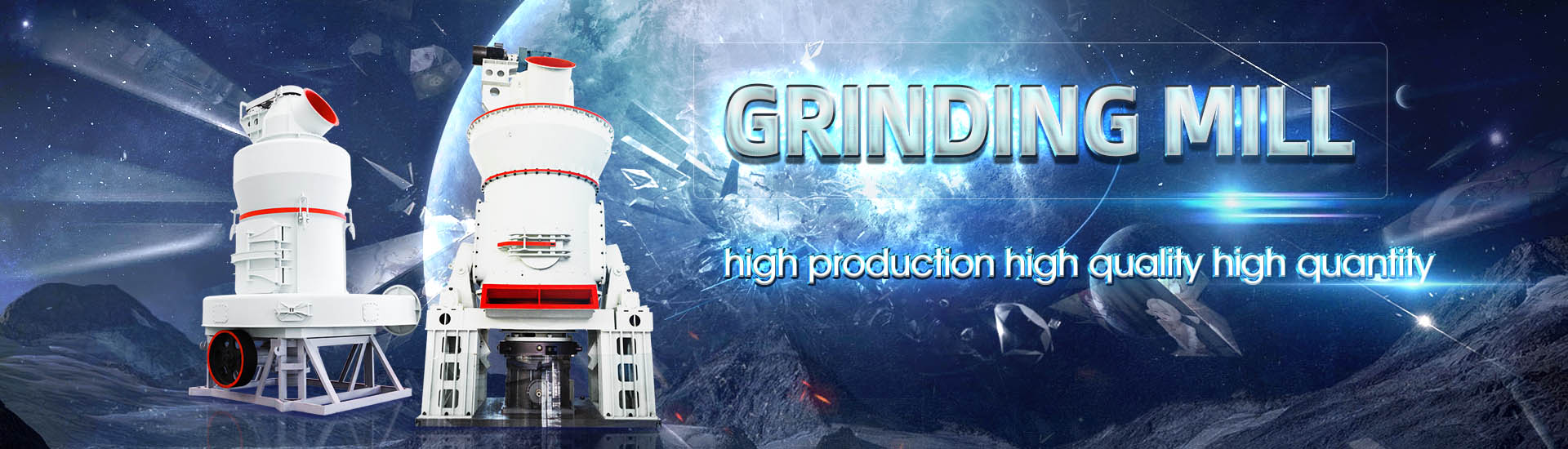
DFHZ series high and medium concentration energysaving mill
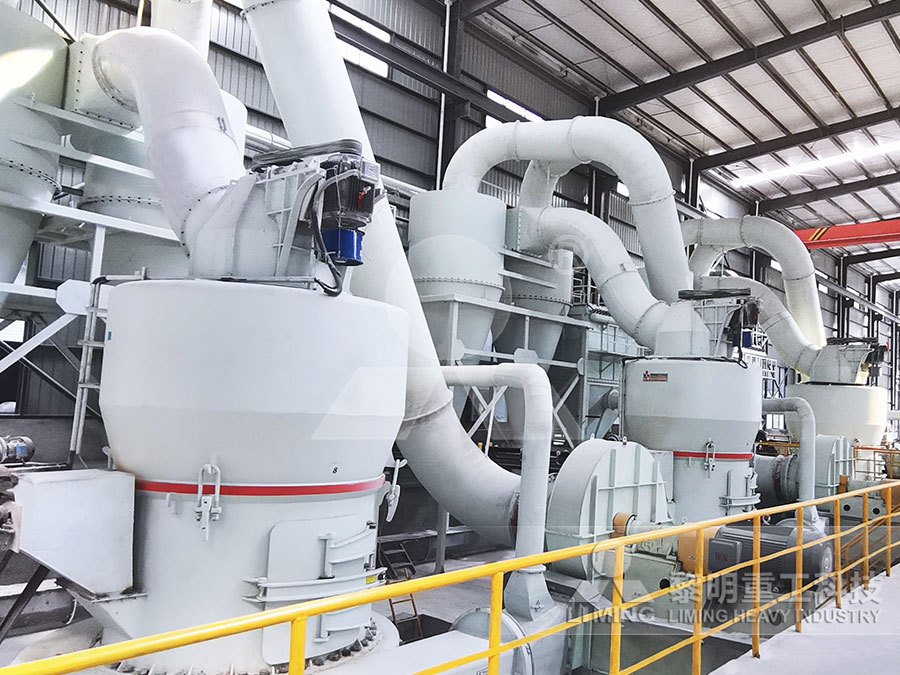
Energy conservation and consumption reduction in grinding
2023年11月1日 The development and application of new fine and ultrafine grinding equipment are particularly important As a new type of grinding equipment, the stirring mill has significant 2009年6月1日 Comparison of a laboratory vertical shaft stirred mill with a ball mill, both operated in a virtually closed circuit with a classifier, indicated that on average 30% energy saving can Comparison of energy efficiency between ball mills and stirred mills 2023年11月21日 As a new type of grinding equipment, the stirring mill has significant advantages such as high energy efficiency, medium saving, simple installation, and easy Energy conservation and consumption reduction in 2023年9月1日 This paper demonstrates the feasibility of using a ceramic medium stirring mill to reduce the energy consumption of grinding operations through an industrial verification Energy conservation and consumption reduction in grinding
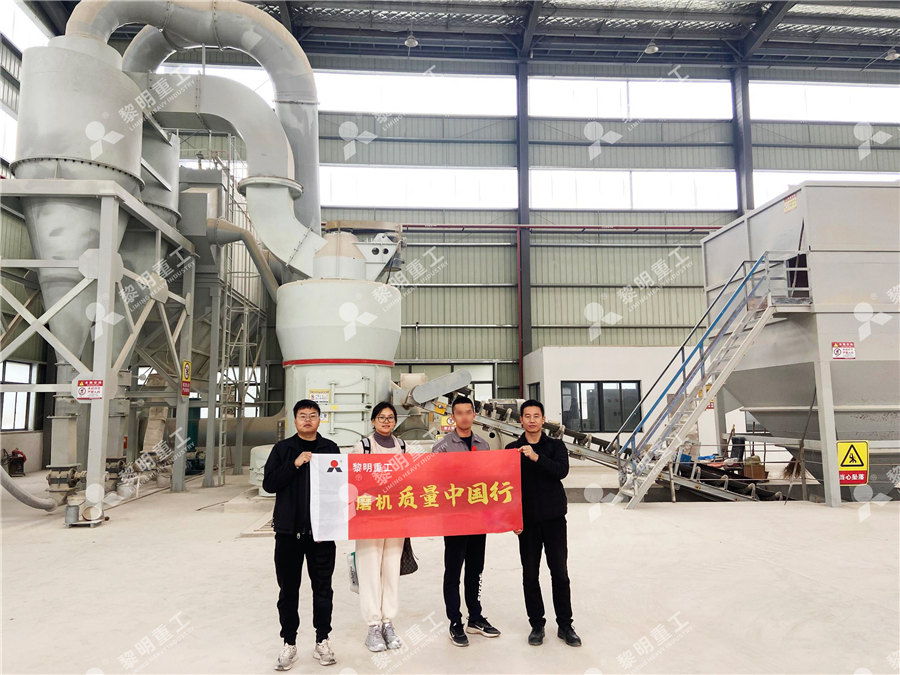
Highefficiency and energyconservation grinding
2021年11月1日 In response to the high consumptions of energy and media during grinding operations, An ingenious technique incorporating ceramic media and a new type of stirring mill 2023年7月10日 The present literature review explores the energyefficient ultrafine grinding of particles using stirred mills The review provides an overview of the different techniques for size reduction and the impact of energy EnergyEfficient Advanced Ultrafine Grinding of 2021年11月1日 Semantic Scholar extracted view of "Highefficiency and energyconservation grinding technology using a special ceramicmedium stirred mill: A pilotscale study" by Highefficiency and energyconservation grinding 2020年6月11日 This paper aims to optimize the machining inputs to enhance energy efficiency (EF) as well as the power factor (PO) and decrease the surface roughness (Ra) for the milling Optimization of Milling Parameters for Energy Savings and
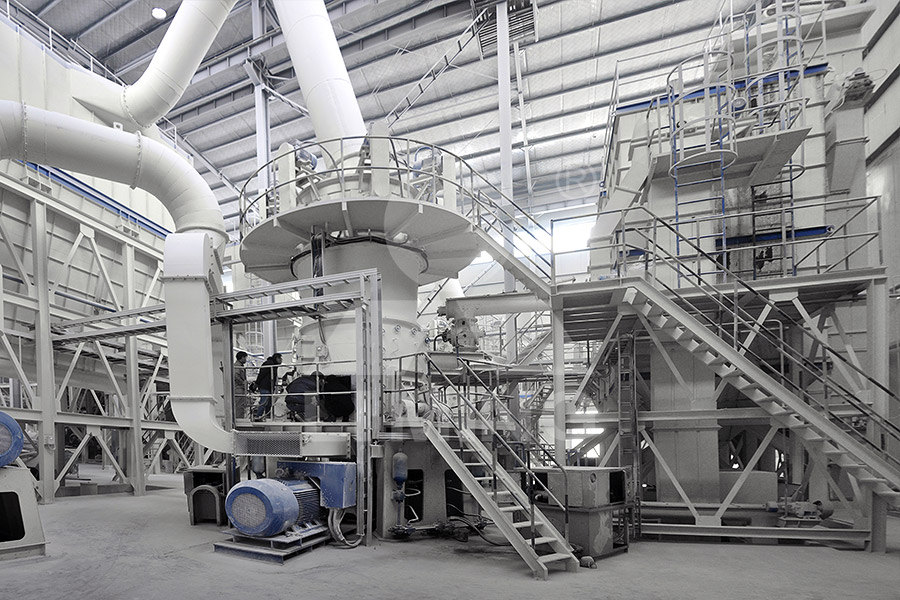
Highefficiency and energyconservation grinding
2021年11月12日 A pilotscale grinding technology of ceramic medium stirred mill was proposed in this study Based on the specific productivity and grinding efficiency, the appropriate 2021年9月12日 Bühler unveils Granulex® 5 series, the next generation hammer mill platform 17 November 2022 House of Raeford opens Louisiana feed mill Increase in fat concentration in feed material from 2 to 55% reduces energy consumption during pelleting by 30% In general, the specific energy required for pelleting (ie, energy consumed by the Energy saving in compound feed mills Feed Additive Magazine2019年8月1日 DOI: 101002/CJCE23212 Corpus ID: ; Ultrasound assisted wet stirred media mill of high concentration LiFePO4 and catalysts @article{Li2019UltrasoundAW, title={Ultrasound assisted wet stirred media mill of high concentration LiFePO4 and catalysts}, author={He Li and Mohammad Rostamizadeh and Kahina Mameri and Daria Camilla Boffito Ultrasound assisted wet stirred media mill of high concentration 2024年11月1日 Ceramic grinding, which in this paper is defined as a method of using ceramic materials as grinding media, is favored by many processing plants as an emerging highefficiency and energysaving Understanding the EnergySaving mechanism of ceramic
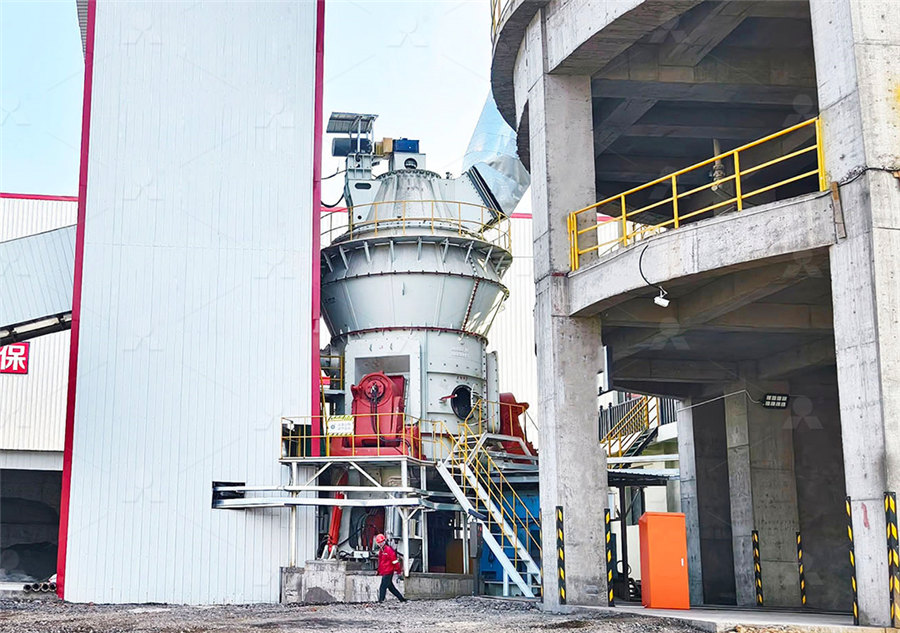
(PDF) Grinding in Ball Mills: Modeling and Process Control
2012年6月1日 The paper presents an overview of the current methodology and practice in modeling and control of the grinding process in industrial ball mills Basic kinetic and energy models of the grinding PDF On Jun 1, 2019, K Balachander and others published Energy Saving Measures in Textile Mill Find, read and cite all the research you need on ResearchGate(PDF) Energy Saving Measures in Textile Mill ResearchGate2023年9月1日 The stirred media mill is a piece of process equipment used in comminution, which uses grinding media, beads of ceramic or similar material, to mediate energy transfer between a rotating impeller Energy conservation and consumption reduction in grinding 2021年1月18日 water savings was approx 20%, which allowed shutting off one of the three highpressure pumps Electrical energy saving amounts to 9,300,000* kWh/ year At the current energy costs this is equivalent to 000 TL 2,100,/ 641,700 EUR** Additional advantages are seen such as reduced material cooling and the lower wear of theEnergy saving and process optimization in a
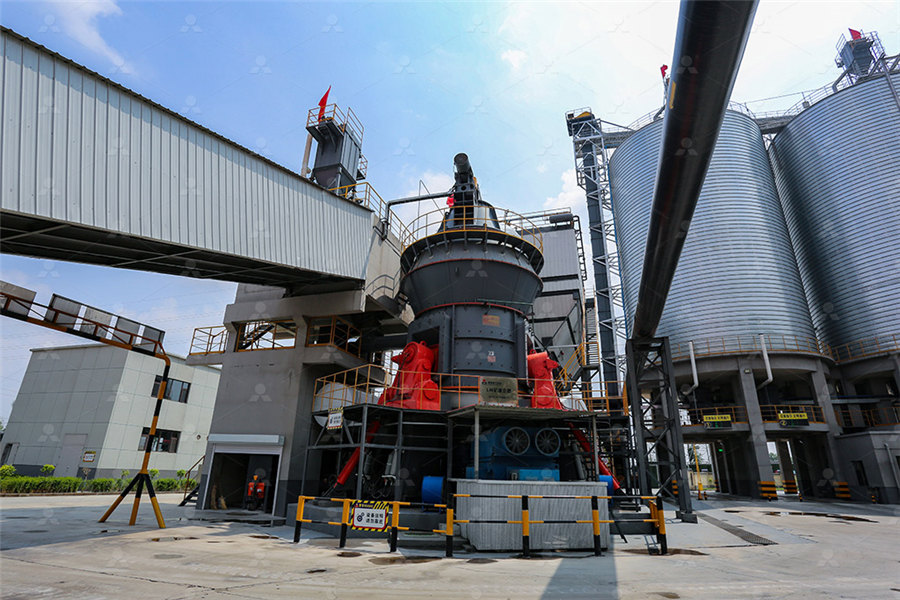
Understanding the EnergySaving mechanism of ceramic
DOI: 101016/jmineng2024 Corpus ID: ; Understanding the EnergySaving mechanism of ceramic balls in tumbling mills @article{Fang2024UnderstandingTE, title={Understanding the EnergySaving mechanism of ceramic balls in tumbling mills}, author={Xin Fang and Caibin Wu and Ningning Liao and Chengfang Yuan and Jiuxiang Zhong 2023年10月8日 medium were obtained using BAP hormone at a concentration of 15 mgL1 The The highest mean of rooting percentage, fresh and dry weight of roots was obtained inEffects of Culture Medium and Concentration of 2023年11月1日 This paper demonstrates the feasibility of using a ceramic medium stirring mill to reduce the energy consumption of grinding operations through an industrial verification experiment Compared with the original twostage ball milling process, the cost of grinding power consumption is significantly reduced by about 5016%, which provides a reference for the Energy conservation and consumption reduction in grinding 2012年12月1日 The inmill load volume and slurry solids concentration have significant influence on the ball mill product size and energy expenditure Hence, better energy efficiency and quality grind can only Optimization of inmill ball loading and slurry solids concentration
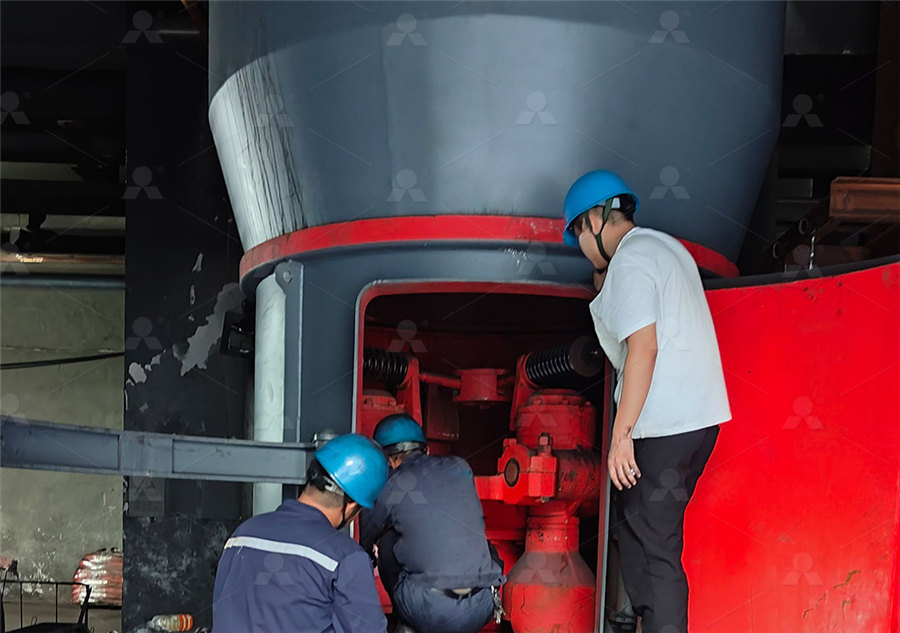
Analysis of energy saving and emission
2021年5月13日 A nalysis of energy saving and emissio n reduction of se condary ber mill base d on data min ing e results of Section 52 show that a er optimiza tion of parameters, a total of 65828 to ns of 2018年2月20日 A regrind ball mill with a mix of small grinding media can be as energy effi cient as an Isa Mill charged with 25 and 35 mm beads In vertical stirred mills, energy savings vary from 30 per cent to 60 per cent To carry out the same fi nal grind, a vertical stirred mill with Millpebs will consume at least 60 per cent less energy than a ball ENERGY SAVINGS AND TECHNOLOGY COMPARISON 2023年11月1日 Grinding operation is the last preparation stage before beneficiation In this stage, the material undergoes the combined action of impact and grinding, so that the ore particle size is diminished and the qualified materials is provided for succeeding beneficiation operations [1, 2]Generally, the quality of the grinding product is also an important factor to determine the Energy conservation and consumption reduction in grinding 2023年7月10日 The present literature review explores the energyefficient ultrafine grinding of particles using stirred mills The review provides an overview of the different techniques for size reduction and (PDF) EnergyEfficient Advanced Ultrafine Grinding of
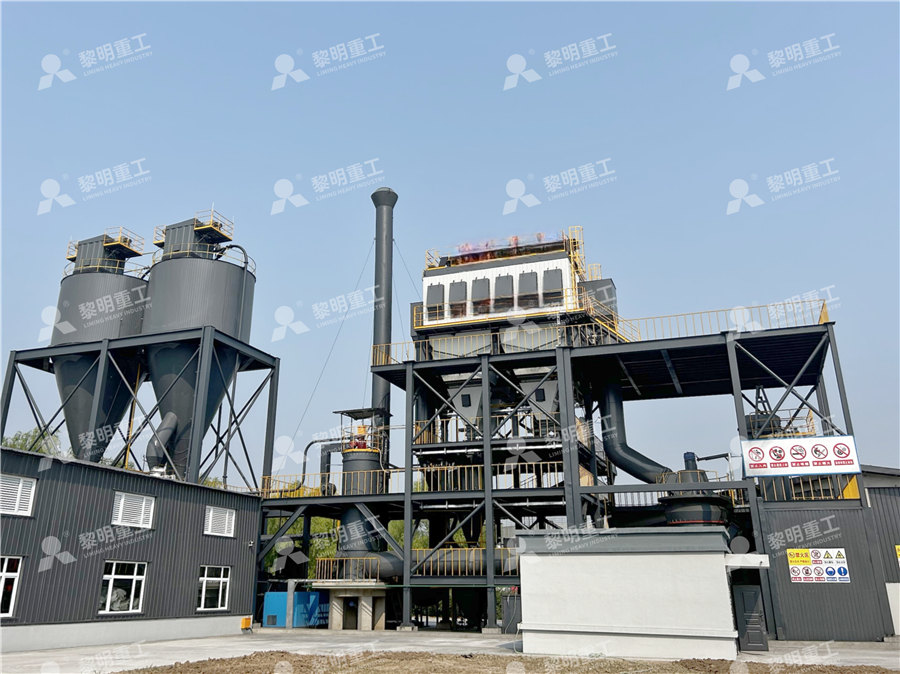
Stirred media mills in the mining industry: Material
2020年5月1日 Stirred media mills are used by the mining industry for ultrafine grinding to enhance liberation, and to decrease particle sizes of industrial minerals to tailor functional properties2021年1月11日 The idea of implementing energy conservation and emission reduction in China IS industry should be as follows Firstly, energy saving goal should be determined, namely determining how much energy saving potential exists in the future; and then the key points should be found out to achieve energy saving goal, namely the key factors that affect total energy Energy conservation path of China iron and steel industry 2018年2月20日 A regrind ball mill with a mix of small grinding media can be as energy effi cient as an Isa Mill charged with 25 and 35 mm beads In vertical stirred mills, energy savings vary from 30 per cent to 60 per cent To carry out the same fi nal grind, a vertical stirred mill with Millpebs will consume at least 60 per cent less energy than a ball ENERGY SAVINGS AND TECHNOLOGY COMPARISON 2007年12月31日 The fact that stirred media mills result in significant energy savings thanks to the grinding media's small size and the ability to mix at a higher speed is now basically known [31] [32][33][34 Chapter 6 Wet Grinding in Stirred Media Mills Request PDF
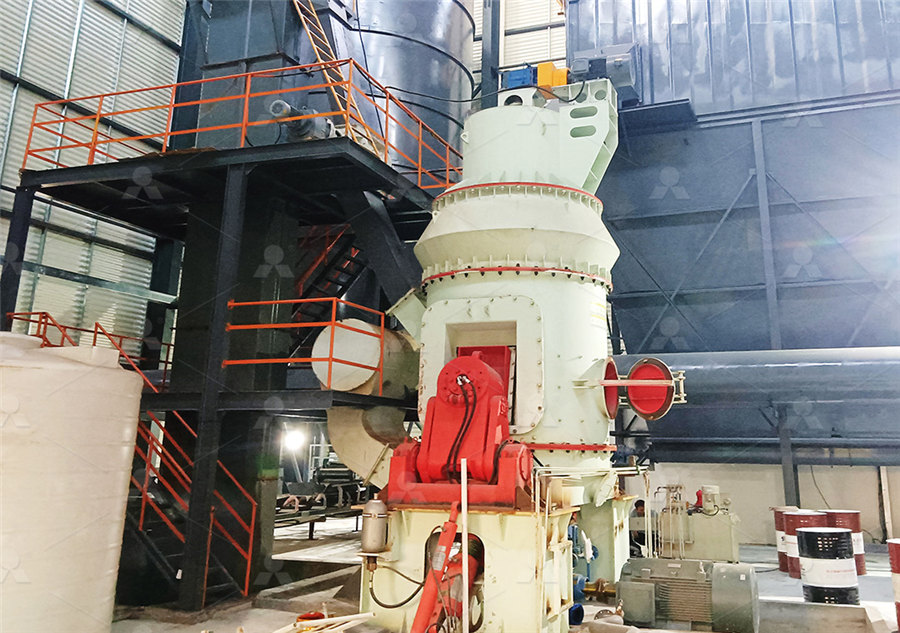
Novel high energy media mill produced macadamia butter:
2023年3月15日 Highenergy media mill (HEMM) is a simple, costeffective and environmentally friendly ultrafine grinding technology Based on nutritional and consumer preferences, MB grinded for 65 min was selected and added with different concentrations (0, 05, 1, 3, 5, 7 g/100 g (w/w)) of rice bran wax (stabilizer) to investigate the spreadability of Reduced Friction: Energysaving ball mills employ spherical or cylindrical grinding media that roll rather than slide within the mill, reducing frictional losses and energy consumption 2The Role of EnergySaving Ball Mills in Mineral Processing MediumIn discussions on high energy ball milling, the more generic term "ball mills" is often used in place of the terms "stirred ball mills" or "Attritors," but the differences between the types of mills are quite distinct And, depending on your High Energy Ball Milling Stirred Ball Mill2009年6月1日 The fact that stirred media mills result in significant energy savings thanks to the grinding media's small size and the ability to mix at a higher speed is now basically known [31][32] [33] [34 Comparison of energy efficiency between ball mills and stirred mills
.jpg)
New materials for methane capture from dilute and mediumconcentration
2013年4月16日 Methane (CH4) is an important greenhouse gas, second only to CO2, and is emitted into the atmosphere at different concentrations from a variety of sources However, unlike CO2, which has a 2018年2月19日 The paper describes the conversion to a new generation of descaling nozzles in a conventional hot strip mill for steel There are descaling stations behind the reheating furnace, on the roughing mill stands, and in front of the finishing mill Before the converting, three high pressure pumps had been in operation to supply the descaling stations The new descaling Energy Saving and Process Optimization in a Conventional Hot Strip Mill 2020年12月21日 First, new designs of energysaving mills have been introduced in the market For example, vertical (tower) V ertimill (Metso) and horizontal Isamill (Glencore T echnology), which use, respectively ,Increasing Energy Efficiency and Productivity of the 2022年1月30日 However, when a low percentage of grinding media is used, it reduces around 25% of the energy used and, in turn, reduces the amount of overgrinding (40% reduction in the F300 control parameter (PDF) Rod Mill Product Control and Its Relation to Energy
.jpg)
Innovative Approaches for Energy Conservation in Modern Spinning Mills
2021年9月7日 The level of reduction in Specific Energy Consumption depends on the use of technology by the mills and amount of investment It is also anticipated that implementation of energy saving techniques on 12 spinning mills can saves the energy equal to run a small capacity spinning mills This can be a turning point to control the energy crisis of 2023年10月1日 A novel high energy media mill (HEMM) was used to prepare macadamia butter (MB) The effect of grinding time on the properties of MB was investigated the macromolecule concentration, as well High energy media mill modified pea dietary fiber: 2021年9月12日 Bühler unveils Granulex® 5 series, the next generation hammer mill platform 17 November 2022 House of Raeford opens Louisiana feed mill Increase in fat concentration in feed material from 2 to 55% reduces energy consumption during pelleting by 30% In general, the specific energy required for pelleting (ie, energy consumed by the Energy saving in compound feed mills Feed Additive Magazine2019年8月1日 DOI: 101002/CJCE23212 Corpus ID: ; Ultrasound assisted wet stirred media mill of high concentration LiFePO4 and catalysts @article{Li2019UltrasoundAW, title={Ultrasound assisted wet stirred media mill of high concentration LiFePO4 and catalysts}, author={He Li and Mohammad Rostamizadeh and Kahina Mameri and Daria Camilla Boffito Ultrasound assisted wet stirred media mill of high concentration
.jpg)
Understanding the EnergySaving mechanism of ceramic
2024年11月1日 Ceramic grinding, which in this paper is defined as a method of using ceramic materials as grinding media, is favored by many processing plants as an emerging highefficiency and energysaving 2012年6月1日 The paper presents an overview of the current methodology and practice in modeling and control of the grinding process in industrial ball mills Basic kinetic and energy models of the grinding (PDF) Grinding in Ball Mills: Modeling and Process ControlPDF On Jun 1, 2019, K Balachander and others published Energy Saving Measures in Textile Mill Find, read and cite all the research you need on ResearchGate(PDF) Energy Saving Measures in Textile Mill ResearchGate2023年9月1日 The stirred media mill is a piece of process equipment used in comminution, which uses grinding media, beads of ceramic or similar material, to mediate energy transfer between a rotating impeller Energy conservation and consumption reduction in grinding
.jpg)
Energy saving and process optimization in a
2021年1月18日 water savings was approx 20%, which allowed shutting off one of the three highpressure pumps Electrical energy saving amounts to 9,300,000* kWh/ year At the current energy costs this is equivalent to 000 TL 2,100,/ 641,700 EUR** Additional advantages are seen such as reduced material cooling and the lower wear of theDOI: 101016/jmineng2024 Corpus ID: ; Understanding the EnergySaving mechanism of ceramic balls in tumbling mills @article{Fang2024UnderstandingTE, title={Understanding the EnergySaving mechanism of ceramic balls in tumbling mills}, author={Xin Fang and Caibin Wu and Ningning Liao and Chengfang Yuan and Jiuxiang Zhong Understanding the EnergySaving mechanism of ceramic 2023年10月8日 medium were obtained using BAP hormone at a concentration of 15 mgL1 The The highest mean of rooting percentage, fresh and dry weight of roots was obtained inEffects of Culture Medium and Concentration of 2023年11月1日 This paper demonstrates the feasibility of using a ceramic medium stirring mill to reduce the energy consumption of grinding operations through an industrial verification experiment Compared with the original twostage ball milling process, the cost of grinding power consumption is significantly reduced by about 5016%, which provides a reference for the Energy conservation and consumption reduction in grinding