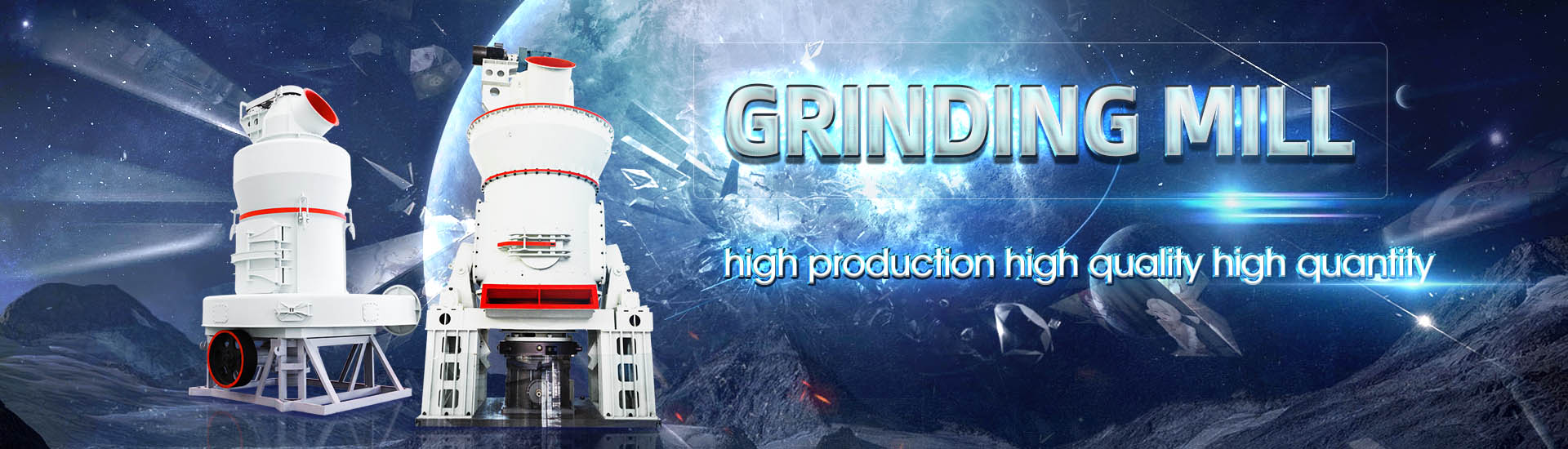
How much does a ball mill consume per ton of cement grinding body
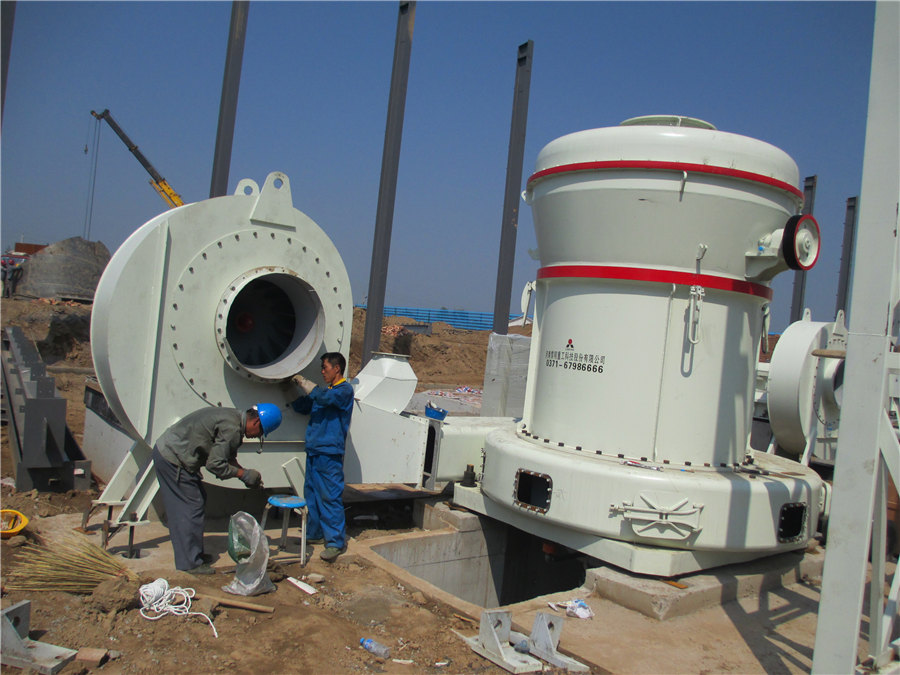
Ball Mill Design/Power Calculation 911Metallurgist
2015年6月19日 A wet grinding ball mill in closed circuit is to be fed 100 TPH of a material with a work index of 15 and a size distribution of 80% passing ¼ inch Optimization of the Cement Ball Mill Operation Optimization addresses the grinding process, maintenance and product quality The objective is to achieve a more efficient operation and OPTIMIZATION OF CEMENT GRINDING OPERATION IN BALL MILLSAs grinding accounts for a sizeable share in a cement plant’s power consumption, optimisation of grinding equipment such as ball mills can provide significant cost and CO 2BALL MILLS Ball mill optimisation Holzinger Consulting2006年3月1日 In the cement industry, the clinker grinding step consumes about onethird of the power required to produce one ton of cement This refers to an average specific power Energy efficiency of cement finish grinding in a dry batch ball mill
.jpg)
Optimization of Cement Grinding Operation in Ball
The consumption of energy by the cement grinding operation amounts to one third of the total electrical energy used for the production of cement The optimization of this process would yield substantial benefits in terms of energy 2023年4月23日 One of the most used tumbling mills is the ball mill This paper reviews different types of grinding media that have been developed and improved over the years and their properties Also(PDF) Grinding Media in Ball MillsA ReviewThe maximum rate of wear of steel balls, using very abrasive materials, is about 03 kg/Mg of material for dry grinding, and 1–15 kg/Mg for wet grinding The normal charge of balls is about Ball Mill an overview ScienceDirect Topics2020年5月1日 In this work, the energy and exergy analyses of a cement ball mill (CBM) were performed and some measurements were carried out in an existing CBM in a cement plant to Energy and exergy analyses for a cement ball mill of a new
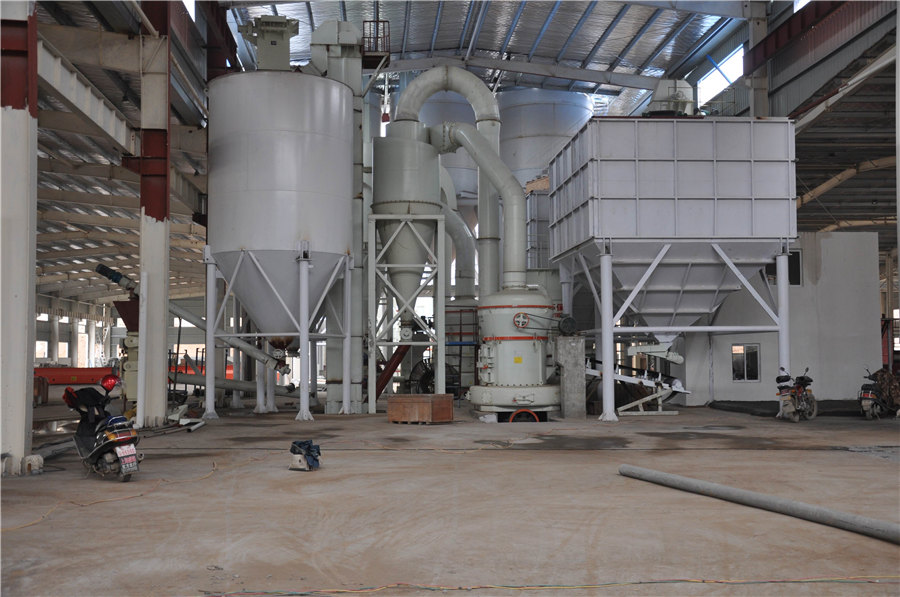
Energy and exergy analyses for a cement ball mill of a new
2020年2月1日 Nowadays, ball mills are used widely in cement plants to grind clinker and gypsum to produce cement In this work, the energy and exergy analyses of a cement ball mill 2017年7月26日 Under the right operating conditions, high power rate crushing can bring mill feed size down to near 80% passing 7,000 microns and finer, which can be handled more How Ball Mill Ore Feed Size Affects Tonnage CapacityFor a ball mill grinding OPC to a fineness of 3200 to 3600 cm2/g (Blaine) the cost of wear parts (ball, liners and mill internals) is typically 015020 EUR per ton of cement For an OK mill grinding a similar product, the cost of wear parts Cement grinding Vertical roller mills VS ball millsBall mills and grinding tools Cement ball mills are typically twochamber mills (Figure 2), where the first chamber has larger media with lifting liners installed, providing the coarse grinding stage, whereas, in the second chamber, medium and fine grinding is carried out with smaller media and classifying linersBALL MILLS Ball mill optimisation Holzinger Consulting
.jpg)
How much does a ball mill with an output of 30 tons per hour
2023年5月29日 The cost of a ball mill with an output of 30 tons per hour can vary based on several factors The size and design of the mill, material of construction, motor power, and auxiliary equipment all 2017年2月13日 The apparent difference in capacities between grinding mills (listed as being the same size) is due to the fact that there is no uniform method of designating the size of a mill, for example: a 5′ x 5′ Ball Mill has a working diameter of 5′ inside the liners and has 20 per cent more capacity than all other ball mills designated as 5′ x 5′ where the shell is 5′ inside diameter and Ball Mills 911Metallurgisto 120⁰ C causes excessive gypsum dehydration media coating if mill ventilation is poorImprovements in New Existing Cement Grinding Mills by Tim 2019年3月8日 212 Pregrinding for Ball Mills Figure 14: Basic Layout of Cement Grinding Using Horomill ® per ton of raw material, IMPROVING THERMAL AND ELECTRIC ENERGY EFFICIENCY AT CEMENT
.jpg)
Crusher Operating Costs: How to Optimize and Reduce
2016年1月11日 It is assumed that power is charged to the plant at the rate of 075d per kilowatthour in the case of the smallest plant, decreasing as the capacity increases to a minimum of 05d per kwhr for the largest The power consumption of a machine or installation is usually expressed in kwhours per ton as being the most convenient method2022年1月1日 The size of grinding media is the primary factor that affects the overall milling efficiency of a ball mill (eg power consumption and particle size breakage)Effect of grinding media on the milling efficiency of a ball mill2020年5月14日 Cement Grinding Packing Cement Mill; Cement Ball Mill; Cement Vertical plant design, cement plant layout, etc But the most important thing is absolutely the cost of a cement factory—how much does it cost to build a cement the total cost of a cement plant is estimated to be US$ 17,000 to US$ 20,000 per ton One How Much Does It Cost To Start A Cement Plant?Fourbody horizontal jar mill The fourbody horizontal tank mill ball mill can be used with four horizontal ball mill tanks with a volume of 3000ml It is mostly used for mixing and grinding laboratory samplesHow much power does a ball mill use? 4 Key Factors to Consider
.jpg)
A Review of the Grinding Media in Ball Mills for Mineral
2023年10月27日 The ball mill is a rotating cylindrical vessel with grinding media inside, which is responsible for breaking the ore particles Grinding media play an important role in the comminution of mineral ores in these mills This work reviews the application of balls in mineral processing as a function of the materials used to manufacture them and the mass loss, as 2021年1月25日 GRINDING BALL USAGE: MEDIA APPLICATION SUITABILITY: Tower Mills: 05”15” grinding balls are recommended The normal top size of media used is 1025mm, but even smaller grinding balls can be Grinding Balls and Other Grinding Media: Key An average paper mill consumes nearly 25 MegaWatts of electricity The pulp making step reuired large amounts of water and electricity Many mills have independent power generators and generate its own electricityHow much electricity does an average paper mill consume?2020年2月1日 Rather than huge expansion, most industries will focus on maximizing resources for maximum pro tability Consequently, a study of the impact of operational parameters on ball mill energy e ciency Energy and exergy analyses for a cement ball mill of a new
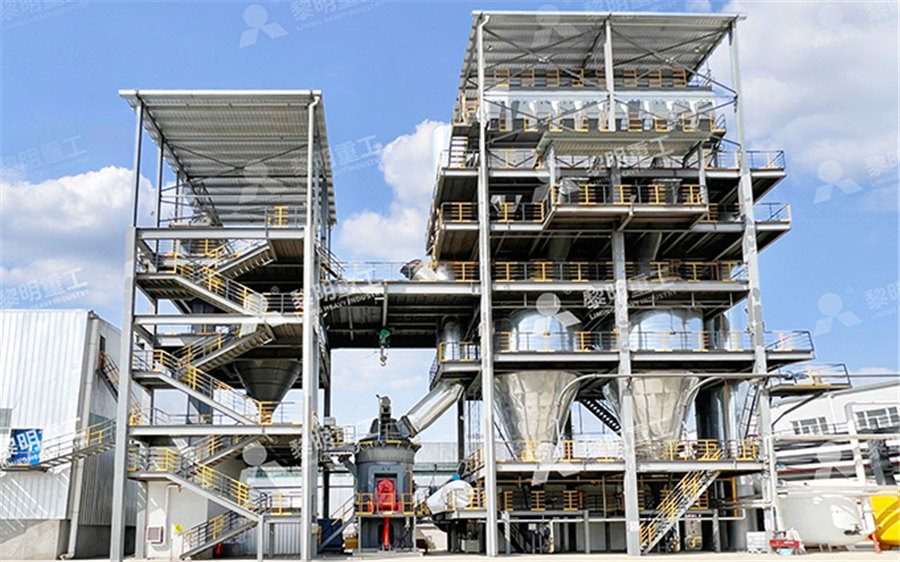
Ball Mill an overview ScienceDirect Topics
The correct sizes are often determined by trial and error, primary grinding usually requiring a graded charge of 105 cm diameter balls, and secondary grinding requiring 52 cm Concha et al (1988) have developed a method to calculate ball mill charge by using a grinding circuit simulator with a model of ball wear in a tumbling mill3 Energy requirements and CO2 emissions of cement production 31 How much CO2 is emitted per ton of cement produced ? Cement production is an energyintensive process due to the high temperatures required to produce clinker in a kiln but also due to the chemical reactions happening during pyroprocessingCement Production Demystified: StepbyStep Process and 2 Saving One Barrel of Oil per Ton (SOBOT) American Iron and Steel Institute, 2005 3 The StateoftheArt Clean Technologies (SOACT) for Steelmaking Handbook, 2nd Edition, Asia Pacific Partnership for Clean Development and Climate, 2010, asiapacificpartnership 4 Calculated from worldsteel LCI database, 2018 5Fact sheet Energy use in the steel industry2017年2月20日 Grinding Mill Specifications Data According to formula 423/√d, where d is equal to internal shell diameter within new liners In this case the thickness used was 60 mm for small mill sizes up to and including 2940 and 80 mm for larger millsGrinding Mill Design Ball Mill Manufacturer 911Metallurgist
.jpg)
(PDF) Power consumption management and simulation of
2022年3月15日 These mills consume enormous amounts of electrical energy (5060%); consequently, comminution costs roughly 60% of the overall investment in a beneficiation plant [2,3]2019年11月18日 mill for cement grinding (4) Electricity consumed by cement mill section 2600 kWh/ton of OPC 1340 MJ/kWh 348 emitting 085092 tons of carbon dioxide per ton of OPC manufactured Study of Energy Use and CO2 Emissions in the ResearchGateWhen dry grinding cement raw material, a protective coating of ground material covers the mill liners and grinding balls It is known that cement raw material is much less abrasive than cement clinker The wear of raw mill liners does not Grinding ball data INFINITY FOR CEMENT 2017年1月17日 produce 580 000 ounces of gold and 600 000 ounces of silver per year After a 2stage crushing, the o re is The grinding process in ball mills is notoriously known to be highly inefficient: Breaking down energy consumption in industrial
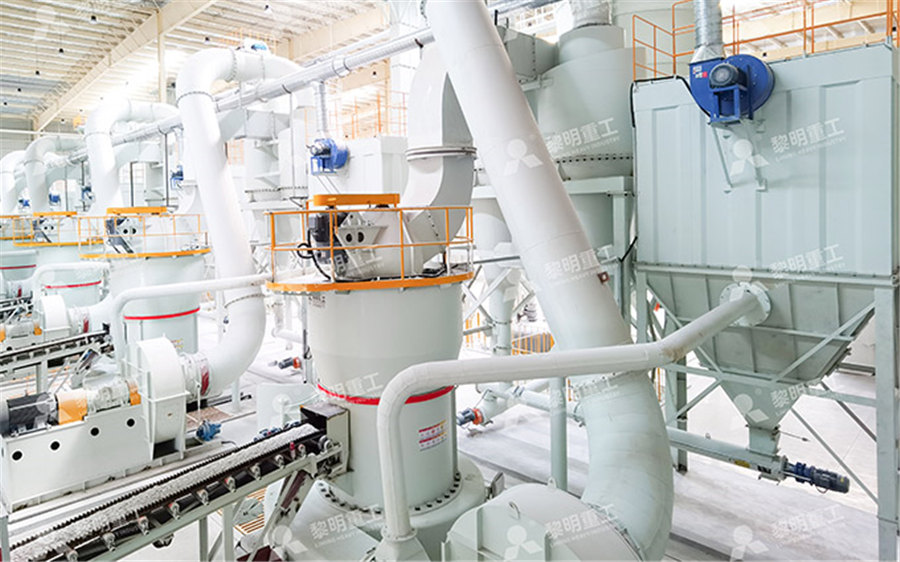
A Comprehensive Guide to Finding the Best Ball Mill for Sale
If you’re in the market for a ball mill, you’re likely looking for a reliable and highquality machine that can handle a wide range of materials and processesBall mills are used for grinding and mixing materials, and they can be found in a variety of industries, from mining and construction to pharmaceuticals and ceramics2015年10月23日 1 Introduction Cement is an energyintensive industry in which the grinding circuits use more than 60 % of the total electrical energy consumed and account for most of the manufacturing cost []The requirements for the cement industry in the future are to reduce the use of energy in grinding and the emission of CO 2 from the kilns In recent years, the production EnergyEfficient Technologies in Cement Grinding IntechOpenIf a ball mill uses little or no water during grinding, it is a ‘dry’ mill If a ball mill uses water during grinding, it is a ‘wet’ mill A typical ball mill will have a drum length that is 1 or 15 times the drum diameter Ball mills with a drum length to diameter ratio greater than 15 are referred to as tube mills Ball mills may be Ball Mill (Ball Mills Explained) saVRee saVReeCement grinding in many plants is done using at least for example a ball mill with dynamic separator in order to The CO2 emissions per ton of cement for each process depend on the Specific fuel and electricity consumption per ton of cement
.jpg)
(PDF) Energy Efficient Ball Mill Circuit – Equipment Sizing
2013年7月15日 Despite reservations of a number of researchers concerning the applicability of Bond's equation for relating specific energy to the size reduction of rocks, his approach has become an industry 2016年3月21日 Pulp Densities Pulp densities indicate by means of a tabulation the percentages of solids (or liquidtosolid ratio) in a sample of pulp This figure is valuable in two ways—directly, because for each unit process and operation in milling the optimum pulp density must be established and maintained, and indirectly, because certain important tonnage calculations are Common Basic Formulas for Mineral Processing Calculations2015年2月16日 Grinding energy was approximately 50 per cent of the ball mill and the drying capabilities allowed direct processing of materials of up to 20 per cent moisture content The main energy issue was the high power consumption of mill fans, with pressure drops of 100mbar not uncommon with high nozzle ring velocities (>70m/s) and internal mill circulating loads of >1000 Best energy consumption International Cement Review2016年10月21日 Grinding media is the working part of a mill It will consume power whether it is doing Rods will be consumed at the rate of 02# per ton on soft easily ground material up to 2# per whereas 4 or 5in balls are more commonly used for ballmill grinding A much higher grinding capacity is obtained in tube mills by using Grinding Balls Rods 911Metallurgist
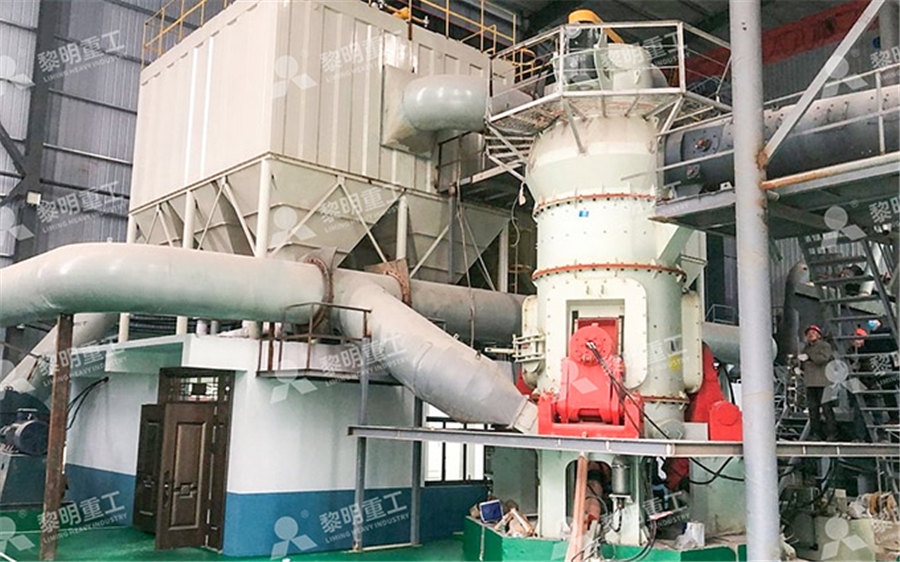
Grinding power : step by step calculation PowderProcess
It is very common in milling application to refer to the size as per the "mesh" measurement The correspondance mesh to microns is given below : US Mesh* Microns Inches Millimeters; 35: 500: 00197: 05: 40: 400: 00165: 04: 45: 354: 00138: 0354: 50: 297: 0 Estimation of the power consumption of a grinding millThe power requirement is depends on the property of the feed and the degree of sizereduction accomplished and is much higher as comparable to other mills and crushers In general, power requirement is between 8 and 80 kWh per ton of Size Reduction1: Grinding – Unit Operations in Food 2021年7月28日 Raw Mill Ball Mill: 2390: Coal Mill Vertical Roller Mill: 1628: Five Stage Preheater Clinkerisation: 17 05: Six+ Stage Preheater Clinkerisation: 4538: Five Stage Preheater Upto Clinkerisation: 4332: Six+ Indian Cement Sector CMA2013年8月1日 The cost associated with grinding media is chiefly determined by two factors, viz the price and wear performance of the grinding media Different operating conditions can be compared with the effective grinding cost or the costeffectiveness of the application (Sepúlveda, 2004)This is a challenging task, since different operating conditions in comminution circuits Consumption of steel grinding media in mills – A review
.jpg)
Energy consumption values of each crusher per tonne
Taking into account formula (5) and table 2, the coefficient of energy of destruction of granite will be 0446 J/m3 or, in terms of kg, 116 kJ/kg2012年7月13日 The production of paper and board is an energy intensive process With an energy use of 64 EJ in 2005, the pulp and paper industry was responsible for about 6 % of the world’s total industrial energy consumption (International Energy Agency (IEA) 2008), being the fourth largest industrial energy user worldwideEnergy prices rose drastically from 2005 until Benchmarking energy use in the paper industry: a benchmarking study A SAG mill is a grinding machine that utilizes steel balls or steel rods in a rotating cylinder to grind materials like rock, ore, and other minerals It is commonly used in the mining and processing industries to grind ores and other materials to the desired size for further processing SAG mills are essential to many industries and are known to be a significant investmentHow Much Does a SAG Mill Cost? ball mills supplier2017年4月29日 911 Metallurgist is a trusted resource for practical insights, solutions, and support in mineral processing engineering, helping industry professionals succeed with proven expertise Grinding Media Wear Rate Calculation in Ball MillGrinding Media Wear Rate Calculation in Ball Mill
.jpg)
cement grinding Unit
Equipment in cement grinding plant The cement grinding machine includes cement vertical mill, cement ball mill, cement roller press, cement seperator, conveyor and other cement equipmentWe can provide scheme design for free according to the requirements of users, and offer appropriate equipment to ensure smooth production with less investment and high profitball mills are used in finish grinding In the ball mills, the clinker and gypsum are fed into one end of a horizontal cylinder and cement exits from the other end Modern ball mills may use between 32 and 37 kWh/ton of electrical energy (Worrell et al, 2013) The power consumption of The Effects of Temperature, Vibration and Dosage on the