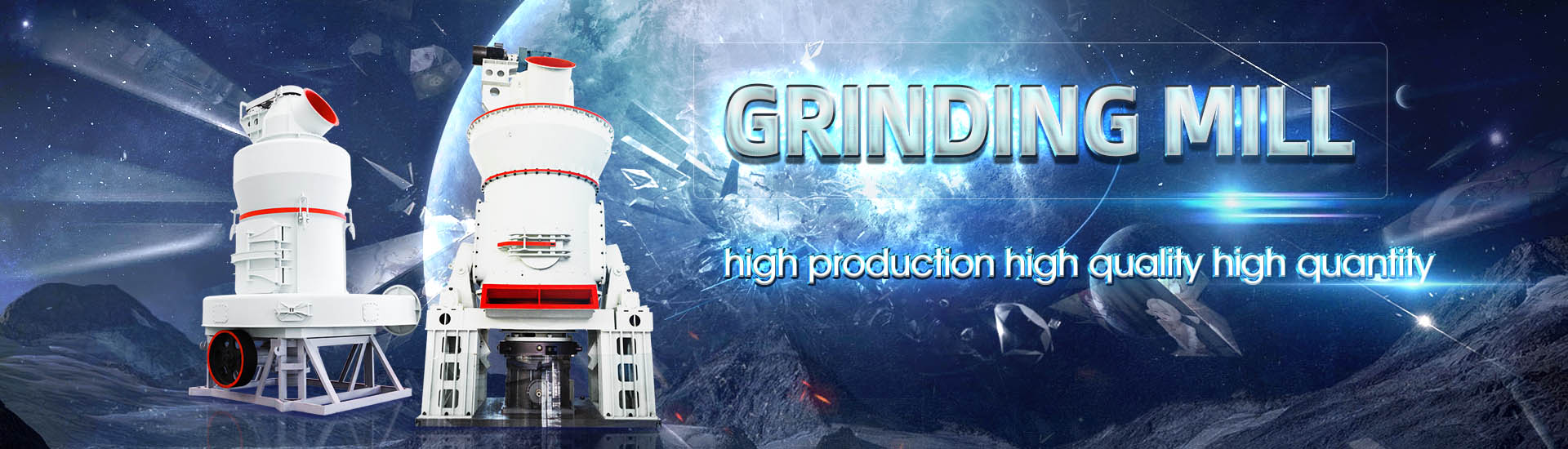
Current limestone production process
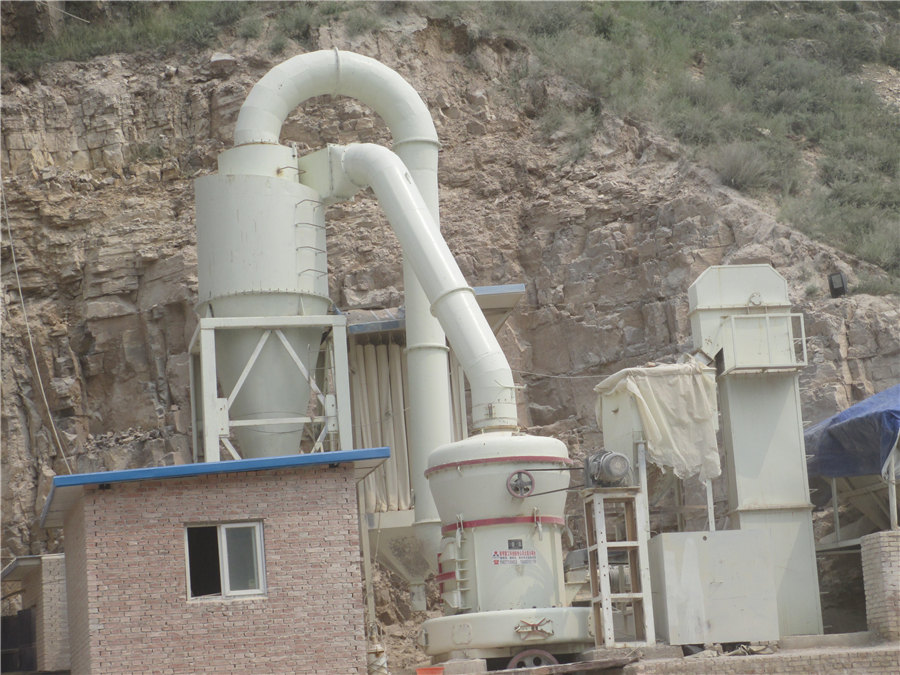
Limestone Quarrying and Processing: A LifeCycle Inventory
Process flow diagram for limestone processing operations Processing commences with transportation of the (raw) stone from the quarry to the processing facility, as depicted by Figure 22022年10月1日 Nowadays the term “lime” (Calcium Oxide, CaO) is assigned to a product derived from limestone in an industrial process known as calcination (Despotou et al, 2016) Hydrated lime lifecycle assessment: Current and future scenarios 2022年10月1日 Supplementary raw materials in limebased binder production have limited effects on CO 2 emissions due to unavoidable emissions from calcite decomposition The Hydrated lime lifecycle assessment: Current and future scenarios 2022年7月1日 The environmental load associated to Hydrated Lime (HL) products is attributed to the limestone decomposition and the industrial production (combustion in the kiln, the electricity, theHydrated lime lifecycle assessment: Current and future
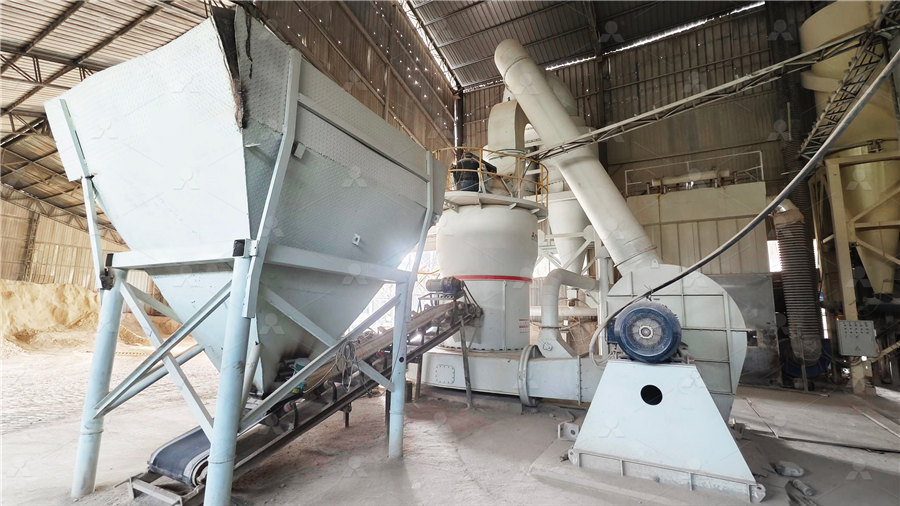
Lime Production an overview ScienceDirect Topics
42 Energy use and emissions The lime production process is energy intensive and results in CO 2 emissions from both mineralogical transformation process and energy used The production of one tonne of lime entails the emission of around 12 tonne of CO 2 (Ochoa George et al, 2010; Sagastume Gutiérrez et al, 2012)This makes lime one of the products with the highest 2022年4月12日 Carbon dioxide (CO2) emissions from China’s cement production process have increased rapidly in recent decades, comprising the secondlargest source of CO2 emissions in the country, next only to China’s provincial process CO2 emissions from cement production 1 Introduction As shown in Figure 1, the overall lime production process basically consists of two lines, the first of which, the production line, essentially comprises the following operations: quarrying, the actual industrial process (incl the Comprehending the lime production processexist Commercially, the term limestone includes dolomite, dolomitic limestone, oolitic limestone, and travertine (Dolley 2007), a porous calcitic rock that is commonly formed near hot springs The production of commercial limestone typically exceeds production of all other stone types,A LifeCycle Inventory of Limestone Dimension Stone Quarrying
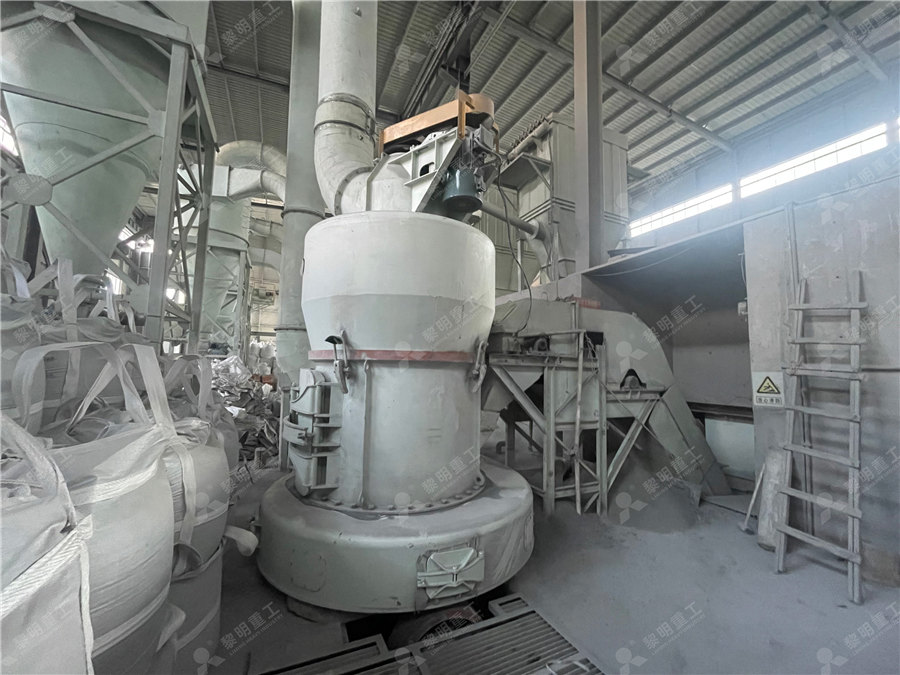
Lime Production From Limestone Current Technology Scribd
Lime Production From Limestone Current Technology Free download as PDF File (pdf), Text File (txt) or read online for free Limestone is naturally occurring and contains calcium, magnesium and carbonate It is used in many industries to neutralize acid and for chemical processes Lime is produced from limestone in a 4 step process: 1) mining limestone, 2) Limestone products are commonly used in industrial processes and are naturally occurring consisting of high levels of calcium, magnesium carbonate and minerals Lime is used in many industries to neutralize acid waste and as an alkali for chemical processes, in agriculture, soil stabilization, building, and industrial purposes such as cement and steel productionLime Production from Limestone Current Technology2023年12月11日 Global cement emission patterns Global emissions from cement production reached 2059 Mt CO 2 in 2018, where energy and processrelated emissions account for 34% and 66% respectively Developed Projecting future carbon emissions from cement production in 2024年3月20日 The article provides an overview of the steel making process, detailing how raw materials like iron ore, coke, and limestone are transformed into versatile and durable steel through a complex series of steps depicted in a flow diagram It discusses the key ingredients involved in steel production, their roles, advantages and disadvantages of the workflow Understanding the Steel Making Process: A Flow Diagram
.jpg)
Blast Furnace Process an overview ScienceDirect Topics
These companies feel uneasy about their dependency and have been trying over the years to find an alternative iron production process to replace the blast furnace process There are, however, alternative ways to produce iron, such as direct reduction processes, as well as smelting processes such as COREX, AISI/DOE Direct Steelmaking process, DIOS, and HIsmeltSpecifically clinker production generates 5052 kg CO 2 / t cl from the limestone decomposition process (CaCO 3 forming CaO and CO 2) during calcination [56] This is true for several technologies modeled: dry process (with or without CCS), wet process and belite cementClinker Production an overview ScienceDirect TopicsEven though equipment is improved and higher production rates can be achieved, the processes inside the blast furnace remain the same The blast furnace uses coke, iron ore and limestone to produce pig iron Coal traditionally has been a Steel Production American Iron and Steel Institute2022年10月1日 The thermal treatment of limestone (mainly CaCO 3) to produce lime (CaO) is a major contributor to CO 2 emissions and the literature on decarbonising the lime industry is scarce Subsequent hydration of lime would lead to the synthesis of slaked/hydrated lime Ca(OH) 2; the production of a tonne of Ca(OH) 2 emits ∼12 tonnes of CO 2 arising mainly from the Decarbonising the lime industry: Stateoftheart ScienceDirect
.jpg)
A practical guide to improving cement manufacturing processes
The cement production process 1 The Quarry: The cement production process begins with the extraction of limestone and clay from the quarry 2 Crusher and PreBlending: The material is then crushed to reduce particle sizes and blended to reduce variability in composition 3 Raw Mill and Kiln: Raw materials and additives areGlobal cement production has reached 39 billion tons However, the clinkerization process, which is the basis of cement production, is responsible for an approximate annual global CO2 emission of 2 billion tons As part of CEMBUREAU’s 5C strategy, the European cement industry aims to achieve carbon neutrality throughout the cementconcrete value chain by 2050 This article is Cement and Clinker Production by Indirect Mechanosynthesis Process The Bessemer Process for Steel production and; The Open Hearth Process of Steelmaking; Steel manufacturing Principle of the Bessemer Process The main raw materials for Steel production in a blast furnace are Iron ore, limestone, coke, and some scrap steel These materials are charged into the blast furnace from the top and converted into How is Steel Made? Steel Production Process – What Is PipingThe whole process of making any type of lime all begins at the limestone quarry after careful surveys Most limestone is extracted through blasting Behind the rock face, holes are drilled to place the explosives When detonated, the explosion dislodges each time up Production European Lime Association
.jpg)
Impact of Limestone Surface Impurities on Quicklime Product
2024年2月27日 The limestone production process comprises operations such as blasting, hauling, crushing, sieving, washing, and sampling, generating small particulate matter, ie, CaO (s), limestone should be processed below a maximum temperature of 1300 °C, which likely corresponds well to many current lime kiln design parameters2020年6月1日 The production of cement primarily depends upon the availability of limestone as cement grade limestone is the primary raw materials in its production The total cement grade limestone reserve available in India is around 14175 billion tonnes as per NMI (National Mineral Inventory) data based on UNFC (United Nations Framework classification) system as on year A review on development of Portland limestone cement: A step this section explains costs of production and economies of scale 21 PRODUCTION PROCESS, INPUTS, AND OUTPUTS The production of lime begins with the quarrying and crushing of limestone Limestone is a general term that covers numerous varieties of sedimentary rock Limestone can be composed of the following four minerals, plus impurities Lime Production: Industry ProfileCurrent State of Limestone Industry KIGAM, 2013, Supporting the Limestone Industries by Developing the Beneficiation Process for Low Grade Limestone (Final Report) KIGAM, 2014, Korea Title Development of Conceptual Cost Estimation Model for an Economic Analysis of Steam Methane Reforming based Hydrogen Production Authors Yeonho Lee Current State of Limestone Industry in Korea
.jpg)
Deep decarbonisation of industry: The cement sector Europa
clinkermaking process (2) Older, less efficient wet kilns have almost been phased out In the more advanced dry process, raw ingredients are calcinated at around 9001250oC in a precalciner to transform limestone into lime, which releases CO 2 as a side product The materials are then fed into a rotary kiln,2021年10月4日 1 Introduction The process emissions of lime production, ie the CO 2 released during limestone calcination excluding that released from the combustion of fossil fuels, are estimated to account for about 1% of the global Natural and enhanced carbonation of lime in its 2019年9月3日 Limestone was used as a flux, its inclusion in the current paper is thought to be beneficial, The lowgrade ferronickel production process can be regar ded as the second most important(PDF) Nickel Laterite Smelting Processes and Some ResearchGate2023年10月21日 Limestone is a sedimentary rock primarily composed of calcium carbonate (CaCO3) in the form of mineral calcite or aragoniteIt is one of the most common and widely distributed rocks on Earth, with a wide range of uses in various industries and natural settings Limestone forms through the accumulation and compaction of marine organisms, primarily the Limestone Types, Properties, Composition, Formation, Uses
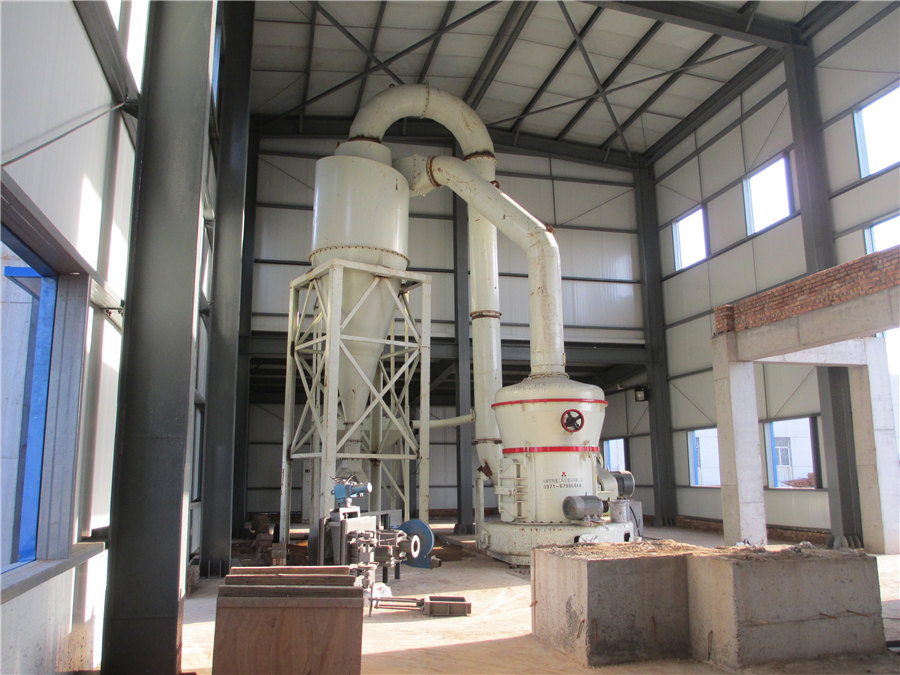
Efficient CO2 capture from lime production by an indirectly
2021年12月1日 Lime (CaO) is an important product used in different sectors of the industry as well as in agriculture The production of lime is achieved through the calcination of limestone (mainly CaCO 3) at temperatures between 900 and 1200 °CThis process is highly endothermic and requires the combustion of fuels such as gas oil, coal, coke, or some types of secondary Kilkenny Limestone’s production process uses diamondwire saws and diamondtipped chainsaws to carve through the massive beds of rock Cooling water, recycled through settlement ponds on the quarry floors, prevents overheating of the saws Kilkenny Limestone® production process BrachotAn English bricklayer made the first portland cement early in the 19th century by burning powdered limestone and clay on his kitchen stove Each step of the cement production process is carefully monitored to ensure efficiency and quality Grinding, Mixing, and BlendingHow Cement is Made Portland Cement AssociationTable 91 Limestone and Other Crushed Rock Production and Energy Consumed by Type a Units 1987 1992 1997 Limestone and Rock Production b Billion tons 12 12 Energy Consumption Coal Thousand tons Withheld 785 430 Fuel oil c Million bbl 36 34 40 Gas Billion Cubic Feet 17 32 54 Gasoline Million Gallons 142 155 147 ElectricityLimestone and Crushed Rock Department of Energy
.jpg)
Simulation and Optimization of an Integrated Process Flow Sheet
2021年3月9日 In this study the process flow diagram for the cement production was simulated using Aspen HYSYS 88 software to achieve high energy optimization and optimum cement flow rate by varying the flow rate of calcium oxide and silica in the clinker feed Central composite Design (CCD) of Response Surface Methodology was used to design the ten experiments for 2024年3月28日 Current environmental impacts Lifecycle climate impacts from today’s clinker production in Europe vary by country, primarily because of variability in technology, shares of alternative fuels Paving the way for sustainable decarbonization of the European 2022年11月6日 The limestone production scheduling for an open pit mine can be described as determining the order in which ‘blocks’ should be extracted to achieve a specific goal, while taking into account a range of physical and An Optimized Open Pit Mine Application for 2021年6月16日 Figure 1 A shows the current process for production of cement, which includes three main stages: raw material extraction and preparation, clinker production, and cement grinding Limestone (CaCO 3) is the main feed constituent Our baseline is a modern cement plant, fired exclusively with fossil fuelsDecarbonizing cement production ScienceDirect
.jpg)
(PDF) CEMENT PRODUCTION PROCESS REPORT A
PDF On Apr 7, 2022, Alick Sinoya published CEMENT PRODUCTION PROCESS REPORT A SINOYA 1 Find, read and cite all the research you need on ResearchGate2022年10月1日 The second factor is the industrial production of quicklime itself, including the combustion of fuels in the kiln, the electricity needed to operate the plant, the transport of different materials, etc Fig 1 shows the flow diagram of a plant that can produce four types of lime products: PL, ML, MoL and HL The process starts from the extraction of limestone from a Hydrated lime lifecycle assessment: Current and future scenarios 2023年2月15日 1 In the process of calcination, the granularity of the raw limestone affects the whole process a lot Since the separation of CO2 proceeds slowly from the surface of the limestone to the inside, the calcination of large particle size is more difficult than that of small ones, and it takes a longer timeLime Production Process and Required Equipment2020年4月14日 Limestone calcined clay cement (LC 3) is being developed as a lowcarbon alternative to conventional cementsThe cement has the potential to reduce CO 2 emissions by up to 30%, at the same time, demonstrating a higher performance in many types of exposure conditions Being a conservative industry, the introduction of a new cement is a challenging Limestone Calcined Clay Cement: Opportunities and Challenges
.jpg)
Implementing Sustainable Cement Production Methods: Two Key
2022年7月8日 The cement factory in Indonesia has been in full operation since August 2015 The factory, with a capacity of 18 million tons of limestone per year, relies heavily on surface miners for their limestone production, which operates during daylight to further help minimize the impact on the local community Maximize Efficiencies While Reducing CostsLimestone (calcite, CaCO3) is an abundant and costeffective source of calcium oxide (CaO) for cement and lime production However, the thermochemical decomposition of limestone (∼800 °C, 1 bar) to produce lime (CaO) results in substantial carbon dioxide (CO2(g)) emissions and energy use, ie, ∼1 tonne [t] of CO2 and ∼14 MWh per t of CaO produced Here, we describe a new ZeroCAL: Eliminating Carbon Dioxide Emissions from Limestone’s 2023年2月17日 Recently, Fennell et al discussed the potential to decarbonize cement production by improving energy efficiency, developing alternative materials, and adjusting the production process 5 Chiang et al demonstrated the electrochemical synthesis of cement by transforming CaCO 3 and water into Ca(OH) 2 via Pt electrodes (), which could be driven by Electrochemical transformation of limestone into calcium Uses of alternative fuels and raw materials in the cement industry as sustainable waste management options Alfonso Aranda UsónAna M LópezSabirónGermán FerreiraEva Llera Sastresa, in Renewable and Sustainable Energy Reviews, 2013 21 Worldwide production One of the wellknown characteristics of cement production is that cement plants are not uniformly Cement Production an overview ScienceDirect Topics