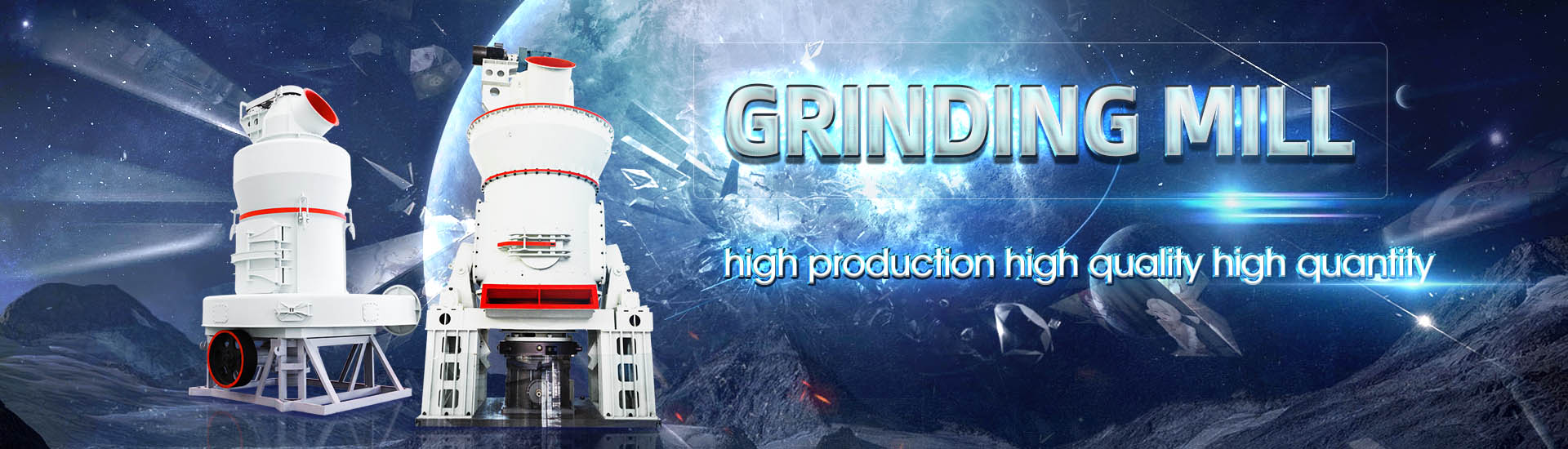
Contract agreement for powder making process of alkaline furnace lining material
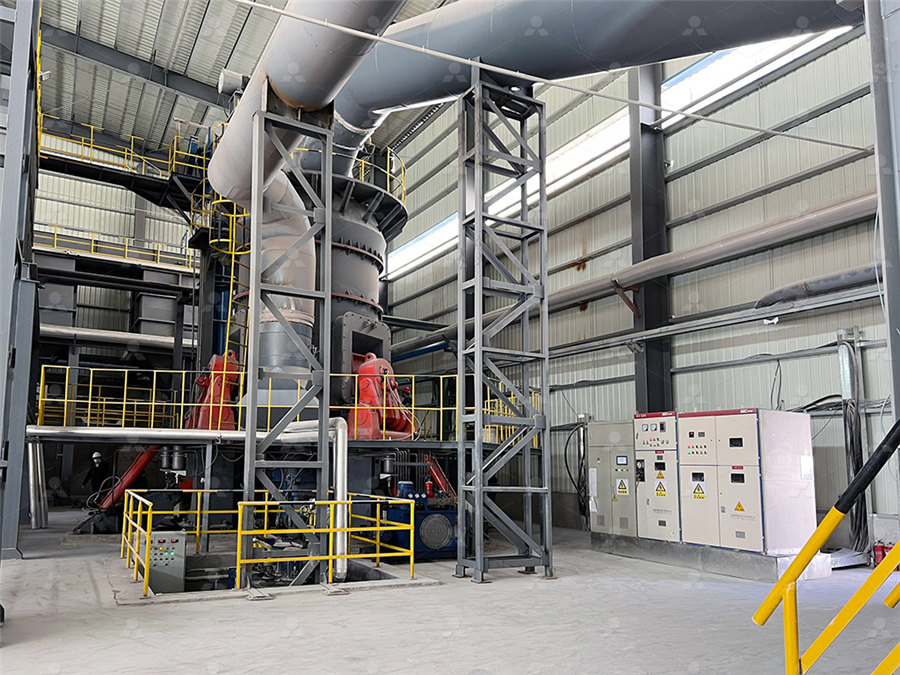
Design, fabrication and properties of lightweight wear lining
2022年3月1日 The design of lightweight wear linings is crucial in terms of the energy and resource efficiency of industrial furnaces and quality of final products This review aims to Capital Refractories offer a full range of coreless induction furnace linings, topping and patching products for a wide range of steels and high temperature alloys A range of chemically bonded high strength materials compatible with Capital’s Coreless Induction Furnace Linings Capital 2020年5月15日 This study aims to characterize alumina (Al2O3) based refractory materials applied on induction furnace lining based on its physical properties such as: the shape and PHYSICAL CHARACTERIZATION OF ALUMINA (Al2O3) 2023年6月1日 Materials for Melting Copper and its Alloys CRL65 Mullite forming material with excellent resistance to chemical, thermal and mechanical damage C65 RFL As CRL 65 but Refractories for Induction Furnaces
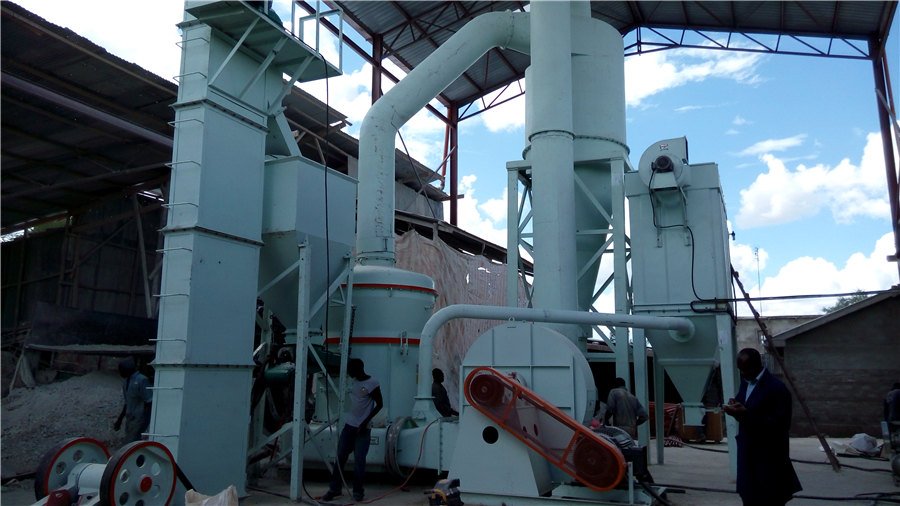
Effects of induction furnace conditions on lining refractory
2023年7月5日 Coreless induction furnace is one of the most widely used equipment in the steelmaking sector, while the lining refractory are the key factors in determining the lifetime of 2019年2月4日 REFRACTORY LINING FOR INDUCTION FURNACE The bottom structural part of Induction Furnace (Figure with details published in a separate article on Induction Furnace) REFRACTORY LINING FOR INDUCTION FURNACE IDC 2017年8月25日 This paper describes the development and behavior of once such newly developed material An Al producer will make the decision to take a furnace offline for repair IMPROVED MONOLITHIC MATERIALS FOR LINING 2019年2月4日 For the convenience of understanding, here we will discuss the types of refractory lining required in a blast furnace area wise as well as the trend in the refractory lining pattern BLAST FURNACE (BF) REFRACTORY LINING PATTERN
.jpg)
Induction Furnace Lining and Industrial Vibrator Design
2024年1月26日 Allied Mineral US has signed (manufacturing) supplier agreement with İDEAL Foundry Technologies for this production Next step of this project will be aimed on 2018年6月13日 require alkaline cleaners, we will concentrate on this group Alkaline cleaners are specifically formulated (proprietary) chemical blends which consist of alkaline salts, wetting agents, and sequestering (chelating) agents Wetting Agents soap and synthetic detergents allow oil to be removed byThe Basics of Alkaline InProcess Cleaning for Metal Lining materials for coretype induction furnace The cored or channel induction furnace lining should be made of refractory castables that are resistant to corrosion, and erosion resistance and have high chemical stability Usually, Induction Furnace Refractory AGRM Refractories2019年9月16日 Refractory lining material can be shaped or unshaped (monolithic material) Dry monolithic refractory material is normally used for the lining of induction furnace Life of refractory lining depends on dryness of Refractory Lining of Coreless Induction Furnace
.jpg)
Effects of induction furnace conditions on lining refractory
2023年7月5日 Coreless induction furnace is one of the most widely used equipment in the steelmaking sector, while the lining refractory are the key factors in determining the lifetime of the induction furnace The multiphysics field dominates the operating conditions of the lining refractory which can be wellstudied using numerical simulation techniques Based on the 2019年12月27日 chemical reactions with aluminium lining material, mechanical damage during cleaning oven to remove slag from the walls and hearth of the furnace and; thermal shock, that arise when loading charge The lining in the upper zone of the furnace is exposed elevated operating temperature; alkali metals; thermal shock by opening the windows bootAluminium melting furnace lining2023年11月28日 Tip 3 – Choose the right material for furnace rebuilds When IR scans indicate that the area of concern is too large for online repairs, the unit must be shut down for a furnace reline or process heater reline Material selection is key to a successful furnace rebuild that will improve efficiency and reliability and lower maintenance costsFive Tips for Achieving Furnace Lining Efficiency2021年6月21日 How do you make highquality washing powder? The best powder detergents are lightweight puffed powders with excellent freeflowing properties Their average bulk density ranges between 250500 g/l, comprising hollow particles with dimensions of 0225mmPowder Detergent: Ingredients Manufacturing Process Explained

How furnace is made making, history, used, components,
A furnace is a device that produces heat Not only are furnaces used in the home for warmth, they are used in industry for a variety of purposes such as making steel and heat treating of materials to change their molecular structure Process The primary heat exchanger is formed from two separate pieces of 409 stainless steel sheet Each 2023年12月4日 Tip 3 – Choose the right material for furnace rebuilds When IR scans indicate that the area of concern is too large for online repairs, the unit must be shut down for a furnace reline or process heater reline Material selection is key to a successful furnace rebuild that will improve efficiency and reliability and lower maintenance costsFive Tips for Achieving Furnace Lining Efficiency2014年10月1日 Alkalis (K and Na compounds, Kobayashi et al, 1979) enter in the blast furnace with the charge materials (should be limited to 2530 kg alkalis/ton pig iron, Kurunov et al, 2009 or 2585 kg (PDF) Alkaline carbonates in blast furnace process2018年12月31日 The Alkali metals enter the blast furnace through the raw materials The alkali in the blast furnace form carbonates, cyanides and silicates at different temperature and heights of the furnace(PDF) Effect of alkali on different iron making
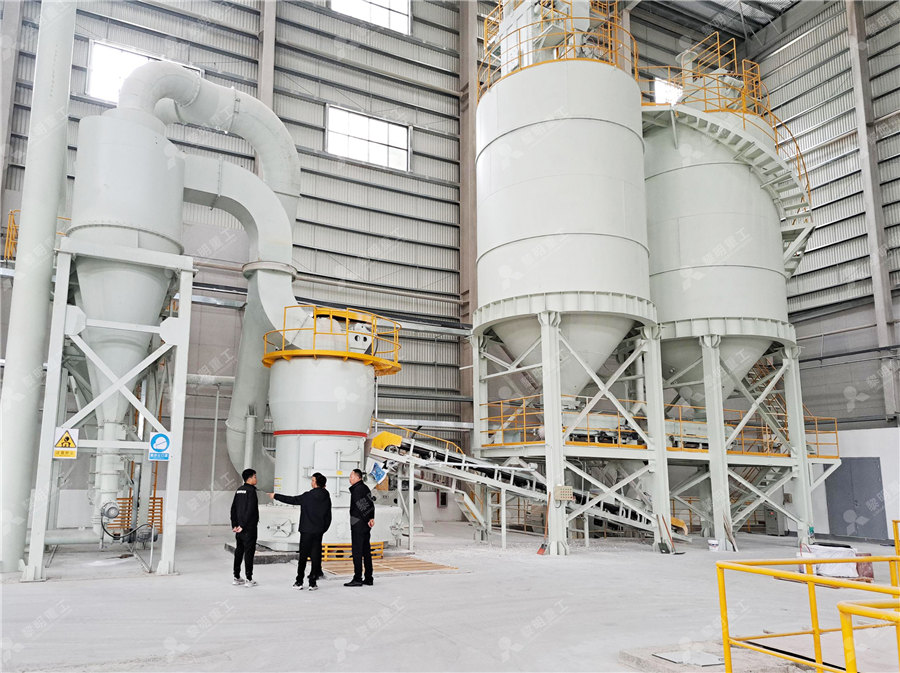
Refractory Lining of the Electric Arc Furnace –
2020年5月6日 Fig 1 Typical crosssection of the EAF showing different zones There are different design features of the EAF but they are mainly grouped into three areas namely (i) tapping design such as side tapping or bottom tapping, The performance of the blast furnace process is quite sensitive on the raw material properties The quality of the raw materials affects directly the productivity and efficiency of the processEFFECT OF ALKALINE ELEMENTS ON COKE STRUCTURE Lining material is an essential component for furnace lining Furnaces are used for various industrial processes such as metal smelting, glassmaking, and chemical reactions These processes require high temperatures, which can damage the furnace walls The lining material is used to protect the walls from the high temperatures and chemical reactionsLining Material: Essential for Furnace Lining2024年11月21日 There are numerous sample material agreements above for you to use as a guide Or we could learn how to make one or at least the contents of an mta agreement together One of the most popular types of material contracts is the material transfer agreement The methods below, however, are for a general material agreement 1 Identify the Materials34+ SAMPLE Material Agreement in PDF

Refractory lining of blast furnace IspatGuru
2014年8月15日 Different types of BF refractories Different types of refractories which are used in blast furnace lining are described below Baked carbon blocks – Micro porous carbon block, semi graphitic carbon block, and micro porous carbon silicon block are made with high temperature electrically calcined anthracite, synthetic graphite and silicon carbide as main raw materials2024年9月27日 The different XRD of nonalkali thermal activated powder (T0) and alkali thermal activated powders T200, T500 and T800 are shown in Fig 7 Muscovite is observed in T0 but reduces with increasing calcination temperature and ultimately disappears in T800 This shows that muscovite converts to reactive aluminosilicate at high temperaturesPreparation of geopolymers from alkaline thermally 2023年11月23日 The alkaliactivated curing of LF slag in the presence of metakaolin facilitates the curing at room temperature, making the process energyefficient 59 Lancennotti et al studied alkaliactivated LF slag using NaOH and SiO 2 /Na 2 O cured in moisture for their compressive strength performance 130 Their studies revealed that alkaliactivated Ladle Furnace Slag: Synthesis, Properties, and Applications2022年2月3日 Blast furnace slag (BFS) is a byproduct resulting from the fusion of iron ore into pig iron, in a process carried out in industrial units called blast furnaces, where the oxides contained in the iron minerals are reduced and the impurities that accompany them are separated []Slag is formed by the melting of impurities from iron ore after the addition of molten materials Characterization of Blast Furnace Slag for Preparing Activated Alkali
.jpg)
REFRACTORY LINING FOR INDUCTION FURNACE IDC
2019年2月4日 induction furnace crucible is made of the same refractory paste as used for constructing the crucible but with a greater addition of bonding materials water Then furnace heating schedule is to be followed carefully which will depend up thickness, nature of on the furnace lining ramming mass etc Selection of Refractories for Lining2017年5月30日 If you install a brick lining without adequate expansion joints, the brick can grow so large that it pushes up the entire lining off the furnace wall This will lead to further inefficiency, requiring the entire process to be repeated 4 Ensuring Effective Furnace Lining Efficiency2024年8月7日 The article describes modern methods for controlling and optimizing the energy mode of melting in electric arc furnaces and units for outoffurnace steel processing using optical emission spectroscopy systems These systems enable the determination of melt and slag temperatures, plasma temperatures in the arc combustion area, and slag composition, as well Potential of controlling the steelmaking process in electric 2023年1月6日 There are several known causes for metal runouts from furnaces and process vessels: 1 Binding and Refractory The most common cause of runouts is the movement/interaction within the structure (whether that be a fixed frame, shell, or adjustable bindings) and the refractory system where metal leaks between refractory bricks or between Predictive Furnace Refractory Maintenance Procedures to
.jpg)
BLAST FURNACE (BF) REFRACTORY LINING PATTERN
2019年2月4日 Blast Furnace is the focus of any integrated steel plant Blast furnace is used to reduce the iron ore to iron The charge, which consists of iron ore, coke and limestone etc in the form of lumps and different ratios, is fed from the top Air heated in the blast furnace stoves, is applied from the bottom of the furnace The2023年8月31日 boundary conditions are shown in Table 1 The furnace lining material in the model is based on quartz ramming material and the furnace material is based on steel Specic parameters are shown in Table 2 Some of the parameters in Table 2 are taken from other works [7 , 19–21] The global setup of mesh for the solution domain is freeEffects of induction furnace conditions on lining 2021年5月15日 Basic oxygen furnace slag (BOFS) is a waste material generated during the steelmaking process and has the potential to harm both the environment and living organisms when disposed of in a landfillAlkaline Activation of Basic Oxygen Furnace Slag Modified 2020年6月10日 Increase in furnace size and productivity has led to an increase in stresses exerted on the refractory lining The Fig 31 summarizes the essential demands made on the quality of refractories based on the stresses and wear processes indicated in the different zones of the furnaces, where different influences prevailing the different regions of blast furnace []Blast Furnace Refractory SpringerLink
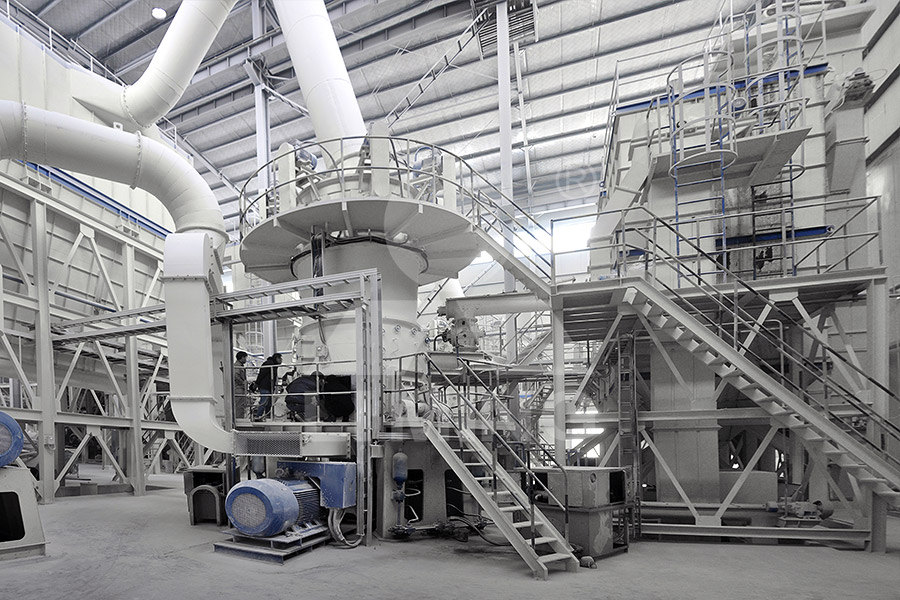
Preparation of geopolymers from alkaline thermally
2024年9月27日 In this study, activated powder was prepared using granite waste powder and burnt coal cinder through alkali thermal activation and subsequently blended with blast furnace slag The prepared geopolymer was characterized and compared in terms of mechanical performance to onepart geopolymer prepared using non activated raw materials2024年7月22日 At present, most electric furnaces use alkaline linings, and acidic lining electric furnaces are only used to produce steel castings or gray cast iron There are several aspects to the performance requirements of electric furnace lining refractory materials There should be sufficient fire resistance and load softening pointElectric Furnace Refractory Lining Material RS Refractories 2022年6月28日 The neutral furnace lining material is a dry kneaded material mixed with corundum sand, powder, aluminummagnesium spinel powder, and sintering agent This kind of ramming material has strong compactness, good thermal What Kind of Ramming Material is Used for the Lining of the 2018年6月13日 require alkaline cleaners, we will concentrate on this group Alkaline cleaners are specifically formulated (proprietary) chemical blends which consist of alkaline salts, wetting agents, and sequestering (chelating) agents Wetting Agents soap and synthetic detergents allow oil to be removed byThe Basics of Alkaline InProcess Cleaning for Metal
.jpg)
Induction Furnace Refractory AGRM Refractories
Lining materials for coretype induction furnace The cored or channel induction furnace lining should be made of refractory castables that are resistant to corrosion, and erosion resistance and have high chemical stability Usually, 2019年9月16日 Refractory lining material can be shaped or unshaped (monolithic material) Dry monolithic refractory material is normally used for the lining of induction furnace Life of refractory lining depends on dryness of Refractory Lining of Coreless Induction Furnace2023年7月5日 Coreless induction furnace is one of the most widely used equipment in the steelmaking sector, while the lining refractory are the key factors in determining the lifetime of the induction furnace The multiphysics field dominates the operating conditions of the lining refractory which can be wellstudied using numerical simulation techniques Based on the Effects of induction furnace conditions on lining refractory 2019年12月27日 chemical reactions with aluminium lining material, mechanical damage during cleaning oven to remove slag from the walls and hearth of the furnace and; thermal shock, that arise when loading charge The lining in the upper zone of the furnace is exposed elevated operating temperature; alkali metals; thermal shock by opening the windows bootAluminium melting furnace lining
.jpg)
Five Tips for Achieving Furnace Lining Efficiency
2023年11月28日 Tip 3 – Choose the right material for furnace rebuilds When IR scans indicate that the area of concern is too large for online repairs, the unit must be shut down for a furnace reline or process heater reline Material selection is key to a successful furnace rebuild that will improve efficiency and reliability and lower maintenance costs2021年6月21日 How do you make highquality washing powder? The best powder detergents are lightweight puffed powders with excellent freeflowing properties Their average bulk density ranges between 250500 g/l, comprising hollow particles with dimensions of 0225mmPowder Detergent: Ingredients Manufacturing Process ExplainedA furnace is a device that produces heat Not only are furnaces used in the home for warmth, they are used in industry for a variety of purposes such as making steel and heat treating of materials to change their molecular structure Process The primary heat exchanger is formed from two separate pieces of 409 stainless steel sheet Each How furnace is made making, history, used, components, 2023年12月4日 Tip 3 – Choose the right material for furnace rebuilds When IR scans indicate that the area of concern is too large for online repairs, the unit must be shut down for a furnace reline or process heater reline Material selection is key to a successful furnace rebuild that will improve efficiency and reliability and lower maintenance costsFive Tips for Achieving Furnace Lining Efficiency
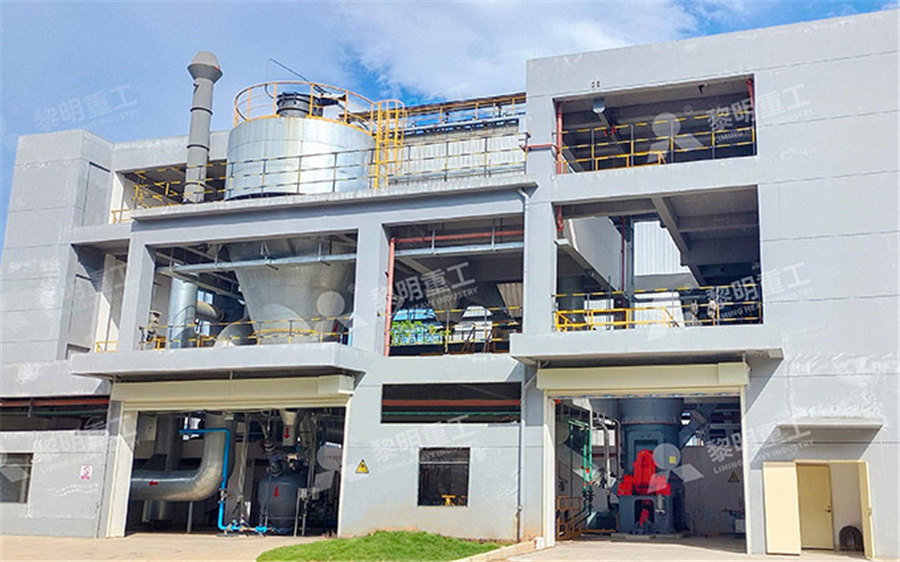
(PDF) Alkaline carbonates in blast furnace process
2014年10月1日 Alkalis (K and Na compounds, Kobayashi et al, 1979) enter in the blast furnace with the charge materials (should be limited to 2530 kg alkalis/ton pig iron, Kurunov et al, 2009 or 2585 kg