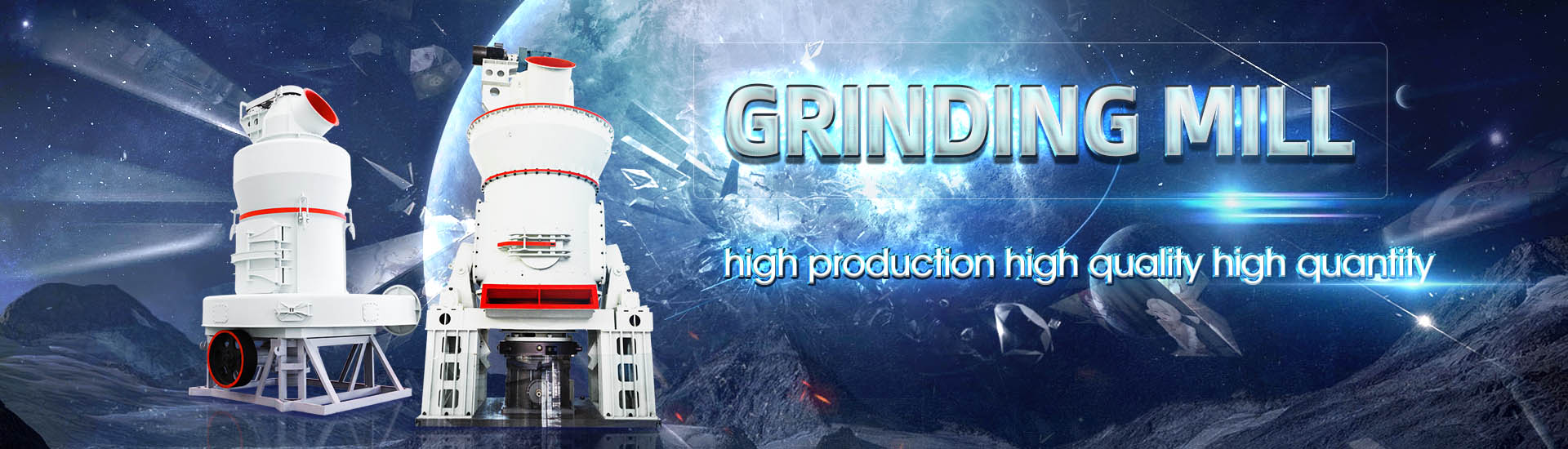
HOME→Conductive powder coating zincrich powder conductive powder coating zincrich powder conductive powder coating zincrich powder
Conductive powder coating zincrich powder conductive powder coating zincrich powder conductive powder coating zincrich powder
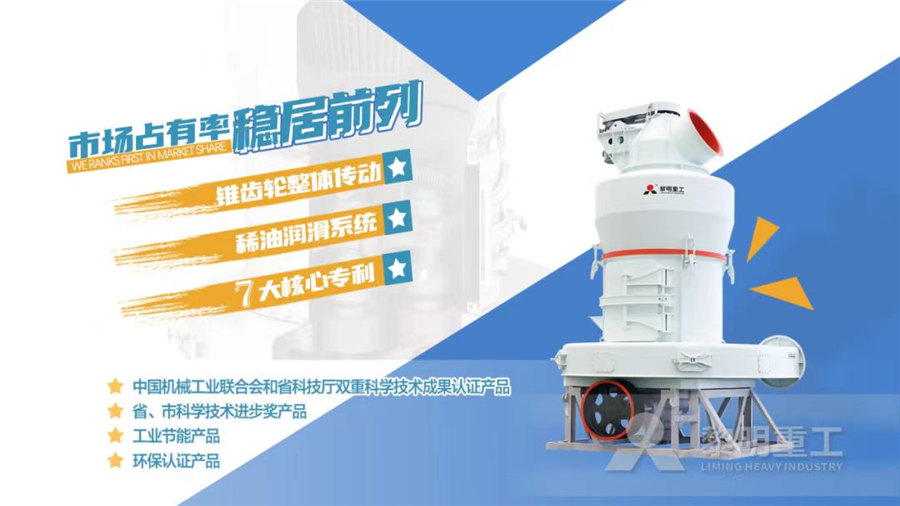
Electrochemical behavior of zincrich powder coatings in artificial
2004年7月30日 Zincrich powder coatings were deposited onto Qpanels made of steel, using Corona’s electrostatic spraying which is the major process for applying powder coatings In 2020年10月1日 By analysing the results of corrosion potential, EIS, SEM and XRD test of zincrich coatings (ZRCs) in 35wt% NaCl solution, it was found that conductive pigment (diiron phosphide, Fe 2 P) can accelerate the activation Improving the performance of zincrich coatings using 2019年1月24日 Conductive polymers are expected to enhance the electrochemical effect of zinc metal in paints Organic coatings with lamellar zinc particles also exhibit better mechanical Effects of conductive polymers (type and concentration) in Zinc rich coatings are being used by many industries for the corrosion protection of steel substrates This study looked at corrosion resistance evaluation of Zincrich powder coatings corrosion in sea water:
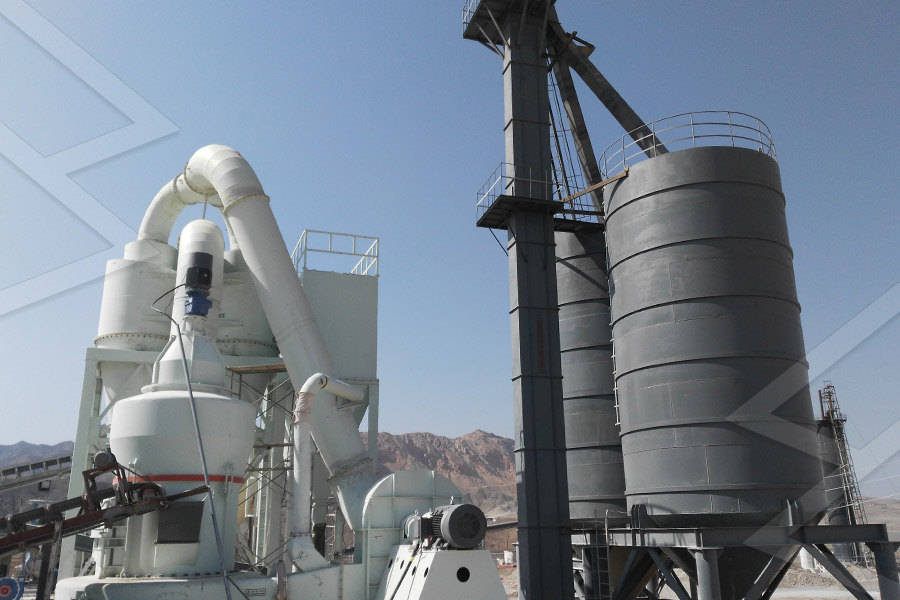
Zincrich powder coatings corrosion in sea water: influence of
Effects of replacing partial zinc dust with conductive pigments on the anticorrosion properties of ethyl silicate zincrich coatings with low zinc content were investigated Salt spray test, salt 2002年12月1日 The effect of addition of conductive pigments like carbon blacks on the corrosion behavior of zincrich powder paints coated steel in artificial sea water was investigated Open Zincrich powder coatings corrosion in sea water: Influence of 2008年1月1日 Request PDF Electrochemical and anticorrosion performances of zincrich and polyaniline powder coatings In this work, hydrochloride polyaniline (PANICl) powder was incorporated as a Electrochemical and anticorrosion performances of zincrich 2002年12月1日 In zincrich powder coatings, the zinc content is limited well below the one reported for liquid ZRPs, due to technical limitations With an epoxy matrix and a zinc concentration of 50% by weight, a real cathodic protection could not be Zincrich powder coatings corrosion in sea water: influence of
.jpg)
Electrochemical behavior of zincrich powder coatings in artificial
2004年7月30日 In this work, three singlecoat zincrich powder coatings were immersed in artificial sea water These formulations are epoxybased and contain a complex mixture of zinc dust which represents 50 or 70 wt%This zinc concentration is well below the one usually reported with liquid ZRPs and, for the third formulation, conductive pigments (carbon blacks) DOI: 101016/S03009440(02)001455 Corpus ID: ; Zincrich powder coatings corrosion in sea water: influence of conductive pigments @article{Marchebois2002ZincrichPC, title={Zincrich powder coatings corrosion in sea water: influence of conductive pigments}, author={Herv{\'e} Marchebois and S{\'e}bastien Touzain and S Joiret and Janez Bernard and Zincrich powder coatings corrosion in sea water: influence of 2022年8月15日 More recently, zincrich powder coatings have been reported [10] and used in industry, but the concentrations of zinc particles (or dust) in these zincrich powder coatings were far below 80 wt%, which is usually required for the solventbased counterparts to provide sufficient corrosion protection to the steel substrates in aggressive environments [10], [11]Extrusionfree fabrication of zincrich powder coatings: Press 2021年4月1日 Among the different types of sacrificial coatings, zinc rich primers (ZRPs) are the most widely used effective anticorrosion coatings Zinc rich primers are usually applied as the base coat above which the top coat of epoxy or polyurethane is applied forming a smooth glossy surface for durable and reliable heavyduty protection [7] as shown in Fig 2 (a)Review Research progress in organic zinc rich primer coatings for
.jpg)
Primer Powders IFS Coatings
Primer Powders Tough, Zinc Rich Primer IFS Conductive Primer provides surface resistance and good chemical and corrosion resistance Product code: ELSS 74220 What do IFS Primer Powders do? Our highquality powder primers will TruZinc: Zincrich Powder Coating Primers Zincrich primers to protect ferrous substrates TruZinc Primers protect ferrous substrates by two mechanisms First, they act as a barrier to water and electrolytes increasing the electrical resistance of the corrosion cell Second, they provide zinc which acts as a sacrificial anodeTruZinc™: Zincrich Powder Coating PrimersA zincrich powder coating, applied onto steel substrate, was studied using electrochemical impedance spectroscopy (EIS) Before immersion when coating is dry, EIS spectra revealed that the EIS characterisation of new zincrich powder coatings2021年1月13日 The electrochemical investigation of the corrosion behavior of epoxy modified silicate zincrich coatings in 35% NaCl solution leads to the impedance value of the zincrich coating increase with the increasing the epoxy content which indicates that the ability of the coating to resist corrosive media is enhanced especially in hydrochloric acid which is Full article: Organic zincrich protective coatings with improved
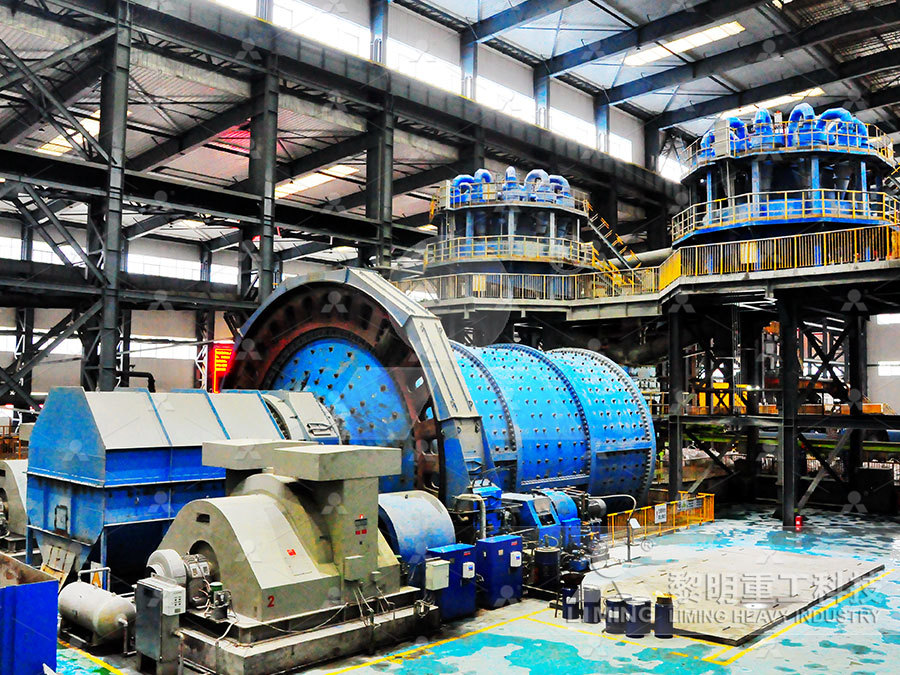
Zinc Rich Primer – Powder Coating Products
Powder Coating Products aims to be a comprehensive destination for all coating needs, offering a diverse range of products including powder, powder equipment, Zinc Rich Primer TCI SKU: 752070138BX55 Starting at $2080 per lb 1 2022年9月27日 In the study, a conductive polypyrrole (PPy) is deposited on the lamellar sericite powder (SCP) surfaces by an in situ oxidization growth method and the prepared PPy/SCP conductive additive is successfully applied on the Fabrication of a Conductive Additive for the 2019年1月24日 Pigment specification Zinc dust consisting of either spherical particles or lamellar particles and the conductive polymers were measured to determine their densities and oil numbers, from which their critical pigment concentrations could be calculated23 The mean particle sizes of the pigments were also determined Redistilled water (pH 650 ± 001, Effects of conductive polymers (type and concentration) in coatings ZincRich Epoxy Coatings Coatings 2022, 12, 1406https: replacing ratio of the conductive additives to zinc powder The coated surface was cured in an ovenFabrication of a Conductive Additive for the ResearchGate
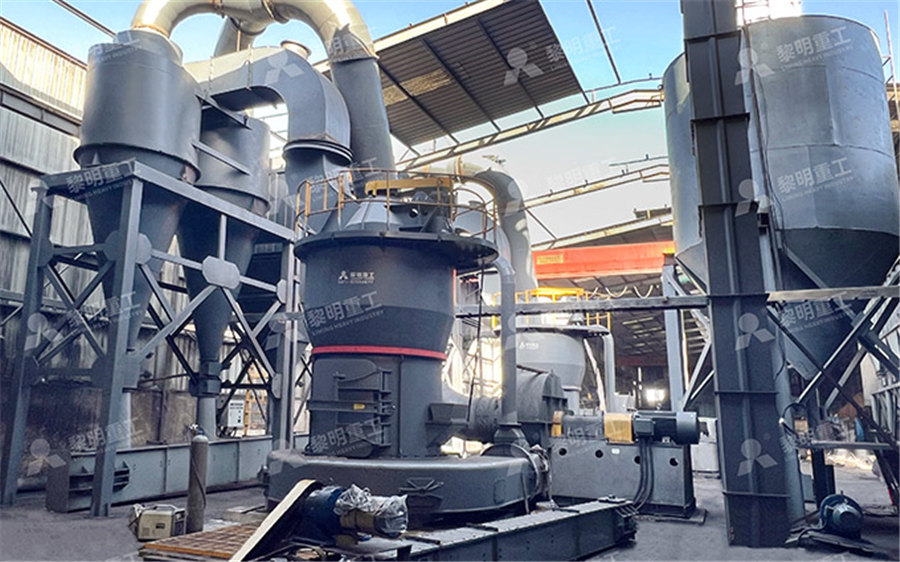
Electrochemical behavior of zincrich powder coatings in artificial
2004年7月30日 Semantic Scholar extracted view of "Electrochemical behavior of zincrich powder coatings in of corrosion potential, EIS, SEM and XRD test of zincrich coatings (ZRCs) in 35wt% NaCl solution, it was found that conductive Environment behaviors and degradation mechanisms of two organic epoxy coatings coated on Learn about the importance of choosing the correct primer for your powder coating project Explore three common primers (Zinc (Zinc Rich, Zinc Free, and Outgas Forgiving) and their applications on various substrates United States With the multitude of metal substrates that can be powder coated one question that commonly How to Choose the Correct Primer for Powder Coating ApplicationsZincrich paints are either organic, consisting of epoxies, chlorinated hydrocarbons, and other polymers; or inorganic based on organic alkyl silicates However, zincrich paint coatings are different than the others as there is a binding material ZincRich Paint American Galvanizers Association2007年6月1日 The zincrich epoxy powder formulation is given in Table 1It was deposited onto steel panels using Corona's electrostatic spaying technique and thermoset coated panels were cured at 200 °C for 20 min in an oven The coating thickness was measured using an Elcometer gauge and was found around 80 μm for all panelsEIS characterisation of new zincrich powder coatings
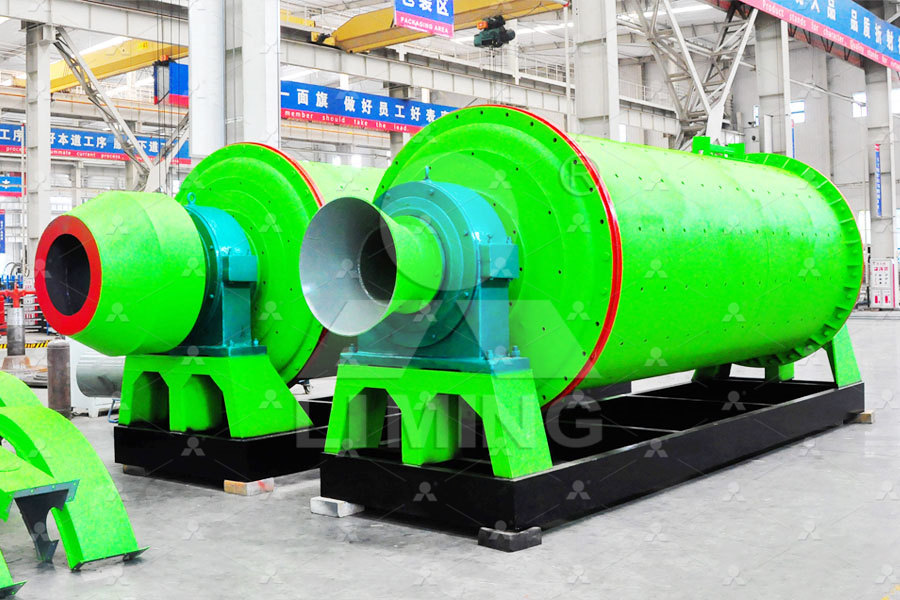
(PDF) Electrochemical behavior of zincrich powder coatings in
2004年7月1日 The optimal dispersion of scaly zinc powder in zincrich coatings has been explored by looking at the surface and crosssectional morphology and studying the cathodic protection time of the PDF On Apr 1, 2005, A Meroufel and others published Electrochemical Impedance Spectroscopy characterization of new zincrich powder coatings Find, read and cite all the research you need on Electrochemical Impedance Spectroscopy characterization of new zinc ZincRich Coatings 121 INTRODUCTION Zincrich coatings, which contain zinc dust and a binding medium, have been widely used since the 1930s for the protection of steel structures from corrosion [345, 1159) They can be used as a primer or as a final coating and can be applied by spray, dip, or brushZincRich CoatingsThe coating tested here is a commercialized zincrich powder coating which presents a good behavior in atmospheric media w6x 2 Experimental Zincrich powder coatings were deposited onto Qpanels made of steel, using Corona’s (PDF) Characterization of zincrich powder coatings
.jpg)
Zincrich Polyester Powder Coatings with Iron Phosphide: Lower Zinc
DOI: 101016/jjiec202312035 Corpus ID: ; Zincrich Polyester Powder Coatings with Iron Phosphide: Lower Zinc Content and Higher Corrosion Resistance @article{Huang2023ZincrichPP, title={Zincrich Polyester Powder Coatings with Iron Phosphide: Lower Zinc Content and Higher Corrosion Resistance}, author={Jin Bo Huang and Marshall 2020年5月14日 By analysing the results of corrosion potential, EIS, SEM and XRD test of zincrich coatings (ZRCs) in 35wt% NaCl solution, it was found that conductive pigment (diiron phosphide, Fe2P) can Improving the performance of zincrich coatings using conductive 2004年4月30日 Zincrich powder coatings were deposited onto steel Qpanels, using Corona’s electrostatic spraying technique, which is the major industrial process for applying powder coatings An electrostatic spray gun for powder (SAMES™ in our case) consists of a tube to carry airborne powder to an orifice at which an electrode is locatedZincrich powder coatings characterisation in artificial sea water2022年9月27日 rich coating, the prepared conductive PPy/SCP (1:2) particles and ferrotitanium powders with different mass proportions are used to r eplace zinc dusts (original zinc content of 80%) with a (PDF) Fabrication of a Conductive Additive for the Anticorrosion
.jpg)
Powder Coating vs Zinc Plating with AR Powder
2023年12月21日 Key Takeaways Durability: Powder coating is more durable than zinc plating, offering better resistance to environmental elements Color and Finish Options: Unlike zinc plating, powder coating provides a wider variety of colors and finishes Environmental Impact: Powder coating is ecofriendlier than zinc plating, with no VOC emissions and less waste2008年1月1日 In this work, hydrochloride polyaniline (PANICl) powder was incorporated as a conductive pigment into powder zincrich primer (ZRP) formulations in order to enhance the electronic conduction paths between zinc particles inside Electrochemical and anticorrosion performances of zincrich 4 Types of ZincRich Coatings 411 A zincrich coating is an anticorrosive coating for iron and steel incorporating zinc dust in a concentration sufficient to enable the zinc metal in the dried film to corrode preferentially to the ferrous substrate, ie, to give galvanic protectionGuide to ZincRich Coating Systems Rust Bullet AustralasiaFIGURE 7 – SEM Photos of zinc powder and zinc flakes Top view and crosssection (below) Effect of Binder Chemistry on Performance New inorganic binder technology has been developed for thin film zinc rich coating applications Conventional organic binder approaches have proven to be ineffective in thin filmZinc Rich Coatings for Fasteners DAU
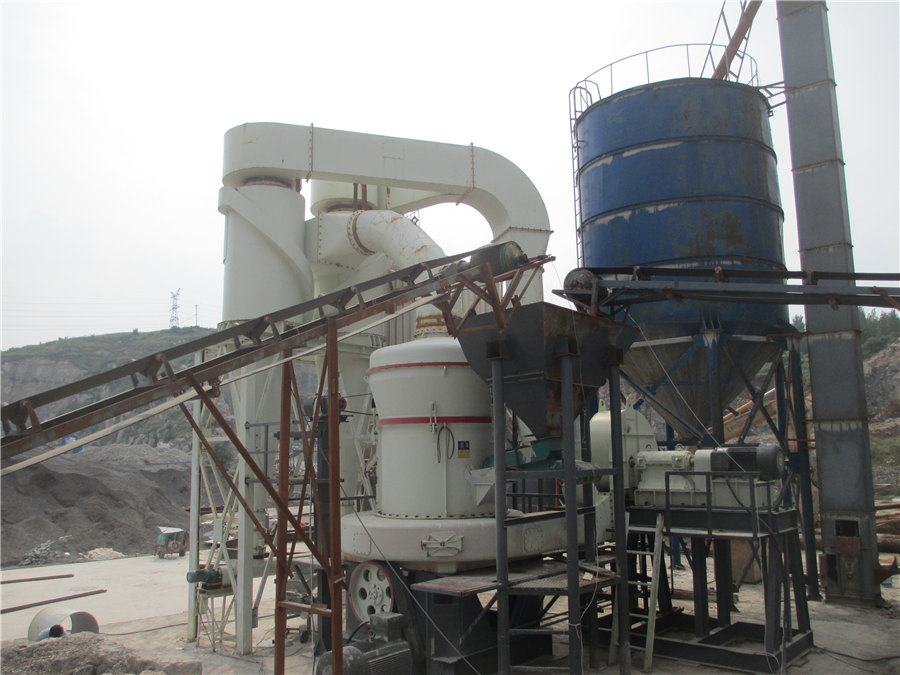
Improving the performance of zincrich coatings
2020年10月1日 By analysing the results of corrosion potential, EIS, SEM and XRD test of zincrich coatings (ZRCs) in 35wt% NaCl solution, it was found that conductive pigment (diiron phosphide, Fe 2 P) can accelerate the activation 2023年1月7日 Difference Between Zinc plating and Powder coating Zinc plating and powder coating are two different processes used to coat metal to protect it from corrosion Zinc plating is a chemical process that applies a thin layer of Zinc Plating vs Powder Coating – What’s the Difference2024年8月1日 To decrease the content of zinc in ZEP coatings and improve the utilization of zinc, thereby enhancing the corrosion protection of ZEP coatings, researchers have applied fillers like carbon nanotubes [12], [13], [14], carbon fibers [15], graphite [16] and graphene [17], [18]These materials are used to increase the conductive connection between zinc powders A waterborne zincrich epoxy anticorrosion coating with electron 2024年5月25日 Many conductive fillers such as carbon black, carbon nanotube and graphene, have been developed to reduce zinc content for zincrich coatings, but very few of them could reduce zinc content by 10 % while maintaining the original corrosion protection ability The carbonbased conductive additives have the issue of corrosion promotion after cathodic Zincrich polyester powder coatings with iron Phosphide: Lower zinc
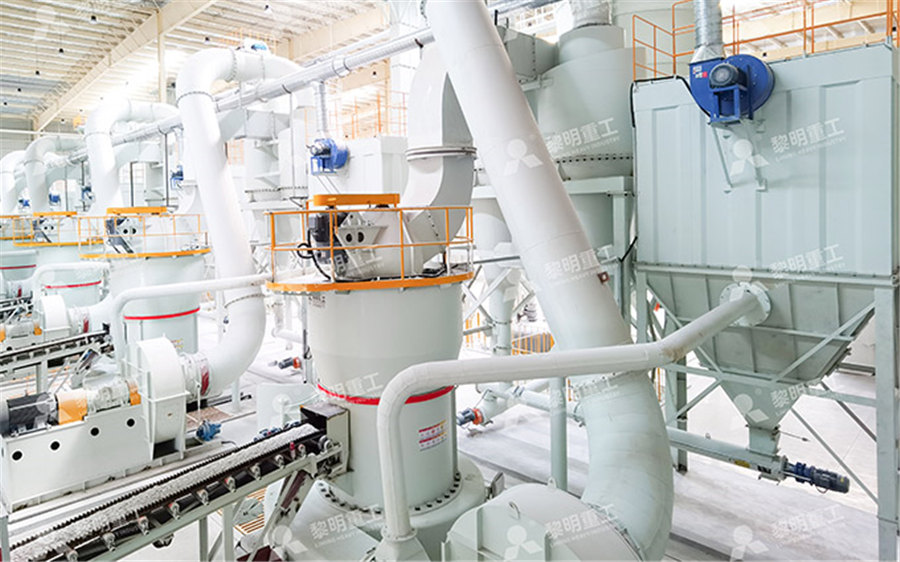
Characterization of zincrich powder coatings by EIS and Raman
2002年8月22日 Semantic Scholar extracted view of "Characterization of zincrich powder coatings by EIS and Raman spectroscopy" by H Novel properties of a conductive polymeric coating with an insulating Application of electrochemical impedance spectroscopy to study the degradation of polymercoated metals A Amirudin D Thieny Materials 2023年12月1日 Powder coatings represent an environmentally friendly VOCfree alternative to widely used solventborne zincrich coatings, with economic and ecological benefitsZincrich Polyester Powder Coatings with Iron Phosphide: Lower Zinc It can replace 10 wt% of zinc in 75 wt% zincrich polyester powder coatings while maintaining the original cathodic protection ability, as long as 86 days for a 40 μm film In addition, iron phosphide can significantly inhibit localized corrosion and decrease corrosion creepage by about 20 % during 2500 h salt spray testsZincrich polyester powder coatings with iron Phosphide: Lower zinc 2016年12月12日 Zinc powder as an anticorrosion pigment is used in paints in which zinc acts as sacrificed electrode High anticorrosion efficiencies of zinc coatings are attained mainly at high pigment volume concentrations (PVC) (Kalendová 2003; Havlík et al 2007)A high zinc concentration in the coating provides electric contact between the zinc particles themselves Enhancing corrosion resistance of zincfilled protective coatings
.jpg)
EIS characterisation of new zincrich powder coatings
2007年6月1日 Semantic Scholar extracted view of "EIS characterisation of new zincrich powder coatings" by A Meroufel et al Novel properties of a conductive polymeric coating with an insulating nanoadditive M Arianpouya M Nematollahi N Arianpouya M Shishesaz Materials Science, Engineering 2016; 62023年11月7日 Additives (pigments) such as zinc phosphate enhance the anticorrosive properties of powder coatings, but their behavior in powder coatings has not been extensively studied In this study, zinc phosphate was incorporated into three powder coating systems: polyester clearcoat, polyester and epoxy coatings with filler BaSO4Study on the AntiCorrosive Performance of Zinc Phosphate in Powder