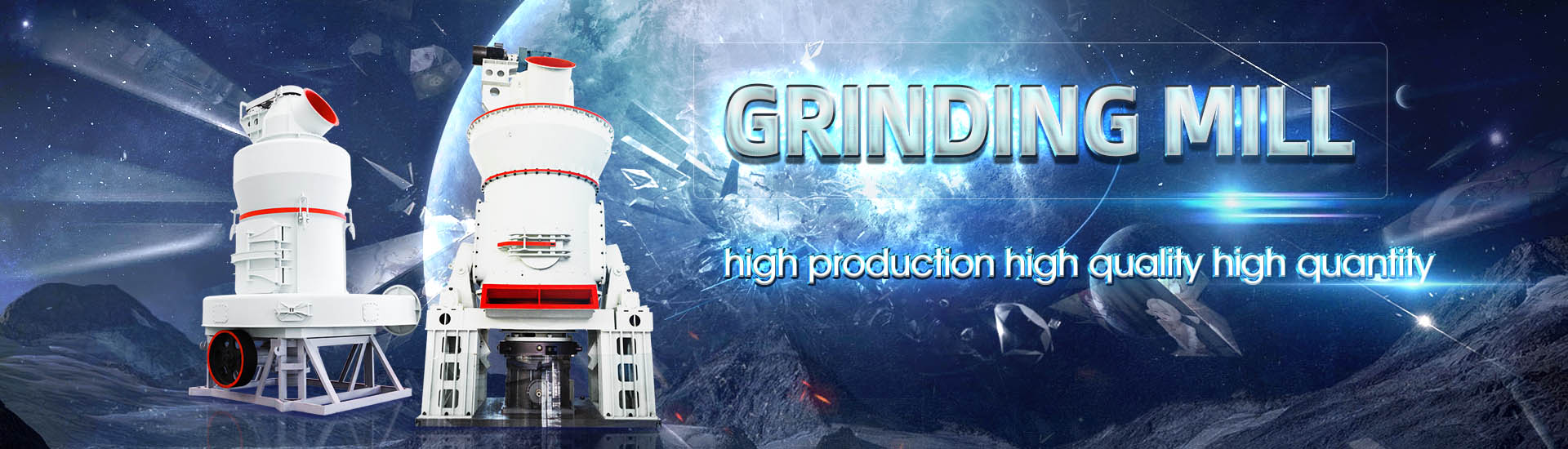
New cement production process
.jpg)
Toward smart and sustainable cement manufacturing process
2024年3月1日 In recent years, efforts have been made to improve the sustainability of cement manufacturing through the use of renewable energy, the capture of CO 2 emissions, and 2024年5月1日 LowCO 2 cement production technologies revolve around minimizing CO 2 emissions in the cement manufacturing process These innovative approaches aim to Roadmap to a netzero carbon cement sector: Strategies, 2022年11月17日 We find that novel suspension preheater rotary kilns account for approximately 99% of cement production in China in 2021 Climate change and fossil depletion are identified Modernizing cement manufacturing in China leads to 2 天之前 Providing a comprehensive guide to the entire cement production process from raw material extraction to the finished product, the industry’s favourite technical reference book is The Cement Plant Operations Handbook International
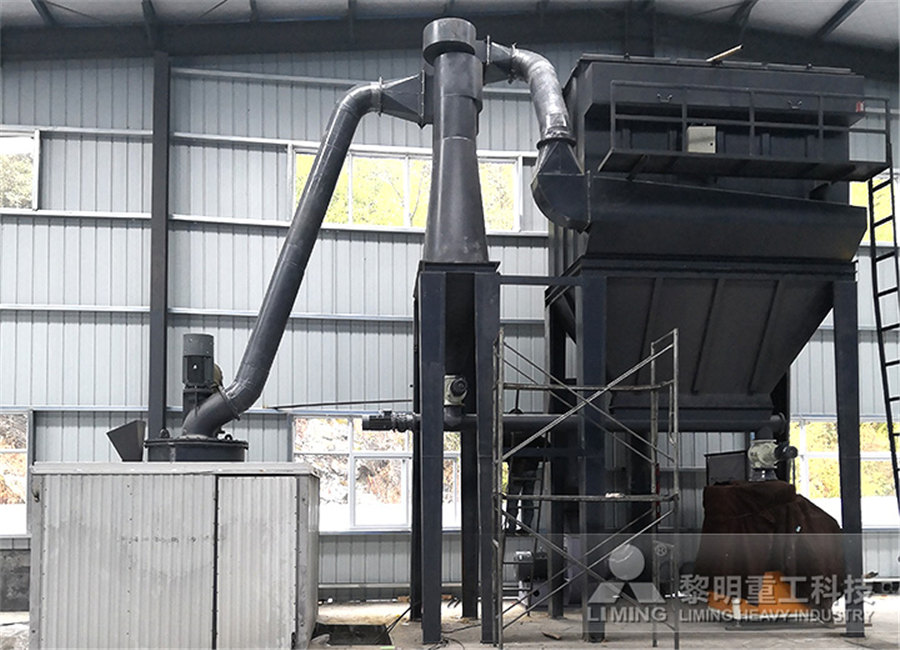
Nearterm pathways for decarbonizing global concrete production
2023年7月29日 New cement production could be curtailed through improved utilization and life extension of instock resources for concrete systems; this curtailment in turn would influence 2019年9月16日 A new process developed at MIT could eliminate the greenhousegas emissions associated with the production of cement, the world’s most widely used building material and a major source of such emissionsNew approach suggests path to emissionsfree 2024年5月22日 There are 4 stages of cement production that help maintain consistent raw material quality with minimal chemistry deviation, from quarry to silo to customer The Quarry: A practical guide to improving cement manufacturing 2021年11月16日 There are four main types of processes used in cement manufacture: Dry Process, Semidry Process, Semiwet Process, and the Wet process In all these processes, Cement Manufacturing—Technology, Practice, and
.jpg)
Revolutionary "true zero carbon" cement uses
2023年9月19日 Sublime's zero – or ultralowcarbon – cement production technology In regular cement manufacturing, limestone is heated to around 1,400 °C (2,5,52 °F) by burning fossil fuels – the first2024年10月16日 Researchers from UCLA’s Institute for Carbon Management (ICM) have developed a method to reduce carbon emissions in cement production drastically, a process that currently contributes around 8% 98% less carbon: New tech promises nearzero emissions from cement 2023年8月15日 In the cement manufacturing process, the raw mix undergoes a drying process to reduce its moisture content to less than 1% This dried mixture, known as the raw mix, is then prepared for introduction into the rotary kiln Cement: History, Types, Manufacturing Process2024年5月22日 The cement production process 1 The Quarry: The cement production process begins with the extraction of limestone and clay from the quarry 2 Crusher and PreBlending: The material is then crushed to reduce particle sizes and blended to reduce variability in composition 3 Raw Mill and Kiln: Raw materials and additives areA practical guide to improving cement manufacturing
.jpg)
How Cement is Made Portland Cement Association
The Cement Manufacturing Process While each cement plant may differ in layout, equipment, and appearance, the general process of manufacturing portland cement is the same: crushed limestone and sand are mixed with ground clay, shale, iron ore, fly ash and alternative raw materials As materials move through the kiln, a series of complex 2020年9月26日 Cement Manufacturing Process Cement Manufacturing Process Cement Manufacturing Process Cement is a material which is used to bind other materials together Binding means it has an effect of gluing the substances together due to cohesive and adhesive action and then hardens and sets in order to become permanent Cement is usually not used Cement Manufacturing Process Chemical Engineering WorldThe cyclone preheating system Phase IV: Calcination The calcination is the core phase of the cement making dry process The calcination of the preheated raw meal takes place in the rotary kiln of the cement plant The rotary kiln is a huge rotating furnace in which the raw meal is heated up to 1450 ⁰C and turned to clinkerHow Is Cement Produced in Cement Plants Cement Making Process5 天之前 The manufacture of Portland cement is a complex process and done in the following steps: grinding the raw materials, mixing them in certain proportions depending upon their purity and composition, and burning them to sintering in a kiln at a temperature of about 1350 to 1500 ⁰C During this process, these materials partially fuse to form nodular shaped clinker by Manufacturing of Portland Cement – Process and Materials
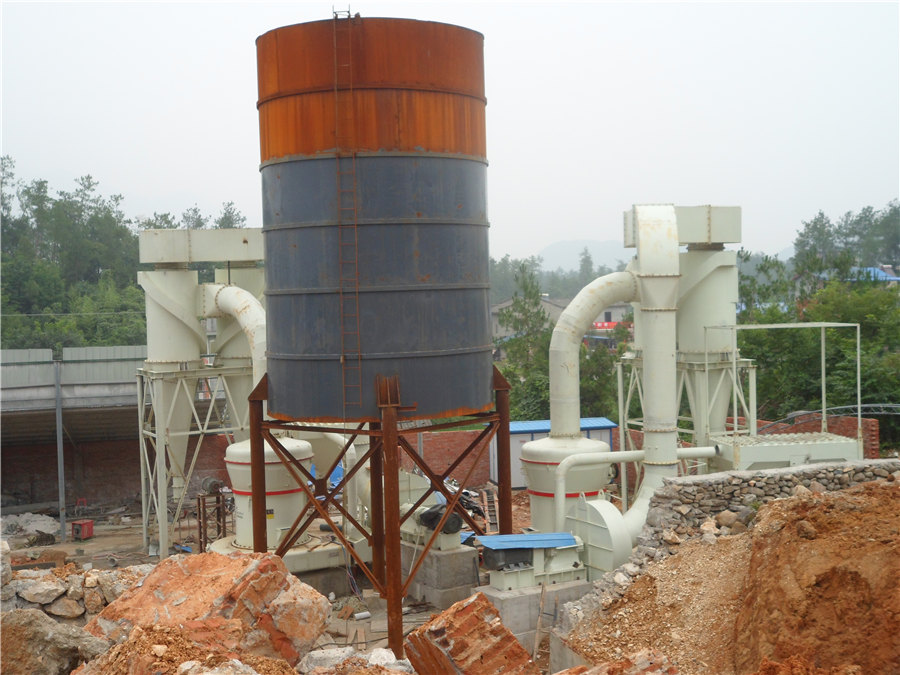
Cement Manufacturing Process: Know Extraction, Processing
2024年9月10日 Cement Manufacturing Process Cement manufacturing is an intricate process involving the extraction and grinding of raw materials, followed by blending and heating in a kiln to produce clinker This clinker is then ground with gypsum to create cement, a 2018年11月30日 Cement production process: Thermal energy demand and CO 2 emissions 30% fuel emissions thermal energy prod process emissions from calcination • ETHZ has simulated and adapted the CAP system to different cementplant flue gases; • New ratebased model was developed and used to validate fullscale CAP simulations for cement plants Process characteristics of clinker and cement production2020年8月25日 A full cement production process includes the cement crushing process, raw mill process, clinker process, and cement grinding process, cement packing process, and related process low production efficiency, and it tends to be replaced by a new dry process cement production cement equipment Raw Material Production Crusher; Vertical Raw Cement Production Process Cement Manufacturing Process AGICO CEMENT2015年12月1日 Regarding the sustainability of the cement production process, waste heat recovery (WHR) provides a potential to recover the energy from the clinker burning process The technology was spearheaded by Japanese companies before being introduced to the Chinese market in 1998 Processwise the technology for these new cement types is in Process technology for efficient and sustainable cement production
.jpg)
The Cement Manufacturing Process Thermo
2023年12月20日 Accurate cement production also depends on belt scale systems to monitor output and inventory or regulate product loadout, as well as tramp metal detectors to protect equipment and keep the operation running Slag use in cement manufacture and cementitious applications George C Wang, in The Utilization of Slag in Civil Infrastructure Construction, 2016 13222 Energy use in cement production The production of cement is an energyintensive Cement Production an overview ScienceDirect Topics2023年12月11日 CO 2 emissions in the cement industry occur primarily in the production process of clinker – an intermediate product for cement 5,6 – where CO 2 is released through both the combustion of Projecting future carbon emissions from cement production 2018年8月28日 CEMENT MANUFACTURING PROCESS PHASE II: PROPORTIONING, BLENDING GRINDING The raw materials from quarry are now routed in plant laboratory where, they are analyzed and proper proportioning of limestone and clay are making possible before the beginning of grinding Generally, limestone is 80% and remaining 20% is the clayCement Manufacturing Process The Engineering Community
.jpg)
THE STORY OF CEMENT MANUFACTURE CEMBUREAU
2021年11月24日 THE STORY OF CEMENT MANUFACTURE What is cement? Cement is a fine, soft, powdery type substance, mainly used to bind fine sand and coarse aggregates together in concrete Cement is a glue, acting as a hydraulic binder, it hardens when water is ie, added Everyone knows the word cement, but it is often confused with concrete or mortar Cement is2021年11月16日 76 4 Cement Manufacturing—Technology, Practice, and Development Fig 42 Modern dry process cement production process 424 Manufacturing of Cement Clinker The prepared raw material is called the “kiln feed” and is fed to the kiln In the kiln, this kiln feed is subjected to a thermal treatment process which consists ofCement Manufacturing—Technology, Practice, and 2023年9月19日 Sublime's zero – or ultralowcarbon – cement production technology In regular cement manufacturing, limestone is heated to around 1,400 °C (2,5,52 °F) by burning fossil fuels – the first Revolutionary "true zero carbon" cement uses electrolysis, 2024年4月18日 In the US, the same amount would cover the state of New York But concrete production releases carbon dioxide (CO₂), one of the greenhouse gases that drives climate change Cement production is an energyintensive process and the greenhouse gas emissions are hard to cut When limestone is heated in a kiln, often fueled by coal, nearly Green cement production is scaling up—and it could cut the
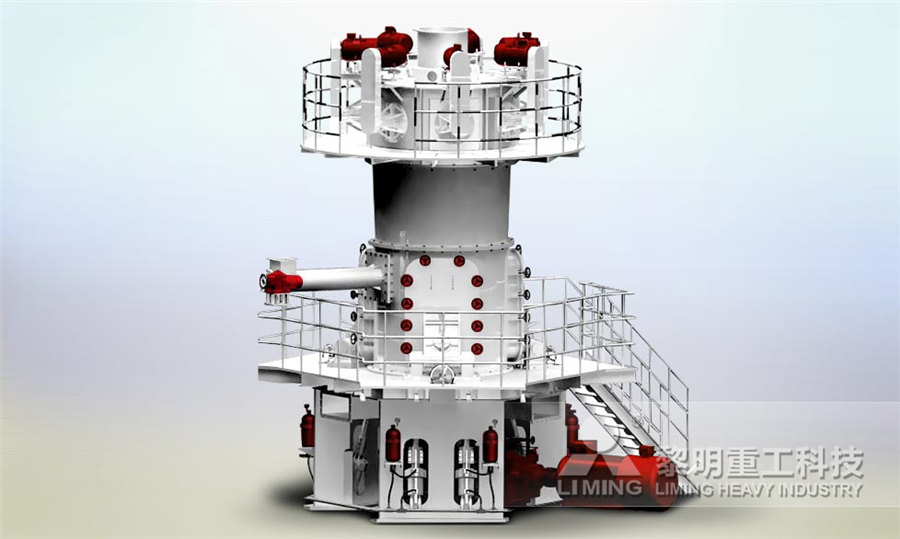
Dry Process Of Cement Manufacturing Dry Cement AGICO
The new dryprocess of cement manufacturing technology makes good use of the limestone resources discarded in the traditional mining method and applies the pre decomposition technology, suspension preheating technology, and multichannel burner to reuse the recycled and lowquality fuels2010年3月27日 The Cement Production Process Cement kilns are massive cylindrical structures, lined with refractory brick, into which a limebearing material and fuel such as coal or gas is fed Although the major impetus for development of the new technology was the potential energy and capital savings, the new technology has brought secondary benefits The Cement Production Process mcilvainecompany10 Cement packaging and shipping The cement is then housed in storage silos, from where it is hydraulically or mechanically extracted and transported to facilities where it will be packaged in sacks or supplied in bulk In either case, it can be shipped by rail car, freighter truck or shipCement Production: How Cement Is Manufactured CEMEX UKManufacturing of cement involves various raw materials and processes Each process is explained chemical reactions for manufacture of Portland Cement Cement is a greenish grey colored powder, made of calcined mixtures of clay Manufacture of Cement Materials and
.jpg)
Cement SpringerLink
2021年3月3日 Cement is produced by a hightemperature (about 1500 °C) reaction in a rotary kiln of carefully proportioned and blended ratios of lime (CaO), silica (SiO 2), alumina (Al 2 O 3), and iron oxide (Fe 2 O 3)The production of cement is a chemical process requiring an accurate blend of the previously cited four key organic oxides and the limitation of several undesirable 2015年4月14日 The diagrams illustrate the phases and apparatus to make cement and how cement is utilised in the production of concrete for construction The production of cement involves a 5 stage, linear process that begins with the mixing of raw materials and culminates in the packaging of new cement Making concrete is a simpler process that involves IELTS Task 1 Process Cement and Concrete Production2019年10月23日 Cement Plant: The Manufacturing Process worldcementassociation 1 Limestone (CaCO3) is taken from a quarry 2 4 3 The limestone is fed into a crusher and then stored until needed The clinker is mixed with additives, such as gypsum, and then ground in a cement mill, which creates cement The cement is then packed and distributed to consumersCement Plant: The Manufacturing Process 4 5 World Portland cement was first introduced in 1824 by Joseph Aspdin, a brick layer from Leeds, England [5] On setting, the color of cement resembles the color of rocks near Portland, England, hence the nameThe Composition of Portland Cement and Production Process
.jpg)
Cement Making Process Cement Production Process Cement
Clinker Calcination Process Replace the Traditional Cement Equipment The comparison data between the wet process cement production line and the new dry process cement production line shows that with the same rotary kiln size (diameter), the production capacity of the cement kiln which adopts the predecomposition production process increases more than 200%, the 2024年9月5日 The Manufacturing Process of Cement Now, let’s explore the steps involved in the cement production process in more detail: 1 Mining and Crushing The process of making cement begins with mining, where raw materials are extracted from quarries Huge machines called excavators dig the limestone out of the earthA Comprehensive Guide to the Cement Manufacturing Process2019年8月26日 Cement Manufacturing and Process Control 41 Cement Manufacturing: Basic Process and Operation To design the Refractory for the lining of different equipments in a cement plant, it high temperature and form a new substance called clinker Clinker comes out of the kiln as dark gray balls, about the size of 0–50 mm Chapter 4 Cement Manufacturing and Process Control2024年10月16日 Researchers from UCLA’s Institute for Carbon Management (ICM) have developed a method to reduce carbon emissions in cement production drastically, a process that currently contributes around 8% 98% less carbon: New tech promises nearzero emissions from cement
.jpg)
Cement: History, Types, Manufacturing Process
2023年8月15日 In the cement manufacturing process, the raw mix undergoes a drying process to reduce its moisture content to less than 1% This dried mixture, known as the raw mix, is then prepared for introduction into the rotary kiln 2024年5月22日 The cement production process 1 The Quarry: The cement production process begins with the extraction of limestone and clay from the quarry 2 Crusher and PreBlending: The material is then crushed to reduce particle sizes and blended to reduce variability in composition 3 Raw Mill and Kiln: Raw materials and additives areA practical guide to improving cement manufacturing The Cement Manufacturing Process While each cement plant may differ in layout, equipment, and appearance, the general process of manufacturing portland cement is the same: crushed limestone and sand are mixed with ground clay, shale, iron ore, fly ash and alternative raw materials As materials move through the kiln, a series of complex How Cement is Made Portland Cement Association2020年9月26日 Cement Manufacturing Process Cement Manufacturing Process Cement Manufacturing Process Cement is a material which is used to bind other materials together Binding means it has an effect of gluing the substances together due to cohesive and adhesive action and then hardens and sets in order to become permanent Cement is usually not used Cement Manufacturing Process Chemical Engineering World
.jpg)
How Is Cement Produced in Cement Plants Cement Making Process
The cyclone preheating system Phase IV: Calcination The calcination is the core phase of the cement making dry process The calcination of the preheated raw meal takes place in the rotary kiln of the cement plant The rotary kiln is a huge rotating furnace in which the raw meal is heated up to 1450 ⁰C and turned to clinker5 天之前 The manufacture of Portland cement is a complex process and done in the following steps: grinding the raw materials, mixing them in certain proportions depending upon their purity and composition, and burning them to sintering in a kiln at a temperature of about 1350 to 1500 ⁰C During this process, these materials partially fuse to form nodular shaped clinker by Manufacturing of Portland Cement – Process and Materials2024年9月10日 Cement Manufacturing Process Cement manufacturing is an intricate process involving the extraction and grinding of raw materials, followed by blending and heating in a kiln to produce clinker This clinker is then ground with gypsum to create cement, a Cement Manufacturing Process: Know Extraction, Processing 2018年11月30日 Cement production process: Thermal energy demand and CO 2 emissions 30% fuel emissions thermal energy prod process emissions from calcination • ETHZ has simulated and adapted the CAP system to different cementplant flue gases; • New ratebased model was developed and used to validate fullscale CAP simulations for cement plants Process characteristics of clinker and cement production
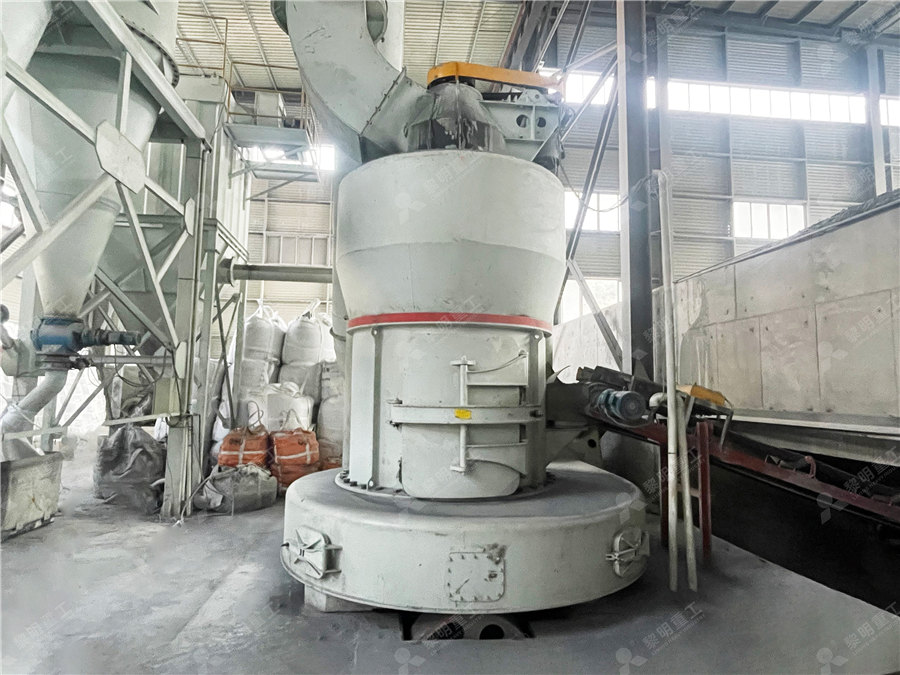
Cement Production Process Cement Manufacturing Process AGICO CEMENT
2020年8月25日 A full cement production process includes the cement crushing process, raw mill process, clinker process, and cement grinding process, cement packing process, and related process low production efficiency, and it tends to be replaced by a new dry process cement production cement equipment Raw Material Production Crusher; Vertical Raw