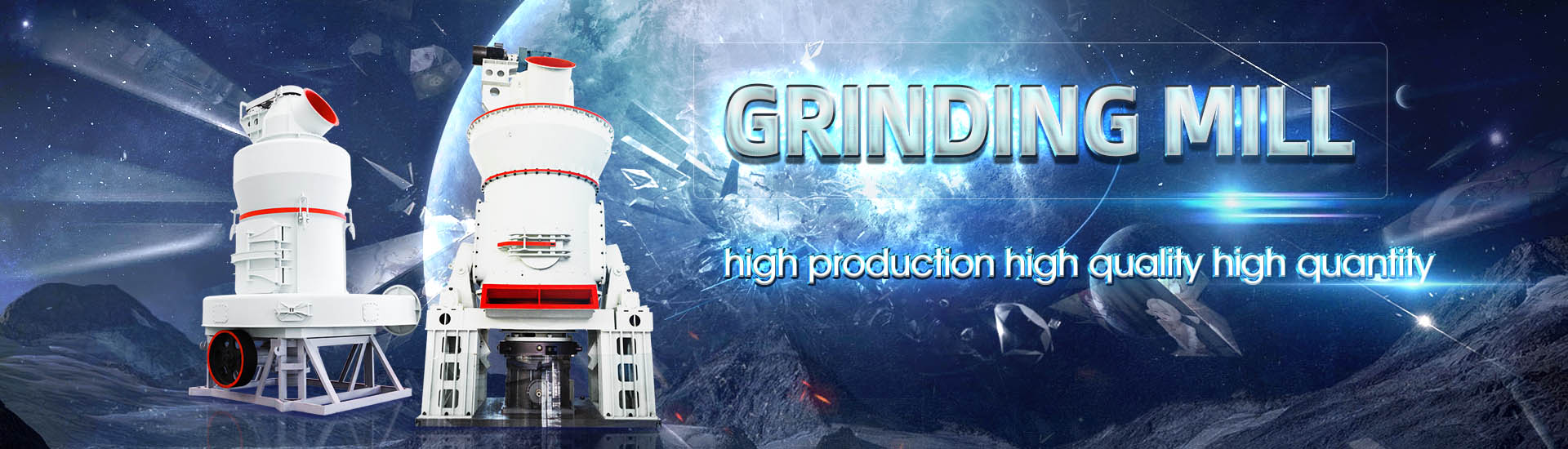
Electrolytic manganese dioxide manganese slag grinding equipment solution
.jpg)
Crushing and grinding of electrodeposited manganese
2011年12月9日 Electrolytic manganese dioxide, for use as an efficient depolarizer in dry cells, is produced by the electrolysis of a solution of manganese sulphate and sulphuric acid at a 2022年3月1日 Electrolytic manganese residue (EMR) contains high concentrations of NH 4+ and heavy metals, such as Mn 2+, Zn 2+, Cu 2+, Pb 2+, Ni 2+ and Co 2+, while carbide slag Synergistic solidification/stabilization of electrolytic manganese 2024年6月1日 This article introduces the process flow of manganese metallurgy and provides a systematic overview of the optimisation of various aspects of the manganese electrolytic Improvement of manganese electrolytic process and 2007年1月1日 In this process, manganese dioxide ore was treated by reductive roasting followed by sulfuric leaching After removal of impurities by neutralisation to the pH range of 4–6 and filtration, manganese in the solution could be sent Manganese metallurgy review Part I: Leaching
.jpg)
Electrodeposition of Manganese Metal and Co
anode slag to separate manganese lead In the electrolytic process of manganese dioxide, EMD is precipitated from the anode and hydrogen evolution occurs in the cathode electrode 2021年12月20日 Electrolytic manganese residue (EMR) is the filter press residue discharged from rhodochrosite (MnCO 3) after leaching with concentrated sulfuric acid, neutralizing and Mechanochemical modification of electrolytic manganese residue 2023年6月30日 Stabilization/solidification is a method to treat large amounts of manganese slag by immobilizing the contaminants through chemicals, industrial solid waste, etc without A Research Progress on Stabilization/Solidification of Electrolytic 2022年6月27日 Benchscale electrowinning of electrolytic manganese dioxide was carried out using the manganese sulfate electrolyte generated through SO 2 leaching of lowgrade BenchScale Electrowinning of Electrolytic Manganese Dioxide
.jpg)
Study on Solidification Treatment of Electrolytic Manganese Slag
2021年8月3日 In order to verify the feasibility of manganese slag as highway subgrade material, in this study, we compared the solidification effect of mixed solidified manganese slag with fly Part I: Leaching of ores/secondary materials and recovery of electrolytic/chemical manganese dioxide (1977) reported a hydrometallurgical process for the recovery of manganese from slag leaching solutions The solution contained Manganese metallurgy review Part I: Leaching 2022年3月1日 Generally, electrolytic metallic manganese (EMM) is produced by the “leachingpurificationelectrodeposition” process since it shows a wide raw materials adaptability, especially for the lowgrade manganese ore (8–15%), without scarifying the product quality (Li et al, 2021a; Li et al, 2021b)China is the largest EMM producer and exporter in the world (Zhang et al, Synergistic solidification/stabilization of electrolytic manganese 2021年5月5日 A novel material (named AEMS) for heavy metal removal was proposed by ball grinding activated electrolytic manganese slag (EMS) with low content of sodium hydroxide For different application scenarios, the two physical properties of the materials were developed: the powdery AEMS (powder) was used to remove heavy metals from wastewaterA novel method for solidification/stabilization of Cd(II),
.jpg)
A critical review on approaches for electrolytic manganese residue
2021年9月15日 Manganese mainly exists as manganese ores in nature, and manganese ores are geographically varied (Li et al, 2018, Zhan and Zhang, 2019)South Africa, Ukraine, Brazil, Australia, India, China, Gabon, and Mexico account for almost 9739% of the global reserves (690,000 kt) with a grade of 15%–50% (Fig 1 a)China only takes 623% (43,000 kt) How to choose the grinding mill equipment in the electrolytic manganese powder workshop? The raw material for the production of electrolytic manganese is manganese ore powder However, since most manganese ores are finegrained or microfinegrained, and there are a considerable amount of highphosphorus ore, highiron ore and cogenerated beneficial metals, it brings How to choose the electrolytic manganese powder grinding mill equipment 2023年5月24日 electrolytic manganese dioxide from manganese oxide ores, high or lowgrade A material balance was performed on the designed flowsheet to check the feasibility of using recycled streams The use of bags around the anodes makes it possible to utilize the iron in the feed as a recyclable reductant for the dissolution of manganese oresSustainable Production of Electrolytic Manganese Huge amounts of manganeserich solid residues are yearly produced worldwide by industrial electrolysis, calling for advanced methods of recycling in the context of the circular economy Here, we review manganese recycling with focus on ore reserves, electrolytic production, residue stockpiling and environmental impact, reducing the amount of residue and improving metal Recyling manganeserich electrolytic residues: a review
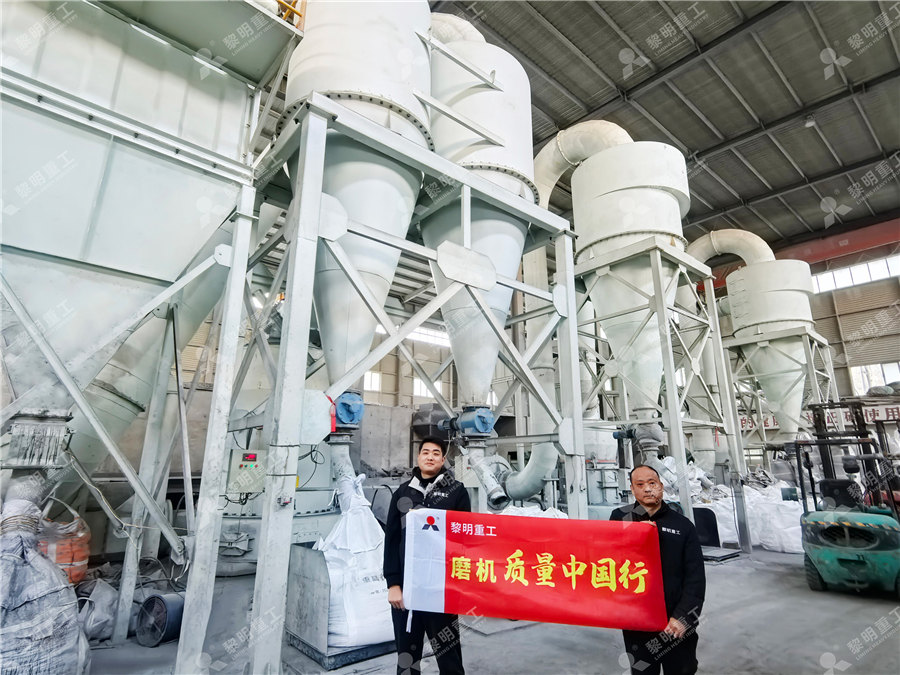
Kinetics and mechanism of manganese reductive leaching
2023年6月1日 0duction process, only 719% of manganese from raw materials is converted into the final product, while the rest enters the anode slag, known as electrolytic manganese anode slag (EMAS) [3]For every 1 ton of electrolytic manganese produced, 50–150 kg of anode slag is generated [4]In China, the annual output of electrolytic manganese is approximately 15 2021年8月5日 Electrolytic manganese residue (EMR), a byproduct of the electrolytic manganese metal production process, contains several hazardous components such as ammonia nitrogen (NH 3N), soluble manganese, and heavy metals In recent years, although a great number of treatment methods have been proposed, there is no mature and economical Selective recovery of manganese from electrolytic manganese 2021年3月25日 The output of electrolytic manganese metal in China has topped the world In the production of electrolytic manganese metal, the electrolytic manganese anode slag (EMAS) will be inevitably produced in anode chamber EMAS contains more than 40% heavy metal components, such as Mn, Pb, Se, etc (Yan et al, 2013; Zhang et al, 2016a; Chen et al, 2015Recycling application of modified waste electrolytic manganese anode 2020年9月11日 The related microbial metabolomics on biological recovery of manganese (Mn) from Electrolytic Manganese Slag (EMS) has not been studied This study aimed at open the door to the metabolic Bioleaching of manganese from electrolytic manganese slag
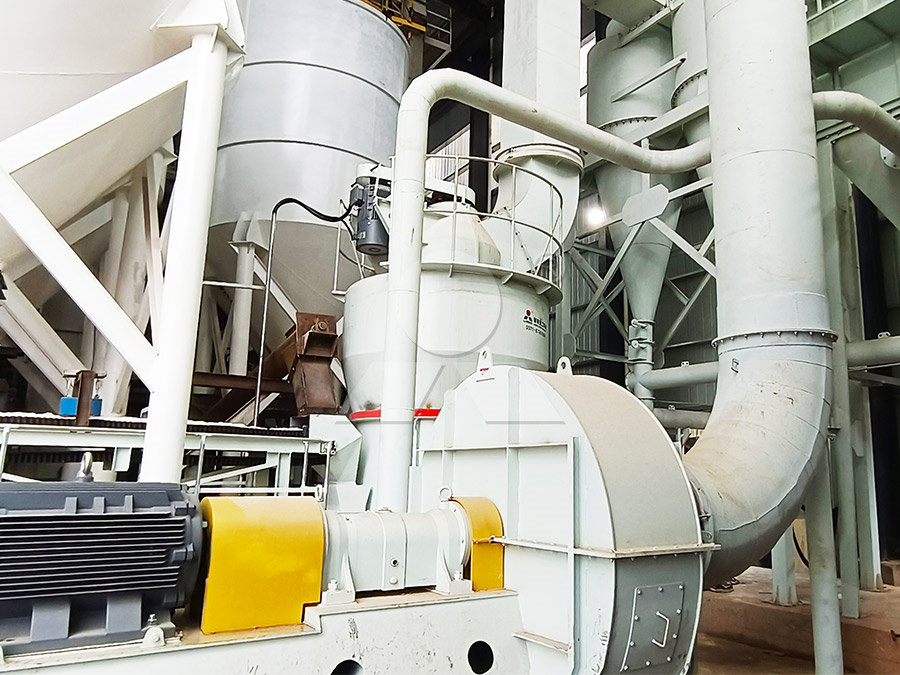
A Research Progress on Stabilization/Solidification of Electrolytic
2023年6月30日 Electrolytic manganese residue (EMR) is a waste residue produced during the production of electrolytic manganese EMR contains a large amount of \({\text{NH}}{4}^{ + }\)N, Mn, and other heavy metal elements such as Zn, Ni, Cu, and CrAlthough many EMR treatment methods have been proposed in recent years, there is no mature and economical industrial 2015年12月9日 Electrolytic manganese dioxide (EMD or ɛ/γMnO 2) is the material most commonly employed as the cathode in primary alkaline batteries and primary nonaqueous lithium cells owing to its relatively low cost, low toxicity, high reduction potential, and high gravimetric capacityUnfortunately, MnO 2based secondary cells tend to have limited cycle life, due to the Electrochemical Behavior of Electrolytic Manganese Dioxide 2023年3月8日 Electrolytic manganese residue (EMR) is a solid waste produced in the process of electrolytic manganese metal (EMM) production In recent years, the accumulation of EMR has caused increasingly serious environmental problems To better understand the state of EMR recycling in recent years, this paper used a comprehensive literature database to conduct a Progress in comprehensive utilization of electrolytic manganese The ground manganese slag has an angular shape as it results from the breakage of larger, brittle particles, and contains the mineral phases α′C 2 S, C 3 MS 2, CaOMnO2SiO 2 and C 2 AS, with the α′C 2 S in particular providing it with hydraulic reactivity 92 The fresh manganese slag is light yellow or light green, with a moisture content between 16%–38% remaining from the Manganese Slag an overview ScienceDirect Topics
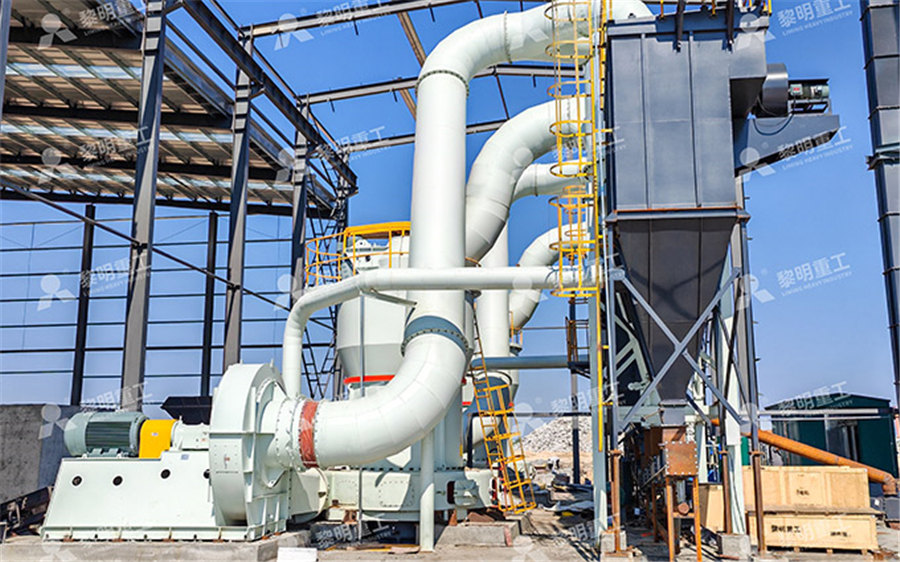
How To Select Equipment For Producing Manganese Powder From Manganese
Manganese metal is divided into metal manganese produced by fire reduction and electrolytic metal manganese produced by wet electrowinning The pyrometallurgical manganese is massive and difficult to crush; The wet electrolytic manganese metal is flake, easy to crush and high purity At the same time, the production scale of manganese metal powder is generally large, but the 1990年1月1日 13 2 6 1 2 1 1 1 1 1 14 156 ELECTROMETALLURGICAL PLANT PRACCE natural manganese ore CRUSHING GRINDING reductant REDUCTION AT 6 5 0 7 5 0 ^ C 1 sulphuric acid REDUCED LEACHING SPENT ELECTROLYTE MANGANOUS SULPHATE S U L P H U R I C ACID FILTRATION residue to waste 1 PURIFICATION ELECTROLYSIS r PILOT PLANT STUDIES FOR THE PRODUCTION OF ELECTROLYTIC MANGANESE 2021年1月1日 Electrolytic Manganese Slag (EMS) is a byproduct of electrolytic manganese industry (Peng et al, 2018)China's electrolytic manganese metalproduction capacity accounts for more than 98% of the world (Shu et al, 2019a)The total amount of EMS that have been produced in China is about 120–130 million tons (Shu et al, 2019b) with an increasing rate of 11 million Bioleaching of manganese from electrolytic manganese slag The invention relates to a production method of electrolytic manganese dioxide, which comprises the following steps: A preparing a mixed solution of crude manganese sulfate and ore pulp; B neutralizing and deironing the solution of crude manganese sulfate and ore pulp; C carrying out three times of deep purification and impurity removal on the crude manganese sulfate solution: Production method of electrolytic manganese dioxide
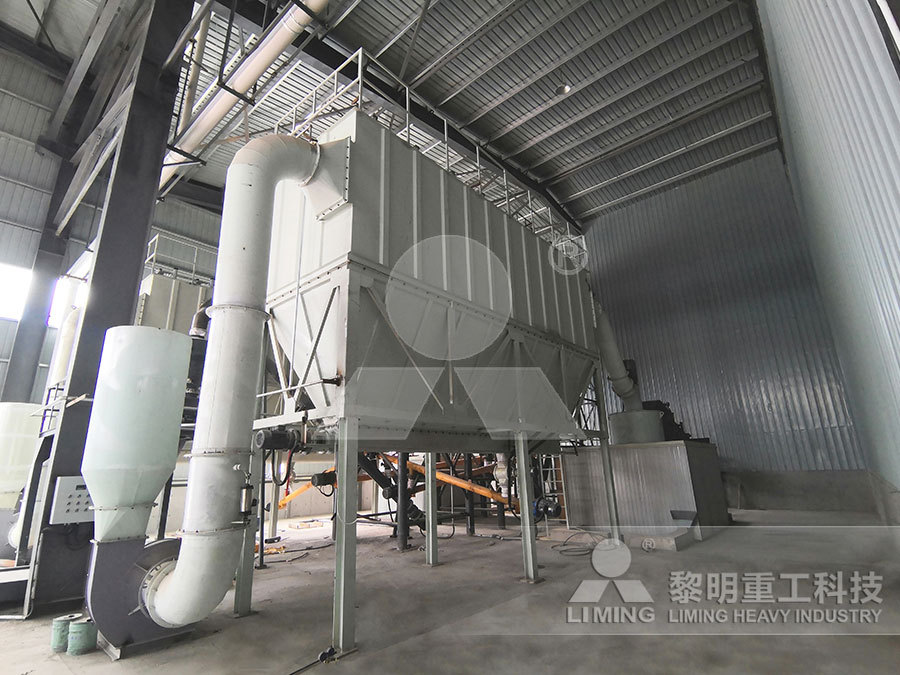
EXECUTIVE SUMMARY DSIR
2024年5月27日 ganese dioxide is electrolytic manganese dioxideEMD Though anodic oxidation of Mn2* salt to manganese dioxide goes back to 1830, yet the usefulness ofEMD was not recognised until 1918 EMD has the ability to function superbly as solid state oxygen electrode in dry cell battery over a wide range of discharge conditions Manganese dioxide, manga2024年1月15日 Electrolytic manganese slag (EMS), a bulk waste generated in industrial electrolytic manganese production, can be a costeffective adsorbent for heavy metals removal after appropriate modification In this study, EMS was activated by NaOH and then used to make the EMSbased doublenetwork hydrogel (an EMS/PAA hydrogel) via a onepot methodA novel doublenetwork hydrogel made from electrolytic manganese slag RSC Advances REVIEW Cite this: RSC Adv, 2015, 5, 58255 Electrolytic manganese dioxide (EMD): a perspective on worldwide production, reserves and its role in electrochemistry Avijit Biswal,abc Bankim Chandra Tripathy,bc Kali Sanjay,bc Tondepu Subbaiahbcd and Manickam Minakshi*a Electrolytic manganese dioxide (EMD) is the critical component of Electrolytic manganese dioxide (EMD): a perspective on Request PDF On Apr 1, 2019, Gigla Tsurtsumia and others published Novel hydroelectrometallurgical technology for simultaneous production of manganese metal, electrolytic manganese dioxide, and Novel hydroelectrometallurgical technology for
.jpg)
Synergistic solidification/stabilization of electrolytic manganese
2022年3月1日 Generally, electrolytic metallic manganese (EMM) is produced by the “leachingpurificationelectrodeposition” process since it shows a wide raw materials adaptability, especially for the lowgrade manganese ore (8–15%), without scarifying the product quality (Li et al, 2021a; Li et al, 2021b)2020年5月6日 that 30`), manganese, the cost of production of electrolytic manganese in India in a 10tonaday plant is not likely to exceed Rs 1,00(1 a ton The work being done at the Laboratory to produce electrolyticbatteryactive manganese dioxide front lowgrade Indian ores, is discussed separately; it is stated that laboElectrolytic Manganese Manganese Dioxide from Low 2013年2月1日 Subsequently the coal ash and manganese slag, produced by the combustion of high sulfur coal and preparation of electrolytic manganese, can be used as raw ingredients for the preparation of Labscale circulation process of electrolytic manganese production 2011年1月1日 1 Introduction Electrolytic manganese slag is enormously produced from the electrolytic manganese metal (EMM) industry as a main solid waste, about 6–9 tons of the solid waste is discharged into the environment for per ton EMM (Duan et al, 2010)In China, there is more than 2 × 10 6 tons of electrolytic manganese slag discharged per year due to nearly Extraction of manganese from electrolytic manganese
.jpg)
Electrolytic manganese dioxide (EMD): a perspective on
2015年7月3日 Electrolytic manganese dioxide (EMD) is the critical component of the cathode material in modern alkaline, lithium, and sodium batteries including electrochemical capacitors and hydrogen production In terms of environmental and cost considerations, EMD is likely to remain the preferred energy material for the future generation, as it has been in recent 2013年6月1日 Electrolytic manganese residue (EMR) is added into ground granulated blastfurnace slag (GGBS) as an activator to prepare EMR–GGBS cement The effects of chemical activation, mechanical Preparation of electrolytic manganese residue–ground Part I: Leaching of ores/secondary materials and recovery of electrolytic/chemical manganese dioxide (1977) reported a hydrometallurgical process for the recovery of manganese from slag leaching solutions The solution contained Manganese metallurgy review Part I: Leaching 2022年3月1日 Generally, electrolytic metallic manganese (EMM) is produced by the “leachingpurificationelectrodeposition” process since it shows a wide raw materials adaptability, especially for the lowgrade manganese ore (8–15%), without scarifying the product quality (Li et al, 2021a; Li et al, 2021b)China is the largest EMM producer and exporter in the world (Zhang et al, Synergistic solidification/stabilization of electrolytic manganese
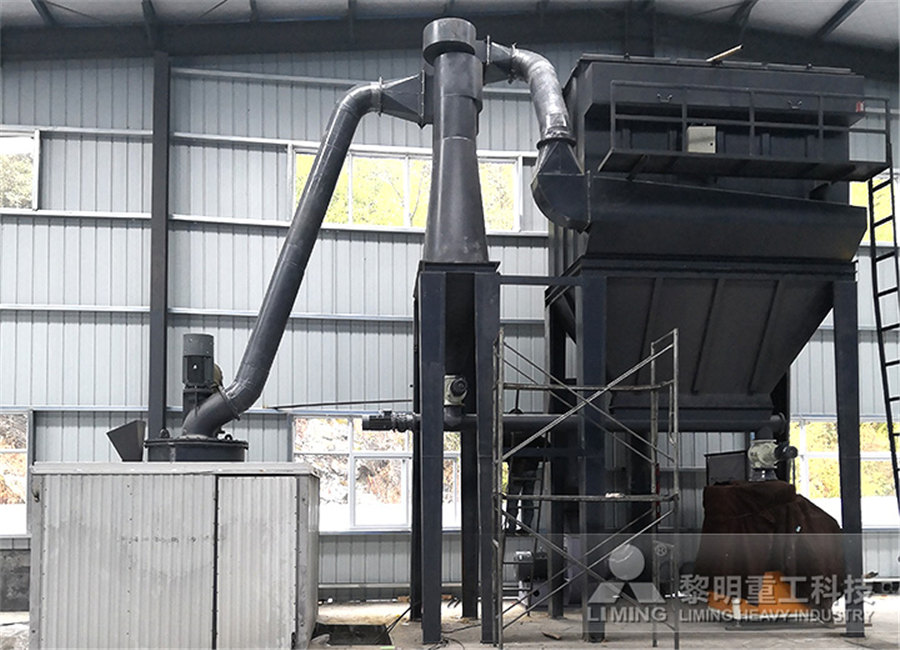
A novel method for solidification/stabilization of Cd(II),
2021年5月5日 A novel material (named AEMS) for heavy metal removal was proposed by ball grinding activated electrolytic manganese slag (EMS) with low content of sodium hydroxide For different application scenarios, the two physical properties of the materials were developed: the powdery AEMS (powder) was used to remove heavy metals from wastewater2021年9月15日 Manganese mainly exists as manganese ores in nature, and manganese ores are geographically varied (Li et al, 2018, Zhan and Zhang, 2019)South Africa, Ukraine, Brazil, Australia, India, China, Gabon, and Mexico account for almost 9739% of the global reserves (690,000 kt) with a grade of 15%–50% (Fig 1 a)China only takes 623% (43,000 kt) A critical review on approaches for electrolytic manganese residue How to choose the grinding mill equipment in the electrolytic manganese powder workshop? The raw material for the production of electrolytic manganese is manganese ore powder However, since most manganese ores are finegrained or microfinegrained, and there are a considerable amount of highphosphorus ore, highiron ore and cogenerated beneficial metals, it brings How to choose the electrolytic manganese powder grinding mill equipment 2023年5月24日 electrolytic manganese dioxide from manganese oxide ores, high or lowgrade A material balance was performed on the designed flowsheet to check the feasibility of using recycled streams The use of bags around the anodes makes it possible to utilize the iron in the feed as a recyclable reductant for the dissolution of manganese oresSustainable Production of Electrolytic Manganese
.jpg)
Recyling manganeserich electrolytic residues: a review
Huge amounts of manganeserich solid residues are yearly produced worldwide by industrial electrolysis, calling for advanced methods of recycling in the context of the circular economy Here, we review manganese recycling with focus on ore reserves, electrolytic production, residue stockpiling and environmental impact, reducing the amount of residue and improving metal 2023年6月1日 0duction process, only 719% of manganese from raw materials is converted into the final product, while the rest enters the anode slag, known as electrolytic manganese anode slag (EMAS) [3]For every 1 ton of electrolytic manganese produced, 50–150 kg of anode slag is generated [4]In China, the annual output of electrolytic manganese is approximately 15 Kinetics and mechanism of manganese reductive leaching 2021年8月5日 Electrolytic manganese residue (EMR), a byproduct of the electrolytic manganese metal production process, contains several hazardous components such as ammonia nitrogen (NH 3N), soluble manganese, and heavy metals In recent years, although a great number of treatment methods have been proposed, there is no mature and economical Selective recovery of manganese from electrolytic manganese