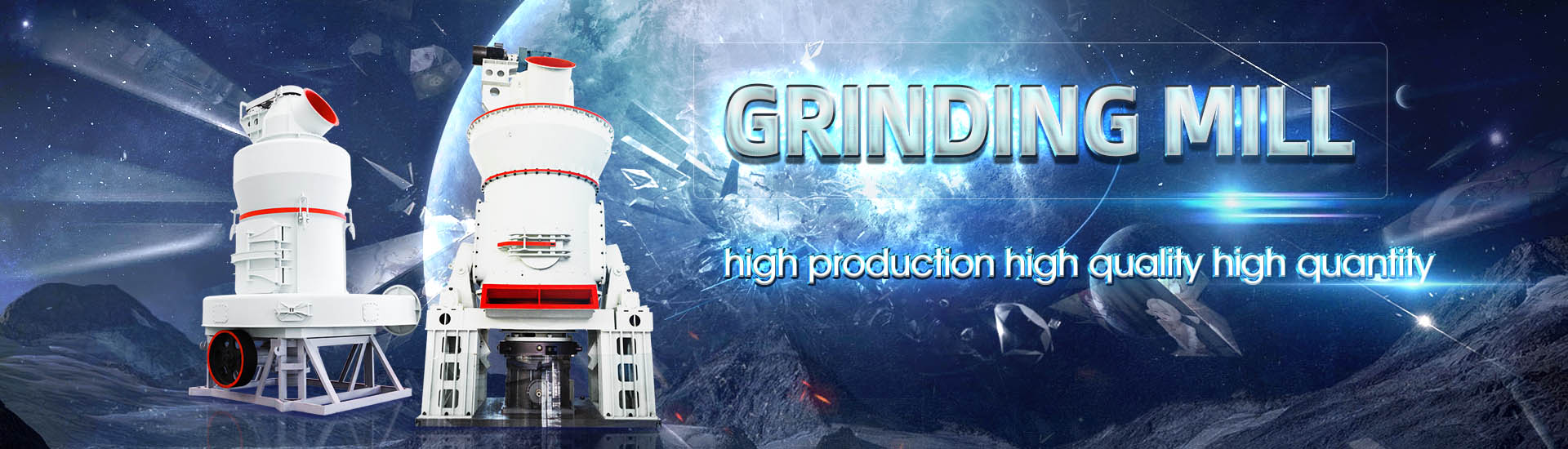
Limestone crusher smelting waste slag treatment technology
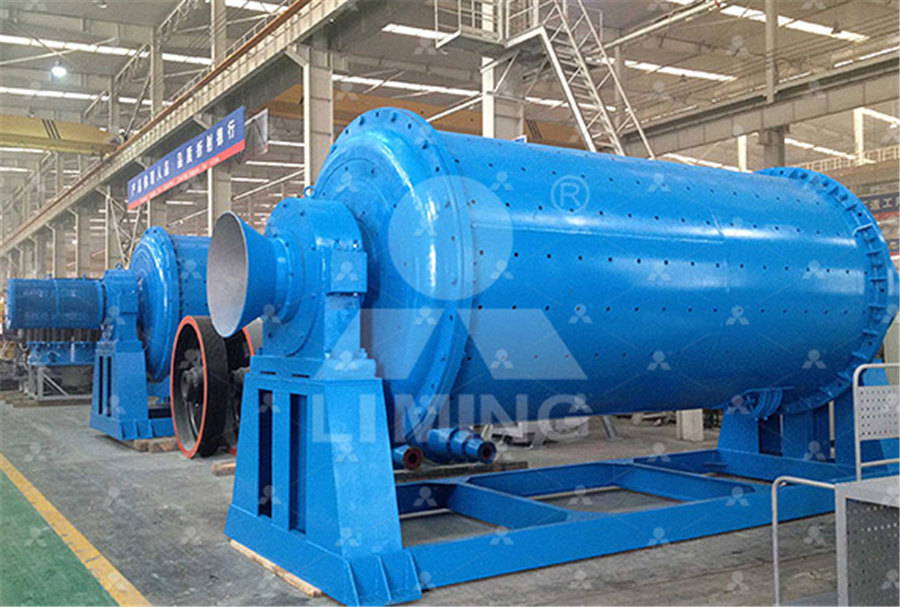
Steel slag in China: Treatment, recycling, and management
2018年8月1日 Steel slag is the oxidized material that is generated when lime, dolomite, and other auxiliary materials are added, and oxygen is blown onto the pig iron produced by a blast 2022年11月1日 Blast furnace slag is the waste slag discharged from smelting pig iron in the blast furnace, belonging to the waterquenched slag It has good potential hydraulic properties Life cycle assessment of melting reduction treatment for iron 2023年10月18日 Harmless treatment technology employs pyrometallurgical treatment, hydrometallurgical treatment, magnetic separation techniques, and stabilization/solidification techniques to recycle valuable components in the Valuable Recovery Technology and Resource Slag is a nonmetallic residue resulting from the iron smelting process, where raw materials such as iron ore, coke, and limestone are fused at high temperatures within a blast furnace During Activation of ultrafine steel slag and ground granulated
.jpg)
Current Development of Slag Valorisation in China Waste
2014年2月19日 In this paper, the current state of iron and steelmaking slags valorisation in China is reviewed The main hot stage slag valorisation processes were introduced to deal 2019年5月23日 Steel slag is the waste generated in the steelmaking process and includes ferric oxide and the impurities of some infusible matters It is the byproduct when slagforming Comprehensive Utilization Technology of Steel Slag2019年12月9日 As a result of extensive RD in this area, the slagprocessing technologies are slowly converging around dry granulation combined with heat recovery In this paper, the slag Granulation and Heat Recovery from Metallurgical Slags2020年6月3日 In this study, Zn/Cubearing smelting slag was recycled via an integrated acid dissolution and hematite precipitation method The slag was dissolved in nitric acid to generate Highpurity recycling of hematite and Zn/Cu mixture from waste smelting
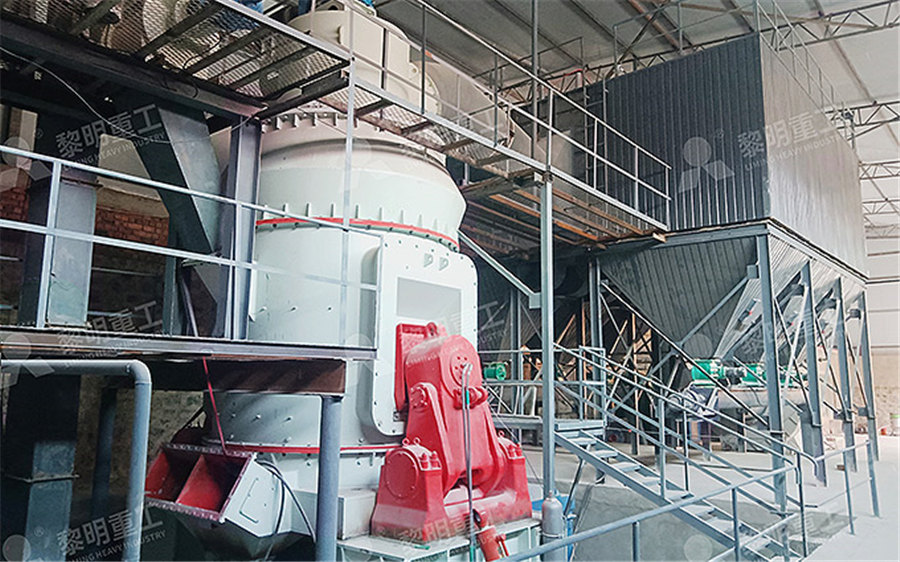
Steel Slag and Limestone as a Rock Filter for
2023年2月8日 The novelty of the current work lies in improving a Vertical Aerated Rock Filter (VARF) using steel slag and limestone media to enhance the efficiency of a rock filter (RF) to eliminate total phosphorus (TP) from domestic 2023年10月18日 As a type of metallurgical solid waste with a significant output, chromiumcontaining metallurgical dust and slag are gaining increasing attention They mainly include stainless steel dust, stainless steel slag, ferrochrome Valuable Recovery Technology and Resource 2017年1月1日 Hughes 2000) Reductive sulfurizing smelting of slag with added CaO has been found conducive to Co recovery (Li et al 2018b) Treatment in slag cleaning furnaces does give rise to dust formation (PDF) Reductivesulfurizing smelting treatment 2020年9月15日 In the georeferenced database built by Kocman et al (2013) more than 3,000 mercury contaminated sites, mostly related to mining (Higueras et al, 2006) and manufacturing (Brocza et al, 2019), have been identified worldwideParticularly in Asia the number of affected facilities and sites (Li et al, 2009) has been increasing due to the unrestricted employment of Mercurybearing wastes: Sources, policies and treatment technologies
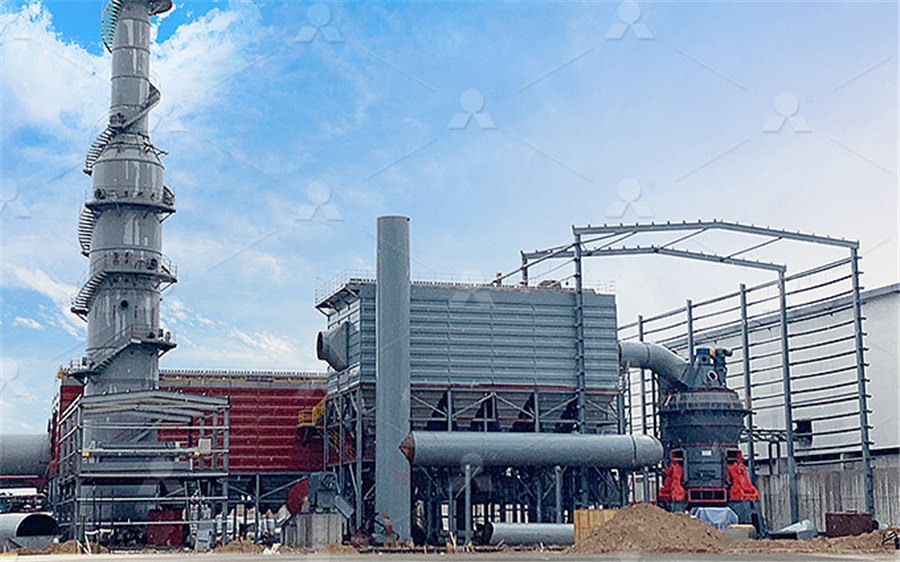
Slag Atomising Technology: Unlocking Real Value
2015年6月15日 The technology is extremely robust, easy to install, and costeffective By air atomising slag into fine, solidified, and cool particles, the operator is able to avoid the safety risks associated with liquid slag handling and water granulation This slag treatment method reduces dust creation and water consumption,2019年2月20日 The Al content in separated silicon is reduced from 7237 ppmw in raw materials to 2423 ppmw by smelting without slag addition and 572 ppmw by smelting with CaOSiO 2 slag treatment Compared with the result by CaOSiO 2 slag, the CaOSiO 2Na 3 AlF 6 slag treatment has a little worse Al removal effect because of the introduction of Separation and purification of silicon from cutting kerfloss 2018年12月1日 Increasing concerns about environmental issues have led to more attention being paid to the recycling of mining wastes and smelting byproducts In the present study, the utilization of gold tailings, waste limestone, red mud, and ferronickel slag was investigated for producing continuous glass fibersTo verify the applicability of the downdrawing process, the Applicability of gold tailings, waste limestone, red mud, and Despite this, many smelting enterprises possess limited recycling and treatment capabilities For instance, a domestic copper refining enterprise generates hundreds of tons of copper slag annually, yet only a minimal amount can be sold to cement plants at a low price of 30 yuan per ton, exacerbated by the high treatment costs, so smelting enterprises mostly choose to pile up Resource utilization strategy of Febearing smelting slag in

Thermodynamic Analysis of Copper Smelting, Considering
2021年5月11日 Practically, the matte grade is adjusted by the ratio of O 2 in the blast to concentrate feed rate, assuming a constant slag composition Due to the fact that the matte grade determines the extent of oxidation of Fe and S, it also determines the extent SO 2 evolution [], and it influences the partitioning of the elements between different phases Fe/SiO 2 ratio: This 2018年6月28日 A novel process was proposed for the separation of Cu and As from Cusmelting waste acid (CSWA) This process includes three steps, namely, the oxidization of As via the addition of H2O2, the selective separation of Cu through the use of Na2S, and the removal of As via the synthesis of scorodite The CSWA was initially oxidized using H2O2 where the As(III) A Novel Process for the Treatment of CopperSmelting Waste 2022年11月1日 Lift cycle assessment (LCA) methodology was applied to evaluating and comparing two waste acid disposal processes in zinc smelting The results indicate that environmental impacts of gas—liquid vulcanization technologies are human toxicity, abiotic depletion potential, and global warming risk, which are mainly caused in neutralizing— Life cycle assessment for waste acid treatment in zinc smelting2016年10月14日 Under the Al2O3FeOSiO2 ternary slag system, at a smelting temperature of 1450 °C, smelting time of 2 h, mass ratio of coke, pyrite, and CaO to waste catalysts of 16, 25, and 0%, respectively Cotreatment of waste smelting slags and gypsum wastes via
36.jpg)
Review on the innovative uses of steel slag for waste minimization
2018年2月5日 Piles of steel slag, a solid waste generated from the iron and steel industry, could be seen due to no utility found for the past century Steel slag has now gained much attention because of its new applications The properties of slag greatly influence its use and thus had got varied applications The chemical composition of steel slag varies as the mineral composition 2021年2月8日 Vegetation reconstruction was widely adopted for the waste slag site But the toxic elements may be made public from slag due to the organic acid secreted by plant roots, which will pollute the surrounding environment and harm human health The purpose of the study was to evaluate the harm of toxic substances released from zinc (Zn) smelting waste slag to Effects of Zinc Smelting Waste Slag Treated with Root2022年2月26日 Blast furnace slag is a solid waste formed by gangue in ore, Swelling bead, also known as slag ball In 1953, Canada studied the technology of producing expanded beads In the production process, a drum with a diameter of 1m, a length of 2M and a speed of about 300 revolutions per minute is installed in front of the furnace to disperse the What is Blast Furnace Slag and How to Process It Eastman Rock Crusher2018年2月5日 Valorization of metallurgical slag as a material for the treatment of polluted water resources has a threefold environmental impact and enhances the sustainability of both the metallurgical industry and watertreatment processes Firstly, the amount of waste slag to be disposed of is reduced; secondly, expensive chemical reagents required for water treatment Valorization of Metallurgical Slag for the Treatment of Water
.jpg)
Detailed opex comparison of modern copper smelting technologies
2019年11月15日 It is well known that there are many ways to process copper concentrates into copper anodes using the pyrometallurgical route All modern copper smelting technologies are fundamentally energy efficient and environmentally safe options, so choosing the right one depends on the desired capacity range, feed impurity levels, plant location, flexibility needs, 2020年1月25日 The development trends of oxygen bottom blowing lead smelting technology are as follows: firstly, the technology is developing towards the direction of largescale production, energysaving and emission reduction, improving labor production efficiency; secondly, the technology is applied to treat various solid wastes comprehensively for The Latest Development of Oxygen Bottom Blowing Lead Smelting Technology2016年5月16日 Reduce, reuse, and recycle are important techniques for waste management These become significant for improving environmental and economic condition of industries Integrated steel industries are generating huge amounts of steel slag as waste through the blast furnace and Linz–Donawitz (LD) process Presently, these wastes are disposed by dumping in Sustainable Approaches for LD Slag Waste Management in 2022年10月1日 A new technology is proposed in which waste cooking oil is used as a reductant to reduce magnetic iron in the copper smelting slag and consequently reduce carbon emissions in the copper smelting Advances in recovery of valuable metals and waste heat from copper slag
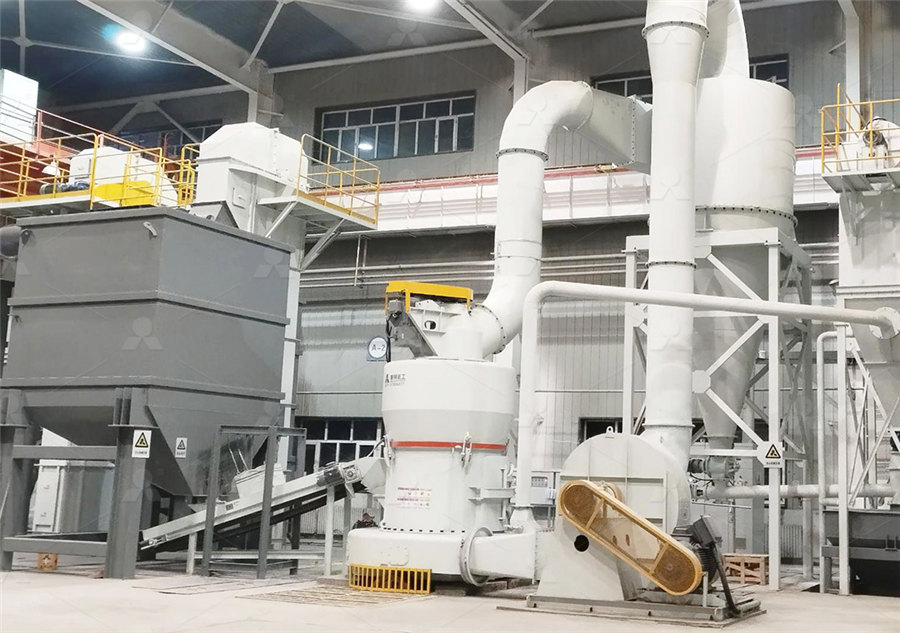
The SPL Waste Management Challenge in
2021年3月16日 The demand for SPL treatment in the US has declined significantly with the decrease of aluminum smelting activities in North America Table XII Estimated SPL generation by aluminum smelters in the US in 2018 2018年11月7日 Steelmaking plants continuously strive to reduce the environmental load in the steelmaking process, resulting in the recycling of energy, water, and other byproducts In this chapter, techniques for the Treatments and Recycling of Metallurgical Slags2021年4月30日 As seen from the test results shown in Table 35, the fluorine in magnesium slag that is generated via the Pidgeon process seriously exceeds the standard limitThus, the slag cannot be landfilled directly because it will cause serious consequences Similarly, with reference to HJ/T2992007 “Solid wasteExtraction procedure for Leaching ToxicitySulfuric acid and Magnesium Slag Generated by Reduction Smelting Using 2023年5月26日 Gypsum sludge refers to a hazardous solid waste produced by the nonferrous smelting industry, and its disposal and utilization are environmentally challenging To investigate the feasibility of replacing limestone with gypsum sludge for smelting slagging, the effect of gypsum sludge and smelting conditions on high lead slag reduction smelting was studied Utilization and detoxification of gypsum sludge by replacing
.jpg)
Review on Comprehensive Recovery Valuable Metals and
2023年3月3日 Copper slag, a waste solid produced in the copper smelting process, is a highquality secondary resource with huge output The recycling and utilization of copper slag is of great interest because it avoids the loss of valuable metals and the threat of harmful metals, and saves a lot of natural resources and energy This paper firstly reviews the main methods for 2023年8月1日 In this study, the energy and exergy of the organic Rankine cycle driven by steel slag waste heat and solar energy were analyzed for various system configurations In the system design, the technology of crushing waste heat pressurized hot smothering technology of steel slag rolls was considered Subsequently, a regenerator was integrated into this system The heat Energy and exergy analysis of waste heat recovery from2023年5月15日 Steel slag is the main solid waste generated in the steelmaking process, accounting for 15 to 20% of crude steel output [1]China's crude steel output in 2021 was 1035 billion tons [2], more than half of the global crude steel output (19505 billion tons) [3], and the steel slag output exceeded 120 million tonsIn contrast, the comprehensive utilization rate of Comprehensive utilization of steel slag: A review2013年7月1日 Steel slag is a byproduct discharged from the steelmaking process, which is characterized by abundant free calcium/magnesium oxide, low cementitious properties, and high contents of heavy metalsTreatment process and utilization technology of steel slag in

A new technological approach to the granulation of slag
2021年11月3日 The technological factors required to improve the operational properties of granulated metallurgical slags demanded in the building industry have been analyzed In order to satisfy these factors, a new technology for hydrovacuum granulation of slag melts (HVG) has been developed It is shown that the main advantage of the proposed HVG process is the 2020年9月24日 Ladle furnaces at Evraz Nizhnii Tagil Iron and Steel Works OJSC produce over 90,000 metric tons of slag per year As this slag cools, it turns into a finegrained powder; if the powder cannot be sold, it is temporarily stored until it can be disposed of [1] We have considered producing easily used flux sinter from the slag generated during ladle processing of steel LadleFurnaceSlag Reprocessing at Evraz Nizhnii Tagil Iron 2023年10月18日 As a type of metallurgical solid waste with a significant output, chromiumcontaining metallurgical dust and slag are gaining increasing attention They mainly include stainless steel dust, stainless steel slag, ferrochrome Valuable Recovery Technology and Resource 2017年1月1日 Hughes 2000) Reductive sulfurizing smelting of slag with added CaO has been found conducive to Co recovery (Li et al 2018b) Treatment in slag cleaning furnaces does give rise to dust formation (PDF) Reductivesulfurizing smelting treatment
.jpg)
Mercurybearing wastes: Sources, policies and treatment technologies
2020年9月15日 In the georeferenced database built by Kocman et al (2013) more than 3,000 mercury contaminated sites, mostly related to mining (Higueras et al, 2006) and manufacturing (Brocza et al, 2019), have been identified worldwideParticularly in Asia the number of affected facilities and sites (Li et al, 2009) has been increasing due to the unrestricted employment of 2015年6月15日 The technology is extremely robust, easy to install, and costeffective By air atomising slag into fine, solidified, and cool particles, the operator is able to avoid the safety risks associated with liquid slag handling and water granulation This slag treatment method reduces dust creation and water consumption,Slag Atomising Technology: Unlocking Real Value2019年2月20日 The Al content in separated silicon is reduced from 7237 ppmw in raw materials to 2423 ppmw by smelting without slag addition and 572 ppmw by smelting with CaOSiO 2 slag treatment Compared with the result by CaOSiO 2 slag, the CaOSiO 2Na 3 AlF 6 slag treatment has a little worse Al removal effect because of the introduction of Separation and purification of silicon from cutting kerfloss 2018年12月1日 Increasing concerns about environmental issues have led to more attention being paid to the recycling of mining wastes and smelting byproducts In the present study, the utilization of gold tailings, waste limestone, red mud, and ferronickel slag was investigated for producing continuous glass fibersTo verify the applicability of the downdrawing process, the Applicability of gold tailings, waste limestone, red mud, and
.jpg)
Resource utilization strategy of Febearing smelting slag in
Despite this, many smelting enterprises possess limited recycling and treatment capabilities For instance, a domestic copper refining enterprise generates hundreds of tons of copper slag annually, yet only a minimal amount can be sold to cement plants at a low price of 30 yuan per ton, exacerbated by the high treatment costs, so smelting enterprises mostly choose to pile up 2021年5月11日 Practically, the matte grade is adjusted by the ratio of O 2 in the blast to concentrate feed rate, assuming a constant slag composition Due to the fact that the matte grade determines the extent of oxidation of Fe and S, it also determines the extent SO 2 evolution [], and it influences the partitioning of the elements between different phases Fe/SiO 2 ratio: This Thermodynamic Analysis of Copper Smelting, Considering 2018年6月28日 A novel process was proposed for the separation of Cu and As from Cusmelting waste acid (CSWA) This process includes three steps, namely, the oxidization of As via the addition of H2O2, the selective separation of Cu through the use of Na2S, and the removal of As via the synthesis of scorodite The CSWA was initially oxidized using H2O2 where the As(III) A Novel Process for the Treatment of CopperSmelting Waste 2022年11月1日 Lift cycle assessment (LCA) methodology was applied to evaluating and comparing two waste acid disposal processes in zinc smelting The results indicate that environmental impacts of gas—liquid vulcanization technologies are human toxicity, abiotic depletion potential, and global warming risk, which are mainly caused in neutralizing— Life cycle assessment for waste acid treatment in zinc smelting