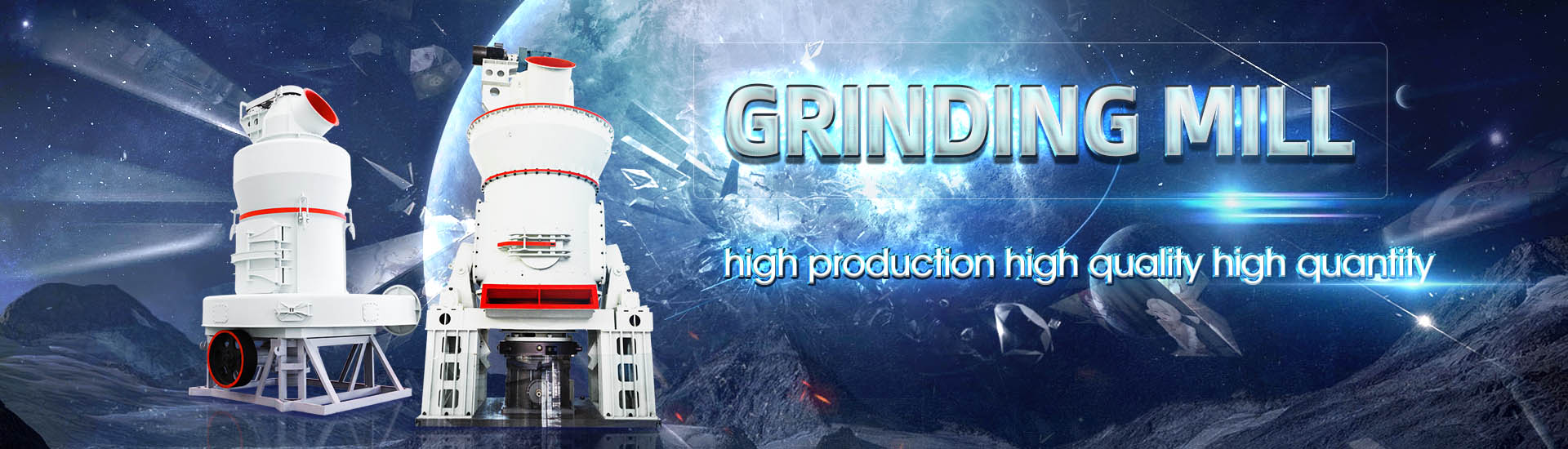
Coal mill maintenance pictures
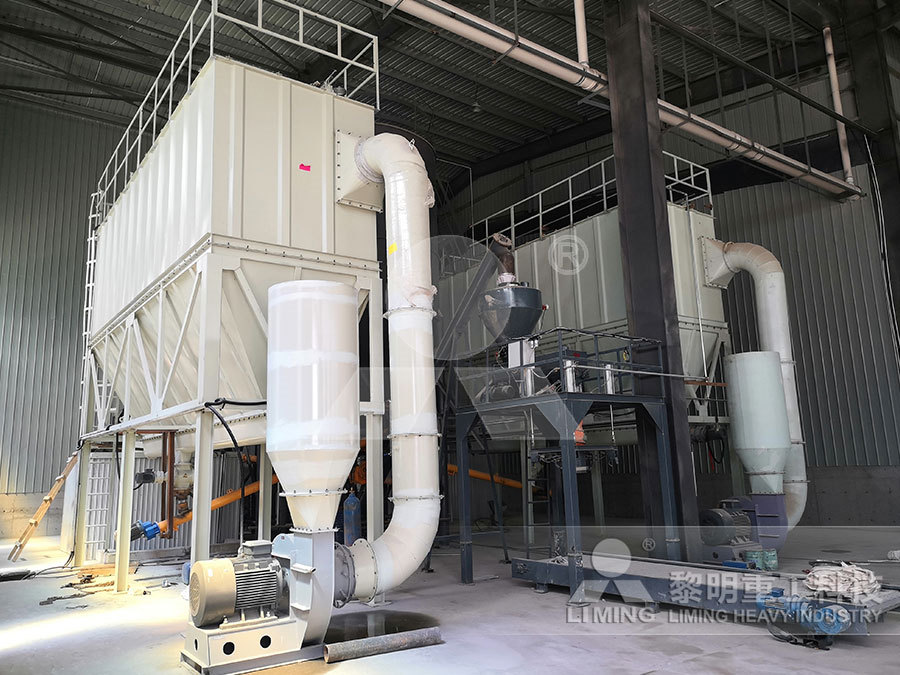
Operation Maintenance of Coal Mills Feeders National
6 天之前 Maintenance planning for Milling system Routine Maintenance and Breakdown Maintenance of Milling Plant Overhauling of Milling Plant Preventive measures for stopping Find Download Free Graphic Resources for Coal Mining Equipment Maintenance Vectors, Stock Photos PSD files Free for commercial use High Quality ImagesCoal Mining Equipment Maintenance Images Freepik2024年10月31日 Regular Maintenance: Routine maintenance of coal mills and associated equipment is vital for preventing mechanical failures This includes inspecting and replacing Coal Mill Safety: A Critical Aspect of Power Plant Operations Coal 2011年1月1日 Analyze technical characteristics of coal handling system and operating characteristics of the relevant machinery and equipment Then, the safe operation of coal Operation and Maintenance of Coal Handling System in Thermal Power
.jpg)
LOESCHEMILLS
2017年8月12日 Individual grinding mill design with a proven track record, encompassing 2, 3 and 4 rollers for fuel throughput rates up to and in excess of 200 t/h Pressure shock 2024年11月11日 It is very vital to do a good job in the maintenance of the coal mill Bearing bush is one of the important parts of ball mill for coal grinding It usually fails due to excessive temperature, which is caused by many factors How To Maintain a Coal Pulverizer? (All You 2023年8月28日 With enhanced grinding efficiency, reliable and safe operation, precise control, low maintenance requirements, and commitment to environmental sustainability, Bellian Coal Mill in Thermal Power Plant: Enhancing Efficiency and 1998年3月30日 This paper describes how an integrated approach to maintenance of the Babcock 10E Coal Mill has been developed at National Power's Blyth 'B' Station on the North An integrated maintenance strategy for the Babcock 10E Coal Mill
.jpg)
Quality Assured Maintenance Management For Coal
2015年10月8日 Maintenance of coal handling plants (CHP) of thermal power stations has traditionally as the processes related to the performance of routine, unscheduled and 2024年11月25日 We’re a world leader in coal pulverizing and boiler mill operations for horizontal and vertical boiler mills—committed to highefficiency performance, reduced maintenance costs, and longer time between outagesBoiler Mill and Coal Pulverizer Performance GE 2018年6月3日 Optimum raw coal feed size for EL pulverizers is ¾” to 1” Raw coal feed should never exceed 1¼”, raw coal this size can plug throats and cause vibration Raw coal that is too fine can plug the pulverizer or delivery components upstream of the pulverizer Regular yard crusher inspection and maintenance is required to maintain optimum rawOptimum Operation and Maintenance of EL PulverizersOur ATOX® Coal Mill is a compact vertical roller mill that can grind almost any type of raw coal The coal mill utilises compression and shear force generated between the large rollers and the rotating table to crush and grind raw coal, ATOX® Coal Mill FLSmidth Cement
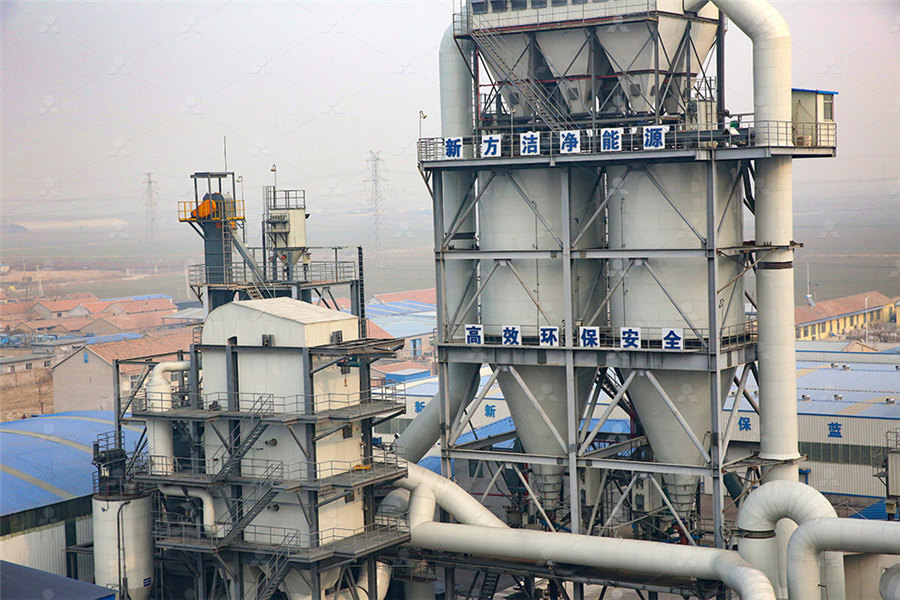
An investigation of performance characteristics
2020年8月12日 This study shows the performance of a currently running vertical roller coal mill (VRM) in an existing coalfired power plant In a power plant, the coal mill is the critical equipment, whose 2021年5月12日 Babcock is helping to keep South Africa’s power going, following the award of a mill maintenance contract at a major power station Babcock’s diverse scope of work for the fiveyear contract covers the daytoday upkeep of the milling plant as well as outage repairs, quality and inventory support, and onsite training and upskilling of the surrounding local communitiesMill maintenance contract at power station awarded Energize2021年6月10日 appropriate detection methods for coal mills Each generating unit at Merom has three Riley Power doubleended ball tube mills The mills can each provide 65 tph of pulverised coal to the boiler, a total of 195 tph per boiler NFPA Annex K5 Coal Firing General Considerations states: “It takes as little as 14 kg of pulverised coal in 283 m3 COAL MILL Land Instruments International2023年10月21日 By using the criticality and output measurement, paper devices a predictive maintenance policy for a coal pulverizing mill Keywords: Predictive maintenance, FMECA, Coal pulverizing mill, t Predictive Maintenance of Coal Pulverizing Mill Using
.jpg)
Mill Inerting and Pulverizer/Mill Explosion Mitigation
2018年6月7日 Coal Mills are the Heart of a Coal Fired Plant Maximum capacity, reliability and performance of your operation rely on the critical – Mechanical Blueprinting and optimization (maintenance practices) – Proper and optimum airflow management – Proper operation and plant staff awareness Ability to identify common causes2020年8月13日 Japan to manufacture supply stateoftheart UBE Vertical Roller Mills for grinding applications related to Raw material, Coal, Clinker and Slag Reliable Performance performs drying grinding classification and pneumatic transportation simultaneously The mill consists of the lower casing, upper casing, tableVERTICAL ROLLER MILLS AMCLSection of coal bowl mill Table 1 Guaranteed coal conditions for mill performance evaluation Coal Moisture % 20 Coal HGI 55 Mill Outlet Temperarure °C 80 Mill Air Flow T/hr 102 Coal Fineness (% passing trough 200 mesh) 70% passing through 200 mesh and 90% passing through 50 mesh Differental Pressure 300 mmwc Coal Output from Mill 609 t/hrA Study on 500 MW Coal Fired Boiler Unit’s Bowl Mill 2020年9月22日 The maintenance to keep these mills in shape is influenced significantly by the results of the fineness testing At a time when many plants are reducing their mill maintenance budget to control costs, one plant is increasing theirs to be able to burn harder to grind coals The fuel cost savings this mill capacity increase providedCoping with Coal Quality Impacts on Power Plant
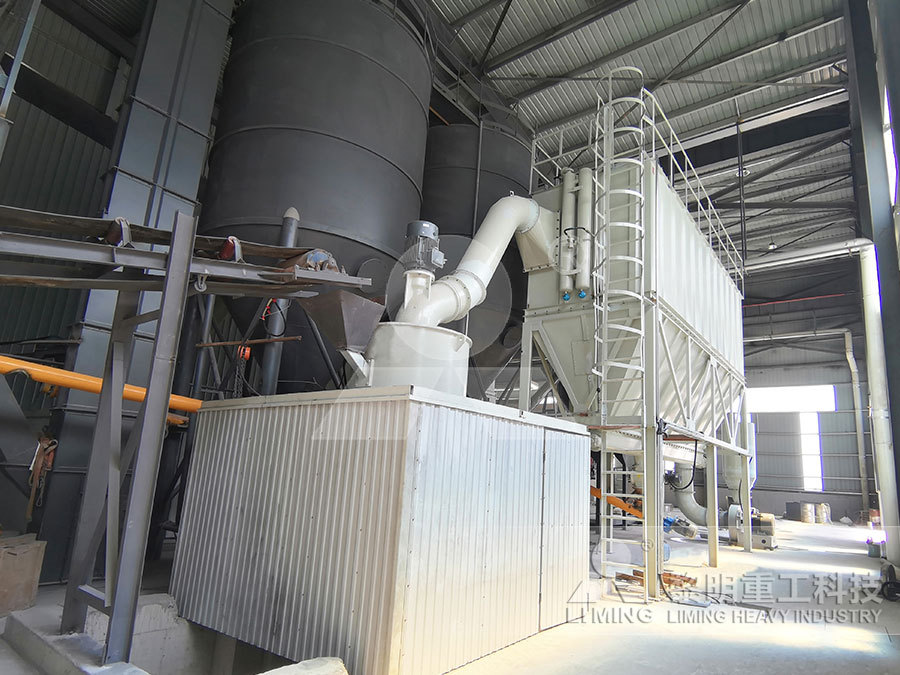
Reliable Coal Pulverizers and Mills » Babcock
Reliable coal pulverizer performance is essential for sustained fullload operation of today's power plants An effective pulverizer must be capable of handling a wide variety of coals and accommodating load swings in utility boilers as large 2023年8月28日 The design of its coal mills focuses on ease of maintenance, with features such as easy access to internal components and efficient cleaning mechanisms Quick and hasslefree maintenance procedures minimize downtime, allowing power plants to operate at maximum efficiency 5 Environmental Sustainability: Bellian Machinery is committed to Coal Mill in Thermal Power Plant: Enhancing Efficiency and The book step wise explains all these issues and their remedies with detailed pictures The book covers Bowl Mill Principle, Constructional Features Major Parts, Bowl Mill Clearances, End Plays Tolerances, Preventive Maintenance, Overhauling, Corrective Maintenance, Component Assembly, Design Requirement of Mills etc Coal Pipe chocking Mill Maintenance – Converting Challenges Into Opportunities2022年7月7日 Coal Mills are used to pulverize and dry to coal before it is blown into the power plant furnace Operation The coal is feed into the coal mill through a central inlet pipe where gravity is used to lead the coal to the bottom of the mill, where the grinding table and some heavy rollers pulverizes the coal to particlesCoal Mills SolidsWiki
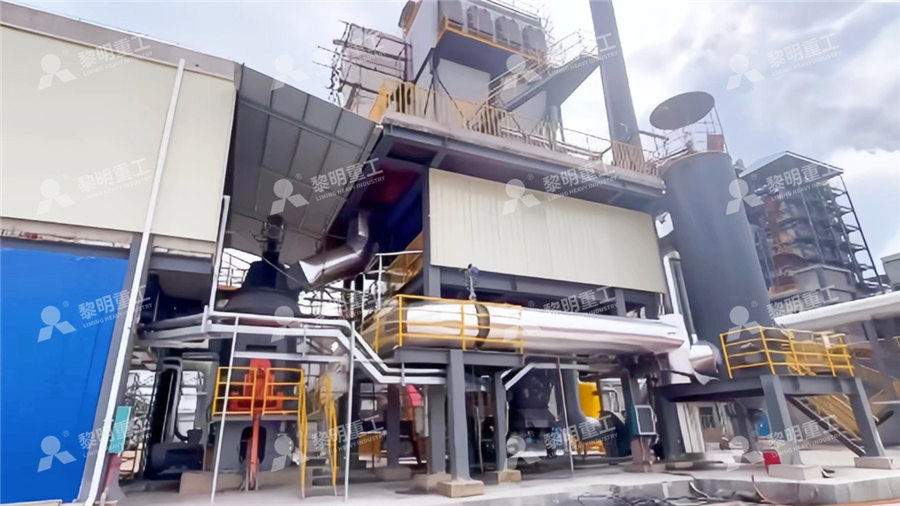
MPS mills for coal grinding AYS Engineering
2021年3月12日 During startup and maintenance the rollers can be lifted by tensioning cylinders Commissioning of many coal mills is currently in progress In the Ukraine an MPS 200 BK for coal grinding was commissioned in early 2013 All performance warranties were fulfilled The warranties were based on a Hardgrove index of 40, the performance tests 2022年1月2日 The document provides installation and operation instructions for the HRM1700M Vertical Roller Coal Mill It describes the mill's technical parameters, components, structure, working principles, and installation process Key aspects include grinding rollers that can be removed for maintenance, a hydraulic system that controls grinding pressure, and a separator Operation Manual: HRM1700M Vertical Roller Coal Mill2013年12月6日 NomenclatureBowl Mills 583 XRS / 803 XRP Bowl mills 58,80 stands for bowl diameter in inches If the number is even then its shallow bowl mill If the number is odd then its deep bowl mill 3 number of rollers three nos X frequency of power supply 50 cyclesIn USA ’x’ means 60 cycles R Raymond, name of the inventorPulverizer Plant OM Aspects eecpowerindia2024年10月31日 In discussion: Coal Mill Safety At best, coal mill safety is not well understood and, at worst, it is ignored When it comes to coal mill systems, most cement plant operators just presume that the supplier of the equipment knows all of the standards and rules and is 100% capable of making a system that conforms to these and is therefore safeIn discussion: Coal Mill Safety Coal Mill Safety, Explosion
.jpg)
Pulverizer Maintenance Guide, Volume 1 Raymond Bowl
The maintenance of the pulverizer mill affects the availability and reliability of the operating unit The efficiency of the mill in providing the desired coal and air mixture to the furnace has increased cost consequences with the addition of NOx controls The repairs and modifications to the mills ensure that the mills operate reliably Keywords2015年8月1日 Substantial savings, owing to reduced maintenance costs and production losses, can be achieved through fewer mill choking incidents, fewer mill runbacks, optimal mill operation, and rapid diagnoses of mill faults [5]Over the years, considerable research has been carried out for improving the operation of coal mills using better controls and diagnosing faults in mills at Review of control and fault diagnosis methods applied to coal mills2021年5月14日 The mill operates 24hours a day and is responsible for the grinding, drying, transporting and classification of the coal Babcock’s mill maintenance specialist says that the reliability of the mill is essential to ensure correct coal fineness, dryness and throughput, with the performance of the milling plant significantly impacting on plant Babcock wins coal milling maintenance contract crownco2017年5月3日 ASSEMBlIES USED IN COAl MIllS key words: preventive maintenance, coal mill, decisionrandom model Abstract: The paper presents a determination method of the most advantageous time of preventive maintenance for milling assemblies used in the energy industry In this particular case, we considered bowlmill pulveriser assemblies used in power DETERMINATION OF PREVENTIVE MAINTENANCE TIME
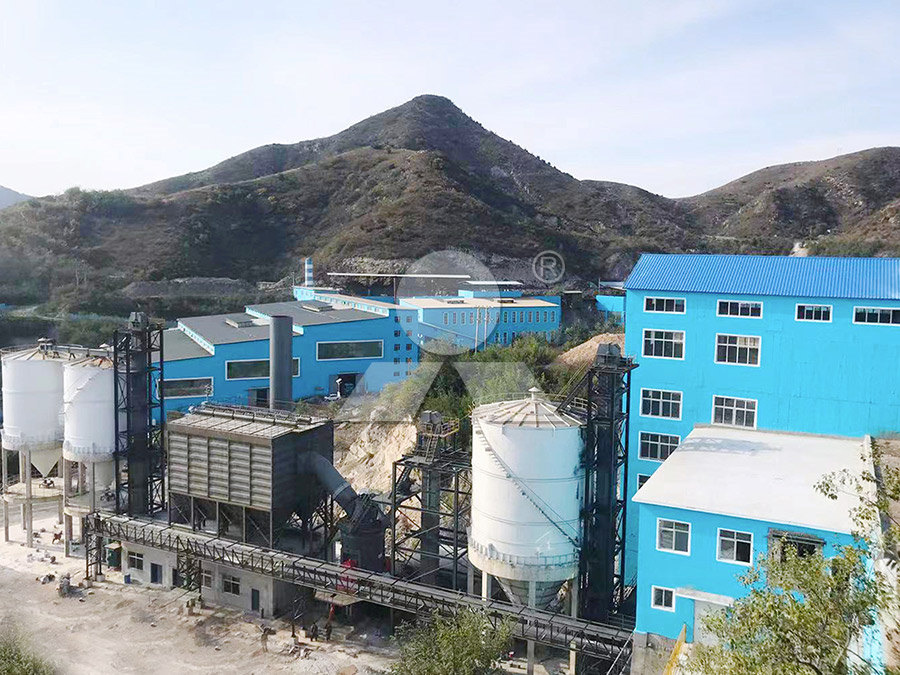
(PDF) MPS mills for coal grinding ResearchGate
2014年1月1日 During startup and maintenance the rollers can be lifted by tensioning cylinders The emission factors of kiln end, kiln head, coal mill, crushing and cement mill was 0156 clinker g/t, 3914 A simple energy balance model of the coal mill is derived in (Odgaard and Mataji 2006), this model is based on a more detailed model found in (Rees and Fan 2003)In this model the coal mill is seen as one body with the mass m mThe following variables are defined: T(t) is the temperature in the coal dust flow in the mill, ṁ PA (t) is the primary air mass flow, T PA (t) is Coal Mill an overview ScienceDirect Topics2016年12月19日 GPSE supplies standalone MPS coal grinding mills as well as complete coal grindingdrying systems Both mill and grinding system can be operated under pressure or suction as well as under air or inert gas atmosphere System configurations cover grinding plants with temporary storage of the pulverised coal in silos (cement works, blastfurnaces inCOAL GRINDING IMPS: more than meets the eye Gebr2024年7月25日 Coal grinding is a critical process in various industries, particularly in power generation and cement production However, the process involves significant safety risks due to the combustible nature of coal dust and the mechanical hazards posed by the operation of the mill Ensuring safety during coal grinding is essential to prevent accidents, exAspects of Coal Mill Safety Coal Mill Safety, Explosion and
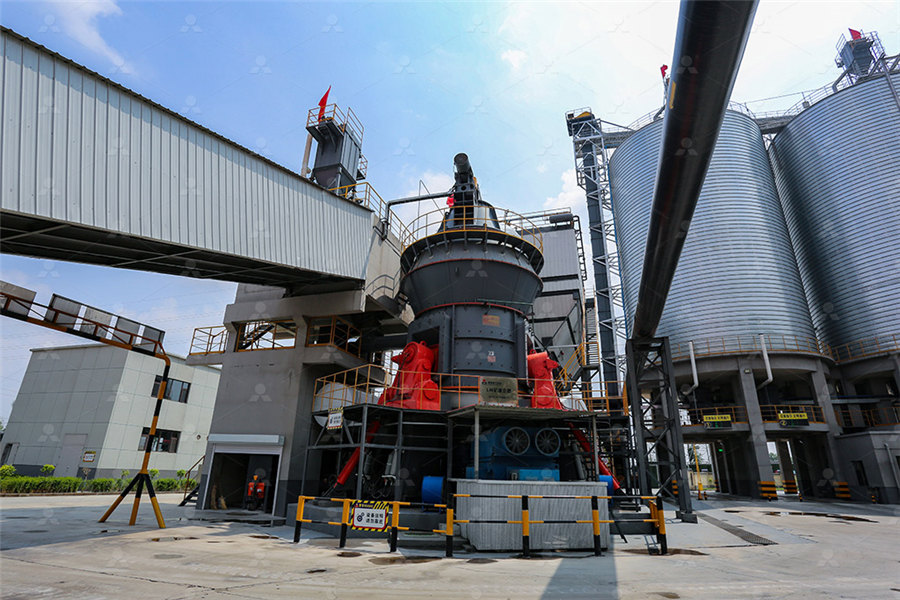
Coal Mills for Cement Plants Loesche
2024年11月26日 Coal grinding mills LOESCHE coal grinding mills are distinguished by characteristics that improve efficiency, safety and environmental protection, from the standard version to topoftherange installations Special versions are available with characteristics that meet special safety regulation or output control requirements2015年10月8日 Maintenance of coal handling plants (CHP) of thermal power stations has traditionally as the processes related to the performance of routine, unscheduled and emergency maintenance It doesn’t include operational factors such as scheduling, procedures, and work/systems control The failures of equipments have led to high maintenance andQuality Assured Maintenance Management For Coal 2017年2月7日 Bowl Mill has long been recognized as the most advantageous design of the coal pulverisers and include low initial cost, low maintenance cost, removal of tramp iron, low power consumption, easy maintenance, wide range output, quiet operation The basic features of Bowl Mill (Puveriser) supplied by BHEL are:BHARAT HEAVY ELECTRICALS LIMITED2024年8月22日 and low maintenance The mill heads are cast integral with trunnions which are supported in special heavy duty watercooled bearings Pressurized air seals between the rotating mill and inlet/outlet boxes prevent leakage of coal dust or air from the mill Each mill is completely enclosed in an insulated soundattenuating housingA Comparison of Three Types of Coal Pulverizers
.jpg)
Optimum Operation and Maintenance of EL Pulverizers
2018年6月3日 Optimum raw coal feed size for EL pulverizers is ¾” to 1” Raw coal feed should never exceed 1¼”, raw coal this size can plug throats and cause vibration Raw coal that is too fine can plug the pulverizer or delivery components upstream of the pulverizer Regular yard crusher inspection and maintenance is required to maintain optimum rawOur ATOX® Coal Mill is a compact vertical roller mill that can grind almost any type of raw coal The coal mill utilises compression and shear force generated between the large rollers and the rotating table to crush and grind raw coal, ATOX® Coal Mill FLSmidth Cement2020年8月12日 This study shows the performance of a currently running vertical roller coal mill (VRM) in an existing coalfired power plant In a power plant, the coal mill is the critical equipment, whose An investigation of performance characteristics 2021年5月12日 Babcock is helping to keep South Africa’s power going, following the award of a mill maintenance contract at a major power station Babcock’s diverse scope of work for the fiveyear contract covers the daytoday upkeep of the milling plant as well as outage repairs, quality and inventory support, and onsite training and upskilling of the surrounding local communitiesMill maintenance contract at power station awarded Energize
.jpg)
COAL MILL Land Instruments International
2021年6月10日 appropriate detection methods for coal mills Each generating unit at Merom has three Riley Power doubleended ball tube mills The mills can each provide 65 tph of pulverised coal to the boiler, a total of 195 tph per boiler NFPA Annex K5 Coal Firing General Considerations states: “It takes as little as 14 kg of pulverised coal in 283 m3 2023年10月21日 By using the criticality and output measurement, paper devices a predictive maintenance policy for a coal pulverizing mill Keywords: Predictive maintenance, FMECA, Coal pulverizing mill, t Predictive Maintenance of Coal Pulverizing Mill Using2018年6月7日 Coal Mills are the Heart of a Coal Fired Plant Maximum capacity, reliability and performance of your operation rely on the critical – Mechanical Blueprinting and optimization (maintenance practices) – Proper and optimum airflow management – Proper operation and plant staff awareness Ability to identify common causesMill Inerting and Pulverizer/Mill Explosion Mitigation2020年8月13日 Japan to manufacture supply stateoftheart UBE Vertical Roller Mills for grinding applications related to Raw material, Coal, Clinker and Slag Reliable Performance performs drying grinding classification and pneumatic transportation simultaneously The mill consists of the lower casing, upper casing, tableVERTICAL ROLLER MILLS AMCL
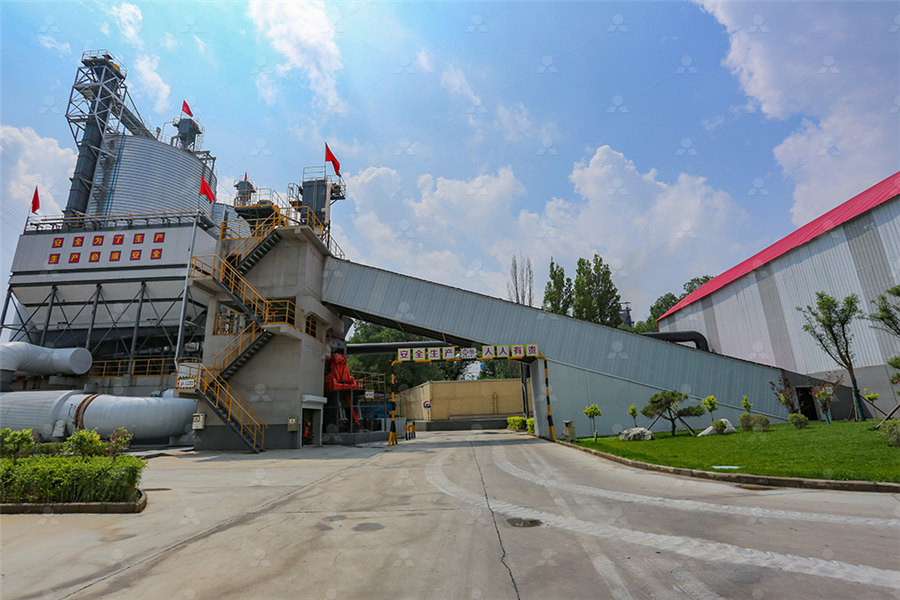
A Study on 500 MW Coal Fired Boiler Unit’s Bowl Mill
Section of coal bowl mill Table 1 Guaranteed coal conditions for mill performance evaluation Coal Moisture % 20 Coal HGI 55 Mill Outlet Temperarure °C 80 Mill Air Flow T/hr 102 Coal Fineness (% passing trough 200 mesh) 70% passing through 200 mesh and 90% passing through 50 mesh Differental Pressure 300 mmwc Coal Output from Mill 609 t/hr2020年9月22日 The maintenance to keep these mills in shape is influenced significantly by the results of the fineness testing At a time when many plants are reducing their mill maintenance budget to control costs, one plant is increasing theirs to be able to burn harder to grind coals The fuel cost savings this mill capacity increase providedCoping with Coal Quality Impacts on Power Plant