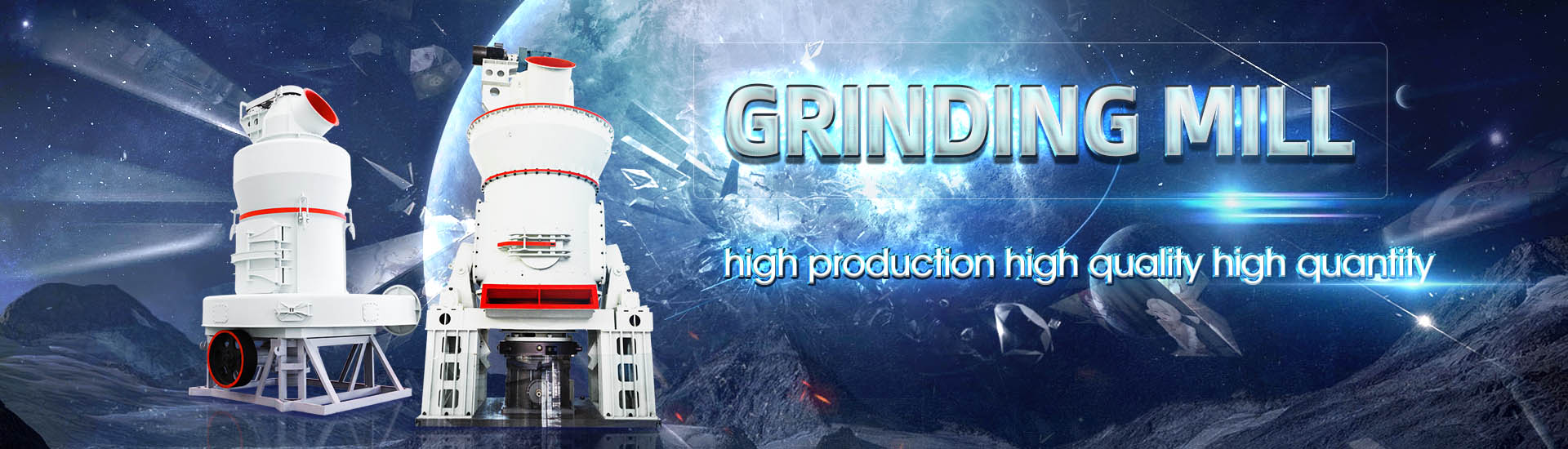
Ore powder making technology plan
.jpg)
Making Metal Powder MPIF
The first step in the overall powder metallurgy (PM) process is making metal powders There are four main processes used in powder production: solidstate reduction, atomization, electrolysis, and chemical In solidstate reduction, selected ore is crushed, typically mixed with carbon, The Sustainability Continuum Powder metallurgy is a recognized "green" A Green TechnologyIron ore and iron ore pellets are important sources of iron for manufacturing steel The iron ore production has significantly expanded in recent years, owing to increasing steel demands in developing countries, such as China and IndiaIron Ore Pelletizing Process: An Overview2019年2月28日 The ores are first mined from multiple ore locations, and then sent to the corresponding dressing plant to produce ore concentrate, which will be sent to distribution Integrated Production and Distribution Planning for the Iron Ore
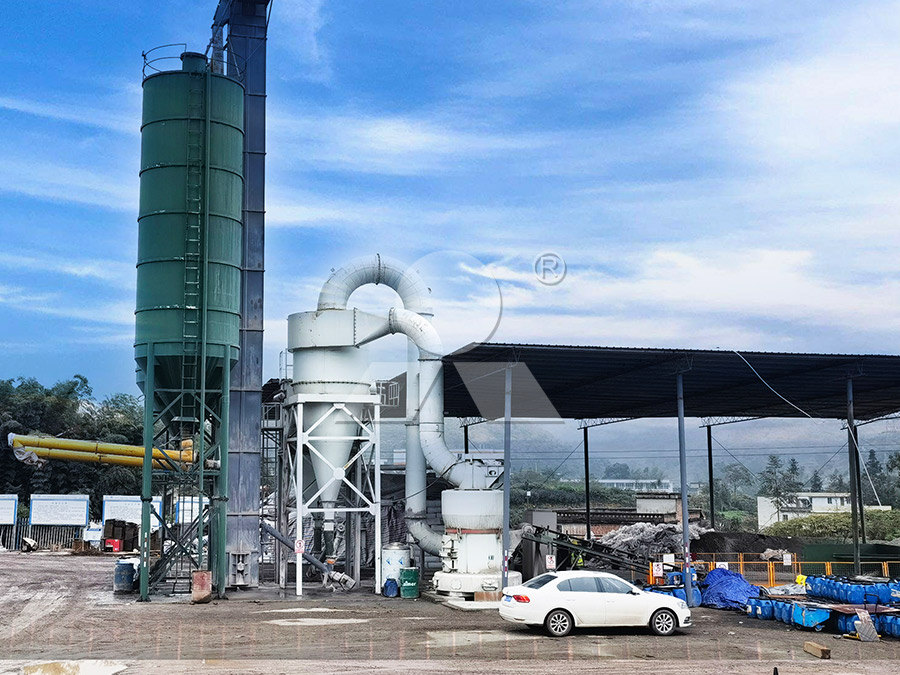
Micronsized ore powder production by propulsion and
2021年9月6日 We describe a micronsized ore powder production by propulsion and rapid unloading of highpressure gas The research consists of three parts Firstly, we obtain the 2020年4月8日 At present, there are many technologies for powder production (eg, gas atomization of the melt, chemical reduction, milling, and mechanical (PDF) Advanced Powder Metallurgy 2021年3月15日 The behavior of iron ore pellet binders is complex Any pellet binder is subject to a handful of practical requirements: that it be readily dispersed through a pellet, that it Iron Ore Pelletization: Part I Fundamentals2018年3月1日 Experiments have been carried out to develop a novel approach of producing iron ore powder First, the iron ore is placed in a highpressure chamber, and then liquid CO2 is Experiment on micronsized particle production of iron ore
.jpg)
Experiment on micronsized particle production of iron ore
2018年3月1日 Experiments have been carried out to develop a novel approach of producing iron ore powder First, the iron ore is placed in a highpressure chamber, and then liquid CO 2 is 2024年10月13日 Ore powder production involves the conversion of mined ore into fine particles through a series of crushing, grinding, and classifying processes The equipment used in this Advancements in ore powder production process 2021年9月6日 We describe a micronsized ore powder production by propulsion and rapid unloading of highpressure gas The research consists of three parts Firstly, we obtain the Micronsized ore powder production by propulsion and 2023年12月11日 The traditional ironmaking technologies (including coking, sintering, pelletizing, and BF ironmaking process) are carbonintensive, which makes the industry a significant contributor to global CO2 emissions Hydrogen replacement of carbon in steelmaking processes is a sustainable way to reduce CO2 emissions First, the reduction thermodynamics and HydrogenBased Reduction Technologies in LowCarbon
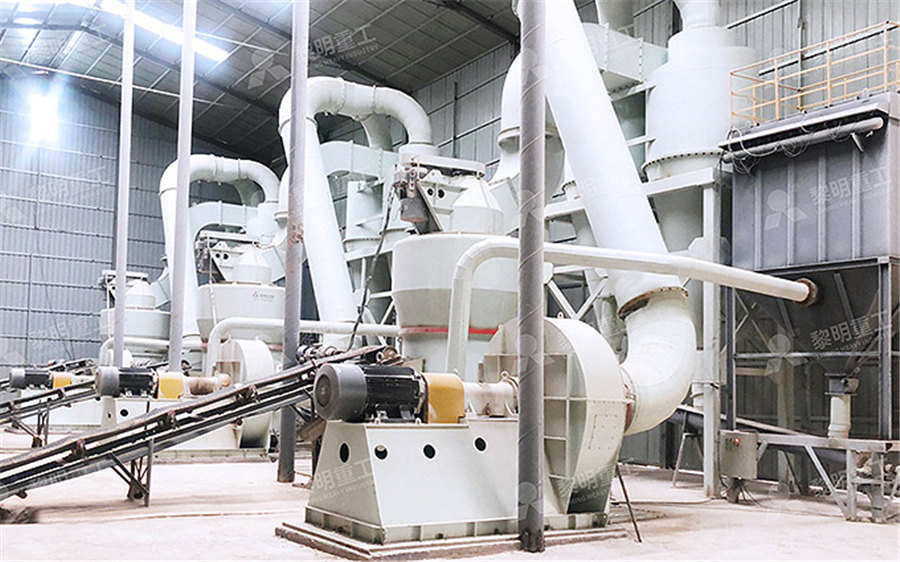
Gold Refinery Process: From Raw Material to
This process helps to increase the surface area of the ore, making it more accessible for subsequent grinding Grinding, on the other hand, involves further reducing the size of the crushed ore into a fine powder The crushed ore is 2023年10月9日 The production of iron sponges by FIOR was 43% of the total production in 1983 The iron ore powder with a particle size of less than 5 mm passes through 4 fluidized bed reactors in turn And the ore powder is preheated to 760 °C in the first stage by natural gas or coal gas, where the reduction reaction by hightemperature gas occurs [30, 32]Development and Problems of Fluidized Bed Ironmaking The ultrafine iron ore powder produced through mechanical activation is a crucial technology for achieving lowtemperature ironmaking This study employs thermogravimetric analysis to investigate the reduction properties of coal powder to iron The characteristics and mechanism of ultrafine iron ore powder 2023年10月9日 It is the process in which iron ore powder is reduced in a fluidized bed The main processes include Novalfer process, HIron reduction process, high iron ore briquette (HIB) process, and FIOR process With progress in industrial technology, users presented higher requirements for quality and varieties of steel, and the electric furnace Direct Reduction Ironmaking SpringerLink
.jpg)
Clean Utilization of Limonite Ore by Suspension
2022年2月17日 As a typical refractory iron ore, the utilization of limonite ore with conventional mineral processing methods has great limitations In this study, suspension magnetization roasting technology was developed and utilized to recover limonite ore The influences of roasting temperature, roasting time, and reducing gas concentration on the magnetization roasting 2022年3月1日 The iron ore slimes, which contain low iron content with high gangue minerals like kaolinite, gibbsite, and quartzite, cannot be used directly for iron production The present study focuses on utilization of iron ore slimes without beneficiation by blending with highgrade fines for making iron ore pellets The pellets were prepared by adding Analysis of iron ore pellets properties concerning raw 2019年6月11日 World resources are estimated to be greater than 800 billion tons of crude ore containing more than 230 billion tons of iron The only source of primary iron is iron ore, but before all that iron ore can be turned into steel, it must go through the sintering process Sinter is the primary feed material for making iron and steel in a blast furnaceSintering: A Step Between Mining Iron Ore and SteelmakingBased on the progress in biomass technology, this study investigates the utilization of landscaping residues (wood waste) subjected to thermal treatment as a reductant for iron ore, to produce two types of C/O (the ratio of carbontooxygen is the molar ratio of carbon in ICCB to oxygen content in iron oxide) iron ore powdergreen carbon Study on strength and reduction characteristics of iron ore powder
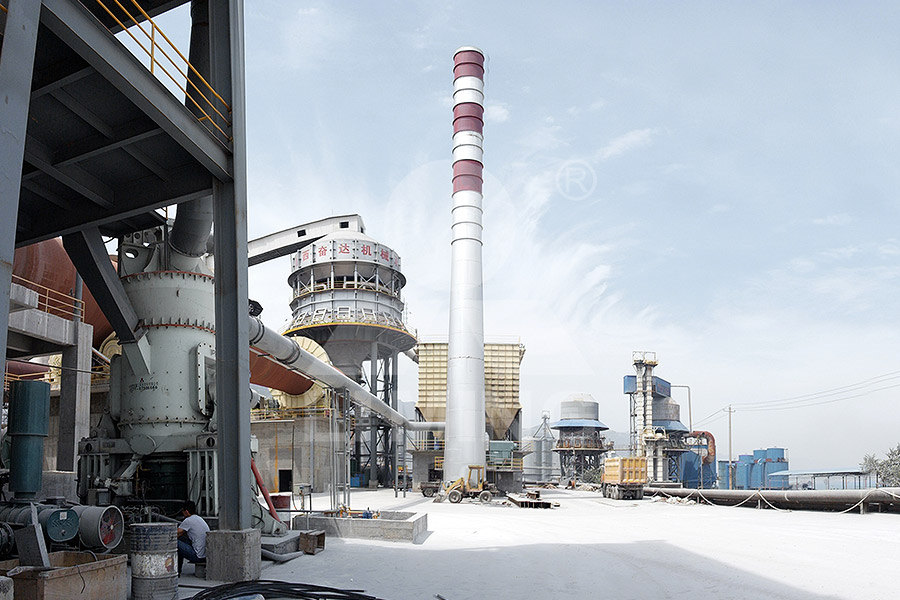
The Process of Making Iron: From Ore to Product Blogs
2024年8月2日 The ore is passed through crushers, which break it down into smaller chunks These chunks are then screened to separate the ore from waste material Grinding The crushed ore is then ground into a fine powder This step is crucial as it increases the ore's surface area, making it easier to extract the iron during subsequent processes2022年7月30日 strength Among them, the overall fluidity of iron ore powder A was poor, and the fluidity of iron ore powder B varied greatly between different particle grades, and the fluidity of iron ore powder C was more balanced and its bonding phase strength was high, while the overall bonding phase strength of iron ore powders B and E was lowStudy on the Basic Characteristics of Iron Ore Powder 2019年7月19日 The coal blend quality and process control of coke making technologies are an important lever to produce quality coke with optimal cost Apart from impacting cost, this improves the CO 2 footprint Heat recovery stampcharged coke making technology was Coke Making: Most Efficient Technologies for GreenhousePDF On Jul 11, 2018, Sandra Lúcia de Moraes and others published Iron Ore Pelletizing Process: An Overview Find, read and cite all the research you need on ResearchGate(PDF) Iron Ore Pelletizing Process: An Overview
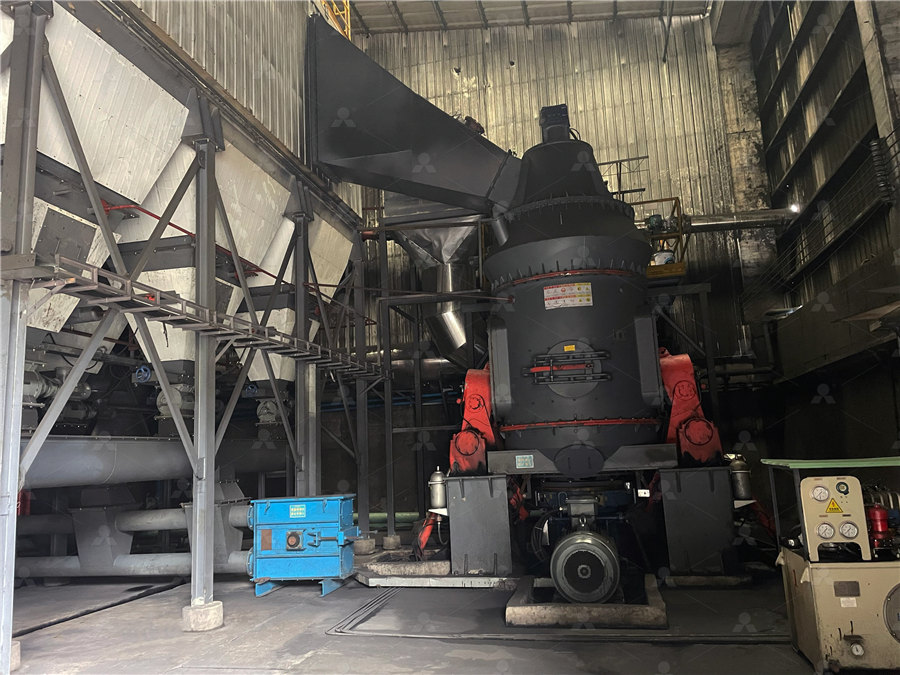
Pelletization of hematite and synthesized magnetite concentrate from
2021年10月1日 Pellets prepared from lowgrade BHQ using conventional beneficiation and magnetization roasting Pellet properties are compared as a function of induration temperature • Pellets of synthesized magnetite at 1250 °C and hematite at 1360 °C have CCS > 250 kg/pellet, porosity > 25% Synthesized magnetite pellet achieved 349% RDI, 8021% RI and 1938% SI2024年3月17日 Steel making is a sophisticated process that turns iron ore into steel, involving methods like the Blast Furnace and Electric Arc Furnace to produce various grades of steel The industry emphasizes sustainability by using additives and recycled materials while ensuring quality through rigorous testing for diverse applicationsA Visual Guide: Steel Making Process Chart Cabaro Group2022年8月22日 The hematite ore powder was stored in a hightemperature vacuum drying oven and dehydrated for at least 48 h before the experiment The microstructure of hematite ore powder in Fig 2 indicated the lack of cracks and holes on the sample surface before the reaction P Fig 2 Microstructure of the hematite ore powder 22Kinetic analysis of iron ore powder reaction with 2012年6月1日 It can be seen that the iron ore has characteristics of multicomponent and low grade And the size of ore powder is 90% passing 74 pm , determined by laser granulometer The crystalline phases were investigated by powder XRD technique, using CuKa radiation at the scanning rate of 8"/min from 10" to 90"Comprehensive Utilization of Paigeite Ore Using Iron Nugget Making
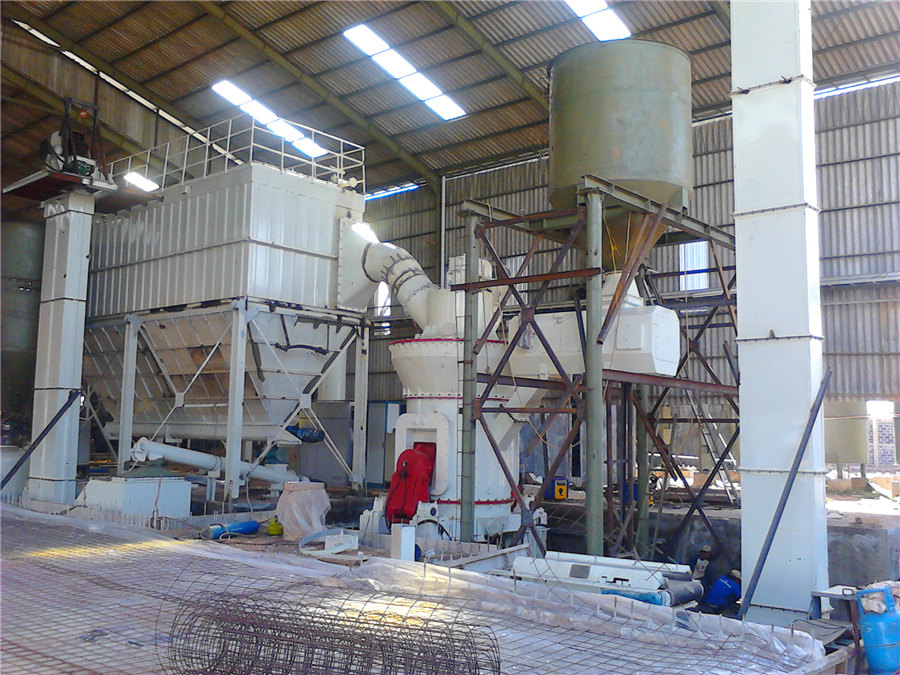
Copper Metallurgy SpringerLink
2023年6月8日 Copper oxide ore, or lowgrade copper sulfide ore exploited from the surface layer or corners in the mining of copper sulfide deposits, is difficult to concentrate through mineral dressing These copper resources can only be extracted economically by hydrometallurgical coppermaking processes including mainly three procedures, namely, leaching 2024年3月16日 The sintering process is an intricate system with a protracted process flow The steps in the manufacturing line are primarily composed of the ingredients and mixing process, the sintering operation process, and the treatment of the sintered ore [39, 40]22 Important parameters and characteristics of sintering process As shown in Fig 2, all variables affecting Application of deep learning in iron ore sintering process: a 2013年4月25日 Issues in Informing Science and Information Technology Volume 10, 2013 Planning an Iron Ore Mine: From Exploration Data to Informed Mining Decisions J E Everett Centre for Exploration Targeting, University of Western Australia, Nedlands, WA, Australia AbstractPlanning an Iron Ore Mine: From Exploration Data to Sintering and lumping of iron ore by iron ore sintering technology is a 42 necessary process in order to maintain stable blast furnace operation It greatly reduces production 43 fluctuations and, more importantly, expands the sources of obtaining various types of iron ore, 44 making it possible to utilize lowgrade iron ore 45 Fig1 Change CO Reduction Process Technology and Development of
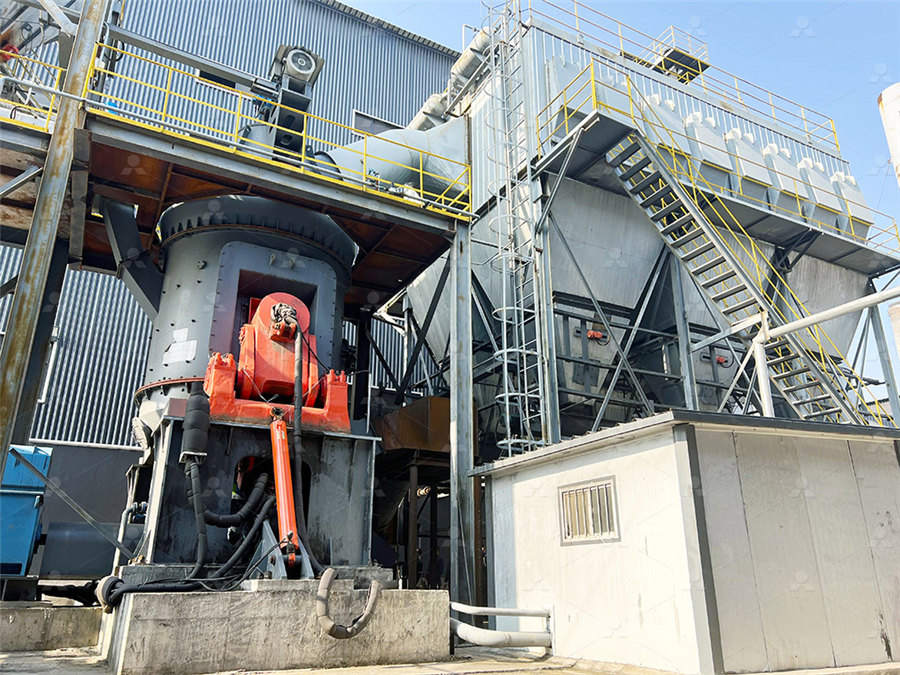
Mine Planning and Optimisation Techniques Applied in an Iron Ore
2019年11月30日 The fiveyear schedule indicate the average stripping ratios that is required in order to make sure that there is enough waste stripping to expose the ore From the 12month rolling plan, stripping ratios and summarised tonnes per month are calculated and shown as profiles for better interpretation and understanding⑥ Adapt measures to local conditions, plan optimization The production line construction plan is designed by the professional team of SBM micropowder technology according to the data of the field examination room and combined Stone Powder Making Machine SBM Ultrafine 2022年7月30日 In order to study in depth the differences in basic characteristics between iron ore fines commonly used by a steel company, and guide the sintering performance plant to choose the best ore (PDF) Study on the Basic Characteristics of Iron Ore Powder The first step in the overall powder metallurgy (PM) process is making metal powders There are four main processes used in powder production: solidstate reduction, atomization, electrolysis, and chemical SolidState Reduction In solidstate reduction, selected ore is crushed, typically mixed with carbon, and passed through a continuous furnaceMaking Metal Powder MPIF
.jpg)
Sintering Properties and Regression Analysis of Imported Iron Ore Powder
2022年11月24日 In order to reduce the sintering allocation scheme and lower the cost of allocation, two semilignite ores with similar properties and large price differences were selected for blending to achieve the purpose of complementary advantages The sintered ore specimens were studied by using FactSage71, an infrared sintering furnace, and regression analysis 2024年8月1日 the reduction reaction, iron ore powder had the highest reaction rate, with iron ore powder reduced by approximately 0055%/s The higher the temperature, the greater the reaction rate Subsequently, the reaction rate of iron ore powder rapidly decreased; at this stage, the reaction rates between different temperatures were insignificant, and theEffect of temperature and reaction path interaction on 2024年9月5日 The disposal of Iron ore tailings Powder (IP) is the primary concern for numerous steel industries Similarly, natural zeolite, a significant byproduct of volcanic eruptions, pollutes the Optimization Studies of Iron Ore Tailings Powder and 2022年4月20日 the leading arm of science and technology policymaking in China Perhaps, most impor tantly, the plan served as the basis for a new phase of largescale Soviet technological aid to China In other words, the 1956 plan helped make science and technology a key part of nationbuilding and state formation in the People’s Republic of ChinaThe Chinese developmental state during the Cold War:
.jpg)
Flash Ironmaking SpringerLink
2022年4月20日 At the University of Utah, an alternative technology to meet these demands, called the FIT, has been under development (Sohn and Mohassab 2016) This novel technology eliminates the highly problematic coke making and pelletization/sintering steps by directly utilizing iron ore concentrate, which is in abundance in the USA and elsewhere2023年12月11日 The traditional ironmaking technologies (including coking, sintering, pelletizing, and BF ironmaking process) are carbonintensive, which makes the industry a significant contributor to global CO2 emissions Hydrogen replacement of carbon in steelmaking processes is a sustainable way to reduce CO2 emissions First, the reduction thermodynamics and HydrogenBased Reduction Technologies in LowCarbon This process helps to increase the surface area of the ore, making it more accessible for subsequent grinding Grinding, on the other hand, involves further reducing the size of the crushed ore into a fine powder The crushed ore is Gold Refinery Process: From Raw Material to 2023年10月9日 The production of iron sponges by FIOR was 43% of the total production in 1983 The iron ore powder with a particle size of less than 5 mm passes through 4 fluidized bed reactors in turn And the ore powder is preheated to 760 °C in the first stage by natural gas or coal gas, where the reduction reaction by hightemperature gas occurs [30, 32]Development and Problems of Fluidized Bed Ironmaking
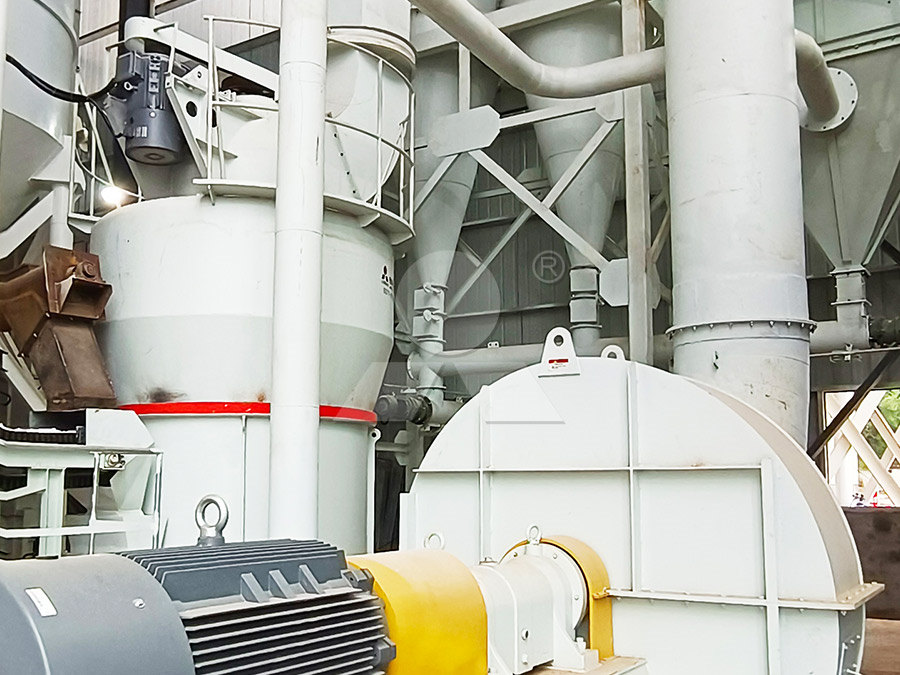
The characteristics and mechanism of ultrafine iron ore powder
The ultrafine iron ore powder produced through mechanical activation is a crucial technology for achieving lowtemperature ironmaking This study employs thermogravimetric analysis to investigate the reduction properties of coal powder to iron 2023年10月9日 It is the process in which iron ore powder is reduced in a fluidized bed The main processes include Novalfer process, HIron reduction process, high iron ore briquette (HIB) process, and FIOR process With progress in industrial technology, users presented higher requirements for quality and varieties of steel, and the electric furnace Direct Reduction Ironmaking SpringerLink2022年2月17日 As a typical refractory iron ore, the utilization of limonite ore with conventional mineral processing methods has great limitations In this study, suspension magnetization roasting technology was developed and utilized to recover limonite ore The influences of roasting temperature, roasting time, and reducing gas concentration on the magnetization roasting Clean Utilization of Limonite Ore by Suspension 2022年3月1日 The iron ore slimes, which contain low iron content with high gangue minerals like kaolinite, gibbsite, and quartzite, cannot be used directly for iron production The present study focuses on utilization of iron ore slimes without beneficiation by blending with highgrade fines for making iron ore pellets The pellets were prepared by adding Analysis of iron ore pellets properties concerning raw
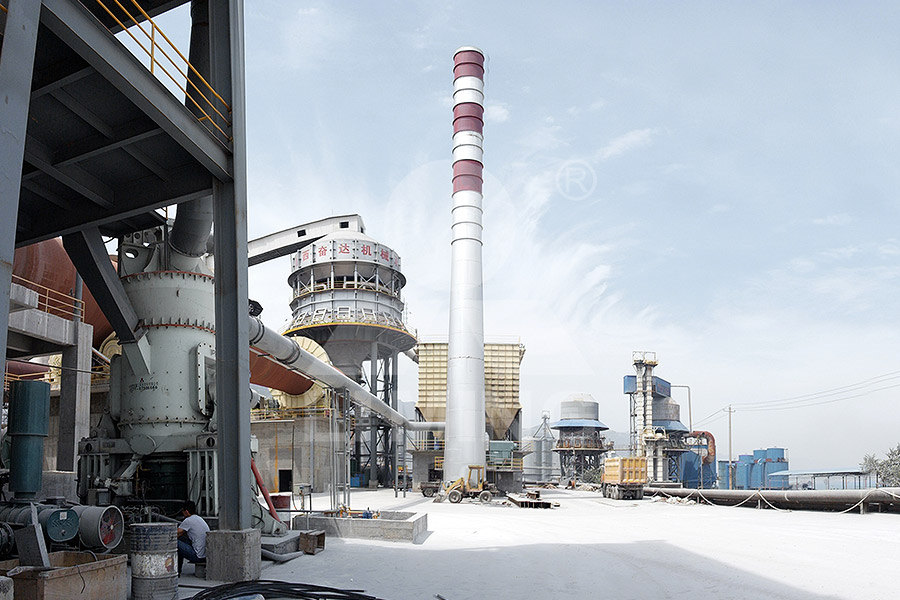
Sintering: A Step Between Mining Iron Ore and Steelmaking
2019年6月11日 World resources are estimated to be greater than 800 billion tons of crude ore containing more than 230 billion tons of iron The only source of primary iron is iron ore, but before all that iron ore can be turned into steel, it must go through the sintering process Sinter is the primary feed material for making iron and steel in a blast furnaceBased on the progress in biomass technology, this study investigates the utilization of landscaping residues (wood waste) subjected to thermal treatment as a reductant for iron ore, to produce two types of C/O (the ratio of carbontooxygen is the molar ratio of carbon in ICCB to oxygen content in iron oxide) iron ore powdergreen carbon Study on strength and reduction characteristics of iron ore powder 2024年8月2日 The ore is passed through crushers, which break it down into smaller chunks These chunks are then screened to separate the ore from waste material Grinding The crushed ore is then ground into a fine powder This step is crucial as it increases the ore's surface area, making it easier to extract the iron during subsequent processesThe Process of Making Iron: From Ore to Product Blogs