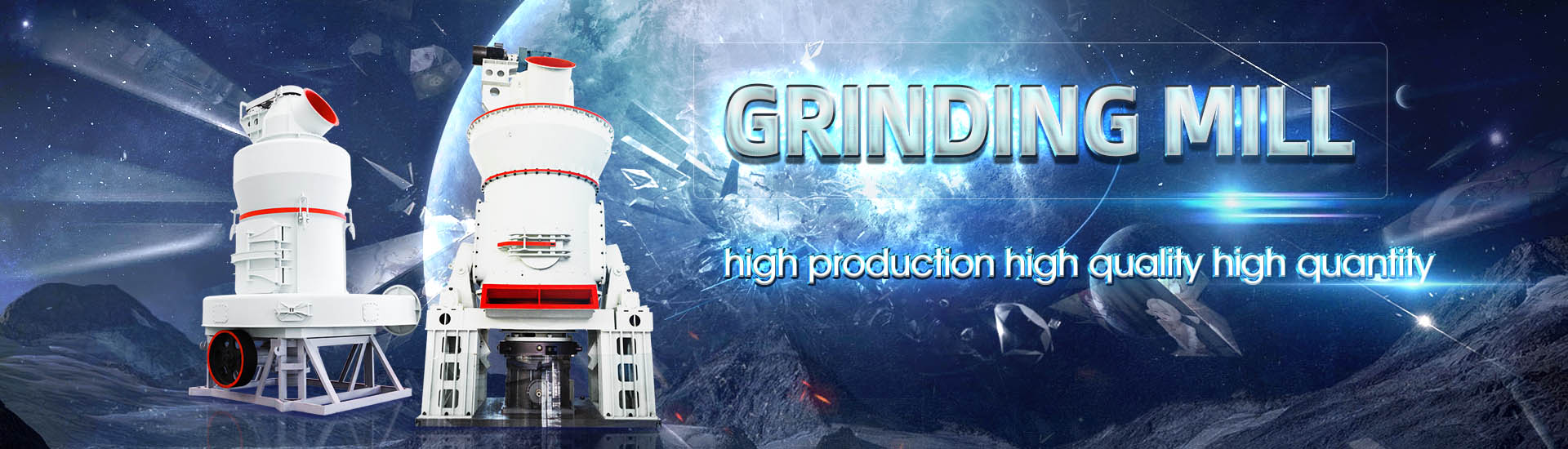
How to change the grinding plate of coal mill
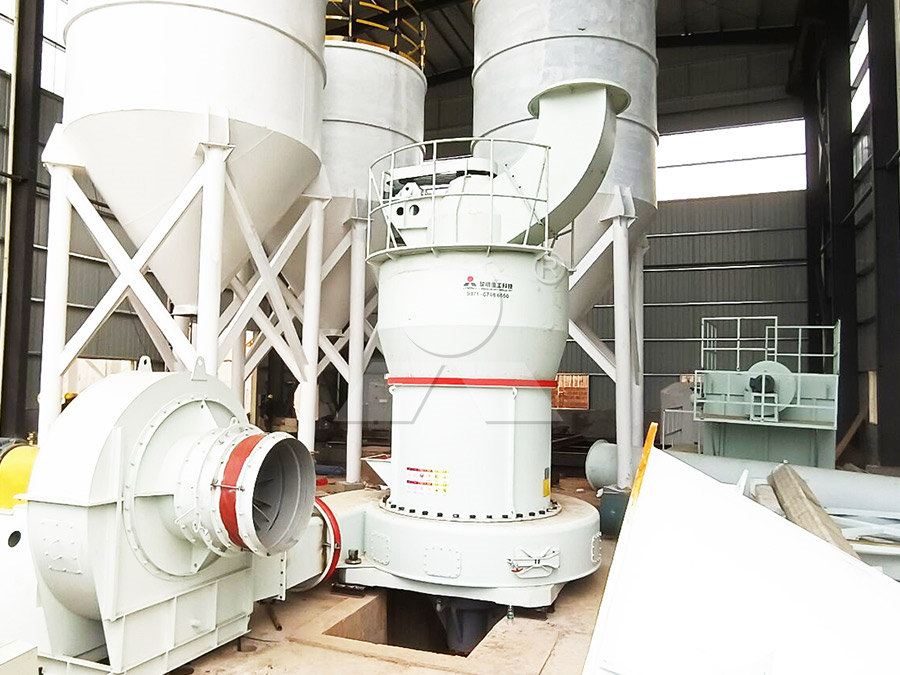
COAL GRINDING IMPS: more than meets the eye Gebr Pfeiffer
GPSE supplies standalone MPS coal grinding mills as well as complete coal grindingdrying systems Both mill and grinding system can be operated under pressure or suction as well as under air or inert gas atmosphere System configurations cover grinding plants with temporary The document provides technical details about the installation and operation of a ZGM medium speed grinding roller type coal mill It describes the key components of the mill including the Coal Mill PDF Mill (Grinding) Screwmills to vary the grinding load as mill load demand changes This optimizes mill grinding force loading characteristics such that the mill grinding force increases as mill load increases Figure 6 illustrates a typical mill gTinding force loading characteristic Coal Pulverizer Design Upgrades to Meet the Demands of Low Vertical Coal Mill (VCM) is equipment for grinding and pulverizing coal into micron size Rotary kilns then use the powders as fuel burners The VCM has a housing section equipped with a lining The layout of the coal mill with a rotary classifier
.jpg)
Coal Mill – Coal Mill In Cement Plant AGICO Cement
The coal mill grinding system is an important part of the dry process cement manufacturing In cement plants, we usually adopt the air swept coal mill system or vertical mill system as the pulverized coal preparation system, which is The coal mill in a cement plant should be reliable and should be operated with great care, or it is easy to cause safety accidents In the process of grinding, storage, transportation, and burning of pulverized coal, the material is fed into the mill through the inlet on the top center of the mill and falls on the grinding plate, Coal Mill in Cement Plant2022年5月31日 Mineral crushing is the main source of energy consumption in mineral processing According to statistics, this consumption accounts for about 35–50% of the total cost of the mine (Curry et al, 2014), or even higherIt may also account for 18% of the global electrical energy consumption (NapierMunn, 2015)More efficient crushing equipment needs to be Analysis of vertical roller mill performance with changes in Coal mill equipment selection 1: lowspeed coal mill The typical representative of low speed coal mill is the ball mill The working principle is: the highpower motor through the gearbox to drive this heavy round plate rotation, the steel ball in the simple is rotated to a certain height and then falls down, through the impact of the steel ball on the coal and between the steel ball How to choose coal grinding equipment? What are the basis for coal mill
.jpg)
(PDF) Modeling and Control of Coal Mill Academia
Finally, the temperature equation is based on heat balance equation of the coal millThe significant heat contribution comes from the primary air flow , moisture of the incoming coal particles, coal flow into the mill (1) and from grinding the moisture coal particles and temperature depends on the The mass of pulverised coal on the table grinding rate and the amount of coal The raw material of coal powder is coal with various hardness, and it drying in the coal mill grinding process to obtain finished coal powder which can be efficiently burned Coal ball mills are widely used in the cement industry and thermal power generation industry, and are also suitable for metallurgical industry, chemical industry, sugar industry and other fieldsCoal Ball Mill Grinding for Different Kinds of Pulverized Coalalso find an application in grinding a wide variety of coal types in cement and power plants Gebr Pfeiffer SE (GPSE) describes its vertical roller mills for coal grinding and provides a case study of an MPS225BK installed at CBR’s Lixhe cement works in Belgium COAL GRINDING Figure 1: MPS coal grinding mill with SLS highefficiency classifierCOAL GRINDING IMPS: more than meets the eye Gebr Pfeiffer2020年8月12日 As one of the three major forces of coal mills, the grinding force exerts a significant impact on the working process of coal mills and parameters like mill current and outlet temperatureAn investigation of performance characteristics and energetic
36.jpg)
An investigation of performance characteristics and energetic
2020年8月12日 To understand the performance of a vertical roller coal mill, the real operational tests have been performed considering three different coal sources Obtained results indicate that grinding pressure, primary air (PA) temperature and mill motor current have a tendency to rise by increasing coal feeding mass flow rates for all used coalSafe operation of coal grinding systems: Raw coal silo protection against fire and explosions Safe operation of coal grinding systems: Raw coal yard management The purchasing process for coal grinding systems needs changes Talk at a Fire and explosion protection of coal grinding 2020年4月7日 Inside the coal mill, the grinding part is composed of a groove type grinding plate and three convex grinding rollers Under the action of spring force or liquid pressure, the grinding rollerModeling of Coal Mill System Used for Fault Coal Mill is the main equipment of the rotary kiln cement clinker production a lifting plate, a compartment plate, lining plates, and the grinding medium (usually steel balls) 33 The transmission so that the length ratio between the drying bin and the grinding bin can reach 1:281 Such a change can grind coal pieces AirSwept Coal Mill of High Quality Fote Machinery
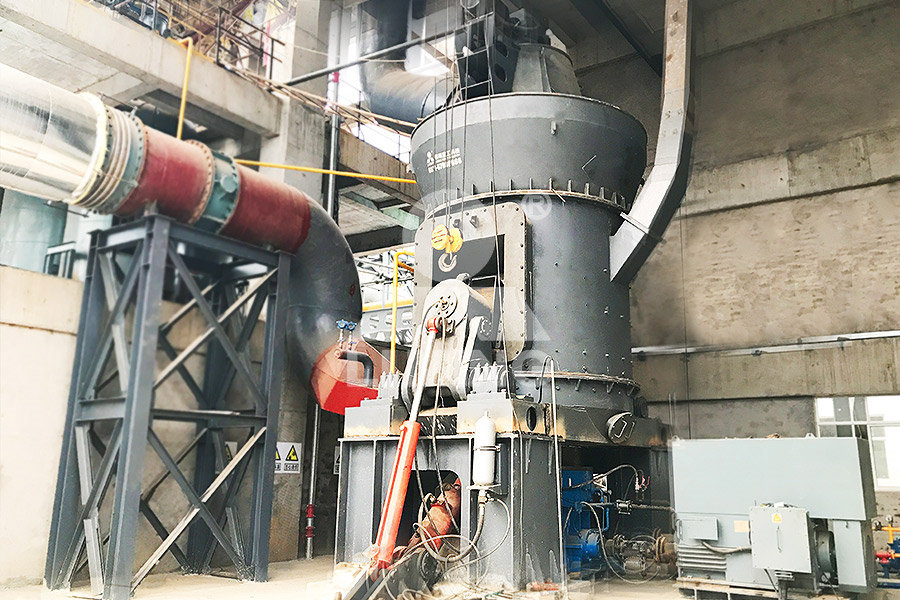
Grinding Mill Liners 911Metallurgist
2015年8月6日 This plate can be either a plain contoured slab liner plate as shown or it may have a molded intermediate rubber lifter if required due to the chordal spacing, the size of the grinding media and feed The rubber plate is held in place by the metal lifter bars A metal spacer sits between the rubber slabs and lifters to keep the liner from shiftingAbstract: The paper presents development and validation of coal mill model (including the action of classifier) to be used for improved coal mill control The model is developed by using the mass and heat balance equations of the coal mill Genetic Algorithm is used to estimate the unknown parameters that are used in the model validationModeling and Control of Coal Mill2022年2月24日 change device proposed in [11] uses the pregrinding of coals Still, the energy consumption process is considered only in terms of the balls in a ball drum millImproving the efficiency of the coal grinding process in ball drum 2024年1月11日 With a ball mill 1 To pulverize crushed coals in a ball mill, you start by feeding the mill with crushed coal Then the grinding media crushes and grinds the coal in the rotating chamber 2 Airflow carries the pulverized coal out of the ball mill 3 Next, you'll need to use the mill classifier to separate the fine coal particles from the airflowHow to Process Coal into Pulverized Coal in 5 Steps?
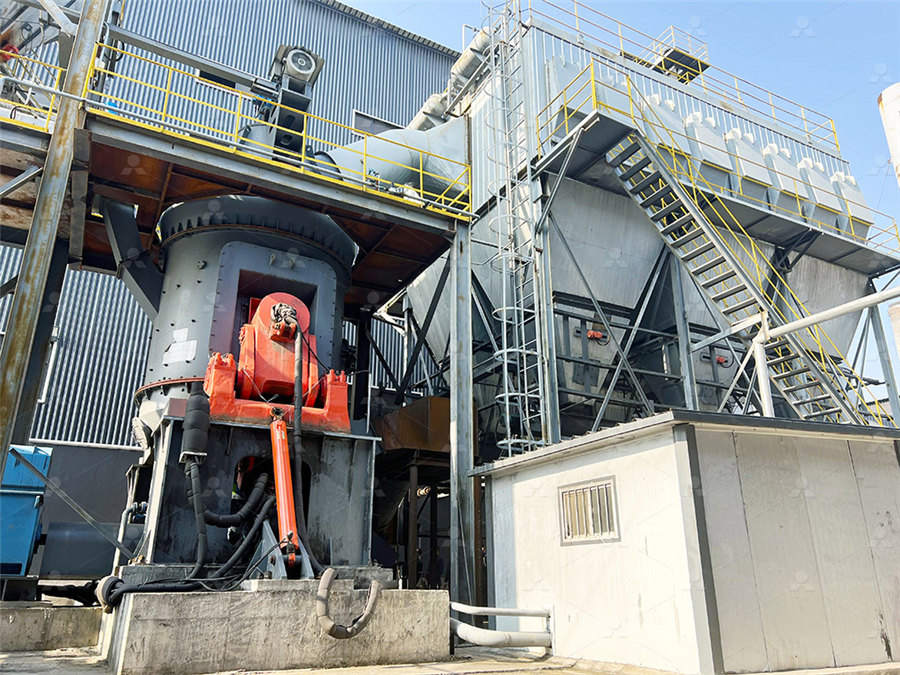
How to choose coal grinding equipment? What are the basis for coal mill
Coal mill is an important part of the pulverizing system and an important auxiliary power equipment in power plant Its main task is to break and grind coal into pulverized coal to provide boiler equipment, its configuration will directly affect A simple energy balance model of the coal mill is derived in (Odgaard and Mataji 2006), this model is based on a more detailed model found in (Rees and Fan 2003)In this model the coal mill is seen as one body with the mass m mThe following variables are defined: T(t) is the temperature in the coal dust flow in the mill, ṁ PA (t) is the primary air mass flow, T PA (t) is Coal Mill an overview ScienceDirect TopicsAs one of the three major forces of coal mills, the grinding force exerts a significant impact on the working process of coal mills and parameters like mill current and outlet temperatureEffect of mill outlet temperature on the coal Safe operation of coal grinding systems: Raw coal silo protection against fire and explosions Safe operation of coal grinding systems: Raw coal yard management The purchasing process for coal grinding systems needs changes Talk at a virtual seminar, November 2023 Accept the probability that the fire and explosion safety of your coal grinding system is nothing more than a mirageOptimisation of coal mill systems, with fire and explosion
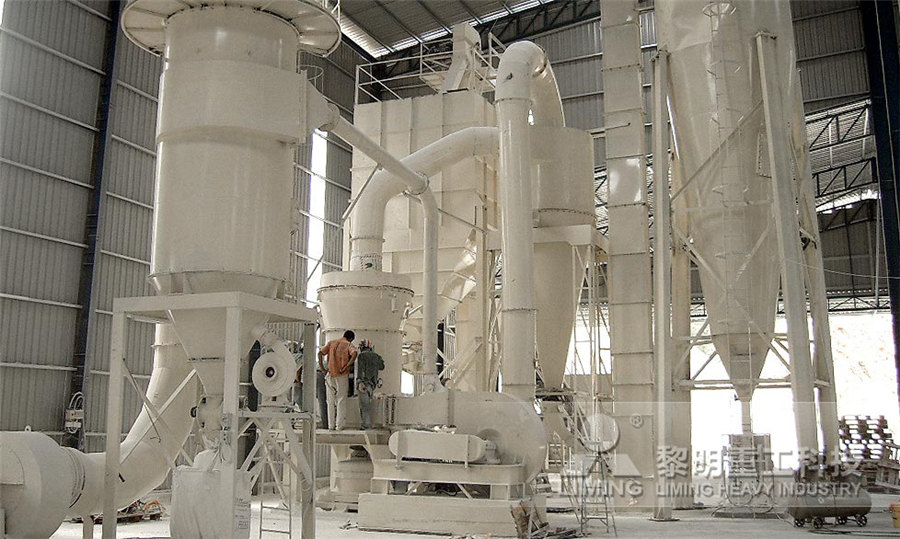
Intro to Size Reduction Schutte Hammermill
thinner hammer and the interior wall of the grinding chamber features a ribbed liner plate This plate has a washboard effect on the material, and works in unison with the hammers and particle on particle impact to reduce the material The biggest difference of course is the group's the use of air assistance to evacuate material from the millVertical mill lining plate is used to protect the coal mill barrel and shell from direct impact and friction At the same time, different forms of lining plate can be used to adjust the motion state of the abrasive body to enhance the grinding effect of the abrasive body on the materialMediumspeed coal mill wearresistant ceramic liner Composite When choosing a coal grinding mill, it is important to consider several factors, including the specific application, grinding requirements, and capacity Factors to consider include the type of material being ground, the desired particle size, the moisture content of the material, What is a Coal Grinding MillVertical Coal Mill (VCM) is equipment for grinding and pulverizing coal into micron size Rotary kilns then use the powders as fuel burners The VCM has a housing section equipped with a lining Technical specifications of vertical roller coal mill
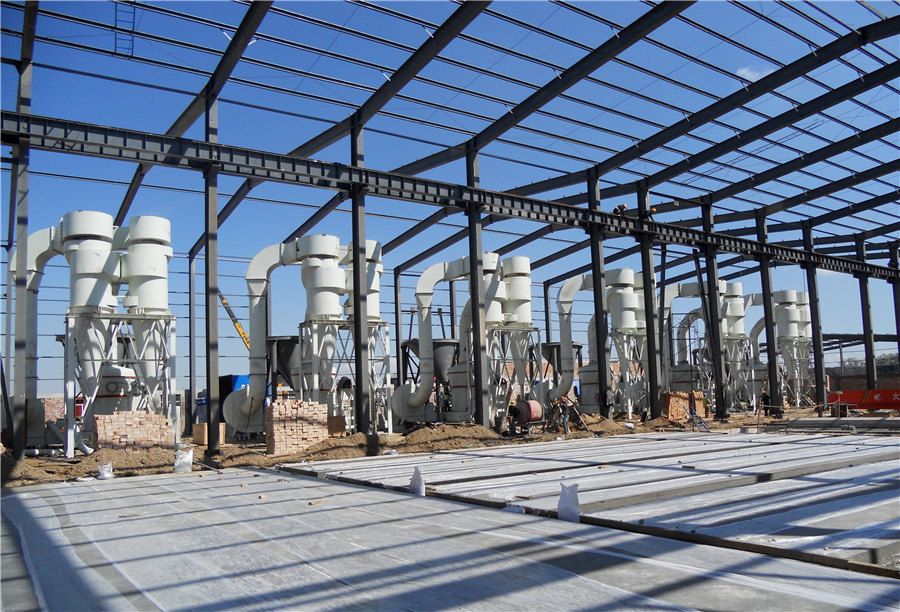
Mill Inerting and Pulverizer/Mill Explosion Mitigation
• Coal characteristics profoundly influence risk – Lower rank coals are generally more easily ignited inside the coal mill – High volatile matter and highly reactive coals encourage preignition inside the mill – Higher moisture content requires temperature extremes inside the mill1800 rpm primary air fan, and four mill outlets supplying pulverized coal to one of the three horizontal rows of (4) dualfuel burners When operating at boiler MCR, each mill had a coal throughput of approximately 53,000 #ffir Specified product fineness was 70% thru 200 mesh and 98% thru 50 mesh Diminishing supply of the original Kansas coalWorldProven Coal Pulverizer Technology Debuts in the US2014年1月1日 Two mill systems are employed for most coal grinding applications in the cement industry These are, on the one hand, vertical roller mills (VRM) that have achieved a share of almost 90% and, on (PDF) MPS mills for coal grinding ResearchGateHere are the 10 ways for your to improve the ball mill performance: Step#1 Change the original grindability Step#2 More crushing and less grinding to reduce the feed size into mill Step#3 Reasonable filling rate of steel ball Step#4 Reasonable size and proportion of steel ball Step#5 Refill steel ball accurately Step#6 Appropriate 10 Ways to Improve the Grinding Efficiency of Your Ball Mill
.jpg)
How it Works: Crushers, Grinding Mills and Pulverizers
2017年6月2日 Autogenous grinding (AG) and semiautogenous grinding (SAG) mills use the material to be ground as the grinding media Autogenous grinding mills use larger rocks to impact and break smaller rocks as the mill rotates 2015年4月9日 Some mills are compartmentalized with each subsequent section having a smaller ball size The material can pass through to the proceeding section, but the balls cannot This ensures that the smaller particles are Grinding Mills and Their Types – IspatGuru2013年8月3日 In Grinding, selecting (calculate) the correct or optimum ball size that allows for the best and optimum/ideal or target grind size to be achieved by your ball mill is an important thing for a Mineral Processing Engineer AKA Calculate and Select Ball Mill Ball Size for Optimum spindle coal pulverising mill’s performance to facilitate optimal plant performance Plant design and mill’s acceptance test data was analysed to understand the design and subsequent changes over the years of the mill’s operation The mill outputs, pulverised coal fineness andPerformance optimisation of vertical spindle coal pulverisers
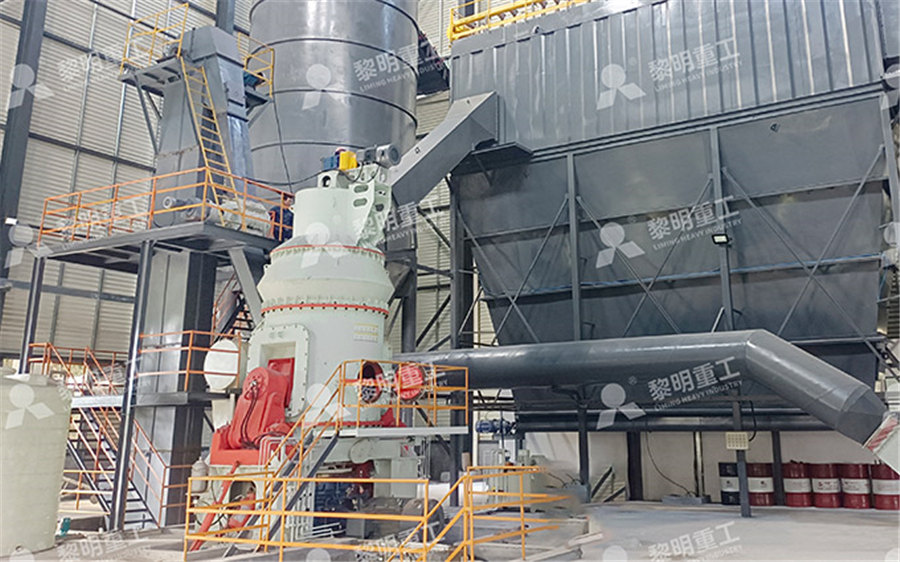
Effect of mill outlet temperature on the coal volatile matter
As one of the three major forces of coal mills, the grinding force exerts a significant impact on the working process of coal mills and parameters like mill current and outlet temperature2016年6月3日 grinding and leaching, as in gold cyanidation circuits; preparation of coalwater and coaloil mixtures; grinding coal tar sludge; and; ultrafine grinding Given the proper feed and the requirement for a fine grind, the Tower mill will show a power savings of up to 50% over a conventional tumbling millTower Mill Operating Work Index 911Metallurgist2022年12月1日 Plates of highmanganese cast steel used for mill lining and beaters of a coal grinding mill: a) inner (IP) and middle plates (MP), b) outer plates (OP) Download : Download highres image (230KB) Download : Download fullsize image; Fig 3 Diagram of mounting plates on the rotor: IP inner plate, MP middle plate, OP outer platesThe wear mechanism of mill beaters for coal grinding madeup used to produce an index relative to the ease of grinding (Hardgrove Grindability Index (HGI)) 111 Some coals, such as some highvolatile bituminous, subbituminous, and lignite coals, can undergo physical change as the natural or seam moisture is released during handling and preparation This change is often sufficient to alter the grindGrindability of Coal by the HardgroveMachine Method1
.jpg)
Analysis of Coal Mill Operation PDF Mill (Grinding) Biomass
This document analyzes the comilling of coal and wood biomass in a ringball mill It describes tests conducted pulverizing hard coal with additions of 8% and 16% pine sawdust at different moisture contents Key findings include: 1) Biomass has weaker grinding properties than coal and increases circulation ratio, layer thickness, and separation area particle concentration in the Safe operation of coal grinding systems: Raw coal silo protection against fire and explosions Safe operation of coal grinding systems: Raw coal yard management The purchasing process for coal grinding systems needs changes Talk at a virtual seminar, November 2023 Accept the probability that the fire and explosion safety of your coal grinding system is nothing more than a mirageSafety Aspects of Coal Grinding Coal Mill Safety, Explosion and