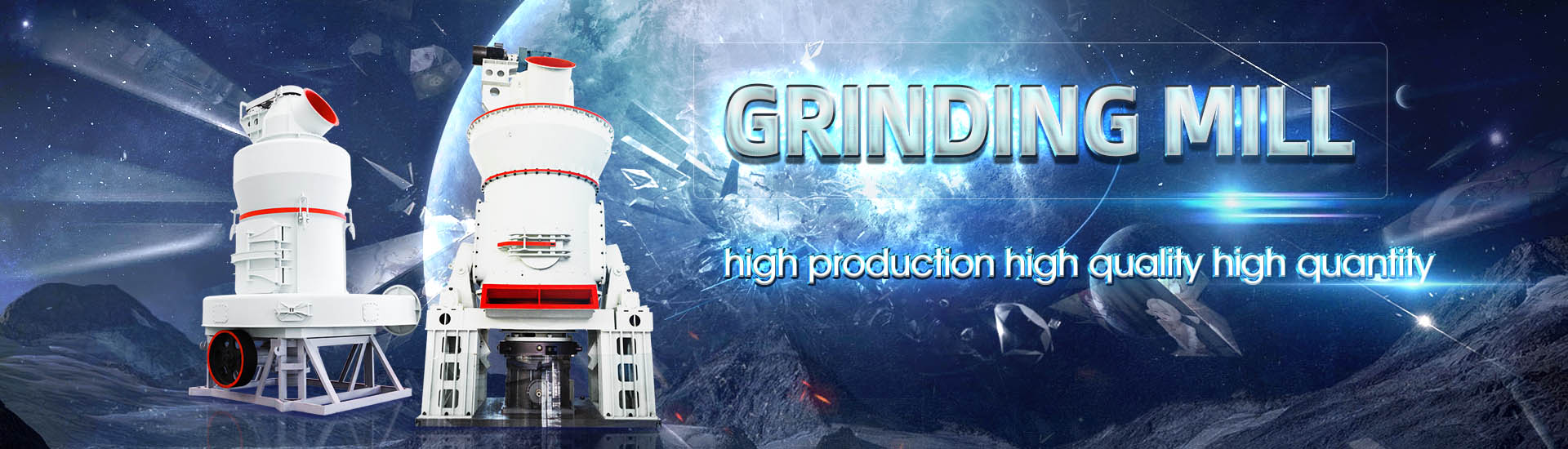
Detailed parameters of ore grinding mill
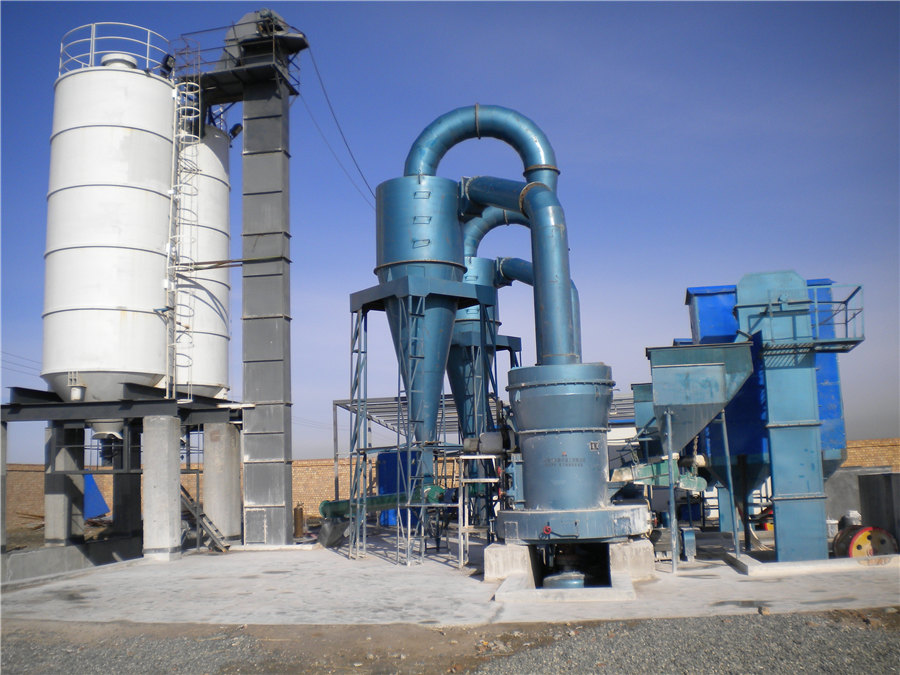
Ore Grinding SpringerLink
2023年7月20日 Grinding operation quality indices mainly include four aspects (1) Grinding fineness, which is the percentage of the ore particles less than pecified size after being grounded and discharged (2) Mill operation rate, which is the percentage of the actual working time of 2023年7月31日 operation (1) Structure parameters of grinding mill, including its specifications, model, aspect ratio, ore discharging method, and liner form (2) Various working parameters of Ore Grinding Methods and Process of Ore Grinding2020年7月23日 Four significant operating variables stirrer speed, grinding time, feed size, and solids concentration were investigated for their effect on the performance of stirred mills The Optimization of stirred mill parameters for fine grinding of 2023年9月1日 Based on the machine learning method, this study analyzed the full process parameters (ie, ball mill power, fresh ore feed rate, hydrocyclone feed pump power, Analyzing process parameters for industrial grinding circuit
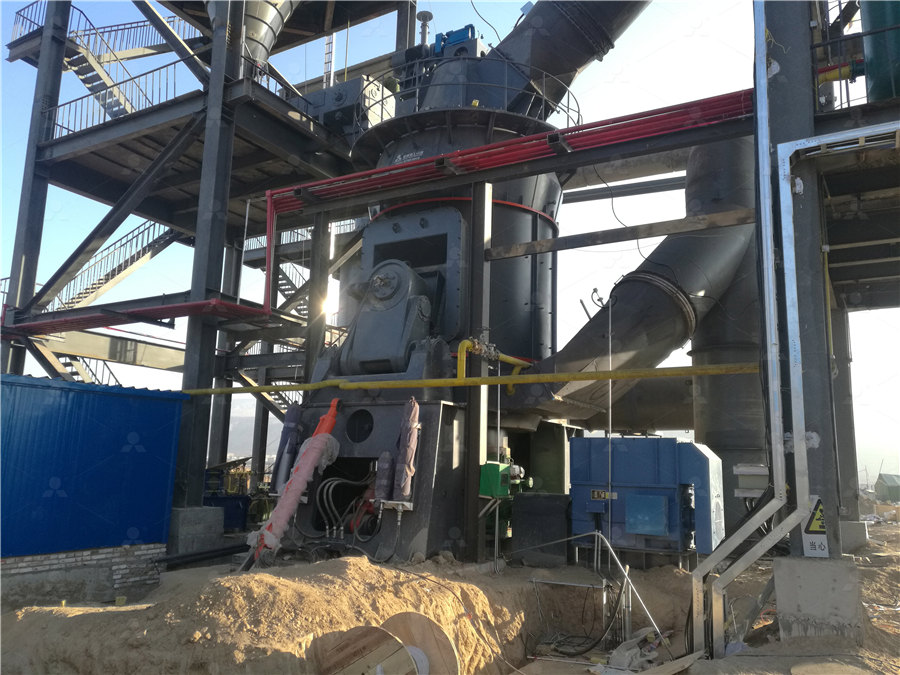
Optimization and Experimental Study of Iron Ore Grinding
2024年9月26日 This study investigated the effect of grinding medium density (38 g/cm 3, 58 g/cm 3, and 78 g/cm 3) on the grinding of iron ore in a laboratory scale ball mill, focusing on 2022年6月1日 In this study, a classical perturbationbased method, a timevarying parameter estimationbased method and the Nelder–Mead simplex method are employed as extremum Extremum seeking control for optimization of an openloop grinding mill 2021年7月1日 Several variables are known to influence the performance of gravityinduced stirred mills, including grinding media characteristics, stirrer geometry and speed, mill Predicting the effect of operating and design variables in grinding 2024年1月1日 The main parameters of grinding and classification process include measurement of millfeeding quantity, mill load measurement, measurement of ore slurry density, Online Measurement and Control for Ore Grinding and Classification
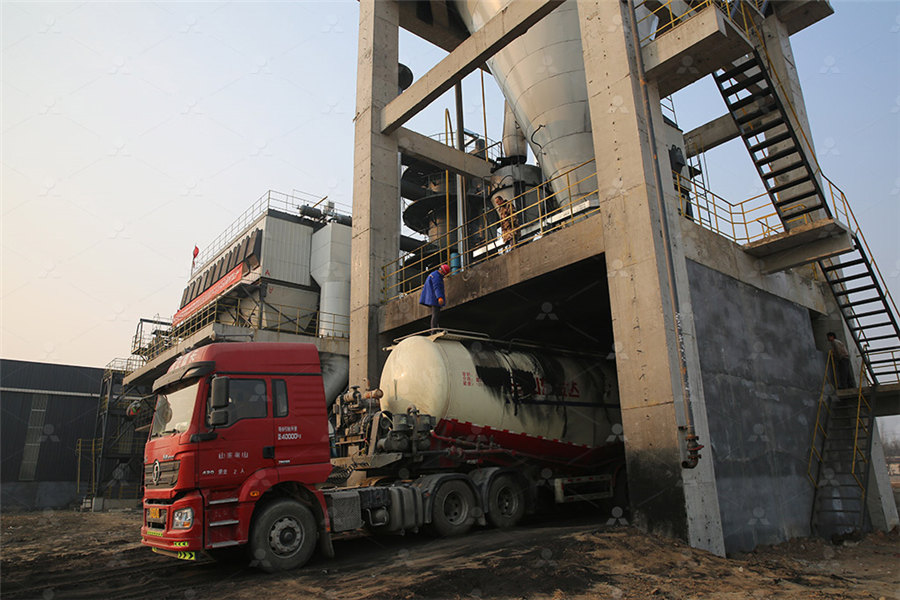
Research on Grinding Law and Grinding
2022年10月13日 Through this study, the best grinding parameters of complex polymetallic ores are obtained to reduce cassiterite overgrinding and sulfide ore undergrinding, so as to save energy consumption in the grinding process of Abstract: A nonlinear phenomenological model of a grinding mill is used to determine five runofmine (ROM) grinding milling circuit parameters The five parameters are fraction of fines and Identifiability of runofmine ore grinding mill circuit parameters 2022年6月1日 The grinding mill can be optimized without the need for a detailed process model The aim of the grinding mill is to grind the ore to below a specification size, several strategies demonstrate the application of the ESCs for optimizing grinding mill performance The parameters used to simulate the model described in Extremum seeking control for optimization of an openloop grinding mill 2020年7月23日 Optimization of stirred mill parameters for fine grinding of PGE bearing chromite ore, Particulate Science and Technology, DOI: 101080/2020 To link to this article: https://doi Optimization of stirred mill parameters for fine
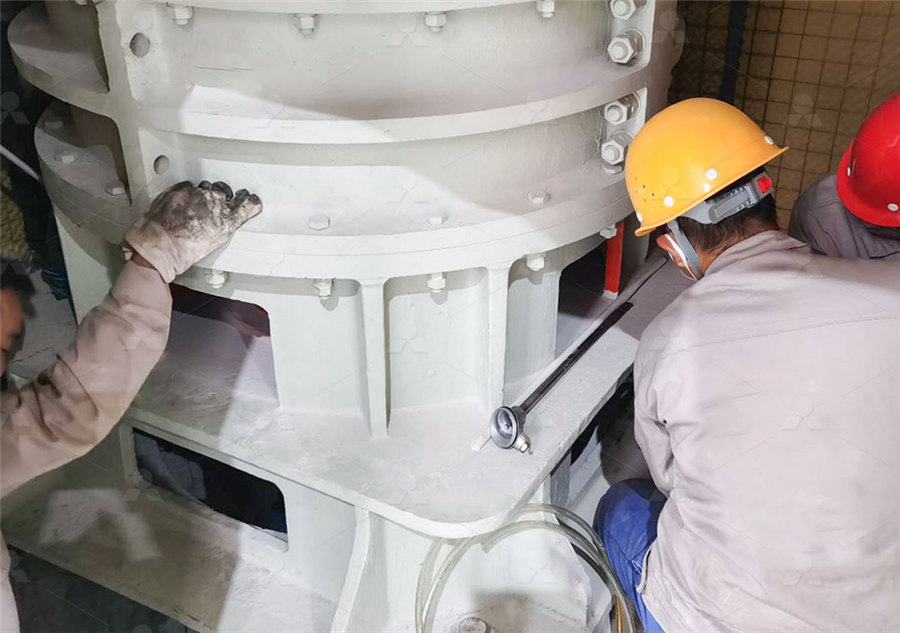
Relationship among operational parameters, ore characteristics, and
2019年2月11日 A detailed test work was carried out with an industrial semiautogenous (SAG) mill in a copper plant in close and open circuits to specify the effects of ore characteristics and operational 2016年6月6日 These mills typically grind ROM ore in a single stage A large example of such a mill was converted from a singlestage milling application to a semi autogenous ballmillcrushing and other aspects of detailed design (including steadystate tests, simulation, and experience), an arbitrary power split between circuits ignores the critical SAG Mill Grinding Circuit Design 911Metallurgist2013年4月16日 ABSTRACT In this study, ultrafine grinding of a refractory silver ore tailings was studied A laboratory scale pintype vertical stirred mill and ceramic beads were employed for the grinding testsInvestigation of some parameters affecting the Ultrafine grinding 2022年7月27日 cessing industry are ball and semiautogenous (SAG) mills, which use both ore and steel balls as grinding media (Wei and Craig, 2009b) In the case of a ball mill the ore is crushed before it enters the mill, whereas a SAG mill receives runofmine (ROM) ore directly (Stanley, 1987) A SAG mill in a singlestage closed circuit con guration, asAnalysis and validation of a runofmine ore grinding
.jpg)
Optimization and Experimental Study of Iron Ore Grinding
2024年9月26日 Energy savings and consumption reduction of ball mills are crucial for industrial production The grinding medium is an important component of a ball mill2017年1月1日 In this investigation, we optimize the grinding circuit of a typical chromite beneficiation plant in India The runofmine ore is reduced to a particle size of less than 1 mm in the comminution (PDF) Performance optimization of an industrial ball mill for 2024年10月13日 Autogenous mills use the ore itself as the grinding media, while semiautogenous mills use a combination of ore and steel balls These mills operate by rotating a large drum filled with the ore, which impacts and grinds the particles against the mill walls Autogenous and semiautogenous mills are more energyefficient and are suitable for fine Understanding the operation of grinding mills in the mining A crushing plant delivered ore to a wet grinding mill for further size reduction The size of crushed ore (F 80) was 40 mm and the SG 28 t/m 3 The work index of the ore was determined as 122 kWh/t A wet ball mill 1 m × 1 m was chosen to grind the ore down to 200 micronsGrinding Mill an overview ScienceDirect Topics
.jpg)
Population balance model approach to ball mill
2024年1月2日 scale mill can be optimized via laboratory scale grinding mill tests The present work demonstrates the application of the population balance model approach to optimizing ball milling in iron ore 2023年5月9日 MILL OPTIMIZATION IN IRON ORE GRINDING* Patrícia Mundim Campos Faria1 Luís Marcelo Tavares 2 Raj K Rajamani 3 Several studies have been carried out in the development of detailed phenomenological grinding models derived from population balance considerations [2,3] N is the mixing parameter which gives the equivalent number POPULATION BALANCE MODEL APPROACH TO BALL 2020年10月9日 In order to obtain the optimal operation parameters of a SAG mill, in this paper, the discrete element method (DEM) is used to simulate the breakage process of the particles by controlling three Operation Analysis of a SAG Mill under Different 2020年7月23日 Abstract The depletion of highgrade ores has forced the utilization of lowgrade ores The small liberation sizes in the lowgrade ores require fine grinding which is an energy intensive operation In the present study, lowgrade chromite ore bearing platinum group of elements (PGE) was used as an experimental material The previous study concluded the Optimization of stirred mill parameters for fine grinding of
.jpg)
Analysis and validation of a runofmine ore grinding mill circuit
2013年4月1日 Two types of mills commonly found in the minerals processing industry are ball and semiautogenous (SAG) mills, which use both ore and steel balls as grinding media (Wei and Craig, 2009b) In the case of a ball mill the ore is crushed before it enters the mill, whereas a SAG mill receives runofmine (ROM) ore directly (Stanley, 1987)2023年12月12日 In addition, the ore properties are one of the important parameters for the optimal utilizing of the ball mill Ore can have various properties, such as hardness, density, moisture content, etc (PDF) Control of ball mill operation depending on ball load and ore 2015年3月15日 The results show that the optimum process parameters for the vertical roller mill are as follows: a grinding fineness of 816wt% of particles less than 0074 mm, a dodecyl amine (DDA) dosage in Research of iron ore grinding in a verticalrollermill2023年7月31日 operation (1) Structure parameters of grinding mill, including its specifications, model, aspect ratio, ore discharging method, and liner form (2) Various working parameters of grinding mill, including fraction of critical speed for grinding mill, filling rate for grinding mill, grinding concentration,grindingcycleload,etc(3)AndgrindOre Grinding Methods and Process of Ore Grinding
制粉-10.25公众号.jpg)
Rethinking Grinding Efficiency in Ball Mills RELO
2021年5月8日 Kolev et al (2021) –In press Improving the energy efficiency in tumbling mills with the use of Relo grinding media (MDPI) • Lab trials conducted using a standard Bond ball mill (@ Wardell Armstrong) • Standard Bond ball mill procedures were followed –only the RELO media PSD and mass of charge adjusted to match spherical media2021年7月1日 The influence of ore shape on grinding process in SAG mill is explored Abstract In the ore milling process, the ore particles are usually irregular polyhedrons, and the grinding media are often spherical More detailed parameters about the device and simulation can be found in Table 2 After all the particles are randomly generated and DEM investigation of SAG mill with spherical grinding media 2014年10月20日 Initially, detailed experimentation was carried out in a 254 cm diameter batch mill and a relationship for mill scaleup using a linear population balance model in wet grinding systems was Population balance model approach to ball mill 2018年10月1日 The impact of ore variability on process performance was observed at the OK Tedi mine in Papua New Guinea, where the variations in feed ore hardness (Bond work index 5–16 kWh/t) and in feed size distributions caused the SAG mill throughput to fluctuate between 700 and 3000 t/h (Sloan et al, 2001)Quantifying variability of ore breakage by impact – Implications
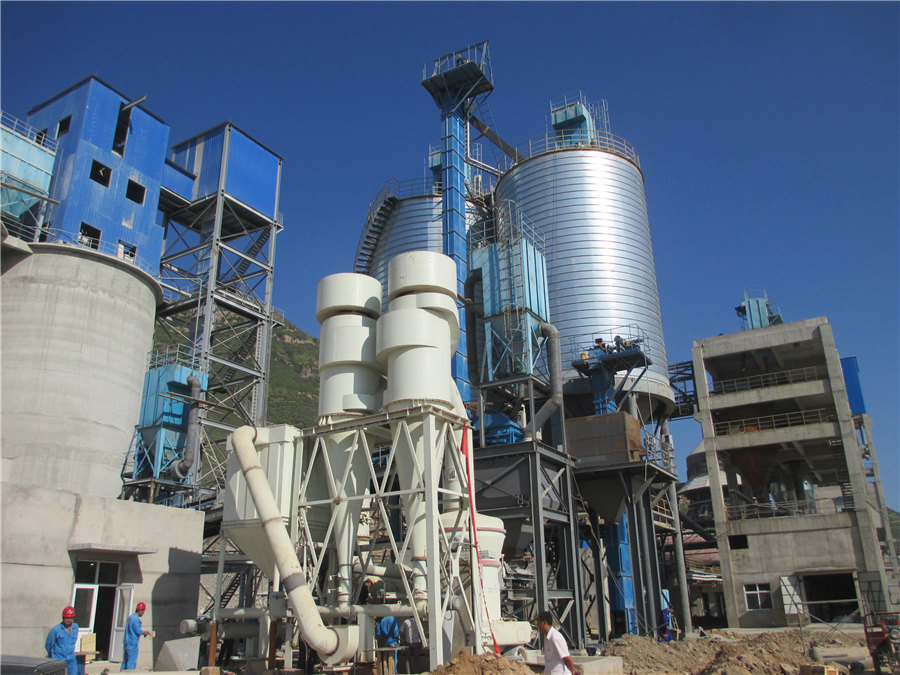
(PDF) Grinding in Ball Mills: Modeling and Process Control
2012年6月1日 As the cylinder starts to rotate, the grinding balls inside the cylinder crush and grind the feed material, generating mechanical energy that aids in breaking bonds, activating the catalyst, and 2023年7月1日 Fig 22 depicts that the magnitude of “a” parameter varies for each ball mill This can be attributed to the variation in the mill diameter, grinding ball size and solid contents Consequently, it is viable to normalize K parameter by taking these parameters into considerationElement based ball mill and hydrocyclone modelling for a copper ore 2021年7月12日 the unknown ore grinding product PSD is calculated by a firstorder kinetics equation 100% under 335 mm, in a Bond ball mill for 5 min The kinetic parameters are determined: k by Equation A Review of Alternative Procedures to the Bond Ball Mill 2023年4月23日 grinding media in a grinding mill with about 2630 wt% chrome by Chen et al [37] using a phosphate ore in a modified ball laboratory ball mill whose electrochemical potential could be controlled(PDF) Grinding Media in Ball MillsA Review ResearchGate
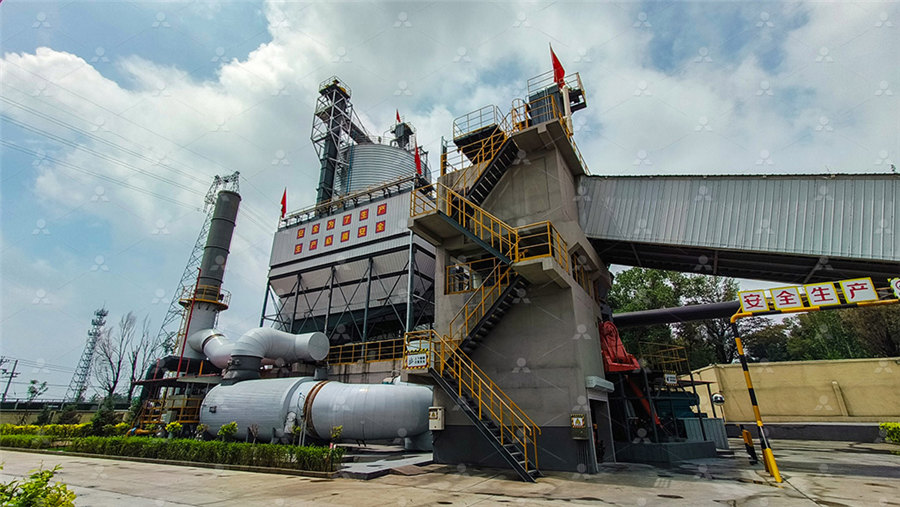
Analysis and validation of a runofmine ore grinding
2022年7月27日 cessing industry are ball and semiautogenous (SAG) mills, which use both ore and steel balls as grinding media (Wei and Craig, 2009b) In the case of a ball mill the ore is crushed before it enters the mill, whereas a SAG mill receives runofmine (ROM) ore directly (Stanley, 1987) A SAG mill in a singlestage closed circuit con guration, asThis ratio is mainly affected by the mineralogical properties of the ore In the same grinding period, reducing charge ratio resulted in the coarser products (RSM) can be successfully used for the determination of stirred mill parameters on ultrafine grinding of refractory Au/Ag ores 126 O Celep et al / Powder Technology 208 (2011 Optimization of some parameters of stirred mill for ultrafine grinding 2021年11月3日 Phosphate mineral powder grinding mills includes ultrafine mills, vertical roller mills, highpressure mills, etc can grind ores into a fine powder At present, for the field of nonmetallic ore, there are ultrafine grinding mills, micropulverizers, superfine vertical roller mills, wet mills, and other industrial ore grinding equipment Phosphate Mineral Powder Grinding Mill SBM Ultrafine 2018年8月8日 The paper presents a study on the effectiveness of the grinding process in an electromagnetic mill devoted to ultrafine grinding, and the influence of processing parameters on the mill’s (PDF) Grinding Kinetics Adjustment of Copper Ore Grinding
.jpg)
Extremum seeking control for optimization of an openloop grinding mill
2022年6月1日 The grinding mill can be optimized without the need for a detailed process model The aim of the grinding mill is to grind the ore to below a specification size, several strategies demonstrate the application of the ESCs for optimizing grinding mill performance The parameters used to simulate the model described in 2020年7月23日 Optimization of stirred mill parameters for fine grinding of PGE bearing chromite ore, Particulate Science and Technology, DOI: 101080/2020 To link to this article: https://doi Optimization of stirred mill parameters for fine 2019年2月11日 A detailed test work was carried out with an industrial semiautogenous (SAG) mill in a copper plant in close and open circuits to specify the effects of ore characteristics and operational Relationship among operational parameters, ore characteristics, and 2016年6月6日 These mills typically grind ROM ore in a single stage A large example of such a mill was converted from a singlestage milling application to a semi autogenous ballmillcrushing and other aspects of detailed design (including steadystate tests, simulation, and experience), an arbitrary power split between circuits ignores the critical SAG Mill Grinding Circuit Design 911Metallurgist
.jpg)
Investigation of some parameters affecting the Ultrafine grinding
2013年4月16日 ABSTRACT In this study, ultrafine grinding of a refractory silver ore tailings was studied A laboratory scale pintype vertical stirred mill and ceramic beads were employed for the grinding tests2022年7月27日 cessing industry are ball and semiautogenous (SAG) mills, which use both ore and steel balls as grinding media (Wei and Craig, 2009b) In the case of a ball mill the ore is crushed before it enters the mill, whereas a SAG mill receives runofmine (ROM) ore directly (Stanley, 1987) A SAG mill in a singlestage closed circuit con guration, asAnalysis and validation of a runofmine ore grinding 2024年9月26日 Energy savings and consumption reduction of ball mills are crucial for industrial production The grinding medium is an important component of a ball millOptimization and Experimental Study of Iron Ore Grinding 2017年1月1日 In this investigation, we optimize the grinding circuit of a typical chromite beneficiation plant in India The runofmine ore is reduced to a particle size of less than 1 mm in the comminution (PDF) Performance optimization of an industrial ball mill for
.jpg)
Understanding the operation of grinding mills in the mining
2024年10月13日 Autogenous mills use the ore itself as the grinding media, while semiautogenous mills use a combination of ore and steel balls These mills operate by rotating a large drum filled with the ore, which impacts and grinds the particles against the mill walls Autogenous and semiautogenous mills are more energyefficient and are suitable for fine A crushing plant delivered ore to a wet grinding mill for further size reduction The size of crushed ore (F 80) was 40 mm and the SG 28 t/m 3 The work index of the ore was determined as 122 kWh/t A wet ball mill 1 m × 1 m was chosen to grind the ore down to 200 micronsGrinding Mill an overview ScienceDirect Topics