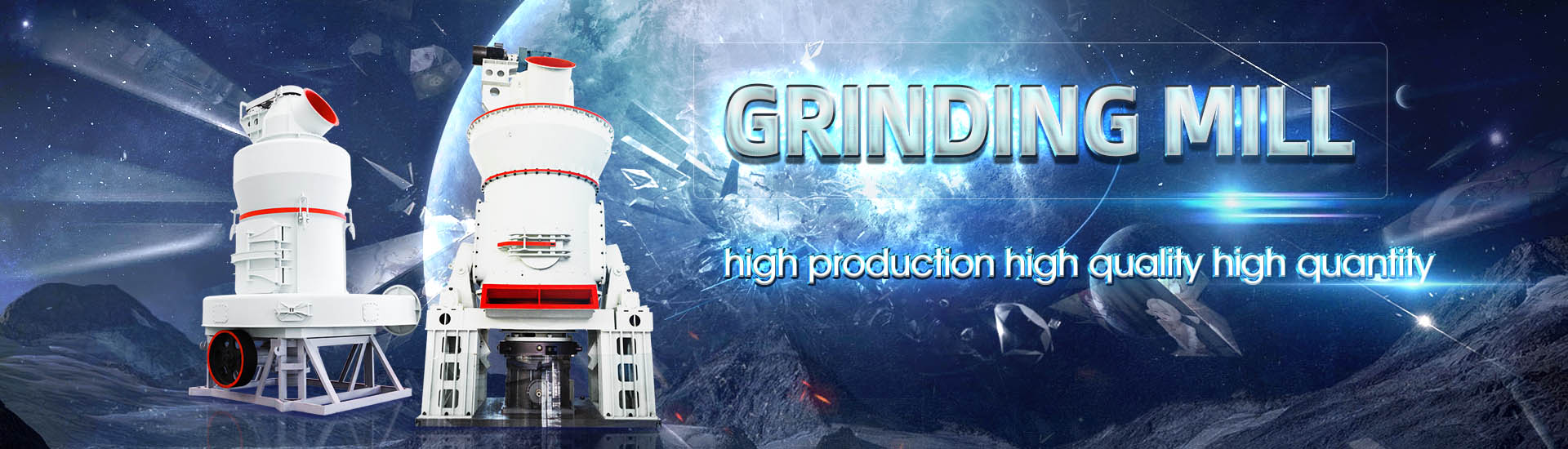
Solid angle coal mill
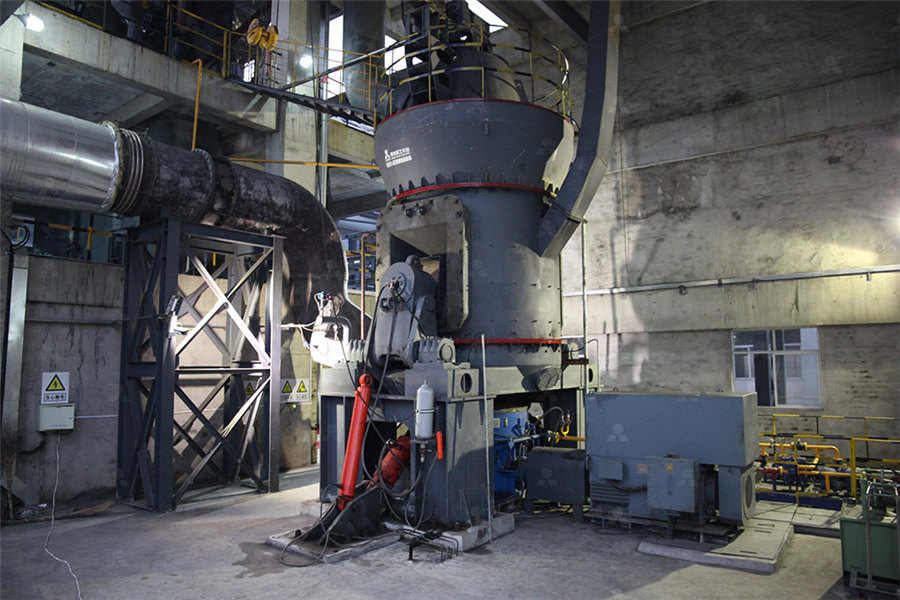
Classification performance of model coal mill classifiers with
2020年3月1日 The classification performance of the air classifier in a vertical coal mill determines the size of pulverized coal particles Thus, the classification performance will 2017年8月12日 vertical roller grinding mills for grinding: • Coal • Cement raw material • Clinker / granulated slag • Industrial minerals, and • Ores The core elements of these plants are the PROCESS OPTIMISATION FOR LOESCHE GRINDING 2024年11月26日 With a low power consumption, low noise and high efficiency operation, the large range of 2, 3 and 4 roller models mean there is a LOESCHE coal mill to suit any application LOESCHE coal grinding mills are Power Industry Loesche2024年11月1日 The authors used the EulerLagrange method to combine the coal drying model in Fluent and successfully obtained the velocity and temperature cloud maps of the gas phase Numerical Study of Flow Field and Particle Motion
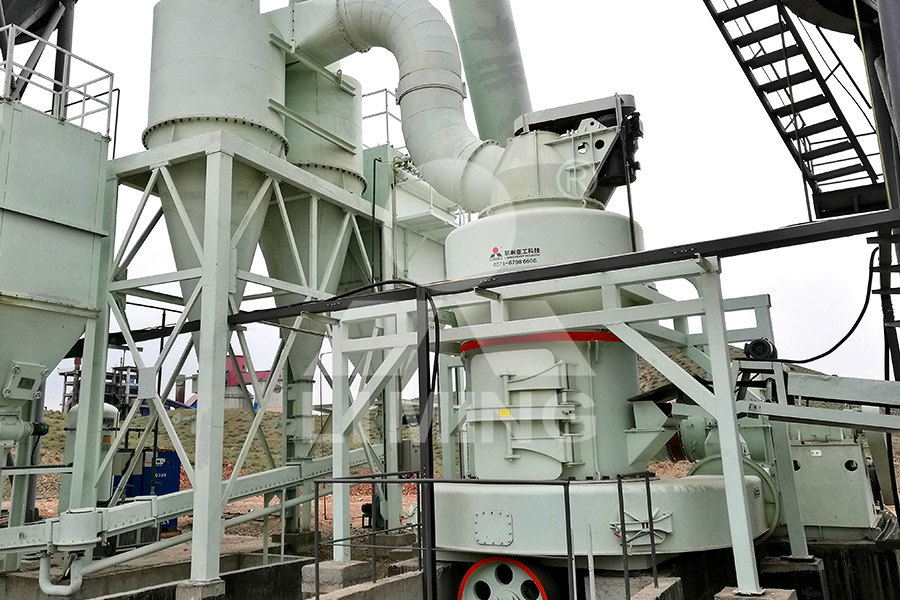
The Influence of Mill Loading on the Distribution of Pulverized Coal
2023年9月1日 The load of the mill affects the amount of pulverized coal in the third channel, but also in the other two channels At the same time, increasing the capacity of the mill reduces The Raymond® Bowl Mill is considered the finest vertical roller mill available for pulverizing coal Each bowl mill system is designed to achieve the best solution for the processing application The mill, feeder, classifier, fan, cyclone, dust Raymond® Bowl Mill Coperion2020年8月12日 This study shows the performance of a currently running vertical roller coal mill (VRM) in an existing coalfired power plant In a power plant, the coal mill is the critical An investigation of performance characteristics and 2020年3月1日 The classification performance of the air classifier in a vertical coal mill determines the size of pulverized coal particles Thus, the classification performance will Classification performance of model coal mill classifiers with
.jpg)
Solid Backfilling Efficiency Optimization in Coal
2023年11月14日 They built an overall research framework and equipment system for underground intelligent sorting and in situ backfill for deep coal mines A novel solid backfilling mining technology that integrated mining, sorting, and 2023年3月1日 Loesche Coal Mill Free download as PDF File (pdf), Text File (txt) or read online for free 1) Loesche has been involved in processing solid fuels like coal since 1925 and has continued innovating coal grinding Loesche Coal Mill PDF Mill (Grinding) Coke 2014年1月1日 Operational data of MPS mills for solid fuel grinding The emission factors of kiln end, kiln head, coal mill, crushing and cement mill was 0156 clinker g/t, 3914 clinker g/t, 1538 coal g/t (PDF) MPS mills for coal grinding ResearchGate2021年3月12日 The main difference of an MPS mill for solid fuels to other MPS mills lies in its pressureshock resistance Mill and classifier housing, feed unit and ex pansion joints are designed to be pressureshock resistant To avoid MPS mills for coal grinding AYS Engineering
.jpg)
Classification performance of model coal mill classifiers with
2020年3月1日 The classification performance of model coal mill classifiers with different bottom incoming flow inlets was experimentally and numerically studied The flow field adjacent to two neighboring impeller blades was measured using the particle image velocimetry technique The results showed that the flow field adjacent to two neighboring blades with the swirling inlet was 2018年12月15日 Woody biomass cofiring with coal at existing pulverizedcoal boilers is known to be a green energy source and is a lowexpense alternative for pure coal combustionComilling woody biomass particles (15 wt%) with coal particles (85 wt%) before burning at a boiler is a complex problem because large woody biomass particles (>300 μm) exit the milling system Analysis of particle behavior inside the classifier of a 2018年3月5日 need improvement to achieve milloptimal performance Coal feed to the mill is important, this was observed to be a limiting constraint on mill capacity when the coal required exceed nominal load requirement KEYWORDS: Air fuel ratio; pulverised fuel distribution; classifier; elutriation; heat balance; isokineticPerformance optimisation of vertical spindle coal right angle Shaft configuration solidshaft Configuration compact, modular Number of stages twostage, threestage Performance lownoise, highpower, high load capacity Applications transmission, for machinery, for industrial applications, industrial, for the metallurgical industry, building, for vertical mills, for grinding Power Max: 900 kW Vertical mill gearbox NGC China Transmission
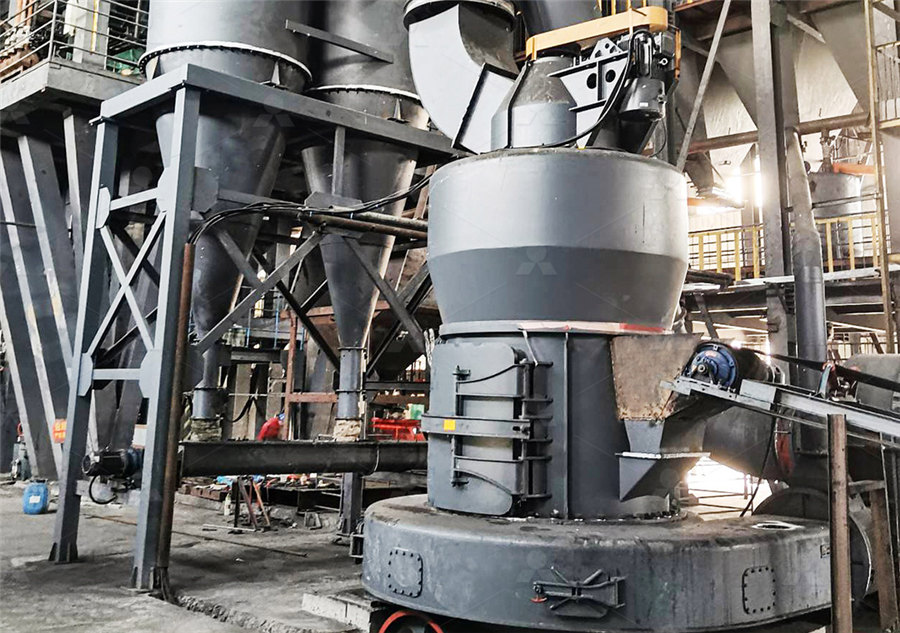
Stress Scrutiny of Reject Handling Components for Coal
2015年8月31日 of the component is Solid Works and stress scrutiny was carried out in ANSYS14 Key words: Scraper, Stiffeners, Stresses, Coal Mill, Solid Works, ANSYS14 I INTRODUCTION Scraper assembly is light in weight which is used to take out the ungrinded material from the mill which gets collected in the pyrite box2019年11月1日 Tangsathitkulchai and Austin [14] documented that the maximum breakage rates for quartz, coal, and copper ore when using a laboratory ball mill were obtained at the solid concentration of 45 vol% The mineral processing plants are using the wet grinding, while dry grinding is widely used at typical thermal power stations and a boiler plant [15 Differences in dry and wet grinding with a high solid KenCut™ highperformance solid carbide end mills from Kennametal are perfect for hardmachining operations Coal Energy ; Oil Gas Wear Solutions ; Oil Gas Production to Tool Cutting Edge Angle Max Tool Cutting Edge Angle Max Number of Flutes Number of Flutes 2 2 (48) 3 3 (1) 4 4 (59) 6 6 (11) 8 8 (4) range select Over All HighPerformance HardMachining • Solid Carbide End Mills Kennametal's KOR™ highperformance solid carbide end mills series offers dynamic milling with low radial engagement Inserts feature five cutting edges Coal Energy ; Oil Gas Wear Solutions ; Oil Gas Production to Maximum Ramp Angle Max Maximum Ramp Angle Max FrontEnd Center Cutting Center Cutting N (128) Y (40) BackEnd KOR5™ • HighPerformance Solid Carbide End Mills
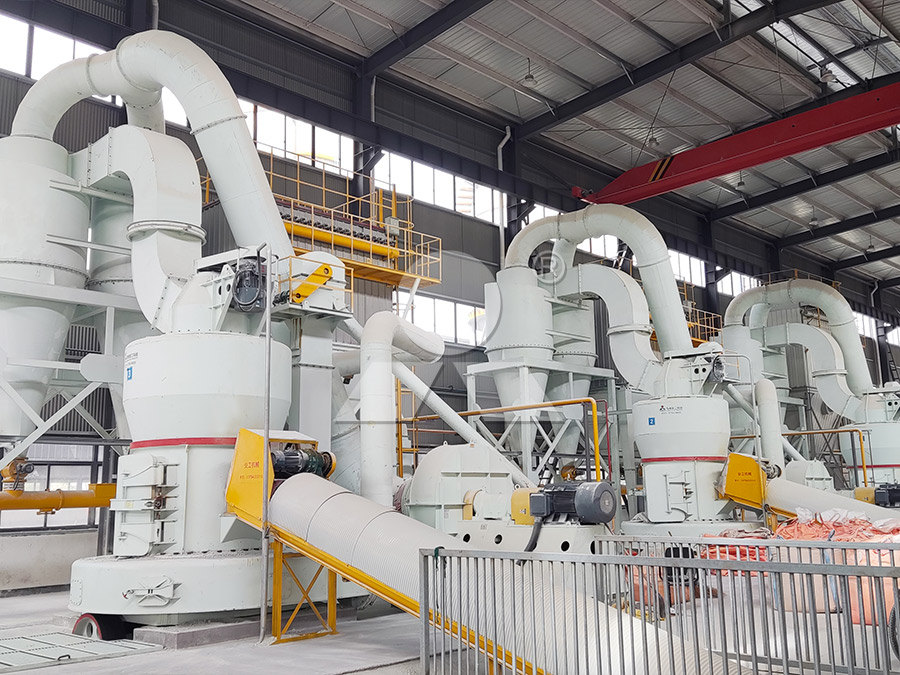
(PDF) Experimental Investigation of Coal Dust Wettability
2016年8月10日 It is important to note that coal surfaces are characterized as lowenergy surfaces, and the critical surface tension (γc) required for effective wetting is approximately 45 mN/mThis type of coal fineness increases the surface area for burning This leads to an increased combustion rate and shelf life of the coal Pulverized coal is typically used in power plants heated in fired furnaces Coal Pulverizers for Solid Fuel Coal Crushers Coal Pulverizers MillsA simple energy balance model of the coal mill is derived in (Odgaard and Mataji 2006), this model is based on a more detailed model found in (Rees and Fan 2003)In this model the coal mill is seen as one body with the mass m mThe following variables are defined: T(t) is the temperature in the coal dust flow in the mill, ṁ PA (t) is the primary air mass flow, T PA (t) is Coal Mill an overview ScienceDirect Topics2014年10月1日 efficiency of coal separation for particle size i m mill,i mass flow rate of coal from the mill for coal particle size i As a result, for the new design analyses, certain steps are going to be checked and controlled These steps are as follows: • The coal mass flow rate from the mill should be approximately 100 kg/s, as in the D00 base Numerical and experimental analysis of pulverized coal mill
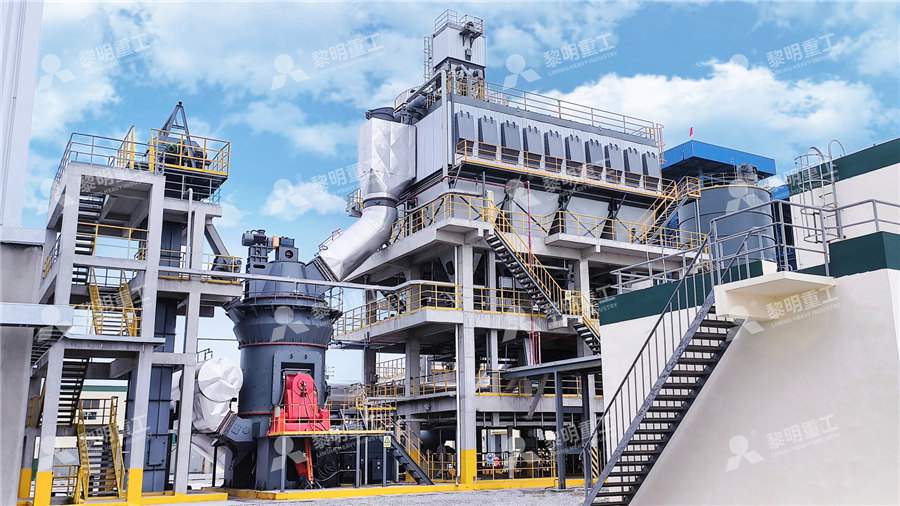
R Todd Swinderman,PE, and Andy Marti,
2014年9月11日 coal handling systems is the increased use of bulk material science This field is focused on the testing and analysis of both the bulk solid and the construction materials that the bulk solids will move on, over or through Bulk material science is an interdisciplinary field, centred on determining Angle of repose The angle of repose for 2021年6月24日 to allow the air core to operate This sounds tricky, but is easy to check because of the “flare” angle of the underflow from the spigot When a cyclone is operating normally, with a stable air core, the underflow discharges from the spigot as a hollow cone The inside angle of the cone the flare angle varies with the spigot sizeIntroduction to Cyclones AusIMM2017年8月25日 when milling titanium alloy using a 20mm diameter solid carbide end mill, is a 12mm diameter of inner circle, four flutes, a 45 ° helix angle, and a 9 ° rake angle of the side cutting edge Keywords Solidcarbideendmill Toolstructuredesign Tool geometry FEM Optimization 1 Introduction Solid end mills are widely used as the cutting tools Simulationbased solid carbide end mill design and 2024年10月31日 Coal mills, essential components in power generation and various industrial processes, pose significant safety risks if not properly managed These mills, used to grind coal into a fine powder for combustion, present potential hazards such as fire, explosion, and mechanical failures This article outlines best practices and precautions to ensure thEnsuring Safety in Coal Mills Coal Mill Safety, Explosion and
.jpg)
Grinding Characteristics of Wood Pellet and Coal Mixtures in a Roller Mill
2020年12月15日 The degree of torrefaction and the TP content have been shown to greatly influence the milling performance, 21,27,28 where welltorrefied biomass is milled in preference to coal2023年11月16日 in coal, as a tracer in a roller mill20 In that study, the WPs were selectively accumulated inside the roller mill and discharged with a particle size larger than that of the coal particlesMilling Characteristics of Coal and Torrefied Biomass Reliable coal pulverizer performance is essential for sustained fullload operation of today's power plants An effective pulverizer must be capable of handling a wide variety of coals and accommodating load swings in utility boilers as large Reliable Coal Pulverizers and Mills » Babcock1 天前 Wall friction angle To measure the friction between a bulk solid and a vessel’s wall material, place a sample of the bulk solid inside a retaining ring on a flat coupon of the wall material Apply a normal load to the bulk solid so that it slides along the stationary wall material, and measure the steady shear stressDesigning Hoppers, Bins, and Silos for Reliable Flow AIChE
.jpg)
A Study on 500 MW Coal Fired Boiler Unit’s Bowl Mill
Section of coal bowl mill Table 1 Guaranteed coal conditions for mill performance evaluation Coal Moisture % 20 Coal HGI 55 Mill Outlet Temperarure °C 80 Mill Air Flow T/hr 102 Coal Fineness (% passing trough 200 mesh) 70% passing through 200 mesh and 90% passing through 50 mesh Differental Pressure 300 mmwc Coal Output from Mill 609 t/hr2023年4月26日 1927 First Loesche coal mill delivered for the Klingenberg power station in Berlin 1953 500th coal mill plant sold worldwide 1961 Introduction of hydraulic spring assembly system 1965 Construction of first pressure mill (LM 122 D) 1980 Delivery of first modular coal mill (LM 263 D) 1985 Delivery of first selfinerting coal grinding plant (LM 212 D) for the steel LOESCHEMILLS mypronamic2014年1月15日 A particle mixing criterion for binary mixture angle of repose had been developed and applied to more binary mixed granular systems including biomass–coal blends The work would be helpful to the investigation of mixed particles system flow behavior and more directly useful to lay the root for the success of biomass–coal blends dense phase Theoretical and experimental investigation on angle of repose of 2023年12月5日 Pulverized coal combustion includes a series of complex physical and chemical processes such as pulverized coal pyrolysis, combustion, turbulentCombined operation mode of subcritical Wflame boiler
.jpg)
132loesche Mills For Solid Fuels Coal MillE Scribd
2021年11月9日 132Loesche Mills for Solid Fuels Coal MillE Free download as PDF File (pdf), Text File (txt) or read online for free Loesche has been designing and manufacturing coal grinding mills since 1925 They provide turnkey grinding plants from small single mills to large modular mills Their mills use roller grinding technology and hydraulic systems to grind coal 2021年1月11日 The specific contact angles of the three coal samples are shown in Fig 7, where the proximate intrinsic contact angle of each coal sample is 60° for Hami lignite, 95° for Anyang coking coal A numerical solution to the effects of surface roughness on water–coal 2023年3月1日 Loesche Coal Mill Free download as PDF File (pdf), Text File (txt) or read online for free 1) Loesche has been involved in processing solid fuels like coal since 1925 and has continued innovating coal grinding Loesche Coal Mill PDF Mill (Grinding) Coke 2014年1月1日 Operational data of MPS mills for solid fuel grinding The emission factors of kiln end, kiln head, coal mill, crushing and cement mill was 0156 clinker g/t, 3914 clinker g/t, 1538 coal g/t (PDF) MPS mills for coal grinding ResearchGate
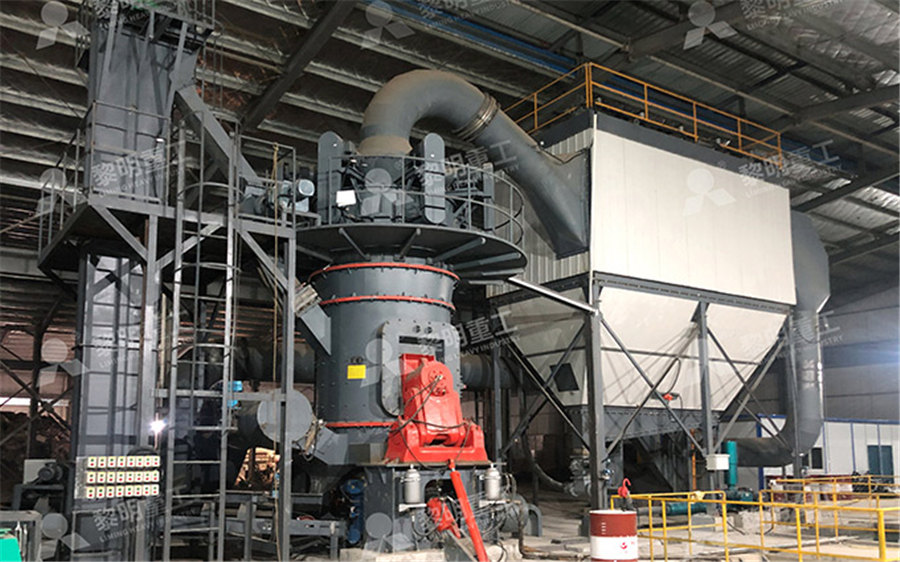
MPS mills for coal grinding AYS Engineering
2021年3月12日 The main difference of an MPS mill for solid fuels to other MPS mills lies in its pressureshock resistance Mill and classifier housing, feed unit and ex pansion joints are designed to be pressureshock resistant To avoid 2020年3月1日 The classification performance of model coal mill classifiers with different bottom incoming flow inlets was experimentally and numerically studied The flow field adjacent to two neighboring impeller blades was measured using the particle image velocimetry technique The results showed that the flow field adjacent to two neighboring blades with the swirling inlet was Classification performance of model coal mill classifiers with 2018年12月15日 Woody biomass cofiring with coal at existing pulverizedcoal boilers is known to be a green energy source and is a lowexpense alternative for pure coal combustionComilling woody biomass particles (15 wt%) with coal particles (85 wt%) before burning at a boiler is a complex problem because large woody biomass particles (>300 μm) exit the milling system Analysis of particle behavior inside the classifier of a 2018年3月5日 need improvement to achieve milloptimal performance Coal feed to the mill is important, this was observed to be a limiting constraint on mill capacity when the coal required exceed nominal load requirement KEYWORDS: Air fuel ratio; pulverised fuel distribution; classifier; elutriation; heat balance; isokineticPerformance optimisation of vertical spindle coal
.jpg)
Vertical mill gearbox NGC China Transmission
right angle Shaft configuration solidshaft Configuration compact, modular Number of stages twostage, threestage Performance lownoise, highpower, high load capacity Applications transmission, for machinery, for industrial applications, industrial, for the metallurgical industry, building, for vertical mills, for grinding Power Max: 900 kW 2015年8月31日 of the component is Solid Works and stress scrutiny was carried out in ANSYS14 Key words: Scraper, Stiffeners, Stresses, Coal Mill, Solid Works, ANSYS14 I INTRODUCTION Scraper assembly is light in weight which is used to take out the ungrinded material from the mill which gets collected in the pyrite boxStress Scrutiny of Reject Handling Components for Coal 2019年11月1日 Tangsathitkulchai and Austin [14] documented that the maximum breakage rates for quartz, coal, and copper ore when using a laboratory ball mill were obtained at the solid concentration of 45 vol% The mineral processing plants are using the wet grinding, while dry grinding is widely used at typical thermal power stations and a boiler plant [15 Differences in dry and wet grinding with a high solid KenCut™ highperformance solid carbide end mills from Kennametal are perfect for hardmachining operations Coal Energy ; Oil Gas Wear Solutions ; Oil Gas Production to Tool Cutting Edge Angle Max Tool Cutting Edge Angle Max Number of Flutes Number of Flutes 2 2 (48) 3 3 (1) 4 4 (59) 6 6 (11) 8 8 (4) range select Over All HighPerformance HardMachining • Solid Carbide End Mills