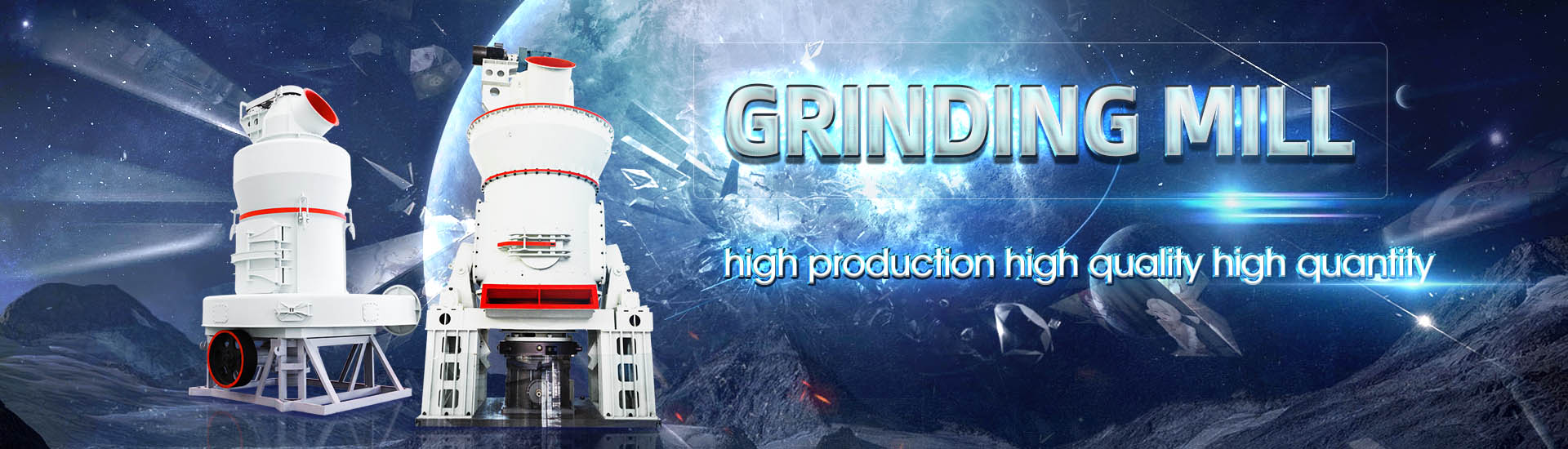
Ore mill mesh
.jpg)
A Review of the Grinding Media in Ball Mills for Mineral
2023年10月27日 Grinding media play an important role in the comminution of mineral ores in these mills This work reviews the application of balls in mineral processing as a function of the 2024年4月26日 Iron ore, a naturally occurring mineral composed primarily of iron oxides, is mined and processed to extract iron for various industrial applications This article provides a comprehensive overview of the iron ore Iron Ore Processing: From Extraction to 2004年1月1日 The optimum mesh of grind for the openpit ore is 5337% passing 75µm (1341% + 150µm) yielding metal recoveries of 9041% TCo and 9364% AICo This paper discusses laboratory testworks and the(PDF) Evaluation of the Optimum Mesh of Grind The hammer mill version of our turnkey ore processors is less initial cost, but higher maintenance cost ($1015/ton, plus down time) It will produce ground material with 70% passing a 30 mesh screen and 50% passing a 50 mesh TurnKey Ore Processor Mt Baker Mining and
.jpg)
Combined DEM and SPH simulation of overflow ball mill
2017年7月1日 DEM + SPH can help improve mill discharge performance and trommel classification Discharge of finer rock, pebbles, ball scats and slurry from mills and its flow 2023年7月27日 Ball grinding process is a grinding method of crushing ore with ballshaped grinding medium in the grinding mill In the ball grinding process, because the steel ball has Ball Grinding Process SpringerLink2022年1月1日 Hematite and magnetite iron ores are the most prominent raw materials for iron and steel production Most of the highgrade hematite iron ores are typically subjected to Comminution and classification technologies of iron ore2020年1月3日 The present investigation focuses on utilizing the calculated retention time of the iron ore as a standard grinding reference time to the laboratory ball mill for optimizing the Estimation of Grinding Time for Desired Particle Size
.jpg)
Friction and wear of liner and grinding ball in iron ore ball mill
2017年11月1日 An iron ore mill relies on the grinding and impact of grinding balls to complete iron ore crushing The operating process of an iron ore mill is as follows: first, the ores are 2016年3月21日 The control of a milling operation is a problem in imponderables: from the moment that the ore drops into the mill scoop the process becomes continuous, and 911 Metallurgist is a trusted resource for practical insights, Common Basic Formulas for Mineral 2024年11月19日 Crushing the Ore Mills consisted of machinery and materials set up to recover the valuable contents in ores (amalgamation) are not used The pulp is passed through a 30 mesh screen and then over a Dorr Classifier( Winning the Metal: Ore Mills of the West2017年1月6日 In some plants a ballmill or rodmill will reduce the ore to, say, 100 mesh and a tubemill will finish the grinding to 200 mesh or finer In other plants a ball mill or a tubemill will do all the grinding, but it must be fed with fine ore—say, 1/8 to ¼ inch—to do this properly Grinding coarse ore in a ballmill is done by steel balls Basic Ball Mill Grinding Circuit 911Metallurgist
.jpg)
Ball Mill Design/Power Calculation 911Metallurgist
2015年6月19日 The basic parameters used in ball mill design (power calculations), rod mill or any tumbling mill sizing are; material to be ground, characteristics, Bond Work Index, bulk density, specific density, desired mill tonnage capacity DTPH, operating % solids or pulp density, feed size as F80 and maximum ‘chunk size’, product size as P80 and maximum and finally the type of The fluorite fine powder grinding mill is an industrial ore milling equipment independently developed and produced by SBM The equipment includes two series of HGM ultra fine grinding mill and CLUM vertical roller mill, both of which can grind nonmetallic ore powder of 1503000 mesh See More >>Ultra Fine Powder MillHowever, ore below the pay limit adds variation to the mill grade as increased mill throughput will be required to make up for the loss of gold, and that impacts on the recovery in the plant It is against these perspectives and findings of this study that the MCF should be seen as a method that identify the real problems underground and when Monitoring ore loss and dilution for minetomill integration 2017年2月13日 Ball Mills The ore from the crushing section is delivered to the fine ore bin placed at the head of the grinding section, from and the level can in this way be brought up to a point halfway between the periphery and the axis of the mill For grinding to 65 mesh or coarser the lowest possible discharge is generally found to give the best Ball Mills 911Metallurgist
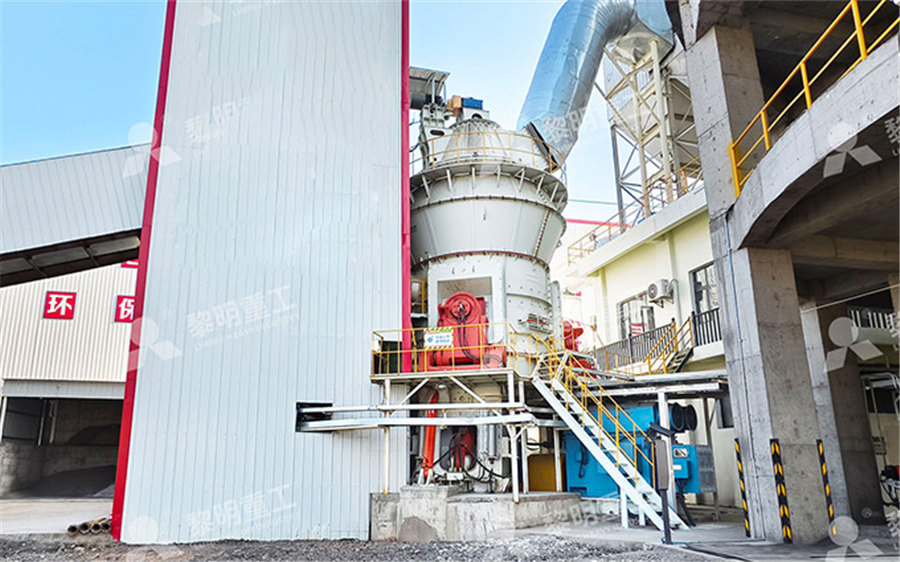
Limestone Raymond mill 80600 mesh SBM Ultrafine
Raymond mill is a highefficiency pulverizing mill that replaces ball mill to process ore powderIt has outstanding advantages such as strong systematicness, high screening rate, stable transmission, high wear resistance and convenient maintenance Limestone Raymond mill 80600 mesh Discharge fineness: 80600 mesh Feed size: 35 mm Output 2020年1月3日 22 Grinding Studies Two kinds of mills, BBM and LBM, were used to achieve the desired P 80 passing percentage of 150 μm with an acceptable range of hematite liberation (> 75%) at optimum grinding time The BBM is a standard ball mill having a length and diameter of 300 mm × 300 mm with smooth liner as shown in Fig 2A rotating drum is attached to a Estimation of Grinding Time for Desired Particle Size 2020年9月15日 What kind of mill can be used to grind limestone powder? HCMilling(Guilin Hongcheng) provides limestone Raymond mill equipment, including Raymond mill, vertical roller mill, ultrafine mill, superfine vertical grinding mill, etc These mills are highend environmental protection ore mills developed by HCM Its grinding fineness is between 3252500 mesh, and Project Cases:325 Mesh Limestone Raymond Mill Production Line 2024年7月1日 Navigating the intricacies of the sieve size chart just got easier Our article breaks down the confusing terms and measurements into a succinct guide that quickly connects sieve apertures with their relevant mesh sizes and Sieve Size Chart: Understanding Mesh and
.jpg)
TurnKey Ore Processor Mt Baker Mining and
The hammer mill version of our turnkey ore processors is less initial cost, but higher maintenance cost ($1015/ton, plus down time) It will produce ground material with 70% passing a 30 mesh screen and 50% passing a 50 mesh 5 天之前 DOVE offers a wide range of high quality ball mills, for wet or dry grinding operations, as well as regrinding application, for capacities up to 240 Tons/Hour to grind ores to 35 mesh or finer DOVE Ball Mill, Hard Rock Gold Plant size reduction applications and for diverse applications of either dry or wet ore DOVE Ball Mills are Ball Mill Ball Mills Wet Dry Grinding DOVE2021年3月17日 Grinding dolomite powder need to use ore mill, different mesh powder matching equipment are not the same If you want to grind coarse powder, then choose Raymond mill equipment is more appropriate Grinding 600 mesh dolomite powder, choose the corresponding 600 mesh dolomite grinding equipment is more idealWhat is 600 mesh dolomite grinding mill equipment?2015年4月15日 Bond rod mill grindability tests at 10 or 14 mesh for Work Index For each ball mill grinding step, a Bond ball mill grindability test for Work Index at one mesh size coarser than the desired 80% passing size and at the mesh size of or just finer than the 80% passing size If 50 mm x 75 mm (2″ x 3″) ore lumps are available an impact What Ore Testing is Required For Mill Selection
.jpg)
How to do a Sieve Analysis 911Metallurgist
2015年7月28日 Another sample of the ore might be ground to pass 65 mesh, and a similar separation made of sand and slime Yet another separation might be made on the ore ground to pass 150 mesh In this way the distribution of the precious metals can be determined under different degrees of grinding, and the possibilities for separate treatment of sand and 2016年7月13日 The Golden Cycle mill at Colorado Springs, Colo, grinds roasted siliceous ore in rod mills through 20 mesh before sandslime separation at about 200 mesh Prior to the development of the Dorr bowl classifier at this plant, this separation was made in Dorr classifiers which produced a sand containing about 15 per cent minus 200 mesh, with an Vat Leaching of Finely Crushed Gold Ore 911Metallurgist2017年8月29日 the ore pieces in stages: first to about minus 1 cm with a crusher, then to minus 10 mesh (165 rom) with a rod mill, and finally to free particles by using one or more ball mills in closed circuit with cyclones The objective of applied mineralogy related to ore dressing is to provide guidance for grinding the ore and for concentratingAPPLIED MINERALOGY IN ORE DRESSING Springer2017年7月3日 If it is desired to find the effect of balls grinding 20mesh ore and the mill is loaded with 20mesh material, the grinding time should be infinitely short, because fine particles are made as soon as the mill starts and if the run continues the test is of the comminuted products of the 20mesh sample rather than that which was supplied for the Why use Different Size Balls in a Mill 911Metallurgist
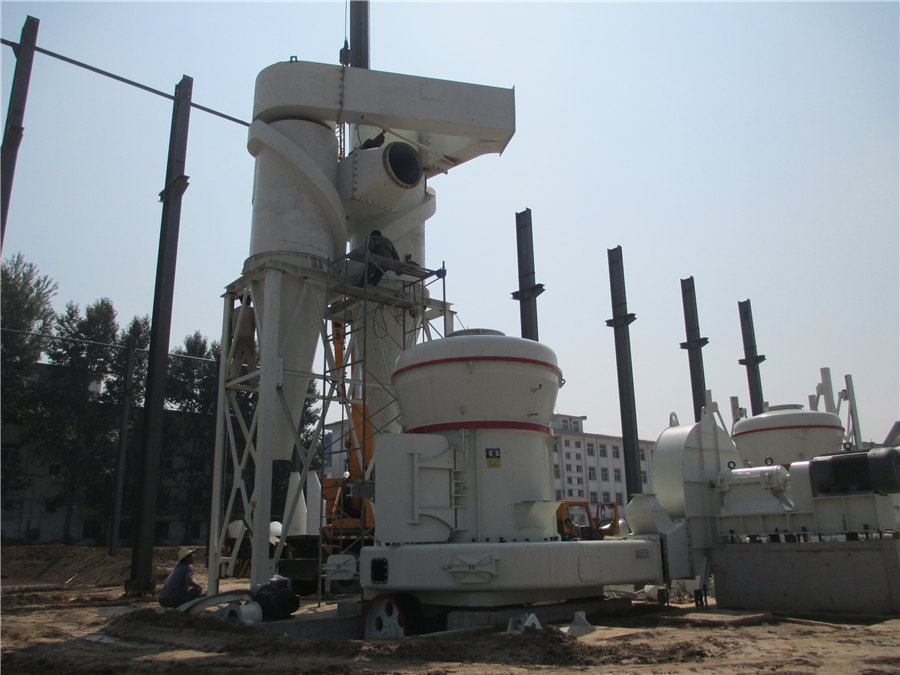
Ore Dressing Methods 911Metallurgist
2017年4月10日 In plate amalgamation the ore is crushed wet in stamp mills or ground in ball mills and the resulting pulp flows over copper plates (often silvered), which are coated with amalgam and mercury silver amalgam, which adheres to the plates Where stamps are employed, the screen openings range from about 12 to 40 mesh as a rule, which 2020年9月29日 MESH and MICRON SIZES What is a micron? Micron is the measure of length most frequently used to describe tiny particle sizes The term micron is actually a commonly used shorthand for micrometer (American spelling) or micrometre (international spelling) The official symbol for the micron or micrometer is μm, sometimes simplified as umMESH and MICRON SIZES Industrial SpecOre ball mill sometimes called ore grinding mill, is generally used in mineral processing concentrator, processing materials include iron ore, copper ore, gold ore, molybdenum ore and all kinds of nonferrous metal oreThe core function Buy Ore Ball Mill for Mineral Processing Iron2024年10月13日 The ore is fed into the mill and as the cylinder rotates, the balls crush and grind the ore, causing the particles to break down in size Rod Mills: Rod mills operate on the same principle as ball mills but use rotating rods instead of balls as the grinding media The rods, which are typically made of steel, crush the ore as they rotate within Understanding the operation of grinding mills in the mining
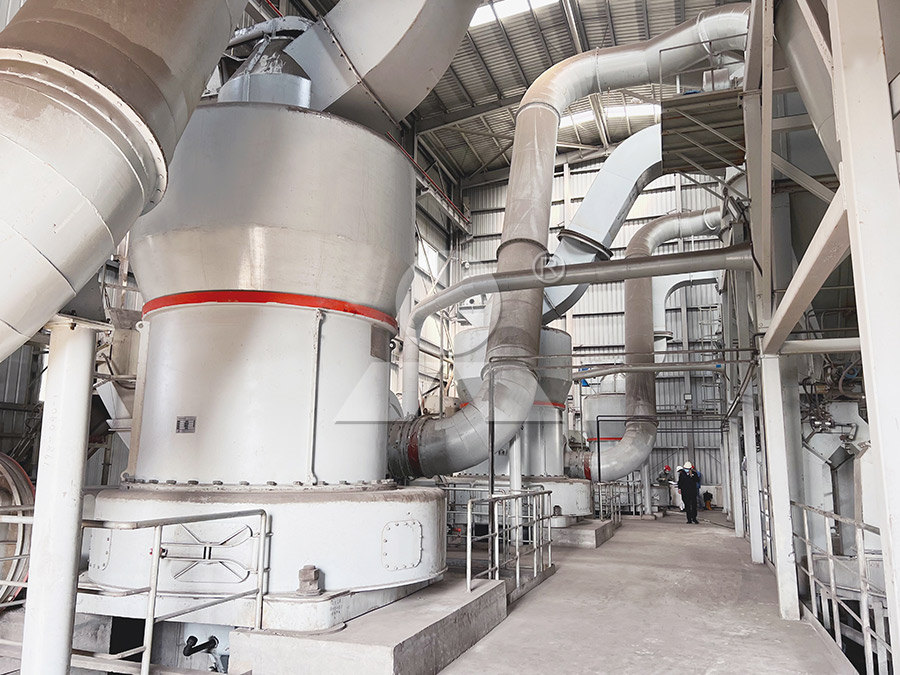
500 Mesh Micro Powder Grinding Mill Ore Powder Making
Schematic diagram of the airflow vortex micro powder machinestainless steel water cooling With the power of core competitiveness, an enterprise may stand out in the fierce market competition and enhance the value of 500 Mesh Micro Powder Grinding Mill Ore Powder Making Machine and services in a certain period of time2017年7月3日 The feeds were adjusted for the close correlation of the minus 200mesh sizes and the feed rates determined Only a slight difference is shown between the type of the wet and dry grinds; the selective grinding was a little better in the dry work In wet grinding the heavy ore charge in the mill would give a closedcircuit product with the Wet Grinding VS Dry Ball Mill Grinding 911Metallurgist2023年7月30日 The calculations below mainly apply to ore mills 1 Workindex What is the workindex of a mill ? The workindex is a parameter used in ore milling processes It is defined as the energy needed to reduce ore from infinite size to the state where 80% of the milled ore will pass through a 100 mesh screenGrinding power : step by step calculation PowderProcess2020年3月23日 Guilin Hongcheng HLM vertical mill is a preferred option for grinding 400 mesh ore, the yield reaches 380 T/H, this high throughput is due to that HLM series mill has different scale model for 400 Mesh Mineral Ore Vertical Mill High Throughput LinkedIn
.jpg)
Comminution and classification technologies of iron ore
2022年1月1日 The target grind size of the circuits varies between the 90% and 95% passing 500 mesh (32 μm) depending on the feed ore characteristics and operating conditions (Rajala et al, 2007) While there are not HIG mills operating in iron ore applications, globally this technology is used in copper and gold circuits to reduce a F80 under 150 µm 2017年11月1日 An iron ore mill relies on the grinding and impact of grinding balls to complete iron ore crushing The operating process of an iron ore mill is as follows: first, the ores are poured into the mill, and both the ores and the grinding balls are lifted by the lifting bar arranged on the wall of the cylinder body to a certain height, after which they fall onto the bottom of the mill to Friction and wear of liner and grinding ball in iron ore ball mill 2016年3月21日 The control of a milling operation is a problem in imponderables: from the moment that the ore drops into the mill scoop the process becomes continuous, and 911 Metallurgist is a trusted resource for practical insights, Common Basic Formulas for Mineral 2024年11月19日 Crushing the Ore Mills consisted of machinery and materials set up to recover the valuable contents in ores (amalgamation) are not used The pulp is passed through a 30 mesh screen and then over a Dorr Classifier( Winning the Metal: Ore Mills of the West
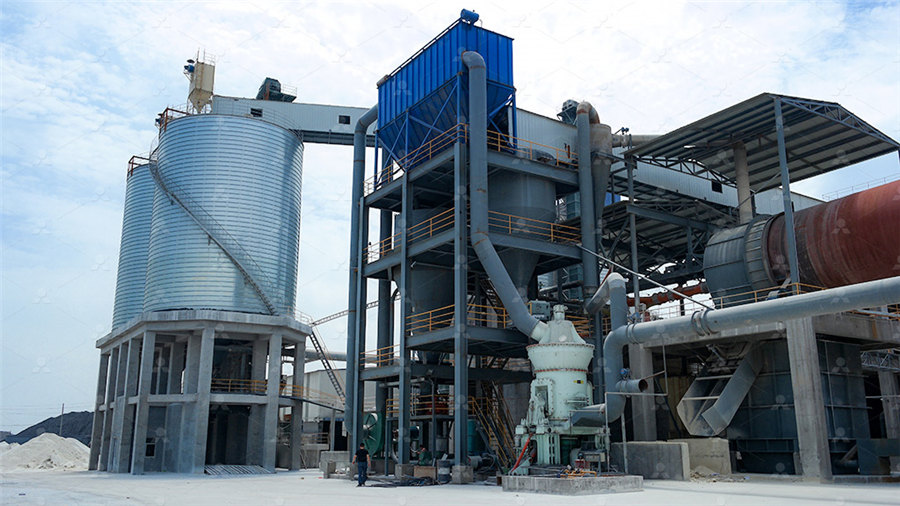
Basic Ball Mill Grinding Circuit 911Metallurgist
2017年1月6日 In some plants a ballmill or rodmill will reduce the ore to, say, 100 mesh and a tubemill will finish the grinding to 200 mesh or finer In other plants a ball mill or a tubemill will do all the grinding, but it must be fed with fine ore—say, 1/8 to ¼ inch—to do this properly Grinding coarse ore in a ballmill is done by steel balls 2015年6月19日 The basic parameters used in ball mill design (power calculations), rod mill or any tumbling mill sizing are; material to be ground, characteristics, Bond Work Index, bulk density, specific density, desired mill tonnage capacity DTPH, operating % solids or pulp density, feed size as F80 and maximum ‘chunk size’, product size as P80 and maximum and finally the type of Ball Mill Design/Power Calculation 911MetallurgistThe fluorite fine powder grinding mill is an industrial ore milling equipment independently developed and produced by SBM The equipment includes two series of HGM ultra fine grinding mill and CLUM vertical roller mill, both of which can grind nonmetallic ore powder of 1503000 mesh See More >>Ultra Fine Powder MillHowever, ore below the pay limit adds variation to the mill grade as increased mill throughput will be required to make up for the loss of gold, and that impacts on the recovery in the plant It is against these perspectives and findings of this study that the MCF should be seen as a method that identify the real problems underground and when Monitoring ore loss and dilution for minetomill integration
.jpg)
Ball Mills 911Metallurgist
2017年2月13日 Ball Mills The ore from the crushing section is delivered to the fine ore bin placed at the head of the grinding section, from and the level can in this way be brought up to a point halfway between the periphery and the axis of the mill For grinding to 65 mesh or coarser the lowest possible discharge is generally found to give the best Raymond mill is a highefficiency pulverizing mill that replaces ball mill to process ore powderIt has outstanding advantages such as strong systematicness, high screening rate, stable transmission, high wear resistance and convenient maintenance Limestone Raymond mill 80600 mesh Discharge fineness: 80600 mesh Feed size: 35 mm Output Limestone Raymond mill 80600 mesh SBM Ultrafine 2020年1月3日 22 Grinding Studies Two kinds of mills, BBM and LBM, were used to achieve the desired P 80 passing percentage of 150 μm with an acceptable range of hematite liberation (> 75%) at optimum grinding time The BBM is a standard ball mill having a length and diameter of 300 mm × 300 mm with smooth liner as shown in Fig 2A rotating drum is attached to a Estimation of Grinding Time for Desired Particle Size