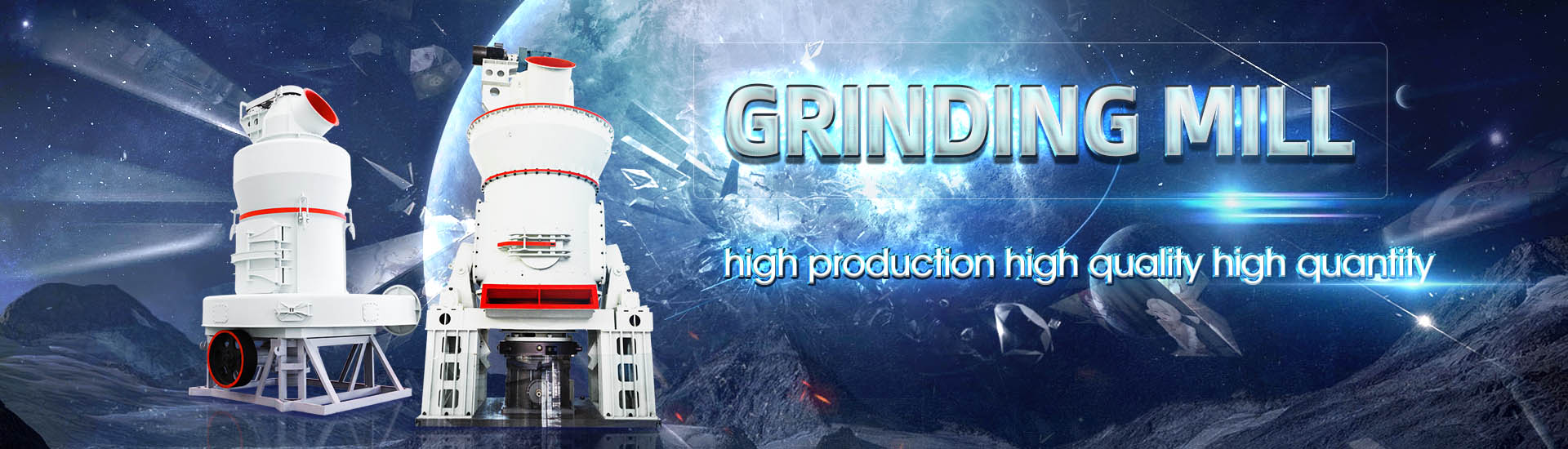
Water atomized iron oxide grinding equipment
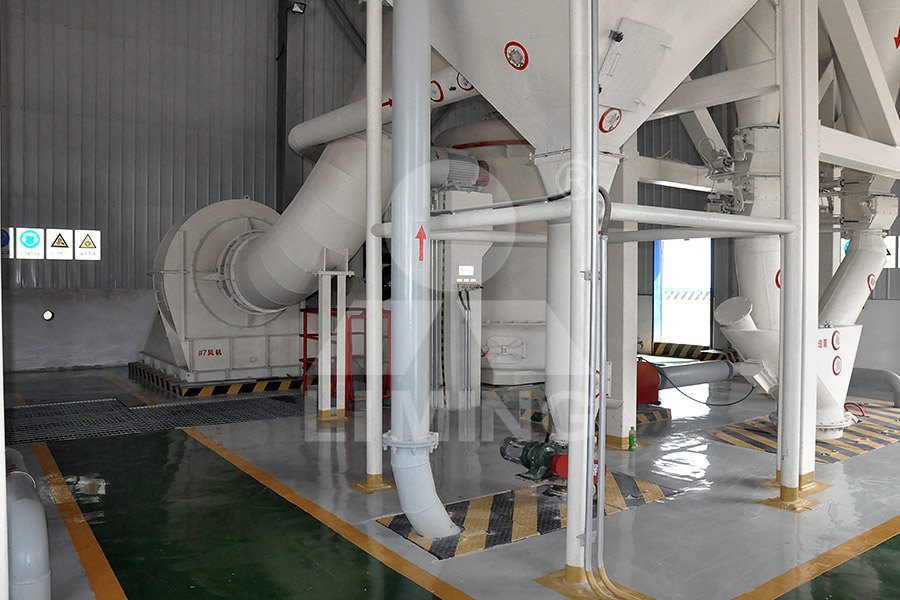
Reduction of surface oxide layers on wateratomized iron
2020年10月1日 Oxide layers on iron and steel powder have different reduction properties The reduction is affected by powder/oxide composition and initial condition Apparent activation 2020年5月9日 In this study, the oxide reduction and oxygen removal in wateratomized iron powder was investigated by means of thermogravimetric analysis in pure hydrogen Two Oxide reduction and oxygen removal in wateratomized iron 2020年5月9日 In this study, the oxide reduction and oxygen removal in wateratomized iron powder was investigated by means of thermogravimetric analysis in pure hydrogen Two 水雾化铁粉中的氧化物还原和除氧:动力学研究,Journal of 2022年1月1日 This study will consider the cooling, solidification and collision of droplets during water atomisation of molten ironcarbon alloys and investigate the feasibility that collisions Particle morphology of water atomised iron‑carbon powders
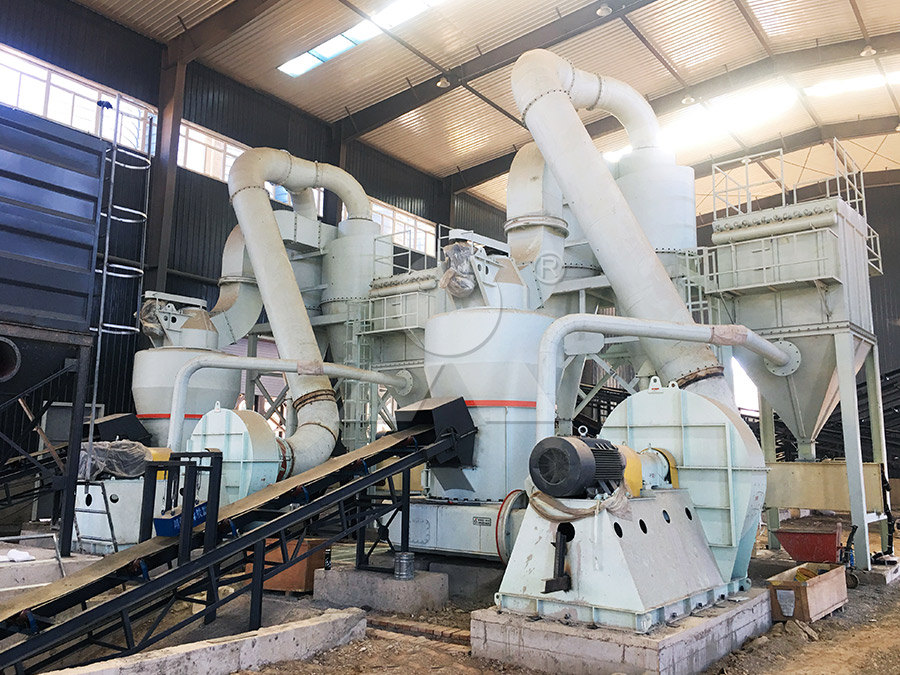
Novel preparation process of iron powders with
2019年11月1日 Hoganas and water atomization processes are currently the major iron powder production techniques in China, but both have obvious drawbacks A novel and clean iron 2022年10月25日 Two types of micro/nanobimodal powders were obtained by mixing the nanopowder with wateratomized iron powder Improved linear shrinkage was observed during Carboncoated iron nanopowder as a sintering aid for wateratomized 2021年11月22日 Consolidation of gasatomized powders to full density by hot isostatic pressing (HIP) is an established process route but utilizing wateratomized powders in HIP involves Effect of Density and Processing Conditions on Oxide Transformations 2022年1月13日 An experimental study was performed to produce spherical iron powders from irregularly shaped water atomized powders This process consists of remelting the water Spheroidization of Iron Powders by Radiative Heat Transfer
.jpg)
New Processing Route for Production of Fine Spherical
2016年2月5日 In the following a new method for producing fine iron powders from iron oxide as byproduct of refined pickling slurries from steel makers as well as the relationship between the 2020年6月25日 Wateratomized iron and steel powder is commonly used as the base material for powder metallurgy (PM) of ferrous components The powder surface chemistry is Evolution of surface chemistry during sintering of water‐atomized iron II Oxide reduction and oxygen removal in water atomized iron powder: a kinetic study J Wendel, S K Manchili, E Hryha, L Nyborg Journal of Thermal Analysis and Calorimetry, 2020, Vol 142, 309320 DOI: 101007/s10973020097246 III Evolution of surface chemistry during sintering of water atomized iron and lowalloyed steel powderSWATHI KIRANMAYEE MANCHILI Chalmers2022年10月25日 The paper examines the influence of carbon coating on iron nanopowder used as a sintering aid for wateratomized iron powder Iron nanopowder without such a coating was used as a reference Carboncoated iron nanopowder as a sintering aid for wateratomized
.jpg)
Carboncoated iron nanopowder as a sintering aid for wateratomized
2022年10月25日 The reduction of surface oxide layers covering commercial wateratomized iron and steel powder grades have been investigated using model thermogravimetric reduction cycles in hydrogenoxide reduction, shown to be applicable for silver oxide [14], nickel oxide [15], iron ores and pure iron oxides [16,17] as well as for water atomized iron powder [18] In this way, the effects of powder chemistry and initial surface oxide condition on the reduction kinetics could be revealedReduction of surface oxide layers on wateratomized 2022年1月1日 Water atomisation can produce metal powders faster and at lower cost than gas atomisation, but it is well known that the powder particles are irregular and may contain a large number of poresThe current study analyses three iron‑carbon alloys with different superheats, produced as powder by water atomisation and compares the particle shapes and porosity in Particle morphology of water atomised iron‑carbon powders2011年10月26日 Powder Metallurgy Progress, Vol11 (2011), No 12 44 Fig1 SE images of particles of powder A showing morphology and distribution of particulate features on the powder surface Fig2 HR SEM+EDX analysis of particulate features on the surface of powder A Onset of the interparticle necks’ development is directly connected to theCHANGES IN OXIDE CHEMISTRY DURING
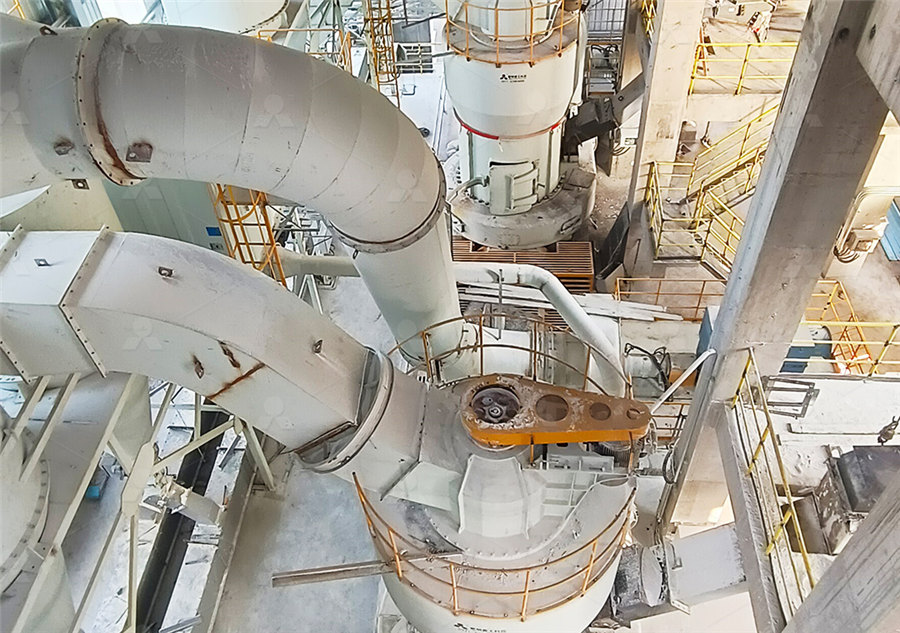
Gothenburg, Sweden 2020 Chalmers
Oxide reduction and oxygen removal in wateratomized iron powder and compacts J Wendel, S K Manchili, E Hryha, L Nyborg Proceedings of World PM 2018 An extended version of this paper was published in Journal of Thermal Analysis and Calorimetry (see Paper II) c Analysis of iron oxide reduction kinetics in the nanometric scale using 2013年3月1日 Water atomized steel powder particles are covered by heterogeneous surface oxide, formed by thin (~ 6 to 8 nm) iron oxide layer covering most of the powder surface, and particulate features formed Characterization of Surface Oxides on WaterAtomizedbehaviors of individual iron oxides including Fe2O3, Fe3O4 and FeO The wateratomized iron powder contained a significant amount of iron oxides, mainly Fe3O4 and FeO, which were formed as a partiallycontinuous surface layer and an inner inclusion DuringHydrogen Reduction Behavior of Oxide Scale in Water 2023年11月23日 21 Material and additive manufacturing The 18Ni300M steel powders used as raw material in the LPBF process were gas and water atomized by two companies The two batches of powders would be designated GA (N 2 gas atomized) and WA (water atomized) for identification purposes The main morphometric difference between the particulate materials is Microstructural and mechanical characterization of additively
.jpg)
Evolution of surface chemistry during sintering
2020年6月26日 Water‐atomized iron and steel powder is commonly used as the base material for powder metallurgy (PM) of ferrous components The powder surface chemistry is characterized by a thin surface oxide 2023年12月4日 The iron nanopowder is covered by a 3–4 nm thick iron oxide layer, while the carbon‑coated iron nanopowder is encapsulated with several nanometric carbon layers Thermogravimetry conducted inCarboncoated iron nanopowder as a sintering aid for 2013年3月1日 Semantic Scholar extracted view of "Characterization of surface oxides on wateratomized steel powder by XPS/AES depth profiling and nanoscale lateral surface analysis" by D Chasoglou et al Water‐atomized iron and steel powder is commonly used as the base material for powder metallurgy (PM) of ferrous components Characterization of surface oxides on wateratomized steel 2018年11月1日 In this study, the surface characteristics of 3 fractions of water‐atomized iron powder, sieved to −20, −45, and −75 μm, were investigated This was done by using X‐ray photoelectron spectroscopy, Auger electron spectroscopy, and scanning electron microscopy equipped with energy‐dispersive X‐ray spectroscopySurface analysis of fine water‐atomized iron powder and
.jpg)
Sintering of wateratomized iron and lowalloyed steel powder
Iron and steel powder grades are extensively used in the powder metallurgy (PM) industry for manufacturing of ferrous structural components, with a major customer in the automotive industry The powder grades are predominantly manufactured by wateratomization, yielding powder particles with highly irregular morphology and good compressibility, making the powder ideal The distribution of oxides in pilot water atomized FeMnC powders was determined by using optical and scanning electron microscopy, combined with energy dispersive Xray microanalysis The oxygen in the atomized powders was mainly present as thin surface oxide layers, which increase in thickness from 10 nm to 50 nm as the particle sizes Particle morphology of water atomised ironcarbon powdersThe reduction of surface oxide layers covering commercial wateratomized iron and steel powder grades have been investigated using model thermogravimetric reduction cycles in hydrogenOverview of asreceived wateratomized iron powderIron nanopowder without such a coating was used as a reference sintering aid to isolate the inuence of the carbon coating Both nanopowder variants were characterised using XPS and HRTEM The results showed a core–shell structure for both variants The iron nanopowder is covered by a 3–4 nm thick iron oxide layer, while the carbon‑coated ironCarboncoated iron nanopowder as a sintering aid for
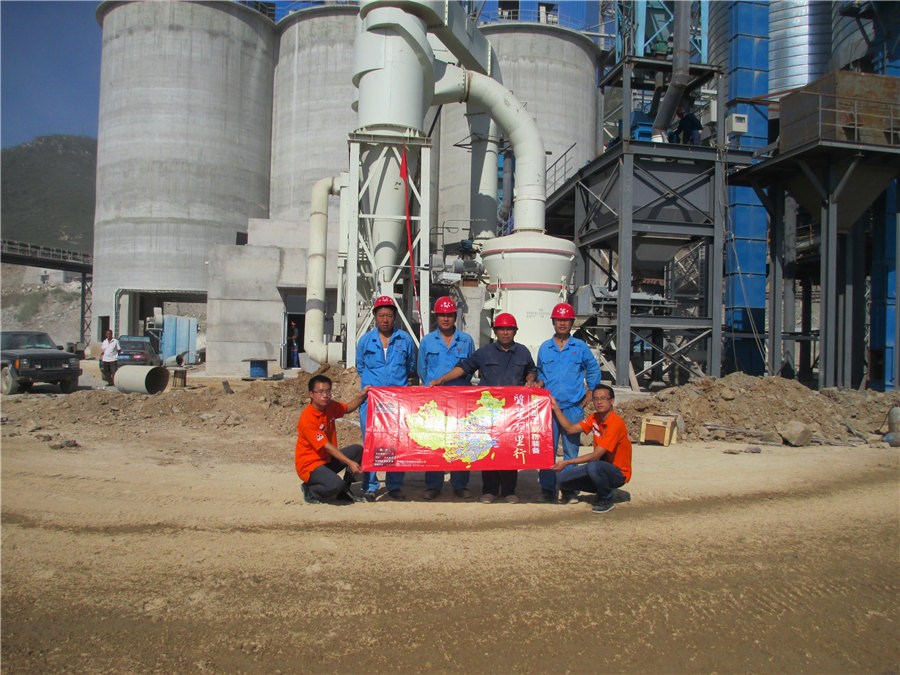
Oxide reduction and oxygen removal in wateratomized
J Wendel et al 1 3 considerablymorediculttoreducethantheironoxide layerandconsequentlyanysinteringatmosphereandtemperatureprogramthatcanprovideadequatesinteringcon2020年1月27日 material in the production of ironbase powder metallurgy parts Key Words: Powder production, Sponge iron, Solid byproduct 1 Introduction Mill scale is a steelmaking byproduct from the rolling mill in the steel hot rolling process Mill scale contains both iron in elemental form and three types of iron oxides: wustite (FeO), hematite (α Production of Sponge Iron Powder by Reduction of a By 2020年1月27日 material in the production of ironbase powder metallurgy parts Key Words: Powder production, Sponge iron, Solid byproduct 1 Introduction Mill scale is a steelmaking byproduct from the rolling mill in the steel hot rolling process Mill scale contains both iron in elemental form and three types of iron oxides: wustite (FeO), hematite (α Production of Sponge Iron Powder by Reduction of a By 2018年9月24日 The second factor which differentiates water atomization from gas atomization is the resulting particle shape Water atomized powder is highly irregular in comparison to gas atomized powders This is due in most part to the relative cooling and spheroidization rates Water atomized powders tend to be moreEconomic Additive Manufacturing using Water Atomized
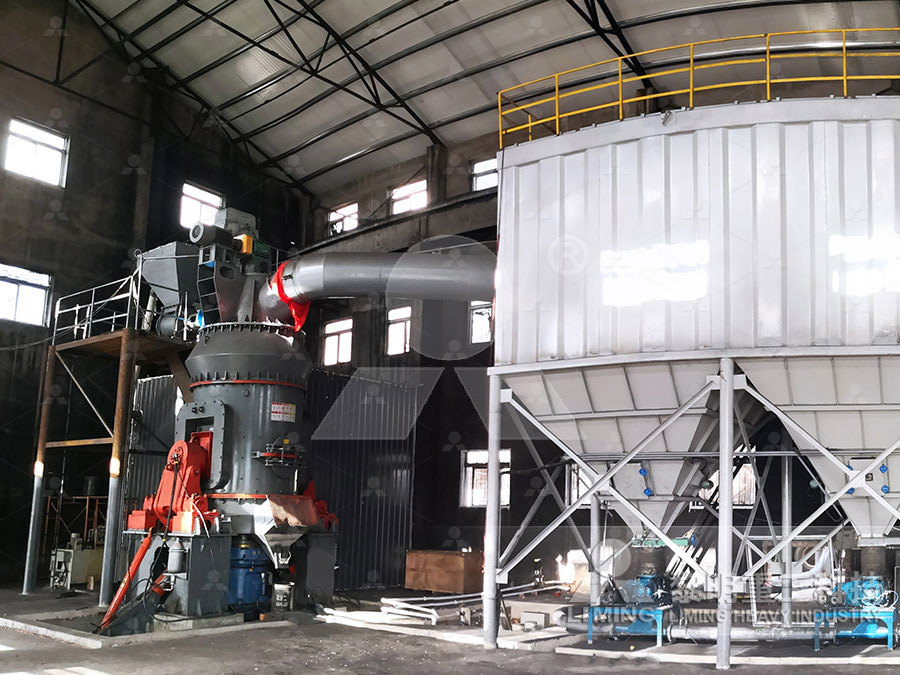
PROPERTIES AND APPLICATIONS FOR IRON POWDER
2022年8月4日 Figure 1: Morphology of typical sources of iron powder: (a) Gas Atomized, (b) Water Atomized, (c) Sponge Iron and (d) Carbonyl get entrapped during the atomization process The internal porosity of the water atomized powders is generally low and the powders produced by this process are very economical compared to their gas atomized counterpart2023年2月1日 This work investigates the feasibility of net shape manufacturing of parts using wateratomized (WA) lowalloy steel with comparable densities to conventional powder metallurgy parts via binder Supersolidus liquid phase sintering of wateratomized low 2021年11月22日 To improve the mechanical properties and performances of wateratomized powder metallurgy steels, it is necessary to enhance the density Consolidating wateratomized steel powders via conventional pressing and sintering to a relative density level > 95 pct involves processing challenges Consolidation of gasatomized powders to full density by hot isostatic Effect of Density and Processing Conditions on Oxide Transformations 2023年10月10日 Water, gas, centrifugal, and vacuum atomization are common techniques Feedstock is typically steel, aluminum, copper, nickel, cobalt alloys Applications and Uses of Atomized Metal Powders Atomized powders are used across industries wherever high precision, consistent, high purity metal powders are required Remove powder buildup and The Atomizing Metal Powder Industry Additive
.jpg)
Characteristics and Sintering of Fine Wateratomized
reduction of the surface iron oxide layer could be determined for both wateratomized and carbonyl powder, and nitrogen and carbonremoval processes could also be shown for carbonyl iron Furthermore, removal of internal oxygen in wateratomized powder by diffusion and subsequent reduction was identified The2022年10月25日 The study’s primary objective is to determine how the presence of carbon on the surface of the iron nanopowder affects the sintering of wateratomized iron powderIn addition, the carbon coating on the iron nanopowder would serve as a source of carbon and participate in the reduction of oxidesCarboncoated iron nanopowder as a sintering aid for wateratomized Reduction of oxides during sintering is a prerequisite for the manufacturing of powder metallurgy steels Inadequate control of the sintering atmosphere may impede sinter neck formation and cause entrapment and growth of oxides in sinter necks, ultimately deteriorating the mechanical properties of sintered components In this study, the oxide reduction and oxygen removal in Oxide reduction and oxygen removal in wateratomized iron 2016年6月5日 Water atomized iron powders with different particle size distributions were compared to the benchmark gas atomized stainless steel powders in terms of their granulometry, particle morphology Binderjetting additive manufacturing with water atomized iron
.jpg)
SWATHI KIRANMAYEE MANCHILI Chalmers
II Oxide reduction and oxygen removal in water atomized iron powder: a kinetic study J Wendel, S K Manchili, E Hryha, L Nyborg Journal of Thermal Analysis and Calorimetry, 2020, Vol 142, 309320 DOI: 101007/s10973020097246 III Evolution of surface chemistry during sintering of water atomized iron and lowalloyed steel powder2022年10月25日 The paper examines the influence of carbon coating on iron nanopowder used as a sintering aid for wateratomized iron powder Iron nanopowder without such a coating was used as a reference Carboncoated iron nanopowder as a sintering aid for wateratomized 2022年10月25日 The reduction of surface oxide layers covering commercial wateratomized iron and steel powder grades have been investigated using model thermogravimetric reduction cycles in hydrogenCarboncoated iron nanopowder as a sintering aid for wateratomized oxide reduction, shown to be applicable for silver oxide [14], nickel oxide [15], iron ores and pure iron oxides [16,17] as well as for water atomized iron powder [18] In this way, the effects of powder chemistry and initial surface oxide condition on the reduction kinetics could be revealedReduction of surface oxide layers on wateratomized
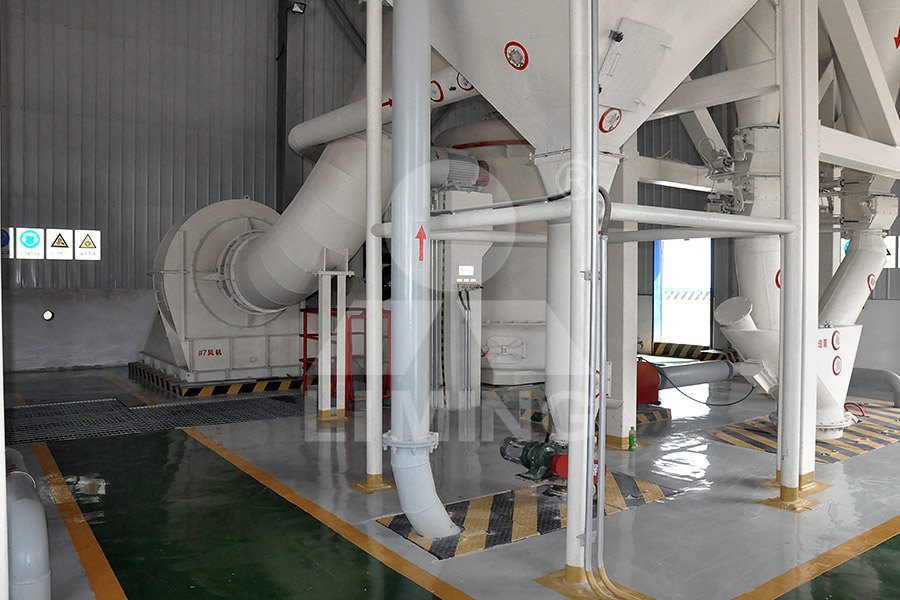
Particle morphology of water atomised iron‑carbon powders
2022年1月1日 Water atomisation can produce metal powders faster and at lower cost than gas atomisation, but it is well known that the powder particles are irregular and may contain a large number of poresThe current study analyses three iron‑carbon alloys with different superheats, produced as powder by water atomisation and compares the particle shapes and porosity in 2011年10月26日 Powder Metallurgy Progress, Vol11 (2011), No 12 44 Fig1 SE images of particles of powder A showing morphology and distribution of particulate features on the powder surface Fig2 HR SEM+EDX analysis of particulate features on the surface of powder A Onset of the interparticle necks’ development is directly connected to theCHANGES IN OXIDE CHEMISTRY DURING Oxide reduction and oxygen removal in wateratomized iron powder and compacts J Wendel, S K Manchili, E Hryha, L Nyborg Proceedings of World PM 2018 An extended version of this paper was published in Journal of Thermal Analysis and Calorimetry (see Paper II) c Analysis of iron oxide reduction kinetics in the nanometric scale using Gothenburg, Sweden 2020 Chalmers2013年3月1日 Water atomized steel powder particles are covered by heterogeneous surface oxide, formed by thin (~ 6 to 8 nm) iron oxide layer covering most of the powder surface, and particulate features formed Characterization of Surface Oxides on WaterAtomized
.jpg)
Hydrogen Reduction Behavior of Oxide Scale in Water
behaviors of individual iron oxides including Fe2O3, Fe3O4 and FeO The wateratomized iron powder contained a significant amount of iron oxides, mainly Fe3O4 and FeO, which were formed as a partiallycontinuous surface layer and an inner inclusion During2023年11月23日 21 Material and additive manufacturing The 18Ni300M steel powders used as raw material in the LPBF process were gas and water atomized by two companies The two batches of powders would be designated GA (N 2 gas atomized) and WA (water atomized) for identification purposes The main morphometric difference between the particulate materials is Microstructural and mechanical characterization of additively