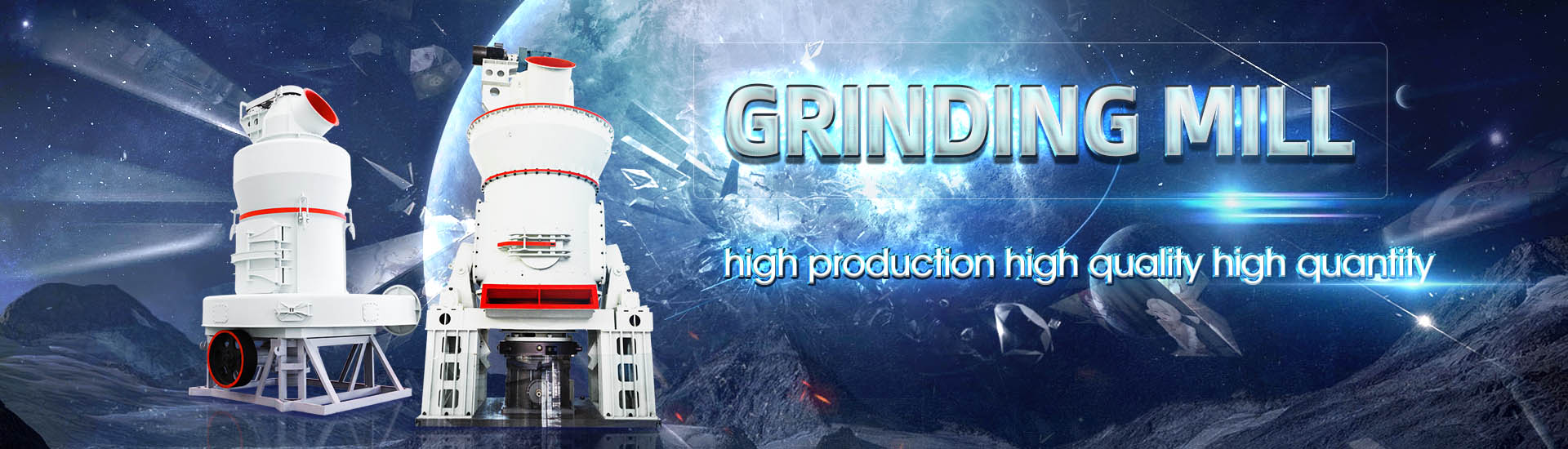
Cement surface ore mill
.jpg)
BALL MILLS Ball mill optimisation Holzinger Consulting
2021年3月12日 Ball mill optimisation As grinding accounts for a sizeable share in a cement plant’s power consumption, optimisation of grinding equipment such as ball mills can provide 2023年10月27日 Grinding media play an important role in the comminution of mineral ores in these mills This work reviews the application of balls in mineral processing as a function of the A Review of the Grinding Media in Ball Mills for Mineral 2017年8月11日 a Loesche mill, with a grinding track diameter of only 11 metres, was used as long ago as 1935 However, the breakthrough in grinding this type of material on the vertical 2 µm 5 µm Loesche2023年7月4日 The vertical roller mill has the advantages of low energy consumption, high output, easy maintenance, etc, and has been widely applied in cement, steel and power Roller Mill SpringerLink
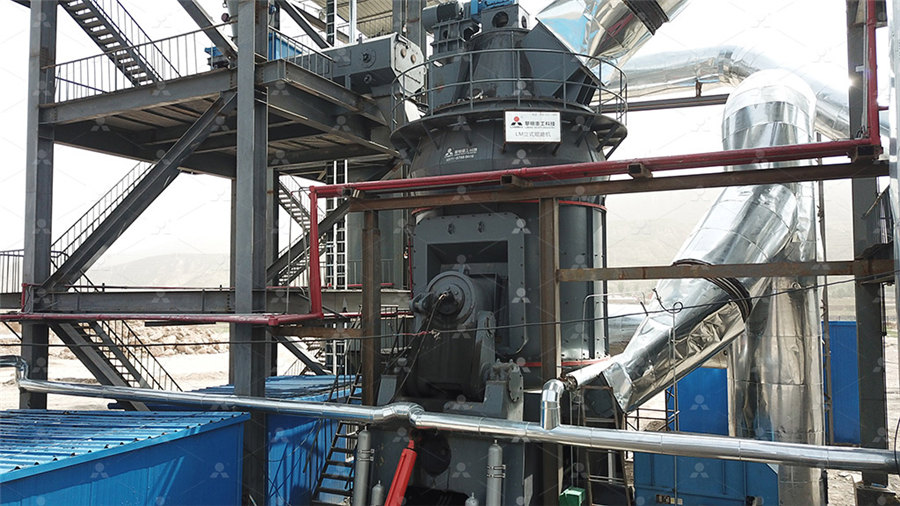
(PDF) Grinding in Ball Mills: Modeling and Process Control
2012年6月1日 The paper presents an overview of the current methodology and practice in modeling and control of the grinding process in industrial ball mills Basic kinetic and energy 2021年1月1日 A twocompartment ball mill with a highly efficient separator is still procured for new cement grinding units installation, although the vertical roller mill has now become a true Review on vertical roller mill in cement industry its 2015年3月15日 This paper presents an experimental approach to measure and model the residence time distribution of vertical roller mill in cement clinker grinding circuitResearch of iron ore grinding in a verticalrollermill2015年4月1日 Production capacity of a fully airswept industrial scale twocompartment KHD Humboldt Wedag® cement ball mill was optimized with the aid of simulation It was proposed Optimization of a fully airswept dry grinding cement raw
7TOCS.jpg)
EnergyEfficient Advanced Ultrafine Grinding of
2023年7月10日 Stirred mills are compressive grinding mills with potential in the mineral and cementbased processing industries for reducing the particle size from a few millimetres to a micron2022年1月23日 This work concentrates on the energy consumption and grinding energy efficiency of a laboratory vertical roller mill (VRM) under various operating parameters For design of experiments (DOE), the response surface method Analysis and Optimization of Grinding 2017年10月26日 The following are factors that have been investigated and applied in conventional ball milling in order to maximize grinding efficiency: a) Mill Geometry and Speed – Bond (1954) observed grinding efficiency to be a Factors Affecting Ball Mill Grinding Efficiency2023年10月27日 The ball mill is a rotating cylindrical vessel with grinding media inside, which is responsible for breaking the ore particles Grinding media play an important role in the comminution of mineral ores in these mills This work reviews the application of balls in mineral processing as a function of the materials used to manufacture them and the mass loss, as A Review of the Grinding Media in Ball Mills for Mineral
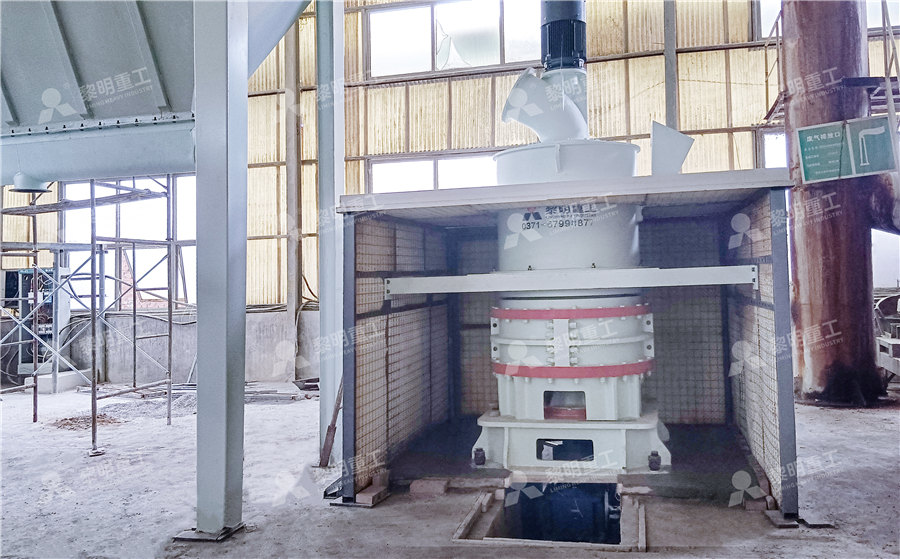
Mill drives INFINITY FOR CEMENT EQUIPMENT
Mill drives Central drive Gear and pinion drive and without impairing the tooth surface contact (telescopic effect) Position deviations of the mill flange are absorbed by the toothed coupling and by the torsional shaft The largest planetary gears for ball mill drives in the cement industry supplied at this writing by the Maag Gear 2013年8月1日 Apart from these cost factors, one of the major unsolved problems in the optimal design of ball mills concerns the equilibrium media size distribution in the mill, which is determined by the rate at which makeup media is added to the mill, as well as the rate at which these grinding media are consumed (Austin and Klimpel, 1985)Reliable prediction of grinding media Consumption of steel grinding media in mills – A reviewAs the main equipment in iron ore pelletizing plants, a damp mill is mainly used for the damp grinding of iron ore to provide materials for the pelletizing disc It can deal with iron ore with a water content of 813%, not only increasing the surface area of the ore particles but also making the ore fully mixed and ground to shorten the whole Damp Mill – Ball Grinding Machine Iron Ore Pelletizing 2021年3月12日 and cement Roller presses are used mainly in combination with a ball mill for cement grinding applications and as finished product grinding units, as well as raw ingredient grinding equipment in mineral applications This paper will focus on the ball mill grinding process, its tools and optimisation possibilities (see Figure 1) The ball millBALL MILLS Ball mill optimisation Holzinger Consulting
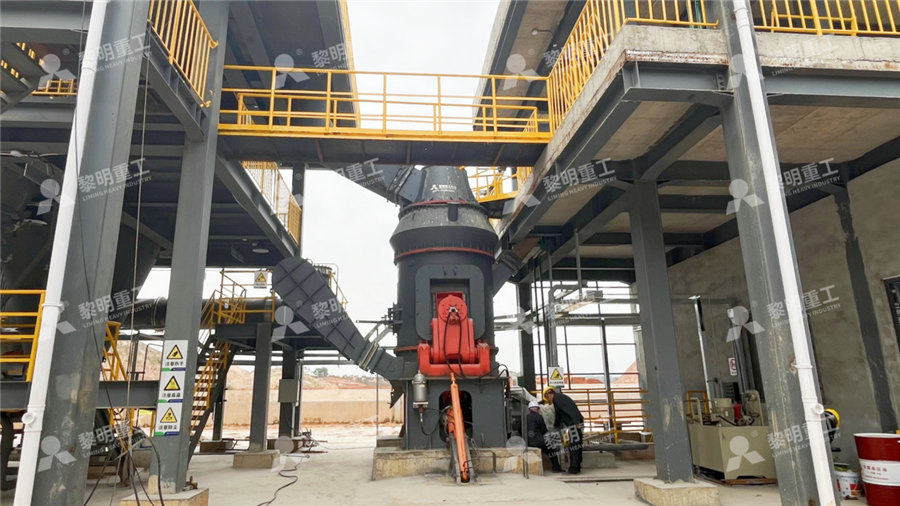
EnergyEfficient Advanced Ultrafine Grinding of Particles
2023年7月10日 The present literature review explores the energyefficient ultrafine grinding of particles using stirred mills The review provides an overview of the different techniques for size reduction and the impact of energy requirements on the choice of stirred mills It also discusses the factors, including the design, operating parameters, and feed material properties, 2013年2月1日 PDF Stirred media mill is one of the most energyefficient types of grinding equipment for wet ultrafine grinding Nevertheless, in a dry mode several Find, read and cite all the research (PDF) Mechanical activation of cement in stirred media millAn ore with a dilution rate of 884% should not be sent to the mill for processing, but action must be taken to separate waste from the ore either underground or on surface If this is not possible, then this material must be treated as waste and Monitoring ore loss and dilution for minetomill 2019年5月6日 The initial and final setting of ecocement containing gold ore tailing (GTs) was decreased and increased by 142% and 142% respectively, as compared to reference OPC paste (Wang et al, 2019 (PDF) Preparation of Portland Cement with Gold Ore Tailings
.jpg)
Ball Mill for Gold Ore, Rock, Copper, Cement Grinding
2024年11月14日 Ball Mill for Gold Ore, Rock, Copper, Cement Grinding, Find Details and Price about Ball Mill Grinding Machine from Ball Mill for Gold Ore, Rock, Copper, Cement Grinding Changsha Mining Equipment Co, LtdSemifinishing grinding system: after ground by cement roller press, materials are divided into three parts through an air classifier: coarse, medium and fine, in which the coarse material is returned to the roller press for regrinding, the medium material is put into a ball mill for further grinding, and the fine material is directly discharged as the finished cement productCement Roller Press Roller Press In Cement Plant Roller 2022年11月1日 The fineness of the final cement product discharged from the mill has a specific surface area (SSA) in the range of 300–500 m 2 /kg depending on the intended cement quality (Saleh and Rahman, 2018) Specific applications require specific cement sizes For example, Zhang (2011) stated that the SSA of Portland cement should exceed 300 m 2 /kg Impact of ball size distribution, compartment configuration, 2024年4月26日 These mills utilize the ore itself as the grinding media, reducing the need for additional grinding media AG/SAG mills are typically used for coarse grinding, where large pieces of ore are efficiently broken down Flotation is a selective separation process that relies on the differences in the surface properties of the ore minerals Iron Ore Processing: From Extraction to Manufacturing
.jpg)
Recycling steel mill scale as fine aggregate in cement mortars
2008年12月1日 Concrete with EAF slag (Fe 2 O 3 > 97%) as fine aggregate up to 30% replacement of natural fine aggregate exhibits higher compressive strength up to 180 days of curing [Qasrawi et al 2009]The characteristic tumbling motion of these mills has given them the name ‘tumbling mills’, which include the ball mill, tube mill and rod mill Ball mills are horizontal rotating cylindrical or conical steel chambers, approximately one third to half full of steel, alloy steel or iron balls, like that shown in Fig 410 A–C , or flint stonesBall Mill an overview ScienceDirect TopicsThe cement separator is also called cement mill separator It is a crucial cement making machine in cement grinding plant Cyclone air separator is a kind of efficiency powder classifier, widely used in cement plants IRON ORE PELLETIZING Pelletizing Disc Annular Cooler Grate Kiln Damp Mill Rotary Drum Mixer Iron Ore Dryer Traveling Cement Separator – Cement Mill Separator Cyclone Air Find your ore mill easily amongst the 42 products from the leading brands (Fritsch GmbH, Retsch, Eriez, ) on DirectIndustry, the industry specialist for your professional purchases Exhibit with us {{>currencyLabel}} vertical cement mills with productivity of 50250t/hOre mill, Ore grinding mill All industrial manufacturers
.jpg)
Grinding Media in Ball Mills for Mineral Processing
2023年11月24日 The cement and pharmaceutical industries normally use dry grinding whereas the mineral processing industry mostly resorts to wetmilling Shahbazi et al , friction coefficients between media and lifter and media–media affect the media position in the mill Also, the surface area, which is affected by media shape, causes the charge to 2023年11月1日 Powder grinding technology was a method of reducing traditional powders to particles in the micrometer range, resulting in a significant increase in material surface area and reactivity [7]This technique had a notable impact on the physical, mechanical, and chemical properties of materials [8, 9]Mechanical grinding was an effective method for processing Mechanical grinding kinetics and particle packing novel 2017年4月1日 Recent installations and developments of loesche vertical roller mills in the ore industry Comminution’12 Proceedings, Cape Town, South Africa (2012), pp 122 Google Scholar Operational experience from the United States’ first vertical mill for cement grinding Cement Industry Technical Conference, IEEE (2005), pp 241249Operational parameters affecting the vertical roller mill 2015年12月1日 Bilge et al [13] adopted a polyacrylic acid as grinding aid to investigate the influence of grinding parameters on the grindability of gypsum ore in a dry ball mill The results showed https An experimental study on the ultrafine grinding of gypsum ore
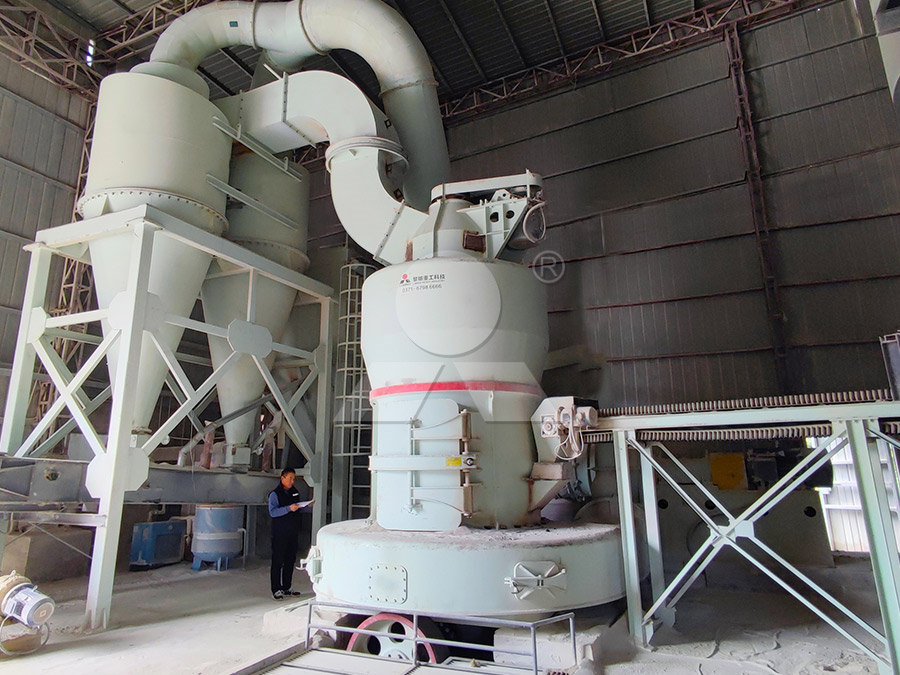
A generic wear prediction procedure based on the discrete
2017年8月1日 Ball mills, ie rotating cylindrical drums filled with a feed material and several hundred thousand metal balls, also known as the charge, are a major category of grinding devices in mineral processing and cement production (Fig 1)Grinding is the final stage of particle size reduction, also known as comminution, which consists in breaking already small ore or clinker 2024年9月1日 hardest materials The OK™ cement mills are available in all sizes 0 100 200 300 400 500 600 700 800 OK 776 OK 434 OK 484 OK 404 OK 524 OK 716 OK 816 OK 666 OK 614 OK 564 OK ™ cement mill production and slag grinding production (t/h) OK 283 OK 373 OK ™ cement mill and slag grinding Actual capacity depends on product fineness OK™ CEMENT MILL2020年5月21日 Irregular concrete surface is unsafe for wheel tires Due to this irregularity the noise caused due to friction increases too Milling helps in restoring the smooth concrete surface This results in better road experience It is a great way to increase the aesthetic appeal of concrete surface Milling polishes the upper surface and makes it shineConcrete Milling: Why, What and How to Mill [Tips]2022年5月9日 By initiating a CL for an industrial cement vertical roller mill (VRM), this study conducted a novel strategy to explore relationships between VRM monitored operational variables and their Modeling of energy consumption factors for an industrial cement
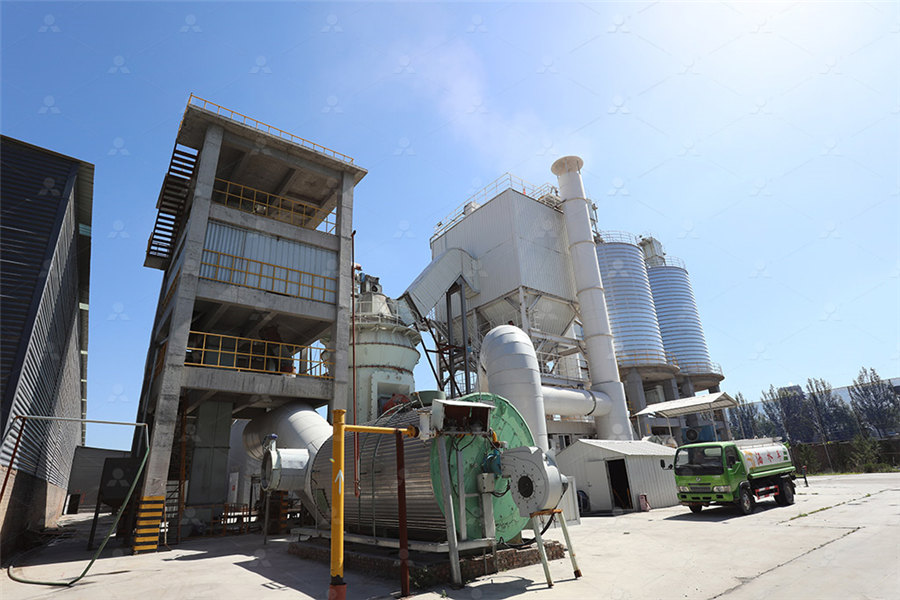
Raw Mill Feeding Cement Plant Optimization
The system consists of material hoppers/bins, weighing, conveying, venting and mill feeding gate Mill Feeding Hoppers Hoppers for limestone/ clay/ iron ore serve the purpose of providing a buffer storage for mill feed and a convenient arrangement for feeding to weigh feeders for proportioning purpose2022年1月23日 This work concentrates on the energy consumption and grinding energy efficiency of a laboratory vertical roller mill (VRM) under various operating parameters For design of experiments (DOE), the response surface method Analysis and Optimization of Grinding 2017年10月26日 The following are factors that have been investigated and applied in conventional ball milling in order to maximize grinding efficiency: a) Mill Geometry and Speed – Bond (1954) observed grinding efficiency to be a Factors Affecting Ball Mill Grinding Efficiency2023年10月27日 The ball mill is a rotating cylindrical vessel with grinding media inside, which is responsible for breaking the ore particles Grinding media play an important role in the comminution of mineral ores in these mills This work reviews the application of balls in mineral processing as a function of the materials used to manufacture them and the mass loss, as A Review of the Grinding Media in Ball Mills for Mineral
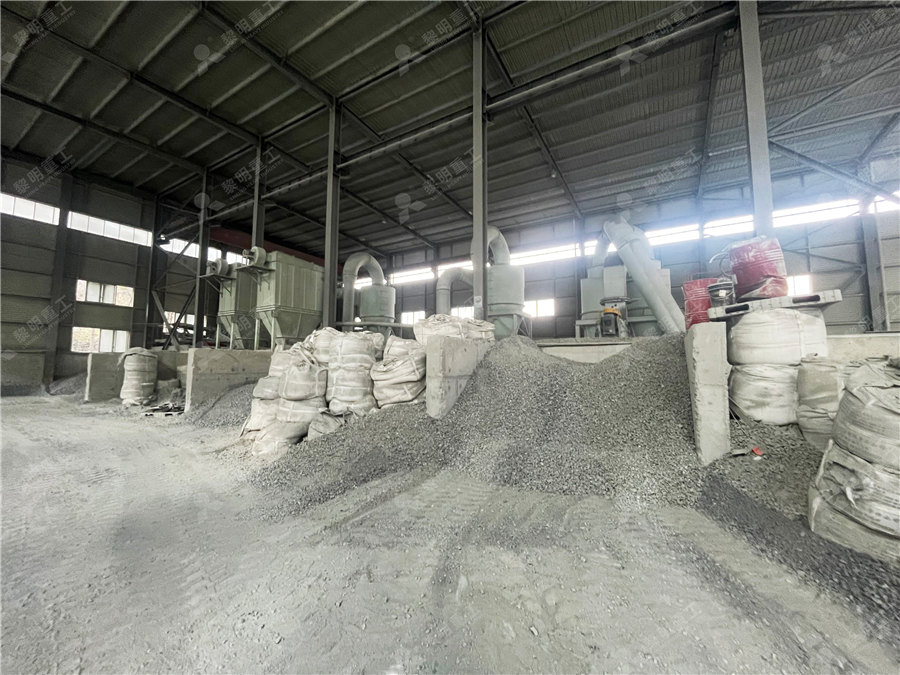
Mill drives INFINITY FOR CEMENT EQUIPMENT
Mill drives Central drive Gear and pinion drive and without impairing the tooth surface contact (telescopic effect) Position deviations of the mill flange are absorbed by the toothed coupling and by the torsional shaft The largest planetary gears for ball mill drives in the cement industry supplied at this writing by the Maag Gear 2013年8月1日 Apart from these cost factors, one of the major unsolved problems in the optimal design of ball mills concerns the equilibrium media size distribution in the mill, which is determined by the rate at which makeup media is added to the mill, as well as the rate at which these grinding media are consumed (Austin and Klimpel, 1985)Reliable prediction of grinding media Consumption of steel grinding media in mills – A reviewAs the main equipment in iron ore pelletizing plants, a damp mill is mainly used for the damp grinding of iron ore to provide materials for the pelletizing disc It can deal with iron ore with a water content of 813%, not only increasing the surface area of the ore particles but also making the ore fully mixed and ground to shorten the whole Damp Mill – Ball Grinding Machine Iron Ore Pelletizing 2021年3月12日 and cement Roller presses are used mainly in combination with a ball mill for cement grinding applications and as finished product grinding units, as well as raw ingredient grinding equipment in mineral applications This paper will focus on the ball mill grinding process, its tools and optimisation possibilities (see Figure 1) The ball millBALL MILLS Ball mill optimisation Holzinger Consulting
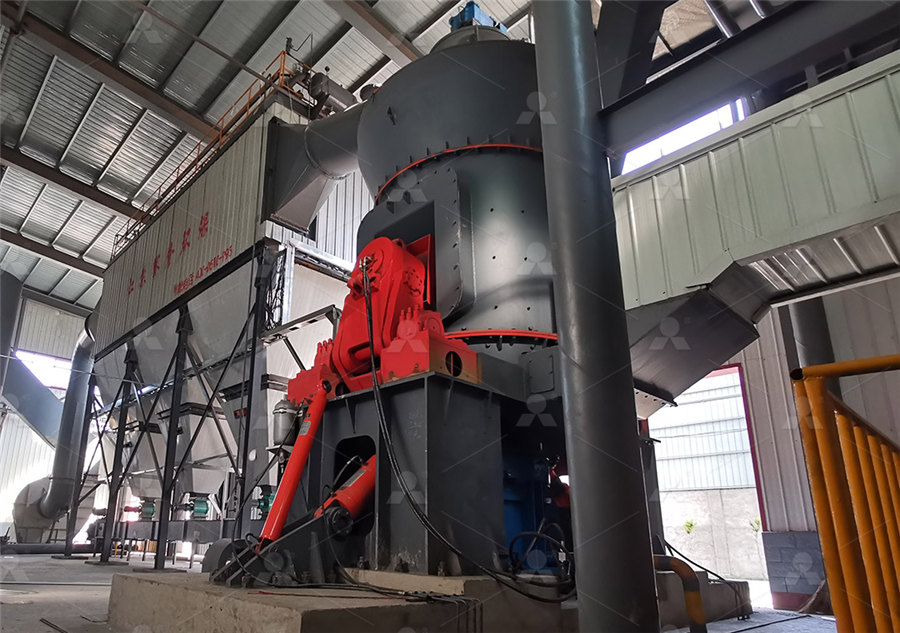
EnergyEfficient Advanced Ultrafine Grinding of Particles
2023年7月10日 The present literature review explores the energyefficient ultrafine grinding of particles using stirred mills The review provides an overview of the different techniques for size reduction and the impact of energy requirements on the choice of stirred mills It also discusses the factors, including the design, operating parameters, and feed material properties, 2013年2月1日 PDF Stirred media mill is one of the most energyefficient types of grinding equipment for wet ultrafine grinding Nevertheless, in a dry mode several Find, read and cite all the research (PDF) Mechanical activation of cement in stirred media mill