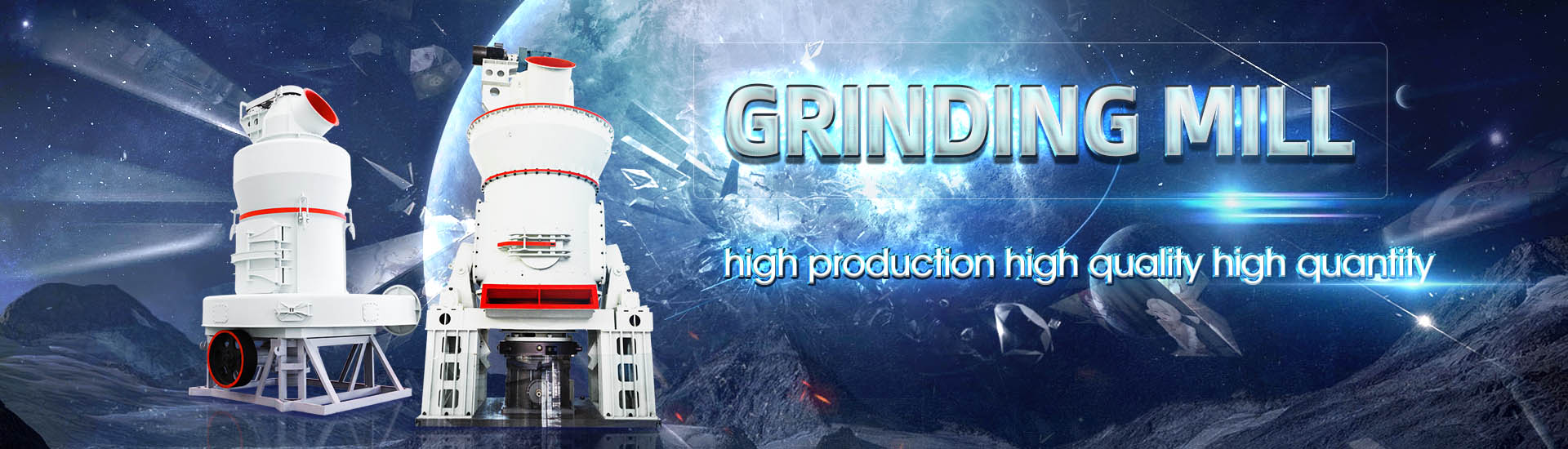
Limestone rotary kiln powder making process
.jpg)
How Lime is Made
While there are multiple kiln types in use, the rotary kiln is the most common kiln found in the US A rotary kiln consists of a rotating cylinder that sits horizontal on an incline Limestone is fed 1977年5月3日 The basic processes in the production of lime are: (1) quarrying raw limestone; (2) preparing limestone for the kilns by crushing and sizing; (3) calcining limestone; (4) 1117 Lime Manufacturing US EPA2022年11月1日 Ranging between 3 GJ/T and 5 GJ/T according to the clinkerization process [5], the rotary kiln process is able to transform the limestone into calcine materials at high Rotary kiln process: An overview of physical mechanisms, 2024年11月24日 Rotary lime kilns are large steel tubes that are lined on the inside with refractory bricks They are slightly inclined from the horizontal and are slowly rotated on a set 22 Lime Kiln Principles And Operations TAPPI
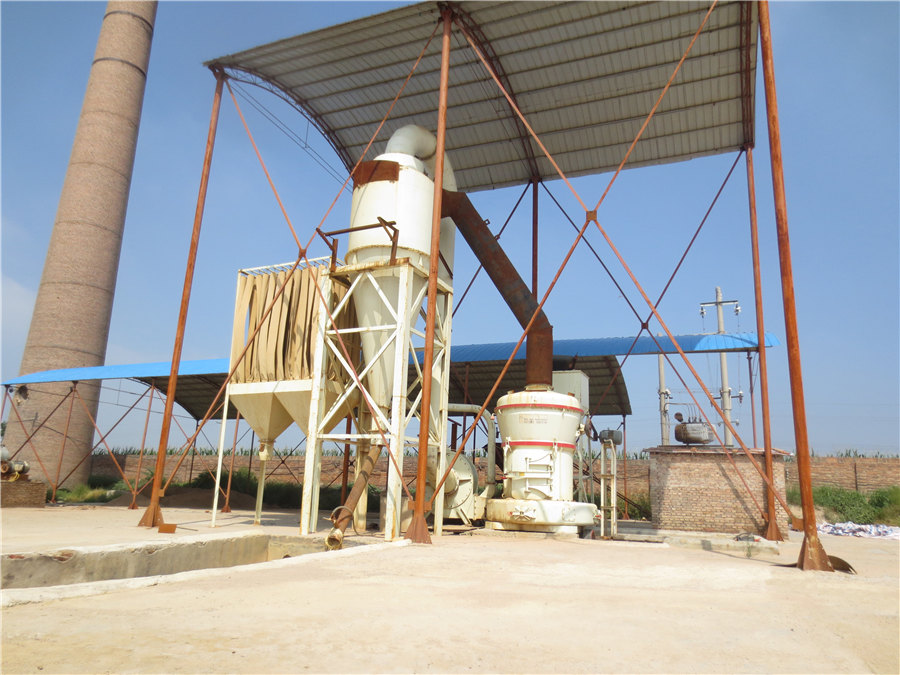
Preparation of Reduced Iron Powder from HighPhosphorus
2023年7月3日 Dephosphorization is essential for utilizing highphosphorus iron ore (HPIO), and this work prepared reduced iron powder via reductive roasting in a semiindustrial rotary kiln 1981年10月22日 Limestone Calcination in a Rotary Kiln AP WATKINSON and J K BRIMACOMBE An experimental study of the calcination of limestone has been carried out in a Limestone calcination in a rotary kiln Springer3 天之前 8 Slide 15 Lime Kiln Heat Rate • Heat rate is a measure of energy efficiency – Units are MM Btu/ton CaO or GJ/tonne CaO – Often stated as MM Btu/ton “product” • Typical range – 5 22 Lime Kiln Principles and Operations TAPPIAn experimental study of the calcination of limestone has been carried out in a highly instrumented pilotscale rotary kiln Local gas, solids, and wall temperatures and pct Limestone calcination in a rotary kiln Metallurgical and
.jpg)
Study on the Influencing Factors for Calcined Lime
2024年1月11日 With calcination process, the limestone is thermally decomposed into quicklime (CaO) and carbon dioxide (CO2) The quick lime is (i) porous (ii) highly reactive due to higher 2024年11月16日 The main raw materials (limestone, clay chalk or basalt) are quarried from natural rocks They are crushed and transferred to preblending storage where other substances (such as sand, iron ore, bauxite, shale, slag, fly ash) are added to get the desired chemical composition which is done in the kiln The main part of the manufacturing Cement Clinker Manufacturing Process with Reactions2023年2月25日 Since the rotary kiln is an equipment used in several solid treatment processes, its modeling depends on the process used Three specific case studies will now be presented: the first is an application in cement manufacturing; the second pertains to waste and biomass treatment in kilns; and the last one relates to other applicationsRotary kiln process: An overview of physical mechanisms, 2024年11月23日 The shaft kiln in a modernized form is still used in some countries, but the dominant means of burning is the rotary kiln These kilns—up to 200 metres (660 feet) long and six metres in diameter in wet process plants Cement Extraction, Processing, Manufacturing
.jpg)
Dolomite – Its Processing and Application in Iron and
2017年6月28日 Type of calcining kiln: Kiln capacity: Limestone size: Specific fuel consumption: Specific power consumption: tpd: mm: kcal/kg: kWh/t: Rectangular PFR kiln: 100400: 30120: 810870: Around 20: The most common process for the production of sintered dolomite is a single stage firing process in a shaft kiln or a rotary kiln The raw dolomite In a wetprocess or preheater system without a precalciner, most of the calcination takes place in the rotary kiln within a moving mass of feed This situation is not ideal for calcination because heat transfer has to take place through a large mass of material and CO 2 has to escape outwards as heat moves inwardsReactions in the cement kiln clinkering Understanding 2014年9月5日 Can be categorized into water treatment, steelmaking and deslagging and high alumina cement Method: crush the proportioned alumyte and limestone, make them into ball and send them into the rotary kiln Cool them after calcining at the temperature of 1,300°C Calcium aluminate is produced after crush and packageCalcium Aluminate Rotary Kiln2024年9月11日 Brief Introduction to Wet Rotary Kiln Process The kiln body of wet rotary kiln is usually relatively long (the aspect ratio is 3040) In order to increase the heat transfer area of the kiln, the chains are often hung at the kiln tail to accelerate water evaporationRotary Kiln, Cement Rotary Kiln, Lime Rotary Kiln, Cement
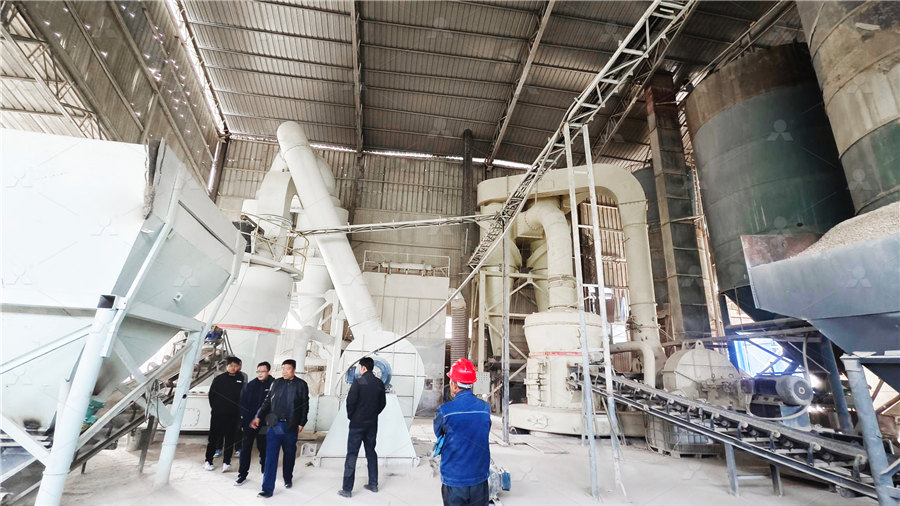
Cement Manufacturing—Technology, Practice, and
2021年11月16日 The kiln system in which the clinkerization takes place is a rotary kiln with or without additional infrastructure called as “suspension preheaters” and precalciner The rotary kiln is a rotating steel tube with a length to diameter ratio between 10 and 40 A slight inclination of 25 to 45 degrees is provided for a smooth flow of material2020年8月21日 use rotary kilns for pyroprocessing to calcinate ores, calcinate limestone to lime for cement, and to common types of kiln; wet process kilns, long dry kiln, travelling grate preheater kiln (lepol), cyclone preheater kiln, cyclone preheater kilns with riser duct firing and, precalciner kilns Heat for Clinker ProductionQuantitative Optimization of Cement Rotary Kiln for The cyclone preheating system Phase IV: Calcination The calcination is the core phase of the cement making dry process The calcination of the preheated raw meal takes place in the rotary kiln of the cement plant The rotary kiln is a huge rotating furnace in which the raw meal is heated up to 1450 ⁰C and turned to clinkerHow Is Cement Produced in Cement Plants Cement Making ProcessIn the gratekiln process, shown in Figure 8, there are three different reactors The drying, preheating, and cooling steps are similar to that of the straight grate process The general concept of heat recovery by using hot gases from Iron Ore Pelletizing Process: An Overview
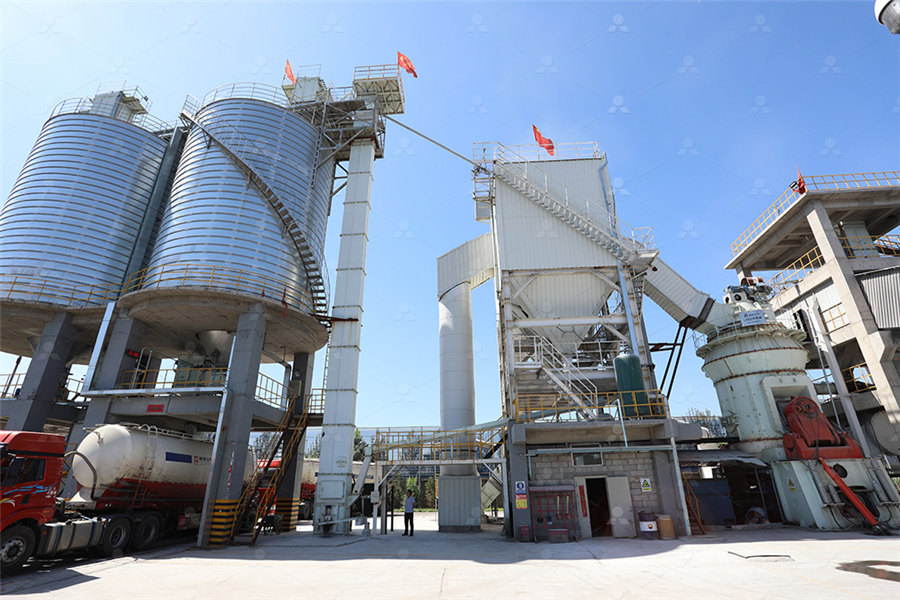
Lime Rotary Kiln Limestone Rotary Kiln
Flexible process configuration: vertical preheater can be configured at the end of the kiln to make full use of the hightemperature flue gas calcined in the lime rotary kiln, preheat the limestone from normal temperature to the initial 2023年11月27日 How to reduce the energy consumption of the rotary kilnelectric furnace (RKEF) process has become an important issue for the stainless steel industry The aim of this study is to reduce the energy consumption of ferronickel production from saprolite nickel laterite in the RKEF process The effects of the slag binary basicity, FeO content, and Cr2O3 content on Enhancing Rotary KilnElectric Furnace Process of Saprolitic 1971年8月17日 rotary kiln pass countercurrently through the downwardmoving raw materials in the preheater vessels Compared to the simple rotary kiln, the heat transfer rate is significantly increased, the degree of heat utilization is greater, and the process time is markedly reduced by the intimate contact of the solid particles with the hot gases116 Portland Cement Manufacturing US EPA2017年8月15日 The materials reach temperatures of 2500°F to well above 3000°F in the kiln Rotary kilns are divided into two groups, dryprocess and wetprocess, depending on how the raw materials are prepared In wetprocess kilns, raw materials are fed into the kiln as a slurry with a moisture content of 30 to 40 percentThe Cement Manufacturing Process Process Systems
.jpg)
How Cement is Made Portland Cement Association
Chunks are then ground into a fine powder Site A Sustainable Future Roadmap to Carbon Neutrality Limestone, marl, and clay are commonly used sources of these primary elements which uses heat generated by the plant to start chemical reactions between the components—making the next process, kiln firing, even more efficient 2022年4月1日 The RKEF process was first applied commercially to treat New Caledonian ore in the late 19th century [3]In general, the literature establishes three stages in the RKEF process [1], [4], [10], [11]: I) drying or preheating in a rotary dryer, II) calcination and partial reduction in a rotary kiln, and III) smelting in an electric arc furnaceThe RKEF process is quite mature and Improving the rotary kilnelectric furnace process for 5 天之前 The manufacture of Portland cement is a complex process and done in the following steps: grinding the raw materials, mixing them in certain proportions depending upon their purity and composition, and burning them to sintering in a kiln at a temperature of about 1350 to 1500 ⁰C During this process, these materials partially fuse to form nodular shaped clinker by Manufacturing of Portland Cement – Process and Materials1 天前 The whole process of making any type of lime all begins at the limestone quarry after careful surveys Most limestone is extracted through blasting Behind the rock face, holes are drilled to place the explosives When detonated, the explosion dislodges each time up to 30,000 tonnes of stoneProduction European Lime Association
.jpg)
Clinkerization Cement Plant Optimization
Alternative fuels like petcoke, rubber tyres, wood chips, etc have been introduced to economize cement making process PrecalcinerKiln Important Operational parameters with brief physical significance: Raw meal, Hot meal and Clinker Parameters: Rotary Kilns Rotary kiln is a rotating cylinder, installed at an inclination of 35 to 4 % to 2021年3月3日 Lime is the least expensive and one of the most heavily used alkali in the world, being essential to our society It is a nonhydraulic binder, excepting the socalled hydraulic lime, meaning that it will not set under waterFor this reason, lime is sometimes called air lime since it hardens on exposure to air It was used for thousands of years in masonry mortars to bind the Lime SpringerLink2024年1月17日 The preheating and partial decomposition of the raw meal is completed by the cyclone preheater, replacing part of the function of the rotary kiln to shorten the length of the return kiln At the same time, the heat What Do You Know About Wet Process Of Section 3: Components of a Cement Kiln Rotary Kiln The rotary kiln is the heart of the cement manufacturing process, where the raw mix undergoes the chemical transformations necessary to form clinker Structure and Working Principle A Comprehensive Guide to Cement Kilns:
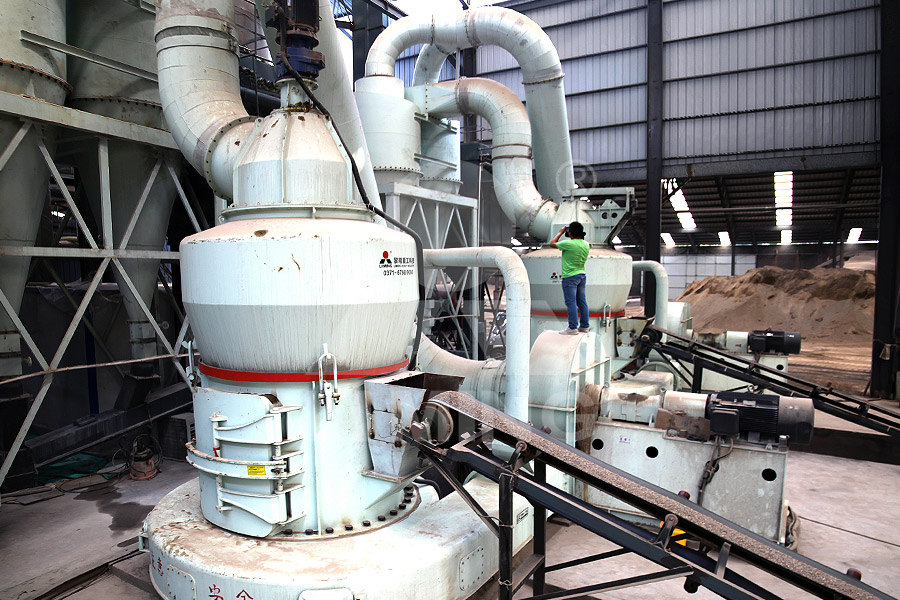
Rotary Kiln IspatGuru
2019年12月26日 Rotary kiln process The rotary kiln carries out several functions simultaneously It is a device for conveying, mixing, heat transfer, and reaction As in limestone calcination, the rotary kiln offers the advantage of handling charge material of finer size with a broad size range and can also handle throughputs at high calcination 2021年8月13日 within the kiln, making monitoring more difficult THE ROTARY KILN Cement is created by heating crushed limestone with clay, slate, blast furnace slag and other materials, then cooling and grinding the resultant clinker to create a fine powder Most modern cement plants use a dry process which is more thermallyefficient than the older wet processCRITICAL MEASUREMENTS IN CEMENT MANUFACTUREROTARY KILN rotary kiln A rotary kiln is a heating furnace that rotates a cylinder (retort), supplies raw materials into the furnace (inside the retort) using a feeding device (screw feeder, etc), and uniformly heattreats the raw materials while stirring Can we ask for a proposal for preprocess and postprocess equipment? Powder Rotary Kiln Tanabe Co, Ltd 株式会社タナベ2024年8月1日 For example, if a rotary kiln uses coal powder as fuel, the cost of lime per ton will increase by about 100 yuan Therefore, the economic benefits of using annular shaft kilns to produce activated lime in steel mills will be more significant In the process of limestone mining, qualified limestone blocks with particle sizes of 4080mm Choosing Right Lime Kiln For Your Lime Calcination Plant
.jpg)
Modeling of Pulverized Coal Combustion in Cement
2024年2月15日 gas components in cement rotary kiln were obtained by numerical simulation of a 3000 t/d rotary kiln with a fourchannel burner Process Description and Mathematic Models Process Description of the Modern Dry Process Cement Rotary Kiln Figure 1 shows the simplified flowchart of the cement rotary kiln system with the modern dry process A set According to the calcination character of limestone, lime rotary kiln is specialized design for production of active lime This type of kiln can work with vertical preheater and vertical cooler to achievethe advantages like high use ratio of raw materials, complete calcination, even quality, good quality lime, high capacity output, environmental and energy saving, simple operation Limestone Slag Calcined Dry Process Rotary Kiln for Cement Making 2020年6月8日 Rotary Kiln At the core of the sintering process, the kiln shell is a long cylinder made of steel, with a typical length ranging between 60100 m and weighing around 1000t Despite this impressive mass, the kiln shell is a giant with feet of clay, exposed to harsh environmental conditions The inner part of the kiln is heated on one side by a Comparison of lime kiln types Blitzco2024年11月16日 The main raw materials (limestone, clay chalk or basalt) are quarried from natural rocks They are crushed and transferred to preblending storage where other substances (such as sand, iron ore, bauxite, shale, slag, fly ash) are added to get the desired chemical composition which is done in the kiln The main part of the manufacturing Cement Clinker Manufacturing Process with Reactions
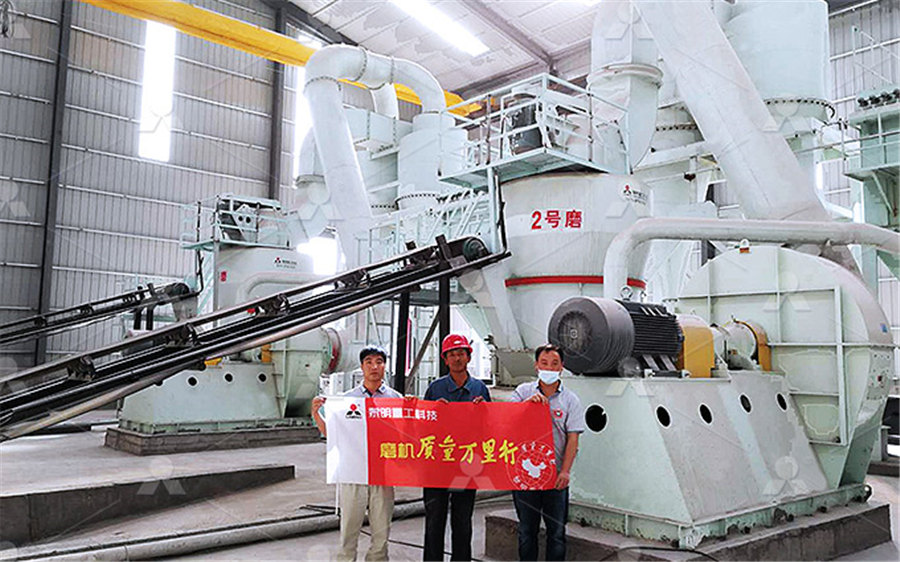
Rotary kiln process: An overview of physical mechanisms,
2023年2月25日 Since the rotary kiln is an equipment used in several solid treatment processes, its modeling depends on the process used Three specific case studies will now be presented: the first is an application in cement manufacturing; the second pertains to waste and biomass treatment in kilns; and the last one relates to other applications2024年11月23日 The shaft kiln in a modernized form is still used in some countries, but the dominant means of burning is the rotary kiln These kilns—up to 200 metres (660 feet) long and six metres in diameter in wet process plants Cement Extraction, Processing, Manufacturing2017年6月28日 Type of calcining kiln: Kiln capacity: Limestone size: Specific fuel consumption: Specific power consumption: tpd: mm: kcal/kg: kWh/t: Rectangular PFR kiln: 100400: 30120: 810870: Around 20: The most common process for the production of sintered dolomite is a single stage firing process in a shaft kiln or a rotary kiln The raw dolomite Dolomite – Its Processing and Application in Iron andIn a wetprocess or preheater system without a precalciner, most of the calcination takes place in the rotary kiln within a moving mass of feed This situation is not ideal for calcination because heat transfer has to take place through a large mass of material and CO 2 has to escape outwards as heat moves inwardsReactions in the cement kiln clinkering Understanding
.jpg)
Calcium Aluminate Rotary Kiln
2014年9月5日 Can be categorized into water treatment, steelmaking and deslagging and high alumina cement Method: crush the proportioned alumyte and limestone, make them into ball and send them into the rotary kiln Cool them after calcining at the temperature of 1,300°C Calcium aluminate is produced after crush and package2024年9月11日 Brief Introduction to Wet Rotary Kiln Process The kiln body of wet rotary kiln is usually relatively long (the aspect ratio is 3040) In order to increase the heat transfer area of the kiln, the chains are often hung at the kiln tail to accelerate water evaporationRotary Kiln, Cement Rotary Kiln, Lime Rotary Kiln, Cement 2021年11月16日 The kiln system in which the clinkerization takes place is a rotary kiln with or without additional infrastructure called as “suspension preheaters” and precalciner The rotary kiln is a rotating steel tube with a length to diameter ratio between 10 and 40 A slight inclination of 25 to 45 degrees is provided for a smooth flow of materialCement Manufacturing—Technology, Practice, and 2020年8月21日 use rotary kilns for pyroprocessing to calcinate ores, calcinate limestone to lime for cement, and to common types of kiln; wet process kilns, long dry kiln, travelling grate preheater kiln (lepol), cyclone preheater kiln, cyclone preheater kilns with riser duct firing and, precalciner kilns Heat for Clinker ProductionQuantitative Optimization of Cement Rotary Kiln for
.jpg)
How Is Cement Produced in Cement Plants Cement Making Process
The cyclone preheating system Phase IV: Calcination The calcination is the core phase of the cement making dry process The calcination of the preheated raw meal takes place in the rotary kiln of the cement plant The rotary kiln is a huge rotating furnace in which the raw meal is heated up to 1450 ⁰C and turned to clinker