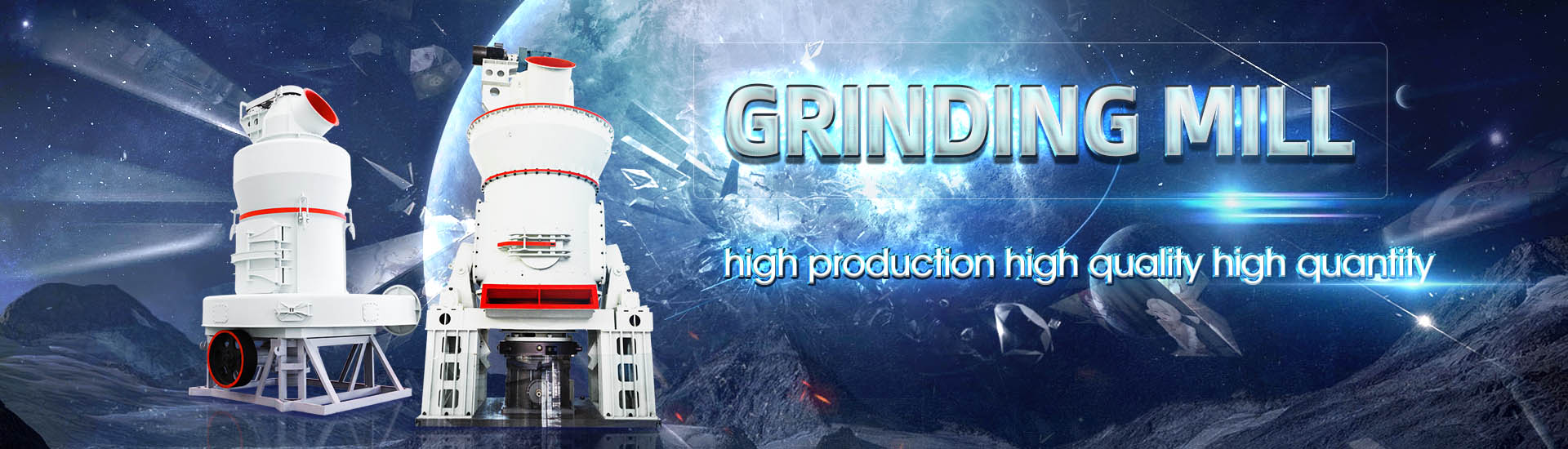
Electrolytic aluminum waste slag grinding machine calcium carbonate reclaimer feeder
.jpg)
The recycling of carbonrich solid wastes from aluminum electrolytic
2024年5月23日 Here, we review carbonrich solid wastes with focus on sources and hazards, detoxification, separation, recovery, recycling and disposal Treatment techniques include 2024年2月1日 The electrolytic aluminum industry generates a large amount lithium (Li)containing electrolytic aluminum slag (EAS) annually, and this can result in severe Efficient lithium recovery from electrolytic aluminum slag via 2024年7月24日 First, the spent aluminum electrolyte slag phase was reconstructed through a calcium sulfate roasting process, which solidified fluorine into CaF 2 and transformed lithium into Li 2 SO 4 > 97% lithium can be Cleaner Process for the Selective Extraction of 2023年5月20日 Spent carbon anode (SCA) discharged from the aluminum electrolysis industry is an unavoidable solid waste with an estimated production of 700 kilotons in 2021, which has Regeneration of raw materials for aluminum electrolysis
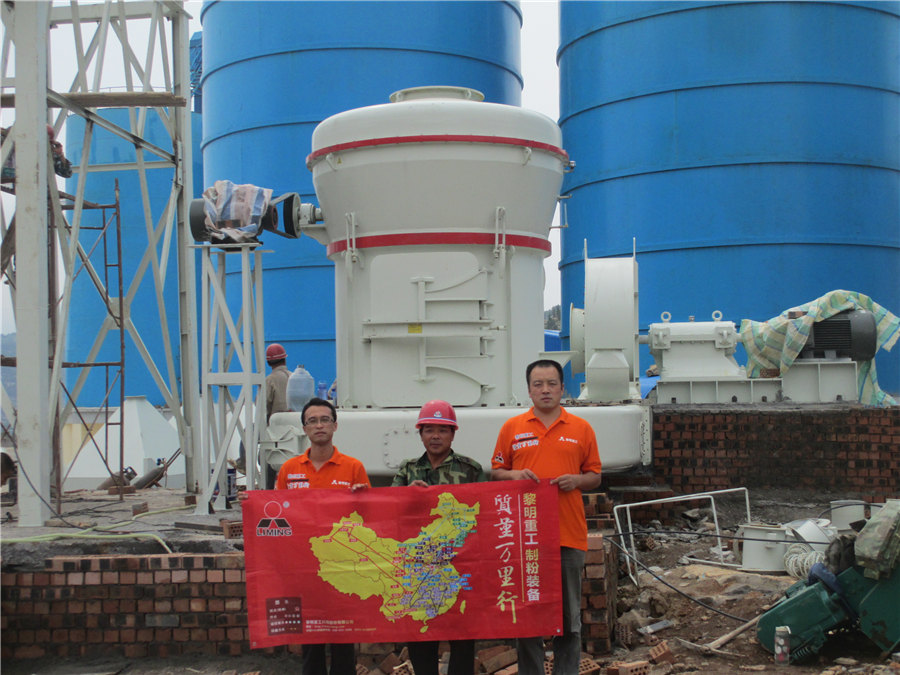
Graphitization transformation of aluminum electrolytic spent
2024年9月15日 Aluminum electrolysis spent cathode carbon (SCC), as typical solid hazardous waste, poses significant environmental risks Harmless treatment of SCC and recycling of its 2024年1月1日 A novel approach for lithium recovery from waste lithiumcontaining aluminum electrolyte by a roastingleaching process Anode carbon residue is produced in the production Efficient lithium recovery from electrolytic aluminum slag via 2024年2月2日 This study proposes the technology of using waste carbide slag to treat carbon dioxide in the tail gas of electrolytic aluminum and innovatively designs a Venturi Research on Using Carbide Slag to Mineralize the Carbon 2023年9月1日 This study employed hydrometallurgical processes to selectively leach lithium from Licontaining aluminum electrolyte slag, using sodium carbonate solution as the leaching agent A notable leaching efficiency of Clean Process for Selective Recovery of Lithium
.jpg)
The recycling of carbonrich solid wastes from aluminum electrolytic
2024年5月23日 Evaluation of fluoride emissions and pollution from an electrolytic aluminum plant located in Yunnan province The spent carbon cathode (SCC) is a hazardous solid waste 2023年4月25日 This article analyzes and summarizes the composition and hazards of the overhaul slag and the current development status of domestic and international electrolytic Research Progress of Electrolytic Aluminum Overhaul Slag 2022年10月10日 One of the main electrolytic aluminum production costs is the consumption of carbon anodes, and carbon anode slag is a common hazardous waste in the aluminum industryRecovery of carbon and cryolite from spent 2022年2月19日 This paper investigated the recovery of rare earth elements (REEs) and aluminum (Al) from the waste slag discharged by FCC catalyst factory (FCC waste slag) via acid leaching and selective Recovery of RareEarth Elements from Molten Salt Electrolytic Slag
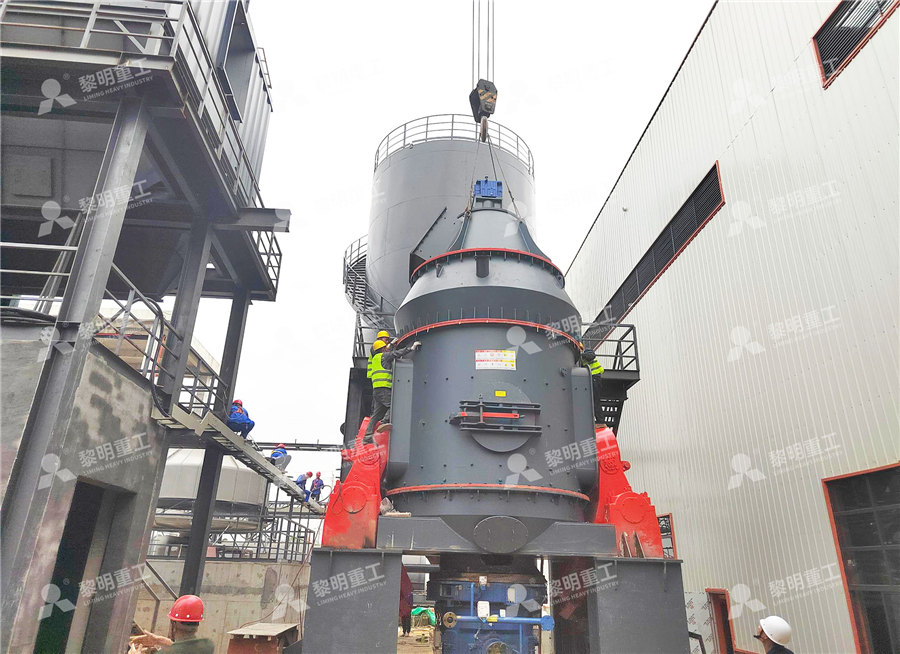
A novel approach for lithium recovery from waste lithium
2021年10月1日 On the other hand, lithium, the lightest metal element in the world, is an important strategic resource because of its contribution to the national economy (Vieceli et al, 2021)The demand for new energy vehicles and various hightech products is gradually increasing with the rapid development of economy (Yang et al, 2019, Li et al, 2021, Yelatontsev and waste in electrolytic aluminum industry about 26kg per tons of aluminum in our country [1], in which the waste cathode carbon block for about 37% [2] These wastes containing soluble fluoride and Study on Harmless and Resources Recovery Treatment 2024年5月26日 Mineral carbonation is one of the known methods for carbon capture, utilization, and storage (CCUS) Slag from the steel industry is studied as a common source of CaCO3 via mineral carbonation owing to its high Ca content Despite numerous preliminary studies, the optimal factors governing the mineral carbonation of steelmaking slag, such as extraction and Experimental study on indirect mineral carbonation using 2023年10月1日 Cryolitealumina (Na 3 AlF 6Al 2 O 3) molten salt electrolysis is the only modern method for the industrial production of metallic aluminum (Ishak et al, 2017)Under the influence of direct current, Al 2 O 3 dissolved in the molten salt is reduced to monolithic aluminum at the cathode (Haraldsson and Johansson, 2020)As the blood of the electrolytic cell, the electrolyte Efficient extraction and recovery of lithium from waste aluminum
.jpg)
Efficient lithium recovery from electrolytic aluminum slag via
2024年2月1日 The electrolytic aluminum industry generates a large amount lithium (Li)containing electrolytic aluminum slag (EAS) annually, and this can result in severe environmental pollution and wasting of Li resources This paper proposes a method for recovering Li from the slag using AlCl 3 as the leaching agent The effects of the leaching temperature, AlCl 3 2022年12月12日 Calcium carbide slag is a waste slag produced after the hydrolysis of calcium carbide to obtain acetylene gas, with very fine particles, offwhite color due to the presence of trace carbon and sulfur impurities, slightly odorous, with Ca(OH) 2 as the main component, and a slag liquid pH value of 12 or more, thus often causing serious pollution to the environment [18]Comprehensive performance study of aluminum ash and calcium 2023年8月10日 Electrolytic manganese residue (EMR) is a general industrial solid waste containing manganese (Mn) and heavy metals that is produced in the process of electrolytic metal manganeseKinetic and thermodynamic analysis on preparation of belitecalcium 2023年12月1日 Nevertheless, strong acids normally result in excessive leaching of mineral residues and unexpected dissolution of impurities, such as aluminum and iron (Chen et al, 2023; Chiang et al, 2014; Kuwahara et al, 2010, 2013; Seo et al, 2018)Sugano et al claimed that in order to produce highquality aluminum silicate zeolite, the calcium content in the raw Producing amorphous calcium carbonate using waste Ca
.jpg)
(PDF) Twoway Valorization of Blast Furnace
2017年2月21日 Twoway Valorization of Blast Furnace Slag: Synthesis of Precipitated Calcium Carbonate and Zeolitic Heavy Metal Adsorbent February 2017 Journal of Visualized Experiments 120(120):e年3月2日 for electrolytic aluminum waste is proposed This mode is to pulverize the electrolytic aluminum waste, and then mix the crushed electrolytic aluminum waste with the raw coal of the circulating fluidized bed boiler [6], then send it to the circulating fluidized bed boiler for combustion In this study, a mixed combustion experiment ofResearch on the Coprocessing of Mixed Electrolytic DOI: 101016/jjclepro2024 Corpus ID: ; Efficient lithium recovery from electrolytic aluminum slag via an environmentally friendly process: Leaching behavior and mechanismEfficient lithium recovery from electrolytic aluminum slag via 2012年12月31日 The main mineral components of waste cathode carbon include sodium fluoride, cryolite, calcium fluoride, silicate minerals and so on, therein the fluorine content is about 986%, and the content Study on Harmless and Resources Recovery Treatment Technology of Waste
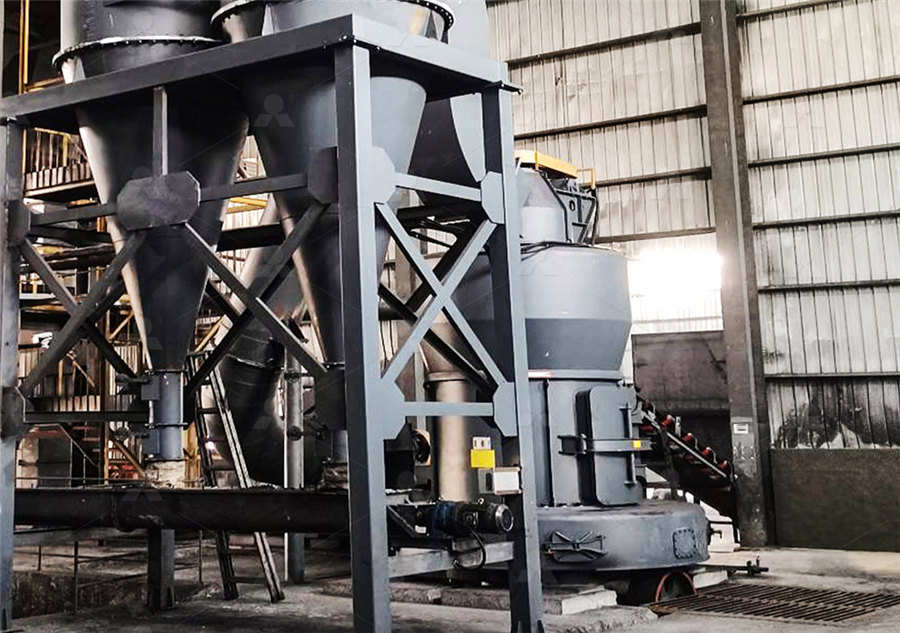
Utilization of aluminum sludge and aluminum slag (dross)
2009年12月1日 Four calcium aluminate cement mixes were manufactured from aluminum sludge as a source of calcium oxide and Al2O3 and aluminum slag (dross) as a source of aluminum oxide with some additions of 2020年12月1日 The rapid development of the electrolytic aluminum industry in China and the increasing demand for aluminum products have led to the development of many lowgrade bauxite mines with an average Li 2 O content of at least 058% (Wang et al, 2013) Due to the use of this lowgrade bauxite in the electrolytic aluminum process, the content of lithium in the Novel process for the extraction of lithium carbonate from 2022年9月1日 Waste carbide slag (WCS) is a typical industrial solid waste with high calcium content, which shows highly potential in preparation of CaCO3 by CO2 mineralization technologyCalcium recovery from waste carbide slag via ammonium 2022年4月1日 Because electrolytic manganese slag contains a was prepared by calcination and desulfurization of industrial waste electrolytic manganese residue, and the original DMR was ground to prepare Synergistic use of electrolytic manganese residue and barium slag
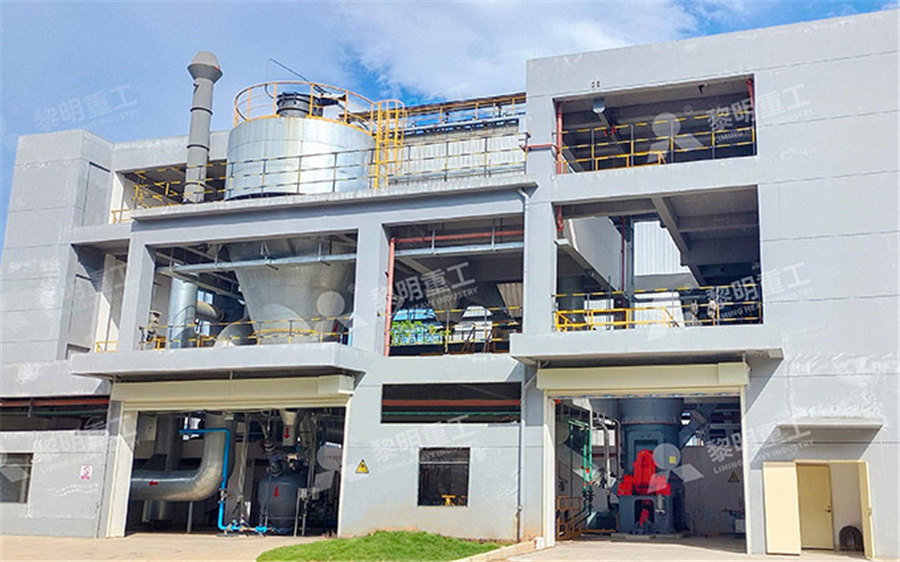
Kinetic and thermodynamic analysis on preparation of belitecalcium
2023年8月10日 Electrolytic manganese residue (EMR) is a solid filter residue obtained from manganese carbonate ore during the production of metal manganese A potential avenue towards largescale utilisation of EMR is its use in cement preparation However, the preparation of cement materials using EMR requires hightemperature calcination In this study, the thermal 2023年8月1日 When the mass ratio of sodium carbonate to fluorinated rare earth moltensalt electrolytic slag was increased from 02 to 06, the recovery of rare earth improved from 801% to 979% and there was almost no change in the leaching efficiency of rare earth when the mass ratio of sodium carbonate to the fluorinated rare earth moltensalt Rare earth recovery from fluoride moltensalt electrolytic slag 2022年8月12日 salt electrolytic slag by sulfation roasting with ammonium sulfate [24] Liu et al used the mixed acid to leach the rareearth oxides from molten salt electrolytic slag The ltrate was treated by solvent extraction and precipitation to obtain rareearth oxides The rareearth uoride remained in the leaching residue [25]Recovery of RareEarth Elements from Molten Salt 2021年11月1日 This study proposes the technology of using waste carbide slag to treat carbon dioxide in the tail gas of electrolytic aluminum and innovatively designs a Venturi gas–liquid–solid threestage Calcium carbide residue as auxiliary activator for onepart
.jpg)
Preparation of MnO2 and calcium silicate hydrate from electrolytic
2015年7月14日 Electrolytic manganese residue (EMR), a high volume byproduct resulting from the electrolytic manganese industry, was used as a cheap and abundant chemical source for preparing MnO2 and EMRmade calcium silicate hydrate (EMRCSH) The MnO2 is successfully synthesized from the metal cations extracted from EMR, which can effectively recycle the 2022年10月9日 1 Department of Mining Engineering, Shanxi Institute of Technology, Yangquan, China; 2 Department of Mining Engineering, Balochistan University of Information Technology, Engineering and Management Sciences (BUITEMS), Quetta, Pakistan; One of the main electrolytic aluminum production costs is the consumption of carbon anodes, and carbon Recovery of carbon and cryolite from spent carbon anode slag 2019年7月8日 The electrolytic aluminum waste, which would inevitably be produced from the electrolytic process in the aluminum industry, is harmful to environment and human bodyThermodynamic analysis of waste heat recovery of aluminum 2024年2月1日 The electrolytic aluminum waste, which would inevitably be produced from the electrolytic process in the aluminum industry, is harmful to environment and human bodyEfficient lithium recovery from electrolytic aluminum slag via
.jpg)
Stepwise extraction of lithium and potassium and recovery
2024年6月29日 Aluminum electrolyte is a necessity for aluminum reduction cells; however, its stock is rising every year due to several factors, resulting in the accumulation of solid waste Currently, it has become a favorable material for the resources of lithium, potassium, and fluoride In this study, the calcification roasting–twostage leaching process was introduced to extract 2022年7月1日 Rare earth element recovery in molten salt electrolysis is approximately between 91 and 93%, whereof 8% is lost in waste molten salt slag Presently, minimal research has been conducted on the Rare earth recovery from fluoride moltensalt electrolytic slag A Novel Indirect Technique for Steelmaking Waste Slag Carbonation for Precipitated Calcium Carbonate Production Jean Mulopo, John Zvimba, Vivian Radebe, Lucky Bologo, Mlawule Mashego, LisaA Novel Indirect Technique for Steelmaking Waste Slag WANG Gongxun;LI Zhi;ZHU Mingqiao Preparation of Recycled Ceramic Tiles by Using Electrolytic Manganese SlagWaste Ceramic Grinding Fine Powder[J] BULLETIN OF THE CHINESE CERAMIC SOCIETY, 2013, 32(8): 14961501Preparation of Recycled Ceramic Tiles by Using Electrolytic
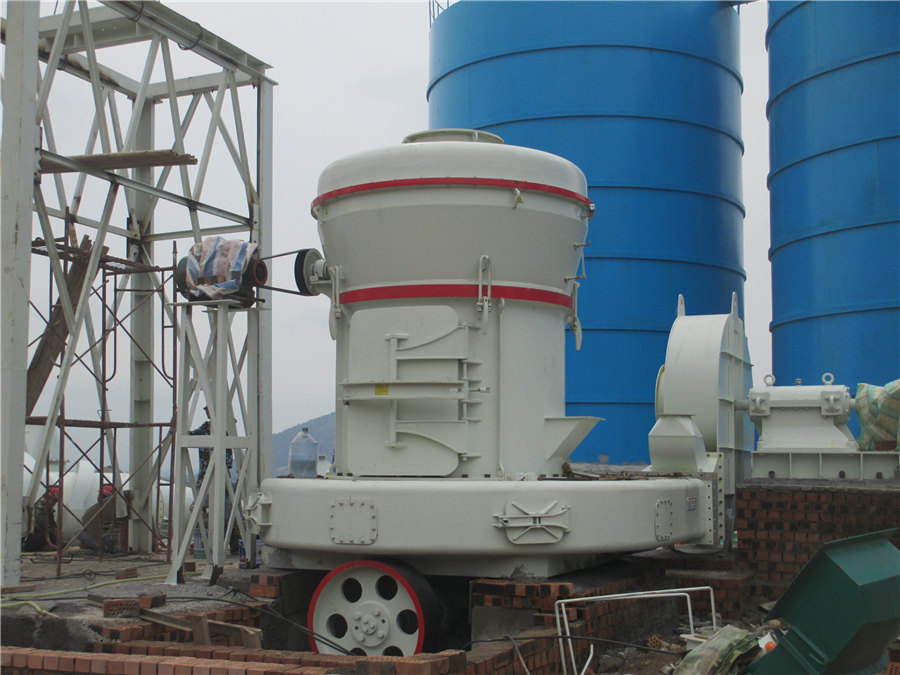
Recovery of carbon and cryolite from spent
2022年10月10日 One of the main electrolytic aluminum production costs is the consumption of carbon anodes, and carbon anode slag is a common hazardous waste in the aluminum industry2022年2月19日 This paper investigated the recovery of rare earth elements (REEs) and aluminum (Al) from the waste slag discharged by FCC catalyst factory (FCC waste slag) via acid leaching and selective Recovery of RareEarth Elements from Molten Salt Electrolytic Slag 2021年10月1日 On the other hand, lithium, the lightest metal element in the world, is an important strategic resource because of its contribution to the national economy (Vieceli et al, 2021)The demand for new energy vehicles and various hightech products is gradually increasing with the rapid development of economy (Yang et al, 2019, Li et al, 2021, Yelatontsev and A novel approach for lithium recovery from waste lithium waste in electrolytic aluminum industry about 26kg per tons of aluminum in our country [1], in which the waste cathode carbon block for about 37% [2] These wastes containing soluble fluoride and Study on Harmless and Resources Recovery Treatment
.jpg)
Experimental study on indirect mineral carbonation using
2024年5月26日 Mineral carbonation is one of the known methods for carbon capture, utilization, and storage (CCUS) Slag from the steel industry is studied as a common source of CaCO3 via mineral carbonation owing to its high Ca content Despite numerous preliminary studies, the optimal factors governing the mineral carbonation of steelmaking slag, such as extraction and 2023年10月1日 Cryolitealumina (Na 3 AlF 6Al 2 O 3) molten salt electrolysis is the only modern method for the industrial production of metallic aluminum (Ishak et al, 2017)Under the influence of direct current, Al 2 O 3 dissolved in the molten salt is reduced to monolithic aluminum at the cathode (Haraldsson and Johansson, 2020)As the blood of the electrolytic cell, the electrolyte Efficient extraction and recovery of lithium from waste aluminum 2024年2月1日 The electrolytic aluminum industry generates a large amount lithium (Li)containing electrolytic aluminum slag (EAS) annually, and this can result in severe environmental pollution and wasting of Li resources This paper proposes a method for recovering Li from the slag using AlCl 3 as the leaching agent The effects of the leaching temperature, AlCl 3 Efficient lithium recovery from electrolytic aluminum slag via 2022年12月12日 Calcium carbide slag is a waste slag produced after the hydrolysis of calcium carbide to obtain acetylene gas, with very fine particles, offwhite color due to the presence of trace carbon and sulfur impurities, slightly odorous, with Ca(OH) 2 as the main component, and a slag liquid pH value of 12 or more, thus often causing serious pollution to the environment [18]Comprehensive performance study of aluminum ash and calcium
.jpg)
Kinetic and thermodynamic analysis on preparation of belitecalcium
2023年8月10日 Electrolytic manganese residue (EMR) is a general industrial solid waste containing manganese (Mn) and heavy metals that is produced in the process of electrolytic metal manganese2023年12月1日 Nevertheless, strong acids normally result in excessive leaching of mineral residues and unexpected dissolution of impurities, such as aluminum and iron (Chen et al, 2023; Chiang et al, 2014; Kuwahara et al, 2010, 2013; Seo et al, 2018)Sugano et al claimed that in order to produce highquality aluminum silicate zeolite, the calcium content in the raw Producing amorphous calcium carbonate using waste Ca