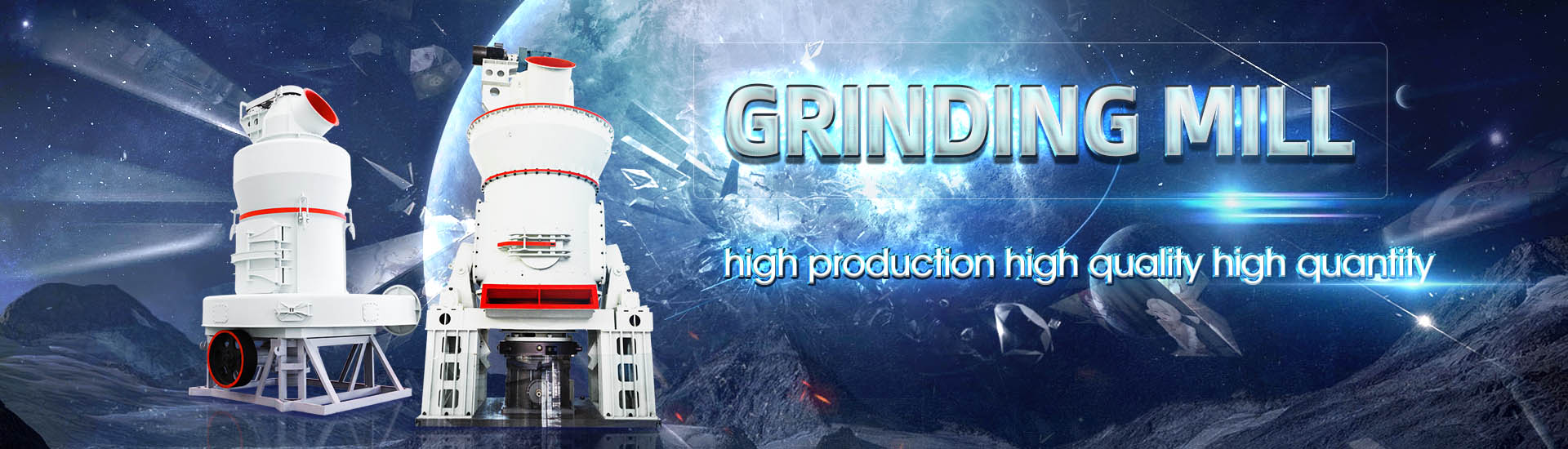
Leaching slag grinding equipment investment cost
.jpg)
Review on comprehensive utilization of nickel laterite ore
2024年11月1日 Hydrometallurgical processes have the advantages of low energy consumption, high nickel leaching rates, and effective cobalt recovery However, their drawbacks include high investment costs, complex operations, short equipment lifespan, and large amounts of difficult Challenges in processing technology and cost control in smelting enterprises contribute to the slag stockpile issue, leading to significant pollution of the surrounding environment and Resource utilization strategy of Febearing smelting slag in 2021年6月23日 Depending on your mineralogical requirements, nickel laterite highpressure acid leaching (HPAL) solutions are available, using Metso Outotec OKTOP autoclaves and other Hydrometallurgical nickel and cobalt plants and processes2023年11月20日 The hydrometallurgical method involves leaching metallic values from the slag in an aqueous acidic or alkaline medium The typical process steps are shown in Fig 12 However, a prior slag grinding to a fine powder is A Review on Environmental Concerns and

Comprehensive Review on Metallurgical Upgradation
2022年2月11日 Due to its characteristics of low investment, low cost, simple process flow, and environmentalfriendly, bioleaching is suitable for treating lowgrade and other refractory 2021年5月1日 A suitable lixiviant or leaching agent is required for the effective extraction of desired metals Leaching stage or solubilization process is where the solid waste is converted Current technologies for recovery of metals from industrial 2019年5月31日 The slowcooled slag is crushed, sieved, and ground before recovery of valuable metals via floatation, magnetic separation, or leaching Thus, investment in equipment and Preface for Thematic Section: Slag Granulation2022年7月11日 The expected benefits to leaching however need to be considered given the energy cost associated with ultrafine grinding and expenditure due to consumption of grinding mediaFull article: The Direct Leaching of Nickel Sulfide
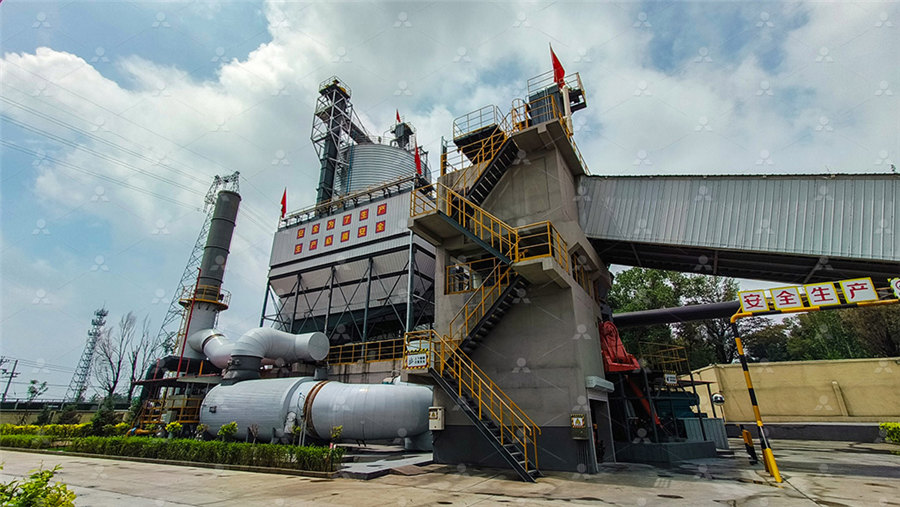
Full article: Synthesis of βSiAlON materials from blast furnace slag
3 天之前 In order to optimize the utilization of blast furnace slag (BFS) and enhance the costeffectiveness and feasibility of βSiAlON preparation, a novel approach involving acetic acid 2019年5月23日 Steel slag is the waste generated in the steelmaking process and includes ferric oxide and the impurities of some infusible matters It is the byproduct when slagforming Comprehensive Utilization Technology of Steel Slag2024年4月9日 Indirect carbonation of steel slag is an effective method for CO2 storage, reducing emissions, and promoting cleaner production in the steel industry However, challenges remain, such as low Ca2+ leaching rates and slag management complexities arising from variations in mineral compositions To address this, a hightemperature modification process is proposed to Mechanistic study on the promotion of Ca2+ leaching in steel slag 2021年5月1日 The smelting process can be divided into three stages, namely decomposition of highvalence sulphide, oxidation of sulphide, and matte smelting and slagging reaction (Fig 1)The efficiency of matte smelting and matteslag separation, as well as the extent of copper losses to slag are mainly affected by the oxidation/reduction potential, matte grade, smelting Comprehensive review on metallurgical recycling and cleaning of copper slag
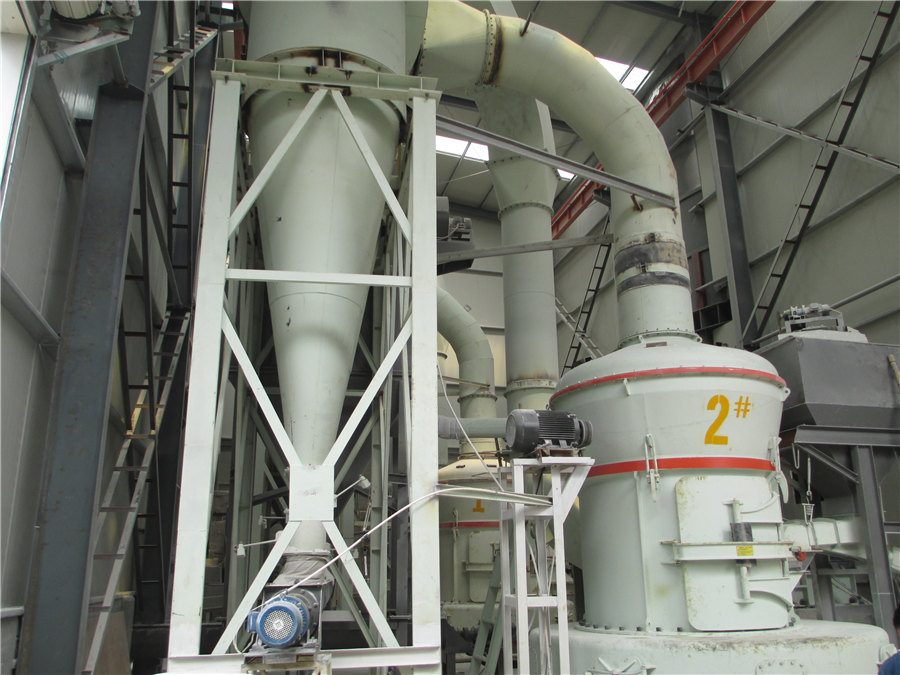
Hydrometallurgical nickel and cobalt plants and processes
2021年6月23日 typically includes pulping, preleaching, pressure leaching in autoclaves, solidliquid separation, and scrubbing stages Similar leaching circuits are used for leaching metallic and intermediate nickel and cobalt products The leaching process results in an aqueous nickel and/or cobalt sulfate solution This solution is further treated through2024年9月1日 The mechanochemical leaching (MCL) process presents promising potential for efficiently extracting zinc from zinc oxide ores This study analyzed the effects of several grinding parameters, including the agitator type, grinding ball size and material, grinding ball addition, and stirring speed, on the zinc leaching Among them, the agitator type affects the flow form and Improvement of mechanochemical leaching of zinc oxide ore 2017年10月13日 Leaching processes are classified based on the method used for the leaching of metals, ie hydrometallurgy (chemicals) or biohydrometallurgy (microbial mediated leaching) Different leaching processes and the leaching of metals from various metal bearing solid wastes are discussed in detail below 631 Hydrometallurgical ProcessesLeaching and Recovery of Metals SpringerLinkAfter that, the solution is filtered to obtain an electrolytic liquor that can produce zinc The zinc powder can be transferred from the electrolyte to the product by the electrodeposition method, and the purified slag and leaching slag can be returned to the steelmaking process to recover valuable metals such as iron 322 Alkali Leaching Recovery of Zinc and Iron from Steel Mill Dust—An Overview
.jpg)
Kinetics analysis of copper extraction from copper smelting slag
2024年9月15日 Under the optimum conditions, 907 % of the copper in the CSS was effectively leached, other copper in the leaching slag mainly existed in the form of finegrained embedded copper sulfide The dominant phase of the leaching slag is magnetite, which could be further recovered by conventional magnetic separation2016年2月29日 In this part, a reliable sampling representing the ore is a key aspect Separation, concentration and leaching processes involve several operations such as screening, classification, solidliquid separations, gravimetry, flotation, and pregnant liquid solution treatment rod mills and ball mills are the classical pieces of grinding Gold Extraction Recovery Processes 911Metallurgist2024年9月7日 which couple ultrafine grinding and oxidative leaching in an effort to reduce the capital costs associated with Pressure Leaching, Bacterial Leaching and Roasting One such processes is MIM Holdings’ ALBION Process 20 CASE STUDY 0 Comparative fine grinding and oxidative leaching testwork was carried out on a sample ofIsaMill Ultrafine Grinding for a Sulphide Leach Process2023年7月25日 The size and capacity of a gold leaching plant significantly impact its cost Larger plants require more substantial investments in infrastructure, equipment, and labor Moreover, higher capacity plants necessitate more extensive processing facilities and a larger workforce, resulting in increased operational costs 2) Ore CharacteristicsFinding the Costs: How Much Does a Gold Leaching Plant Really Cost?
.jpg)
Efficient and reliable handling of GBFS and GGBFS at grinding
2008年3月3日 The use of GGBFS as a partial Portland cement replacement takes advantage of the energy invested in the slagmaking process and its corresponding benefits with respect to the enhanced cementitious properties of the slag Grinding slag for cement replacement requires only about 25% of the energy needed to manufacture normal Portland cement4 天之前 The doubleimpeller leaching tank is composed of a vertical shaft, a motor base, an impeller, a coupling, a tank cover, a reducer base, a tank body, a coupling support, etc The slurry in the doubleimpeller leaching tank flows Leaching Tank JXSC Machine5 天之前 The gold CIP process includes seven operation stages: preparation of leaching pulp, cyanide leaching, carbon adsorption, goldloaded carbon desorption, electrolysis to obtain muddy gold, degold carbon recycling, and Gold Carboninpulp (CIP) Process JXSC Mineral2024年4月24日 16th Global Slag Conference, Exhibition Awards 2024 23 24 April 2024, Dubai, UAE The 16th Global Slag Conference has successfully taken place in Dubai, UAE, with 175 registered delegates from 32 countries, two field trips to slag grinding plants and the Global Slag Awards dinner at a spectacular camp on the edge of the Arabian DesertReview of 16th Global Slag Conference 2024
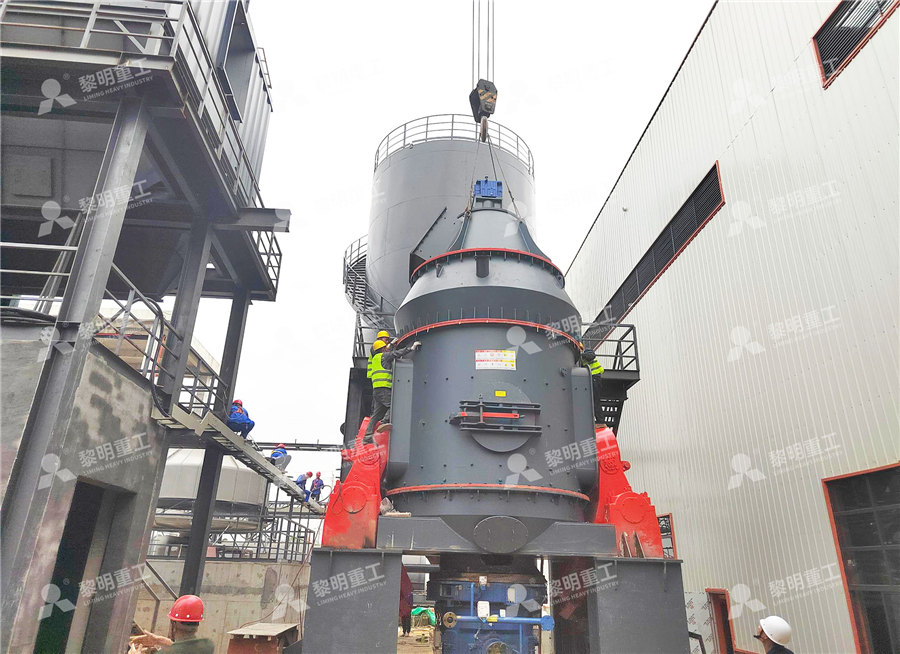
Calcium leaching from waste steelmaking slag
2014年10月1日 Slag leaching experiments conducted by HCl (01 M) also confirmed that CaO was more active than other Cacontaining minerals, its leaching ratio was more than 80%; followed by was silicates, its 2022年2月2日 Banza et al proposed to use oxidationleachingextraction process to treat copper slag, oxidizing and leaching the slag with a mixed solution of H 2 O 2 and H 2 SO 4 under normal pressure, and then using extractant to recover valuable metals step by step The recovery rate of copper can reach 80%A Review of Comprehensive Utilization of Copper Slag of China2024年3月1日 The presence of PVDF prevents the contact of leaching solution and LiCoO 2, which is the decisive factor leading to the low leaching efficiency of electrode materialsTherefore, a dualstrengthening pretreatment method is proposed to remove PVDF more efficiently and enhance the leaching of the LiCoO 2To determine the enhanced effect of the PVDF removal An innovative dualstrengthening pretreatment to improve 2024年6月1日 An innovative vanadium slag‑manganese roasting‑sulfuric acid leaching process (Wen et al, 2019b; Wen et al, 2020b; Wen et al, 2022) involved manganese roasting of vanadium slag, followed by leaching in sulfuric acid at a constant pH of 25 and a temperature of 60 °C for 60 min which resulted in a vanadium leaching efficiency of 894%Review of leaching, separation and recovery of vanadium
.jpg)
Earlystage recovery of lithium from spent batteries via CO
2024年7月29日 Schwich et al 18 investigated an effective ecofriendly “EarlyStage Lithium Recovery” (ESLR) method involving Li leaching through carbonation with supercritical CO 2 in a costintensive 2022年6月3日 Mass transfer is impeded in the leaching of very fine particles if some form of liquid agitation is not introduced due to high settling velocities Solvent: An ideal solvent will have a high saturation limit, high selectivity for the desired solute and Solid Liquid Extraction (Leaching) The Engineer's Perspective2019年5月23日 The process of making steel slag cement is a simple manufacturing technique with less investment and low cost Meanwhile, steel slag cement has excellent performances such as high longterm strength, low heat of hydration, and wear resistance At present, the main grinding equipment of steel slag at home and abroad include ball mill the Comprehensive Utilization Technology of Steel Slag2021年12月3日 Copper slag is generated when copper and nickel ores are recovered from their parent ores using a pyrometallurgical process, and these ores usually contain other elements which include iron Environmental and Socioeconomic Impact of
46.jpg)
Lithium Production and Recovery Methods:
2023年6月29日 The leach solution from slag leaching is also refined The intermediates from both leaching steps are mixed, and a new battery material is grinding, and sieving, it is possible to obtain metals (Equations (7)–(10)) 2009年1月31日 The possibility of hydrometallurgical processing of converter slag from nickel production aimed at integrated use of mineral raw materials and environmental protection is shown(PDF) Ferric leaching of copper slag flotation tailings2022年10月20日 Grinding options for slag and pozzolan Figure 1: annual cost of operating a hot gas generator for drying materials 184,000 185,000 186,000 187,000 188,000 189,000 190,000 operation and lower capital investment cost2 Ball mills have undergone considerable Table 2: example of wear life on FLSmidth’s OK Mill GRINDING Grinding options for slag and pozzolan PEC 2023年3月28日 The increasing lithiumion battery production calls for profitable and ecologically benign technologies for their recycling Unfortunately, all used recycling technologies are always associated Universal and efficient extraction of lithium for lithiumion
.jpg)
Copper Slag Beneficiation Process Equipment JXSC
2024年1月3日 Commonly Used Mineral Processing Equipment for Copper Slag Crushing Equipment At present, it mainly uses jaw crushers The application of other crushing equipment with high efficiency and large crushing ratio, such as deep cavity jaw crushers, doublemoving jaw crushers, inertial cone crushers, etc, is also receiving increasing attention2024年6月13日 Morphology, crystal structure, and surface chemistry of spodumene and their effects on electrochemical leaching It has been found that the morphology and crystal structure of ores greatly impact Direct extraction of lithium from ores by electrochemical leaching Despite this, many smelting enterprises possess limited recycling and treatment capabilities For instance, a domestic copper refining enterprise generates hundreds of tons of copper slag annually, yet only a minimal amount can be sold to cement plants at a low price of 30 yuan per ton, exacerbated by the high treatment costs, so smelting enterprises mostly choose to pile up Resource utilization strategy of Febearing smelting slag in 2019年7月1日 Large amounts of lead slag are produced during the production of primary lead and secondary lead Considering lead concentrate smelting as an example, a primary lead smelting system production of 1 t of lead will discharge 7100 kg of lead slag (Hou, 2011)At the secondary lead recycling process, for each ton of metallic lead produced, 100–350 kg of slag A review on lead slag generation, characteristics, and utilization
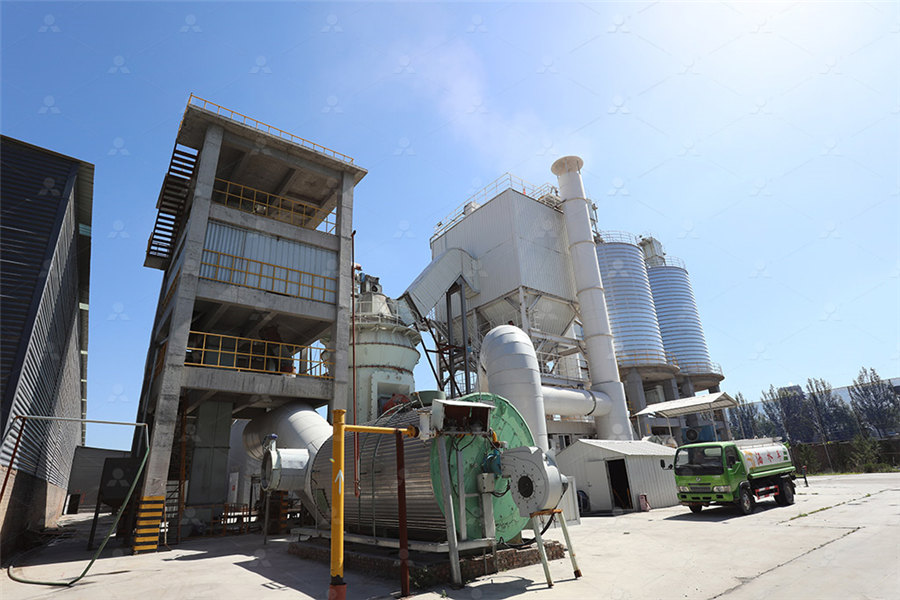
Mechanistic study on the promotion of Ca2+ leaching in steel slag
2024年4月9日 Indirect carbonation of steel slag is an effective method for CO2 storage, reducing emissions, and promoting cleaner production in the steel industry However, challenges remain, such as low Ca2+ leaching rates and slag management complexities arising from variations in mineral compositions To address this, a hightemperature modification process is proposed to 2021年5月1日 The smelting process can be divided into three stages, namely decomposition of highvalence sulphide, oxidation of sulphide, and matte smelting and slagging reaction (Fig 1)The efficiency of matte smelting and matteslag separation, as well as the extent of copper losses to slag are mainly affected by the oxidation/reduction potential, matte grade, smelting Comprehensive review on metallurgical recycling and cleaning of copper slag2021年6月23日 typically includes pulping, preleaching, pressure leaching in autoclaves, solidliquid separation, and scrubbing stages Similar leaching circuits are used for leaching metallic and intermediate nickel and cobalt products The leaching process results in an aqueous nickel and/or cobalt sulfate solution This solution is further treated throughHydrometallurgical nickel and cobalt plants and processes2024年9月1日 The mechanochemical leaching (MCL) process presents promising potential for efficiently extracting zinc from zinc oxide ores This study analyzed the effects of several grinding parameters, including the agitator type, grinding ball size and material, grinding ball addition, and stirring speed, on the zinc leaching Among them, the agitator type affects the flow form and Improvement of mechanochemical leaching of zinc oxide ore
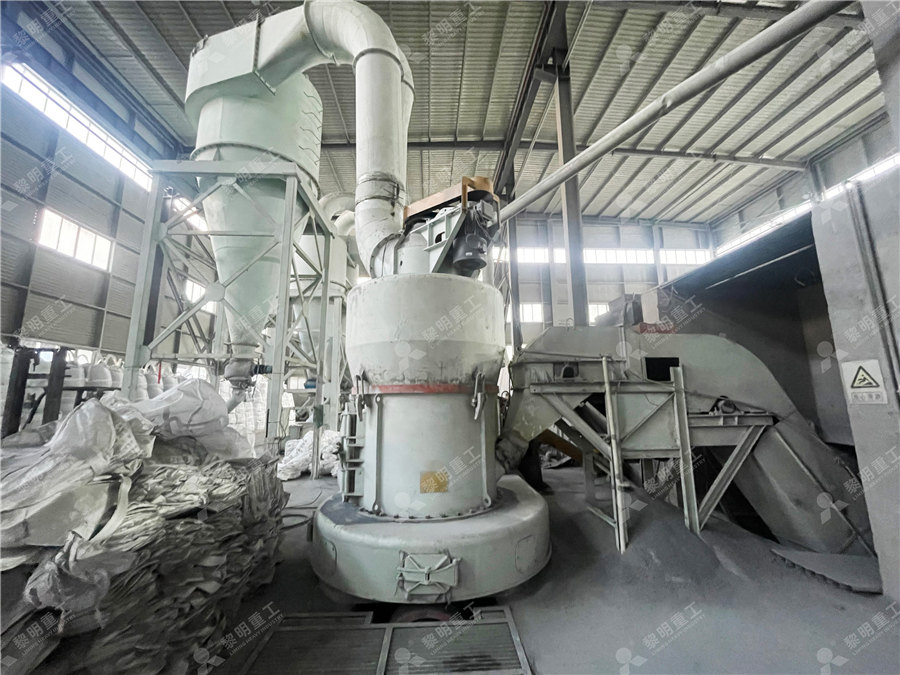
Leaching and Recovery of Metals SpringerLink
2017年10月13日 Leaching processes are classified based on the method used for the leaching of metals, ie hydrometallurgy (chemicals) or biohydrometallurgy (microbial mediated leaching) Different leaching processes and the leaching of metals from various metal bearing solid wastes are discussed in detail below 631 Hydrometallurgical ProcessesAfter that, the solution is filtered to obtain an electrolytic liquor that can produce zinc The zinc powder can be transferred from the electrolyte to the product by the electrodeposition method, and the purified slag and leaching slag can be returned to the steelmaking process to recover valuable metals such as iron 322 Alkali Leaching Recovery of Zinc and Iron from Steel Mill Dust—An Overview 2024年9月15日 Under the optimum conditions, 907 % of the copper in the CSS was effectively leached, other copper in the leaching slag mainly existed in the form of finegrained embedded copper sulfide The dominant phase of the leaching slag is magnetite, which could be further recovered by conventional magnetic separationKinetics analysis of copper extraction from copper smelting slag 2016年2月29日 In this part, a reliable sampling representing the ore is a key aspect Separation, concentration and leaching processes involve several operations such as screening, classification, solidliquid separations, gravimetry, flotation, and pregnant liquid solution treatment rod mills and ball mills are the classical pieces of grinding Gold Extraction Recovery Processes 911Metallurgist
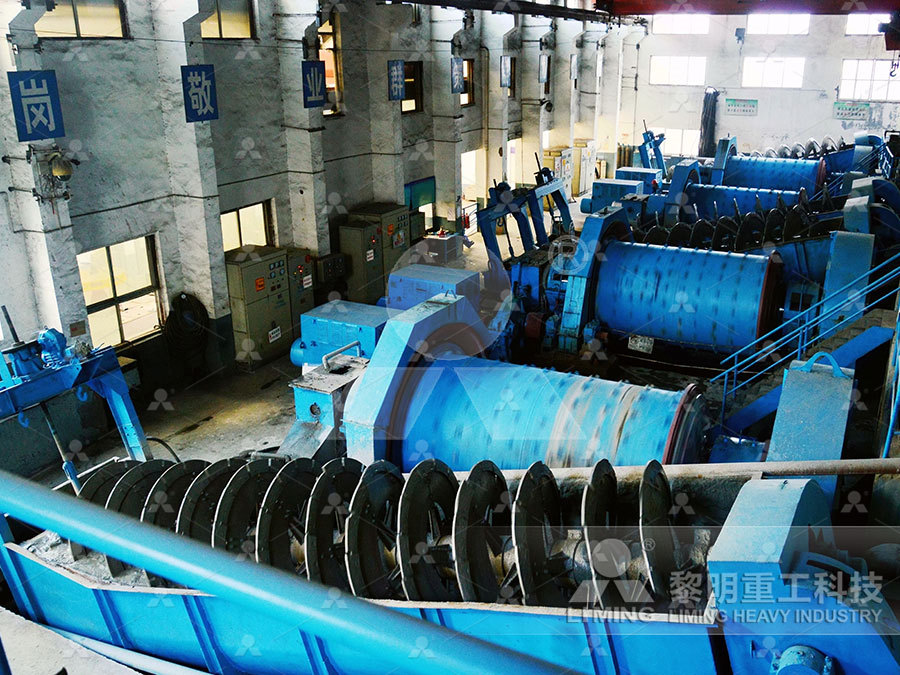
IsaMill Ultrafine Grinding for a Sulphide Leach Process
2024年9月7日 which couple ultrafine grinding and oxidative leaching in an effort to reduce the capital costs associated with Pressure Leaching, Bacterial Leaching and Roasting One such processes is MIM Holdings’ ALBION Process 20 CASE STUDY 0 Comparative fine grinding and oxidative leaching testwork was carried out on a sample of2023年7月25日 The size and capacity of a gold leaching plant significantly impact its cost Larger plants require more substantial investments in infrastructure, equipment, and labor Moreover, higher capacity plants necessitate more extensive processing facilities and a larger workforce, resulting in increased operational costs 2) Ore CharacteristicsFinding the Costs: How Much Does a Gold Leaching Plant Really Cost?