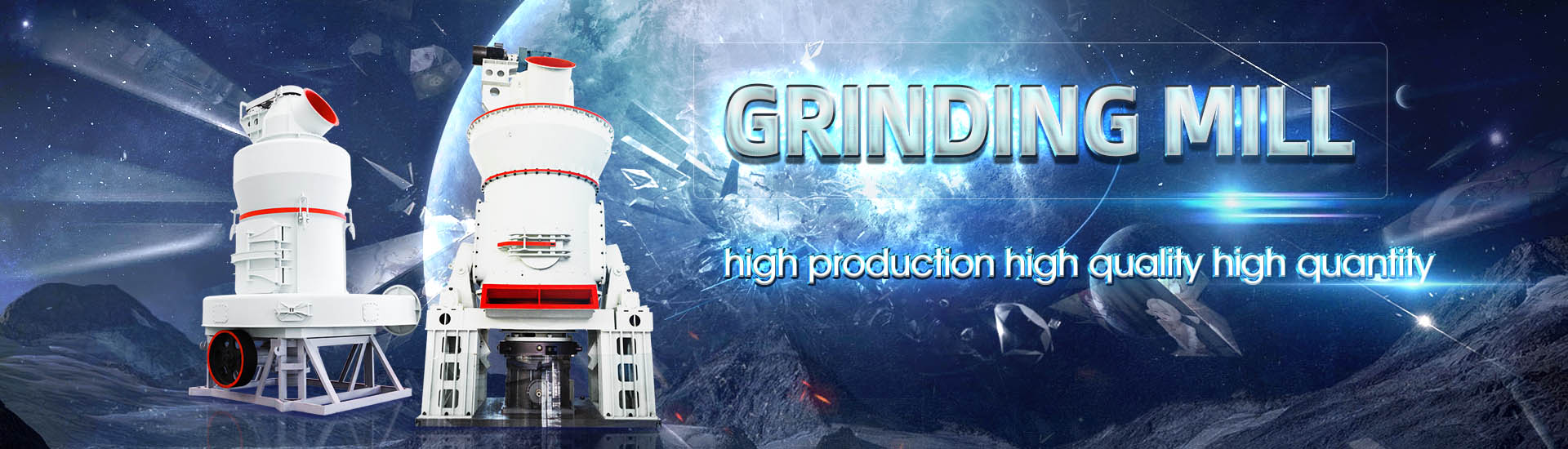
Difficulties in direct lead smelting process
.jpg)
Challenges and Opportunities of a Lead Smelting
2018年8月18日 Abstract Managing complex material streams within a lead smelting/reduction process has a long history at Aurubis After modernization of the secondary lead smelter in 2012年10月1日 The application of oxygenrich side blowing furnaces in the direct leadsmelting process has excellent potential and ideal capability for coprocessing various feedstocks, such as zincSituation and Technology Progress of Lead 2018年8月19日 Managing complex material streams within a lead smelting/reduction process has a long history at Aurubis After modernization of the secondary lead smelter in 1991, Challenges and Opportunities of a Lead Smelting Process for 2023年10月23日 With the increasingly complicated sources of lead smelting materials, it is becoming more difficult to optimize process parameters during the bottomblowing lead oxidation smelting process Building a bottomblowing MultiPhase Equilibrium Model of Oxygen
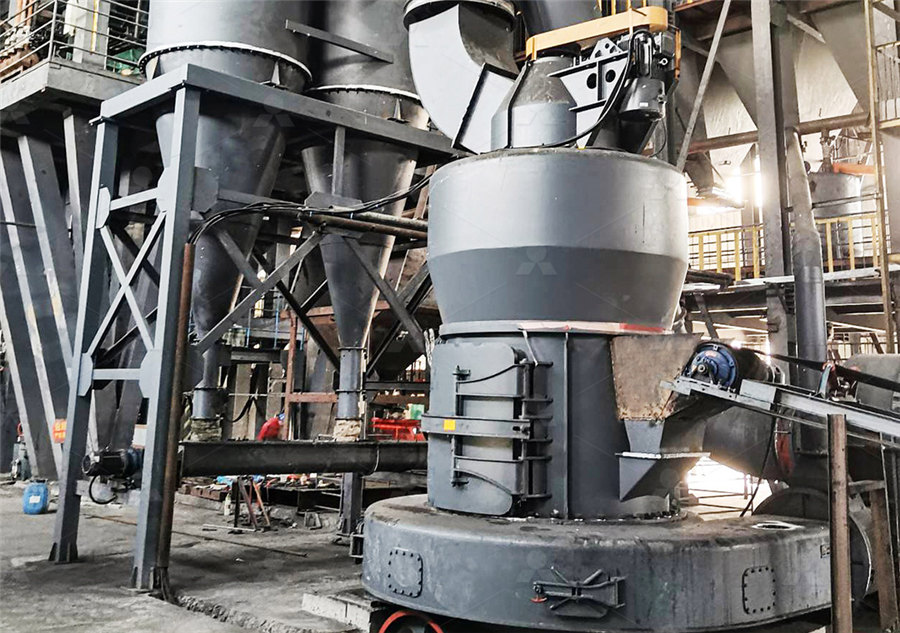
Process for Direct Smelting of Lead Concentrates
2017年8月25日 Charges of lead were inductionmelted in clay graphite crucibles, and excess lead concentrates were placed on the surface of the lead The crucibles were covered and the 2023年8月20日 LCA is a data model (Zhang et al, 2022), and data acquisition and collection are the main difficulties in evaluating the environmental impacts of heavy metal smelting Zhang et Life cycle assessment of a typical lead smelting process in In view of the difficulty in environmental and economic treatments of leadbearing wastes generated in lead and zinc smelter,a new reducingmatting smelting process was proposed toRecovery of lead and silver from leadbearing wastes using2012年2月3日 Currently, the most important direct smelting technologies for the production of lead are the KIVCET, the QSL, and the Isasmelt/Ausmelt processes In direct smelting Lead Smelting an overview ScienceDirect Topics
.jpg)
Metallurgy of the direct smelting of lead Springer
2017年8月26日 DIRECT LEAD SMELTING PROCESSES Current direct smelting processes, commercialized or developed to the pilot plant stage, are sum marized in Table 1 In each 2015年9月10日 126 Primary Lead Smelting 1261 General15 Lead is found naturally as a sulfide ore containing small amounts of copper, iron, zinc, precious metals, and other trace elements The lead in this ore, typically after being concentrated at or Process Particulateb PM10c Lead SO 2 Ore crushingd (SCC 30301004) 0023 0018 0001 NA126 Primary Lead Smelting US EPAAlthough this process is efficient and environmentally friendly (achieving a direct yield of bismuth of 8925 %, with the crude bismuth having a purity of 8569 %, and capable of enriching valuable metals such as lead, copper, and silver, as well as fixing 9637 % of sulfur), it has the drawback of high energy consumption (with smelting Advancements in the separation, purification, and smelting 2020年1月17日 This old practice experiences more and more difficulties being technologies for primary lead smelting Most of these processes were based on direct and mainly continuous smelting technologies but only some, like the Kivcet, QSL, Isa/Ausmelt and individual auxiliary plant sections with the smelting process a virtually wastefree productionMODERN APPLIED TECHNOLOGIES FOR PRIMARY LEAD
.jpg)
CoSmelting Process of Pb Concentrate and Zn Leaching
The application of oxygenrich side blowing furnaces in the direct leadsmelting process has excellent potential and ideal capability for coprocessing various feedstocks, such as zinc leaching residues, jamesonite precipitates, lead paste and lead–silver dregs, etc In this study, the industrial application for this process has been investigated and the material balance has been 2014年12月23日 An analytical framework of lead elemental flow was established based on substance flow analysis and aimed at solving lead metal pollution during the lead bullion smelting process The sources and endpoints of lead flow in liquid highlead slag direct reduction process were researched by monitoring and analyzing both sampled and accounting data of batching Lead Flow Analysis of Lead Bullion Smelting Process2021年12月28日 Lead was recovered through a direct smelting reduction route from a lead concentrate by using mixtures of Na2CO3 and SiC to 1000 °C The lead concentrate was obtained from the mining State of Zacatecas, México by traditional mineral processing and froth flotation The experimental trials showed that 86 wt% of lead with a purity up to 97% can be Lead Recovery from a Lead Concentrate throughout Direct Smelting 2023年4月5日 The blast furnace and direct reduction processes have been the major iron production routes for various iron ores (ie goethite, hematite, magnetite, maghemite, siderite, etc) in the past few decades, but the challenges of maintaining the iron and steelmaking processes are enormous The challenges, such as cumbersome production routes, scarcity of Recent Trends in the Technologies of the Direct Reduction and Smelting
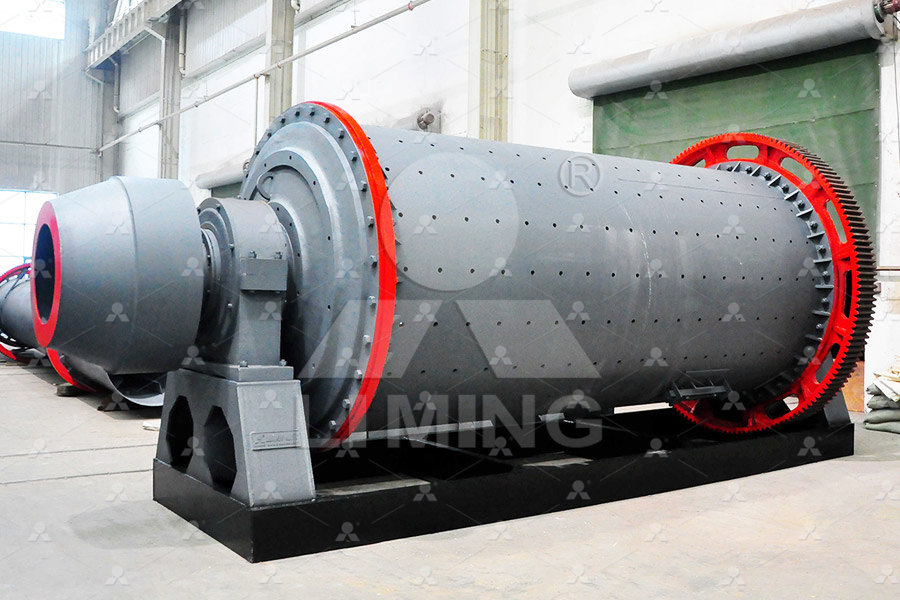
Reduction of LeadRich Slags with Coke in the Lead Blast Furnace
2020年1月25日 The lead blast furnace has historically been a staple in the lead smelting process Its main purpose is the reduction of a PbOrich feed with metallurgical coke, in order to produce metallic lead Despite the rise of new technologies over the past decades, it remains highly relevant, as many lead production sites still use a blast furnace in 2015年1月1日 The SKS lead smelting process is a reduction and refining process of lead compounds to elemental lead in a series of hightemperature furnaces (the first oxidation reaction occurs in a bottom blowing furnace, then the reduction reaction occurs in a blast furnace) the inevitable measurement errors and the difficulty of quantified monitoring Statistical entropy analysis of substance flows in a lead smelting process2018年1月19日 Direct smelting of lead bearing materials is carried out in compact and sealed units, allowing for reduction of heat loss and tight emission control Shumskiy VA (2012) Role of the raw material grade in selecting a lead smelting process sl: TMS, 2010 LeadZinc, pp 475–480 Google Scholar Fathi H (2002) Textbook of pyrometallurgy Pyrometallurgical Processing of Secondary Lead Material: An 2020年1月25日 More than 80% lead production is adapt SKS technology The application of SKS lead smelting technology greatly increases the automation degree of the lead smelting process, improves the operating environment, and reduces the three wastes emission and the production cost, which has become the world’s most widely used lead smelting processThe Latest Development of Oxygen Bottom Blowing Lead Smelting
.jpg)
Lead Flash Smelting Process SpringerLink
2023年6月7日 Lead flash smelting process is a technology of producing lead bullion by flash smelting with lead sulfide concentrate as raw material It is an oxygenenriched direct lead smelting technology in lead smelting The main facilities include flash smelting furnaces and slag cleaning electric furnaces A flash smelting furnace is composed of a 2023年9月15日 The Outotec® Direct Zinc Smelting (DZS) process provides a means for the pyrometallurgical treatment of zinc concentrates to produce a highpurity, oxide fume and low zinc content, discard slagThe Outotec Direct Zinc Smelting Process ResearchGate2018年8月18日 Due to the nature of the lead smelting process, these elements will combine depending on the metallurgical operating conditions of the furnace generating intermetallic compounds, known as speiss The formation of speiss has been a constant topic for metallurgist operating processes such as the secondary leadChallenges and Opportunities of a Lead Smelting 2021年12月28日 The production of primary lead is a process of extracting lead from lead sulfide concentrates by smelting The smelting process includes the sinter plant–blast furnace route and direct smelting reduction, including oxidation, reduction, and refining In the sinter plant–blast furnace route, PbS is oxidized in the solid state to remove Lead Recovery from a Lead Concentrate throughout
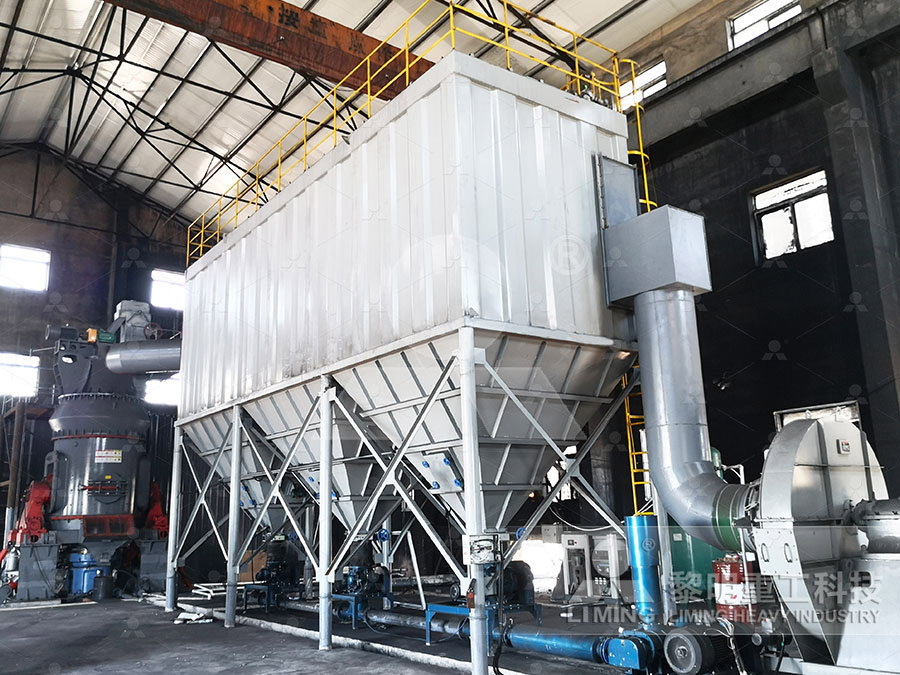
Top submerged lance direct zinc smelting ETN Socrates
2017年3月16日 by TSL flowsheets to process EAF dusts (Hughes et al, 2007; Lee et al, 2006) as well as direct processing of zinc concentrates, which is the topic of this paper 12 Direct zinc processing – future solutions Over the past 25 years, fundamental investigations have been conducted into the direct smelting of zinc sulphide concentrates2019年7月1日 Large amounts of lead slag are produced during the production of primary lead and secondary lead Considering lead concentrate smelting as an example, a primary lead smelting system production of 1 t of lead will discharge 7100 kg of lead slag (Hou, 2011)At the secondary lead recycling process, for each ton of metallic lead produced, 100–350 kg of slag A review on lead slag generation, characteristics, and utilization2006年1月1日 It takes almost 25 hours for the whole industrial flow, and there are too many factors that add great difficulties into the modeling of the process 2 Innumerable physical chemical reactions, biochemical reactions and phase transitions are contained in the smelting process, which is accompanied by the transmission and transformation of the INTELLIGENT FAULT DIAGNOSIS IN LEADZINC SMELTING PROCESSDirect smelting processes an increasing proportion, and some 7% of primary lead production is by the zinc–lead blast furnace (the Imperial Smelting Process) In addition to refined pig lead, important byproducts of lead smelting include antimony as antimonial lead alloys, copper, silver, gold, cadmium, bismuth, sulfuric acid, and zinc as Lead Smelting an overview ScienceDirect Topics
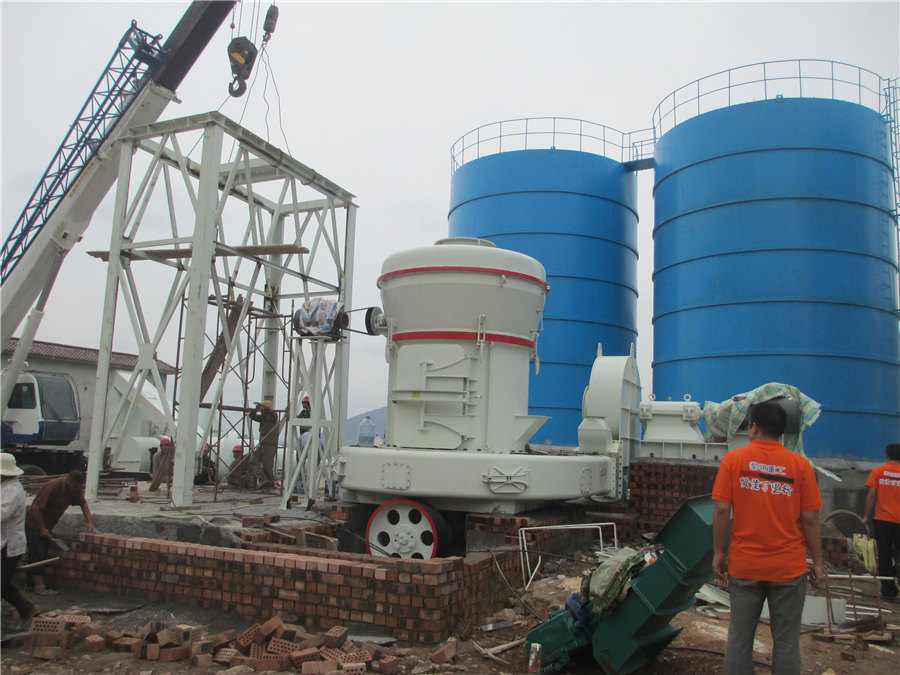
Lead recovery from a lead concentrate throughout direct smelting
2021年12月28日 A pyrometallurgical process for the direct reduction of molten highlead smelting slag obtained by the Shuikoushan (SKS) method was reported in this article using solid anthracite as the fuel and 2022年12月1日 There are fewer impurities in the leaching residue after leaching, and the lead content is about 50 % and can be directly recycled back into the lead smelting process for recycling In conclusion, the oxidation leaching of zinc and germanium from zinc oxide dust with potassium dichromate under ultrasound proves to be efficient, economical and Efficient recovery of valuable metals from leadzinc smelting In view of the difficulty in environmental and economic treatments of leadbearing wastes generated in lead and zinc smelter,a new reducingmatting smelting process was proposed to recycle secondary lead from multiple leadbearing wastes in this paper In the process,the designed mixture of lead sludge,lead slag,lead ashes and pyrite cinder was used as a smelting Recovery of lead and silver from leadbearing wastes usingMetal smelting is a process in which waste materials containing precious metals are mixed with fluxes, collectors, and reductants to obtain a precious metalcollector alloy Metal smelting and refining processes generate wastes that may contain multiple hazardous metals, such as lead, zinc, nickel, copper, cadmium, chromium, mercury Metal Smelting an overview ScienceDirect Topics
.jpg)
Secondary Lead Smelting at the Beginning of the 21
2022年7月18日 etc) The entire process results in four different intermediate products: 1) Lead paste for smelting, 2) Metallic lead for melting or smelting, 3) Polypropylene for recycling purposes, and 4) Lead contaminated plastic fraction which has to be disposed or, if permitted, can be charged to a furnaceThis paper briefly describes the status of China's lead smelting,the progress of China's lead smelting technology is introduced in the traditional sintering process,a new poolsmelting process,rebornLead smelting process,the liquid richlead slag direct reducing technology,and pointed out the new technology of waste batteries autoseparationbottomblowing smelting Status and progress of lead smelting technology in China2017年8月26日 veloping a flash smelting process for sulfidic lead concentrates" Beginning with laboratory experi ments and followed by testing the different smelter units on a pilotplant scale, the company was ready by 1964 to build a pilotplant including all units necessary for the complete process PROCESS DESCRIPTION In traditional lead smelting LEAD CONCENTRATES Springer2024年4月21日 Guide to Modern Smelting Processes – T09002 3 • Environmental Impact: Smelting processes can have environmental consequences, including emissions of greenhouse gases and other pollutants Modern smelting endeavors to mitigate these impacts through cleaner technologies and sustainableGuide to Modern Smelting Processes CED Engineering
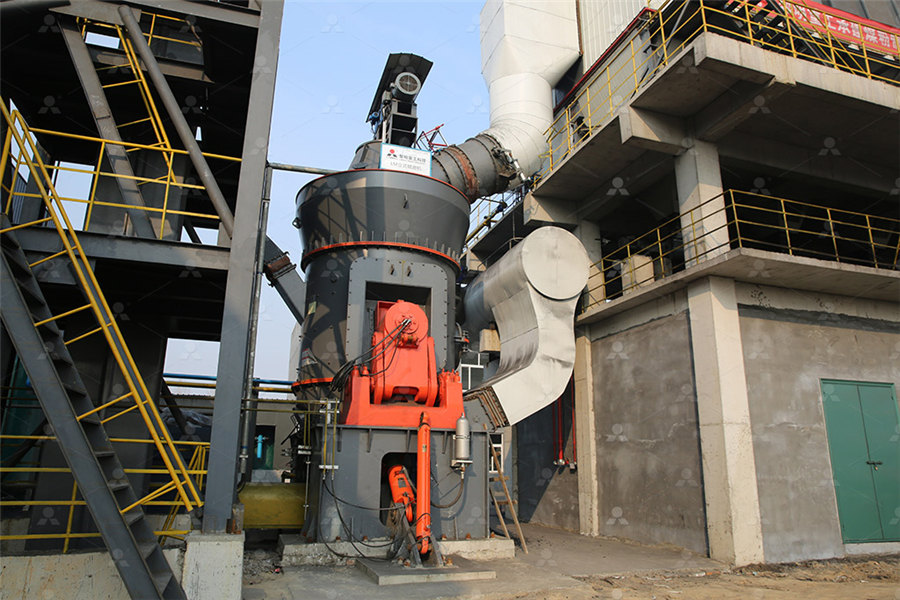
Top Submerged Lance Direct Zinc Smelting ResearchGate
paper discusses Direct Zinc Smelting (DZS) Process In Stage 1 of this novel two stage TSL application the sulphide sulphur from the zinc concentrate is the energy carrier used to smelt the2023年7月8日 Lead and Zinc Smelting Industry Description and Practices Lead and zinc can be produced pyrometallurgically or hydrometallurgically, depending on the type of ore used as a charge In the pyrometallurgical process, ore concentrate containing lead, zinc, or both is fed, in some cases after sintering, into a primary smelter Lead concentraLead and Zinc Smelting International Finance CorporationLead processing, preparation of the ore for use in various products Lead (Pb) is one of the oldest metals known, being one of seven metals used in the ancient world (the others are gold, silver, copper, iron, tin, and mercury) Its low melting point of 327 °C (621 °F), coupled with its easyLead processing Smelting, Refining Uses Britannica2015年9月10日 126 Primary Lead Smelting 1261 General15 Lead is found naturally as a sulfide ore containing small amounts of copper, iron, zinc, precious metals, and other trace elements The lead in this ore, typically after being concentrated at or Process Particulateb PM10c Lead SO 2 Ore crushingd (SCC 30301004) 0023 0018 0001 NA126 Primary Lead Smelting US EPA
.jpg)
Advancements in the separation, purification, and smelting
Although this process is efficient and environmentally friendly (achieving a direct yield of bismuth of 8925 %, with the crude bismuth having a purity of 8569 %, and capable of enriching valuable metals such as lead, copper, and silver, as well as fixing 9637 % of sulfur), it has the drawback of high energy consumption (with smelting 2020年1月17日 This old practice experiences more and more difficulties being technologies for primary lead smelting Most of these processes were based on direct and mainly continuous smelting technologies but only some, like the Kivcet, QSL, Isa/Ausmelt and individual auxiliary plant sections with the smelting process a virtually wastefree productionMODERN APPLIED TECHNOLOGIES FOR PRIMARY LEADThe application of oxygenrich side blowing furnaces in the direct leadsmelting process has excellent potential and ideal capability for coprocessing various feedstocks, such as zinc leaching residues, jamesonite precipitates, lead paste and lead–silver dregs, etc In this study, the industrial application for this process has been investigated and the material balance has been CoSmelting Process of Pb Concentrate and Zn Leaching2014年12月23日 An analytical framework of lead elemental flow was established based on substance flow analysis and aimed at solving lead metal pollution during the lead bullion smelting process The sources and endpoints of lead flow in liquid highlead slag direct reduction process were researched by monitoring and analyzing both sampled and accounting data of batching Lead Flow Analysis of Lead Bullion Smelting Process
.jpg)
Lead Recovery from a Lead Concentrate throughout Direct Smelting
2021年12月28日 Lead was recovered through a direct smelting reduction route from a lead concentrate by using mixtures of Na2CO3 and SiC to 1000 °C The lead concentrate was obtained from the mining State of Zacatecas, México by traditional mineral processing and froth flotation The experimental trials showed that 86 wt% of lead with a purity up to 97% can be 2023年4月5日 The blast furnace and direct reduction processes have been the major iron production routes for various iron ores (ie goethite, hematite, magnetite, maghemite, siderite, etc) in the past few decades, but the challenges of maintaining the iron and steelmaking processes are enormous The challenges, such as cumbersome production routes, scarcity of Recent Trends in the Technologies of the Direct Reduction and Smelting 2020年1月25日 The lead blast furnace has historically been a staple in the lead smelting process Its main purpose is the reduction of a PbOrich feed with metallurgical coke, in order to produce metallic lead Despite the rise of new technologies over the past decades, it remains highly relevant, as many lead production sites still use a blast furnace in Reduction of LeadRich Slags with Coke in the Lead Blast Furnace2015年1月1日 The SKS lead smelting process is a reduction and refining process of lead compounds to elemental lead in a series of hightemperature furnaces (the first oxidation reaction occurs in a bottom blowing furnace, then the reduction reaction occurs in a blast furnace) the inevitable measurement errors and the difficulty of quantified monitoring Statistical entropy analysis of substance flows in a lead smelting process
.jpg)
Pyrometallurgical Processing of Secondary Lead Material: An
2018年1月19日 Direct smelting of lead bearing materials is carried out in compact and sealed units, allowing for reduction of heat loss and tight emission control Shumskiy VA (2012) Role of the raw material grade in selecting a lead smelting process sl: TMS, 2010 LeadZinc, pp 475–480 Google Scholar Fathi H (2002) Textbook of pyrometallurgy