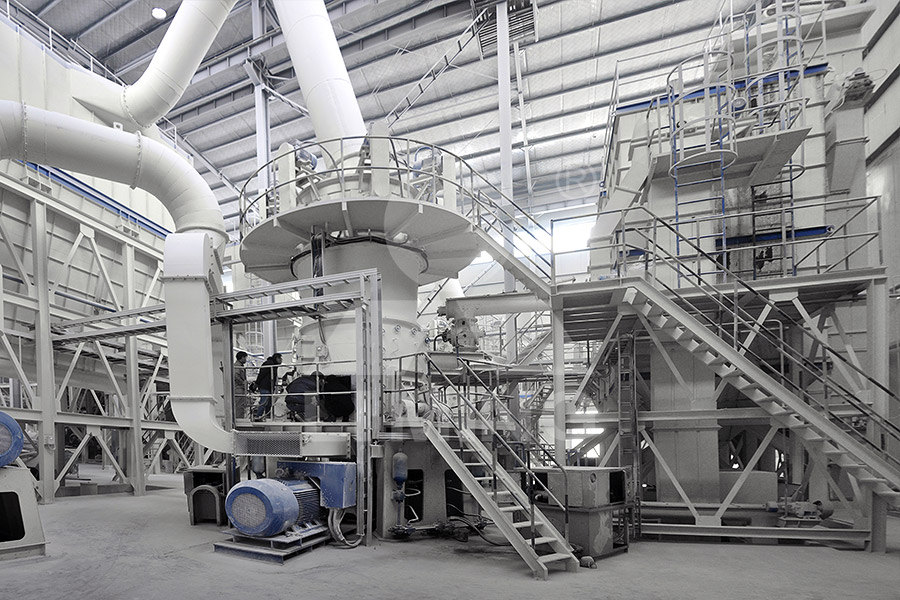
(PDF) Desulfurization techniques process and
2022年7月11日 Due to the most recent environmental requirements, wide desulfurization has become an increasingly important way to obtain ultraclean fuels for transportation of less than 15 ppmw of sulfur,2024年2月5日 Herein, we propose a gasliquid flow electrocatalysis system that couples H 2 S oxidation and O 2 reduction processes to effectively recover sulfur and H 2 O 2 with low Highlyefficient natural gas desulfurization and simultaneous 2022年7月11日 a deep desulfurization process for light oil by photosensitized oxidation using a triplet photosensitizer and hydrogen peroxide in an oil/water twophase liquidliquid extraction system,Desulfurization techniques process and future 2024年6月1日 Oxidative desulfurization (ODS) has emerged as a prominent technique for the removal of sulfur compounds from fuels, aiming to comply with stringent environmental Efficient and promising oxidative desulfurization of fuel
G[R.jpg)
Desulphurisation an overview ScienceDirect Topics
Desulfurization is the process to solidify the sulfur in the coal, thereby preventing the generation of SO 2 during coal combustion [76,77] Currently, various desulfurization methods have been 2019年3月13日 Most coalfired power plants in China use wet flue gas desulfurization (WFGD) as the main method for SO 2 removal Presently, the operating of WFGD lacks accurate modeling method to predict outlet Modeling and optimization of wet flue gas 2023年5月10日 As a novel desulfurization method, we developed piezocatalysts that do not require adding any oxidants and can be performed at room temperature A microwave method Studying the mechanism and kinetics of fuel desulfurization Among the desulfurization processes, the oxidative desulfurization (ODS) process is a promising method to achieve very low and nearzero sulfur content of the fuel In this process, sulfur Insights to the oxidative desulfurization process of fossil
.jpg)
Recycle Performance of Heterogeneous Catalyst
2023年12月11日 Recycle Performance of Heterogeneous Catalyst Metal OxidesBased Layered Double Hydroxide for Oxidative Desulfurization Process of 4methyldibenzothiophene The desulfurization of oil must be resolved as 2021年4月1日 In pervaporation desulfurization, dense and nonporous polymeric membranes separate the sulfur compounds from other hydrocarbons based on their solubility, affinity, and diffusivity [18] Fig 5 showed a schematic diagram of the pervaporation desulfurization process The sulfur compounds in the vapor phase, first absorb in polymer membrane and Review on recent advances in adsorptive desulfurization2024年1月1日 The Kevitsa concentrator employs a Cu–Ni fractional selective flotation circuit with a desulfurization circuit at the end of the process The original flotation circuit is a typical conventional polymetallic ore flotation (See Fig 12) where copper is concentrated in the first circuit, and this is followed by a nickel flotation circuit Two Insights into the design of polymetallic ore flotation circuits 2017年5月16日 Keywords: Flue Gas Desulfurization, FGD sytem design, SO 2 removal, limestone scrubbing, flue gases 1 Introduction 1The term flue gas desulfurization has traditionally referred to wet scrubbers that remove sulphur dioxide (SO 2) emissions from large boilers (mainly coal and oil fired combustion) However, because of theAnalytical Investigation and Design of Flue Gas
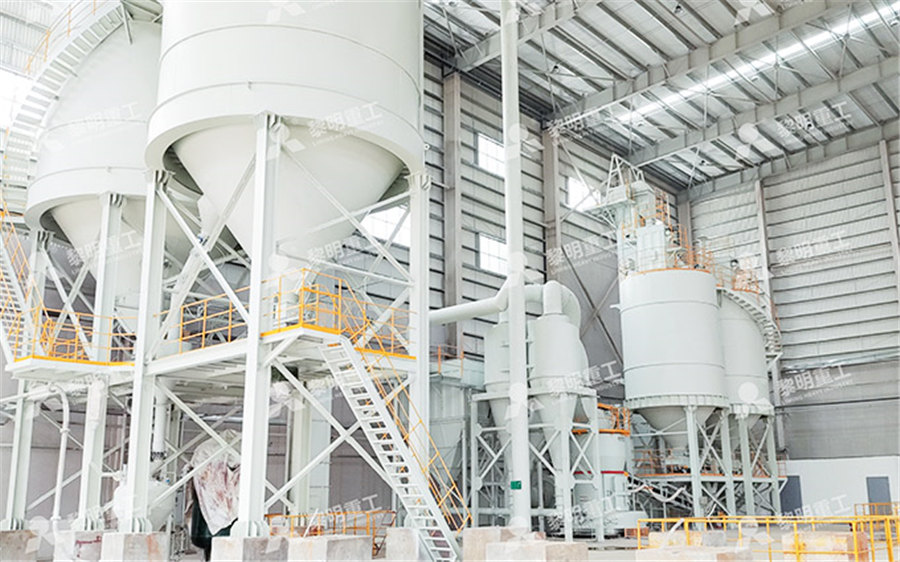
Recent advances in process and materials for dry desulfurization
Currently, desulfurization technologies can be categorized into three main types: wet flue gas desulfurization (FGD) [11], [12], [13], semidry desulfurization [14] and dry desulfurization [15]Wet flue gas desulfurization is widely employed in largescale desulfurization processes due to its high efficiency and low energy consumption [16]However, it poses a significant environmental 2019年7月13日 With the increasingly prominent global energy and environmental problems, more and more enterprises have been required to desulfurize the exhausted gases Different enterprises have different demands for the desulfurization process, thus the choice of desulfurization process methods has become a focus of attention Since the evaluation of the Method of Desulfurization Process Selection Based on DOI: 101016/JCEP201105008 Corpus ID: ; Removal of fine particles by heterogeneous condensation in the doublealkali desulfurization process @article{Bao2011RemovalOF, title={Removal of fine particles by heterogeneous condensation in the doublealkali desulfurization process}, author={Jingjing Bao and Linjun Yang and Bin Lu Removal of fine particles by heterogeneous condensation in the double 2011年8月1日 Removal of fine particles by heterogeneous condensation in the rotatingstreamtray scrubber was investigated experimentally for the doublealkali desulfurization process in this paperRemoval of fine particles by heterogeneous condensation in the double
.jpg)
(PDF) Comparison of flue Gas Desulfurization Technologies
2018年10月15日 The double alkali process is widely us ed in China because of its sim ple process, good operation stability, high desulfurization efficiency and low desulfurization cost2019年3月13日 PSO with a penalty function algorithm is applied to improve the economy of desulfurization process Aimed at the minimization of operating cost, the operating parameters, including lime slurry pH, temperature, lime slurry density, and number of circulating pumps in operation, are optimized Circuits Syst Signal Process 33 (open in a new Modeling and optimization of wet flue gas desulfurization 2023年10月10日 Recycle Performance of Heterogeneous Catalyst Metal OxidesBased Layered Double Hydroxide for Oxidative Desulfurization Process of 4methyldibenzothiophene October 2023;Recycle Performance of Heterogeneous Catalyst 2011年8月1日 Recently, the doublealkali desulfurization process is widely applied in cleaning of flue gas from coalfired boiler and industrial furnace with different scale due to various advantages, such as high desulfurization efficiency and operation reliability, low engineering investment and operation cost [10], [11]Removal of fine particles by heterogeneous condensation in the double
.jpg)
An evaluation of desulfurization technologies for
The current industrial method for removal of sulfur from fuels is hydrodesulfurization (HDS), which is a high temperature, high pressure catalytic process This makes HDS a very costly option for deep desulfurization 2024年11月8日 Desulfurization gypsum is a byproduct of chemical recovery of sulfur from flue gas in thermal power plants to reduce air pollution an equivalent circuit model was established based on the microstructural changes during the hardening process to analyse the patterns of the AC impedance characteristics during the hardening of the BSAC mortar Effect of desulfurization gypsum on alternatingcurrent Figure1 is a typical limestonegypsum desulfurization process In the whole desulfurization process, the alkaline absorbent slurry reacts with flue gas in the spray tower, so that SO2 contacts water and gets dilute acid, and then neutralizes with RI)OXH*DVLQKLQD Emission Transformation of Coal 2023年10月14日 analysis of the copper and nickel concentration process of the Boliden Kevitsa mine The problem was solved in three ways: oneatthetime optimal design of copper and nickel circuits, simultaneous optimal design of copper and nickel circuits, and optimal design of one circuit for both copper and nickel recoveries Figure 1 Methodology 3 ResultsOn the sustainable design of polymetallic flotation circuits
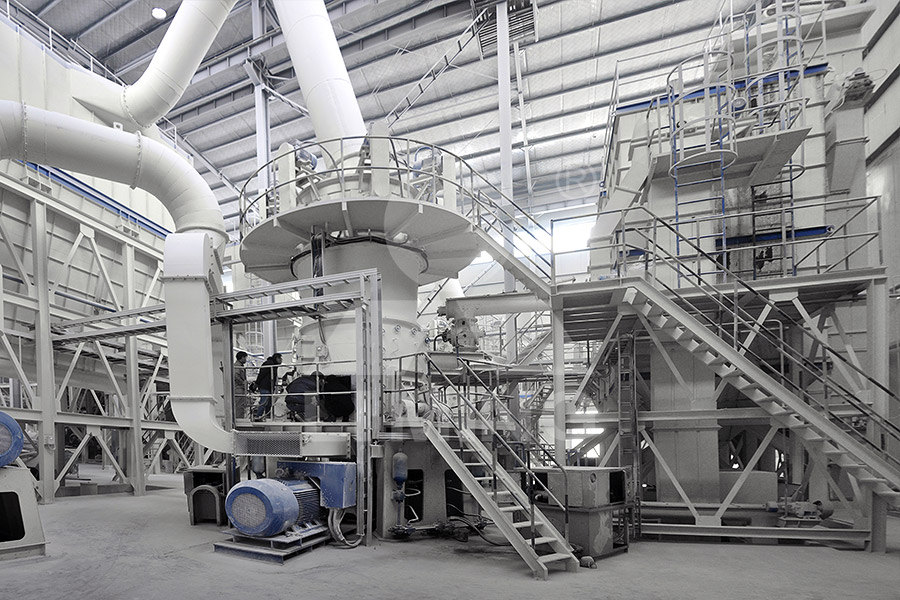
A critical review on the chelatediron desulfurization process
2024年5月1日 The desulfurization process of HCO was carried out by implementing a batch adsorption desulfurization process with AC as an adsorbent The sorbent activated carbon (AC) was characterized2000年7月31日 Dry Flue Gas Desulfurization Technology Dry FGD technology includes lime or limestone spray drying; dry sorbent injection, including furnace, economizer, duct, and hybrid methods; and circulating fluidizedbed scrubbers The Claus process is commonly used in oil refinery for converting gaseous H 2 S into molten sulfur by two main steps Dry Flue Gas Desulfurisation Technology ScienceDirect2017年7月1日 The most common types of FGD system are based on the contact between the flue gases and an alkaline sorbent such as lime or limestone (Wang et al, 2005)Furthermore, the major types of largescale power plant FGD systems include (i) spray towers, (ii) spray dryers and (iii) dry sorbent injection systems (Song et al, 2012)These FGD systems can achieve about Enhancing the recovery of gypsum in limestonebased wet 2024年1月10日 Flue gas desulfurization (FGD) is a critical process for reducing sulfur dioxide (SO2) emissions from industrial sources, particularly power plants This research uses calcium silicate absorbent Modeling based on machine learning to investigate flue gas
.jpg)
FlueGas Desulphurization an overview ScienceDirect Topics
Fluegas desulfurization processes can be classified as oncethrough or regenerable, depending on how the sorbent is treated after it has sorbed SO 2 or how the generated solids by the process are handled (Srivastava and Jozewicz, 2001; US EPA, 2003c; Jafarinejad, 2016a) In oncethrough technologies, the spent sorbent is disposed of as a 2012年3月1日 Strategies for heavy oil desulfurization were evaluated by reviewing desulfurization literature and critically assessing the viability of the various methods for heavy oil The desulfurization methods including Desulfurization of heavy oil Applied 2011年7月11日 The influencing factors of flue gas desulfurization rate by using both sodium hydroxide and steel slag as desulfurization agents were studied in bubbling reactor The results exhibited that the desulfurization rate can remain over 80% for long time under the optimum desulfurization conditions: reaction time was 2 h, steel slag amount was 40 g, SO2 inlet Study of NaOHsteel slag double alkali sintering flue gas 2011年5月14日 Removal of fine particles by heterogeneous condensation in the rotatingstreamtray scrubber was investigated experimentally for the doublealkali desulfurization process in this paper A supersaturated vapor phase, necessary for condensational growth Removal of fine particles by heterogeneous condensation in
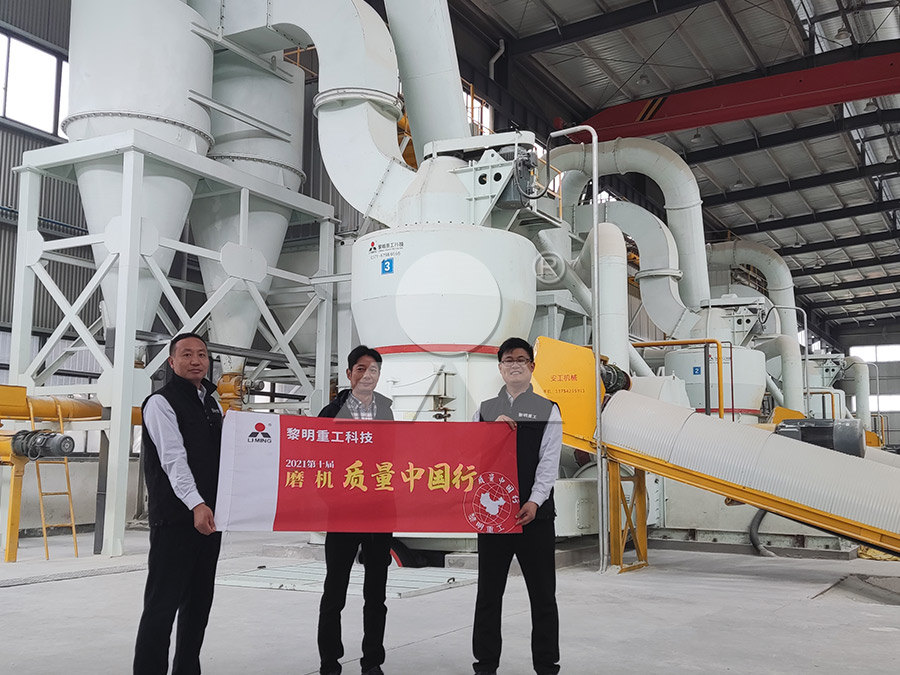
Research progress on desulfurization technology of high
2022年1月6日 As the mainstreams of bauxite desulfurization technologies, the bauxite predesulfurization (roasting, electrochemistry, biology, flotation, etc) and Bayer process desulfurization (oxidation and 2022年11月18日 The kinetics of carbide slag desulfurization process conforms to pseudorstorder kinetics, and the sulfur content of calcium carbide slag reaches to 1000 mgSO 2 g−1 A project demonstration was carried out in the gold smelting Tielu Plant of Zhenyuan Huashuo Precious Metals Development Co,Desulphurization mechanism and engineering practice 2021年11月1日 Flue gas desulfurized gypsum mainly comes from thermal power plants, smelters, and largeenterprise boilers, and contains industrial byproducts produced through a wet desulfurization combustion process, where SO 2 gas and lime slurry react under strong oxidation conditions The main component of this gypsum is calcium sulfate dihydrate, which also Production and resource utilization of flue gas desulfurized 2023年3月1日 Improving the quality of ammonium sulfate produced from the flue gas desulfurization process by using ammonium persulfate Author links open overlay panel Haoran Xu a b c, Tian Wang a b c Removal of fine particles by heterogeneous condensation in the doublealkali desulfurization process Chem Eng Process, 50 (8) (2011), pp 828835, 10 Improving the quality of ammonium sulfate produced from
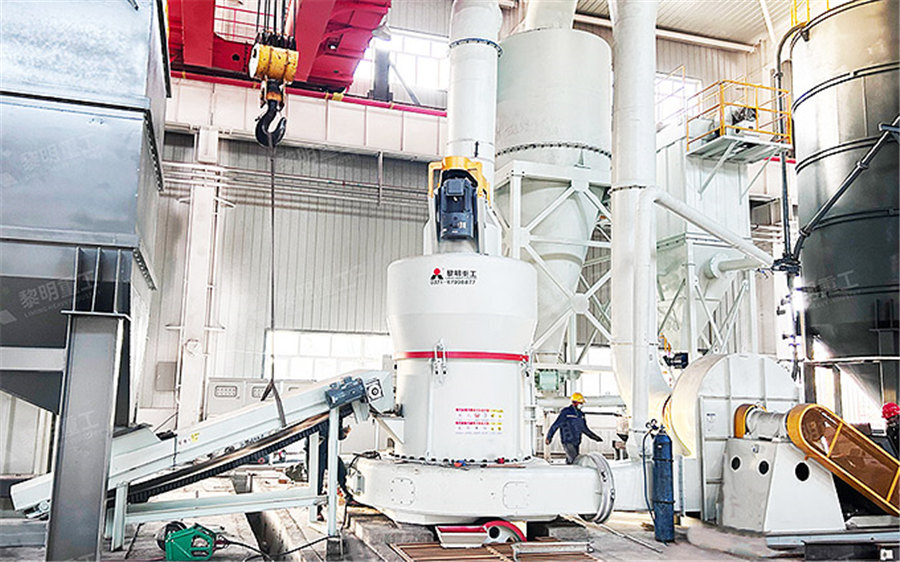
Study on Optimization of natural gas desulfurization
2017年8月23日 Fig 1 Process of DE acidification by MDEA 3 Simulation of desulfurization process Cycle volume is preliminary designed by using empirical formula and internal formula of HYSYS After simulating the technological process, the concentration and cycle volume of MDEA lean liquid are optimized on the basis of theoretical calculation2023年10月16日 Desulfurization Process of 4methyldibenzothiophene Nur Ahmad1,2, R Rohmatullaili1, Yulizah Hanifah1,2, Sahrul Wibiyan2, Recycle Performance of Heterogeneous Catalyst Metal OxidesBased Layered Double Hydroxide for Oxidative Desulfurization Process of 4methyldibenzothiophene Recycle Performance of Heterogeneous Catalyst Metal 2023年12月11日 Recycle Performance of Heterogeneous Catalyst Metal OxidesBased Layered Double Hydroxide for Oxidative Desulfurization Process of 4methyldibenzothiophene The desulfurization of oil must be resolved as Recycle Performance of Heterogeneous Catalyst 2021年4月1日 In pervaporation desulfurization, dense and nonporous polymeric membranes separate the sulfur compounds from other hydrocarbons based on their solubility, affinity, and diffusivity [18] Fig 5 showed a schematic diagram of the pervaporation desulfurization process The sulfur compounds in the vapor phase, first absorb in polymer membrane and Review on recent advances in adsorptive desulfurization
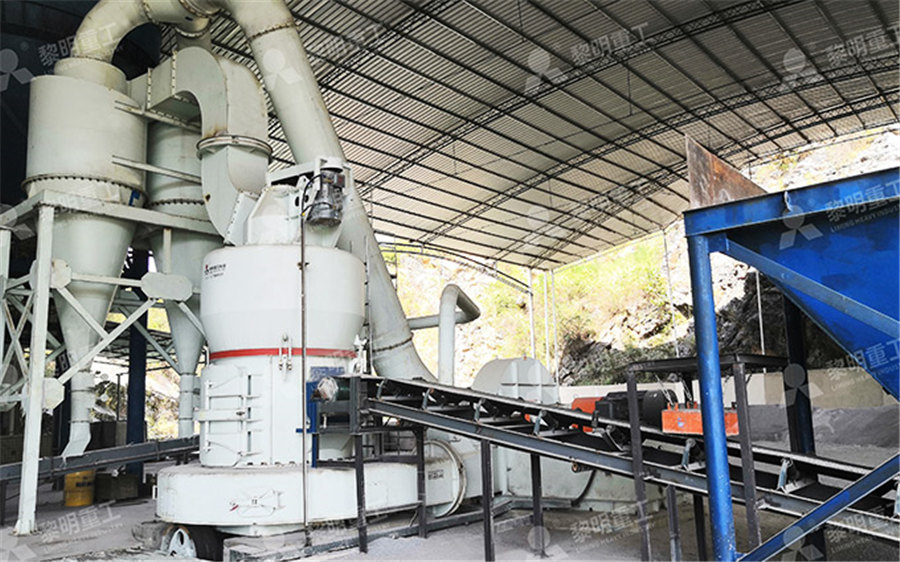
Insights into the design of polymetallic ore flotation circuits
2024年1月1日 The Kevitsa concentrator employs a Cu–Ni fractional selective flotation circuit with a desulfurization circuit at the end of the process The original flotation circuit is a typical conventional polymetallic ore flotation (See Fig 12) where copper is concentrated in the first circuit, and this is followed by a nickel flotation circuit Two 2017年5月16日 Keywords: Flue Gas Desulfurization, FGD sytem design, SO 2 removal, limestone scrubbing, flue gases 1 Introduction 1The term flue gas desulfurization has traditionally referred to wet scrubbers that remove sulphur dioxide (SO 2) emissions from large boilers (mainly coal and oil fired combustion) However, because of theAnalytical Investigation and Design of Flue Gas Currently, desulfurization technologies can be categorized into three main types: wet flue gas desulfurization (FGD) [11], [12], [13], semidry desulfurization [14] and dry desulfurization [15]Wet flue gas desulfurization is widely employed in largescale desulfurization processes due to its high efficiency and low energy consumption [16]However, it poses a significant environmental Recent advances in process and materials for dry desulfurization 2019年7月13日 With the increasingly prominent global energy and environmental problems, more and more enterprises have been required to desulfurize the exhausted gases Different enterprises have different demands for the desulfurization process, thus the choice of desulfurization process methods has become a focus of attention Since the evaluation of the Method of Desulfurization Process Selection Based on
.jpg)
Removal of fine particles by heterogeneous condensation in the double
DOI: 101016/JCEP201105008 Corpus ID: ; Removal of fine particles by heterogeneous condensation in the doublealkali desulfurization process @article{Bao2011RemovalOF, title={Removal of fine particles by heterogeneous condensation in the doublealkali desulfurization process}, author={Jingjing Bao and Linjun Yang and Bin Lu 2011年8月1日 Removal of fine particles by heterogeneous condensation in the rotatingstreamtray scrubber was investigated experimentally for the doublealkali desulfurization process in this paperRemoval of fine particles by heterogeneous condensation in the double 2018年10月15日 The double alkali process is widely us ed in China because of its sim ple process, good operation stability, high desulfurization efficiency and low desulfurization cost(PDF) Comparison of flue Gas Desulfurization Technologies2019年3月13日 PSO with a penalty function algorithm is applied to improve the economy of desulfurization process Aimed at the minimization of operating cost, the operating parameters, including lime slurry pH, temperature, lime slurry density, and number of circulating pumps in operation, are optimized Circuits Syst Signal Process 33 (open in a new Modeling and optimization of wet flue gas desulfurization