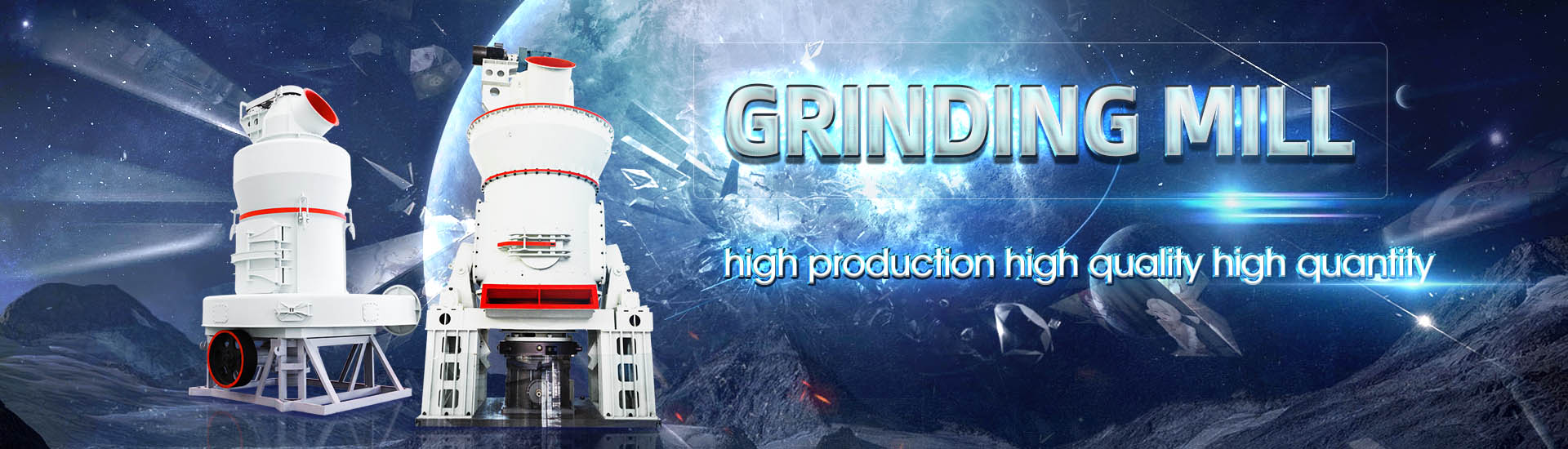
Sintering flue gas desulfurization gas
.jpg)
Resource utilization of semidry flue gas desulfurization ash
2024年4月1日 Semidry desulfurization technology has gained prominence in sintering flue gas desulfurization due to its notable advantages such as minimal equipment corrosion, dry waste 2023年12月1日 The novel Mn/CeCabased desulfurizers with high desulfurization performance are prepared by the dippingroasting method for lowtemperature dry sintering flue gas Mechanism and experimental study of desulfurizing agent 2023年2月11日 Industrial flue gas desulfurization can effectively reduce sulfur dioxide emissions to atmosphere, but emits large amounts of desulfurization byproducts Calciumbased Resource utilization of flue gas calciumbased desulfurization The basic principle of deep desulfurization of sintering flue gas in iron and steel plant based on the lowtemperature oxidation method is to use sodium hydroxide solution as a desulfurization Deep desulfurization of sintering flue gas in iron and steel
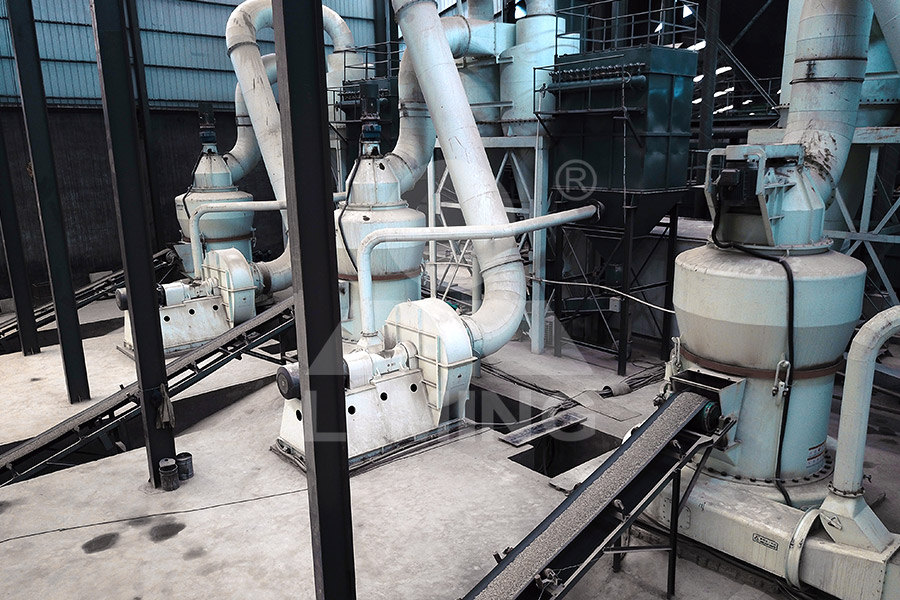
Lowtemperature oxidation behavior and mechanism of semi
2021年3月17日 The lowtemperature wet oxidation behavior of semidry desulfurization ash from iron ore sintering flue gas in ammonium citrate solution was investigated for efficiently utilizing 2017年9月8日 For a typical sintering flue gas desulfurization system by limestonegypsum method, this seriflux effluent was often needed to be recycled into the system after the The efficient removal of thallium from sintering flue gas 2022年12月28日 Under the simulated sintering flue gas condition, the effect of CO 2 concentration, temperature and relative humidity on the desulfurization of calciumbased adsorbent were carried out The mechanism of CaCO 3 Effect of CO2 on the Desulfurization of Sintering The new flue gas desulfurization system of 108m 2 sintering machine is reformed, combined with the applicable scope of common desulfurization and dust removal process and the basic STUDY ON SINTERING FLUE GAS DESULFURIZATION
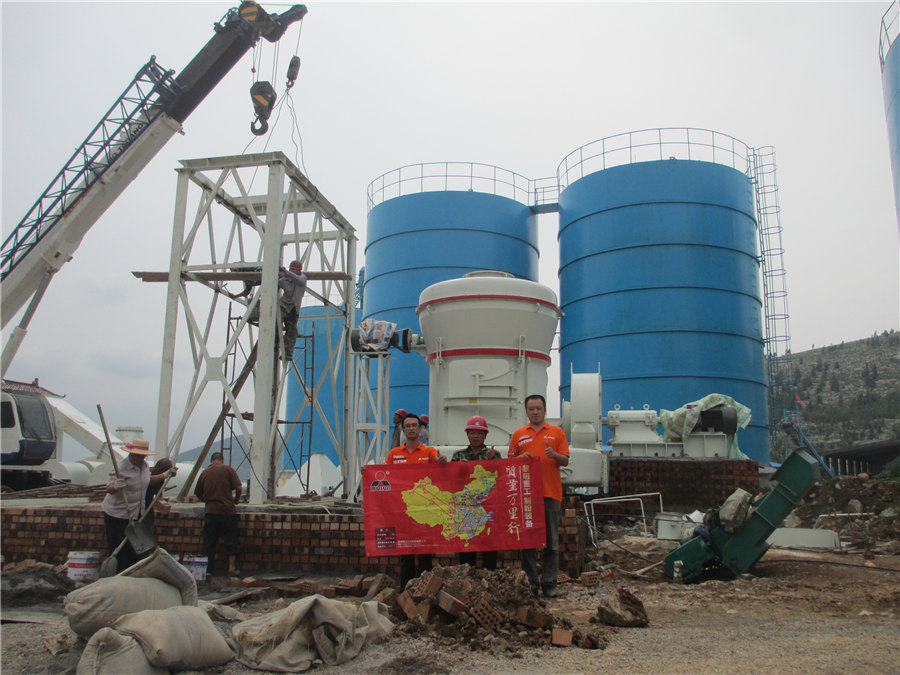
Performance on desulfurization and denitrification of one
2022年12月1日 Performance on removal of SO 2 and NO X from sintering flue gas was analyzed Mechanism on desulfurization and denitrification of activated carbon was disclosed 2017年9月8日 The sintering flue gas desulfurization wastewater was taken from a large iron and steel corporation, and the composition of the wastewater is shown in Table 1 The operation equipments are digital speed agitator SXJQ1 (Greatwall Scientific Industrial and Trade Co, Ltd (Zhengzhou, China)) and homogenizer (Specimen and Model Factory (Shanghai The efficient removal of thallium from sintering flue gas 2021年3月17日 Iron ore sintering is an important part of a long steelmaking process with sulfur dioxide emissions accounting for 40%–80% of the total sulfur dioxide emissions in steel companies [1,2,3,4]Semidry flue gas desulfurization technology combines the characteristics of wet and dry flue gas desulfurization processes, and it has significant advantages such as low Lowtemperature oxidation behavior and mechanism of semi 2023年12月1日 A novel Mn/CeCabased desulfurizer was prepared by dippingroasting method to improve the performance of single calcium hydroxide (Ca(OH) 2) for sintering flue gas desulfurization (FGD) at 100–350 ℃In this study, metal dopants iron oxide (Fe 2 O 3) and magnesium oxide (MgO) are added to improve the microstructure of single Ca(OH) 2 and Mechanism and experimental study of desulfurizing agent
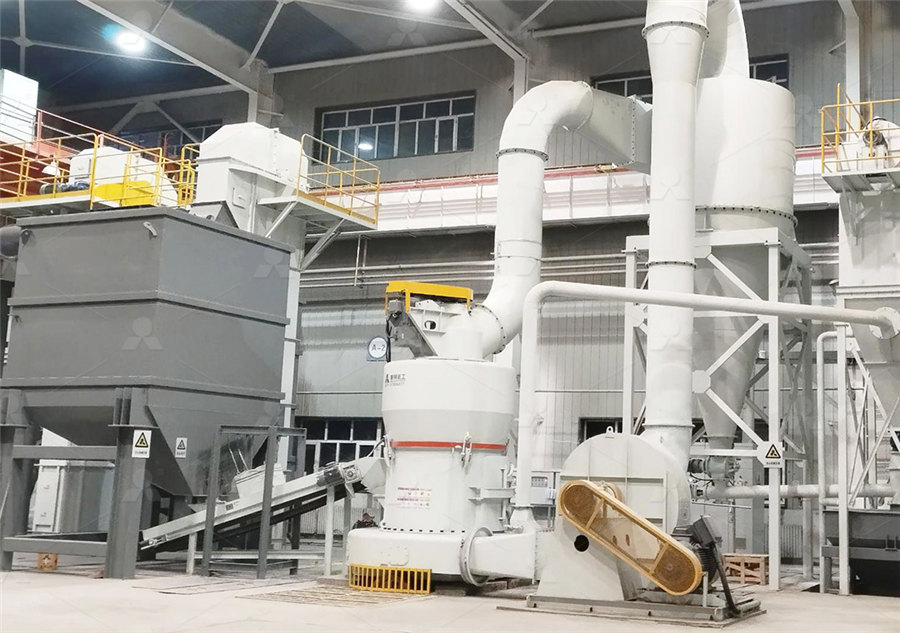
O3 oxidation combined with semidry method for
2021年6月1日 The desulfurization technologies for sintering/pelletizing flue gas are divided into three categories: wet desulfurization technology (Hrastel et al, 2010), semidry desulfurization technology However, in the process of flue gas desulfurization, the bucket elevator is used to dump absorbent and circulating materials from the top of the 2021年7月1日 However, the sintered flue gas’s temperature is low, so it needs to be heated to the initial temperature of SCR, resulting in huge energy consumption Therefore, the development of lowtemperature SCR technology is suitable for sintering flue gas denitrification and a guarantee for controlling the NO x emission afterwardsEmissions of air pollutants from sintering flue gas in the 2016年8月1日 At present, wet flue gas desulfurization (FGD) is a relatively mature and most widely applied technology in iron and steel industry to control the SO 2 emission However, it is not much effective for the absorption of NO X because NO X from the sintering flue gas mainly exists in the form of NO which is poorly soluble in water [3]Simultaneous desulfurization and denitrification of sintering flue gas 2022年12月28日 The effect of carbon dioxide (CO2) on the desulfurization of sintering flue gas with hydrate (Ca(OH)2) as an absorbent was investigated, and the formation of calcium carbonate (CaCO3) and its effect on the desulfurization was discussed The competitive relationship between carbon dioxide (CO2) and sulfur dioxide (SO2) with the deacidification agent in Effect of CO2 on the Desulfurization of Sintering Flue Gas
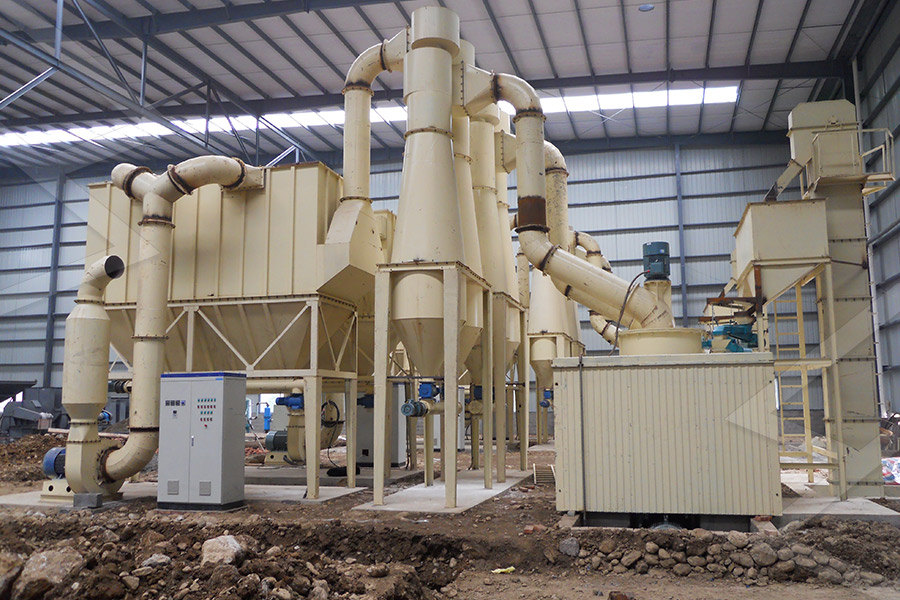
Performance on desulfurization and denitrification of one
2022年12月1日 At present, the typical treatment technologies for the removal of SO 2 and NO x from sintering flue gas can be classified into two types, namely wet process and dry process (Cheng and Zhang, 2018a)The wet processes are commonly subdivided into oxidation adsorption methods and complexing adsorption methods, which have positive effects on desulfurization 2022年10月20日 Although more and more desulfurization equipment has been put into use in sintering plants, how to effectively remove sulfur dioxide from sintering flue gas in a desulfurization tower is still a great challenge in China The desulfurization tower, as a critical part, needs further improvement and optimization Therefore, based on the numerical simulation of Structure Optimization Research Based on Numerical 2018年10月15日 Research Cottrell has demonstrated the commercial availability of limestone flue gas desulfurization on a 115 MW installation Certain chemistry and process considerations were taken into account (PDF) Comparison of flue Gas Desulfurization Technologies2022年10月20日 Based on the comprehensive analysis, these optimized structures are recommended in the design of an ammoniabased wet sintering flue gas desulfurization tower This work not only develops a Structure Optimization Research Based on
.jpg)
Oxidation modification of semidry desulfurization ash from sintering
2015年1月21日 The semidry desulfurization ash obtained from sintering flue gas contains a large amount of CaSO3, which has an important stabilizing influence on desulfurization ash, and thereby restricts its disposal and comprehensive utilization In order to solve this problem, lowtemperature static oxidation and hightemperature dynamic roasting were adopted for studying 2016年9月28日 The established model was firstly verified by the industrial operation data of a 2 × 220 m² sintering flue gas desulfurization tower Then, using the model, numerical simulations of simultaneous 3D simulation of sintering flue gas desulfurization and 2023年4月1日 Realization of low temperature and high efficiency oxidation of CaSO 3 is the key to solve the issue of ecological hazards caused by semidry sintering flue gas desulfurization ash The subcritical hydrothermal technology was employed for the oxidation of CaSO 3, achieving 8983% of CaSO 3 at 180 °C, 2 MPa for 120 min with a solidtoliquid ratio of 1:20Subcritical hydrothermal oxidation of semidry ash from iron 2017年11月1日 To effectively solve the problem of reutilizing semidry sintering flue gas desulfurized ash (SSFGDA) from steel plants, a new technology is proposed in this paper in which ash is added to a boiling furnace to obtain SO 2 during sulfuric acid production Using thermodynamics and simulation calculations, the hightemperature characteristics of CaSO 3 Utilization of semidry sintering flue gas desulfurized ash for
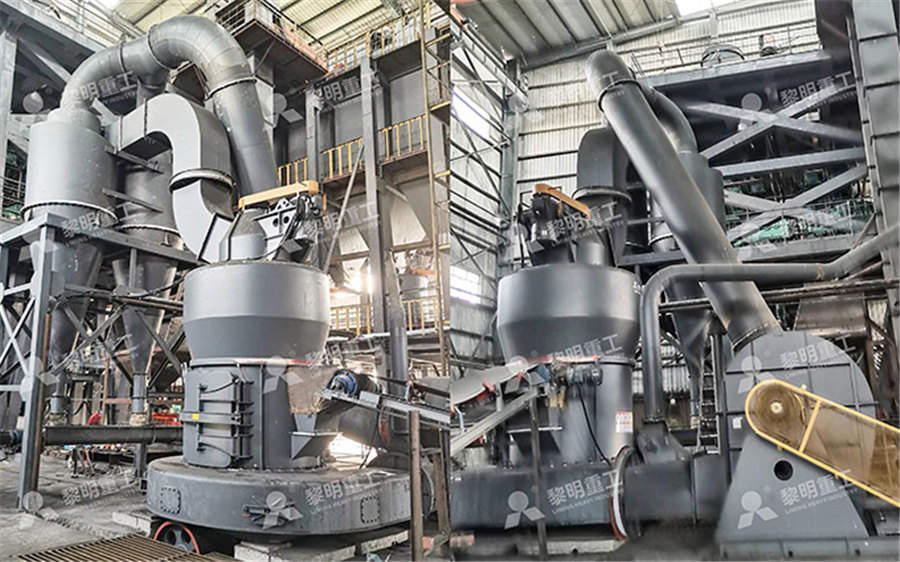
Progress of Desulfurization and Denitration Technology of Flue Gas
2019年3月1日 [9] Wang X H and Fang X C 2008 Progress in Simultaneous Removal of SO2 and NOX from Flue Gas Contemporary Chemical Industry 37 197200 Google Scholar [10] Li H, Niu M and Miao Y 2013 Analysis of LimestoneGypsum Flue Gas Desulfurization Technology for Sintering Machine Science Technology Information 138138 Google Scholar2017年6月1日 The model used in the numerical simulation is based on a 2 × 220 m 2 sintering flue gas desulfurization tower with the height of 26 m and the diameter of 165 m as illustrated in Fig 1 (a)The sintering flue gas move into the Ca(OH) 2 slurry via equally distributed flue gas pipes in the absorbing tower With the effects of Ca(OH) 2 slurry and oxygen from oxidation air 3D simulation of sintering flue gas desulfurization and denitration in 2011年7月1日 SO2 Emission of sintering flue gas accounts for more than 70% of total SO2 emission of steel industry The purpose of this paper was to use steel slag for desulfurization of sintering flue gasExperimental Investigation of Sintering Flue Gas Desulfurization 2022年12月1日 Industrial flue gas desulfurization technologies include the dry method (Kang et al, 2022), the semidry method (Cai et al, 2022), and the wet method (Cui et al, 2021) Dry and semidry desulfurization methods rely on the properties of the absorbent Its sulfur adsorption capacity and desulfurization rate are lower than those of the wet methodSimultaneous desulfurization and denitrification of flue gas
.jpg)
Simultaneous desulfurization and denitrification of sintering flue gas
DOI: 101016/JCJCHE201604005 Corpus ID: ; Simultaneous desulfurization and denitrification of sintering flue gas via composite absorbent @article{Wang2016SimultaneousDA, title={Simultaneous desulfurization and denitrification of sintering flue gas via composite absorbent}, author={Jie Wang and Wenqi Zhong}, journal={Chinese Journal of Chemical Abstract Read online The new flue gas desulfurization system of 108m2 sintering machine is reformed, combined with the applicable scope of common desulfurization and dust removal process and the basic principles of desulfurization and dust removal process selection, the advanced and reliable rotary spray dryer absorber(SDA) technology is selected for flue gas Study on sintering flue gas desulfurization process selection2024年11月1日 Wei et al [17], [18] explored the use of subcritical hydrothermal oxidation to oxidize semidry desulfurization ash derived from iron ore sintering flue gas Under the conditions of an initial pressure of 4 MPa, a reaction temperature of 240 °C, a solid–liquid mass ratio of 1:20, and a reaction time of 90 min, the oxidation rate of CaSO 3 Carbothermal reduction of flue gas desulfurization ash The new flue gas desulfurization system of 108m 2 sintering machine is reformed, combined with the applicable scope of common desulfurization and dust removal process and the basic principles of desulfurization and dust removal process selection, the advanced and reliable rotary spray dryer absorber(SDA) technology is selected for flue gas desulfurization Taking the STUDY ON SINTERING FLUE GAS DESULFURIZATION
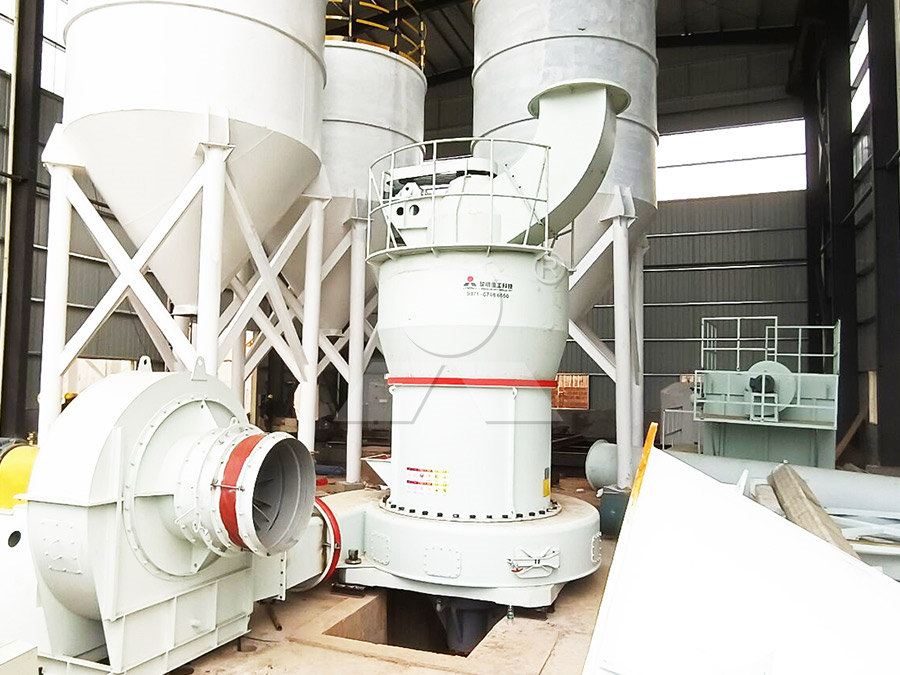
FlueGas Desulphurization an overview ScienceDirect Topics
Fluegas desulfurization (FGD) is a scrubbing technique that uses an alkaline reagent (typically a sodium or calciumbased alkaline regent) to remove SO 2 from flue gas In all, the Hg t removal efficiency of ESP + FGD in the sintering flue gas was more than 97%, 2020年9月10日 The properties of activated coke (AC) for sintering flue gas purification greatly affect the efficiency of desulfurization and denitration, but they gradually change during cycles The change in properties of coalbased AC during cycles was studied to clarify the change law and AC optimization index The AC oxygen content rapidly increases from 1349 to 1787 wt% Properties change of activated coke for sintering flue gas 2021年5月1日 Wet Flue Gas Desulfurization (WFGD) is a flue gas purification technology widely used in coalfired power plants, steel sintering machines, marine exhaust gas washing (Caiazzo et al, 2013), etc Desulfurization efficiency is the core of SO 2 removal In principle, the absorption process can be regarded as a gasliquid mass transferProcess optimization of S (IV) oxidation in flue gas desulfurization 2020年8月15日 Postcombustion flue gas desulfurization and denitrification technologies are essential in achieving the full compliance of fine particulate matter (PM25, aerodynamic diameter less than 25 μm) air quality standards by 2030 in China as sulfur dioxide (SO2) and nitrogen oxides (NOX) are the main precursors of PM25 Some studies have addressed the Comprehensive evaluation of flue gas desulfurization and
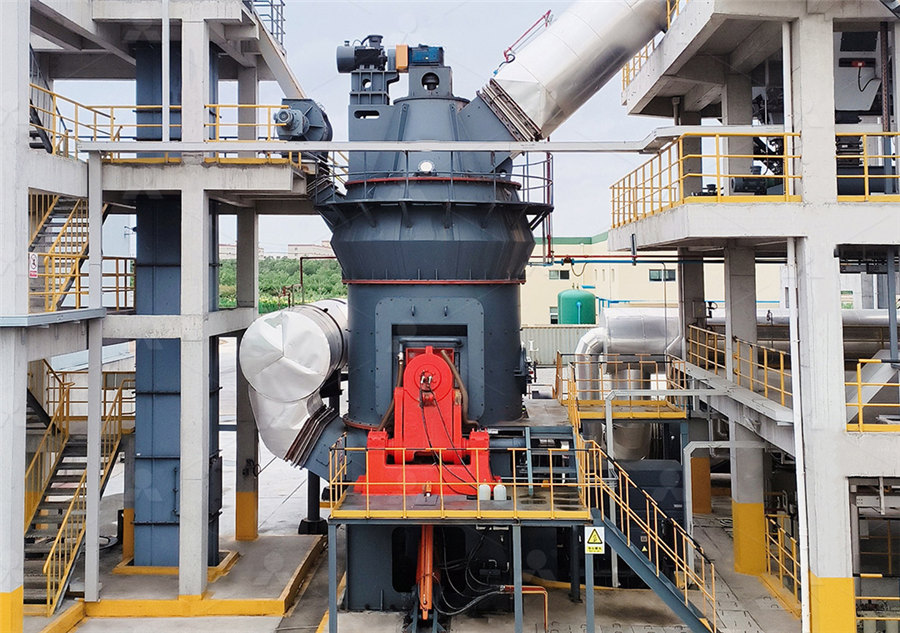
A novel and clean utilization of flue gas desulfurization ash
2024年10月15日 Over half of the SO 2 emissions in the iron and steel industry stem from the sintering process Consequently, desulfurizing gases from the sintering process is central to emission control efforts Presently, flue gas desulfurization technologies are categorized into wet, semidry, and dry methods2023年4月20日 Flue gas desulfurization 1 Introduction The rapid development of industrial technology has promoted significant progress in human society, but it has also because the sintering flue gas desulfurization process is a gas–solid reaction, even though the solid phase diffusion is obvious Still because there is no liquid phase reaction, itsResource utilization of flue gas calciumbased gas inlet baffle valve of the flue gas desulfurization system and open the flue bypass valve The flue gas can be directly sent to the main chimney through the original flue and discharged to the atmosphere The height of the chimney is 155 m, and the dust emission concentration in the exhaust gas of the sintering flue gas is less than orSTUDY ON SINTERING FLUE GAS DESULFURIZATION 2017年9月8日 The sintering flue gas desulfurization wastewater was taken from a large iron and steel corporation, and the composition of the wastewater is shown in Table 1 The operation equipments are digital speed agitator SXJQ1 (Greatwall Scientific Industrial and Trade Co, Ltd (Zhengzhou, China)) and homogenizer (Specimen and Model Factory (Shanghai The efficient removal of thallium from sintering flue gas
.jpg)
Lowtemperature oxidation behavior and mechanism of semi
2021年3月17日 Iron ore sintering is an important part of a long steelmaking process with sulfur dioxide emissions accounting for 40%–80% of the total sulfur dioxide emissions in steel companies [1,2,3,4]Semidry flue gas desulfurization technology combines the characteristics of wet and dry flue gas desulfurization processes, and it has significant advantages such as low 2023年12月1日 A novel Mn/CeCabased desulfurizer was prepared by dippingroasting method to improve the performance of single calcium hydroxide (Ca(OH) 2) for sintering flue gas desulfurization (FGD) at 100–350 ℃In this study, metal dopants iron oxide (Fe 2 O 3) and magnesium oxide (MgO) are added to improve the microstructure of single Ca(OH) 2 and Mechanism and experimental study of desulfurizing agent 2021年6月1日 The desulfurization technologies for sintering/pelletizing flue gas are divided into three categories: wet desulfurization technology (Hrastel et al, 2010), semidry desulfurization technology However, in the process of flue gas desulfurization, the bucket elevator is used to dump absorbent and circulating materials from the top of the O3 oxidation combined with semidry method for 2021年7月1日 However, the sintered flue gas’s temperature is low, so it needs to be heated to the initial temperature of SCR, resulting in huge energy consumption Therefore, the development of lowtemperature SCR technology is suitable for sintering flue gas denitrification and a guarantee for controlling the NO x emission afterwardsEmissions of air pollutants from sintering flue gas in the
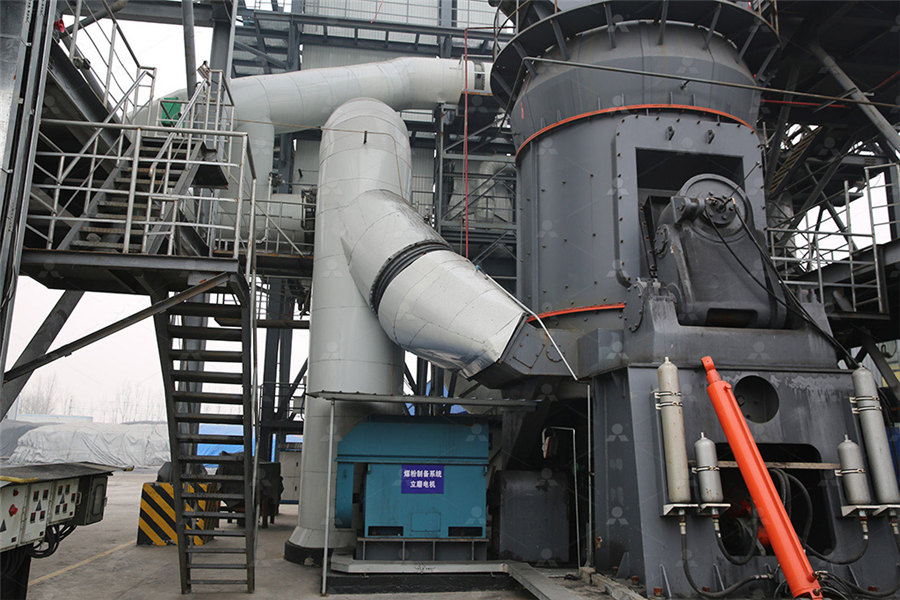
Simultaneous desulfurization and denitrification of sintering flue gas
2016年8月1日 At present, wet flue gas desulfurization (FGD) is a relatively mature and most widely applied technology in iron and steel industry to control the SO 2 emission However, it is not much effective for the absorption of NO X because NO X from the sintering flue gas mainly exists in the form of NO which is poorly soluble in water [3]2022年12月28日 The effect of carbon dioxide (CO2) on the desulfurization of sintering flue gas with hydrate (Ca(OH)2) as an absorbent was investigated, and the formation of calcium carbonate (CaCO3) and its effect on the desulfurization was discussed The competitive relationship between carbon dioxide (CO2) and sulfur dioxide (SO2) with the deacidification agent in Effect of CO2 on the Desulfurization of Sintering Flue Gas 2022年12月1日 At present, the typical treatment technologies for the removal of SO 2 and NO x from sintering flue gas can be classified into two types, namely wet process and dry process (Cheng and Zhang, 2018a)The wet processes are commonly subdivided into oxidation adsorption methods and complexing adsorption methods, which have positive effects on desulfurization Performance on desulfurization and denitrification of one 2022年10月20日 Although more and more desulfurization equipment has been put into use in sintering plants, how to effectively remove sulfur dioxide from sintering flue gas in a desulfurization tower is still a great challenge in China The desulfurization tower, as a critical part, needs further improvement and optimization Therefore, based on the numerical simulation of Structure Optimization Research Based on Numerical
.jpg)
(PDF) Comparison of flue Gas Desulfurization Technologies
2018年10月15日 Research Cottrell has demonstrated the commercial availability of limestone flue gas desulfurization on a 115 MW installation Certain chemistry and process considerations were taken into account