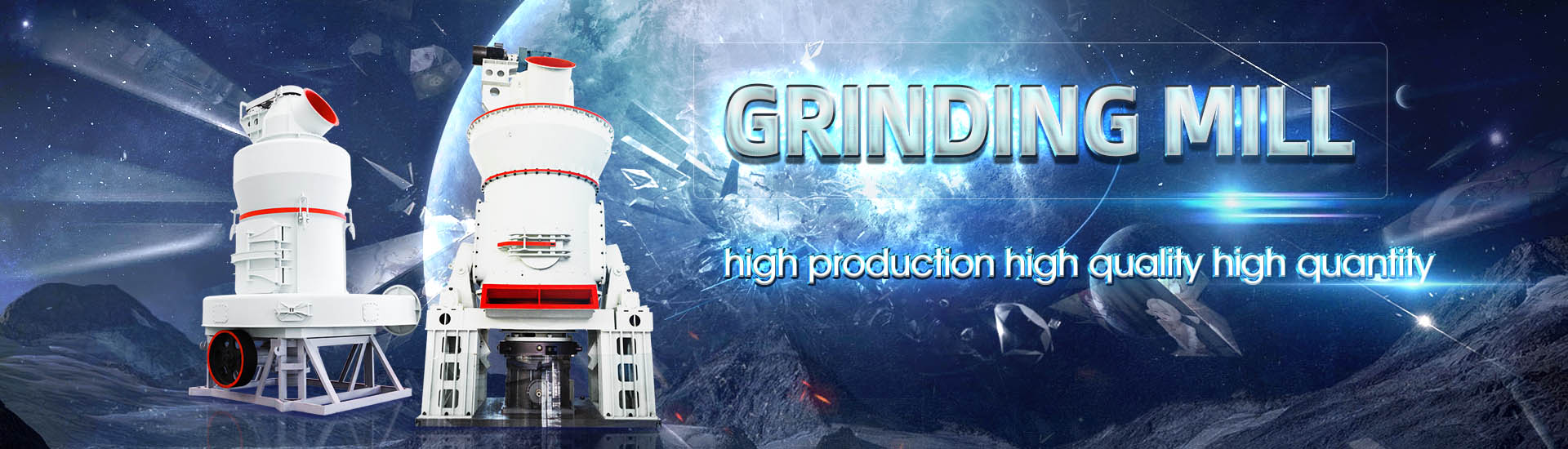
Process structure flow chart of ore powder making plant
.jpg)
Simplified process flowsheet of Itakpe iron ore processing plant
The present study presented a systematic study and design of iron ore production process in Itakpe for 15mt The study revealed that with The steelmaking processes are considered extremely2018年7月11日 Figure 2 shows a flowchart of a typical pelletizing plant, highlighting the additive preparation, mixing and pelletizing feed preparation, the balling step, in this case using a disc pelletizer(PDF) Iron Ore Pelletizing Process: An OverviewFigure 2 shows a flowchart of a typical pelletizing plant, highlighting the additive preparation, mixing and pelletizing feed preparation, the balling step, in this case using a disc pelletizer, and the induration stepIron Ore Pelletizing Process: An Overview2023年6月2日 Processing of the ore ranges from simple crushing and screening to a standard size, through to processes that beneficiate or upgrade the quality of the iron ore products This Iron Ore production in the Pilbara Rio Tinto
]@S0{UDKK%G24F3JGHC.jpg)
Simplified flow chart showing typical iron ore
2024年7月1日 The aim is to establish correlations between basic iron ore tailings data and CS parameters, providing a screening approach to determine whether laboratory results fall within expected ranges or2024年4月26日 Iron ore, a naturally occurring mineral composed primarily of iron oxides, is mined and processed to extract iron for various industrial applications This article provides a comprehensive overview of the iron ore Iron Ore Processing: From Extraction to Mineral processing flowsheet design is the design of process flow from ore processing to beneficiation product output, in which raw ores and beneficiation products are design objects, Mineral Processing Flowsheet Design SpringerLink2021年3月15日 Iron ore concentration typically involves comminution, separation, and agglomeration Comminution is the grinding of the ore to liberate the valuable ironbearing Iron Ore Pelletization: Part I Fundamentals
.jpg)
Iron Ore Pelletizing Process: An Overview IntechOpen
2018年7月17日 Figure 2 shows a flowchart of a typical pelletizing plant, highlighting the additive preparation, mixing and pelletizing feed preparation, the balling step, in this case using a disc 2022年10月20日 Making iron and steel from iron ore requires a long process of mining, crushing, separating, concentrating, mixing, agglomeration (sintering and pelletizing), and Iron Ore Processing, General SpringerLink2014年11月26日 Pellets plants based on rich iron ore fines are rare and not very economical The entire pelletizing process can be divided into two main segments of sub processes namely (i) the segment of the cold sub processes and (ii) the segment of the hot sub processes to make the ore plastic so that it can nucleate seeds which grows into well formed Iron Ore Pellets and Pelletization Process IspatGuruMost ores also contain some other nonore minerals (eg, hematite) and some other sulphide minerals, especially pyrite (FeS 2) When ore is first processed (typically close to the mine) it is crushed to gravelsized chunks and then 82: Mining and Ore Processing Geosciences
-2.jpg)
Direct Reduced Iron and its Production
2013年3月16日 Feed material for the DR process is either sized iron ore of size ranging from 10 mm to 30 mm or iron ore pellets of size ranging from 8 mm to 20 mm produced in an iron ore pellet plant The gas based process uses a shaft 2024年3月16日 The sintering process is an intricate system with a protracted process flow The steps in the manufacturing line are primarily composed of the ingredients and mixing process, the sintering operation process, and the treatment of the sintered ore [39, 40]22 Important parameters and characteristics of sintering process As shown in Fig 2, all variables affecting Application of deep learning in iron ore sintering process: a 2024年11月16日 The last stage of making cement is the final grinding process In the cement plant, there are rotating drums fitted with steel balls Clinker, after being cooled, is transferred to these rotating drums and ground into such a fine powder that each pound of it contains 150 billion grains This powder is the final product, cementHow Cement is Made Cement Manufacturing Process1 天前 South Deep’s gold plant has the capacity to process around 330,000 tonnes of ore per month and the capability to treat more underground ore than most other plants in the Far West Rand Region of South Africa The amount of rock processed per month (at full capacity) would be the equivalent of a pile 125m in diameter and almost 50m high, and Gold Fields South Deep Gold Mine How we process
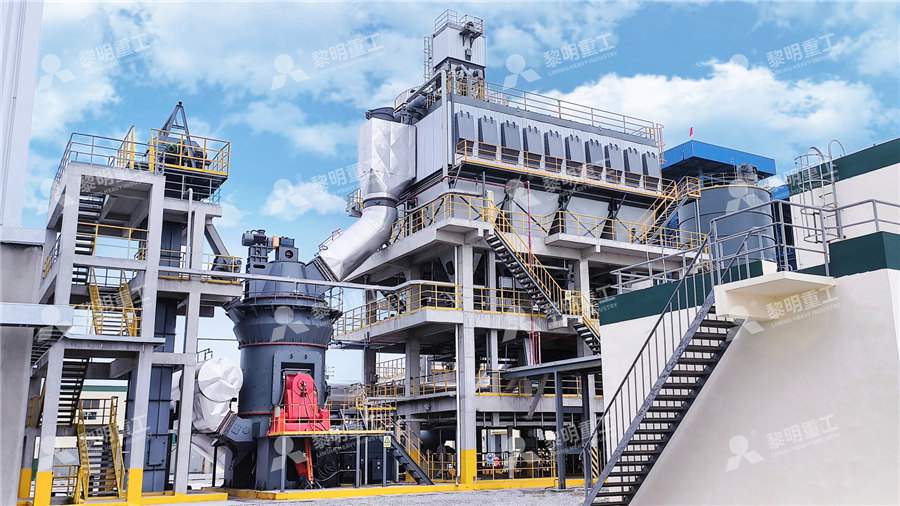
Chapter 2 Production and Processing of Aluminum
1999年5月7日 tal structure also contains 12–20% by weight of water Tropical monohydrate bauxite grades yielding 35–55% Al 2 O 3 1 process, invented in the 19th century, is by far the most important process used in the production of alumi plant is a dry white powder that is the feedstock for aluminum smelting 22 Primary Aluminum Production2018年7月17日 ore pelletizing plant The idea of rolling moist fine ore in a drum to form balls and then drying and firing it was first patented by A G Andersson in Sweden in 1912 Further development was performed to bring the idea to reality In 1943, E W Davies and coworkers demonstrated the process using an experimental shaft furnaceIron Ore Pelletizing Process: An Overview IntechOpenThe sinter plant turns iron ore into sinter, which is the optimal product for the blast furnace Sinter is made by burning a mix of iron ore powder, fluxes and recycled substances from the steel plant to create an opengrained, consistent substance The sinter is then crushed, cooled and screened for dust Sometimes, iron ore is supplied in the form of iron ore pelletsRaw materials Sinter plant ArcelorMittal2022年11月30日 Sintering is a complex physicochemical reaction process in which the original mixture ore gradually changes from powder to block solid under the condition of high temperature heating The typical physical and chemical Data‐driven modelling methods in sintering
.jpg)
(PDF) EVOLUTION AND GROWTH OF IRON ORE
2022年6月16日 The TG process is indicated for treating any type of iron ore The GK is more appropriate for magnetite ores or mixtures with hematite, although there are some GK plants operating with 100% of 2016年1月8日 The first commercial production of phosphate rock began in England in 1847 A wide variety of techniques and equipment is used to mine and process phosphate rocks in order to beneficiate lowgrade ores and remove Mining and Beneficiation of Phosphate Ore2016年3月11日 The extent to which fine crushing can be carried out will vary and depends on the ore characteristics, plant and crusher design Unfortunately, the ore characteristics are generally beyond our control, so the concentration of effort lies primarily on the plant arrangement, equipment design and operationCrushing Plant Flowsheet DesignLayout 911MetallurgistDownload scientific diagram Operational flow chart of a platinum mine from publication: Assessing the bluewater footprint of an opencast platinum mine in South Africa AbStRACt South Africa's Operational flow chart of a platinum mine ResearchGate
.jpg)
Understanding the Steel Making Process: A Flow Diagram
2024年3月20日 The article provides an overview of the steel making process, detailing how raw materials like iron ore, coke, and limestone are transformed into versatile and durable steel through a complex series of steps depicted in a flow diagram It discusses the key ingredients involved in steel production, their roles, advantages and disadvantages of the workflow 2023年10月18日 The main air pollutants in the sintering process of iron ore are polychlorinated dibenzopdioxins, polychlorinated dibenzofurans (PCDD/Fs) and harmful dustFlow diagram of iron ore sintering process [13] ResearchGate2022年11月24日 In order to reduce the sintering allocation scheme and lower the cost of allocation, two semilignite ores with similar properties and large price differences were selected for blending to achieve the purpose of complementary advantages The sintered ore specimens were studied by using FactSage71, an infrared sintering furnace, and regression analysis Sintering Properties and Regression Analysis of Imported Iron Ore Powder2012年10月26日 7 Process Design • Process design criteria • A statement of what the plant will be required to do and the framework in which it will have to accomplish it It includes: • The capacity of the plant, • Material to be treated, • The sources of feed, • The product, • Time schedule for the commissioning of the various stages, • General information regarding the Mineral processing plant design and optimisation PPT
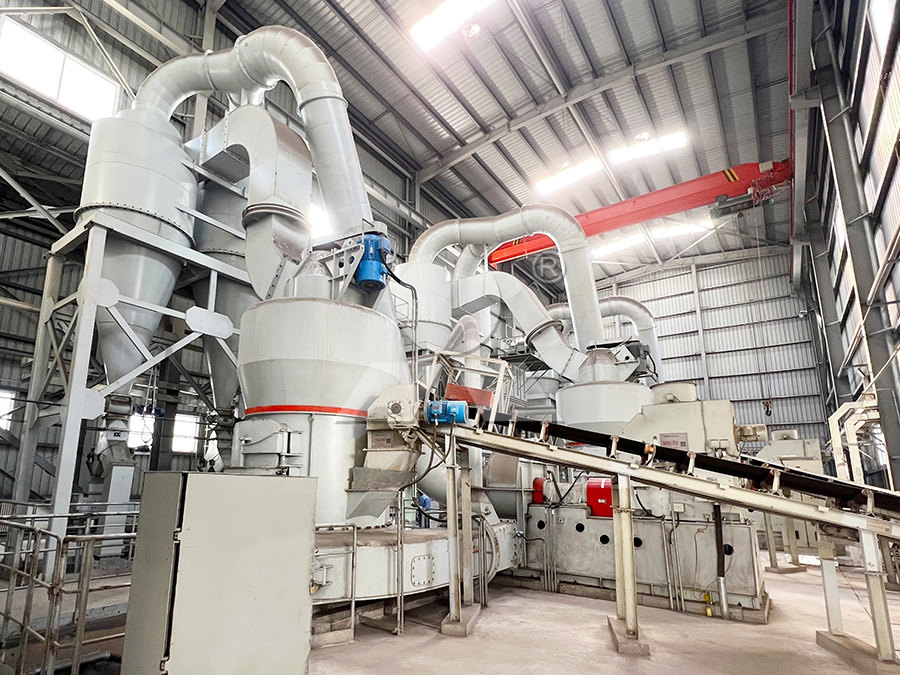
Agglomeration of Iron Ores SpringerLink
The research into pelletizing process started in early twentieth century and developed in three stages: the first stage started with the 120 t/d pelletizing pilot plant that was built in Germany in 1926; the second stage started in the 1940s, when the United States investigated the feasibility in processing and utilization of the abundant taconite lean ore resources in the Great Lakes 2018年7月11日 The iron ore production has significantly expanded in recent years, owing to increasing steel demands in developing countries However, the content of iron in ore deposits has deteriorated and lowgrade iron ore has Iron Ore Pelletizing Process: An Overview1 Steel: Steel structures are one of the most popular substrates for powder coating It's durable, strong, and versatile, making it a prime choice for various industries Powdercoated steel is commonly seen in automotive parts, Powder Coating Process Explained – A Detailed 21 Midrex Process Midrex is the most successful gasbased DR process; it is a continuous process It is basically a countercurrent process where a hot and highly reducing gas (95vol% of this gas mixture being hydrogen and carbon monoxide with a ratio of H 2:CO varying from 15 to 16) reduces lump iron ore or pellets to metallic iron as the metallic charge descends through Direct Reduction Process an overview ScienceDirect Topics
.jpg)
Recent Trends in the Technologies of the Direct Reduction
2023年4月5日 Schematic flow chart of the reductionsmelting process of iron ore using noncoking or charcoal as reductants Therefore, the availability of DRI using noncoking coal as a reducing agent is determined by the availability of iron ore with over 65% Fe quality and the availability of a cheap source of noncoking coalDownload scientific diagram Process flow chart of gratekiln pelletizing plant from publication: Comprehensive Utilization of IronBearing Converter Wastes Utilization and Waste Process flow chart of gratekiln pelletizing plant Download 2023年11月24日 The Steel Making Process: An Overview The process of making steel is a captivating sequence, marked by precision and careful control Let's look at an overview of this process, which typically includes the following key stages: Iron Making, Steel Making, Continuous Casting, and Rolling Firstly, the ironmaking phase involves converting iron ore into molten Mastering the Steel Making Process: Flowchart PPT2015年3月21日 This is because these plants are installed to pelletize the iron ores which are beneficiated at these mines Such plants receive the iron ore by rail and/or slurry pipelines Many other pelletizing plants are installed away from the iron ore mines These plants are independent of iron ore mines These plants receive iron ore mostly by rails Understanding Pellets and Pellet Plant Operations IspatGuru
)D`ERF`389RMI4.jpg)
Schematic description of the crushing plant, (1) primary
This method simulated the complete crushing process of the cone crusher and realized loop optimization Moreover, researchers have proposed the empirical model (Eloranta and Evertsson, 2006), the 2015年8月26日 Returning to the overall process; that is the process for the sulfide ores and the oxide ore as I said are treated differently Direct from the pit the oxide ore is piled onto large lined leach pads and the sulfuric acid The top photo shows one of these leach pads with the new thick black plastic liner visible on the right of the padCopper Mining Extraction Process Flow Chart2024年9月10日 For carbon neutrality, the use of sinter should be decreased owing to higher CO2 emission in the sintering process of the blast furnace operations This trend might contribute to the increased use of iron ore pellets with lower CO2 emission in the fabrication process, high reducibility and gas permeability due to higher mechanical strength The pelletizing process A New Approach of Pelletizing: Use of LowGrade Ore as a2014年11月26日 Pellets plants based on rich iron ore fines are rare and not very economical The entire pelletizing process can be divided into two main segments of sub processes namely (i) the segment of the cold sub processes and (ii) the segment of the hot sub processes to make the ore plastic so that it can nucleate seeds which grows into well formed Iron Ore Pellets and Pelletization Process IspatGuru

82: Mining and Ore Processing Geosciences
Most ores also contain some other nonore minerals (eg, hematite) and some other sulphide minerals, especially pyrite (FeS 2) When ore is first processed (typically close to the mine) it is crushed to gravelsized chunks and then 2013年3月16日 Feed material for the DR process is either sized iron ore of size ranging from 10 mm to 30 mm or iron ore pellets of size ranging from 8 mm to 20 mm produced in an iron ore pellet plant The gas based process uses a shaft Direct Reduced Iron and its Production 2024年3月16日 The sintering process is an intricate system with a protracted process flow The steps in the manufacturing line are primarily composed of the ingredients and mixing process, the sintering operation process, and the treatment of the sintered ore [39, 40]22 Important parameters and characteristics of sintering process As shown in Fig 2, all variables affecting Application of deep learning in iron ore sintering process: a 2024年11月16日 The last stage of making cement is the final grinding process In the cement plant, there are rotating drums fitted with steel balls Clinker, after being cooled, is transferred to these rotating drums and ground into such a fine powder that each pound of it contains 150 billion grains This powder is the final product, cementHow Cement is Made Cement Manufacturing Process
.jpg)
Gold Fields South Deep Gold Mine How we process
1 天前 South Deep’s gold plant has the capacity to process around 330,000 tonnes of ore per month and the capability to treat more underground ore than most other plants in the Far West Rand Region of South Africa The amount of rock processed per month (at full capacity) would be the equivalent of a pile 125m in diameter and almost 50m high, and 1999年5月7日 tal structure also contains 12–20% by weight of water Tropical monohydrate bauxite grades yielding 35–55% Al 2 O 3 1 process, invented in the 19th century, is by far the most important process used in the production of alumi plant is a dry white powder that is the feedstock for aluminum smelting 22 Primary Aluminum ProductionChapter 2 Production and Processing of Aluminum2018年7月17日 ore pelletizing plant The idea of rolling moist fine ore in a drum to form balls and then drying and firing it was first patented by A G Andersson in Sweden in 1912 Further development was performed to bring the idea to reality In 1943, E W Davies and coworkers demonstrated the process using an experimental shaft furnaceIron Ore Pelletizing Process: An Overview IntechOpenThe sinter plant turns iron ore into sinter, which is the optimal product for the blast furnace Sinter is made by burning a mix of iron ore powder, fluxes and recycled substances from the steel plant to create an opengrained, consistent substance The sinter is then crushed, cooled and screened for dust Sometimes, iron ore is supplied in the form of iron ore pelletsRaw materials Sinter plant ArcelorMittal