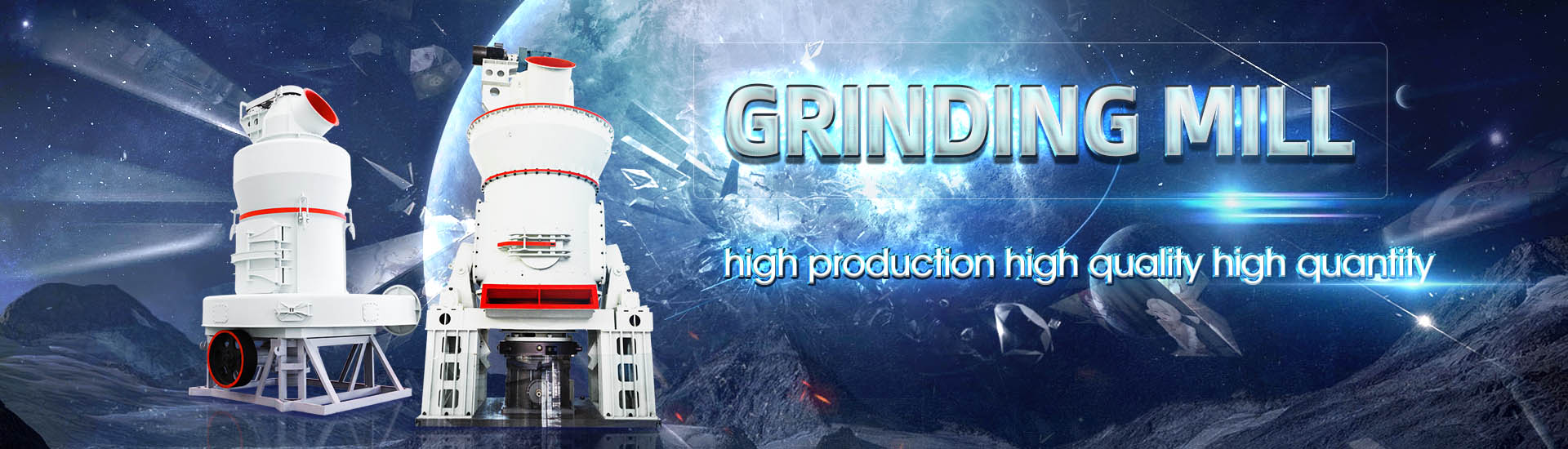
Alkaline furnace lining material powder making process
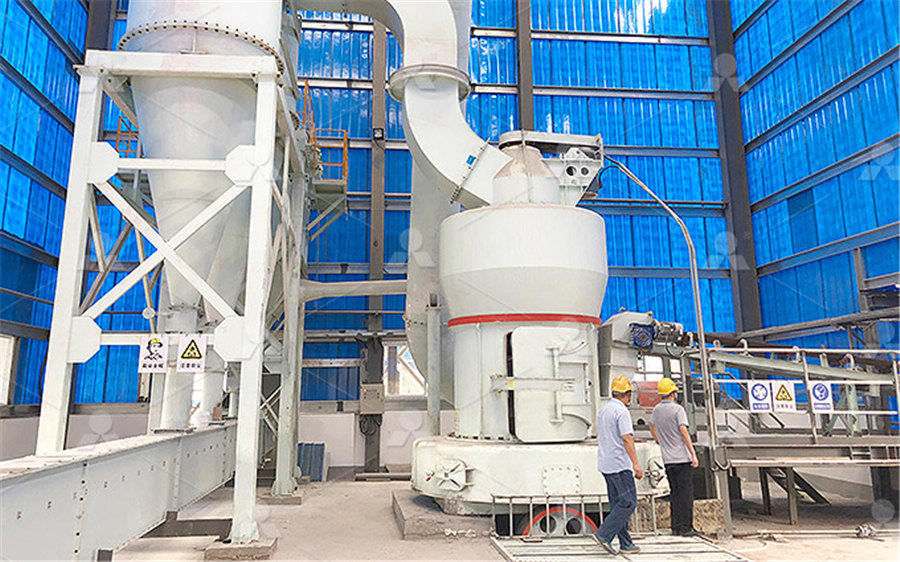
Review articleDesign, fabrication and properties of
2022年3月1日 Lightweight wear lining refractories are generally fabricated by replacing conventional dense aggregates with lightweight aggregates Several process routes, such as partial sintering, insitu decomposition, adding poreforming agent, direct foaming, and 2020年5月15日 Main objective of this thesis is to characterize the physical properties of Alumina (Al2O3) based refractory applied on inductionfurnace lining, which are: to find out the size and PHYSICAL CHARACTERIZATION OF ALUMINA (Al2O3) 2023年6月22日 A new range of silica based lining materials (Reference Figure 1) has been developed utilizing advanced large grain technology (ALGT) The material employs a grain Innovative Refractory Technology for Coreless Induction 2024年6月22日 Lightweight aggregates are the key materials to produce lightweight refractories for the working lining of hightemperature furnaces, which play an important role in the State of the art of lightweight aggregates used in lightweight
.jpg)
Induction Furnace Lining and Industrial Vibrator Design
2024年1月26日 Refractory material lining requires two steps for induction furnaces: Floor portion: Floor material is filled and compacted Wall portion: Liner form is positioned on the 2023年11月23日 This paper reviews the production process, the mineralogical and morphological properties, stabilization techniques, and the applications of ladle furnace (LF) slag One of the prime focuses of waste remediation and Ladle Furnace Slag: Synthesis, Properties, and The melting process of induction furnace is relatively simple Taking smelting alloy steel as an example, after tapping of the previous furnace, furnace body shall be maintained first, Induction Furnace Melting SpringerLink2023年7月5日 Coreless induction furnace is one of the most widely used equipment in the steelmaking sector, while the lining refractory are the key factors in determining the lifetime of Effects of induction furnace conditions on lining refractory
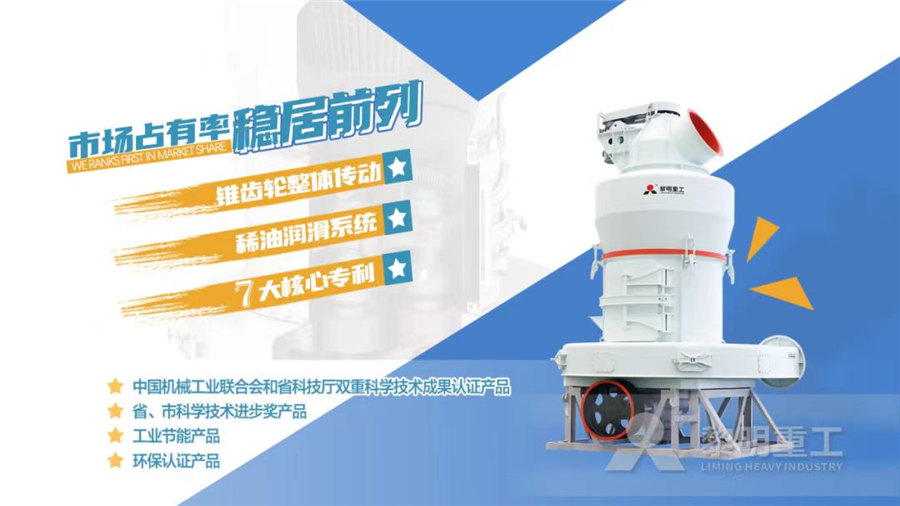
A study on the performance of alkaliactivated materials
2024年1月12日 The raw materials used in the experimental work in this study were LFS produced in the final stage of the steelmaking process in a steel plant in Xinjiang (China) and 2020年3月1日 In an attempt to generate a systematic approach to select FL ceramic materials, an evolutionary screening procedure (ESP) is proposed in this paper, where a multiobjective Materials selection of furnace linings with multicomponent refractory 2015年3月2日 The term ‘basic’ refers to the refractory linings of the furnace which are made of alkaline materials (dolomite and magnesite) Refractory linings must have specific properties to withstand high temperatures, the corrosive Understanding Steel Making Operations in Basic 2023年11月23日 The alkaliactivated curing of LF slag in the presence of metakaolin facilitates the curing at room temperature, making the process energyefficient 59 Lancennotti et al studied alkaliactivated LF slag using NaOH and Ladle Furnace Slag: Synthesis, Properties, and
.jpg)
Refractory Materials for 30 tons Copper Melting Furnace — Lining
2024年8月19日 This material has a good effect on a 16ton industrial frequency copper melting furnace in a copper material factory, and the furnace lining life exceeds three years (more than 700 furnaces)2022年3月1日 The design of lightweight wear linings is crucial in terms of the energy and resource efficiency of industrial furnaces and quality of final products This review aims to present a systematic overview of the design, fabrication, properties, and application of lightweight wear lining refractoriesDesign, fabrication and properties of lightweight wear lining 2017年12月17日 The blast furnace is the most popular iron making process The furnace through the raw materials The alkali in the blast furnace form carbonates, cyanides and silicates at different Effect of alkali on different iron making processes2023年6月22日 furnace: To achieve consistent lining life of coreless induction furnaces, these play very important roles • ATop/Bottom Blocks: Need to check every time before lining to make sure it has tightened properly and in good shape/condition Bad Condition of both top and bottom blocks (Reference Figure 2) directly affects the performance of Innovative Refractory Technology for Coreless Induction
.jpg)
Refractory Lining of Coreless Induction Furnace IspatGuru
2019年9月16日 For the lining of induction furnace, refractory materials are normally monolithic refractories made of dry powder which is required to be compacted with homogenous density Further, there are heat losses by conduction, convection and radiation, and hence the improvement in best refractory material and optimization in wall thickness of Smelting Process 1) The Furnace Lining Materials Required Shall Be Selected According to the Type of Smelting Steel Some steel grades are only suitable for smelting in alkaline furnaces When smelting high manganese steel grades and alloys in an acid furnace, (MnO) will combine with SiO2 in the furnace lining to form a low melting point Induction Furnace Steel Making Hani Metallurgy2018年12月31日 The Alkali metals enter the blast furnace through the raw materials The alkali in the blast furnace form carbonates, cyanides and silicates at different temperature and heights of the furnace(PDF) Effect of alkali on different iron making processes2020年10月19日 According to the raw materials and smelting furnace need different acid and alkaline divided into lining, our factory is using acidic lining Play lining, is to use the material such as quartz sand, the furnace wall do a layer isolation smelting furnace materials and within the induction coils, protect the induction coilsHow to improve the induction furnace lining life
.jpg)
Aluminium melting furnace lining
2019年12月27日 chemical reactions with aluminium lining material, mechanical damage during cleaning oven to remove slag from the walls and hearth of the furnace and; thermal shock, that arise when loading charge The lining in the 2023年6月1日 Materials for Melting Copper and its Alloys CRL65 Mullite forming material with excellent resistance to chemical, thermal and mechanical damage C65 RFL As CRL 65 but with a low temperature bonding system for fritting with a removable former CRL MCR Mullite based lining with excellent resistance to alkali attack Silica 1 Grade Acid lining based on natural Refractories for Induction Furnaces2014年1月1日 The OH process started as an acid process with acid lining in the furnace, and then adopted the basic lining and new steelmaking practice as well The process had two main differences relative to the Bessemer process: (1) pig iron and scrap of any composition could be melted in any ratio and (2) better control of the steel quality was possibleConverter Steelmaking ScienceDirect2016年3月21日 With increasing demand of highquality clean steel, cleanliness is of paramount importance in steel production and casting Tundish plays an important role in controlling the continuously cast steel quality as it links a batch vessel, ladle, to a continuous casting mold Tundish is also the last vessel in which metal flows before solidifying in mold For controlling Tundish Technology for Casting Clean Steel: A Review
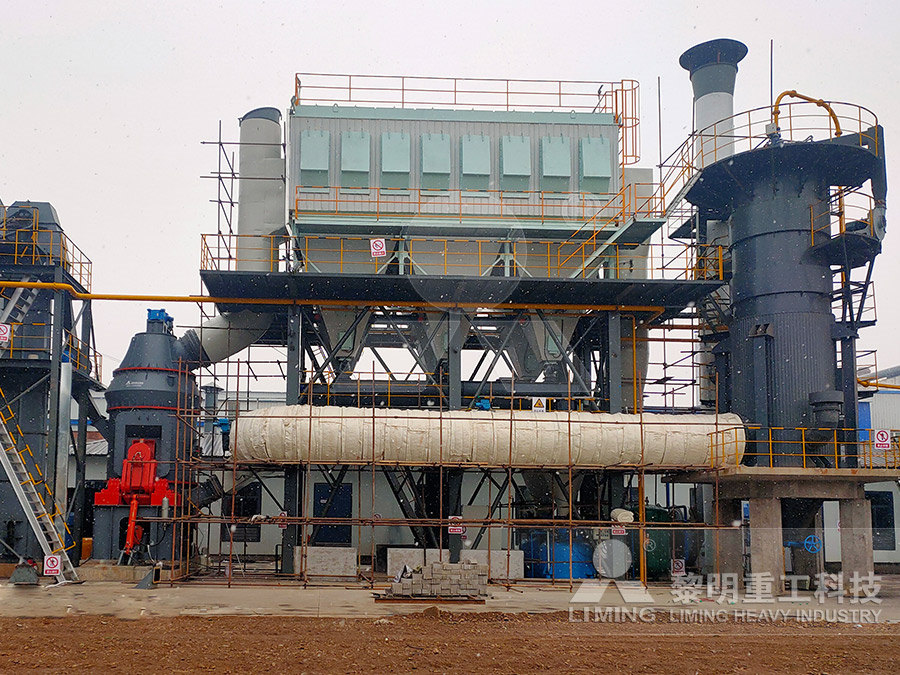
Postmortem Analysis of MagnesiaCarbon Refractories from
2023年10月20日 Thermodynamic calculations were carried out to study the extent of MgO solubility in a ladle furnace slag using FactSage™ v82 FactPS and FToxid databases []Figure 3 illustrates the calculated isothermal section of the Al 2 O 3CaOMgO slag at 1650 °C (stable liquid phase regions corresponding to different SiO 2 contents from 5 wt% to 20 wt% have 2023年12月4日 Thermal Ceramics is a business of Morgan Advanced Materials Five Tips for Achieving Furnace Lining Efficiency By Steve Chernack, Morgan Advanced Materials lining without the proper expansion joints, the brick could grow and end up pushing the entire lining off the furnace wall Tip 5 – Proper installation is key to successFive Tips for Achieving Furnace Lining Efficiency2022年9月3日 CaO and MgO are both reported as effective activators for blast furnace slag However, the synergistic effect of these two components on the mechanical properties of alkaliactivated blast furnace slag remains unclear In this study, the flexural and compressive strengths of alkaliactivated blast furnace slag powder with MgO and CaO range from 0% to 30% by the The Influence of CaO and MgO on the Mechanical Properties of Alkali The lining practice best suited to a particular furnace depends upon the capacity and design of the furnace, operation practice adopted during making of a heat, and furnace output For successful and consistent performance of the lining, the important aspects are (i) use of proper grade and quality of the lining material, (ii) careful and Induction Furnace and Steelmaking IspatGuru
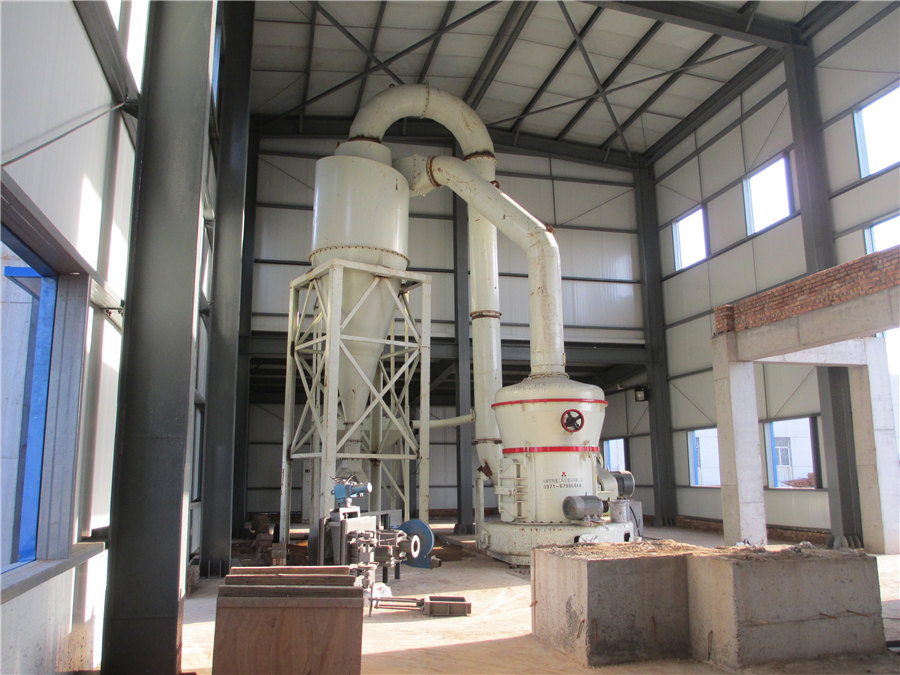
Investigation of Alkaline Hydrolysis in Refractory Linings
2018年7月12日 to alkaline hydrolysis of the castable refractory lining Representative samples of powder material and peeled off refractory layer from the surface were collected for detailed investigation Laboratory characterization and thermal design analysis were conducted to understand the probable causes and mechanisms of the refractory lining degradationMaterials 2022, 15, 6128 2 of 13 environment for 28 days is 13 times of that with Ca(OH)2Moreover, as pointed out in Jin’s study that the blast furnace slag powder with MgO shows lower 1 day The Influence of CaO and MgO on the Mechanical 2016年9月15日 Materials The LS was supplied by SSAB, Finland The asreceived slag was collected prior to being exposed to air humidity or rainy weather The fraction used in this study was an unmilled fine fraction below 8 mm and had a d 50 value of approximately 57 µm The alkalineactivating solution was composed of chemical grade sodium silicate (Na 2 SiO 3) with Alkali Activation of Ladle Slag from SteelMaking Process2022年12月15日 The oxidation of chromium in the solid phase depends on the presence of alkali and alkaline earth metals at high temperatures, whereas sodium, potassium, and calcium salts can cause the oxidation of trivalent chromium to hexavalent chromium [11, 12], thus further promoting the search for alternative refractory materials for alkali recovery Interface behaviour and corrosion behaviour of magnesia
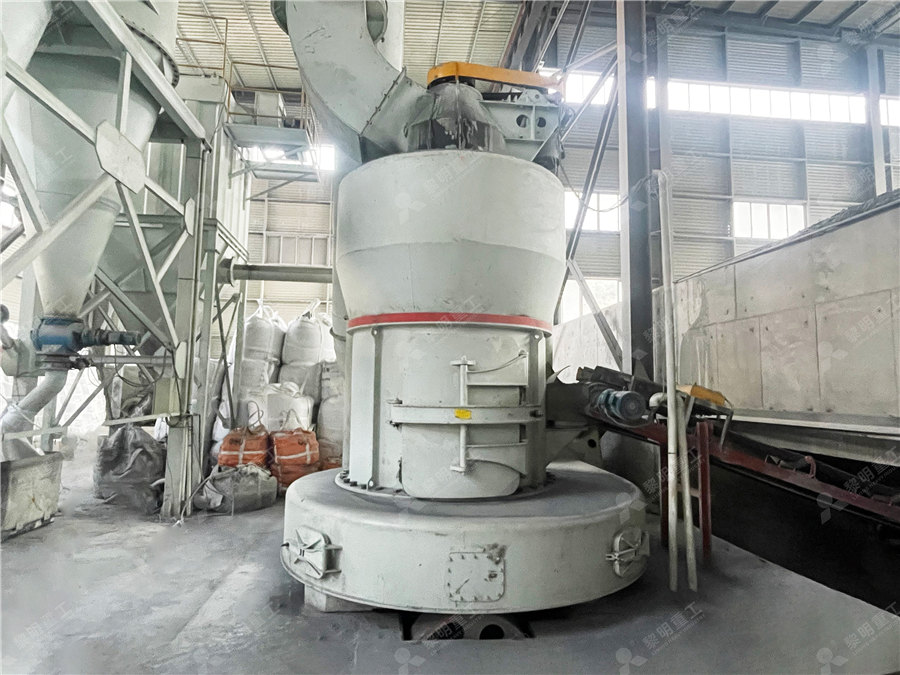
Wear mechanism for blast furnace hearth refractory
2003年1月20日 reaction mechanisms and enhanced refractory lining deterioration for the blast furnace hearth have been identified From an understanding of these wear mechanisms acting upon the hearth2017年12月17日 Citation: Dastidar MG, Sarkar BK, Mitra MK, et al Effect of alkali on different iron making processes Material Sci Eng 2018;2(6):304‒313 DOI: 1015406/mseij20180200075 Alkali effect on blast furnace Among all the iron making processes the blast furnace is the dominant process all over the world The study of alkali is thereforeEffect of alkali on different iron making processes2005年11月30日 The lifetime of a blast furnace (BF), and, consequently, the price of steel, strongly depends on the degradation of micropore carbon refractory materials used as lining materials in the BF hearthWear mechanism for blast furnace hearth refractory lining2020年4月15日 Induction crucible furnaces with industrial frequency (IChT) have been used since the 50s of the last century The performance of the furnaces guarantees temperature that is lower than 1450°C for (PDF) Causes of the Quartzite Lining Destruction during
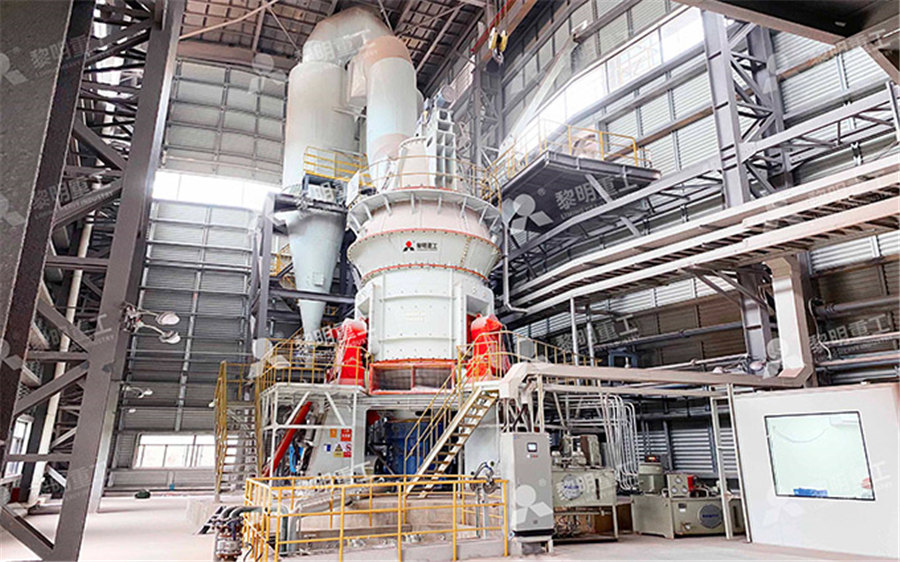
Five Tips for Achieving Furnace Lining Efficiency
2023年11月28日 Make sure the materials have enough studs to hold them in place and have sufficient joints for expansion or shrinkage For instance, if you install a brick Figure 3 Variety of materials used in furnace rebuilds and process equipment Figure 3 Variety of materials used in furnace rebuilds and process equipment2022年11月29日 5 New process and new materials of furnace lining materials ① In the traditional lining materials, ultrafine powder (mostly in a few microns) can improve the corrosion resistance and thermal shock stability of lining materials, such as silicon powder, aluminum oxide powder, white corundum powder, spinel powder, etc ② Dry formingWhat are the types of lining materials for medium frequency furnaces 2024年8月7日 The article describes modern methods for controlling and optimizing the energy mode of melting in electric arc furnaces and units for outoffurnace steel processing using optical emission spectroscopy systems These systems enable the determination of melt and slag temperatures, plasma temperatures in the arc combustion area, and slag composition, as well Potential of controlling the steelmaking process in electric 2019年7月19日 Carbon may also be introduced to a much smaller extent from fluxing materials and other process additives that are charged to the furnace Using the default values in the IPCC Guidelines for iron (004) and steel (001) for the fraction of carbon gives an emission factor of 011 tCO 2 /tcs for carbon removed from the iron as CO 2 Basic Oxygen Furnace: Most Efficient Technologies for Greenhouse
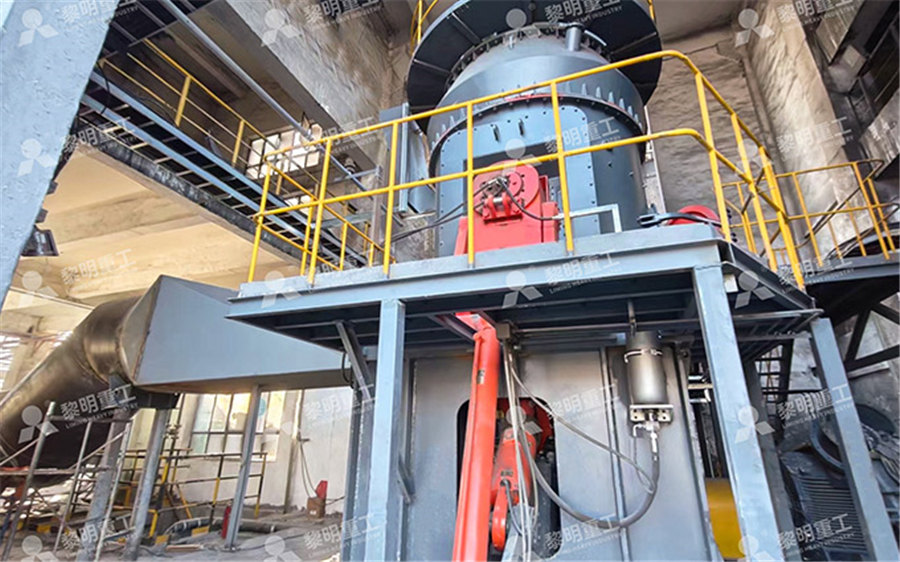
Understanding Steel Making Operations in Basic
2015年3月2日 The term ‘basic’ refers to the refractory linings of the furnace which are made of alkaline materials (dolomite and magnesite) Refractory linings must have specific properties to withstand high temperatures, the corrosive 2023年11月23日 The alkaliactivated curing of LF slag in the presence of metakaolin facilitates the curing at room temperature, making the process energyefficient 59 Lancennotti et al studied alkaliactivated LF slag using NaOH and Ladle Furnace Slag: Synthesis, Properties, and 2024年8月19日 This material has a good effect on a 16ton industrial frequency copper melting furnace in a copper material factory, and the furnace lining life exceeds three years (more than 700 furnaces)Refractory Materials for 30 tons Copper Melting Furnace — Lining 2022年3月1日 The design of lightweight wear linings is crucial in terms of the energy and resource efficiency of industrial furnaces and quality of final products This review aims to present a systematic overview of the design, fabrication, properties, and application of lightweight wear lining refractoriesDesign, fabrication and properties of lightweight wear lining
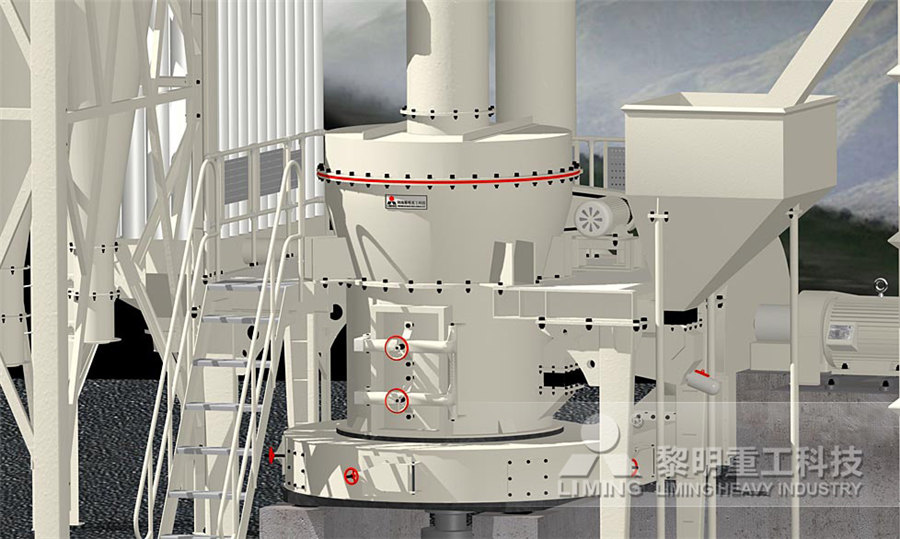
Effect of alkali on different iron making processes
2017年12月17日 The blast furnace is the most popular iron making process The furnace through the raw materials The alkali in the blast furnace form carbonates, cyanides and silicates at different 2023年6月22日 furnace: To achieve consistent lining life of coreless induction furnaces, these play very important roles • ATop/Bottom Blocks: Need to check every time before lining to make sure it has tightened properly and in good shape/condition Bad Condition of both top and bottom blocks (Reference Figure 2) directly affects the performance of Innovative Refractory Technology for Coreless Induction 2019年9月16日 For the lining of induction furnace, refractory materials are normally monolithic refractories made of dry powder which is required to be compacted with homogenous density Further, there are heat losses by conduction, convection and radiation, and hence the improvement in best refractory material and optimization in wall thickness of Refractory Lining of Coreless Induction Furnace IspatGuruSmelting Process 1) The Furnace Lining Materials Required Shall Be Selected According to the Type of Smelting Steel Some steel grades are only suitable for smelting in alkaline furnaces When smelting high manganese steel grades and alloys in an acid furnace, (MnO) will combine with SiO2 in the furnace lining to form a low melting point Induction Furnace Steel Making Hani Metallurgy
.jpg)
(PDF) Effect of alkali on different iron making processes
2018年12月31日 The Alkali metals enter the blast furnace through the raw materials The alkali in the blast furnace form carbonates, cyanides and silicates at different temperature and heights of the furnace2020年10月19日 According to the raw materials and smelting furnace need different acid and alkaline divided into lining, our factory is using acidic lining Play lining, is to use the material such as quartz sand, the furnace wall do a layer isolation smelting furnace materials and within the induction coils, protect the induction coilsHow to improve the induction furnace lining life