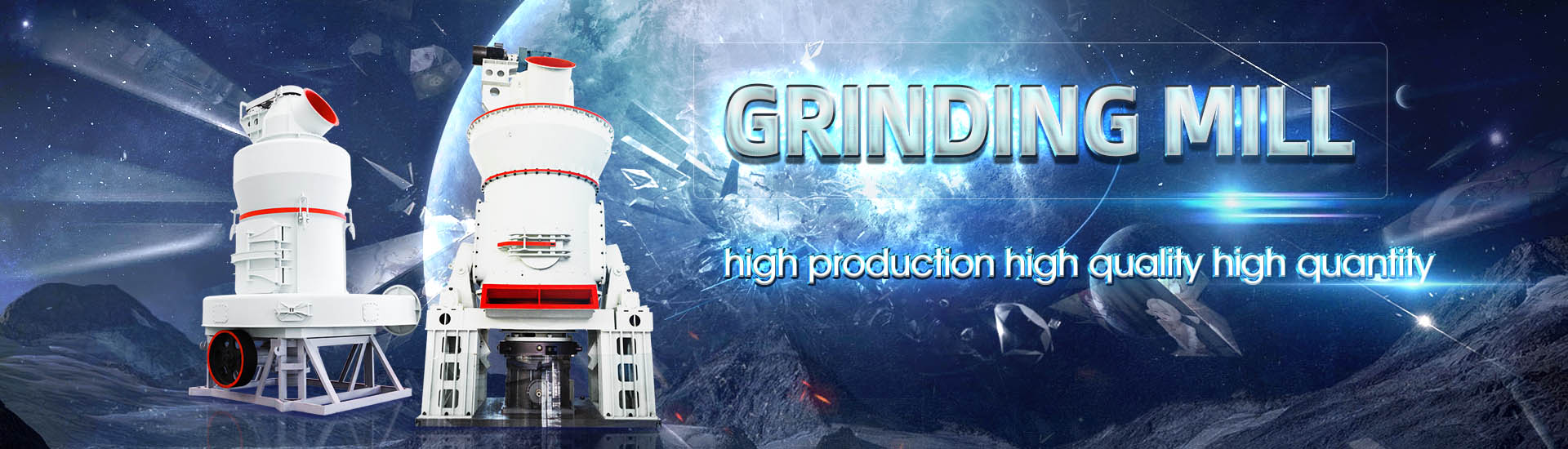
Ore mill diameter

Calculate and Select Ball Mill Ball Size for Optimum Grinding
2013年8月3日 In Grinding, selecting (calculate) the correct or optimum ball size that allows for the best and optimum/ideal or target grind size to be achieved by your ball mill is an important thing for a Mineral Processing Engineer AKA Metallurgist to do Often, the ball used in ball 2024年9月24日 grinding quartz and copper ore in a laboratory ball mill, there has been defined a general form of the equation for determining: the optimal ball diameter depending on the grain THE OPTIMAL BALL DIAMETER IN A MILL 911 2023年10月27日 Kabezya and Motjotji observed that 30 mm diameter balls were better than 10 mm and 20 mm diameter balls in grinding a quartzite ore of a feed size from −8 to +56 mm A Review of the Grinding Media in Ball Mills for Mineral 2023年11月24日 Kabezya and Motjotji observed that 30 mm diameter balls were better than 10 mm and 20 mm diameter balls in grinding a quartzite ore of a feed size from −8 to +56 mm Grinding Media in Ball Mills for Mineral Processing
.jpg)
The Effect of Ball Size Diameter on Milling Performance
2024年4月28日 Milling is the third and final stage of comminution after crushing which involves the reduction of solid particle sizes to micron size level The size reduction is achieved by a 2015年6月19日 Use this online calculators for Motor Sizing and Mill sizing as well as mill capacity determinators In extracting from Nordberg Process Machinery Reference Manual I will also provide 2 Ball Mill Sizing (Design) Ball Mill Design/Power Calculation1988年4月1日 Ball mill scaleup is primarily by increasing mill diameter This is subject to diameter relationships varying from the square root of the diameters in an inverse ratio to the Diameter factors affecting ball mill scaleup ScienceDirect2024年1月1日 Batchgrinding tests with the PGM ore samples used a laboratory mill with a diameter of 600 mm and a length of 485 mm Samples were characterized elsewhere and the Simulating largediameter industrial ball mills from batch
.jpg)
THE OPTIMAL BALL DIAMETER IN A MILL
Grinding media play an important role in the comminution of mineral ores in these mills This work reviews the application of balls in mineral processing as a function of the materials used to manufacture them and the mass loss, as 2022年6月29日 imperfect and ore hardness can vary with size, grindability tests are designed to best represent the size reduction of the industrial equipment analysed For that reason, it is SAG Mill Testing Test Procedures to Characterize Ore The optimal ball diameter in a mill 333 The grinding efficiency of the narrow particle size fractions with ball charge of various diameters has been observed through the constant of milling rate k in the equation of the grinding kinetics THE OPTIMAL BALL DIAMETER IN A MILL2024年10月13日 Generally, a larger mill diameter allows for higher throughput and more grinding media, resulting in better particle size reduction The length of the mill affects the residence time of the material, with longer mills providing increased contact between the grinding media and the ore 2 Total Horsepower:Understanding ball mill specifications for optimal performance
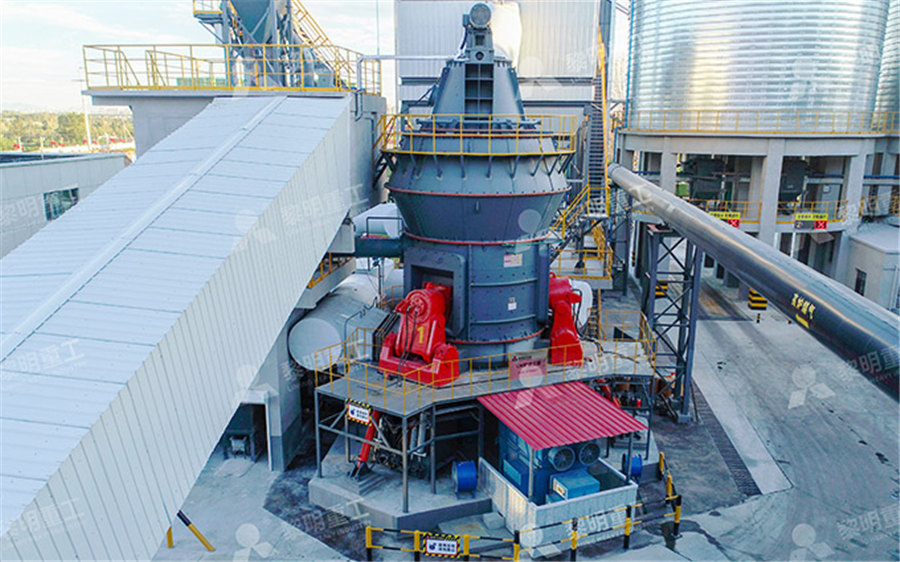
What are the models of gold ore ball mills? NEWS
2024年10月13日 Gold ore ball mills are classified based on the mill diameter and loaded capacity Several popular models are available, with different specifications to suit various mining and mineral processing applications Here are some common models of gold ore ball mills: 1 Wet Overflow Ball Mill: This mill incorporates a steel drum with a layer of 2018年4月17日 The early history of autogenous mills in the United States and Canada has featured mills of large diameter and short length Primary autogenous and semiautogenous mills in Sweden and South Africa have much larger length to diameter ratios than mills in the United States and Canada Ore Testing for AG SAG Grinding Mill DesignAutogenous and SAG SemiAutogenous Mill Design Calculations2013年8月1日 Apart from these cost factors, one of the major unsolved problems in the optimal design of ball mills concerns the equilibrium media size distribution in the mill, which is determined by the rate at which makeup media is added to the mill, as well as the rate at which these grinding media are consumed (Austin and Klimpel, 1985)Reliable prediction of grinding media Consumption of steel grinding media in mills – A reviewDependence of milling rate constant k while grinding particular size fractions of copper ore upon ball diameter db in the charge Figure 3 shows the dependence of optimal ball diameter dbo on mean grain quartz diameter d in a fraction, in the coordinate system [lnd; lndbo] in Fig 3 points to the fact that there is a strong correlating (PDF) The Optimal Ball Diameter in a Mill Academia
.jpg)
Energy Efficiency Analysis of Copper Ore Ball Mill Drive
2022年8月29日 drive system to be overloaded when the mill filled with copper ore is started For this reason, the mill is stopped only in the case of a failure or planned maintenance work The aim is to minimize the potential number of startups, as the mill at a standstill must be later started under full load In the case of a prolonged downtime, the moist entirely possible for a relatively ‘soft’ ore with Axb ~70 to have similar SAG milling Ecs requirements as a relatively competent ore with Axb ~40, depending on the cumulative differences in circuit conditions The challenge with data obtained from productionscale mills is that ‘onevariableatatime’ trials are rareSAG Mill Design and Benchmarking Using Trends in the 2023年11月2日 III181 0 5 10 15 20 25 Number 02 23 34 45 56 6+ Mill diameter (m) Figure 1: Ball mill diameters used for power draw analysis 0 400 0 800 1200 0 400 800 1200Large Diameter SAG Mills Need large Diameter Ball Mills 2024年1月1日 Good agreement was reached when model predictions were compared to the discharge of largediameter mills grinding Itabirite iron ore and PGM ore In both cases it was evident that the model slightly overestimated product fineness, but this could be corrected by reducing the s 1 E parameter by 5 % This value is strongly correlated with the no Simulating largediameter industrial ball mills from batch
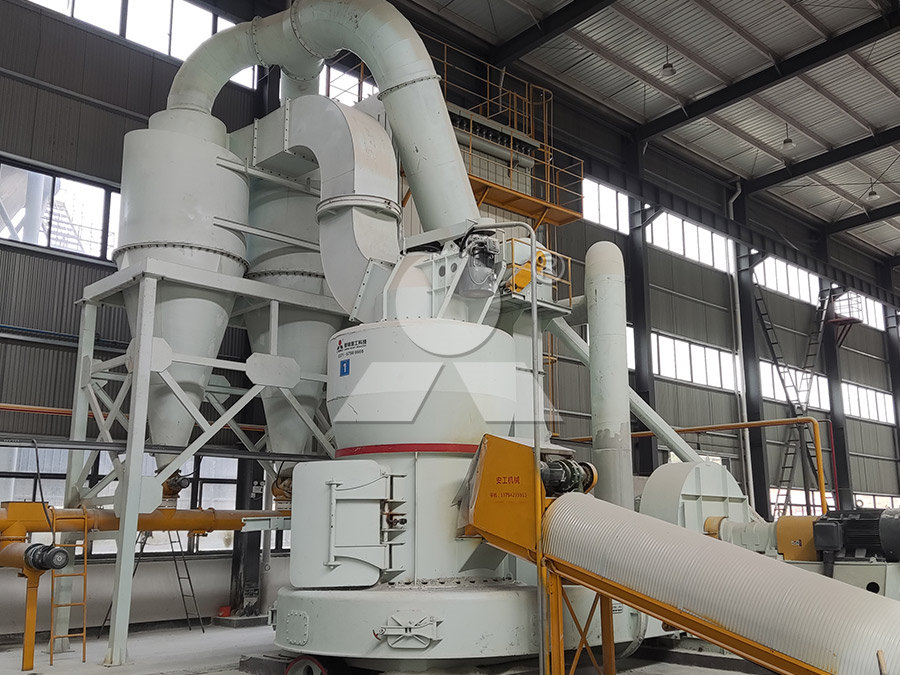
What Factors Will Influence Ball Mill Grinding
2021年3月26日 Ball mill grinding efficiency is influenced by many factors: ore grindability, feed size, grinding product size, ball mill diameter and length, ball mill working speed, liner type, steel ball loading system, grinding concentration, 2012年1月1日 Simulation outcomes suggest that mill diameter, topup ball diameter, inmill flow pattern, and two scaleup correction factors in Austin's model have a greater bearing on mill productThe optimal ball diameter in a mill Request PDF2017年2月13日 BallRod Mills, based on 4″ liners and capacity varying as 26 power of mill diameter, on the 5′ size give 20 per cent increased capacity; on the 4′ size, 25 per cent; and on the 3′ size, 28 per cent EFi, used and fo is the Ball Mills 911Metallurgist2015年4月16日 a mill grindout (no ore feed) of 10 to 20 minutes is also performed before mill inspection or relining The complete grindout is required to obtain the accurate ball load measurement or the percentage by volume of balls in the Optimization of mill performance by using SciELO
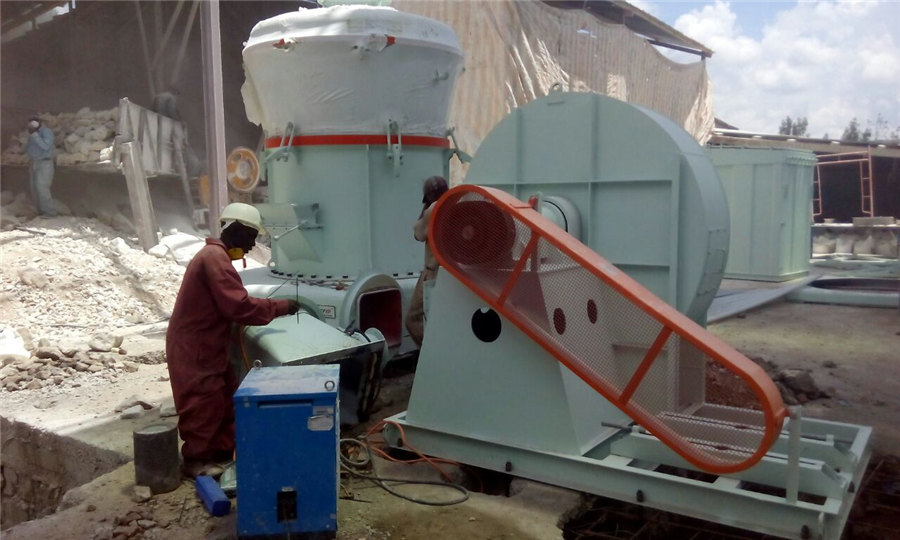
SAG Mill Grinding Circuit Design 911Metallurgist
2016年6月6日 The ratio of the trunnion thickness to trunnion diameter in a mill of 2,134 m diameter is almost twice that of a mill of 5,8 m diameter, ie a ratio (T/D) of 0,116 to 0,069 for the large mill However the design stress levels at the trunnion/head transition in the case of the large mill are almost 250% of those in the small mill2024年10月16日 The aspect ratio (mill diameter/mill length) of autogenous and semi autogenous mills varies widely and can be as high as three or as low as 05(PDF) Toward a Simple Approach Determining Single Stage SAG mill 2024年7月26日 diameter cores (>150mm) Therefore, it is not costeffective to test a large number of samples at pilotscale, and smallscale tests were developed for ball mill index values for a given ore type (McKen, Verret, Williams, 2006) SAG Mill Testing Test Procedures to Characterize Ore 2024年1月2日 a pilotscale ball mill (0416 m diameter) and Vale’s industrial mill (518 m diameter), in operation in Vitoria, Espírito Santo, Brazil The pilotscale and the batch mills used were those Population balance model approach to ball mill
.jpg)
SAG Mill Liner Design 911Metallurgist
2016年6月6日 Interlock mill drive motor(s) with new ore feed supply so that mill, especially a semiautogenous mill, does not run “starved” for feed This will reduce occasions for damage to mill liner by severe ballonlinercontact To further complicate the problem, larger diameter mills are often designed to be operated either unidirectionally 1988年4月1日 ( 7 ) Since as mill diameter increases the mill speed in rpm decreases and the number of balls per unit of capacity decreases, the number of ball to ore con tacts decreases (8) As mill diameter increases some of the balls are lifted higher and the average energy level of the ball to ore contacts increases with mill diameterDiameter factors affecting ball mill scaleup ScienceDirect2024年11月20日 Ore grinding machines can be divided into many types according to different classification methods, each with significant characteristics The following is a general introduction to the types of oregrinding machines Ore Grinding Machines: Ball Mill, Rod Mil2021年7月1日 The increase in mill diameter evidently resulted in an increase in mill holdup, but without an associated increase in mill power Indeed, the increase in mill diameter resulted in even a reduction in mill power from 846 to 602 W The net result was a dramatic reduction in specific breakage rates with increase in mill diameter, shown in Fig 19 Predicting the effect of operating and design variables in
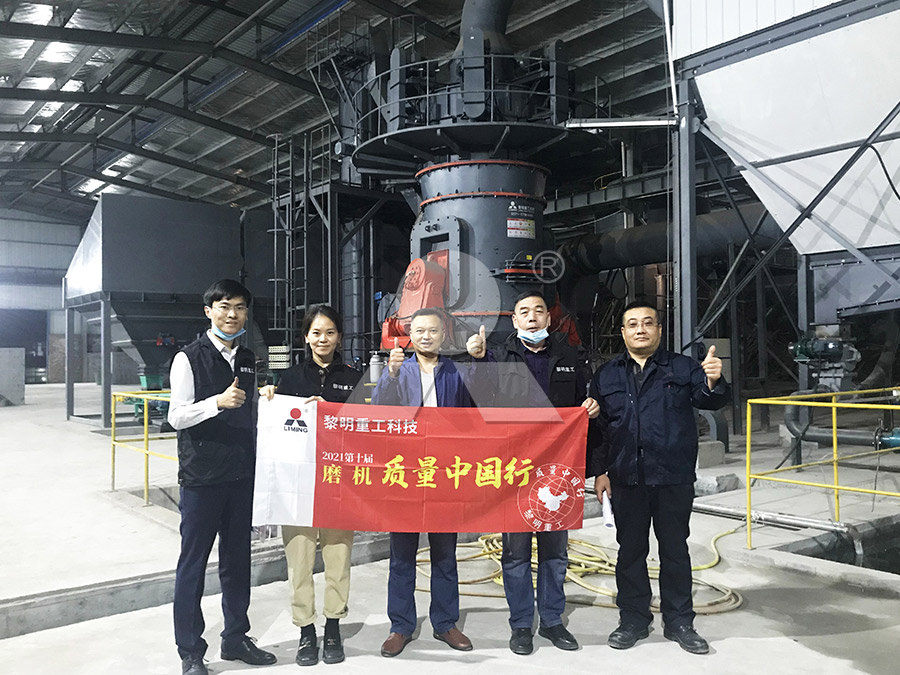
HPGR 911Metallurgist
2016年7月14日 A Cerro Verde expansion used a similar flowsheet as the 2006commissioned circuit to triple circuit capacity The expansion circuit includes eight MP1250 cone crushers, eight HPGRs (also 24 x 17m units, with 5 MW 2024年4月26日 Grinding Mills: Grinding mills, such as ball mills and rod mills, are commonly used for grinding iron ore These mills contain grinding media (steel balls or rods) that tumble and impact the ore, causing it to break into smaller particles The choice of grinding mill depends on factors such as the desired product size, capacity requirements Iron Ore Processing: From Extraction to Manufacturing2022年1月1日 Population balance modeling approach to determining the mill diameter scaleup factor: Consideration of size distributions of the ball and particulate contents of the mill Based on the machine learning method, this study analyzed the full process parameters (ie, ball mill power, fresh ore feed rate, hydrocyclone feed pump power Population balance modeling approach to determining the mill diameter 1987年7月1日 The performance of various diameter ball mills can now be simulated using the following mechanisms: (1) an orespecific breakage distribution function determined from pendulum tests (the results are given in Table III); (2) a breakagerateparticlesize relationship for a given ball mill diameter obtained from the known constant relationship Modelling the performance of industrial ball mills using
.jpg)
(PDF) A mechanistic model of SAG mills ResearchGate
2014年1月1日 Figure 8Comparison of measured (symbols) and predicted size distributions (lines) from milling of copper ore in a 6´x 2´ pilotscale AG mill (Carvalho and Tavares, 2014) The assumption that 2022年1月1日 Variation of the mill diameter exponent γ with the upper cutoff size of the product x* and size distribution of the particulate contents of the mill (as characterized by wt% passing 149 μm) for dry grinding of vanadium ore in 464 and 749 cm diameter ball millsPopulation balance modeling approach to determining the mill diameter 12 m diameter and a length of 3–5 m, made of steel plates and reaching up to 22 MW consumption power For the mill feed; the substancepouredintothe mill tobe ground, can be either ore alone (AG mill) or ore with grinding medium (SAG mill) The grinding medium can be steel balls (Ball mill) or steel rod (Rod mill) Inside a mill, maExperimental observations of mill operation parameters 2018年10月23日 Dimensionality in ball mill dynamics N Arbiter Introduction The theoretical analysis of tumbling mill energetics and performance has largely neglected mill dimensionality, and, in particular, the importance of the length/diameter (LID) ratio This is in spite of the fact that practice varies substantially:Dimensionality in ball mill dynamics Springer
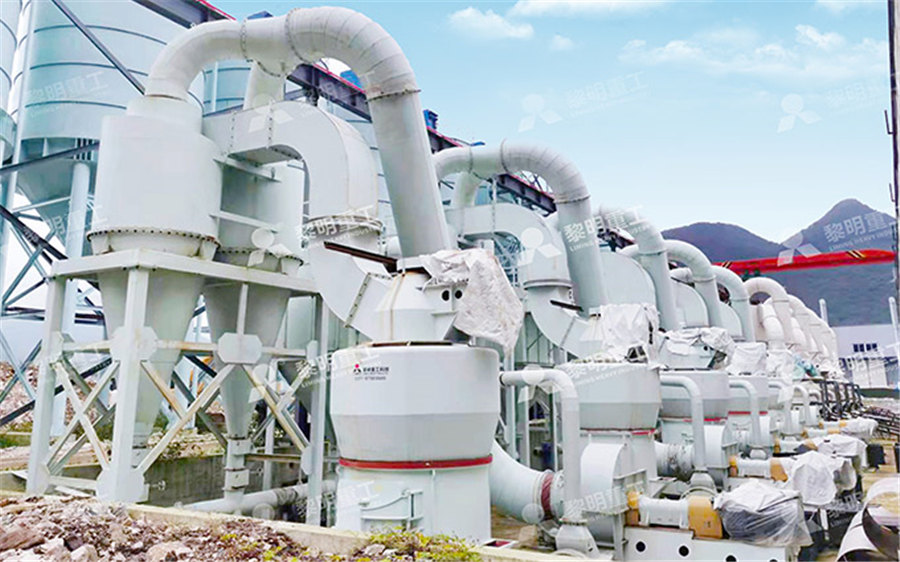
THE OPTIMAL BALL DIAMETER IN A MILL
The optimal ball diameter in a mill 333 The grinding efficiency of the narrow particle size fractions with ball charge of various diameters has been observed through the constant of milling rate k in the equation of the grinding kinetics 2024年10月13日 Generally, a larger mill diameter allows for higher throughput and more grinding media, resulting in better particle size reduction The length of the mill affects the residence time of the material, with longer mills providing increased contact between the grinding media and the ore 2 Total Horsepower:Understanding ball mill specifications for optimal performance2024年10月13日 Gold ore ball mills are classified based on the mill diameter and loaded capacity Several popular models are available, with different specifications to suit various mining and mineral processing applications Here are some common models of gold ore ball mills: 1 Wet Overflow Ball Mill: This mill incorporates a steel drum with a layer of What are the models of gold ore ball mills? NEWS2018年4月17日 The early history of autogenous mills in the United States and Canada has featured mills of large diameter and short length Primary autogenous and semiautogenous mills in Sweden and South Africa have much larger length to diameter ratios than mills in the United States and Canada Ore Testing for AG SAG Grinding Mill DesignAutogenous and SAG SemiAutogenous Mill Design Calculations
.jpg)
Consumption of steel grinding media in mills – A review
2013年8月1日 Apart from these cost factors, one of the major unsolved problems in the optimal design of ball mills concerns the equilibrium media size distribution in the mill, which is determined by the rate at which makeup media is added to the mill, as well as the rate at which these grinding media are consumed (Austin and Klimpel, 1985)Reliable prediction of grinding media Dependence of milling rate constant k while grinding particular size fractions of copper ore upon ball diameter db in the charge Figure 3 shows the dependence of optimal ball diameter dbo on mean grain quartz diameter d in a fraction, in the coordinate system [lnd; lndbo] in Fig 3 points to the fact that there is a strong correlating (PDF) The Optimal Ball Diameter in a Mill Academia2022年8月29日 drive system to be overloaded when the mill filled with copper ore is started For this reason, the mill is stopped only in the case of a failure or planned maintenance work The aim is to minimize the potential number of startups, as the mill at a standstill must be later started under full load In the case of a prolonged downtime, the moist Energy Efficiency Analysis of Copper Ore Ball Mill Drive entirely possible for a relatively ‘soft’ ore with Axb ~70 to have similar SAG milling Ecs requirements as a relatively competent ore with Axb ~40, depending on the cumulative differences in circuit conditions The challenge with data obtained from productionscale mills is that ‘onevariableatatime’ trials are rareSAG Mill Design and Benchmarking Using Trends in the

Large Diameter SAG Mills Need large Diameter Ball Mills
2023年11月2日 III181 0 5 10 15 20 25 Number 02 23 34 45 56 6+ Mill diameter (m) Figure 1: Ball mill diameters used for power draw analysis 0 400 0 800 1200 0 400 800 年1月1日 Good agreement was reached when model predictions were compared to the discharge of largediameter mills grinding Itabirite iron ore and PGM ore In both cases it was evident that the model slightly overestimated product fineness, but this could be corrected by reducing the s 1 E parameter by 5 % This value is strongly correlated with the no Simulating largediameter industrial ball mills from batch