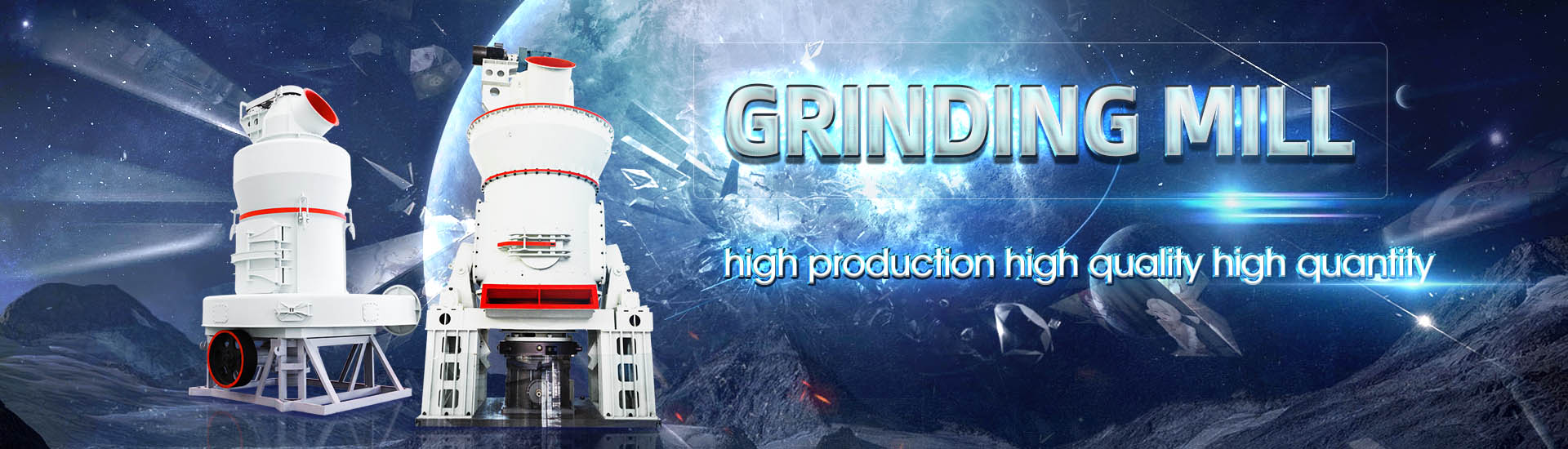
Lime ore steel ball ratio
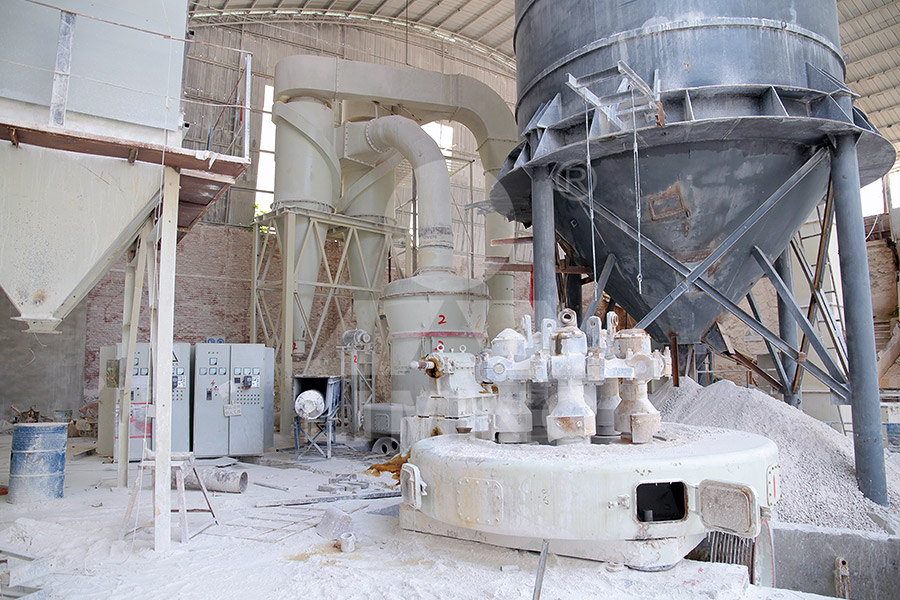
Effect of ball mill grinding parameters of hydrated lime fine
2013年5月1日 The influence of several grinding parameters such as charged material volume, ball filling ratio, and mill rotation speed on energy efficiency of fine grinding of hydrated lime 2023年2月15日 What is steel grinding ball proportioning? Steel grinding ball proportioning in a ball mill has two implications One is to determine which types of balls to install The other is to determine the proportion of balls of various Method of Steel Grinding Ball Proportioning and 2021年8月22日 In this paper, a value in use model based on mass balance and heat balance was developed and used to evaluate the impact of lime quality on the BOF process The model has been successfully(PDF) Value in use of lime in BOF steelmaking In sintering, calcined lime charging of around 1–2% has been done by several investigators 1, 2) and it is a useful practice in many steel plants Most of them have found very good performance in micro balling in secondary drum, sinter Development on Iron Ore Pelletization Using
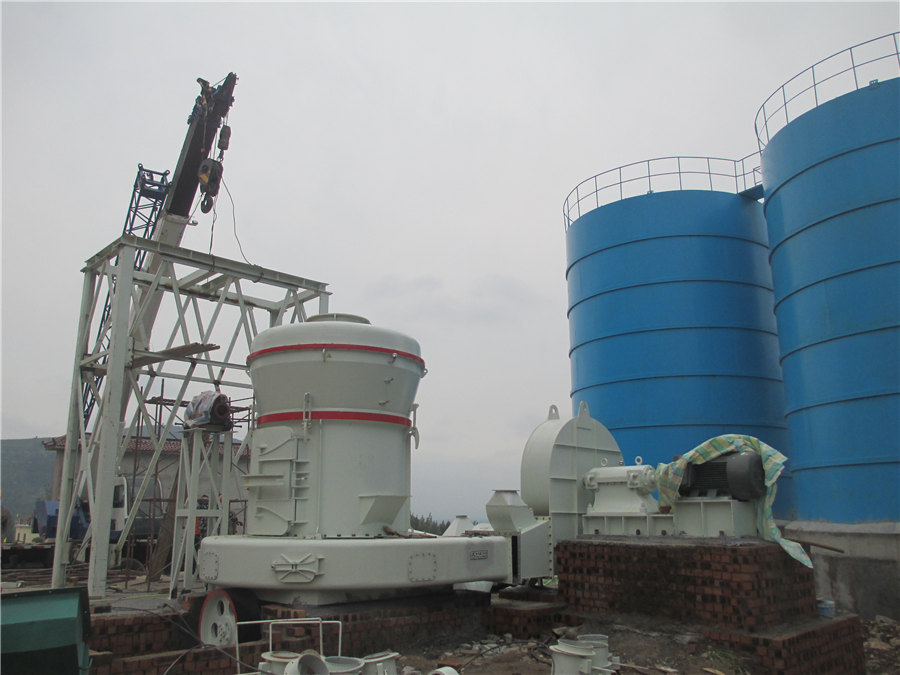
Value in use of lime in BOF steelmaking process: Ironmaking
2021年8月22日 The calculation results show that goodquality lime could increase the scrap ratio, reduce the lime consumption, and reduce iron loss, accordingly, improve the steel 2024年7月15日 In this paper, a value in use model based on mass balance and heat balance was developed and used to evaluate the impact of lime quality on the BOF process The Value in use of lime in BOF steelmaking process2013年5月1日 In this paper, a series of dry grinding experiments with a hydrated lime powder using a ball mill were carried out to investigate the effect of various grinding parameters such Effect of ball mill grinding parameters of hydrated lime fine 2022年1月1日 The calculation results show that goodquality lime could increase the scrap ratio, reduce the lime consumption, and reduce iron loss, accordingly, improve the steel quality, Value in use of lime in BOF steelmaking process
.jpg)
Management of Lime in Steel MDPI
2018年7月4日 Steel uses between 140 and 160 million tons of lime globally A big part of lime production is captive produced within steel mills, especially in the developing world EU28 lime production is estimated at about 20 million tons, 2023年4月23日 balls grind coarser ore particles efficiently and smaller balls grind fine particles more efficiently [44] Larger balls break particles by impact, whilst smaller balls break by abrasion(PDF) Grinding Media in Ball MillsA Review2023年2月15日 A beneficiation plant in Singapore loads balls into a ϕ 1500mm×3000mm wet grid type ball mill, determines the filling rate ϕ = 50%, and selects cast steel grinding balls δ = 45 t/m 3 The ball mill processes the Method of Steel Grinding Ball Proportioning and 2024年8月27日 This study explores the effect of steel ball size and proportion on mineral grinding characteristics using Discrete Element Method (DEM) simulations Based on batch grinding kinetics, this paper analyzes the contact Investigating the Influence of Medium Size and
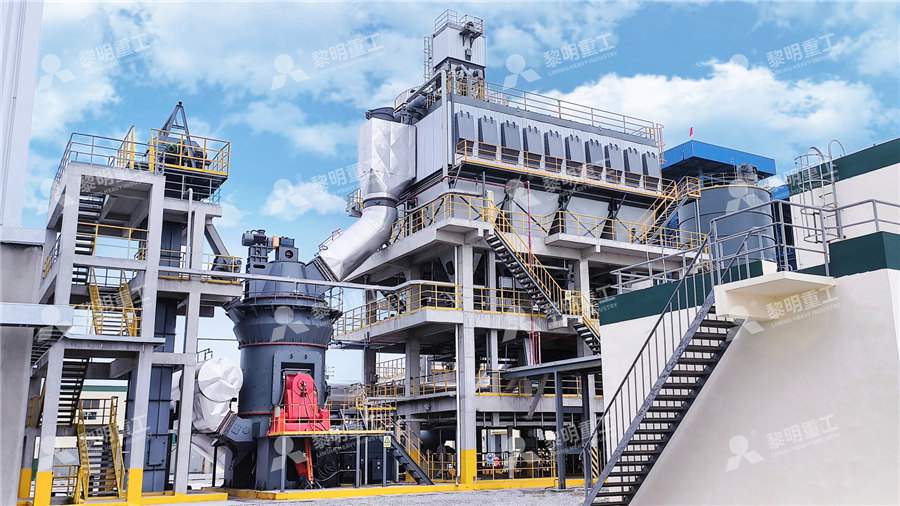
Ball Mills 911Metallurgist
2017年2月13日 In all ore dressing and milling Operations, including flotation, cyanidation, gravity concentration, and amalgamation, the Working Principle is to crush and grind, often with rod mill or ball mill, the ore in order to liberate the minerals In the chemical and process industries, grinding is an important step in preparing raw materials for subsequent treatment2023年11月12日 height till it slides and falls over other ore/pellets at drum bottom During free fall it causes impact and renders breaking of particle into smaller fragmentsEffect of Lime coating of iron ore pellets on Iron 2024年9月11日 The proportion of steel balls can be added according to the size of the steel balls (ф120mm, ф100mm, ф80mm) , Ф60mm, ф40mm) Steel ball addition: different ball mill models have different total ball loads Why is the steel ball amount only added 80% during the ball mill runningin process, because the ball mill is installed, the size and The ratio of grinding steel balls to ball mills2013年5月1日 Too small a material ball ratio increases the probability of ballball collision, which not only reduces the processing capacity of the mill but also increases direct impact, balltoball grinding, and grinding between the ball and the liner plate; consequently, increasing useless steel consumption Too large a material ball ratio indicates too Effect of ball mill grinding parameters of hydrated lime fine

(PDF) Effect of Slurry Density on Load Dynamic and
2012年4月17日 Based on the spectrum feature of the shell vibration or acoustic signal, three soft sensor models of mill load, such as mineral to ball volume ratio, charge volume ratio and pulp density are 2023年4月13日 The effect of ball size and interstitial filling on the performance of dry ball mill grinding was investigated for a limestonetype brecciated uranium ore The optimum grinding was obtained with the combination of different balls (127–375 mm) and interstitial filling of 50% (20% ball filling ratio at fixed material filling ratio = 4%) The net power consumption in a ball mill is Optimization of Ball Mill Grinding of a LimestoneType Basic oxygen steelmaking (BOS) slag, a product of hot metal element (eg, Si, Mn, Fe, P) oxidation and flux (eg lime, dolomite) dissolution, plays a critical role in the production of highquality crude steel, although its behavior inside the BOS vessel (formation and reaction with metal droplets and gas) is still not clear and its recycling has always been challengingBasic Oxygen Steelmaking Slag: Formation, Reaction, and 2018年8月31日 The EU28 total lime demand in 2017 was estimated at about 20 million tons, out of which about 40% are consumed in the iron and steel industry(PDF) Management of Lime in Steel ResearchGate
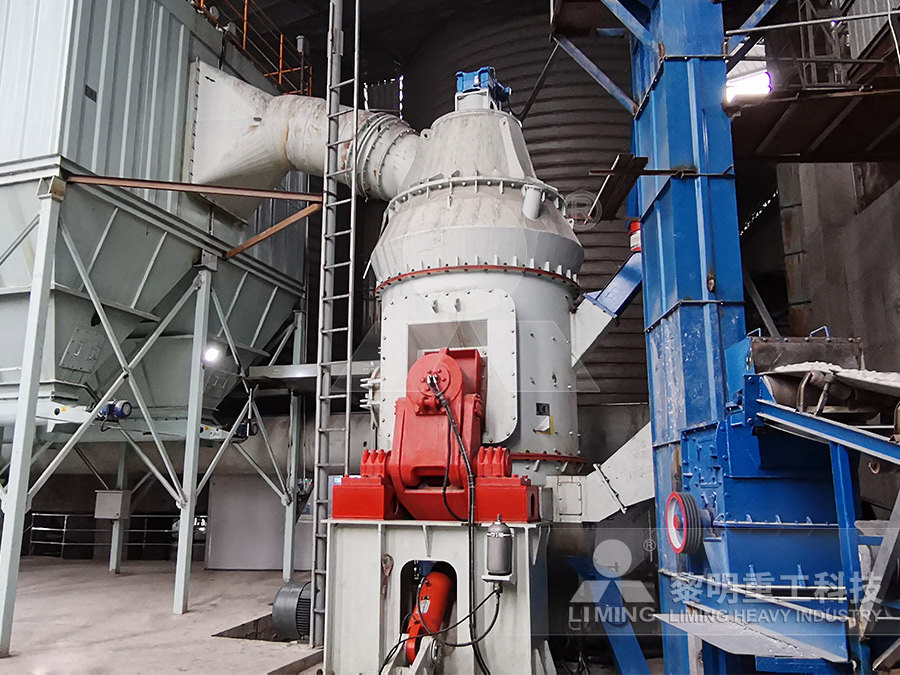
A Novel Sintering Process for Porous Iron Ore Sintering
2022年8月12日 The iron ore is preprocessed in the presence of calcined lime for the temporary closure of pores, which further prevents water absorption during the granulation process in drum in the presence of water The calcined lime coated iron ore provides surface coating on them, which enhances the reaction kinetics, inhibits water absorption into the 2024年1月9日 height till it slides and falls over other ore/pellets at drum bottom During free fall it causes impact and renders breaking of particle into smaller fragmentsEffect of Lime coating of iron ore pellets on Iron 2020年10月9日 The mill speed, fill level ratio, and steel ball ratio can significantly affect mill operation, and our conclusions can provide a reference for an actual situation Based on ore Operation Analysis of a SAG Mill under Different Conditions Based on 2013年5月1日 The influence of several grinding parameters such as charged material volume, ball filling ratio, and mill rotation speed on energy efficiency of fine grinding of hydrated lime and the product Effect of ball mill grinding parameters of hydrated lime fine
.jpg)
Stabilization of iron ore tailing with lowcarbon lime/carbide
2024年1月26日 The massive accumulation of iron ore tailing (IOT) results in land resource wastage and increases the possibility of environmental pollutionIn this study, the feasibility of using lowcarbon alkaliactivated ground granulated blastfurnace slag (lime/Carbide slag (CS)GGBS) and coal fly ash (CFA) instead of portland cement (PC) for solidifying IOT was 2023年5月27日 1) Steel balls Steel balls are durable and can withstand the high impact forces of the milling process They are also relatively inexpensive and readily available However, steel balls can cause contamination of the lithium ore due to the presence of iron This can be a significant issue, especially if the lithium ore is intended for use in Ball Milling in Lithium Ore Processing: A Comprehensive Guide2014年10月31日 Pal et al [56] performed a development slagging experiment by smelting operation of pellet iron ore using calcined lime instead of limestone and magnesium oxide in a carbonaceous atmosphere Thus Development on Iron Ore Pelletization Using Calcined Lime 2020年5月26日 Iron ore consists of various oxides of iron (occurring as ironcontaining minerals) mixed with oxides of other metals (such as Al and Si) In the traditional route to produce steel, the ore is first ground and most of the noniron oxide minerals are removed through various means, a process referred to as beneficiationThe beneficiated ore is then made into various forms of Analysis of the Theoretical and Practical Energy Springer
.jpg)
The energy efficiency of ball milling in comminution
2002年11月1日 A ball mill employs steel balls to generate a grinding action, ie ore particle comminution via impact and abrasion with steel balls, and is a key component of beneficiation plant production2012年6月1日 It consists of one or more rotating cylinders partially filled with grinding balls (made of either ceramic or steel) and feed material (Monov et al 2013) The cylinder can be mounted either (PDF) Grinding in Ball Mills: Modeling and Process ControlAll the raw materials and additives have been received from Tata Steel, India The size fraction of iron ore fines From the Table 2 it is evident that Noamundi hematite ore contains very high alumina and it has adverse ratio of silica to Development on Iron Ore Pelletization Using 2017年4月29日 In the previous discussion the fact was established that the work done by a ball when it strikes at the end of its parabolic path is proportional to its weight and velocity; then, since the velocity may be considered as constant for all the balls in the mill, the work done by a ball is proportional to its weight Since the amount of ore crushed varies as the work done upon it, it Grinding Media Wear Rate Calculation in Ball Mill
.jpg)
Adaptability analysis of H2rich gas injection and sintered ore
2024年11月1日 With the OreA ratio increased from 0 wt% to 18 wt% under no injection conditions, the m ˃315mm decreased from 3616 g to 3561 g, and the RDI dropped from 724% to 693% From this, increasing the OreA ratios adversely affected the lowtemperature reduction degradation of the sintered ore2018年7月4日 The EU28 total lime demand in 2017 was estimated at about 20 million tons, out of which about 40% are consumed in the iron and steel industry Steel remains the major consumer after environment and construction The lime industry is quite mature and consolidated in developed countries, with enough reserves and production to serve regional markets while Management of Lime in Steel MDPI2024年7月24日 RoM ball mill is pebble ported most of the steel balls can discharge through the pebble ports and cause logistic problems of separating steel balls from rocks prior to sending the pebbles for RoM BALL MILLS A COMPARISON WITH AG/SAG 2012年12月1日 The inmill load volume and slurry solids concentration have significant influence on the ball mill product size and energy expenditure Hence, better energy efficiency and quality grind can only (PDF) Optimization of inmill ball loading and slurry solids
.jpg)
Iron Ore Pellets and Pelletization Process IspatGuru
2014年11月26日 Iron Ore Pellets and Pelletization Process Pelletizing of iron ore was started in the 1950s to facilitate the utilization of finely ground iron ore concentrates in steel production For the pelletizing of iron ore there are two main types of processes namely, the straight travelling grate (STG) process and the grate kiln (GK) process2023年9月20日 fect of the various grinding parameters such as ball charge filling ratio, material charged ratio, and mill speed on the properties of hydrated lime and fineness of the product using a ball mill 2Effect of ball mill grinding parameters of hydrated lime 2023年4月23日 balls grind coarser ore particles efficiently and smaller balls grind fine particles more efficiently [44] Larger balls break particles by impact, whilst smaller balls break by abrasion(PDF) Grinding Media in Ball MillsA Review2023年2月15日 A beneficiation plant in Singapore loads balls into a ϕ 1500mm×3000mm wet grid type ball mill, determines the filling rate ϕ = 50%, and selects cast steel grinding balls δ = 45 t/m 3 The ball mill processes the Method of Steel Grinding Ball Proportioning and
.jpg)
Investigating the Influence of Medium Size and
2024年8月27日 This study explores the effect of steel ball size and proportion on mineral grinding characteristics using Discrete Element Method (DEM) simulations Based on batch grinding kinetics, this paper analyzes the contact 2017年2月13日 In all ore dressing and milling Operations, including flotation, cyanidation, gravity concentration, and amalgamation, the Working Principle is to crush and grind, often with rod mill or ball mill, the ore in order to liberate the minerals In the chemical and process industries, grinding is an important step in preparing raw materials for subsequent treatmentBall Mills 911Metallurgist2023年11月12日 height till it slides and falls over other ore/pellets at drum bottom During free fall it causes impact and renders breaking of particle into smaller fragmentsEffect of Lime coating of iron ore pellets on Iron 2024年9月11日 The proportion of steel balls can be added according to the size of the steel balls (ф120mm, ф100mm, ф80mm) , Ф60mm, ф40mm) Steel ball addition: different ball mill models have different total ball loads Why is the steel ball amount only added 80% during the ball mill runningin process, because the ball mill is installed, the size and The ratio of grinding steel balls to ball mills
.jpg)
Effect of ball mill grinding parameters of hydrated lime fine
2013年5月1日 Too small a material ball ratio increases the probability of ballball collision, which not only reduces the processing capacity of the mill but also increases direct impact, balltoball grinding, and grinding between the ball and the liner plate; consequently, increasing useless steel consumption Too large a material ball ratio indicates too 2012年4月17日 Based on the spectrum feature of the shell vibration or acoustic signal, three soft sensor models of mill load, such as mineral to ball volume ratio, charge volume ratio and pulp density are (PDF) Effect of Slurry Density on Load Dynamic and2023年4月13日 The effect of ball size and interstitial filling on the performance of dry ball mill grinding was investigated for a limestonetype brecciated uranium ore The optimum grinding was obtained with the combination of different balls (127–375 mm) and interstitial filling of 50% (20% ball filling ratio at fixed material filling ratio = 4%) The net power consumption in a ball mill is Optimization of Ball Mill Grinding of a LimestoneType Basic oxygen steelmaking (BOS) slag, a product of hot metal element (eg, Si, Mn, Fe, P) oxidation and flux (eg lime, dolomite) dissolution, plays a critical role in the production of highquality crude steel, although its behavior inside the BOS vessel (formation and reaction with metal droplets and gas) is still not clear and its recycling has always been challengingBasic Oxygen Steelmaking Slag: Formation, Reaction, and