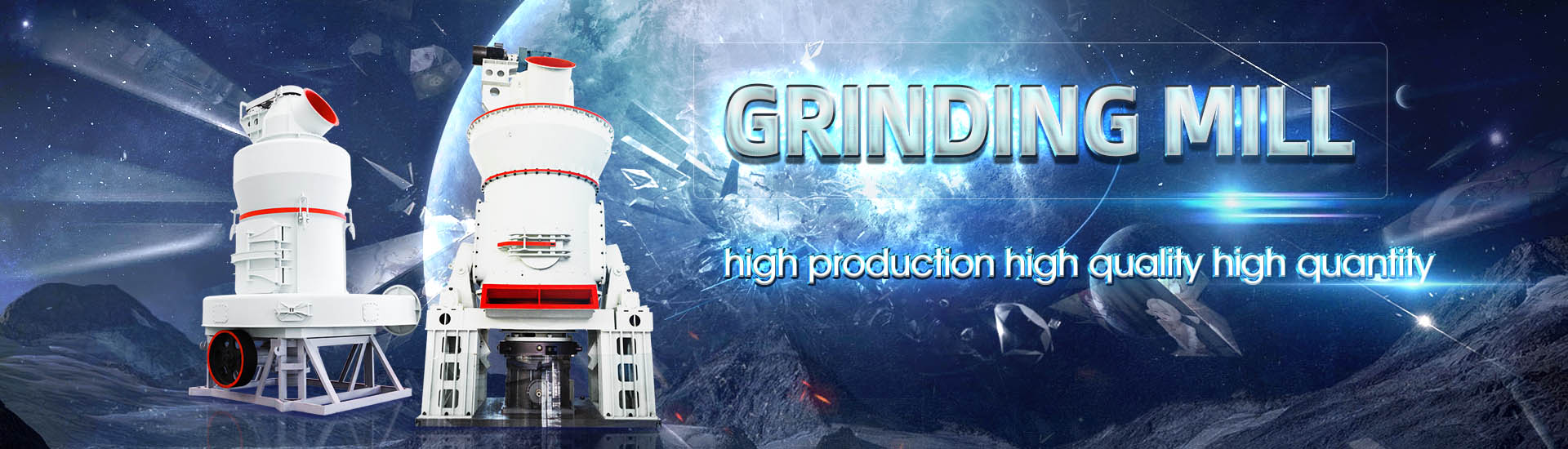
HOME→Is it efficient to use an ore grinding mill to process the smelting waste residue of a limestone crusher
Is it efficient to use an ore grinding mill to process the smelting waste residue of a limestone crusher
.jpg)
Energy Use of Fine Grinding in Mineral Processing
Fine grinding is usually performed in highintensity stirred mills; several manufacturers of these stirred mills exist Two frequently used stirred mills include the Isamill, produced by 展开2023年9月28日 The correlation between the mill power and the operating variables in the grinding process is modelled by using the response surface method (RSM), which solves the MultiObjective Optimization for an Industrial Grinding and 2020年6月1日 The purpose of comminution in ore processing is to reduce particle size in order to improve liberation of valuable minerals and so enable separation from the undesirable Stirred media mills in the mining industry: Material 2023年7月20日 Moist grinding, a special grinding method, is used to prepare pellets for smelting According to the grinding medium features, ore grinding is mainly classified into ball grinding Ore Grinding SpringerLink
.jpg)
Improving Energy Efficiency Across Mineral Processing
1 天前 In particular, the comminution and smelting of metalbearing ores are both highly energyintensive processes If resource companies can optimise the energy efficiency across these 2022年8月31日 The grinding process, as a primary stage of ore/raw material processing, is a necessary operation in beneficiation plants It not only provides the appropriate particle size for subsequent separation operations but also Grinding Modeling and Energy Efficiency in 2022年10月4日 The worldwide mining industry consumes a vast amount of energy in reduction of fragment size from mining to mineral processing with an extremely lowenergy efficiency, Reduction of Fragment Size from Mining to Mineral 2020年12月3日 This study is conducted with the aim of investigating the efficiency of open and closedcircuit molybdenite ore comminution processes (primary and secondary mill, A process mineralogy approach to study the efficiency of
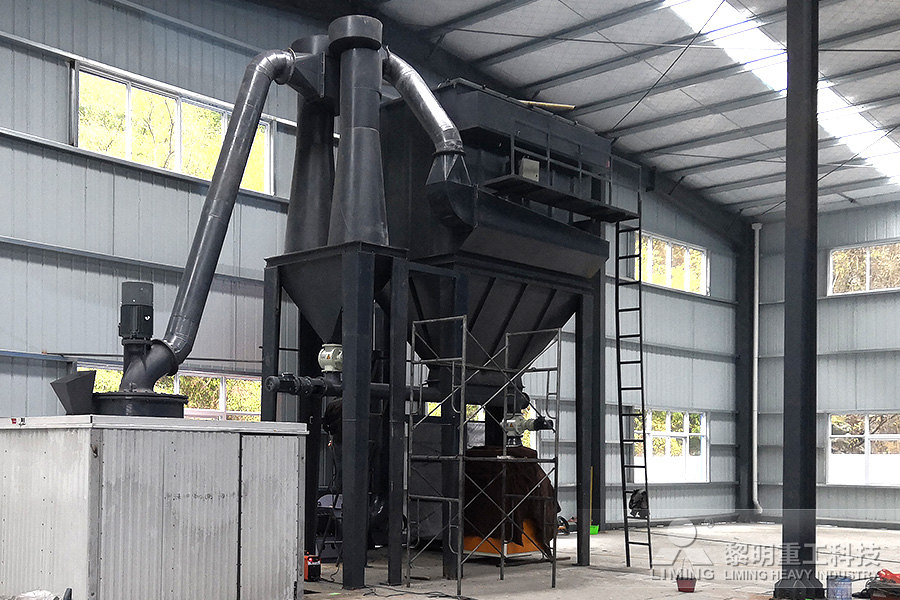
Towards waterless operations from mine to mill ScienceDirect
2022年9月1日 There is a prominent need to reduce water use in the production of primary raw materials Efficient management of fines is an essential aspect of waterless operations from 2021年12月11日 Ball milling uses steel balls to realize grinding effect, that is, to achieve the ore particle comminution through impact and abrasion with steel balls, and plays an important role The Effect of Grinding Media on Mineral Breakage Properties 2022年8月31日 The grinding process, as a primary stage of ore/raw material processing, is a necessary operation in beneficiation plants welcomes papers that highlight innovations and future trends in modeling grinding and Grinding Modeling and Energy Efficiency in 2013年12月18日 Fine grinding, to P80 sizes as low as 7 μm, is becoming increasingly important as mines treat ores with smaller liberation sizes This grinding is typically done using stirred mills such as the Isamill or Stirred Energy Use of Fine Grinding in Mineral Processing
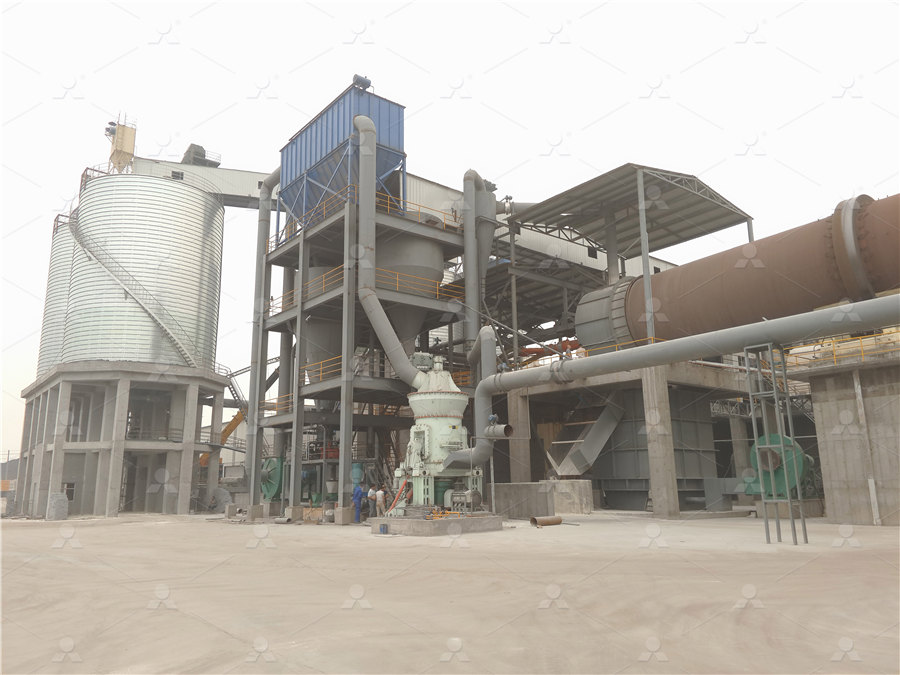
Understanding the operation of grinding mills in the mining
2024年10月13日 The rods, which are typically made of steel, crush the ore as they rotate within the mill Rod mills are often used for coarser grinding and are less efficient than ball mills Autogenous Mills and SemiAutogenous Mills: Autogenous mills use the ore itself as the grinding media, while semiautogenous mills use a combination of ore and steel balls2019年10月8日 The rod mill is developed on the basis of the ball mill It has the advantages of reliable processing technology, low investment, less auxiliary equipment and simple process flow It can be combined with the ball mill to form a different grinding process The rod mill mainly grinds the ore by the pressure and the grinding force of the grinding rodCrushing and Grinding Process JXSC Machine2012年6月1日 The paper presents an overview of the current methodology and practice in modeling and control of the grinding process in industrial ball mills Basic kinetic and energy models of the grinding (PDF) Grinding in Ball Mills: Modeling and Process Control2020年2月1日 Like the HallHéroult process, the overall principles behind the Bayer process of refining bauxite has not changed drastically since its conception However, different equipment has been developed and introduced over the years to increase energy and process efficiency and also to increase alumina recovery [139] There are various practises The aluminium industry: A review on stateoftheart
.jpg)
Aspects of Spodumene Lithium Extraction Techniques MDPI
2024年9月30日 Lithium (Li), a leading cathode material in rechargeable Liion batteries, is vital to modern energy storage technology, establishing it as one of the most impactful and strategical elements Given the surge in the electric car market, it is crucial to improve lithium recovery from its rich mineral deposits using the most effective extraction technique In recent years, both 2022年10月4日 A notable fact is that the energy efficiency of conventional milling is only about 1%, as mentioned in Sect 1 An earlier experimental study indicated that about 80–90% of the energy input of a ball mill was used in heating the material (Schellinger 1951, 1952), and a recent study showed that over 75% of the electrical energy was used to heat the slurry (Bouchard et Reduction of Fragment Size from Mining to Mineral 2011年3月3日 Early mineral processing techniques employed the use of grinding mills as the first phases of liberating and isolating desirable minerals from gangue In the early phases it was also recognized that some form of size classification associated with the grinding mill would allow for more efficient operation of these grinding mills We will look atImplementing strategies to improve mill capacity and 2022年2月28日 Generally, grinding process efficiency can mainly be improved by either improving the grinding behavior of the material being ground or enhancing the grinding machines Recently, the use of additives socalled grinding aids, which is applied in a small amount of 001–025 wt% related to the mass of product, has reduced these problems and been Grinding SpringerLink
.jpg)
Grinding Mills in the Mineral Processing Industry
2024年7月19日 This automated grinding media feeder is designed to maintain the optimal grinding media load in the mill, ensuring consistent power draw and efficient operation The PLC (Programmable Logic Controllers) is programmed to monitor the grinding mill’s power draw, automatically dispensing grinding media when needed to maintain the desired load and 2023年10月10日 Types of Grinding Mills Grinding mills play a crucial role in the mining process, as they are responsible for reducing large chunks of ore into smaller particles that can be further processed There are various types of Understanding the SAG Mill in Copper Ore 2023年7月10日 The present literature review explores the energyefficient ultrafine grinding of particles using stirred mills The review provides an overview of the different techniques for size reduction and (PDF) EnergyEfficient Advanced Ultrafine 2024年9月22日 These mills typically have a larger diameter and length, allowing for a higher ball charge and improved contact between the grinding media and the ore particles The increased capacity of high capacity ball mills enables iron ore processors to handle larger ore feed rates, meet production targets, and reduce overall operational costs 2 Enhancing iron ore grinding efficiency with high capacity ball mills
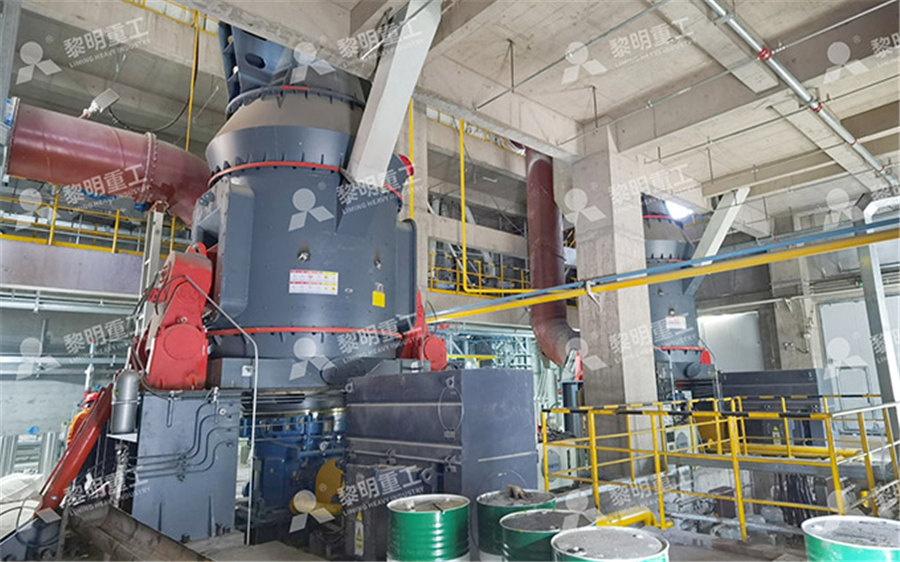
Tips to improve grinding profitability with mill liners
2020年3月30日 A mill lining should be optimized by design in order to minimize problems, utilize the mill’s capacity and keep a good liner profile throughout the wear life2024年1月13日 Table 1 Chemical composition of typical grinding media (% wt) Adapted from [24] 211 Cast Iron Cast iron can be grey cast iron or white cast iron, but white cast irons are commonly used in Grinding Media in Ball MillsA Review ResearchGate2015年3月15日 For the grinding tests, a Loesche mill LM45 (table diameter 045 m) is used (Fig 2a) This pilot scale mill is a special development for ore grinding, which is reflected by several features The mill has four rollers, which are able to stress the particle bed with grinding pressures of up to 5000 kN/m 2 Various different roller geometries Research of iron ore grinding in a verticalrollermill2020年9月1日 Moreover, Bradshaw suggested ‘process mineralogy’ as a bridge for the ore processing, geology, and metallurgy She highlighted that the textural study of the ore would help to design the process flowsheet [11]Naturally, one should keep in mind that it is not possible to consider all the geological textures; however, the key ore textures can be usedBreakage process of mineral processing comminution
.jpg)
Towards waterless operations from mine to mill ScienceDirect
2022年9月1日 Waste rocks occupy space from ore in the grinding mill, thus lowering the mill’s ore grinding capacity and mineral concentrator’s concentrate production Moreover, in most cases, waste rock is harder and, consequently, more difficult to grind than the ore which is often found in the weaker areas of the rock2022年6月29日 If the stick grinding phenomenon occurs in the operation of the energysaving gold mill, it is necessary to first analyze the changes in the properties of the ore, such as the amount of ore fed, the amount of water fed, and the amount of sand returned How to use the gold ore wet pan mill:How to use and maintain the gold ore wet pan mill2016年6月6日 AG/SAG mills grind ore through impact breakage, attrition breakage, and abrasion of the ore serving as media (both in terms of grinding efficiency and in capital efficiency through incremental throughput) are well SAG Mill Grinding Circuit Design 911Metallurgist2017年1月17日 Grinding mills are infamous for their extremely low energy efficiency It is generally accepted that the energy required to produce new mineral surfaces is less than 1% of the electricity consumed Breaking down energy consumption in industrial
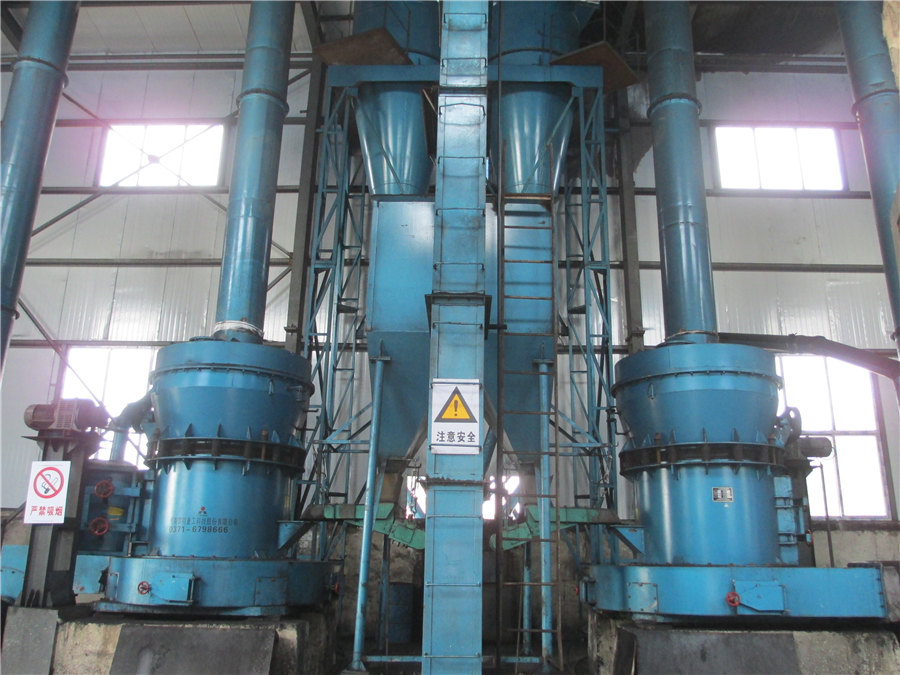
Physical Bauxite Processing: Crushing and Grinding of Bauxite
2022年1月23日 Additionally, when the downstream process involved grinding mills, the fines created from highspeed crushing circuit were a benefit to the comminution process In general, if the feed material, application parameters, and downstream process match with the capabilities of a highspeed impact style crusher, this is the crusher type to use2023年1月1日 In the metal mining industry, comminution regularly involves crushing and grinding and is widely acknowledged as the process consuming the most energy, accounting for up to 75 % of the energy consumed by a processing plant (Tromans, 2008)Crushing is shown to be more energyefficient than grinding in the comminution processing chain; however, the Evaluating the performance of an industrialscale high 2024年4月21日 Guide to Modern Smelting Processes – T09002 7 Use of Retorts in Ancient Smelting Processes Figure 2 Ancient Retort An ancient retort (see image above), used in ancient smelting processes, served several important purposes: 1 Ore Concentration: Retorts were used to concentrate the desired metal from ore TheGuide to Modern Smelting Processes CED Engineering2023年7月27日 Rod grinding process is an ore grinding method which uses a long round metal rod as the grinding medium in a mill to smash the ore In the rod grinding process, when the rod medium moves in the barrel of the ore mill, there is a line contact between them the rod milling process can replace the shorthead cone crusher for fine crushing and Rod Grinding Process SpringerLink
.jpg)
How to Calculate Grinding Mill Operating Efficiency
2017年9月13日 When accurate mill ore feed rate in dry tons per hour, mill power draw in kilowatts, and mill feed and product size analyses in microns are available the Bond Equation can be used to measure the operation of comminution machines, reporting it as operating work index2023年12月26日 Grinding mills are infamous for their extremely low energy efficiency It is generally accepted that the energy required to produce new mineral surfaces is less than 1% of the electricity consumed toBREAKING DOWN ENERGY CONSUMPTION IN 2023年4月23日 Ball mills use various grinding media to grind the ore inside them into finer products Spherical balls a re mostly used for ball mill processes, and they change their shape with time due t o the (PDF) Grinding Media in Ball MillsA Review ResearchGate2016年11月22日 Grinding efficiency is one of the most important considerations in the selection of grinding operation conditions because it has a significant impact on the productivity, quality, energy consumption and cost Focusing on the core issues of grinding process, the paper presents some fundamental research findings in relation to grinding material Effect of different parameters on grinding efficiency and its
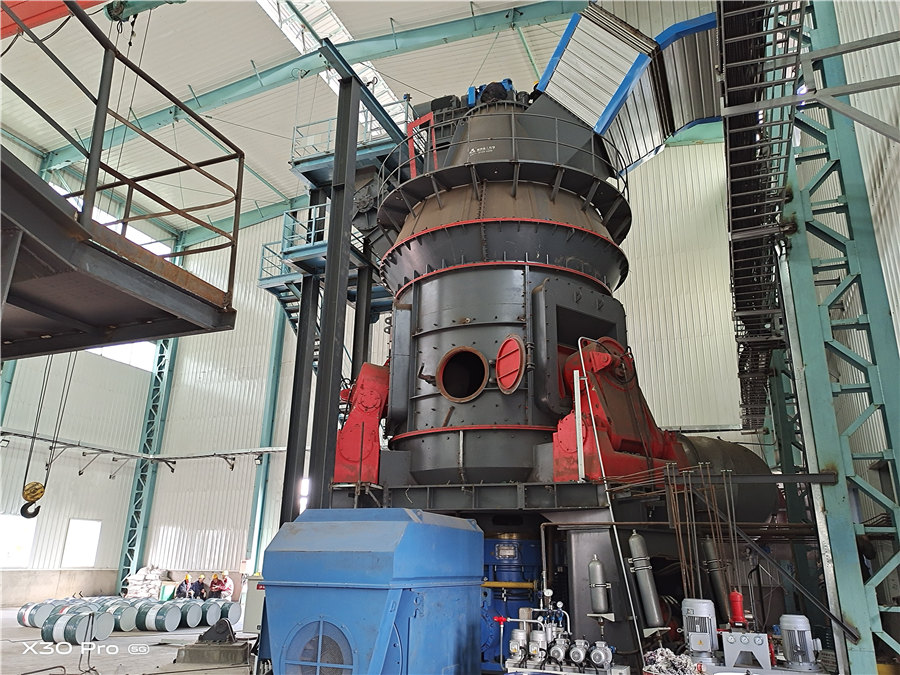
Grinding Modeling and Energy Efficiency in
2022年8月31日 The grinding process, as a primary stage of ore/raw material processing, is a necessary operation in beneficiation plants welcomes papers that highlight innovations and future trends in modeling grinding and 2013年12月18日 Fine grinding, to P80 sizes as low as 7 μm, is becoming increasingly important as mines treat ores with smaller liberation sizes This grinding is typically done using stirred mills such as the Isamill or Stirred Energy Use of Fine Grinding in Mineral Processing2024年10月13日 The rods, which are typically made of steel, crush the ore as they rotate within the mill Rod mills are often used for coarser grinding and are less efficient than ball mills Autogenous Mills and SemiAutogenous Mills: Autogenous mills use the ore itself as the grinding media, while semiautogenous mills use a combination of ore and steel ballsUnderstanding the operation of grinding mills in the mining 2019年10月8日 The rod mill is developed on the basis of the ball mill It has the advantages of reliable processing technology, low investment, less auxiliary equipment and simple process flow It can be combined with the ball mill to form a different grinding process The rod mill mainly grinds the ore by the pressure and the grinding force of the grinding rodCrushing and Grinding Process JXSC Machine

(PDF) Grinding in Ball Mills: Modeling and Process Control
2012年6月1日 The paper presents an overview of the current methodology and practice in modeling and control of the grinding process in industrial ball mills Basic kinetic and energy models of the grinding 2020年2月1日 Like the HallHéroult process, the overall principles behind the Bayer process of refining bauxite has not changed drastically since its conception However, different equipment has been developed and introduced over the years to increase energy and process efficiency and also to increase alumina recovery [139] There are various practises The aluminium industry: A review on stateoftheart 2024年9月30日 Lithium (Li), a leading cathode material in rechargeable Liion batteries, is vital to modern energy storage technology, establishing it as one of the most impactful and strategical elements Given the surge in the electric car market, it is crucial to improve lithium recovery from its rich mineral deposits using the most effective extraction technique In recent years, both Aspects of Spodumene Lithium Extraction Techniques MDPI2022年10月4日 A notable fact is that the energy efficiency of conventional milling is only about 1%, as mentioned in Sect 1 An earlier experimental study indicated that about 80–90% of the energy input of a ball mill was used in heating the material (Schellinger 1951, 1952), and a recent study showed that over 75% of the electrical energy was used to heat the slurry (Bouchard et Reduction of Fragment Size from Mining to Mineral
.jpg)
Implementing strategies to improve mill capacity and
2011年3月3日 Early mineral processing techniques employed the use of grinding mills as the first phases of liberating and isolating desirable minerals from gangue In the early phases it was also recognized that some form of size classification associated with the grinding mill would allow for more efficient operation of these grinding mills We will look at2022年2月28日 Generally, grinding process efficiency can mainly be improved by either improving the grinding behavior of the material being ground or enhancing the grinding machines Recently, the use of additives socalled grinding aids, which is applied in a small amount of 001–025 wt% related to the mass of product, has reduced these problems and been Grinding SpringerLink