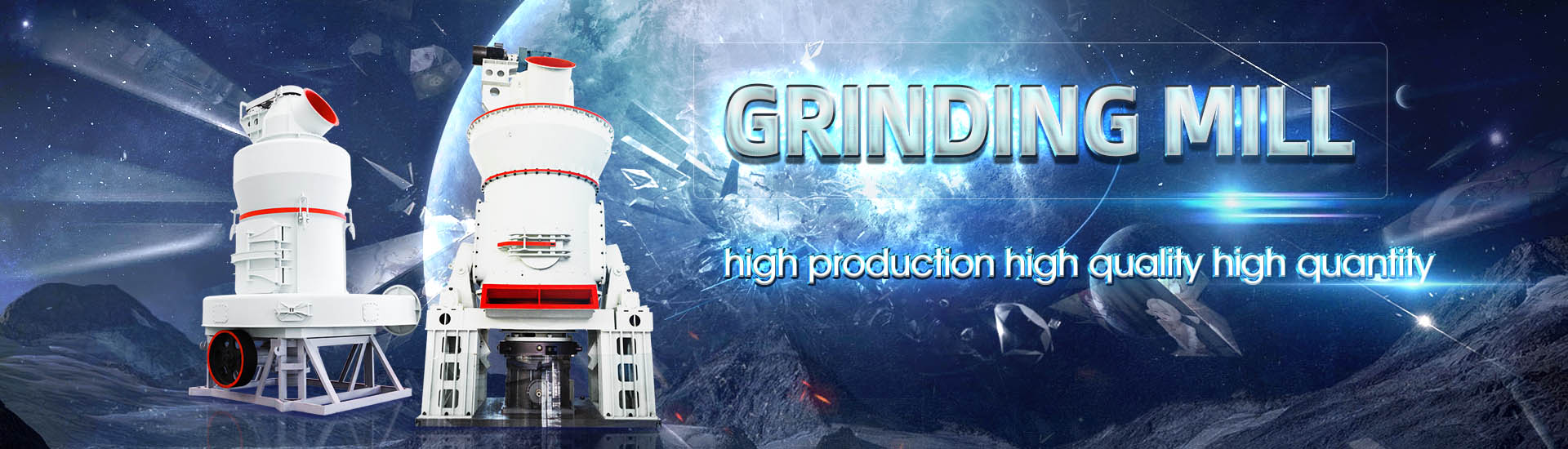
Operational procedures for secondary crushing of large ores
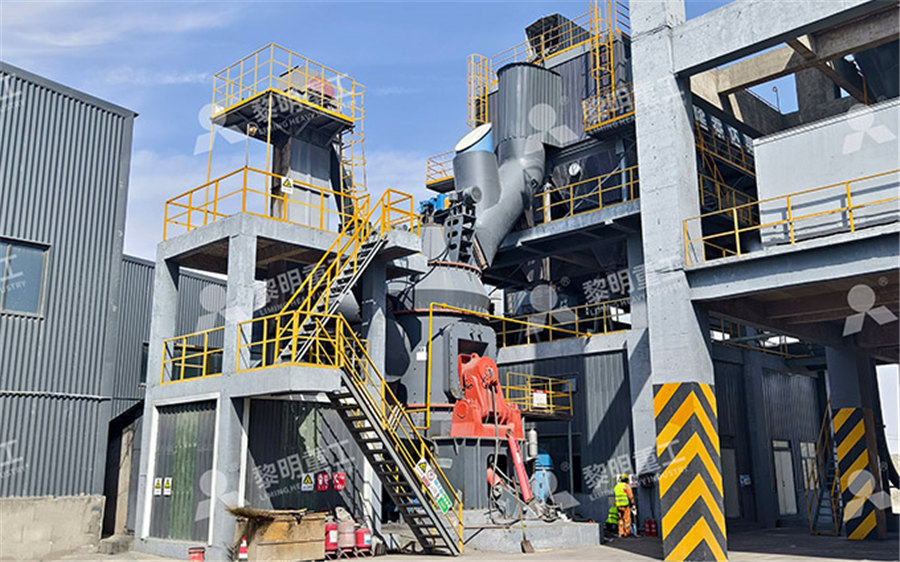
COMPARISON OF SECONDARY CRUSHING OPERATIONS
2024年1月18日 zontal (HSI) shaft impact crushers are conventionally preferred for secondary and tertiary crushing processes P imary crushing operations could be declared as the main size reduction2020年9月20日 The 2S crushing consisted of primary and secondary crushers as Jaw and HSI (horizontal shaft impactor), respectively, while 3S crushing was composed of primary, secondary and tertiary(PDF) COMPARISON OF SECONDARY CRUSHING 2024年9月24日 There are three main steps in designing a good crushing plant: process design, equipment selection, and layout The first two are dictated by production requirements and Crushing Plant Design and Layout Considerations 911 2020年6月4日 The size reduction process of rocks in cone crushers is one of the most important issues, particularly for the secondary and tertiary stages of crushing operations In this study, Evaluation of size reduction process for rock aggregates in
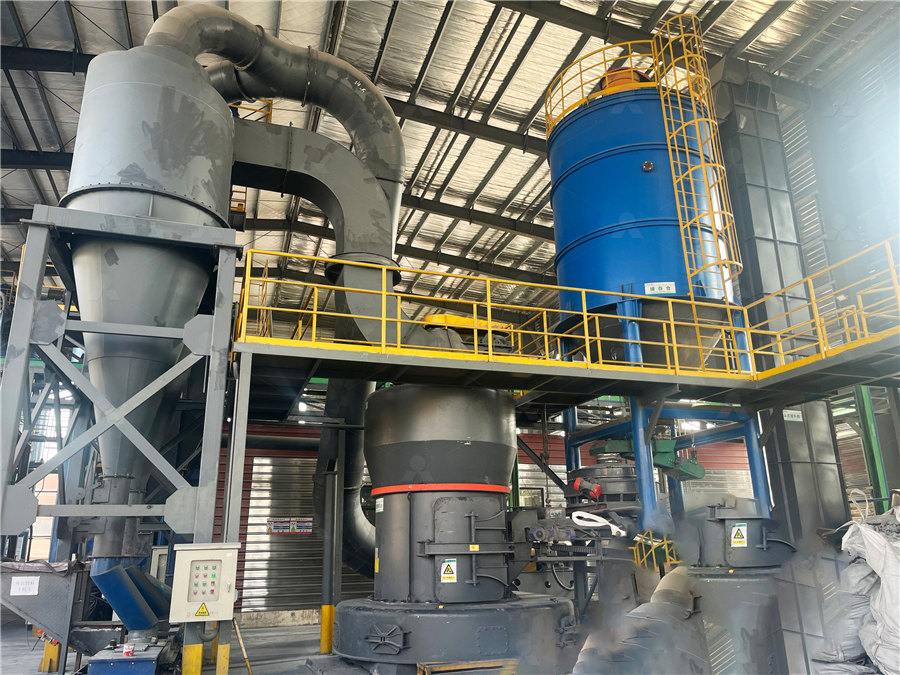
Crushed ore agglomeration and its control for heap leach operations
2013年2月1日 Based on the extensive experience of heap leaching operations, crushed ore agglomeration can be successfully considered and utilized as a pretreatment step for the heap 2021年8月15日 Comminution is an important unit operation of the mineral processing chain that involves rock blasting and mechanical comminution (crushing and grinding) The goal is to A review of modeling and control strategies for cone crushers 2017年3月4日 In the field of extractive metallurgy, mineral dressing is the process of separating commercially valuable minerals from their ores There are two major categories of processing One is(PDF) SIZE REDUCTION BY CRUSHING Detail descriptions of designs are given of large gyratory crushers that are used as primary crushers to reduce the size of large runofmine ore pieces to acceptable sizes Descriptions of Mineral Processing Design and Operations ScienceDirect
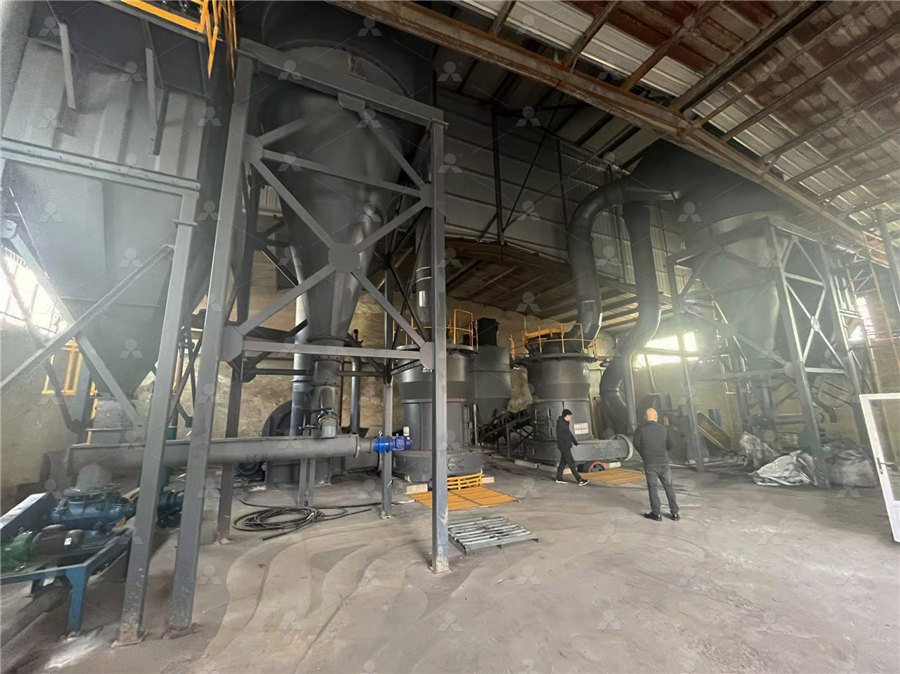
Crushing Explained Gold Rock Projects
In the mining and minerals industry, crushing is a crucial process for breaking down large ore chunks into smaller, manageable sizes The primary and secondary crushing stages are 2020年6月4日 The size reduction process of rocks in cone crushers is one of the most important issues, particularly for the secondary and tertiary stages of crushing operations In this study, 17 different rock types were considered for the evaluation of their size reduction variations that occurred in a laboratoryscale cone crusher Based on several mineralogical, physico Evaluation of size reduction process for rock aggregates in 2022年4月26日 The optimization capabilities for crushing plants comprise a system solution with the twofold application of 1) Utilizing the simulation platform for identification and exploration of operational (PDF) Optimization Capabilities for Crushing 2023年2月28日 The primary crusher is used to reduce the size of large rocks and stones, while the secondary crusher further breaks them down into smaller pieces the mechanical principles involved in their operation, and the Primary Crusher vs Secondary Crusher:
.jpg)
Types of Crushers: Choosing the Right One for Each Stage
2024年7月17日 Crushing is a multistage process that includes primary crushing, secondary crushing, and tertiary crushing Different types of crushing equipment are used at each stage to meet various crushing requirements Primary crushing breaks down large raw materials into mediumsized pieces for easier handling in subsequent processes2021年8月15日 Several works from the literature have reported applications of process control strategies in the mineral processing industry For example, Wei and Craig (2009) published a survey with qualitative data from process control solutions, and Bouffard (2015) reported quantitative data supporting the benefits of such strategies A series of works (Bouchard et al, A review of modeling and control strategies for cone crushers 2013年2月1日 Crushed ore agglomeration as a pretreatment step for heap leaching is reviewed The acceptance of binder is limited due to the lack of acidtolerant binders Concise overviews of quality control and characterization tools are provided Different agglomerationheap leaching systems are summarized HPGR grindingagglomeration may have some advantagesCrushed ore agglomeration and its control for heap leach operations2024年2月6日 All types, gold, copper, large quartz rocks: Efficient crushing of largesized hard ores: Double Toggle: Hard and abrasive, iron ore, chromite, diamondbearing rock: Powerful crushing action for very hard and abrasive ores: Hydraulic: Varied, nickel, tin, and various hard ores; sticky clay ores: Adjustable and precise, good for ores requiring Understanding Types of Jaw Crusher: A Comprehensive
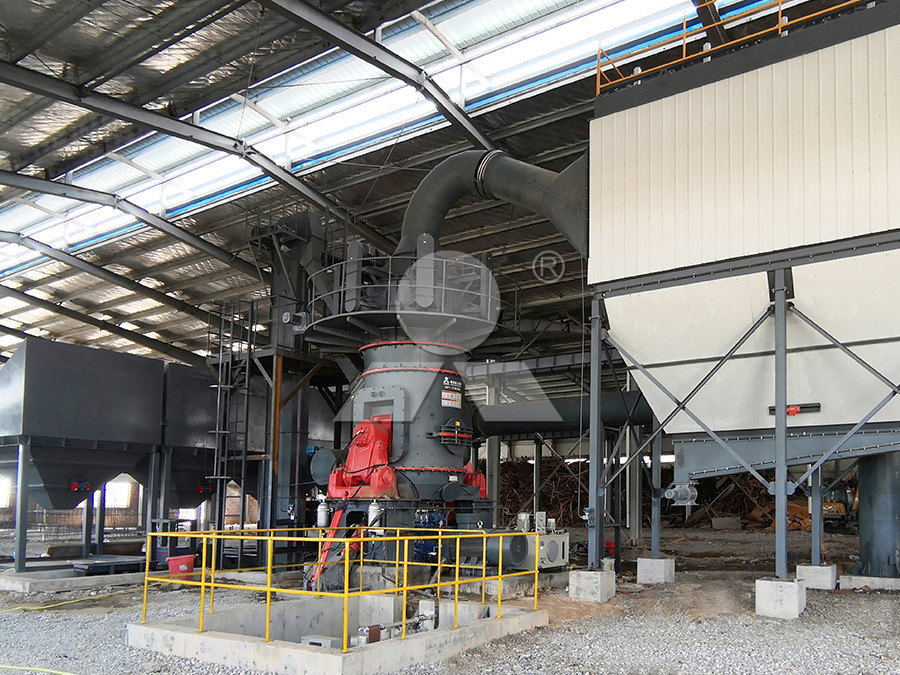
(PDF) Variability Study of Bond Work Index and Grindability Index
2021年6月17日 It is a wellknown fact that the value of the Bond work index (wi) for a given ore varies along with the grinding size In this study, a variability bysis is carried out with the Bond standard 2020年8月6日 Leaching of copper from a Jordanian copper ore has been studied using a stirred batch reactor with hydrochloric acid as the main lixiviant, under the following conditions: temperature 25 – 45 oC Leaching of Copper Ores: Effects of Operating Variables2023年12月1日 All operations in size reduction, both crushing and grinding are of course determined by the feed characteristics of the minerals (rock/ore) moving into the circuit The key parameters we need are theSIZE REDUCTION BY CRUSHING METHODS By2021年9月8日 ores containing a low concentration of copper in the ore (oxide, mixed ores, and secondary sulfide ores) can be affected by the leaching of ground ore followed by solvent extraction and electrowinning This technology is applied in a number of large copper productions, including Escondida (Chile), CollahuasiCurrent Status of CopperOre Processing: A Review
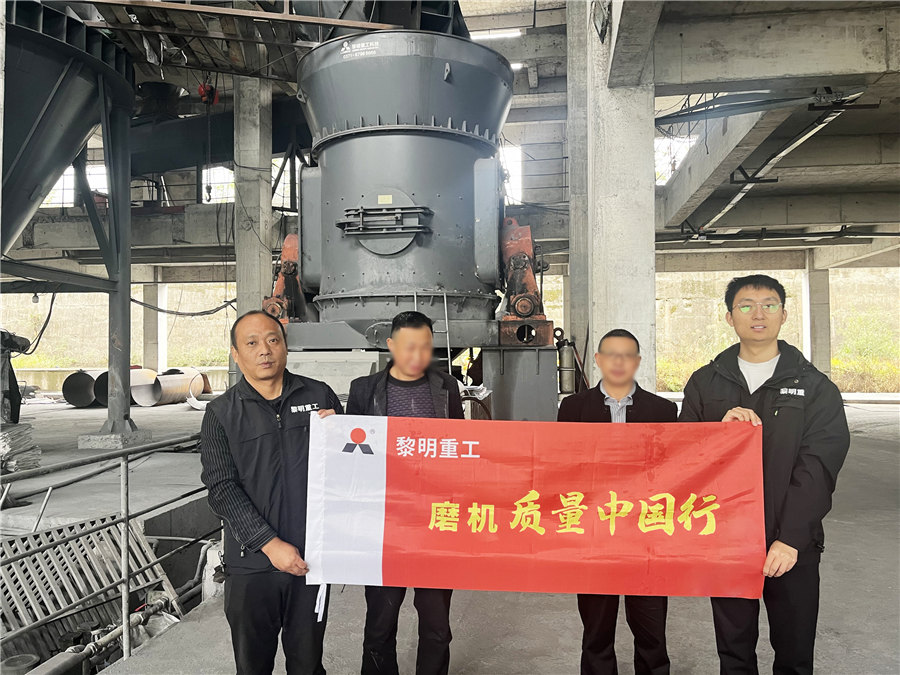
LECTURE NOTES ON MINERAL DRESSING OSME
2024年3月5日 So mineral dressing or ore dressing is commonly regarded as processing of raw ores to Intermediate crushing or secondary crushing: The feed material is usually product of a jaw crusher 3 Fine crushing or coarse grinding: The feed material is usually comes from the secondary Crushing is a mechanical operation in which a force of large SECONDARY CRUSHING OVERVIEW Secondary crushing of the SAG mill feed, when implemented correctly, has been shown to significantly reduce SAG mill and total circuit specific energy Very fine feed, good process control and or the presence of some coarse rock in the feed (partial secondary crushing) has been required to make a successful projectSHEDDING LIGHT ON SECONDARY CRUSHING B Putland,2014年1月1日 In mining operations, the layout of crushing plants and ancillary equipment and structures is a crucial factor in meeting production requirements while keeping capital and operational costs to a Factors affecting the performance of crushing plant operations2021年9月8日 Abstract An analysis of flowsheets for processing sulfide and oxide copper ores, reagent modes, processing equipment, and flotation indicators in some domestic and foreign processing plants and productions is carried out Autogenous and semiautogenous mills are commonly used in the primary grinding stage in ore processing plants, which excludes Current Status of CopperOre Processing: A Review
.jpg)
Rock Crushing Process in Mining 911Metallurgist
2015年7月18日 secondary crushing is the second, Tertiary crushing is the third, Quaternary crushing is a rare forth stage of rock crushing, Coarse crushing includes crushing operations discharging at sizes 4 to 6in or coarser; intermediate crushing comprises operations taking feeds 6 or 8in maximum and making products down to 1/2″ or 3/8″2 All crushers have a limited reduction ratio meaning that size reduction will take place in stages 32 Operation stages: The operating stages in minerals processing have remained the same for SIZE REDUCTION BY CRUSHING METHODS By2022年4月1日 Mineral processing operations generally follow a set of specific steps to separate ores into products rich in valuable minerals (concentrate) and waste streams The breakdown of the mineral processing steps within the mining chain is illustrated in Fig 3 Run of mine ore undergoes an initial process of crushing, milling and classification to Review on advances in mineral processing technologies 2023年1月1日 India is endowed with large resources of iron ore, Primary and secondary crushing was done by gyratory crushers For sticky iron ores with a high clay content, primary and secondary sizers were also used instead of gyratory crushers The capital and operational costs of crushing and grinding processes are substantial Hence, economics Iron ore beneficiation: an overview ScienceDirect
.jpg)
Field monitoring and performance evaluation of crushing plant operation
Crushing plants are of great interest in reducing a particle size of rocks and ores as milling operations need to consider sustainable development Since the crushing plants operate under harsh conditions and involve very abrasive material, multiple Grinding consumes large amount of energy, therefore effective 622 E Yilmaz carrying out of 2023年10月30日 The selection and design of crushing equipment in the mineral processing industry are influenced by several key factors, all of which are critical for achieving efficient and effective ore processing Chief among these factors is the material's inherent characteristics The hardness, abrasiveness, moisture content, and size distribution of the ore significantly impact The selection and design of Crushing equipmentThe current crushing setup is operating at 15 tonnes per hour which is low compared to their production rate such that ore from the ground is piling up Crushing reduces the physical size of large rocks, exposing more surface area of rock, thus exposing any gold that may be in the rock and increasing the probability of obtaining the gold Design of a crushing system that improves the crushing 2024年7月26日 Table 1 – Summary of Grindability Test Procedures 1Weight requested for the test, for typical ores (SG = 28g/cm3) Denser samples require more weight, proportional to the SG 2Approximate weight consumed in the test for typical ores (SG = 28g/cm3) 3Minimum whole core size required for a complete test Partial results can sometimes be SAG Mill Testing Test Procedures to Characterize Ore
.jpg)
Crushing
2024年7月26日 %PDF15 %âãÏÓ 2847 0 obj > endobj 2859 0 obj >/Filter/FlateDecode/ID[51FE817BD90CBA4BBEA8005>18E7D8FB3B00754EDA2F>]/Index[2847 22]/Info 2846 2022年10月4日 21 Energy Rock drilling, blasting, and comminution (crushing and grinding) consume a vast amount of energy in hard rock mines As mentioned in Sect 1, statistics from hard rock mines indicates that drilling and blasting consumes 2% and comminution does 53% of the total energy input in the whole production chain from mining to mineral processing (Spathis Reduction of Fragment Size from Mining to Mineral 2016年1月27日 The following items make up an EXAMPLE Crushing Plant Startup Sequence Procedure that all must be checked in preparation and before the equipment in the Crushing Plant is started If maintenance has occurred since the last operating shift, ensure that the MCC is energized and that all safety locks have been removed from equipment startersCrushing Plant Startup Sequence Procedure2023年7月3日 The ores are generally contaminated with earthly or undesired materials (impurities) These are called gangue or matrix The process of metallurgy depends upon the nature of the ore and the impurities present in it Some common steps involved in the metallurgical operations are : 1) Crushing and grinding of the oreCrushing, Grinding and Concentration of the Ore
.jpg)
(PDF) DESIGN AND OPERATIONS CHALLENGES OF A SINGLE
2017年6月30日 A review on the design and operations challenges of a single toggle jaw crusher is presented for crushing rocks and mineral ores to the appropriate sizes for direct application or further %PDF16 %âãÏÓ 4215 0 obj > endobj 4235 0 obj >/Encrypt 4216 0 R/Filter/FlateDecode/ID[87C03FABF6FB2246BC4F9AB649B4B217>]/Index[4215 26]/Info 4214 0 R/Length 101 AusIMM – Leading the way for people in resourcesfor Merensky ores according to the mineralogy 10,11 But in practice most operations have final grinds that are not significantly different than for Merensky ores and tend toward 60% minus 200 meshThe extractive metallurgy of South Africa's platinum ores2020年6月4日 The size reduction process of rocks in cone crushers is one of the most important issues, particularly for the secondary and tertiary stages of crushing operations In this study, 17 different rock types were considered for the evaluation of their size reduction variations that occurred in a laboratoryscale cone crusher Based on several mineralogical, physico Evaluation of size reduction process for rock aggregates in
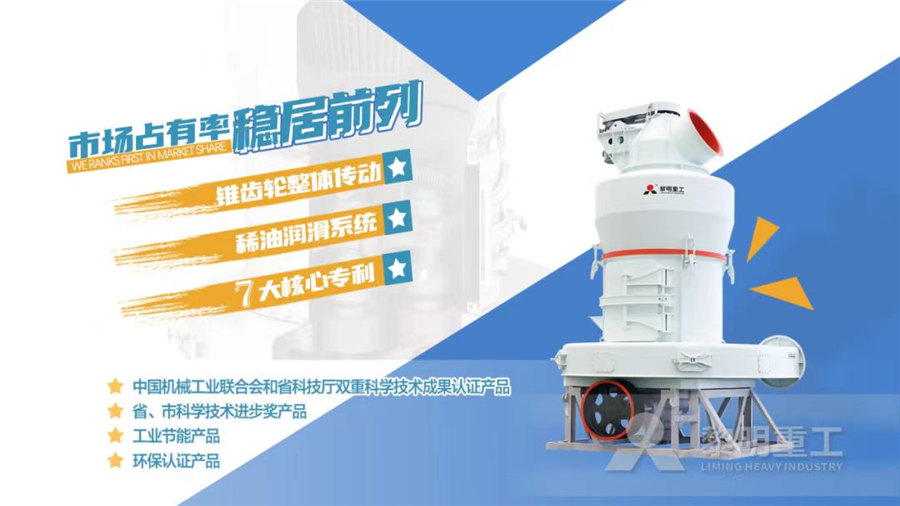
(PDF) Optimization Capabilities for Crushing
2022年4月26日 The optimization capabilities for crushing plants comprise a system solution with the twofold application of 1) Utilizing the simulation platform for identification and exploration of operational 2023年2月28日 The primary crusher is used to reduce the size of large rocks and stones, while the secondary crusher further breaks them down into smaller pieces the mechanical principles involved in their operation, and the Primary Crusher vs Secondary Crusher: 2024年7月17日 Crushing is a multistage process that includes primary crushing, secondary crushing, and tertiary crushing Different types of crushing equipment are used at each stage to meet various crushing requirements Primary crushing breaks down large raw materials into mediumsized pieces for easier handling in subsequent processesTypes of Crushers: Choosing the Right One for Each Stage2021年8月15日 Several works from the literature have reported applications of process control strategies in the mineral processing industry For example, Wei and Craig (2009) published a survey with qualitative data from process control solutions, and Bouffard (2015) reported quantitative data supporting the benefits of such strategies A series of works (Bouchard et al, A review of modeling and control strategies for cone crushers
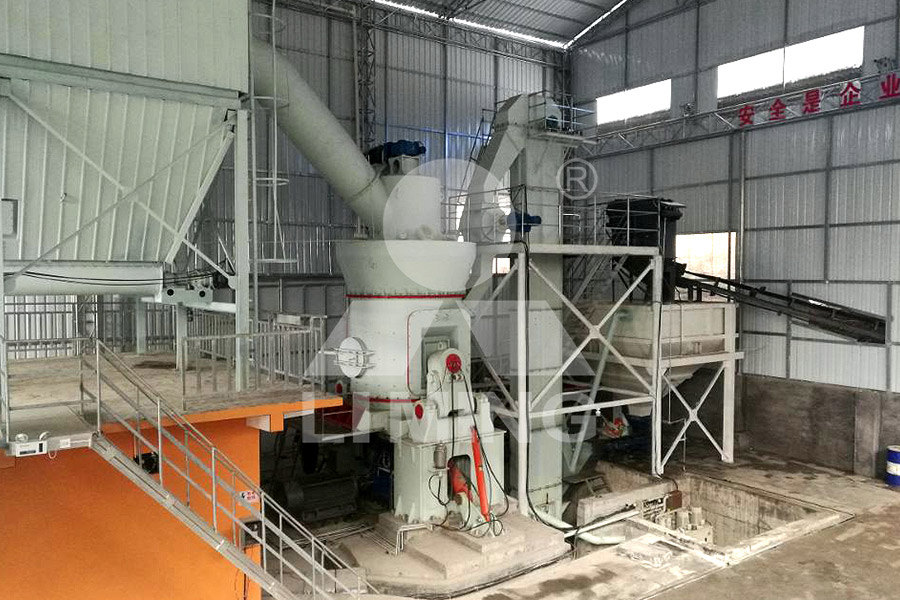
Crushed ore agglomeration and its control for heap leach operations
2013年2月1日 Crushed ore agglomeration as a pretreatment step for heap leaching is reviewed The acceptance of binder is limited due to the lack of acidtolerant binders Concise overviews of quality control and characterization tools are provided Different agglomerationheap leaching systems are summarized HPGR grindingagglomeration may have some advantages2024年2月6日 All types, gold, copper, large quartz rocks: Efficient crushing of largesized hard ores: Double Toggle: Hard and abrasive, iron ore, chromite, diamondbearing rock: Powerful crushing action for very hard and abrasive ores: Hydraulic: Varied, nickel, tin, and various hard ores; sticky clay ores: Adjustable and precise, good for ores requiring Understanding Types of Jaw Crusher: A Comprehensive 2021年6月17日 It is a wellknown fact that the value of the Bond work index (wi) for a given ore varies along with the grinding size In this study, a variability bysis is carried out with the Bond standard (PDF) Variability Study of Bond Work Index and Grindability Index 2020年8月6日 Leaching of copper from a Jordanian copper ore has been studied using a stirred batch reactor with hydrochloric acid as the main lixiviant, under the following conditions: temperature 25 – 45 oC Leaching of Copper Ores: Effects of Operating Variables
.jpg)
SIZE REDUCTION BY CRUSHING METHODS By
2023年12月1日 All operations in size reduction, both crushing and grinding are of course determined by the feed characteristics of the minerals (rock/ore) moving into the circuit The key parameters we need are the