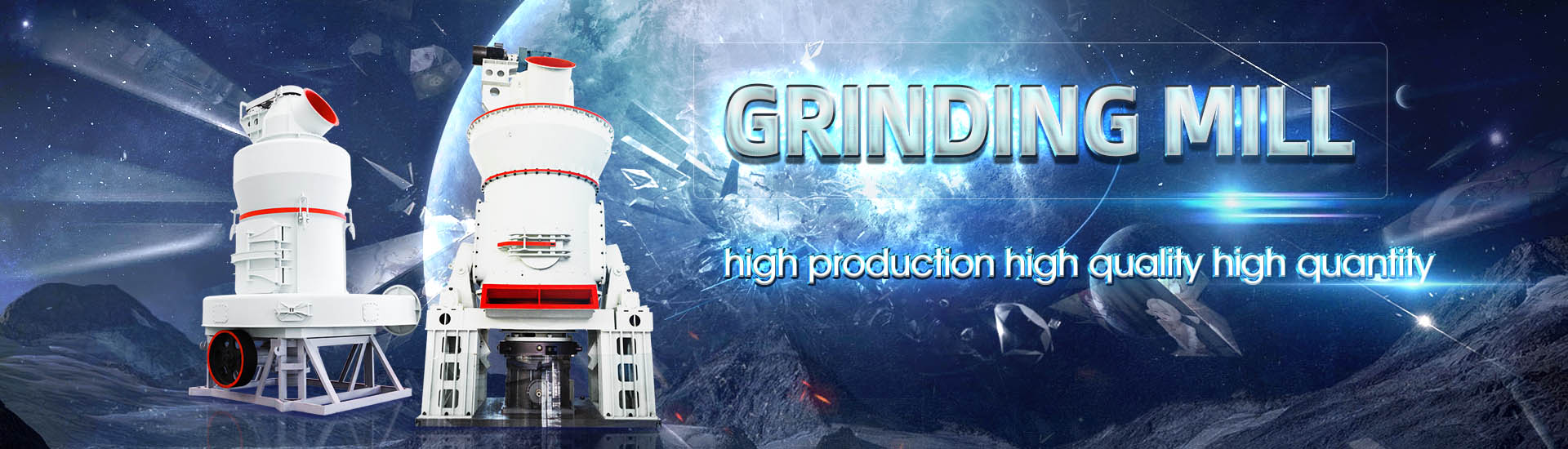
HOME→Vertical abrasive layer thin slag discharge large grinding main reducer current low how to operate
Vertical abrasive layer thin slag discharge large grinding main reducer current low how to operate
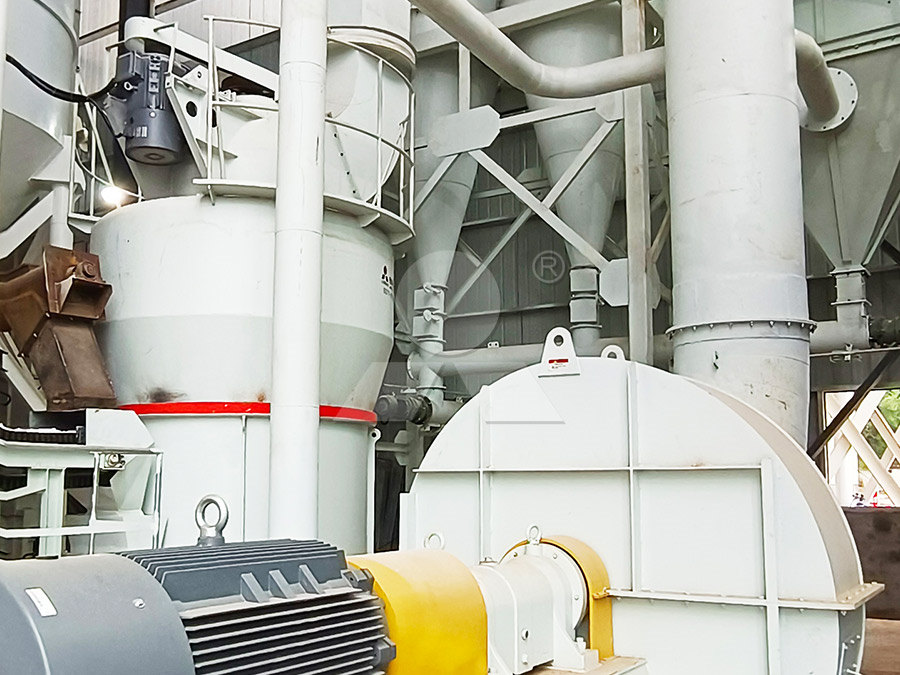
A highshear and lowpressure intelligent precision grinding
2024年5月15日 A super elastic composite abrasive tool (SECAT) that attains highshear and lowpressure grinding modes has been developed to improve surface quality Its contact state 2023年1月1日 The hybrid abrasive electrical discharge grinding process is aimed at providing a machining with good MRR and surface finish The hybridization of EDM with abrasive grinding Advancements in abrasive electrical discharge grinding 2024年3月1日 Propose a multistep grinding process optimization method for hard brittle materials with variable grinding depth Prove the effectiveness of the optimization method and Optimization of grinding process for hard and brittle 2023年10月6日 In electrical discharge diamond grinding, only grains with protrusion heights greater than the width of the interelectrode gap produced material removal behavior on the Material removal mechanism and corresponding models in the grinding
.jpg)
Study on the formation of surface affected layer in grinding
2024年10月16日 The results show that the ground surface is mainly affected by grinding heat, while the grinding sub surface (ie, plastic deformation zone) is greatly affected by plastic 2024年2月2日 To increase the grinding force ratio of tangential to normal force and enhance surface/subsurface quality during silicon grinding, a novel approach employing a newly Study on highshear and lowpressure grinding using a new 2021年7月15日 Based on the clustering effect of shearthickening fluids (STFs), a highshear lowpressure flexible grinding wheel has been developed In order to explore the material Simulation Analysis of Cluster Effect of HighShear Low 2022年5月2日 To improve the machining efficiency and quality, this paper applied the smoothed particle hydrodynamics (SPH) method to simulate the machining behavior of single abrasive Analysis of the highefficiency and lowdamage abrasive
.jpg)
Investigation of material removal in innerjet electrochemical grinding
2017年6月14日 Innerjet ECG with the proposed abrasive tool shows good efficiency and flexibility for processing hardtocut metals with a large removal depth2024年5月1日 Vertical surface grinding (VSG) is an effective method that can adapt to multiple machining tasks, including stock removal machining to get high productivity and finish Force modeling of vertical surface grinding considering 2023年12月29日 Micromachines 2021 % , ) High Simulation Analysis of Cluster Effect of HighShear Low Abstract – Electrical Discharge Grinding (EDG) and conventional abrasive grinding are two different methods to machine Polycrystalline Diamond (PCD) with different removal mechanismsElectrical Discharge Grinding Versus Abrasive Grinding in
.jpg)
Design of Mini Abrasive Vertical Belt Grinding Machine
The main aim of this paper is to design vertical abrasive belts grinding machine to achieve good tolerance as well as better surface finish for various materials such as metal, glass, ceramic 2024年5月16日 Inconel718 alloy is widely used in the manufacture of curved parts in aviation and aerospace domain due to its excellent thermal and structural properties The traditional grinding methods frequently results in low machinability such as grinding burns, surface scratches and clogging in grinding wheel for difficulttomachine materials In this work, to eliminate the Study on HighShear and LowPressure Grinding Using 2020年9月22日 In abrasive belt grinding Titanium alloy blade of aviation engine experiment, through the single factor experiment method, the influence of abrasive belt linear speed and workpiece feeding speed (PDF) Design of Mini Abrasive Vertical Belt Grinding Machine 2008年3月3日 The use of GGBFS as a partial Portland cement replacement takes advantage of the energy invested in the slagmaking process and its corresponding benefits with respect to the enhanced cementitious properties of the slag Grinding slag for cement replacement requires only about 25% of the energy needed to manufacture normal Portland cementEfficient and reliable handling of GBFS and GGBFS at grinding
.jpg)
Onmachine electric discharge truing of small ballend fine
2019年10月1日 Wang et al [23] carried out EDM truing experiments on the small ballend fine diamond abrasive grinding wheel and analyzed the relationship between the electrical parameters and contour accuracy 2015年10月12日 Electrical discharge grinding (EDG) and conventional abrasive grinding are two different methods to machine polycrystalline diamond (PCD) with different removal mechanisms This paper discussed the quality issues of PCD tools produced by the two processes Although remarkably similar surface roughness and tool sharpness were obtained in both processes, it Electrical discharge grinding versus abrasive grinding in 2024年6月9日 Highprecision dressing of coarsegrained arcshaped diamond grinding wheels is one of the research hotspots in the field of precision grinding However, the dressing of coarsegrained grinding wheels is very difficult The electrical discharge aided grinding (EDAG) dressing technology has been innovatively proposed, which can achieve high efficiency and precision Precision dressing of arcshaped coarsegrained diamond 2023年11月4日 Preparation of abrasive tools and abrasive layer As shown in Fig 1, the novel abrasive tool consists of the wheel matrix, the clamping pieces, bolts, and the abrasive layerDevelopment of novel highshear and lowpressure
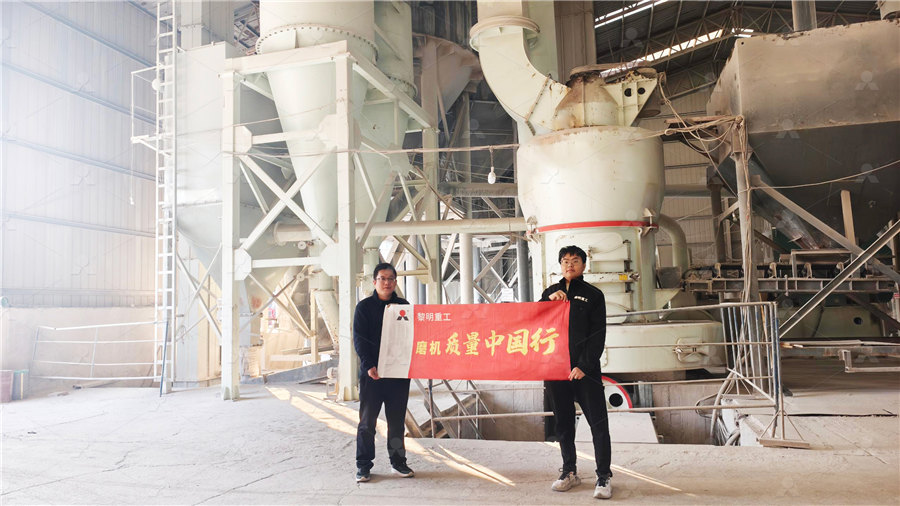
How does the vertical mill grind steel slag? hcmilling
2023年11月28日 Steel slag grinding is an important link in the steel slag treatment and comprehensive utilization process It is generally believed that steel slag has a glass body structure, high iron content, and high product fineness requirements, making it difficult to grind using vertical mills However, ball mill grinding steel slag requires predrying and the process 5 天之前 The following refers to bonded abrasives (grinding wheels, etc) and coated abrasives, where the abrasive or grinding agent consists of grit small particles usually of aluminum oxide (Al2O3), or silicon carbide (SiC) In bonded abrasives, the grains are bonded with phenolic resin or ceramics (vitrified wheels) to form a slightly porousPocket Guide to Grinding Technique Atlas Copco2024年5月15日 The nonNewtonian fluids and abrasive grains are mixed with a proper proportion to constitute the abrasive system The preparation process of an efficient abrasive layer has been discussed in our previous studies [26,27,28,29]Table 1 shows the components and conditions of the abrasive layer The compact warp and weft strands of the Kevlar 29 A highshear and lowpressure intelligent precision grinding 2018年4月12日 Over the last century, substantial advances have been made, based on improved understanding of the requirements of grinding processes, machines, control systems, materials, abrasives, wheel preparation, coolants, lubricants, and coolant delivery This paper reviews a selection of areas in which the application of scientific principles and engineering Towards High Productivity in Precision Grinding MDPI
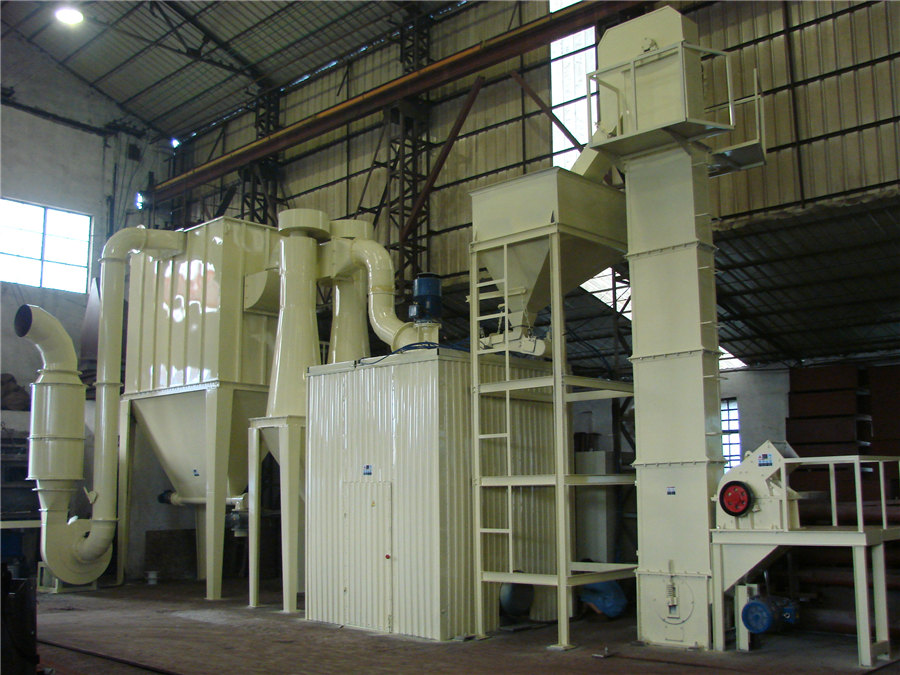
Electric discharge milling: a stateoftheart review
2021年8月19日 Electric discharge machining (EDM) is widely used to fabricate complex 3D geometries with a high aspect ratio in electrically conductive hard materials EDMmilling (EDMM) is an advancement of EDM which can cut complex features at the microlevel with high accuracy and precision This study reports an overview of EDMM in micro and macrodomain with 2016年1月28日 Stereoscopic SEM pictures even give detailed information about abrasive layer profile and potential cutting edges [MATS75] The disadvantage is, however, that the abrasive layer has to fit into the SEM chamber, be cleaned for the chamber vacuum, and potentially be coated with conductive gold or graphite coatings 6223 Other MethodsGrinding Wheel Microdesign—Abrasive Layer and Wear2022年8月1日 A hybrid machining process that combines the working principles of conventional abrasive grinder and an electrical discharge machine, mentioned as Abrasive Electrical Discharge Grinding (AEDG) is Advancements in abrasive electrical discharge grinding 2019年11月9日 Surface quality of workpiece could be significantly improved by ELID grinding However, ELID grinding bearing outer ring raceway with small inner diameter has small space, which limits installation of electrode In this work, ELID grinding bearing outer ring raceway acting as cathode is proposed But electric spark discharge will occur in ELID grinding with workpiece Influence of oxide layer on grinding quality in ELID grinding
.jpg)
Advancements in abrasive electrical discharge grinding
2023年1月1日 E Ya Grodzinskii conducted experiments around Electrical discharge machining along abrasive grinding around, as cited by P Koshy, et al [4], which Grodzinskii called Electrical Discharge Diamond Grinding (EDDG)Koshy et al explains the mechanism of the hybrid EDDG process, and how this mechanism improved the machining quality and rate through hybridization2023年9月15日 In view of the high specific removal energy, high heat generation rate, low heat transfer efficiency, and easytoproduce local hightemperature and grinding burns, new macrostructured grinding wheel forms were proposed, namely, large spiral angle grooved grinding wheels (LSGGW, β>85°) and large spiral angle flow disturbance grooved wheels (LSDG Study on flow field and convective heat transfer 2020年8月12日 This study proposes a novel motion optimization method for a manipulator equipped with a soft robotic hand for object transportation The flexibility of the soft robotic hand induces large vibrationsForce controlbased vibration suppression in robotic grinding of large 2010年4月19日 Electrical discharge diamond grinding (EDDG), which integrates diamond grinding and electrodischarge machining (EDM), is a new hybrid machining process for shaping electrically conductive very (PDF) Electrodischarge Grinding: Energy
.jpg)
Developments in Electrical Discharge Grinding
2014年4月28日 Electrical Discharge Grinding is a very complex hybrid machining process of electrical discharge machining and grinding which is suitable for machining of flat surface materials by generating the 2020年4月16日 In this work, we reported a novel grinding method with high tangential grinding force and low normal grinding force using specially developed grinding tools The tools were made of flexible composites based on the principle of liquid body armor and the shear thickening mechanism of nonNewtonian fluid During grinding, abrasive particles are capable of Experimental investigation on highshear and lowpressure grinding 2020年7月16日 Gasquenched steel slag abrasive was obtained by gas quenching with hightemperature liquid steel slag as raw material The phase composition, thermal properties, micromorphology, magnetic properties, and mechanical properties of the particles were characterized by using an Xray diffractometer, a differential thermal analyzer, a scanning Structure characterization and grinding performance of gas 21 Inconel 718 workpiece The average grain size of Inconel 718 is about 90 μm; Fig 1 shows the scanning electron microscope (SEM) image of the workpiece The chemical compositions and properties of the material are respectively listed in Tables 1 and 2The Inconel 718 workpiece is cut into small pieces with dimensions of 10 mm × 10 mm × 2 mm using wire EDMSurface integrity of Inconel 718 in electrical discharge grinding
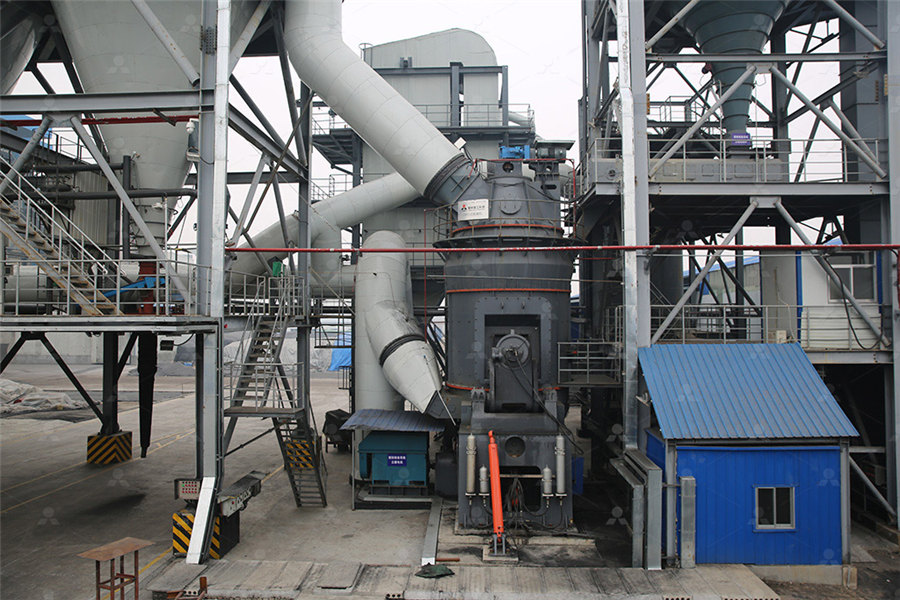
Towards Sustainable Grinding of DifficulttoCut Alloys—A
2024年3月11日 31 Development of Grinding Techniques Grinding is the most commonly used technology in abrasive machining and one of the most critical technologies for precision manufacturing difficulttocut alloys such as superalloys [2, 15, 31] and titanium alloys [32, 33] with high strengthIt is meaningful to study and improve the sustainability of grinding technology2024年2月2日 Figure 2a–f shows a comparative illustration of the highshear and lowpressure grinding principle using the previous BAAT with the metal substrate and the new BAAT with combined elastomer and metal substrates It includes the three recycling stages, ie, the initial stage, the aggregation stage, and the recovery stage [28,29,30]In the initial stage, the Study on highshear and lowpressure grinding using a new 2022年1月11日 Gas drainage through underground boreholes is the main method for gas control and utilization in soft high gassy seam However, this method has technical problems including shallow drilling depth, low drilling efficiency, and frequent engineering accidents This paper proposes a prismatic grooved drill pipe To verify its slag discharge effect, a numerical Slag discharge characteristics and engineering application of 2024年8月30日 As shown in Fig 1 (a), the liquidbodyarmorlike grinding wheel consists of an abrasive layer, an elastomer, and a substrateThe abrasive layer is a highperformance fiber impregnated with the abrasive system, as illustrated in Fig 1 (c) As shown in Fig 1 (d), when the abrasive layer is in contact with the workpiece surface and undergoes relative motion, the Modeling and simulation of temperature field in highshear and low
.jpg)
Simulation Analysis of Cluster Effect of HighShear Low
2023年12月29日 Micromachines 2021 % , ) High Abstract – Electrical Discharge Grinding (EDG) and conventional abrasive grinding are two different methods to machine Polycrystalline Diamond (PCD) with different removal mechanismsElectrical Discharge Grinding Versus Abrasive Grinding in The main aim of this paper is to design vertical abrasive belts grinding machine to achieve good tolerance as well as better surface finish for various materials such as metal, glass, ceramic Design of Mini Abrasive Vertical Belt Grinding Machine2024年5月16日 Inconel718 alloy is widely used in the manufacture of curved parts in aviation and aerospace domain due to its excellent thermal and structural properties The traditional grinding methods frequently results in low machinability such as grinding burns, surface scratches and clogging in grinding wheel for difficulttomachine materials In this work, to eliminate the Study on HighShear and LowPressure Grinding Using
.jpg)
(PDF) Design of Mini Abrasive Vertical Belt Grinding Machine
2020年9月22日 In abrasive belt grinding Titanium alloy blade of aviation engine experiment, through the single factor experiment method, the influence of abrasive belt linear speed and workpiece feeding speed 2008年3月3日 The use of GGBFS as a partial Portland cement replacement takes advantage of the energy invested in the slagmaking process and its corresponding benefits with respect to the enhanced cementitious properties of the slag Grinding slag for cement replacement requires only about 25% of the energy needed to manufacture normal Portland cementEfficient and reliable handling of GBFS and GGBFS at grinding 2019年10月1日 Wang et al [23] carried out EDM truing experiments on the small ballend fine diamond abrasive grinding wheel and analyzed the relationship between the electrical parameters and contour accuracy Onmachine electric discharge truing of small ballend fine 2015年10月12日 Electrical discharge grinding (EDG) and conventional abrasive grinding are two different methods to machine polycrystalline diamond (PCD) with different removal mechanisms This paper discussed the quality issues of PCD tools produced by the two processes Although remarkably similar surface roughness and tool sharpness were obtained in both processes, it Electrical discharge grinding versus abrasive grinding in
.jpg)
Precision dressing of arcshaped coarsegrained diamond
2024年6月9日 Highprecision dressing of coarsegrained arcshaped diamond grinding wheels is one of the research hotspots in the field of precision grinding However, the dressing of coarsegrained grinding wheels is very difficult The electrical discharge aided grinding (EDAG) dressing technology has been innovatively proposed, which can achieve high efficiency and precision 2023年11月4日 Preparation of abrasive tools and abrasive layer As shown in Fig 1, the novel abrasive tool consists of the wheel matrix, the clamping pieces, bolts, and the abrasive layerDevelopment of novel highshear and lowpressure