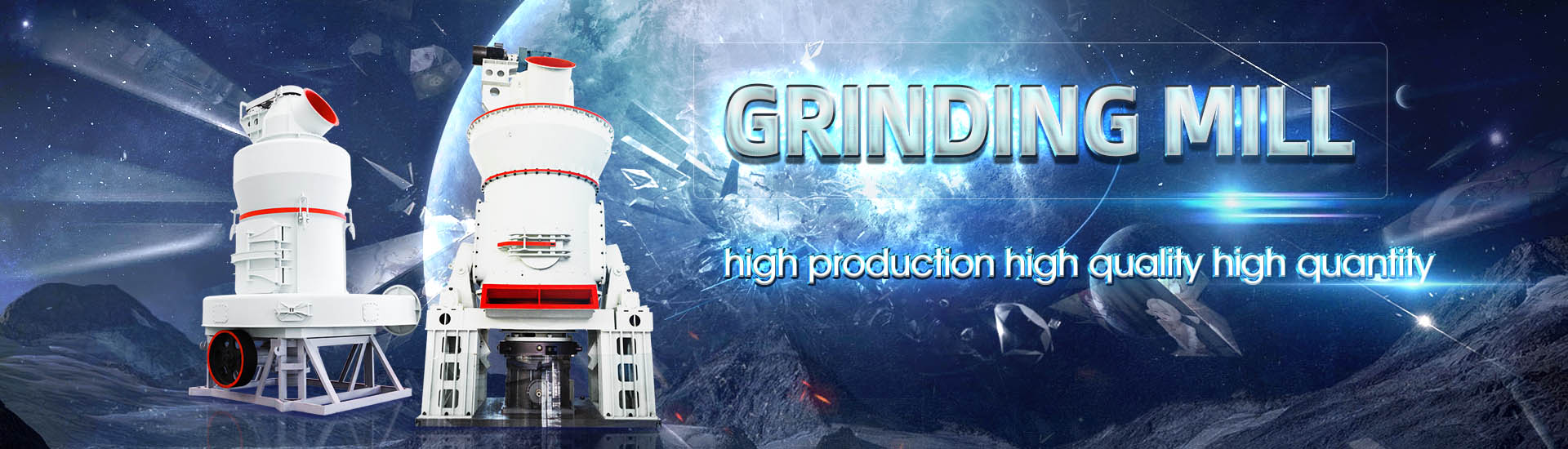
Coal grinding cement process, gypsum
.jpg)
Reactivity activation of waste coal gangue and its impact on the
2020年2月20日 Mechanical activation is a physicochemical change of coal gangue by grinding or ball milling processes Grinding not only reduces the particle size and dehydrates clays, but Highly energy intensive unit operation of coal grinding is intended to provide a fine coal as a fuel for calcination and clinkerization Coal grinding operation is monitored for following parameters Coal Grinding Cement Plant OptimizationGrinding and calcining of gypsum with Pfeiffer grinding plants TEXT Eckhard Sander, Gebr Pfeiffer SE, Kaiserslautern/Germany For the production of plaster products natural gypsum, synthetic gypsum or a mixture of both are calcined Depending on the production process two different modifications of the hemihydrate CaSO 4 x ½ H 2 O are obtained Grinding and calcining of gypsum with Pfeiffer grinding plants2016年3月1日 Next, in November 2014, Titan Cement ordered a Gebr Pfeiffer SE type MPS 2800 BK vertical roller mill for coal grinding, to be set up at line 1 at its Beni Suef plant In January 2015, Suez Cement, Italcementi’s Egyptian arm, said that it would spend US$84m during the year to convert its Helwan and Tourah 2 cement plants to use coalCoal for cement: Present and future trends

Everything you need to know about clinker/cement
Everything you need to know about clinker/cement Grinding if You read and understand this article , you will be ready to be a cement grinding area manager FEED AND FEED SYSTEM Feed Temperature Plants with satellite coolers 2020年8月25日 A full cement production process includes the cement crushing process, raw mill process, clinker process, and cement grinding process, cement packing process Coal Mill In Cement Plant; Cement Roller Press; The clinker is taken from the clinker silo and sent to the feed bin where it is mixed with gypsum and additives before Cement Production Process Cement Manufacturing Process AGICO CEMENT2023年1月1日 Portland cement is a fine powder produced by grinding Portland cement clinker Clinker along with up to 5% gypsum is ground together in a cement mill developed a process in which coal and/or Petcoke could be microground and an oil–coal mixture fired by a kiln originally intended for oil firing (Gulf Cement Co, Coal utilization in the cement and concrete industriesThe use of fossil fuels such as coal, natural gas, and oil is common in cement production, both as a fuel for the kiln and as a source of heat for other parts of the process which leads to CO2 emitted by combustionHowever chemical reactions happening in the kiln (calcination) are also responsible for up to 60% of the total of emissions of the cement production process [PCA]Cement Production Demystified: StepbyStep Process and
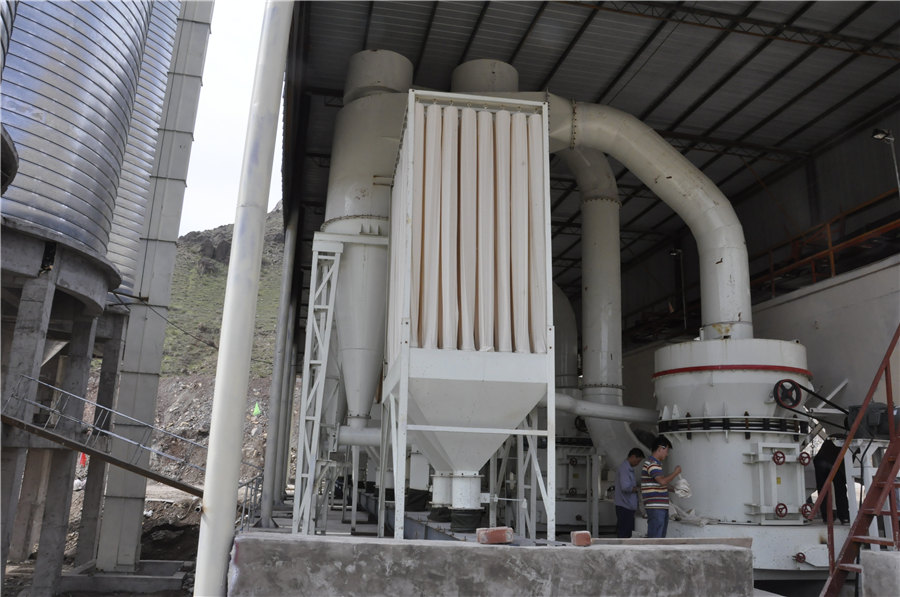
How Cement is Made Portland Cement Association
Some manufacturers grind the raw materials dry, while others use a wetgrinding process involving water Quarrying Cement manufacturers quarry raw materials including limestone, clay, The clinker keeps cooling and a ball mill grinds it with gypsum or other ingredients into fine cement—about 150 billion grains per poundSummary: The main trends concerning grinding processes in the cement industry are still higher efficiency, reduction of the power consumption and system simplicity In the case of new orders, vertical mills have increased their share to over 60 % and ball mills have fallen to less than 30 % It is somewhat surprising that the number of different grinding processes and mill types used Grinding trends in the cement industry Cement Lime GypsumCement grinding process The whole workflow of the cement grinding plant is as follows: the cement clinker, gypsum, and mixture in the cement silo are mixed by the belt conveyor in a certain proportion and transported to the cement roller press, cement mill or group of them for grindingCement Grinding Plant Overview Cement Grinding Unit AGICO CementFinish milling is the grinding of clinker to produce a fine grey powder Gypsum (CaSO 4) is blended with the ground clinker, along with other materials, to produce finished cement The gypsum controls the rate of hydration of the cement in the cementsetting process Significant amounts of electrical energy are required for millingThe Cement Production Process
.jpg)
The role of gypsum in cement Indian Cement Review
2019年1月11日 It can be seen from above that in cement grinding process if the cement grinding temperature is not appropriately controlled the added gypsum would convert to hemi FGD gypsum: Generated in fluidised gas de 2023年7月10日 Cement manufacturing is a significant industrial activity that plays a vital role in the construction sector However, the process of cement production is associated with various environmental Cement Manufacturing Process and Its Environmental 2023年12月20日 Cement manufacturing is a complex process that begins with mining and then grinding raw materials that include limestone and clay, to a fine powder, called raw meal, which is then heated to a sintering temperature as The Cement Manufacturing Process Thermo Fisher 2016年10月5日 In this chapter an introduction of widely applied energyefficient grinding technologies in cement grinding and description of the operating principles of the related equipments and comparisons over each other in terms of grinding efficiency, specific energy consumption, production capacity and cement quality are given A case study performed on a EnergyEfficient Technologies in Cement Grinding IntechOpen
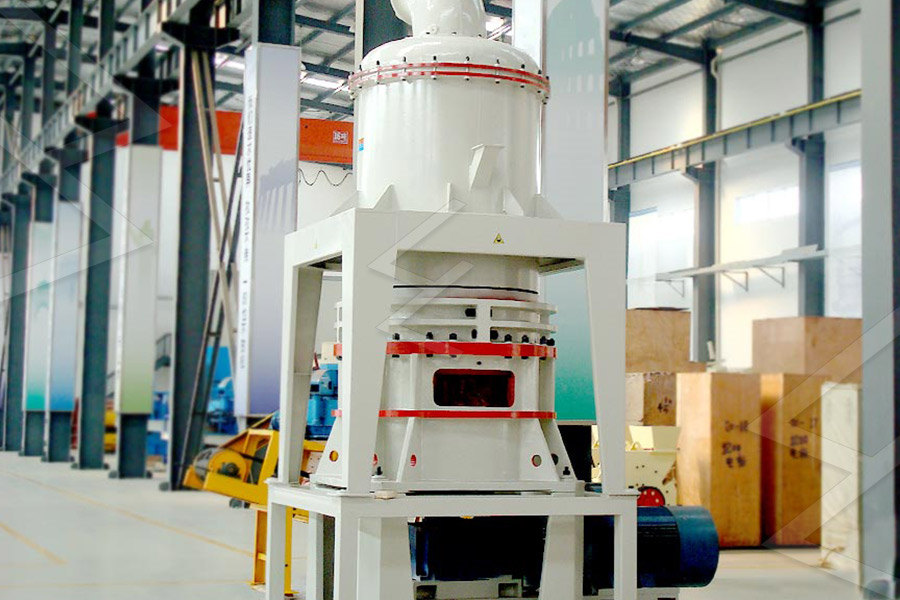
What Do You Know About Wet Process Of Cement Production
2024年1月17日 According to statistics, the dry cement production line grinding operation consumes Power accounts for more than 60% of the power of the whole plant, of which raw material grinding accounts for more than 30%, coal grinding accounts for about 3%, and cement grinding station account for about 40%2022年7月18日 Gypsum is indispensable to cement as it regulates the setting time of cement and impacts its strength We look at the various aspects of sourcing and processing of gypsum that makes this retarding agent of cement an important component in the manufacturing process while being a sustainable ingredient Gypsum is a soft sulphate mineral composed []The Power of Gypsum Indian Cement ReviewPortland Pozzolana Cement Manufacturing Process Portland pozzolana cement shall be manufactured by mixing and intergrinding Portland cement clinker, pozzolanic materials, and gypsum The manufacturing process is approximately the same as ordinary Portland cement, which can be divided into four processes: raw material crushing, raw material PPC Cement Manufacturing Process Portland Pozzolana Cement GYPSUM BASED PRODUCTS (GYPSUM POWDER, GYPSUM BOARD PVC LAMINATED GYPSUM CEILING TILES (INTEGRATED PRODUCTION UNIT) CONCRETE BLOCK AND READY MIX CONCRETE Clinker Grinding for Cement Gypsum From Synthetic Gypsum PVC Solvent Cement(CPVC UPVC) Composite Marble Slabs PVC Solvent Cement Non Abrasive, Asbestos, Cement, Refractory Products, Gypsum, Marble
.jpg)
Resistance to Grinding and Cement Paste Performance of Blends
2021年4月19日 Grinding of finished cement is performed in a single stage, intergrinding materials with very different grindabilities This intergrinding process has many different interactions among the different components of the finished cement In a context of developing more sustainable and less energy intensive processes, it is important to understand the process can be divided into the following primary components: raw materials acquisition and handling, kiln feed preparation, pyroprocessing, and finished cement grinding Each of these process components is described briefly below The primary focus of this discussion is on pyroprocessing operations, which116 Portland Cement Manufacturing US Environmental 2024年1月11日 The 5step process to pulverize coal efficiently The coal pulverization process involves a precise sequence of steps Each is systematically designed to convert raw coal into a fine, efficient powder But How to Process Coal into Pulverized Coal in 5 Steps?Cement raw material; Cement and granulated blastfurnace slag; Coal and petcoke; Gypsum; Clay; Limestone; Quicklime and lime hydrate; Mining/Ores/Minerals; Other materials; References; Grinding Plants Grinding, drying, classifying Gebr Pfeiffer
.jpg)
Grinding process is a critical stage in cement
2023年8月21日 • Cement Grinding: After the clinker is cooled, it is finely ground with gypsum and other additives to produce cement The grinding process involves reducing the clinker particles to a specific fineness, typically 2011年10月21日 Description of the inerting process in coalgrinding systems Inerting systems avoid dust explosions and smouldering fires in silos, coal mills and filter equipment by creating an inert atmosphere In the case of abnormal levels of carbon monoxide (CO), oxygen or heat, the inerting process is initiated automatically through a processcontrol Emergency inerting systems for coalgrinding applications Global Cement1 Introduction Two mill systems are employed for most coal grinding applications in the cement industry These are, on the one hand, vertical roller mills (VRM) that have achieved a share of almost 90 % and, on the other hand, ball mills whose share decreased to just over 10 %MPS mills for coal grinding Cement Lime Gypsum ZKGThe dry process cement production line is widely used in cement industry it is generally divided into the following processes: prehomogenization of raw materials, homogenization of raw materials, clinker firing, cement grinding, and so on Get A free quote! Skip to content +86 Coal Mill In Cement Plant; Cement Roller Press; Cement Separator;Dry Process Of Cement Production 3005000TPD AGICO CEMENT
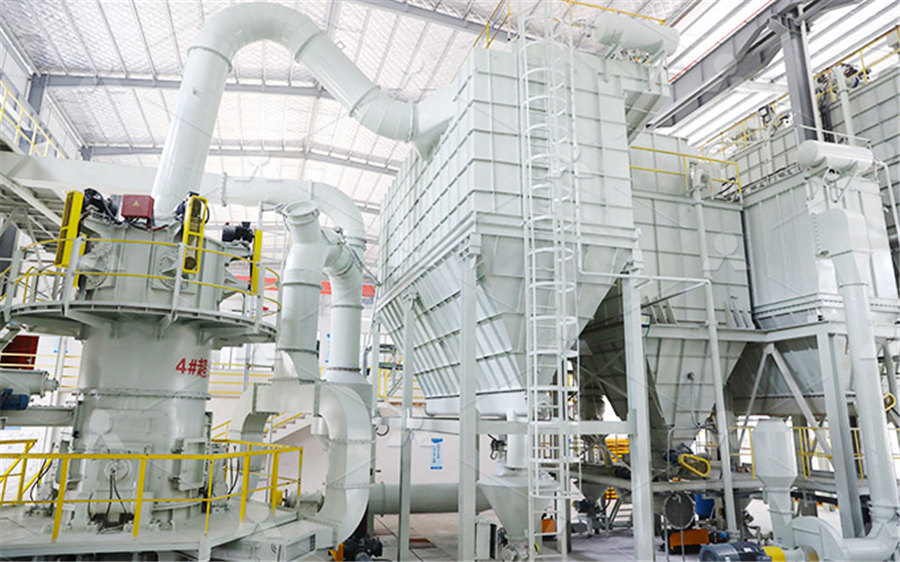
6 Cement Equipment For Dryprocess Cement Production Line
2023年12月26日 As we all know, the dryprocess cement production line is commonly used in the cement industry The new type of dryprocess cement production process includes four main sections: Prehomogenization of raw materials, homogenization of raw materials, clinker firing, cement grinding, etc Raw material conveying system The raw material, including limestone, 2022年7月15日 Gypsum cements possess considerably greater strength and hardness as compared to nongypsum cement Water required in gypsum based cement for the hydration process is less The use of gypsum as an additive in cement ranges from 25 to 5 per cent In its natural form, gypsum can be found as thick layers in shale and as attractive crystals No The Future of Gypsum Indian Cement Review2023年8月21日 ICR looks at the inner workings of grinding mills in the cement industry to understand the technological advancements that are reshaping the landscape against the foreground of sustainability Innovations to enhance the grinding processes are aimed at minimising their environmental footprint while increasing efficiency and performance In CuttingEdge Grinding Solutions Indian Cement ReviewCement Manufacturing Coal grinding mills are used in the cement manufacturing industry to grind various materials, including clinker and gypsum, into fine powders that are used to produce cement Coal grinding mills are critical components of the cement manufacturing process, ensuring efficient and consistent grinding of materials Mining IndustryWhat is a Coal Grinding Mill
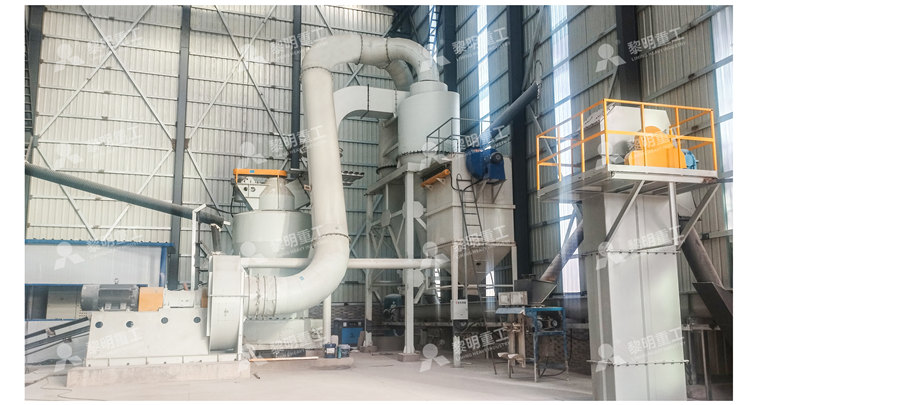
Coal utilisation in the cement and concrete industries
2013年1月1日 As of 2009, world cement output was estimated at 304 billion tonnes (metric tons) 6 China represents 561% of the world’s output while the USA represents 20% 7 Fuel used by the US cement industry is 60% coal, 13% petroleum coke, and 3%, natural gas 8 According to the US Energy Information Administration (EIA), the manufacture of cement Also, coal is utilized to make cement clinkers Over the previous months, the price of coal has risen by over 50% on the global market due to intensified carbon emission taxes 3 Energy Costs Energyintensive processes like grinding, kiln operations, and quarrying of raw materials are all necessary for the production of cementCement Prices – Historical Graph [Realtime Updates]2016年1月20日 Fig 4 shows material flows during the cement grinding Clinker, gypsum, and additives are matched in required proportions by a weigh feeder, after which they are conveyed to the mill that performs the remaining grinding The grinding process occurs in a closed system with an air separator that divides the cement particles according to sizeAnalysis of material flow and consumption in cement production process 2014年1月1日 Two mill systems are employed for most coal grinding applications in the cement industry These are, on the one hand, vertical roller mills (VRM) that have achieved a share of almost 90% and, on (PDF) MPS mills for coal grinding ResearchGate
.jpg)
Cement manufacturing process PPT Free Download SlideShare
2014年6月10日 This document discusses Portland cement and the cement manufacturing process It begins with an overview of what cement is and how it is used to make concrete It then describes the industrial process for manufacturing cement, involving grinding raw materials like limestone and clay at high temperatures in a kiln to form clinker, which is then pulverized with Stage 2: Grinding, Proportioning, and Blending The crushed raw ingredients are made ready for the cementmaking process in the kiln by combining them with additives and grinding them to ensure a fine homogenous mixture The composition of cement is proportioned here depending on the desired properties of the cement Generally, limestone is 80%, and the remaining 20% How Cement is Made Cement Manufacturing ProcessLoesche has now sold two of its biggest coal/petcoke grinding mills for the cement industry in Mexico These are to be used in the cement plants of the group Cooperativa La Cruz Azul, SCL – on the one hand in the plant in the province of Hidalgo, 80 km north of Mexico City, and on the other in the Lagunas plant in the province of Oaxaca in southern MexicoTwo coal/petcoke grinding plants for Mexico Cement Lime Gypsum2024年8月20日 Uses of Gypsum in Cement Gypsum acts as a binding agent in the cement and controls various factors in it It is also used in the walls where fire protection is required since it has a natural fireresistance property Let’s look at its uses Hydration Process: Rate of hardening: During the final grinding process of the cement, gypsum is addedUses of Gypsum in Cement BricknBolt
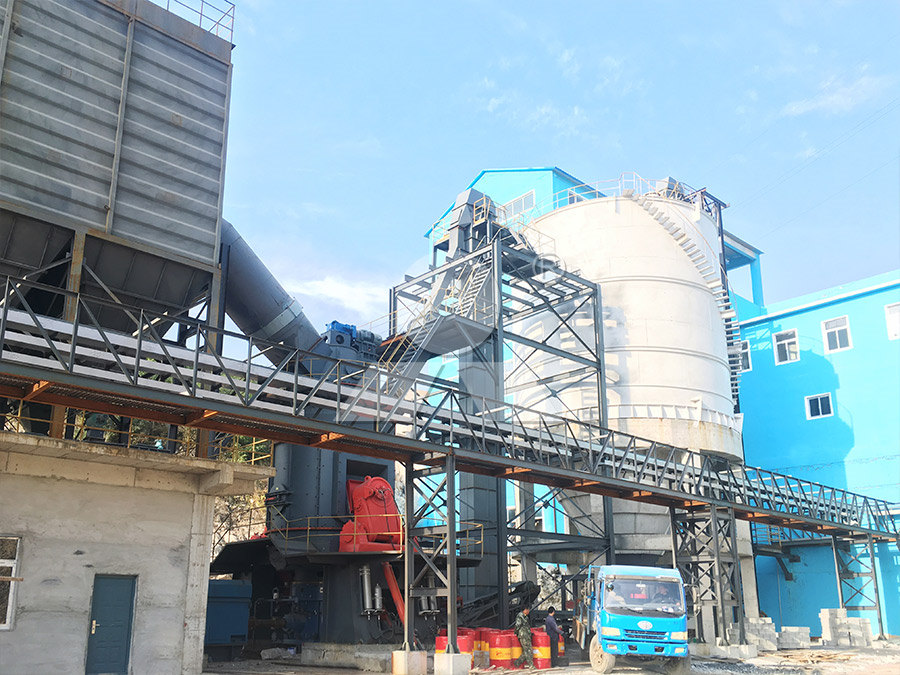
PFEIFFER MILLS FOR THE CEMENT INDUSTRY
7 // Almost any plant for the grinding of cement raw material is a combination of machines specially adapted to the particular physical properties of the material to be ground As a result, our plants work efficiently without any trouble » Highly efficient grinding, drying, and separating in one unit » Outstanding production capacities exceeding 1,400 t/h in one single mill2022年8月10日 Grinding might be an individual step in the cement production line but it is a crucial one, given the energy consumption and impact on the quality of output that it gives ICR explores how grinding methods have evolved with the help of technology and with the use of modernage grinding aids Grinding in the cement []Grinding: Smarter Solutions Indian Cement Review