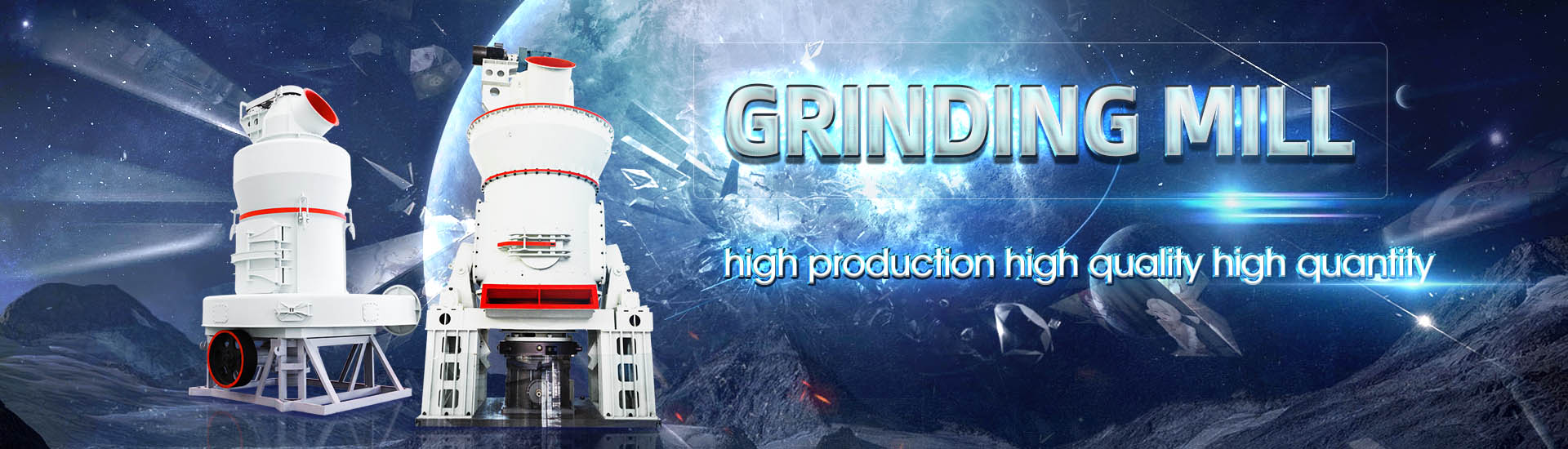
Operation procedures for cement grinding station dryer
.jpg)
The Cement Plant Operations Handbook International
2 天之前 The Cement Plant Operations Handbook is a concise, practical guide to cement manufacturing and is the standard reference used by plant operations personnel worldwide Providing a comprehensive guide to the entire cement production process from raw material2014年3月28日 Cement mill specific powerconsumption 4 Othersystems5 Debottlenecking 6 Projectaudit 7 Riskassessment 14 Plantassessmentlist 202 1 General2 Administration Cement plant operations handbook for dry process 2023年9月4日 Cement production in cement grinding plants is performed by cogrinding clinker and gypsum in dedicated mills (eg ball mills, vertical roller mills), and by possibly using Concrete Sustainability Council cscecoKey sections covering burning, grinding and quality control are supported by a range of essential chapters on cement hydration, plant reporting, maintenance and much moreThe Cement Plant Operations Handbook from
.jpg)
FCB FLAG™ station Fives Group
2024年3月4日 FCB FLAG™ station features the FCB Horomill® grinding plant advantages and meets cement producers requirements in terms of minimized capital investment, maximized 2021年3月12日 The cement industry uses a wide range of different systems in raw material, coal, and cement grinding While new plants mainly focus on highly energy‑efficient systems, Thomas Holzinger, Holzinger Consulting, grinding 2022年4月11日 Two basic types of clinker production processes exist, depending on the way the row materials are prepared before entering the kiln system: in the wet method, water is added I03 cement June 2010 GSgct IEAETSAP2024年11月26日 Explore Amrit Cement's stateoftheart cement grinding unit Learn about our cement grinding process and plant stages for high quality cementCement Grinding Unit Process High Quality
.jpg)
Maintenance of dryer in cement grinding station Henan
Regular maintenance of the dryer is essential for the smooth operation of the cement grinding station By taking the necessary steps to maintain the dryer, operators can ensure the efficient 2019年1月3日 Clinker grinding technology is the most energyintensive process in cement manufacturing Traditionally, it was treated as "low on technology" and "high on energy" as grinding circuits use more than 60 per cent of total energy Clinker grinding technology in cement High grinding efficiency For the structure, of the cement mill, we adopt the advanced obstructing equipment for internal powder, add the activated device to the fine grinding chamber, and there is the special grate plate at the end of the Cement Grinding Unit Cement Grinding Plant2020年8月25日 The Portland cement manufacturing process is representative of all types of cement limestone and clay are the main raw materials of cement making, the cement raw materials will be processed into a raw meal by Cement Production Process Cement
.jpg)
Drying of raw materials INFINITY FOR CEMENT EQUIPMENT
Dryinggrinding plants working in conjunction with hammer mills with capacities up to 360 t/h, have been erected by the Orenstein u Koppel Co (W Germany) Basic features of dryinggrinding plants were already described in 1938 by NC Rockwood in 2021年3月12日 common solution to grind raw materials and cement Roller presses are used mainly in combination with a ball mill for cement grinding applications and as finished product grinding units, as well as raw ingredient grinding equipment in mineral applications This paper will focus on the ball mill grinding process, its tools and optimisationBALL MILLS Ball mill optimisation Holzinger ConsultingEO can be applied to all the grinding stages that occur on a typical cement plant: Coal grinding; Raw material grinding; Finished cement grinding; Further EO can be used with all the different technologies and grinding circuit configurations applied by cement manufacturers on their grinding units Presently most common configurations are:ABB Ability™ Expert Optimizer for cementThe vertical roller mill (VRM) is a type of grinding machine for raw material processing and cement grinding in the cement manufacturing processIn recent years, the VRM cement mill has been equipped in more and more cement plants around the world because of its features like high energy efficiency, low pollutant generation, small floor area, etc The VRM cement mill has a Vertical Roller Mill Operation in Cement Plant
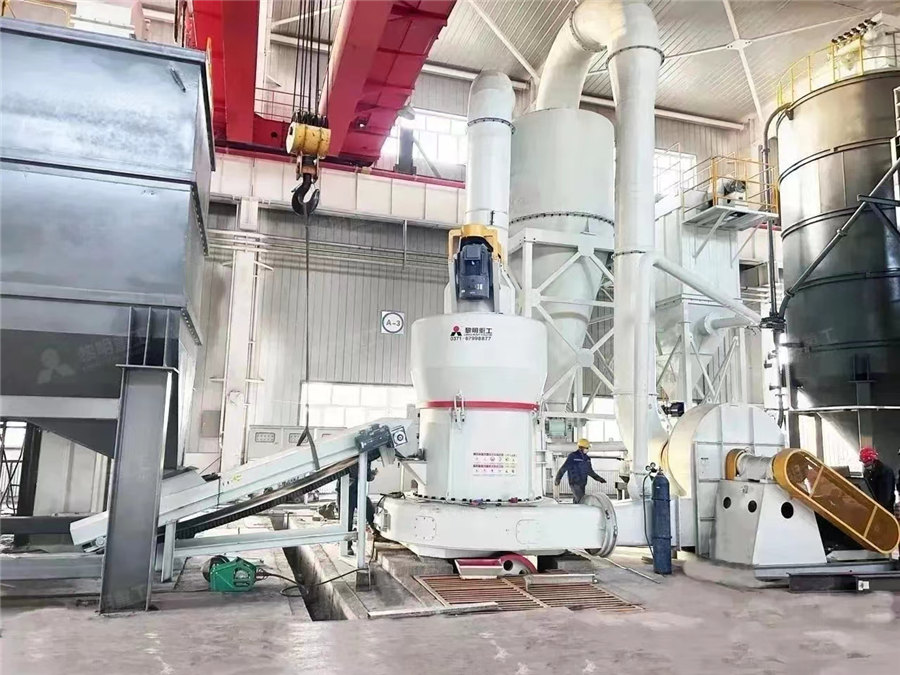
CEMENT PRODUCTION AND QUALITY CONTROL
2019年7月20日 to produce PPC type of cement, (Clinker+Gypsum) to Produce OPC type of Cement, (Clinker+Gypsum+Limestone) to produce PLC type of cement, (Special clinker + Gypsum) to produce LHHS type of cement After grinding, the finished product (cement) is stored in cement silos ready for dispatch 8 Cement packing and Dispatch2024年6月3日 Stable clinker burning with maximum combustion effi ciency for energysaving operation of facilities Control of cement grinding systems Stable quality of cement product with cement grinding at maximum effi ciency for energysaving operationMonitoring Control Systems for Cement Plants Fuji Drying and grinding are generally being done in either air swept ball mill or a vertical mill The selection of mill system will depend mostly on the factors like initial capital cost, drying and grinding capacity required, cost of energy (power) etc Coal Fineness: It is understood generally that the finer we grind, the easy it is for burning Coal Grinding Cement Plant Optimization2020年2月1日 Nowadays, ball mills are used widely in cement plants to grind clinker and gypsum to produce cement In this work, the energy and exergy analyses of a cement ball mill (CBM) were performed and Energy and exergy analyses for a cement ball mill of a new
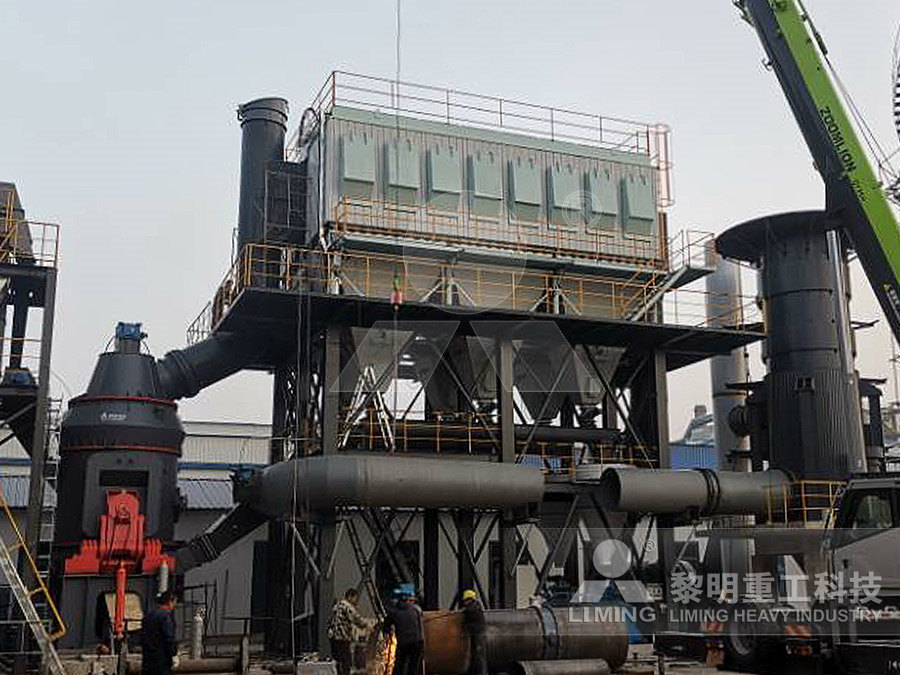
FCB FLAG™ station Fives Group
2024年3月4日 FCB FLAG™ station The FLexible Advanced Grinding station • The best available technologies in grinding, drying classifying • Zero water injection leading to better cement quality • The lowest electrical consumption in the market • High flexibility to adapt to the production of any type of cement • Easy assembly, operation maintenance • Fast delivery Fig 103a shows the relationship between the spe cific surface ace to Blaine and the residue on the 30 Micron sieve of various types of separatorsThe area between the dotted curves shows the relationship in the case of various types of turbo separators, while the area between the solid lines shows the situation in the case of plants equipped with cyclone separa torsFinish grinding INFINITY FOR CEMENT EQUIPMENT2016年10月5日 1 Introduction Cement is an energyintensive industry in which the grinding circuits use more than 60 % of the total electrical energy consumed and account for most of the manufacturing cost []The requirements for the cement industry in the future are to reduce the use of energy in grinding and the emission of CO 2 from the kilns In recent years, the production EnergyEfficient Technologies in Cement Grinding2024年10月12日 Regardless of Rotary kiln operation or grinding, it is necessary to clarify the inherent logical relationship of the system, which requires the operator to have a clear understanding of the characteristics of the system process and equipment fully understand the dialectical relationship between qualitative and quantitativeimportant operation tips for cement vertical mill
.jpg)
Cement Plant Operation Handbook PDF Mill (Grinding)
2017年4月25日 Cement Plant Operation Handbook Free ebook download as PDF File (pdf), Text File (txt) or read book online for free Cement Plant Operation HandbookOur ROTAX2® Rotary Kiln for cement delivers high production capacity and requires minimal energy and space The twobase design saves on construction time and costs and this rotary kiln never needs kiln axis alignment Pyroprocessing with proven operational reliabilityROTAX2® Rotary Kiln FLSmidth CementGrinding operation is monitored for following parameters to ensure objectivity and economy of operation Grinding Operation Objectives and KPIs Chemical analysis of cement, generally on hourly basis Product fineness, Blain surface and 45micron residue Cement SO3, % Grinding aid usage, grams/tonne Cement moisture, % Production rate, tonnes/hourCement Grinding Cement Plant OptimizationThe proportioned raw material is feed first to a grinding mill In the mill, particles ground in to very fine sizes In the grinding unit, drying, grinding and mixing takes place simultaneously Hot gas from clinker burning unit is passed into the Cement Manufacturing Process INFINITY FOR
.jpg)
Cement Grinding Plant CHAENG
2024年10月26日 The cement grinding unit produced by Xinxiang Great Wall Machinery integrates drying, grinding, powder classification, dust removal, and cement packaging We can provide cement grinding units with different Types of Cement Kilns: Overview of wet, dry, semidry, and semiwet process kilns Components of a Cement Kiln: Detailed examination of the rotary kiln, preheater, precalciner, and cooler Kiln Operation and Optimization: Key Comprehensive Guide to Cement Kilns: 2024年3月16日 Commissioning Guide Lines Free download as PDF File (pdf), Text File (txt) or read online for free The document provides instructions for commissioning various components of a cement plant, including the raw mill, limestone crushing, shale/gypsum/coal crushing, raw meal handling, and kiln startup It describes checking equipment is correctly Commissioning Guide Lines PDF Mill (Grinding) Cement44 Comments / Cement plant Operation ( CCR operator), KILN OPERATION, Process , Operation and Important Formulas / By admin which is mainly drying, heat up and calcination) Oxygen concentration of the kiln exit gas (as an indicator for the efficiency of combustion) STARTUP AND SHUTDOWN PROCEDURES The start up and the shut down of a Kiln Control and Operation INFINITY FOR CEMENT EQUIPMENT
.jpg)
Cement Grinding Plant Overview Cement Grinding Unit Cement
2019年10月11日 There is no doubt that cement grinding mill and cement roller press are the core equipment of cement grinding unit Cement grinding machine selection will directly decide the quality and cost of whole cement grinding unknit According to the real cement projects, there are three common solutions for cement grinding plantThe final manufacturing stage at a cement plant is the grinding of cement clinker from the kiln, mixed with 45% gypsum and possible additives, into the final product, cement In a modern cement plant the total consumption of electrical energy is about 100 kWh/t The cement grinding process accounts for approx 40% if this energy consumptionCEMENT GRINDING SYSTEMS INFINITY FOR CEMENT EQUIPMENTFeaturing all the process benefits of the classic FCB Horomill® grinding plant, the FCB FLAG™ station is Fives’ top solution for: Entering new markets; Adapting operations to market changes; Boosting production of all types of cement; The unit’s standard design enables fast delivery and startupIts modular concept and preassembled parts minimize site work and associated costFives Modular grinding with FCB FLAG™ station Fives Group2024年11月26日 Cement Clinker Grinding Station can make full use of Industrial waste such as the slag , fly ash, furnace slag and coal gangue around the city, so it is an environmental protection industry FTM cement mill station is featured with relatively simple process, easy operation, less investment in process equipment, energy saving, and environmental protectionCement Grinding stationcement ball millGrinding mill stationGrinding
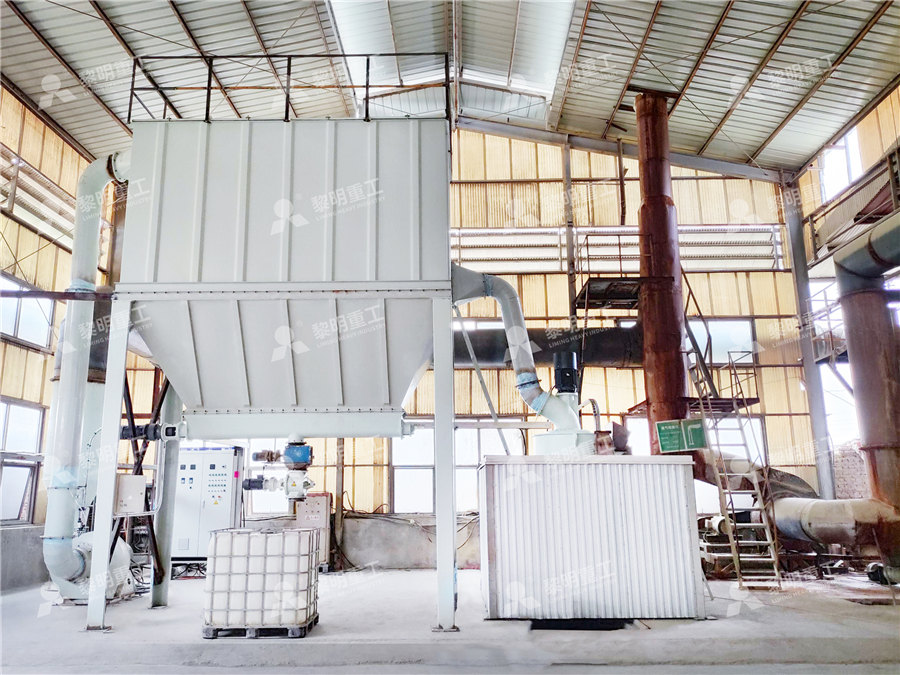
Fives Modular grinding with FCB FLAG™ station
Fives’ FCB FLAG™ station is an integrated grinding unit that offers toprated technologies in grinding efficiency, drying capacity and classifying quality As an industrial engineering Group with an heritage of over 200 years, Fives designs and supplies machines + 2019年1月3日 Clinker grinding technology is the most energyintensive process in cement manufacturing Traditionally, it was treated as "low on technology" and "high on energy" as grinding circuits use more than 60 per cent of total energy Clinker grinding technology in cement High grinding efficiency For the structure, of the cement mill, we adopt the advanced obstructing equipment for internal powder, add the activated device to the fine grinding chamber, and there is the special grate plate at the end of the Cement Grinding Unit Cement Grinding Plant2020年8月25日 The Portland cement manufacturing process is representative of all types of cement limestone and clay are the main raw materials of cement making, the cement raw materials will be processed into a raw meal by Cement Production Process Cement
.jpg)
Drying of raw materials INFINITY FOR CEMENT EQUIPMENT
Dryinggrinding plants working in conjunction with hammer mills with capacities up to 360 t/h, have been erected by the Orenstein u Koppel Co (W Germany) Basic features of dryinggrinding plants were already described in 1938 by NC Rockwood in 2021年3月12日 common solution to grind raw materials and cement Roller presses are used mainly in combination with a ball mill for cement grinding applications and as finished product grinding units, as well as raw ingredient grinding equipment in mineral applications This paper will focus on the ball mill grinding process, its tools and optimisationBALL MILLS Ball mill optimisation Holzinger ConsultingEO can be applied to all the grinding stages that occur on a typical cement plant: Coal grinding; Raw material grinding; Finished cement grinding; Further EO can be used with all the different technologies and grinding circuit configurations applied by cement manufacturers on their grinding units Presently most common configurations are:ABB Ability™ Expert Optimizer for cementThe vertical roller mill (VRM) is a type of grinding machine for raw material processing and cement grinding in the cement manufacturing processIn recent years, the VRM cement mill has been equipped in more and more cement plants around the world because of its features like high energy efficiency, low pollutant generation, small floor area, etc The VRM cement mill has a Vertical Roller Mill Operation in Cement Plant
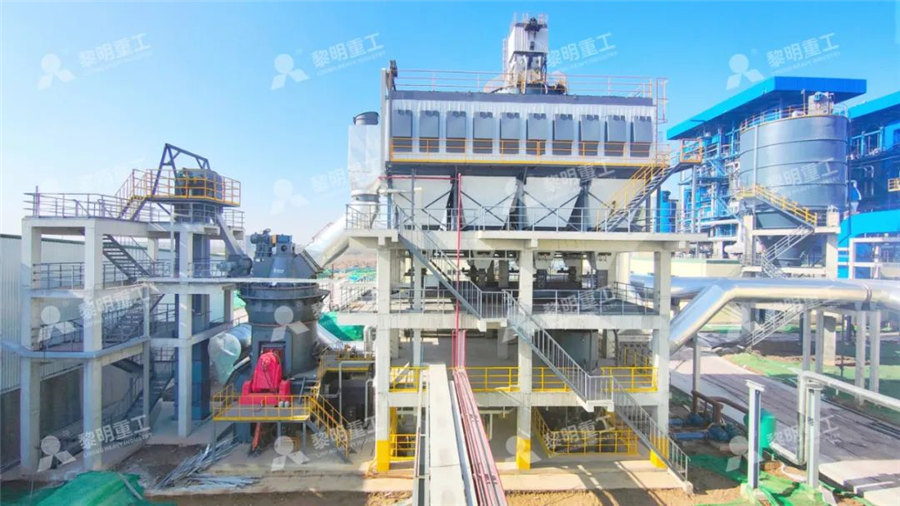
CEMENT PRODUCTION AND QUALITY CONTROL
2019年7月20日 to produce PPC type of cement, (Clinker+Gypsum) to Produce OPC type of Cement, (Clinker+Gypsum+Limestone) to produce PLC type of cement, (Special clinker + Gypsum) to produce LHHS type of cement After grinding, the finished product (cement) is stored in cement silos ready for dispatch 8 Cement packing and Dispatch2024年6月3日 Stable clinker burning with maximum combustion effi ciency for energysaving operation of facilities Control of cement grinding systems Stable quality of cement product with cement grinding at maximum effi ciency for energysaving operationMonitoring Control Systems for Cement Plants Fuji