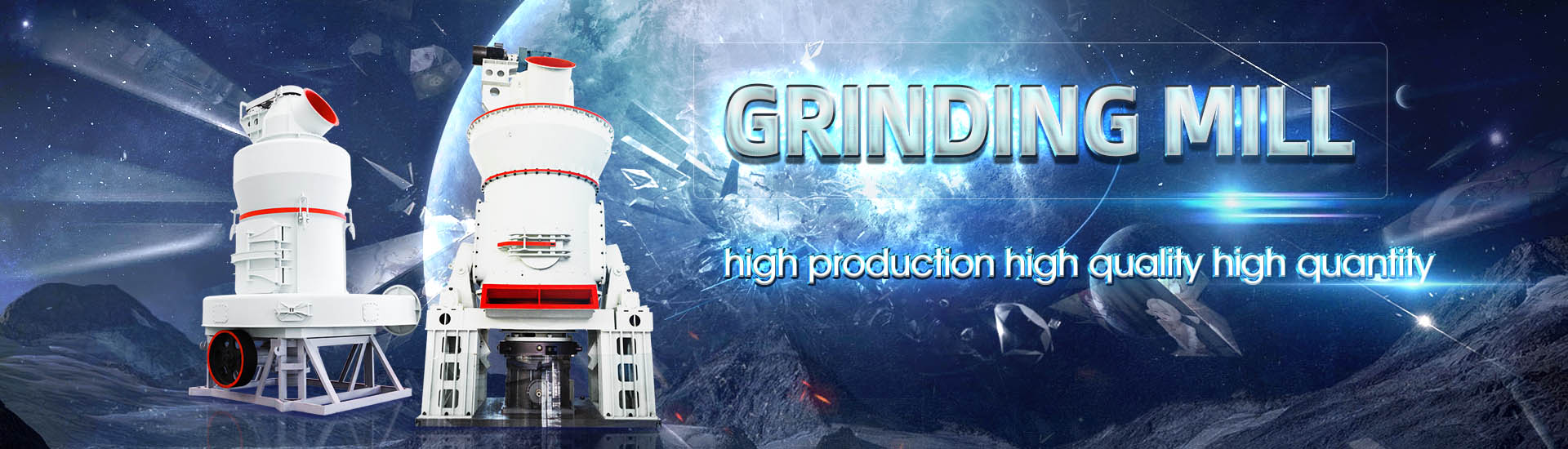
Grinding processing capacity and cost
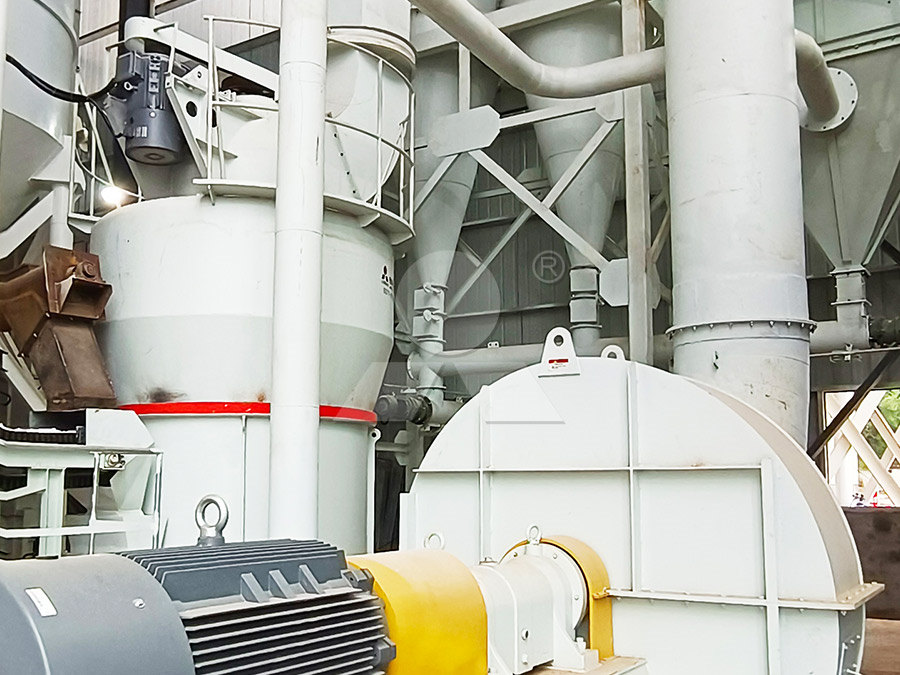
MultiObjective Optimization of the Surface Grinding Process
16 小时之前 This paper effectively integrates Taguchi, Response Surface Methodology (RSM), and Genetic Algorithm (GA) approaches for both single and multiobjective optimization, 2024年11月1日 To address this gap, this paper introduces an optimization method for grinding process parameters that considers carbon emissions and seeks to balance emissions, time, Grinding process optimization considering carbon emissions, cost 2006年6月1日 Highperformance grinding is essential to achieve high dimensional accuracy and surface integrity of ground components at optimum cost efficiency The objectives of this paper Highperformance grinding—A review ScienceDirect2016年12月28日 A scatter search based optimisation approach is developed to optimise the grinding parameters of wheel speed, work piece speed, depth of dressing and lead of dressing using a multiobjective (PDF) Cost Optimization of Surface Grinding
.jpg)
Cost reduction in grinding plants through process
2018年10月23日 Cost reduction in grinding plants through process optimization and control Yc Lo, AE Oblad and JA Herbst Abstract The major cost in comminution is energy 2022年6月24日 Grinding is a manufacturing process which significantly contributes in producing high precision and durable components required in numerous applications such as aerospace, (PDF) A comprehensive review on the grinding process: 1996年2月1日 The major cost in comminution is energy consumption, which can be as high as 50% of the operating cost Improvements in plant operations have resulted in up to a 15% Cost reduction in grinding plants through process optimization and 2016年1月10日 From the practical evidence, HPGR raise competitive capacity in mineral mining and processing, which is particularly crucial at the time of unstable or tumbling prices of HIGH PRESSURE GRINDING ROLLS—A PROMISING AND
.jpg)
BALL MILLS Ball mill optimisation Holzinger Consulting
2021年3月12日 As grinding accounts for a sizeable share in a cement plant’s power consumption, optimisation of grinding equipment such as ball mills can provide significant cost 2024年11月1日 The global manufacturing sector has played a crucial role in job creation, but it also exerts substantial environmental pressure Projections indicate a significant 56 % increase in energy consumption and a 46 % rise in CO2 emissions between 2010 and 2040 (Zhong et al, 2017)This rapid industrial growth has led to a notable surge in energy usage, contributing to Grinding process optimization considering carbon emissions, cost 2024年2月29日 What is CNC Grinding Understanding the Basics of CNC Grinding Computer Numerical Control grinding (CNC grinding) falls in the category of machining processes that rely on computerized controls to remove materials from the workpieces By using specialized grinding machines and tools, CNC grinders offer unparalleled accuracy and notably increased What Is CNC Grinding? The Future Of Machine Processing2021年11月29日 the lower the cost of operation (eg power requirements) Traditional surface processing for gold recovery is designed to achieve recovery through ‘whole ore leaching’ This involves grinding 100 per cent of the ore into sub 50 75 micron particles The Python relies on coarser grinding (much cheaper) andPotential Benefits of Underground Processing for the

High Pressure Grinding Roll and Magnetic Separation for
2024年6月20日 such as long process and high energy consumption [2021, ] Thus, the research on the high pressure grinding roll and magnetic separation process of Gongchangling concentrator is of great signicance to reduce the particle size of the ball mill, improve the processing capacity, and reduce the cost of grindingMining: crushinggrinding costsExtracting useful resources from mined ores requires comminution This is the integrated sequence of crushing and grinding operations, which breaks down mined rubble (310 cm diameter), effectively into talcum powder (30100µm), which can in turn enter the metal refining process with sufficient surface area to extract the valuable materialsMining crushing grinding costs Thunder Said Energy2011年3月3日 The grinding operation in a mineral processing facility typically consumes the majority of the energy used In addition to energy, these mills consume special steel rods or balls as well as the steel mill linings Combining all of these factors we see why grinding is one of the highest costs involved in mineral processing Keeping these costs inImplementing strategies to improve mill capacity and 2023年10月19日 The production and processing capacity of the equipment directly aects and limits the scale and eciency of the concentrator The particle size characteristics of the products signicantly aect the indicators of subsequent separation operations Therefore, improving the grinding eciency and reducing the grinding cost was of great signicanceGrinding Contribution and Quantitative Separation of
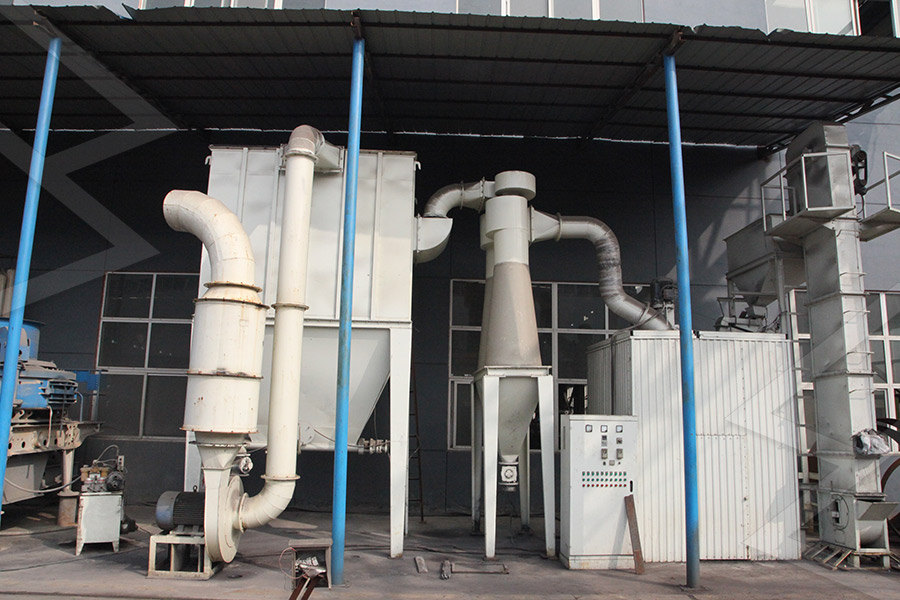
Optimizing Grinding and Regrinding Capacity in Mill Design
2019年4月25日 This allocation of nondirect cost requires careful judgement to ensure that the cost assigned to grinding reflects the actual total cost of grinding as closely as possible Estimate Total Grinding Cost (including Regrind) Versus Primary Grind The regrinding cost will generally be only a small fraction of the primary grinding cost2016年11月22日 Early studies of the grinding process were based on the mechanics of an average individual grit on the wheel surface (Alden, Citation 1914; Guest, Citation 1915) Some aspects of the grinding process by which a grit grinds can be illustrated by the geometrical relationship between the grit and the workpiece during a grinding processEffect of different parameters on grinding efficiency and its 2023年9月28日 The grinding and classification process is one of the key subprocesses in mineral processing, which influences the final process indexes significantly and determines energy and ball consumption of the whole plant Therefore, optimal control of the process has been very important in practice In order to stabilize the grinding index and improve grinding MultiObjective Optimization for an Industrial Grinding and The cost associated with high capacity processing of a hard, fine grained silica rich magnetite ore are presented in this paper, with the emphasis on comminution circuit options The objective is to evaluate several options involving different Reducing Grinding Energy and Cost Magnetite
.jpg)
HIGH PRESSURE GRINDING ROLLS—A PROMISING AND
2016年1月10日 zation of operating cost in order to reach profitability The article gives a review of the experience gained in the use of high pressure grinding rolls (HPGR) Grinding efficiency has been acquiring more importance in the world’s mining and processing industry in recent years, mainly, because of growing energy costs and global water deficiencyA theoretical design study for high capacity processing of a hard, fine grained silica rich magnetite ore, with several circuit options was carried out to assess the energy efficiency, operating cost and the project economics expressed through NPV The CO2 emission was estimated and the carbon tax added in the operating costReducing grinding energy and cost — magnetite iron ore design case 2009年1月1日 The results of a theoretical option study for high capacity processing of a hard, finegrained silicarich magnetite ore is presented in this paper, with the emphasis on comminution circuit Processing of Magnetite Iron Ores–Comparing Grinding OptionsMetso Select™ horizontal grinding mills are a preengineered range of classleading horizontal grinding mills, designed from industry leading experience and expertise The preengineered package eliminates time and costs usually spent in the engineering and selection stages Learn more about the Select™ horizontal grinding mills >Grinding mills for mining and minerals processing Metso
.jpg)
Cost reduction in grinding plants through process
2018年10月23日 Cost reduction in grinding plants through process optimization and control Yc Lo, AE Oblad and JA Herbst Abstract The major cost in comminution is energy consumption, which can be as high as 50% ofthe operating cost Improvements in plant operations have resulted in up to a 15% reduction in energy usage (kwhrlt] These im2024年4月23日 The history of CNC grinding traces back to the mid20th century when advancements in computer technology began to intersect with traditional machining methods In the 1950s and 1960s, early computer numerical control (CNC) technology emerged, allowing for the automation of machining processes Initially, CNC systems were primarily used in milling CNC Grinding Explained:Process, Types, Advantages And 2022年1月23日 Additionally, when the downstream process involved grinding mills, the fines created from highspeed crushing circuit were a benefit to the comminution process In general, if the feed material, application parameters, and downstream process match with the capabilities of a highspeed impact style crusher, this is the crusher type to usePhysical Bauxite Processing: Crushing and Grinding of Bauxite2023年4月23日 Comminution is a very important and resultdetermining step in mineral processing This is because further downstream processes in the beneficiation chain depend entirely on it(PDF) Grinding Media in Ball MillsA Review ResearchGate
.jpg)
Analysis of grinding mechanics and improved grinding force
2023年7月1日 Grinding is the most widely used highefficiency and lowcost finishing process in the manufacturing industry 1 During grinding, the interaction between the grinding wheel and workpiece generates grinding force at sliding, elastic/plastic deformation, and chipforming stages 2, 3 Grinding force is an important parameter to measure grinding performance, and it has a 2023年4月18日 The machine should have enough power to handle the plastic material and complete the grinding process High power means high capacity and vice versa You need to keep in mind that higher power consumption will The Ultimate Guide to Plastic Grinding Machine: 2024年5月29日 grind (smaller finished particle size), energy and maintenance costs increase and, everything else being equal, the capacity of the grinding system will be reduced The cost(s) of grinding The cost of grinding can be broken down into three general categories: Equipment cost, energy cost and maintenance costGrinding considerations when pelleting livestock feeds2021年6月24日 settingup of a processing cost model that re ects xed and variable cost components is recommended Once established, the model can then be used over a range of processing rates and re ned as the project develops Table 1 shows typical sources of scoping level processing cost estimates For projects where a concentrate would be producedGuidelines for mineral process plant development
.jpg)
(PDF) Electrochemical grinding process, current state and
2014年1月1日 Electrochemical grinding is one of the widely used nonconventional grinding processes to grind electrically conductive materials and difficulttomachine alloys (such as stainless steel 2021年4月14日 The groove profile of ballbearing raceway is of vital importance to ensure the bearing transmission accuracy It is an attempt to apply electrolytic inprocess dressing (ELID) groove grinding for A HighSpeed Precision Bearing Internal Grinding Machine and Grinding 2024年10月10日 The grinding process is a key link in mineral processing production and a typical complex, controlled process The steadystate model is limited by its model structure and thus difficult to applyied in a control system A hybrid modeling method driven by multisource compensation is proposed in this paper based on the mechanism model using key equipment Hybrid Modeling and Simulation of the Grinding and MDPI2013年12月18日 Fine grinding, to P80 sizes as low as 7 μm, is becoming increasingly important as mines treat ores with smaller liberation sizes This grinding is typically done using stirred mills such as the Isamill or Stirred Media Detritor While fine grinding consumes less energy than primary grinding, it can still account for a substantial part of a mill’s energy budget Overall Energy Use of Fine Grinding in Mineral Processing
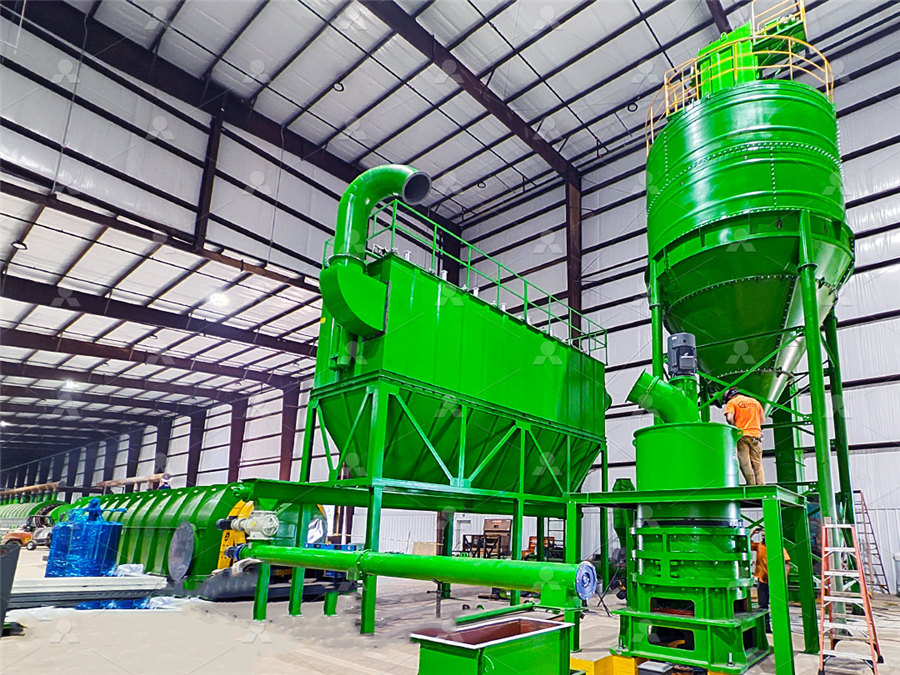
BALL MILLS Ball mill optimisation Holzinger Consulting
2021年3月12日 grinding applications and as finished product grinding units, as well as raw ingredient grinding equipment in mineral applications This paper will focus on the ball mill grinding process, its tools and optimisation possibilities (see Figure 1) The ball mill comminution process has a high electrical energy consumption, especially when2021年11月1日 Convectional methods follow several challenges like more energy consumption, material stability, cost economics, etc Among improved grinding methods, cryogenic grinding has proved a superior (PDF) Key issues and challenges in spice grinding2017年2月13日 Highcapacity, low cost grinding, wet or dry Simple, efficient, dependable; eliminate fines, slimes Write for Bulletin Wet or dry grinding A dry process requires usually dry grinding If the feed is wet and sticky, it is often necessary to lower the moisture content below 1 % Grinding in front of wet processes can be done wet or dryBall Mills 911Metallurgist2024年11月1日 The global manufacturing sector has played a crucial role in job creation, but it also exerts substantial environmental pressure Projections indicate a significant 56 % increase in energy consumption and a 46 % rise in CO2 emissions between 2010 and 2040 (Zhong et al, 2017)This rapid industrial growth has led to a notable surge in energy usage, contributing to Grinding process optimization considering carbon emissions, cost
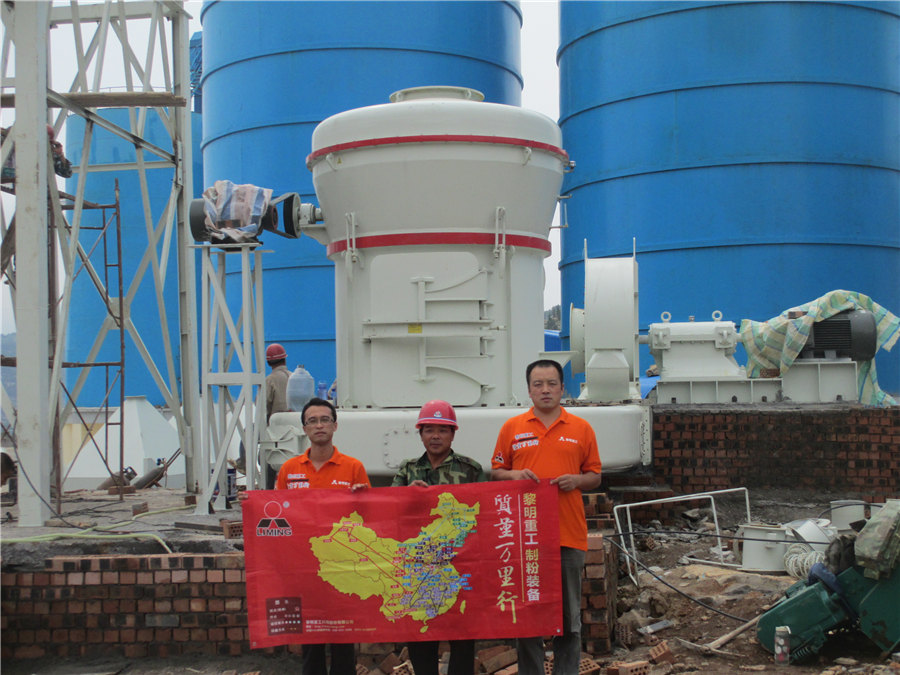
What Is CNC Grinding? The Future Of Machine Processing
2024年2月29日 What is CNC Grinding Understanding the Basics of CNC Grinding Computer Numerical Control grinding (CNC grinding) falls in the category of machining processes that rely on computerized controls to remove materials from the workpieces By using specialized grinding machines and tools, CNC grinders offer unparalleled accuracy and notably increased 2021年11月29日 the lower the cost of operation (eg power requirements) Traditional surface processing for gold recovery is designed to achieve recovery through ‘whole ore leaching’ This involves grinding 100 per cent of the ore into sub 50 75 micron particles The Python relies on coarser grinding (much cheaper) andPotential Benefits of Underground Processing for the 2024年6月20日 such as long process and high energy consumption [2021, ] Thus, the research on the high pressure grinding roll and magnetic separation process of Gongchangling concentrator is of great signicance to reduce the particle size of the ball mill, improve the processing capacity, and reduce the cost of grindingHigh Pressure Grinding Roll and Magnetic Separation for Mining: crushinggrinding costsExtracting useful resources from mined ores requires comminution This is the integrated sequence of crushing and grinding operations, which breaks down mined rubble (310 cm diameter), effectively into talcum powder (30100µm), which can in turn enter the metal refining process with sufficient surface area to extract the valuable materialsMining crushing grinding costs Thunder Said Energy
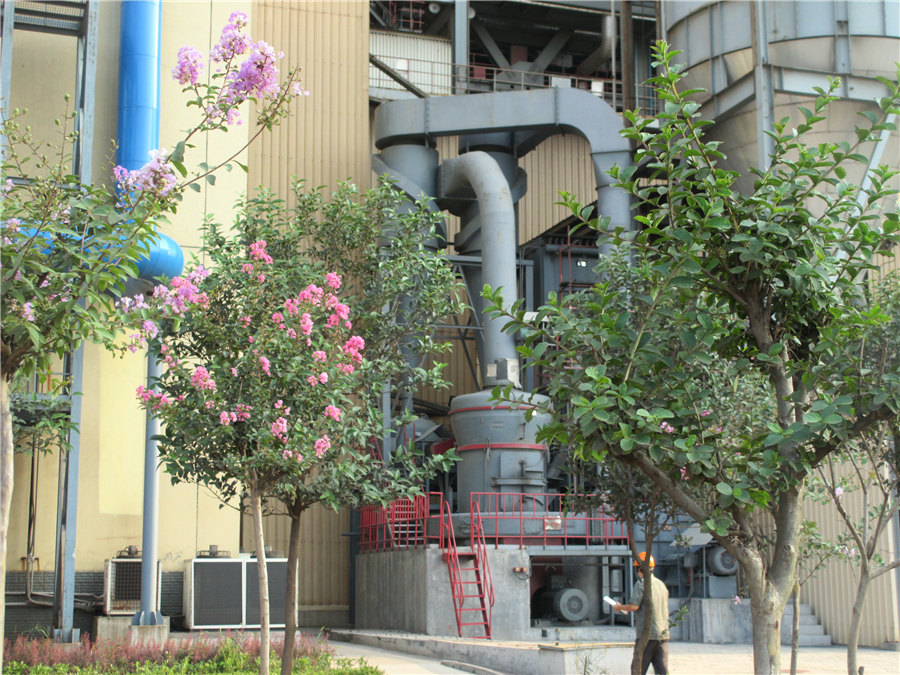
Implementing strategies to improve mill capacity and
2011年3月3日 The grinding operation in a mineral processing facility typically consumes the majority of the energy used In addition to energy, these mills consume special steel rods or balls as well as the steel mill linings Combining all of these factors we see why grinding is one of the highest costs involved in mineral processing Keeping these costs in2023年10月19日 The production and processing capacity of the equipment directly aects and limits the scale and eciency of the concentrator The particle size characteristics of the products signicantly aect the indicators of subsequent separation operations Therefore, improving the grinding eciency and reducing the grinding cost was of great signicanceGrinding Contribution and Quantitative Separation of 2019年4月25日 This allocation of nondirect cost requires careful judgement to ensure that the cost assigned to grinding reflects the actual total cost of grinding as closely as possible Estimate Total Grinding Cost (including Regrind) Versus Primary Grind The regrinding cost will generally be only a small fraction of the primary grinding costOptimizing Grinding and Regrinding Capacity in Mill Design2016年11月22日 Early studies of the grinding process were based on the mechanics of an average individual grit on the wheel surface (Alden, Citation 1914; Guest, Citation 1915) Some aspects of the grinding process by which a grit grinds can be illustrated by the geometrical relationship between the grit and the workpiece during a grinding processEffect of different parameters on grinding efficiency and its
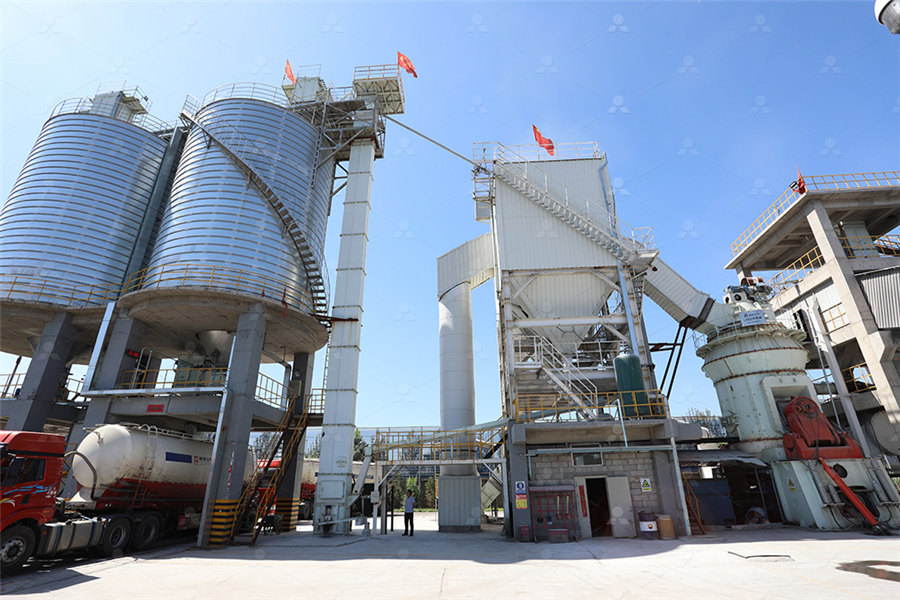
MultiObjective Optimization for an Industrial Grinding and
2023年9月28日 The grinding and classification process is one of the key subprocesses in mineral processing, which influences the final process indexes significantly and determines energy and ball consumption of the whole plant Therefore, optimal control of the process has been very important in practice In order to stabilize the grinding index and improve grinding