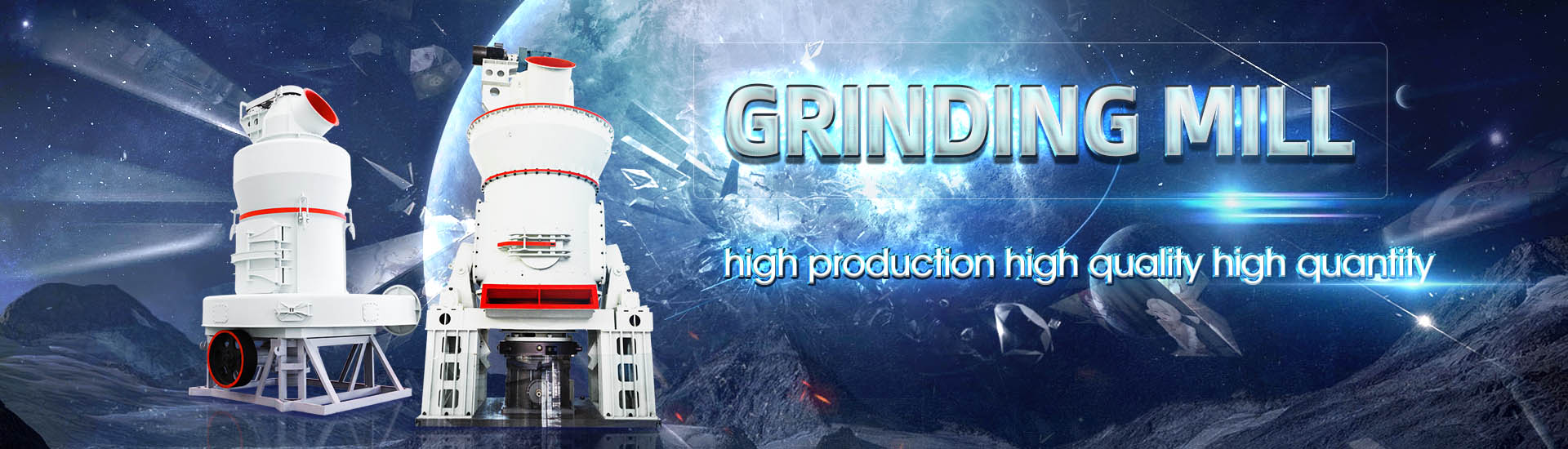
UM464 raw material mill installed power
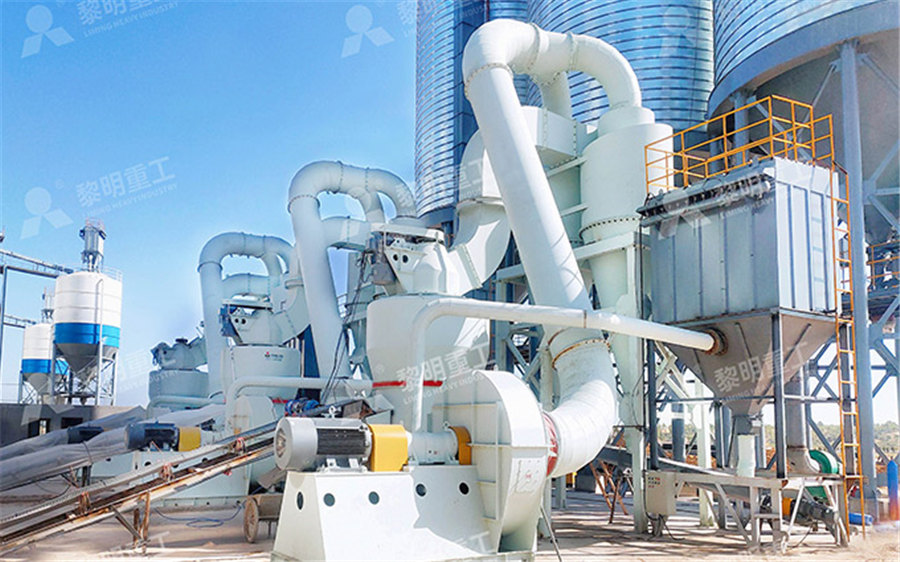
An innovative approach for determining the grinding media
2021年1月22日 According to the energy consumption method, the mathematical function models of installed power and mill productivity vs spacefilling factors were established to calculate 2014年4月1日 The newly developed modular roller mill for grinding cement raw material, cement clinker, and additives with an installed power of up to 12,000 kW was specifically designed to (PDF) The latest innovative technology for vertical roller mills 2021年3月12日 type of installation: ball mills, combined in circuit with an air classification system of varying generations and sophistications Depending on the local market situation and BALL MILLS Ball mill optimisation Holzinger Consulting2023年12月6日 raw material grinding, a modular vertical roller mill with 5 m table diameter and 4 rollers was added The existing kiln systems were partly modernized, one kiln system was Grinding Process Optimization Featuring Case Studies
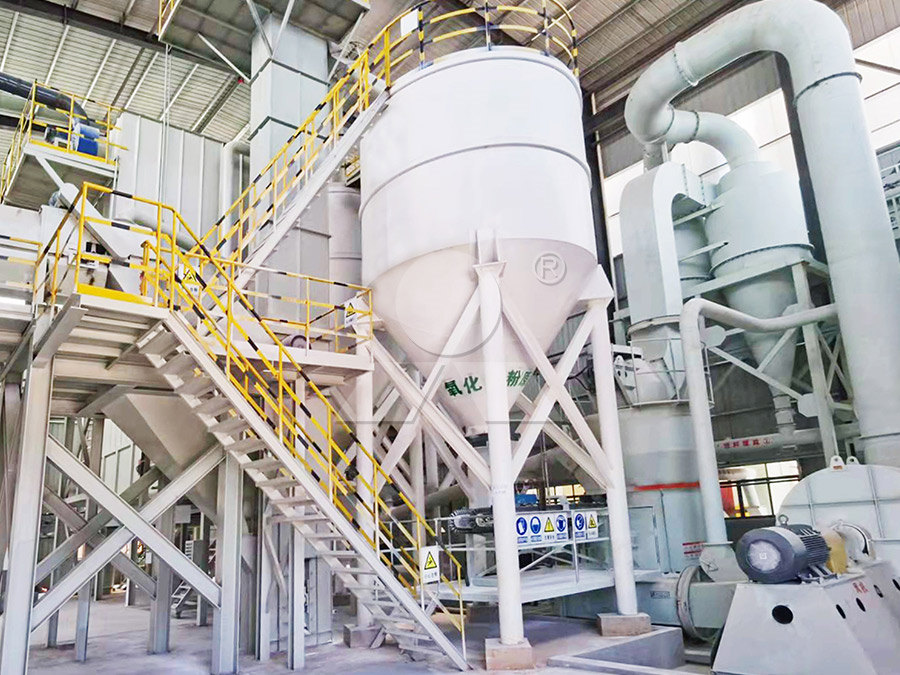
A case study on energy and exergy analyses for an industrial
2021年2月1日 VRM unit consumes around 975 kWh/t more energy to grind raw material than the IBAT unit In this study, the analyses of energy and exergy were implemented for an 2021年1月22日 Based on the statistics of the electricity consumption of the raw material mill system of 1005 production lines in China between 2014 and 2019, it is found that the average A Survey and Analysis on Electricity Consumption of Raw Material Mill 2016年1月4日 Vertical roller mills are adopted in 20 cement plants (44 mills) in Japan In the vertical roller mill which is widely used in the raw material grinding process, raw materials input Vertical roller mill for raw Application p rocess materials2021年1月22日 Based on the statistics of the electricity consumption of the raw material mill system of 1005 production lines in China between 2014 and 2019, it is found that the average A Survey and Analysis on Electricity Consumption of Raw Material Mill
.jpg)
Overhaul of raw material mill gearbox saves more than
2022年9月12日 For the planned overhaul of the 82ton raw material mill gearbox, the company was looking for a cost and timeefficient solution for mounting and dismounting The cement 2014年4月1日 The newly developed modular roller mill for grinding cement raw material, cement clinker, and additives with an installed power of up to 12,000 kW was specifically designed to meet those needs (PDF) The latest innovative technology for vertical roller mills 2017年1月1日 7 CEM 6000 kW drive for a raw material mill FLSmidth Maag Gear 8 MultiDrive with four drive units GPSE mill with an installed power of 12 000 kW and fea(PDF) Drives for large vertical roller millsThe Horomill used as a raw mill is claimed to combine the effectiveness of the vertical roller mill and the roller press with a very low pressure drop in the circuit It is also expected to offer some advantage in handling raw materials Everything you need to know about cement
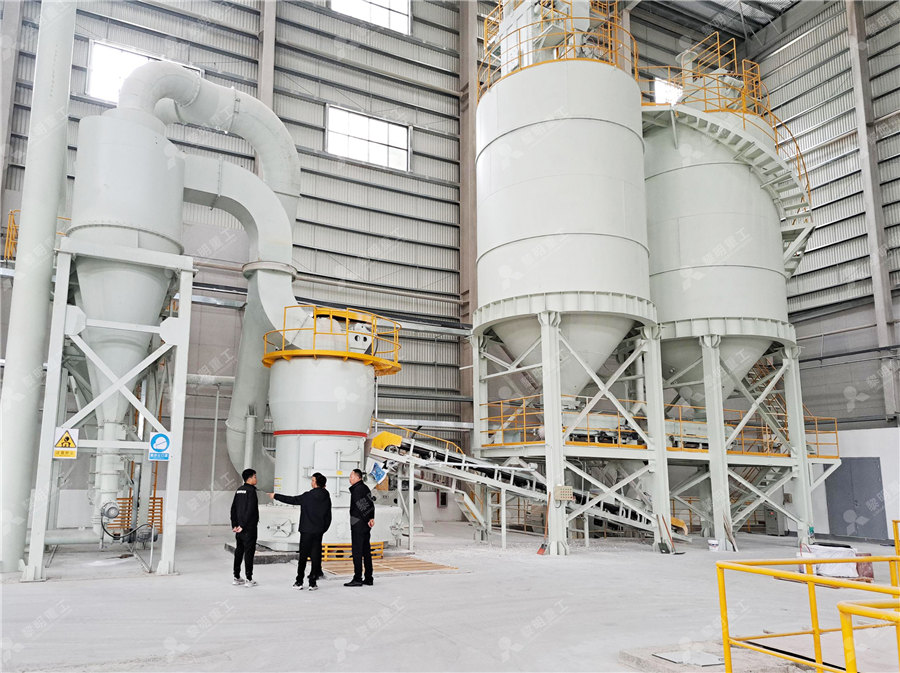
Machining Power Calculator and Formulas
Assuming the efficiency is 100%, the power required to remove the material is the same as the power used by the machine’s motor Each machine has a maximum power limit that it can handle Therefore, it is helpful to calculate the power required to perform a machining operation such as milling or turning and compare it to our machine’s abilityUnderstanding the different types of raw materials used in paper production is crucial for producing highquality paper that meets various industrial and consumer demands In this guide, we will explore the different types of raw materials used in paper production, including woodbased raw materials, recycled paper, and nonwood fiber materialsRaw Materials Used in Paper Production CNBMVertical raw mill is one kind of raw mill, generally used to grind bulk, granular, and powder raw materials into required cement raw meal in the cement manufacturing plantVertical raw mill is an ideal grinding mill that crushing, drying, grinding, grading transfer set in one It can be widely used in cement, electric power, metallurgy, chemical industry, nonmetallic ore, and other industriesVertical Raw Mill Cement Raw Mill Raw Mill In Cement Plant2023年5月12日 The most energyintensive process is grinding The main equipment for grinding construction materials are balltube mills, which are actively used in industry and are constantly being improved The main issue of improvement is to reduce the power consumption of a balltube mill with crosslongitudinal movement of the loadPower Calculation of BallTube Mill Drives in the
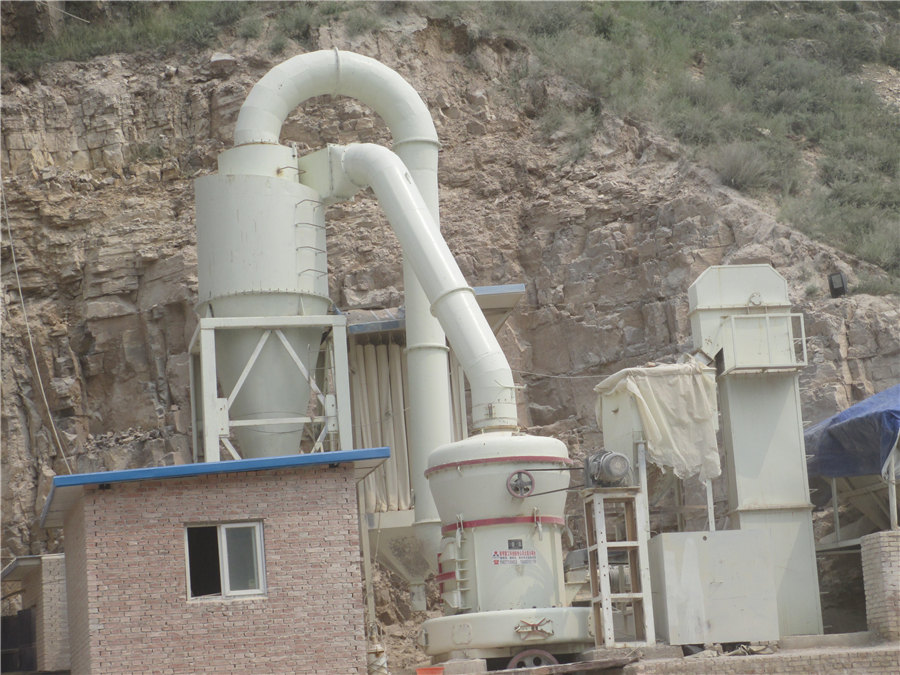
Paper Making Process: From Raw Materials to Finished
2023年7月13日 In the process of making paper, manufacturers treat raw materials like wood fiber and recycled fiber mechanically and chemically to produce paper products The process of making paper has steps like preparing the raw materials, pulping, refining, screening, pressing, drying, and finishing, which improves the paper’s properties and final product2016年10月5日 A raw material moisture of up to 8 % can be dried when utilizing the preheater exit gases only If hot air from an air heater is also supplied, then a raw material moisture of up to 18 % can be handled The power requirement is 10–20 % lower than a ball mill, depending upon the grindability and moisture content of the raw material Other EnergyEfficient Technologies in Cement Grinding2023年11月2日 Please describe the typical feed mill's raw material intake flow, and how quality assurance is managed during that process Brackx: Our customers will usually have an elaborate set of quality procedures in place at their intake gate to make sure that the quality of the incoming raw materials is checked before they release it into productionHow raw material identification can safeguard the feed mill 2015年6月19日 The basic parameters used in ball mill design (power calculations), rod mill or any tumbling mill sizing are; material to be ground, characteristics, Bond Work Index, bulk density, specific density, desired mill Ball Mill Design/Power Calculation
.jpg)
Grid Interconnection Studies of Bagasse Based Co
2016年7月18日 • An excellent Raw Material for power generation •Existing 81 sugar mills with an annual capacity of about six million tons sugar •The industry crushes about 30 40 million Sr No Name of Sugar Mill Installed Capacity (MW) Spillover to National Grid (MW) Summer Winter Summer Winter 1 Fatimah Sugar Mills 120 107 年8月28日 Ideally, the plant should be situated near riceproducing areas to reduce transportation costs for raw materials Proximity to the market or distribution centers is also essential for minimizing delivery times and costs The Ultimate Guide to Planning and 2018年8月1日 First raw material cost or clean cotton cost is calculated Then conversion cost is estimated and added with raw material cost to give cost of production of yarn or yarn cost If energy meter is not available in the mills, the power consumption per machine shift is estimated based on installed motor HP and expected load factor While Estimating yarn cost in spinning mills Indian Textile Journal2017年7月29日 Roller mill for cement raw material grinding in China Roller mill for cement clinker grinding in Mexico Coal grinding plant in Poland 4 Advantages of Polysius roller mills at a glance: Installed power kW Throughput (Raw material of average grindability, 12 % R 009 mm) tph Amm Bmm CmmPolysius Roller Mills For grinding
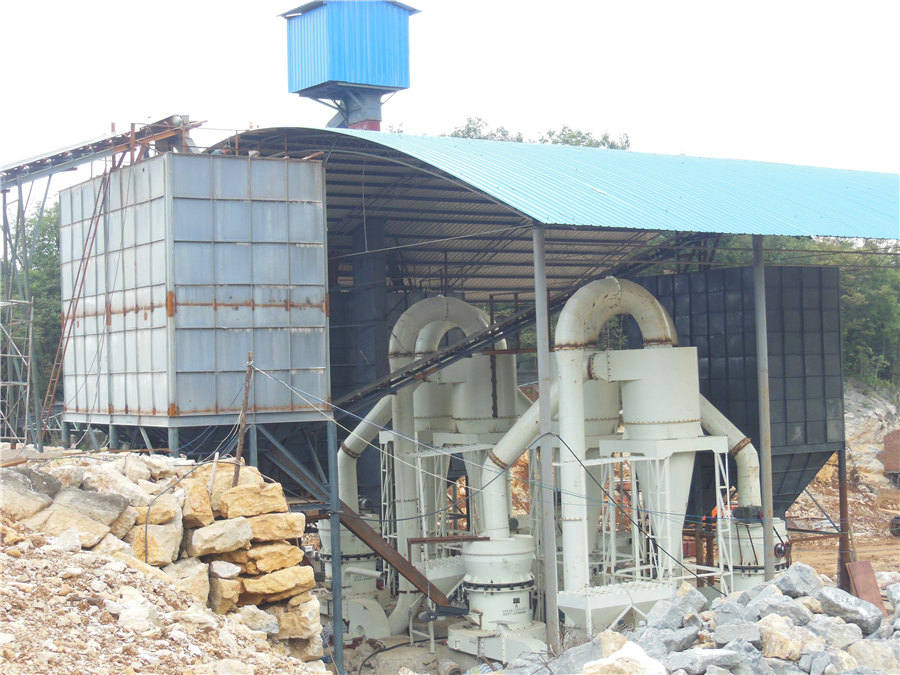
(PDF) Prediction of Raw Mill Fan Vibrations Based on
2023年6月15日 In the cement manufacturing process, kiln process fans play a vital role This article presents an extensive investigation into the prediction of Raw Mill Fan vibrations using machine learning models2021年1月29日 Vertical roller mills, VRMs, are widely used for grinding raw materials in factories engaged in the extraction and processing of minerals Any machine used for grinding or crushing consumes around Increase productivity of vertical roller mill using seven QC tools2022年3月8日 Advertisement Paper is made up of linked fibers, whether it is created in an advanced mill or by hand The fibers can be made from fabric rags, cellulose fibers from plants, and, most importantly, treesThe Ultimate List of Raw Materials for Paper Industry2015年1月30日 The generation of mill scale represents about 2% of steel produced and that is available as a secondary raw material, due to its richness in iron (about 70 to 72 % total Fe) [3] Since, it is Mill Scale: A Potential Raw Material for Iron and Steel Making
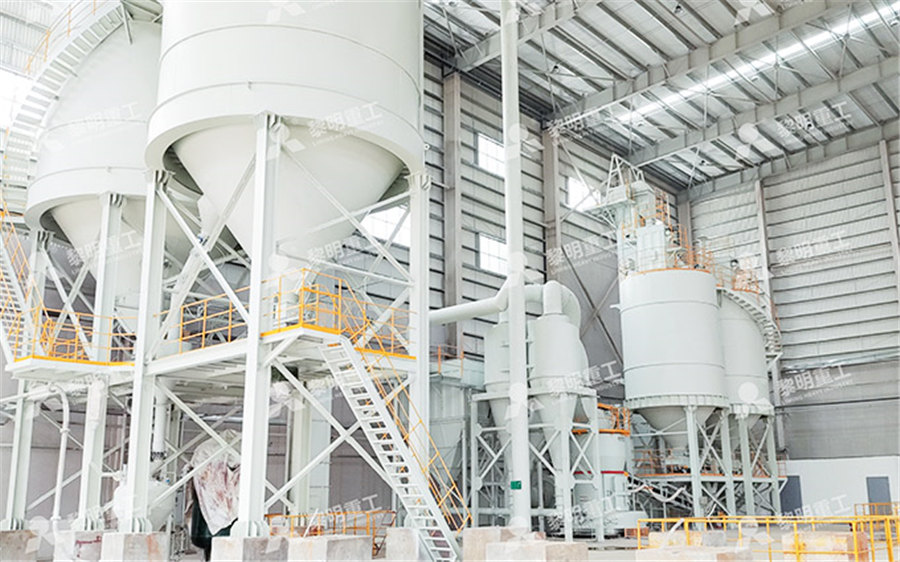
Vertical roller mill for raw Application p rocess materials
2016年1月4日 collected by the mechanical transportation equipment installed below the mill such as chain conveyor and bucket elevator etc And then they are retransported to fresh The tube mill comminutes raw materials by impact and friction between grinding balls, (Tube mill power) kW 2550 2650 (Pregrinder power) kW ― 1120 Raw mill is also called cement raw mill, similar to cement ball mill, it is an important cement milling equipment used in the cement production process Raw mill is mainly used for grinding cement raw meal in the cement factory Cement Raw Mill in Cement Plant for Cement 2021年3月10日 mineral raw materials on a large scale This idea became reality Today the company looks back on a longtime success story of developing the most modern mill technologies Behind the name of Gebr Pfeiffer more than 500 employees are all united in the endeavor to carry Jacob Pfeiffer‘s passion and drive from generation to generationPASSION FOR GRINDING irpcdnmultiscreensite1996年1月1日 To predict power draw based on mill dimensions etc a power model such as Morrell's "C" model (Morrell, 1996) is used The equations of this model can be easily entered into a spreadsheet or Power draw of wet tumbling mills and its
.jpg)
Material Particle size distribution for raw mill inlet
Furthermore, the power consumption of the raw mill grinding process was reduced by 67 percent by using exterior hot gas, as suggested in an energy and exergy analysis of the mill by Atmaca 2017年8月12日 • Material grindability • Material temperature • Material moisture • Mixture composition • Composition of raw material • Grinding roller wear • Fineness (Blaine) or residue (VOA) • Mill motor speed • Mill air flow/mill differential pressure • Temperature after the mill • Pressure before the mill • Grinding stock feedPROCESS OPTIMISATION FOR LOESCHE GRINDING 2020年11月22日 Pulp and paper mills generate huge amount of wastewater depending on the type of processes used in the plant whose unsafe disposal can be very hazardous to environment and human health(PDF) Characteristics and Treatment of Pulp and Paper Mill 2017年5月1日 roller mill 5000 – 4 roller raw material mill in operation in North America and detailed operational data of s everal other 4 an d 6 Installed drive power 3,300 kW (PDF) Grinding process optimization — Featuring case
.jpg)
Installed power (kW) Electrical Installation Guide
2022年6月22日 The installed power is the sum of the nominal powers of all powerconsuming devices in the installation This is not the power to be actually supplied in practice This is the case for electric motors, where the power rating refers to the output power at its driving shaft The input power consumption will evidently be greaterRaw mill is generally called cement raw mill, raw mill in cement plant, it refers to a common type of cement equipment in the cement plantIn the cement manufacturing process, raw mill in cement plant grind cement raw materials into the raw mix, and the raw mix is sent to the cement kiln to make cement clinker, next, clinker and other admixtures will be ground into finished cement by Raw Mill, Cement Raw Mill, Raw Mill In Cement PlantOptimasi Parameter Operasi Raw Mill Untuk Menurunkan Power Consumption Menggunakan Metode Response Surface Methodology (RSM) Studi Kasus Raw Mill Tuban 2 PT Solusi Bangun Indonesia Tbk Hatmono, Tri (2023) Optimasi Parameter Operasi Raw Mill Untuk Menurunkan Power Consumption Menggunakan Metode Response Surface Methodology (RSM) Studi Optimasi Parameter Operasi Raw Mill Untuk Menurunkan 2014年4月1日 The newly developed modular roller mill for grinding cement raw material, cement clinker, and additives with an installed power of up to 12,000 kW was specifically designed to meet those needs (PDF) The latest innovative technology for vertical roller mills
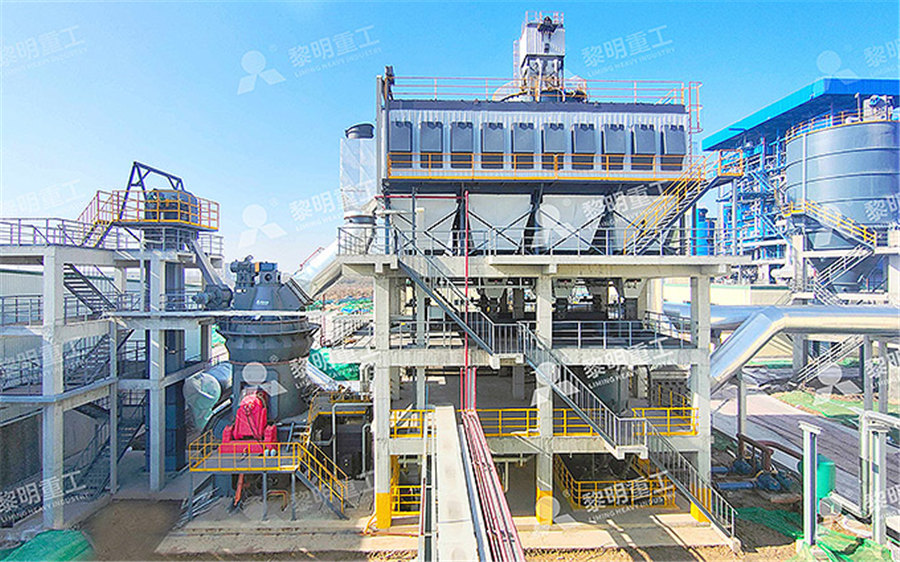
(PDF) Drives for large vertical roller mills
2017年1月1日 7 CEM 6000 kW drive for a raw material mill FLSmidth Maag Gear 8 MultiDrive with four drive units GPSE mill with an installed power of 12 000 kW and feaThe Horomill used as a raw mill is claimed to combine the effectiveness of the vertical roller mill and the roller press with a very low pressure drop in the circuit It is also expected to offer some advantage in handling raw materials Everything you need to know about cement Assuming the efficiency is 100%, the power required to remove the material is the same as the power used by the machine’s motor Each machine has a maximum power limit that it can handle Therefore, it is helpful to calculate the power required to perform a machining operation such as milling or turning and compare it to our machine’s abilityMachining Power Calculator and FormulasUnderstanding the different types of raw materials used in paper production is crucial for producing highquality paper that meets various industrial and consumer demands In this guide, we will explore the different types of raw materials used in paper production, including woodbased raw materials, recycled paper, and nonwood fiber materialsRaw Materials Used in Paper Production CNBM
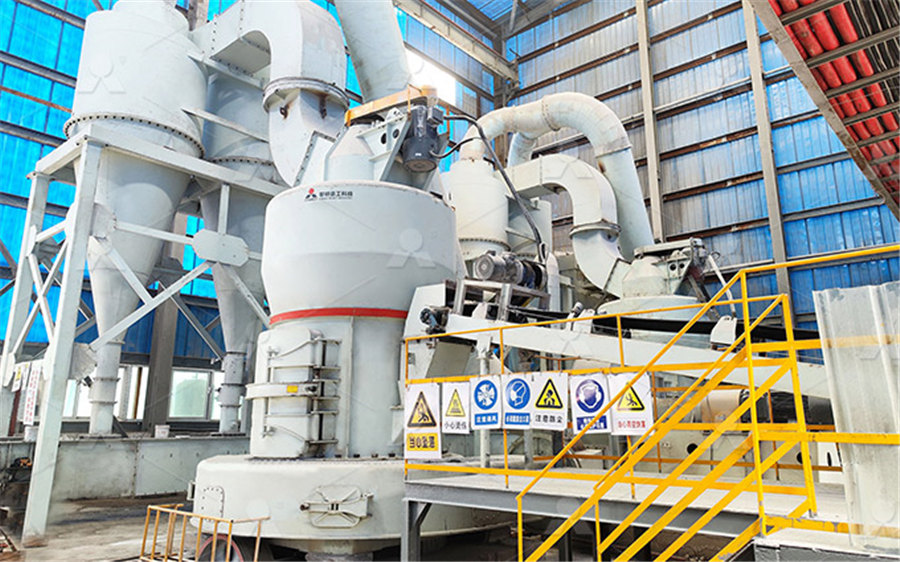
Vertical Raw Mill Cement Raw Mill Raw Mill In Cement Plant
Vertical raw mill is one kind of raw mill, generally used to grind bulk, granular, and powder raw materials into required cement raw meal in the cement manufacturing plantVertical raw mill is an ideal grinding mill that crushing, drying, grinding, grading transfer set in one It can be widely used in cement, electric power, metallurgy, chemical industry, nonmetallic ore, and other industries2023年5月12日 The most energyintensive process is grinding The main equipment for grinding construction materials are balltube mills, which are actively used in industry and are constantly being improved The main issue of improvement is to reduce the power consumption of a balltube mill with crosslongitudinal movement of the loadPower Calculation of BallTube Mill Drives in the 2023年7月13日 In the process of making paper, manufacturers treat raw materials like wood fiber and recycled fiber mechanically and chemically to produce paper products The process of making paper has steps like preparing the raw materials, pulping, refining, screening, pressing, drying, and finishing, which improves the paper’s properties and final productPaper Making Process: From Raw Materials to Finished 2016年10月5日 A raw material moisture of up to 8 % can be dried when utilizing the preheater exit gases only If hot air from an air heater is also supplied, then a raw material moisture of up to 18 % can be handled The power requirement is 10–20 % lower than a ball mill, depending upon the grindability and moisture content of the raw material Other EnergyEfficient Technologies in Cement Grinding
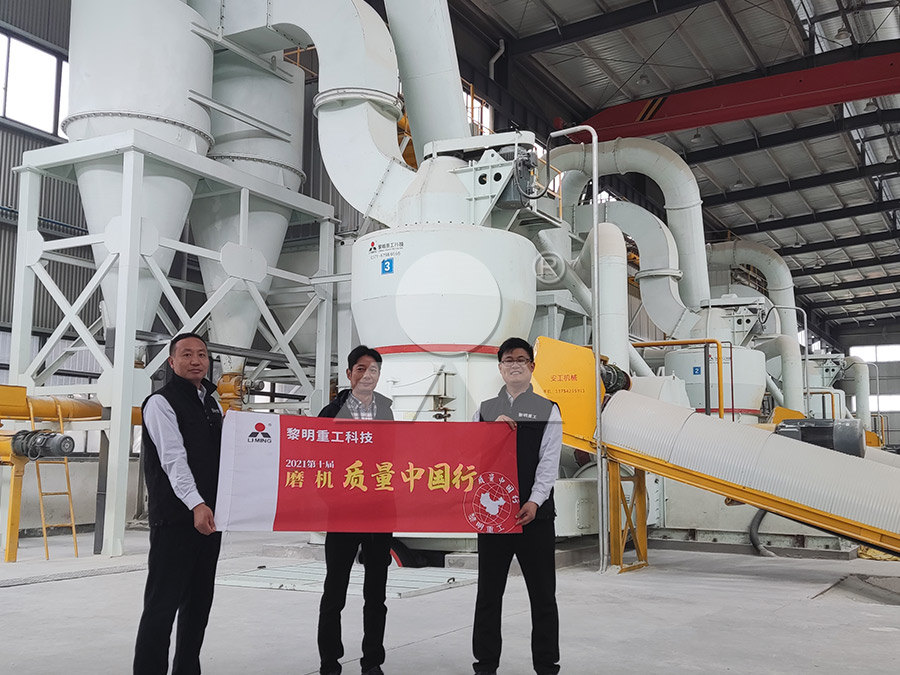
How raw material identification can safeguard the feed mill
2023年11月2日 Please describe the typical feed mill's raw material intake flow, and how quality assurance is managed during that process Brackx: Our customers will usually have an elaborate set of quality procedures in place at their intake gate to make sure that the quality of the incoming raw materials is checked before they release it into production