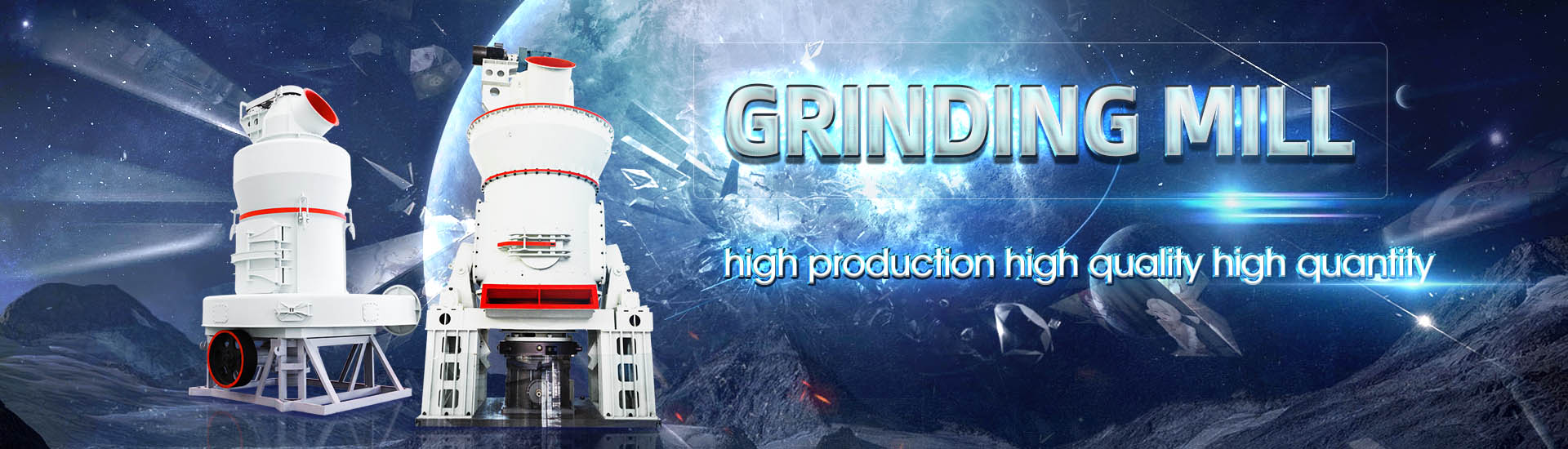
Iron sulfur equipment process flow
.jpg)
A critical review on the chelatediron desulfurization process
2024年7月1日 To address these issues and increase the high valueadded resource utilization of sulfur resources, we proposed a cleancycle process of chelatediron desulfurization process 2009年9月19日 The LOCAT® process is a liquid phase oxidation process based on a dilute solution of a proprietary, organically chelated iron in water that converts the hydrogen sulfide LOCAT Process Oil Gas Process EngineeringWith Merichem Technologies exclusive sulfur recovery technology, this patented liquid redox system uses a chelated iron solution to convert H 2 S into innocuous, elemental sulfur LOCAT® Advantages Can remove H 2 S from virtually any LOCAT® Sulfur Recovery Solution Merichem2019年8月23日 Sulfur attaches to metal ions, creating a number of significant sulfide ore minerals such as galena (lead sulfide), pyrite (iron sulfide), chalcocite (copper sulfide), and sphalerite (zinc sulfide) Mined sulfur is mostly from salt Sulfur Processing Equipment, Process Flow,
.jpg)
125 Iron And Steel Production US EPA
2015年9月10日 Iron is produced in blast furnaces by the reduction of iron bearing materials with a hot gas The large, refractory lined furnace is charged through its top with iron as ore, 2022年3月1日 Sintering of iron ores is an enormous energyintensive and resources consuming process Introducing a selective waste gas recirculation (SWGR) to the sintering process Model of an iron ore sinter plant with selective waste gas A hydrometallurgical HNO 3 process plant can be built with modular stainlesssteel equipment, ie, no titaniumlined autoclaves are required Hematite produced from sulfate solutions often Hydrometallurgical Processes for the Recovery of Metals 2008年4月1日 Sulfur flow for new generation steel manufacturing process is analyzed by the method of material flow analysis, and measures for SO2 emission reduction are put forward as Sulfur flow analysis for new generation steel manufacturing process
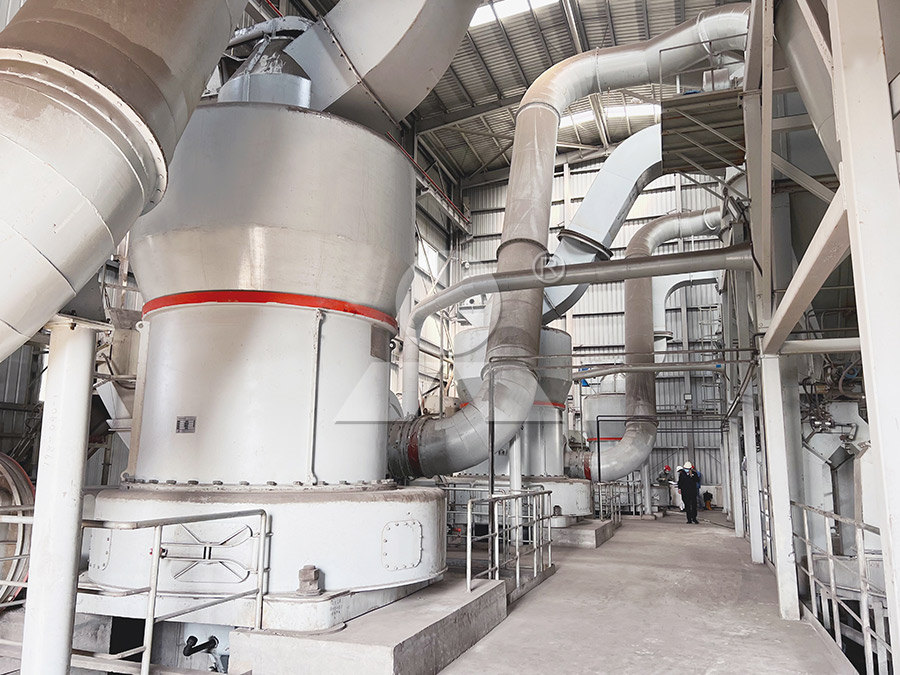
Sulphur removal in ironmaking and oxygen steelmaking
2023年8月26日 There are four stages where sulphur can be removed: in the blast furnace (BF), during hot metal (HM) pretreatment, in the converter and during the secondary metallurgy 2009年9月19日 The LOCAT® process is a liquid phase oxidation process based on a dilute solution of a proprietary, organically chelated iron in water that converts the hydrogen sulfide to water and elemental sulfur The process is not reactive to CO2 A small portion of the chelating agent degrades in some side reactions and is lost with the precipitated sulfurLOCAT Process Oil Gas Process Engineering2023年1月20日 The iron flow battery’s electrolyte is also nontoxic, unlike some other flow battery chemistries, such vanadium, where vanadium pentoxide is dissolved in sulphuric acid Meanwhile NGK said that its devices went through Iron flow, sodiumsulfur battery technologies at 2022年3月1日 Introducing a selective waste gas recirculation (SWGR) to the sintering process reduces the energy consumption, stack gas volume flow, and sulfur dioxide emissions of an iron sinter production Simulating this complex process in flowsheet simulations of integrated iron and steelworks is a fast and costeffective opportunity to validate new Model of an iron ore sinter plant with selective waste gas
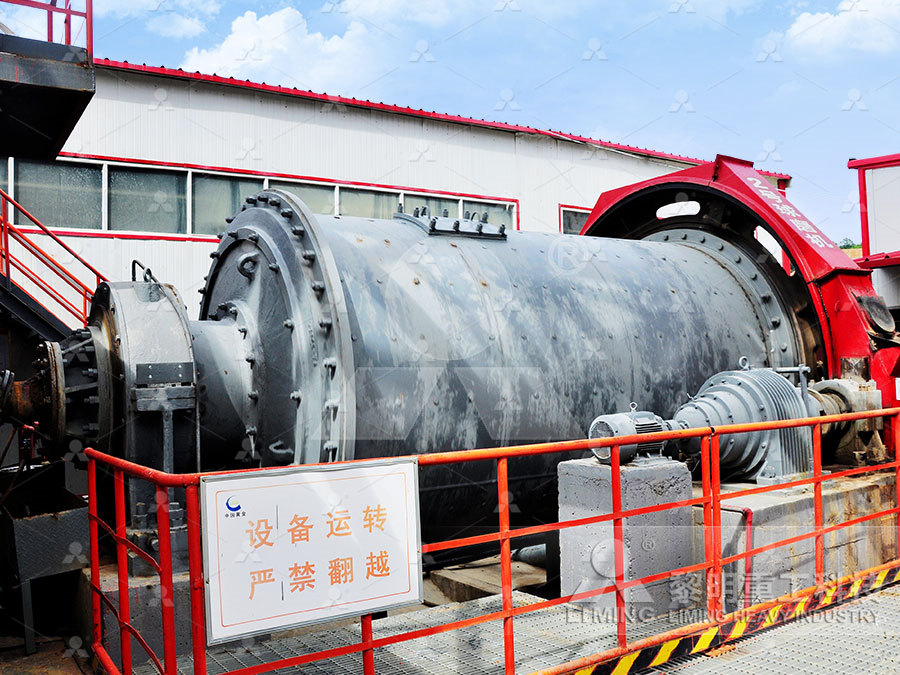
Direct Reduced Iron and its Production Processes – IspatGuru
2013年3月16日 Feed material for the DR process is either sized iron ore of size ranging from 10 mm to 30 mm or iron ore pellets of size ranging from 8 mm to 20 mm produced in an iron ore pellet plant The gas based process uses a shaft furnace for the reduction reaction The coal based process uses any one of the four types of reactors for the reduction Download scientific diagram Sulfuriodine cycle process flow diagram from publication: High Efficiency Generation of Hydrogen Fuels Using Nuclear Power OAK B188 High Efficiency Generation of Sulfuriodine cycle process flow diagram ResearchGate2022年9月1日 1 Introduction The sulfur components in the oil (elemental sulfur, hydrogen sulfide and organic sulfides) can cause serious corrosion damage to refinery equipment, storage facilities and transport pipelines during the processing of high sulfur oil, which results in frequent serious accidents caused by oxidative spontaneous combustion of iron sulfide (Hughes et al, Oxidative selfheating modeling of iron sulfides during the 2020年6月10日 In present application point of view of iron, steel is the most important product, followed by cast iron Wrought iron is used in very small quantity for ornamental purposes Blast furnace iron making is the most popular process for extraction of iron from its ores Other wellknown processes are EAF and Direct Reduction Iron (DRI) processesIron and SteelMaking Process SpringerLink
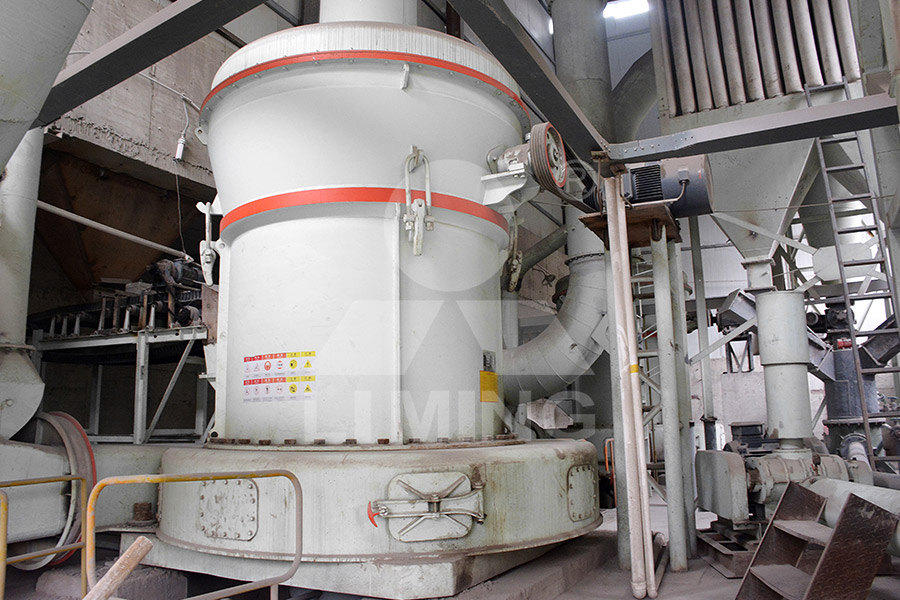
Optimized Production of High Purity Sulphuric Acid via Contact Process
2023年5月29日 Figure 1: Complete Process Flow Diagram of the Sulphuric Acid Production Process Figure 1 is a sli ght modification of a s implified H 2 SO 4 process flowsheet sh owing the 3 primaryPetroleum, natural gas and other fossil fuels contain significant amounts of sulfur When burned, the sulfur becomes sulfur oxides (SO x), which can cause significant damage to the environment and human healthTo minimize such damage and to ensure that finished products meet performance specifications, the sulfur is removed and transformed into useful chemicals, Sulfur Removal and Recovery SpringerLink6 天之前 ROTARY DRUM DRYERS COOLERS As a wet process, pelletizing typically requires a drying step This is frequently carried out in a rotary dryer, a highcapacity dryer that utilizes a cascading motion to dry pellets, while also rounding and polishing them as they tumble through the drumIn some cases, a rotary cooler may follow the dryer to cool material prior to Pelletizing Plant Equipment Process Development2021年11月1日 Ironsulfur (Fe–S) clusters are among the most common cofactors observed across nature and comprise the largest class of metalloproteins These clusters are structurally diverse, existing in simple forms such as [1Fe–0S], where a single iron atom is coordinated by four cysteine groups, found in rubredoxins of sulfurmetabolizing archaea, and in complex Mitochondrial iron–sulfur clusters: Structure, function, and an
制粉项目-2023.11.17.jpg)
Enzymatic and Chemical In Vitro Reconstitution of IronSulfur Cluster
2021年7月23日 Ironsulfur (FeS) clusters are key cofactors for proteins involved in essential cellular processes such as DNA replication and repair, ribosome biogenesis, tRNA thiomodification, and coenzyme synthesis biology evidence were gathered to prove that the maturation of FeS proteins in living cells is a tightly controlled process that 2015年9月10日 lance with highpressure nitrogen The process duration varies with the injection rate, hot metal chemistry, and desired final sulfur content, and is in the range of 5 to 30 minutes 12514 Steelmaking Process — Basic Oxygen Furnaces In the basic oxygen process (BOP), molten iron from a blast furnace and iron scrap are refined125 Iron And Steel Production US EPA2024年11月14日 Exciting elements video containing the iron and sulfur reaction The demonstration video for iron and sulfur reaction can be found at 720 minutes It shows the exothermic reaction of two elements, iron and sulfur, to form the compound, iron sulfide The two solids are mixed and heated in a testtube (or ignition tube)Iron and sulfur reaction Experiment RSC Education2017年11月19日 Sulfuric acid manufacturing and process flow diagram Download as a PDF or view online for free The sulfur trioxide is then absorbed in concentrated sulfuric acid in an absorption tower to produce more sulfuric acid Read less (62%–78% H2SO4) Contact Process 2 Iron pyrite (FeS2) (Silicon free FeS2 contain about 534% S) Sulfuric acid manufacturing and process flow diagram PPT
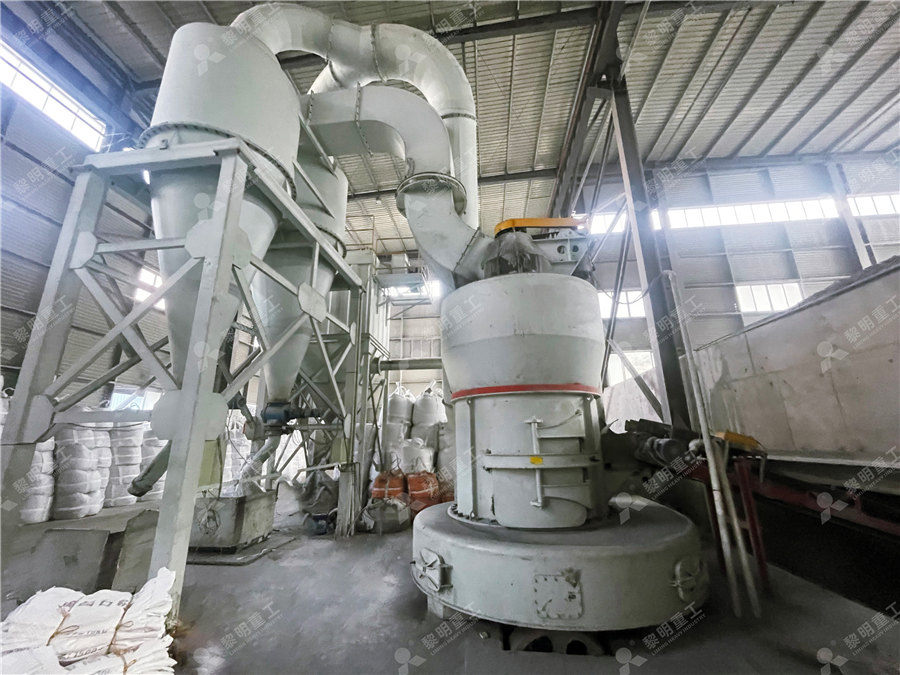
Coal based Direct Reduction Rotary Kiln Process – IspatGuru
2017年2月14日 The metallic iron in this process is produced by the reduction of iron oxide below the fusion temperature of iron ore (1535 deg C) by utilizing carbonaceous material present in the noncoking coal As the iron ore is in direct contact with the reducing agent throughout the reduction process, it is often termed as direct reduced iron (DRI)2019年7月19日 This process employs a twostage fluidized bed where natural gas is reformed for the production of the reducing atmosphere The iron fines are dried at 800 °C in a preheater system and then circulating fluidized bed (CFB) where they are metallized up to 70% by employing natural gas and air (Fig 823) The material is sent to the FB where it Direct Reduced Iron: Most Efficient Technologies for 2009年8月12日 Iron–sulphur (Fe–S) clusters have long been recognized as essential and versatile cofactors of proteins involved in catalysis, electron transport and sensing of ambient conditions Despite the Function and biogenesis of iron–sulphur proteins Nature2024年8月19日 Best for: Investmentminded buyers who want a proven, broadspectrum filter for sulfur and iron Not best for: The rare well with extreme sulfur concentrations over 8 ppm Pros: The build quality is impressive — you’ll never worry about what will break down next Eliminates the worst rotten egg odors — the smell completely vanished, and the water tastes greatSulfur Filters For Well Water 2024: 6 Expert Picks QWL
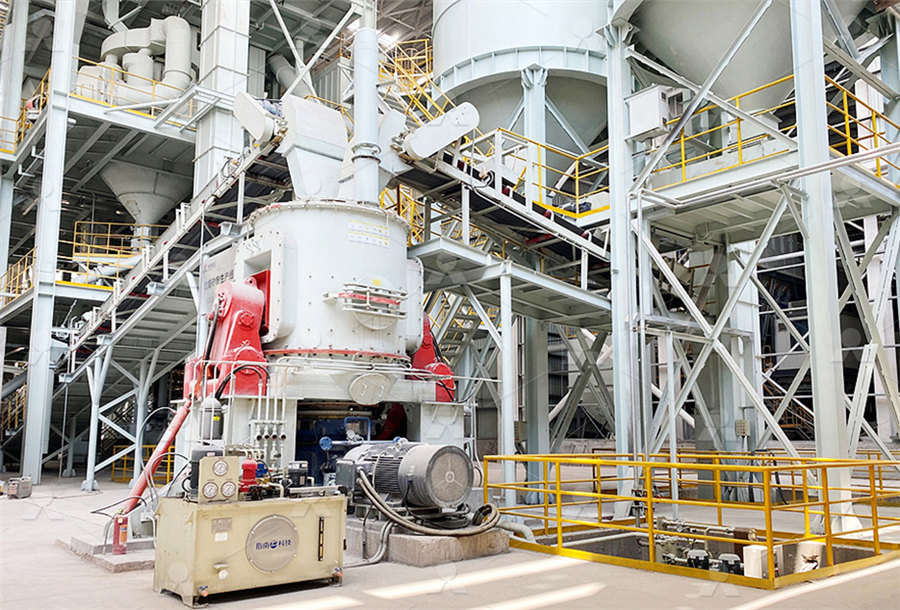
Direct Reduction Process an overview ScienceDirect Topics
21 Midrex Process Midrex is the most successful gasbased DR process; it is a continuous process It is basically a countercurrent process where a hot and highly reducing gas (95vol% of this gas mixture being hydrogen and carbon monoxide with a ratio of H 2:CO varying from 15 to 16) reduces lump iron ore or pellets to metallic iron as the metallic charge descends through Ironsulfur (Fe–S) clusters are essential cofactors most commonly known for their role mediating electron transfer within the mitochondrial respiratory chain aconitase inactivation slows the flow of metabolites through the TCA cycle, Mitochondrial iron–sulfur clusters: Structure, The blast furnace process has auxiliary equipment associated with it This auxiliary equipment and the gaseous pathways inside a blast furnace process are shown in Fig 2 The blast furnace process can be briefly described as follows Iron oxides, flux agents, and metallurgical coke are added to a skip car at the stock houseBlast Furnace Process an overview ScienceDirect Topics2023年1月1日 The iron and steel industry is an important cornerstone of the national economy In 2020, China produced 1053 billion tons of crude steel, accounting for 565% of the world's total output (Li et al, 2019)) In 2020, China's iron and steel industry emitted 574,000 tons of SO 2, 1,114,000 tons of NO x and 897,000 tons of particulate matter Since 2017, the air pollutant Multiprocess and multipollutant control technology for
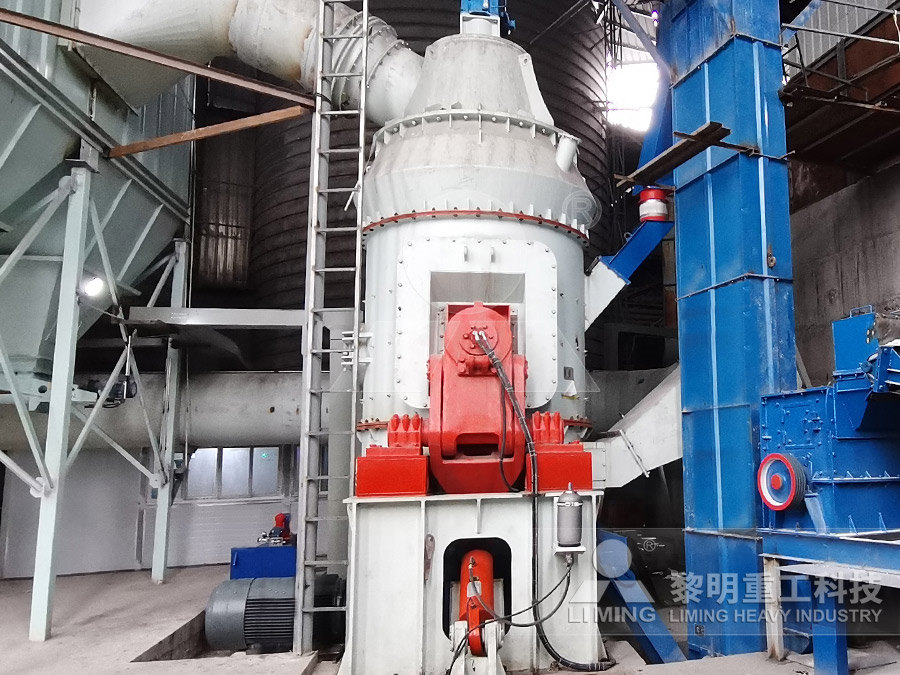
SRU Sulphur Recovery Process 911Metallurgist
2016年5月9日 SRU Process THE Sulfur Recovery FLOWSHEET The flowsheet above is a typical example of economical treatment of lowgrade sulphur by flotation Due to the variable nature of the sulphur in these deposits, testwork, such as is offered by the 911metallurgy Equipment Company and Laboratories, is recommended to determine the exact flowsheet 2024年2月29日 Sulfurdriven autotrophic denitrification (SADN) has demonstrated efficacy in nitrate (NO3−) removal from the aquatic environment However, the insolubility of elemental sulfur (S0) (maximum 5 μg/L at 25 °C) limited the NO3− removal rate In this study, we investigated the performance of a laboratoryscale S0packed bed reactor (S0PBR) under various volumetric Improved Performance of SulfurDriven Autotrophic MDPI2024年6月3日 The process involves sieving and sodium carbonate leaching, enabling significant sulfur reduction from 512 to 081% and simultaneous enrichment of iron content from 4712 to 5527% The sulfur content in the treated HPAL residue falls below the permissible level for the ironmaking industry, rendering it suitable for use as a lowgrade iron oreSulfur Removal and Iron Recovery from HighPressure Acid The natural gas is assumed to be methane with a lower heating value of 50 MJ/kg and a density of 06 kg/m 3 , and that the electricity is produced solely from natural gas assuming a gross energy Process flow diagram (PFD) of the H2SO4 production plant

Distribution of functional microorganisms and its significance for iron
2021年9月9日 The biogeochemical cycles of sulphur (S), iron (Fe) and nitrogen (N) elements play a key role in the reservoir ecosystem However, the spatial positioning and interrelationship of S, Fe and N cycles in the reservoir sediment profile have not been explored to a greater extent Here, we measure the gradients of Fe2+, SO42−, NO3−, NH4+, DOC, TC and TN in the pore The aim of this work is to investigate the level of damage to the heat exchanger in a Sulfur Recovery Unit (SRU) of a petroleum refinery The byproducts of oil refining are submitted to special Flow diagram of the Sulfur Recovery Unit (SRU)The ironsulfide redox flow battery systems can be advantageous for energy storage, particularly when the electrolytes have pH values greater than 6 Advantages Exhibit improved energy conversion efficiency and stability for energy storageIronsulfide Redox Flow Batteries PNNL2009年9月19日 The LOCAT® process is a liquid phase oxidation process based on a dilute solution of a proprietary, organically chelated iron in water that converts the hydrogen sulfide to water and elemental sulfur The process is not reactive to CO2 A small portion of the chelating agent degrades in some side reactions and is lost with the precipitated sulfurLOCAT Process Oil Gas Process Engineering
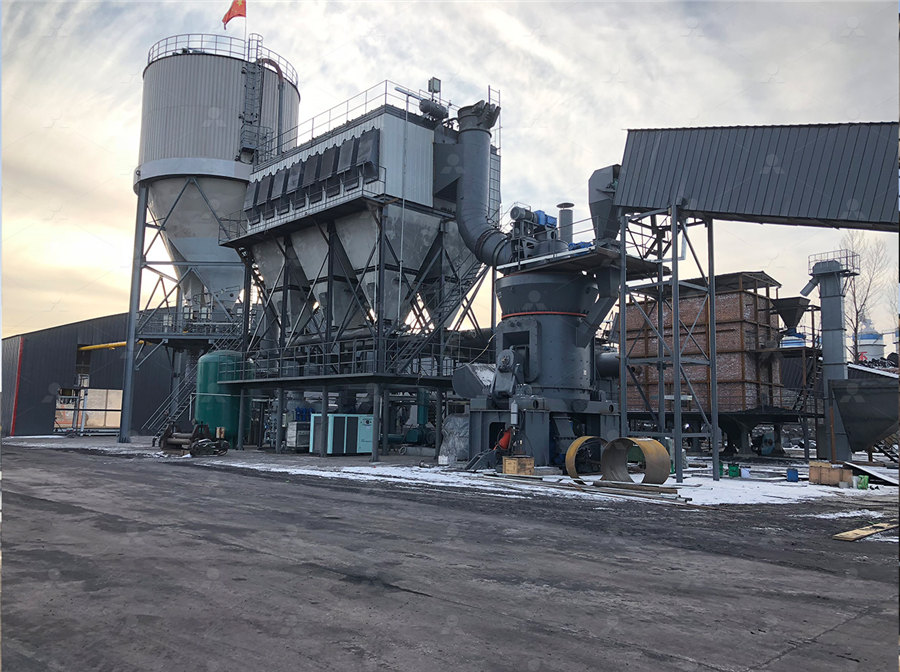
Iron flow, sodiumsulfur battery technologies at
2023年1月20日 The iron flow battery’s electrolyte is also nontoxic, unlike some other flow battery chemistries, such vanadium, where vanadium pentoxide is dissolved in sulphuric acid Meanwhile NGK said that its devices went through 2022年3月1日 Introducing a selective waste gas recirculation (SWGR) to the sintering process reduces the energy consumption, stack gas volume flow, and sulfur dioxide emissions of an iron sinter production Simulating this complex process in flowsheet simulations of integrated iron and steelworks is a fast and costeffective opportunity to validate new Model of an iron ore sinter plant with selective waste gas 2013年3月16日 Feed material for the DR process is either sized iron ore of size ranging from 10 mm to 30 mm or iron ore pellets of size ranging from 8 mm to 20 mm produced in an iron ore pellet plant The gas based process uses a shaft furnace for the reduction reaction The coal based process uses any one of the four types of reactors for the reduction Direct Reduced Iron and its Production Processes – IspatGuruDownload scientific diagram Sulfuriodine cycle process flow diagram from publication: High Efficiency Generation of Hydrogen Fuels Using Nuclear Power OAK B188 High Efficiency Generation of Sulfuriodine cycle process flow diagram ResearchGate
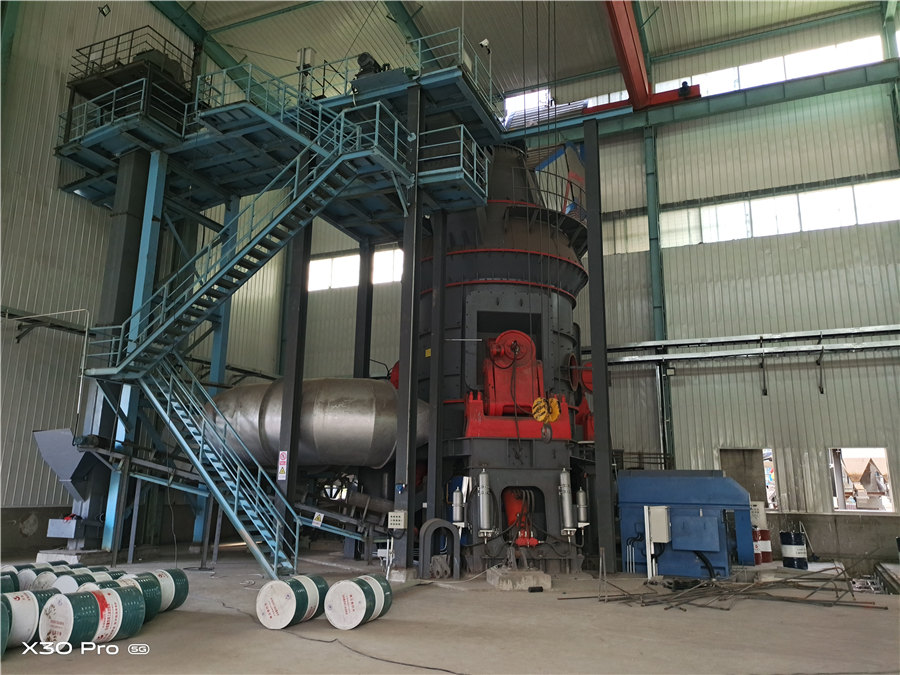
Oxidative selfheating modeling of iron sulfides during the
2022年9月1日 1 Introduction The sulfur components in the oil (elemental sulfur, hydrogen sulfide and organic sulfides) can cause serious corrosion damage to refinery equipment, storage facilities and transport pipelines during the processing of high sulfur oil, which results in frequent serious accidents caused by oxidative spontaneous combustion of iron sulfide (Hughes et al, 2020年6月10日 In present application point of view of iron, steel is the most important product, followed by cast iron Wrought iron is used in very small quantity for ornamental purposes Blast furnace iron making is the most popular process for extraction of iron from its ores Other wellknown processes are EAF and Direct Reduction Iron (DRI) processesIron and SteelMaking Process SpringerLink2023年5月29日 Figure 1: Complete Process Flow Diagram of the Sulphuric Acid Production Process Figure 1 is a sli ght modification of a s implified H 2 SO 4 process flowsheet sh owing the 3 primaryOptimized Production of High Purity Sulphuric Acid via Contact ProcessPetroleum, natural gas and other fossil fuels contain significant amounts of sulfur When burned, the sulfur becomes sulfur oxides (SO x), which can cause significant damage to the environment and human healthTo minimize such damage and to ensure that finished products meet performance specifications, the sulfur is removed and transformed into useful chemicals, Sulfur Removal and Recovery SpringerLink
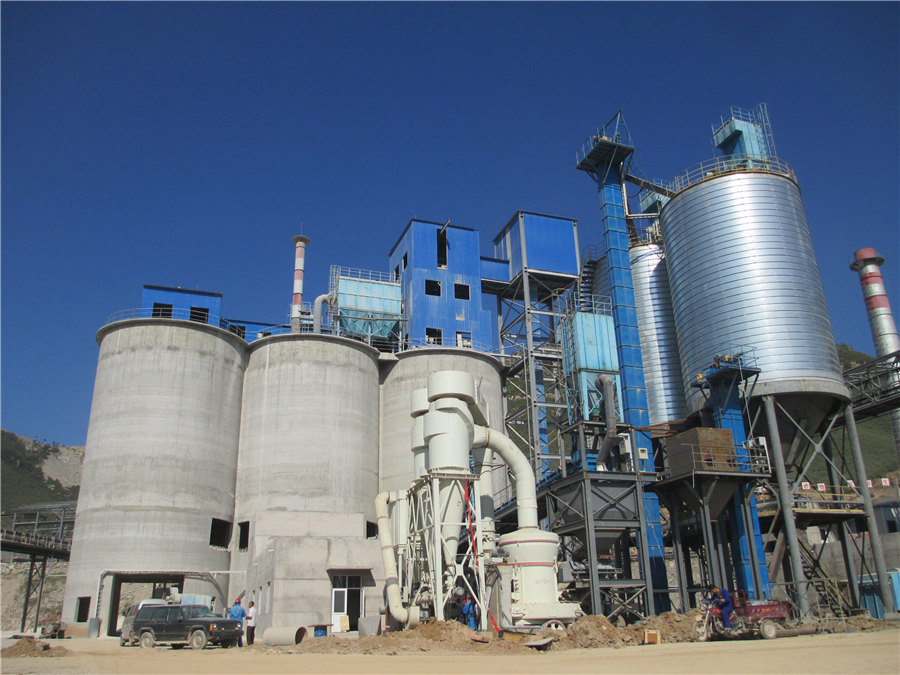
Pelletizing Plant Equipment Process Development
6 天之前 ROTARY DRUM DRYERS COOLERS As a wet process, pelletizing typically requires a drying step This is frequently carried out in a rotary dryer, a highcapacity dryer that utilizes a cascading motion to dry pellets, while also rounding and polishing them as they tumble through the drumIn some cases, a rotary cooler may follow the dryer to cool material prior to