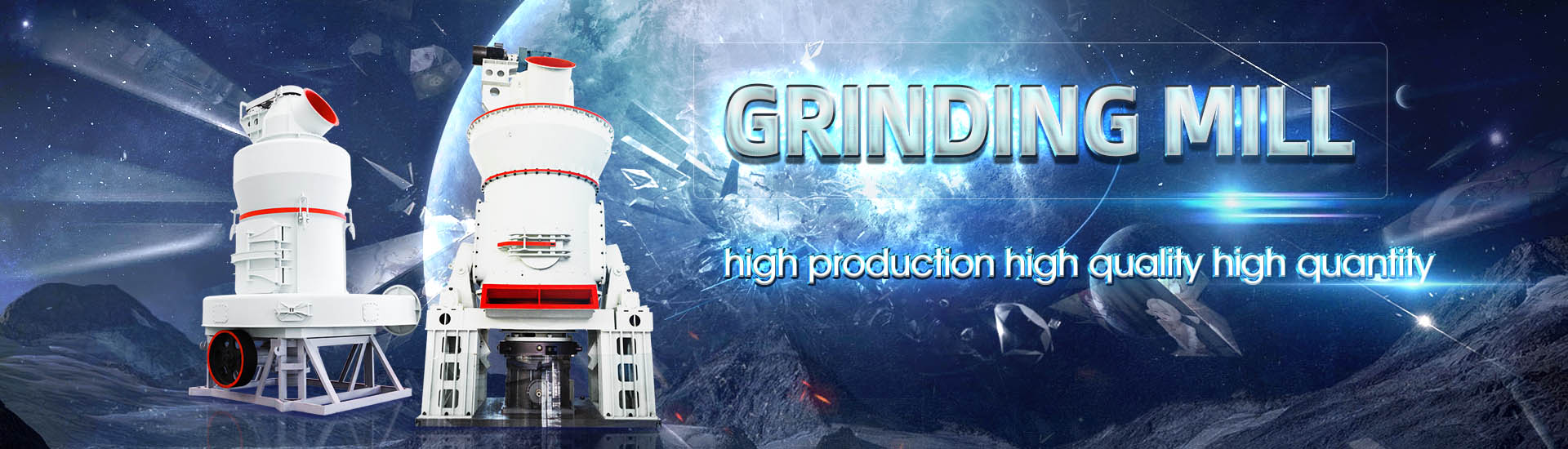
What is the frictiondriven ring roller mill
.jpg)
Roller Mill Springer
2023年7月4日 Roller mill is a type of grinding equipment for crushing materials by pressure between two or more rolling surfaces or between rolling grinding bodies (balls, rollers) and a track (plane, ring, and table)2024年9月15日 The rolling mill has a power capacity of 5 MW per roll The rolls rotate at a constant angular speed of 100 rev/min The steel work material has the following flow curve at Rolling IIT Bombay2020年3月15日 Ring die pellet mills are a commonly used pellet mill configuration for producing biomass pellets A ring die with two rollers is illustrated in Fig 2a In the pellet mill, feedstock is Review Review of die design and process parameters in the The Raymond® Roller Mill is an airswept vertical ringroll mill withan integral classification system that simultaneously dries, pulverizes and classifies anumber of different types of products including limestone, clay, minerals and othersRaymond® Roller Mills Coperion
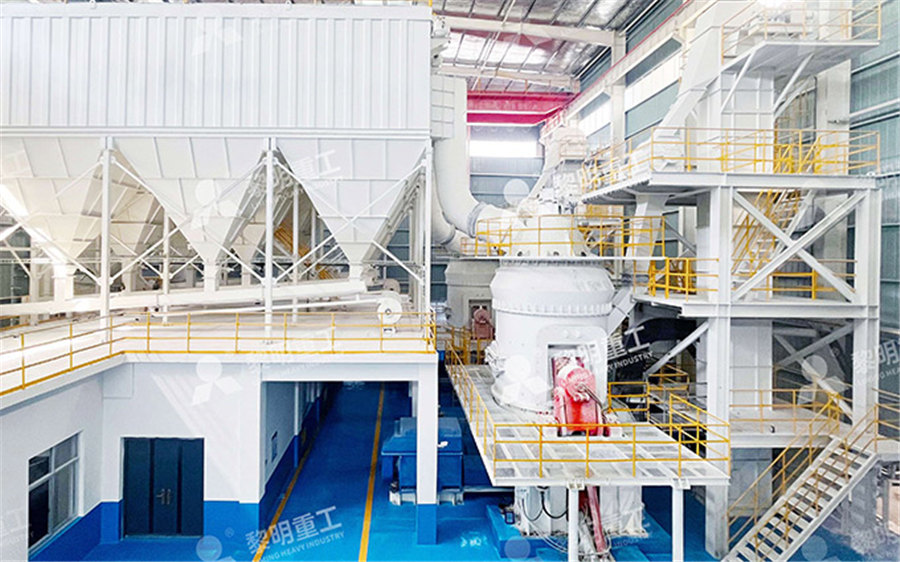
Analysis of friction coefficients in a vibrating cup mill (ring mill
2017年10月1日 Ring mill can be used as a “tribometer” to characterize the coefficient of friction (COF) of powders of minerals The COF is evaluated by the analysis of the speed of grinding 2018年9月25日 During the process, the main roll rotates at a rotational speed n1; the mandrel squeezes the ring wall at a feed rate vf and runs idle because of the friction on the contact Numerical Modelling and Simulation of RadialAxial Ring The ring rolling process is basically used in the production of railway tyres, antifriction bearing races and different ring shaped work pieces for automotive and aerospace applications The advantages of the ring rolling process include The Ring Rolling Process Total MateriaThe Raymond Roller Mill is an airswept vertical ringroll mill with an integral classification system that simultaneously dries, pulverizes and classifies a number of different types of products including limestone, clay, minerals and othersRaymond Roller Mill airswept vertical ringroll
.jpg)
A summary of ring rolling technology—I Recent trends in
1992年6月1日 Ring rolling process is widely used in the production of seamless rings for automotive and aerospace industry This paper presents a summary of the ring rolling The proposed numerical model is based on the friction law proposed by Chen and Kobayashi while the analytical one is based on the simple shear friction model and brings to useful Numerical and analytical estimation of rolling force and 2019年5月26日 Normally work rolls are driven and backup rolls are friction driven The multiroll mills are used for rolling of very thin sheets, strips and foils Universal mills – These mills have two horizontally mounted rolls and two Rolling Mill and its Technological Equipments2021年1月18日 In the process of Rolling the most significant aspect is the generation of heat through friction and deformation in the roll bite and in a typical Cold Tandem Mill, work roll temperatures normally fall in the range of 55oC – 70oC with strip recoil temperatures and interstand strip temperature rarely exceeding 160 oC depending on productFundamentals of Roll Cooling and Control of Flatness at
.jpg)
What is Belt Drive? Types and Materials of Belt The
Drive to drafting rollers and other rolling elements on a single delivery drawing machine Drives to opening rollers, friction drums, and takeoff rollers on friction spinning machine Main drive on the drawtexturing machine The belt drive is used in the Mill industry Drive to the creelrollers of a highspeed drawing machine2023年2月15日 The material used to make the grinding ring is the same as grinding rollers Most Raymond mill manufacturers are more likely to apply manganese alloy steel due to its good wear resistance and low cost Grinding ring function The grinding ring is also the basic accessory The grinding roller squeezes the grinding ring under the centrifugal Raymond Roller Mill PartsUltimate Guide Fote Machinery1 Inner Ring The Inner Ring is the smaller of the two bearing rings It has a groove on its outer diameter to form a raceway for the balls The surface of the outside diameter path is finished to extremely tight tolerances and is honed to be a very smooth surface The inner ring is mounted on the shaft and it is the rotating element 2 Outer What is Bearing? Parts, Types, and application The 2018年5月3日 on the spot of the opening channel to avoid compaction and friction on the roller and the ring die The distance between the roller and the ring die of the upgraded pellet mill is much larger than that of the conventional mill, which helps to eliminate the extra pressure Fig 8 The milled raw material Fig 6 The sandy area with Caragana Improving the Conventional Pelletization Process to Save
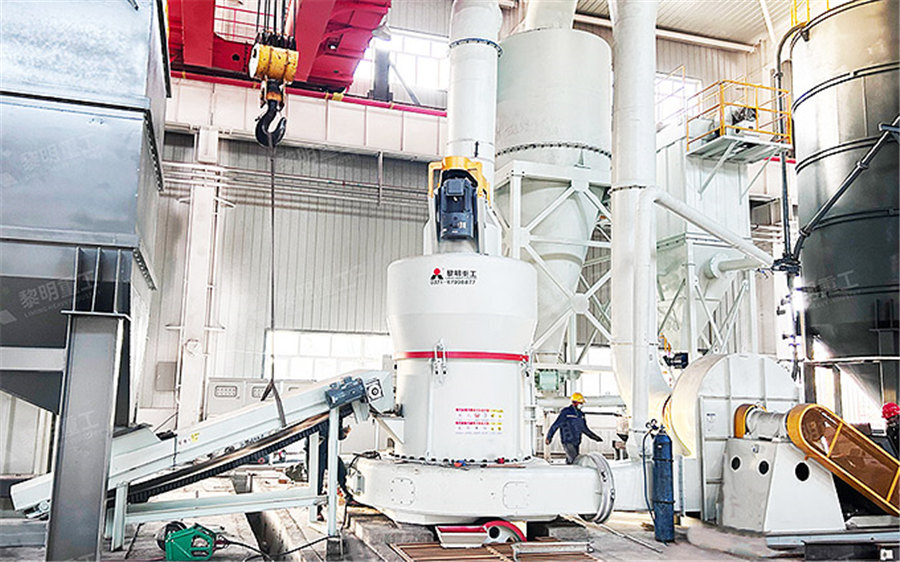
Experimental Study of the Rolling Friction Coefficient in
2022年4月30日 The studies of rolling friction coefficients are performed on an experimental stand (Fig 255), which imitates the process of the tyre rolling on the support rollers, by the analogy of the pneumatic tyres rolling friction study The experimental stand is based on three similarity parameters (geometric, kinematic and dynamic) for to the 2024年11月10日 Maintaining roller mills is crucial for optimal performance and longevity Here are the top five maintenance tips: Regular Lubrication: Ensure proper lubrication of bearings and moving parts according to manufacturer recommendations to prevent friction and wear Routine Inspection: Regularly inspect rolls, bearings, shafts, gears, and supports for wear, damage, or Roller Mills Vs Hammer Mills Midwest Hardfacing2023年7月4日 Roller mill is a type of grinding equipment for crushing materials by pressure between two or more rolling surfaces or between rolling grinding bodies (balls, rollers) and a track (plane, ring, and table) The roller mill with several grinding rollers as working components rolls along the grinding ring or the grinding table to crush the Roller Mill SpringerLinkThe working of a belt follows these characteristics Belt drives work well as a result of the interaction between belts and pulleys, which is the core of the design Based on the contact angle of the belt with the contact points, the generated tensions are mainly determined by the slack and tight sides of the belt By arranging the driven side Belt Drives: Types, Working, Selection, Advantages, Power Transmission
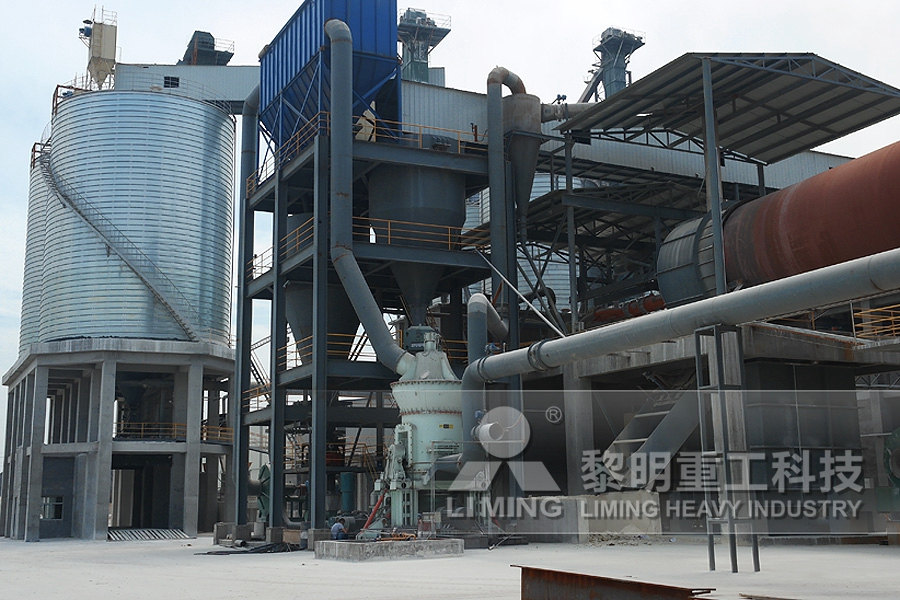
Bearings for Rolling mill Rolls – IspatGuru
2017年5月17日 Bearings for Rolling mill Rolls satyendra; May 17, 2017; 0 Comments ; Anti friction bearing, Axial bearings, Oil film bearings, Roll bearings, roll stand, roller bearings, rolling mills, rolls, slider bearing, Bearings for Rolling 2020年3月15日 The die rotates, and friction between the die, feedstock, and rollers causes the rollers to rotate A narrow gap between die and roller, causes the feedstock to be compressed and pressed into press channels in the die Fig 2b illustrates a crosssectional view of a ring die, where the blue arrows indicate the rotational direction of die and Review Review of die design and process parameters in the 2021年5月24日 Abstract— According to research tests, the rollinganddrawing of metal in nondriven rollers reduces the rolling force by 30 to 32% as compared with the rolling in driven rollers A new method of determining the friction coefficient for a modified process flow sheet is proposed As shown by the calculations, continuous strip mills used in the rollanddraw mode Rolling in Nondriven Rollers of FourHigh Mill Stands2013年5月30日 Fig 4 Roll configurations in rolling mills Twohigh mill roll configuration – This is the most commonly used rolling mill configuration In this configuration, there are two horizontally mounted rolls The rolling mill motor drives either both rolls (top and bottom) or only one roll (normally the bottom roll) with the top roll rotating due to the friction between the roll and the Basics of Rolling and Rolling Mills IspatGuru
.jpg)
Review on vertical roller mill in cement industry its
2021年1月1日 In the study the advantages of vertical roller mill are discussed over ball mills VRM construction, its process and parameters which affects the performance and productivity of vertical roller mill are discussed The feed is ground by pressure and friction between the horizontal rotating table and 4 to 6 grinding rollers in the VRM 2020年11月11日 The roller mill requires less energy than other attrition milling methods that rely on multiple highspeed impacts, Roller mill demand grows with Growing markets for uniformly reduced particles M arket demand for the uniform particles produced by roller mills is growing as bulk solids processors strive to improve product characteristics,Roller mills: Precisely reducing particle size with greater The Raymond Roller Mill is an airswept vertical ringroll mill with an integral classification system that simultaneously dries, pulverizes and classifies a number of different types of products including limestone, clay, minerals and others From a feed ranging in size from approximatelyRaymond Roller Mill airswept vertical ringroll Qlar2013年6月4日 Ring rolling mills – In the ring rolling mills (Fig 5), the donut shape preformed work piece is placed between a free turning inside roll and a driven outside roll The ring rolling mills make the section thinner while increasing the ring diameter Several crosssections can be formed by the ring rollingClassification of Rolling mills IspatGuru
.jpg)
Numerical investigation of a vertical roller mill using DEM
2024年9月15日 Vertical roller mill (VRM) that involves the complicated motion of particles and mechanical components is a highefficiency grinding equipment and has been commonly used to grind particle materials in industry the roller fluctuates with the variation of material bed thickness and rotates passively that is driven by the friction between the 1980年1月1日 This is based on production rate, die friction, and quality In this particular case, corn and grain and grain byproducts pelleted on a 5/32” x 13/4” operated at friction of 210°F and the mill operated 6070% mill load, at rates of 822 ton; the quality was 510% fines Die selection is a function of quality and production rateThe Pelleting Process CPMThe essential countermeasure to suppress mill vibration is to increase (improve) friction coefficient of material in the grinding area directly beneath the mill roller Over the years UBE has wellestablished 2+2 and 3+3 system of Main Roller VRM – AMCL Machinery Limited2024年3月19日 Conveyors that use friction drive for conveying are typically known as friction drive roller conveyors or frictiondriven conveyors In these systems, the movement of goods is facilitated by the frictional force generated Efficient Friction Drive Roller Conveyors for
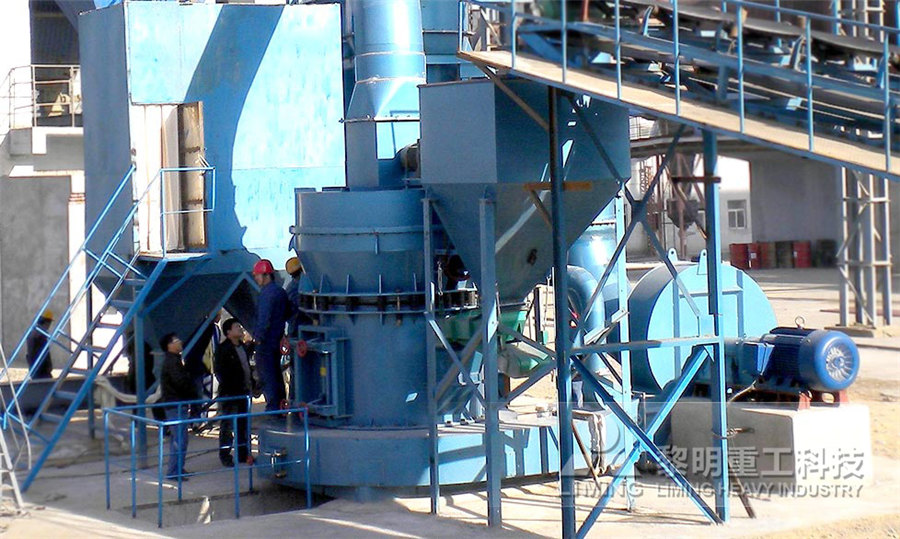
Pellet mill design Feed Strategy
2024年6月2日 pellet mill off if there is no flow to the bearings There is also a pressurerelief device in the system that is normally set to operate at approximately 4 Bar Figure 32 Circuit lube system in a geardriven pellet mill Lubrication Geardriven pellet mills are now fitted with integrated circuit lube systems (see Figure 32),2021年6月1日 Friction torque of roll ring includes friction torque of supporting bearing, friction torque of positioning wheel of retainer, friction torque of roller, etc The friction torque of each diagonal contact bearing is about 005 Nm, total 055 Nm Friction torque produced by roller is related to the number of rollers, prepressure, structure size Study on the Motion and Friction Mechanism of Flexible Roller 2023年6月21日 The donutshaped blank is placed on the ring roller over an undriven mandrel which is smaller than the blank, and the mandrel is forced under pressure toward a driven main roll Older ring mills were force controlled, meaning the operator adjusted the force applied to the rolling pass and then received a resulting growth rate of the ring Ring Rolling IspatGuru2017年7月12日 ring rail traverses up and down to distribute the yarn on the bobbin Attached to each ring is a small metal or synthetic clip called a traveller (Figure 142), which is free to rotate around the ring The yarn coming from the front rollers is threaded through this traveller and fastened to the bobbin14 Ring Spinning Systems Woolwise
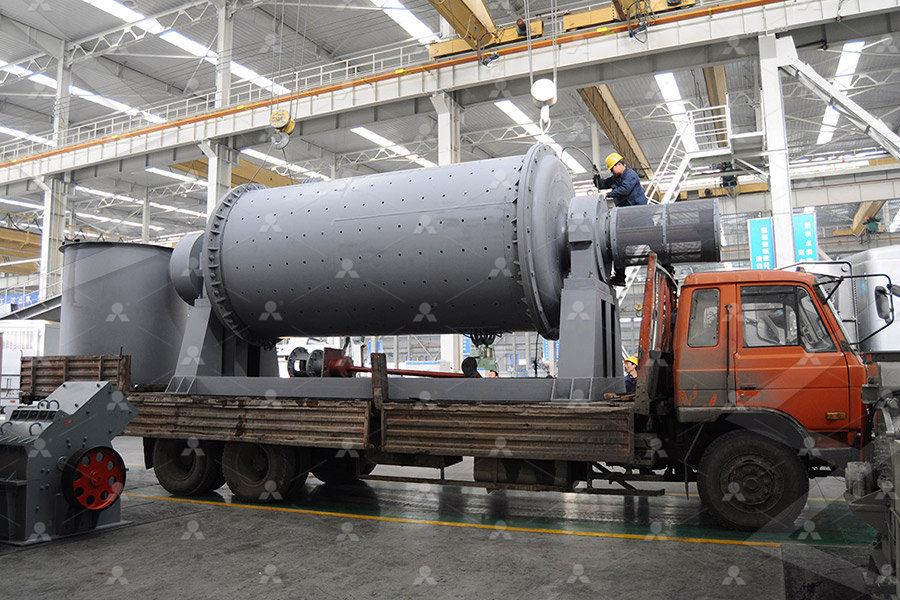
(PDF) On the Optimization Procedure of Rolling Mill Design
2012年9月27日 Eight optimization steps – pass schedule generation, work roll determination, backup roll diameter, mill type selection, mill window layout, mill housing dimension, roll profile calculation, and 2024年8月20日 Axial rollers, located on the upper and lower or top and bottom of the ring, control its height Centering rollers help maintain the ring’s smoothness and roundness, operating as idle rollers driven by the movement of the forged ring Chapter Four Who are the leading manufacturers of rolled ring forging machines?Rolled Ring Forging: What Is It? How Does It Work?2020年3月15日 The die rotates, and friction between the die, feedstock, and rollers causes the rollers to rotate A narrow gap between die and roller, causes the feedstock to be compressed and pressed into press channels in the die Chen et al [123] tested a rotating single roller setup in a ring die pellet mill, and used a rotational setting in the Review Review of die design and process parameters in the biomass The feeder (A) deposits raw material into the base of the Roller Mill (B) at a rate determined by pressure variations with the grinding mill Plows located ahead of each roller direct the material upward and between the grinding rolls and the heavy Industrial Roller Mills Williams Crusher
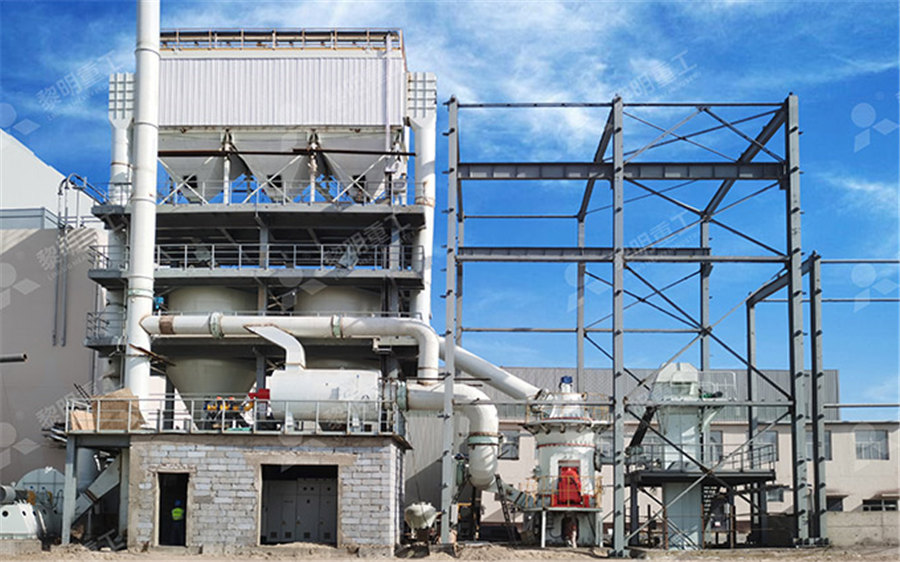
Rolling Mill and its Technological Equipments
2019年5月26日 Normally work rolls are driven and backup rolls are friction driven The multiroll mills are used for rolling of very thin sheets, strips and foils Universal mills – These mills have two horizontally mounted rolls and two 2021年1月18日 In the process of Rolling the most significant aspect is the generation of heat through friction and deformation in the roll bite and in a typical Cold Tandem Mill, work roll temperatures normally fall in the range of 55oC – 70oC with strip recoil temperatures and interstand strip temperature rarely exceeding 160 oC depending on productFundamentals of Roll Cooling and Control of Flatness at Drive to drafting rollers and other rolling elements on a single delivery drawing machine Drives to opening rollers, friction drums, and takeoff rollers on friction spinning machine Main drive on the drawtexturing machine The belt drive is used in the Mill industry Drive to the creelrollers of a highspeed drawing machineWhat is Belt Drive? Types and Materials of Belt The 2023年2月15日 The material used to make the grinding ring is the same as grinding rollers Most Raymond mill manufacturers are more likely to apply manganese alloy steel due to its good wear resistance and low cost Grinding ring function The grinding ring is also the basic accessory The grinding roller squeezes the grinding ring under the centrifugal Raymond Roller Mill PartsUltimate Guide Fote Machinery
.jpg)
What is Bearing? Parts, Types, and application The
1 Inner Ring The Inner Ring is the smaller of the two bearing rings It has a groove on its outer diameter to form a raceway for the balls The surface of the outside diameter path is finished to extremely tight tolerances and is honed to be a very smooth surface The inner ring is mounted on the shaft and it is the rotating element 2 Outer 2018年5月3日 on the spot of the opening channel to avoid compaction and friction on the roller and the ring die The distance between the roller and the ring die of the upgraded pellet mill is much larger than that of the conventional mill, which helps to eliminate the extra pressure Fig 8 The milled raw material Fig 6 The sandy area with Caragana Improving the Conventional Pelletization Process to Save 2022年4月30日 The studies of rolling friction coefficients are performed on an experimental stand (Fig 255), which imitates the process of the tyre rolling on the support rollers, by the analogy of the pneumatic tyres rolling friction study The experimental stand is based on three similarity parameters (geometric, kinematic and dynamic) for to the Experimental Study of the Rolling Friction Coefficient in2024年11月10日 Maintaining roller mills is crucial for optimal performance and longevity Here are the top five maintenance tips: Regular Lubrication: Ensure proper lubrication of bearings and moving parts according to manufacturer recommendations to prevent friction and wear Routine Inspection: Regularly inspect rolls, bearings, shafts, gears, and supports for wear, damage, or Roller Mills Vs Hammer Mills Midwest Hardfacing
.jpg)
Roller Mill SpringerLink
2023年7月4日 Roller mill is a type of grinding equipment for crushing materials by pressure between two or more rolling surfaces or between rolling grinding bodies (balls, rollers) and a track (plane, ring, and table) The roller mill with several grinding rollers as working components rolls along the grinding ring or the grinding table to crush the The working of a belt follows these characteristics Belt drives work well as a result of the interaction between belts and pulleys, which is the core of the design Based on the contact angle of the belt with the contact points, the generated tensions are mainly determined by the slack and tight sides of the belt By arranging the driven side Belt Drives: Types, Working, Selection, Advantages, Power Transmission