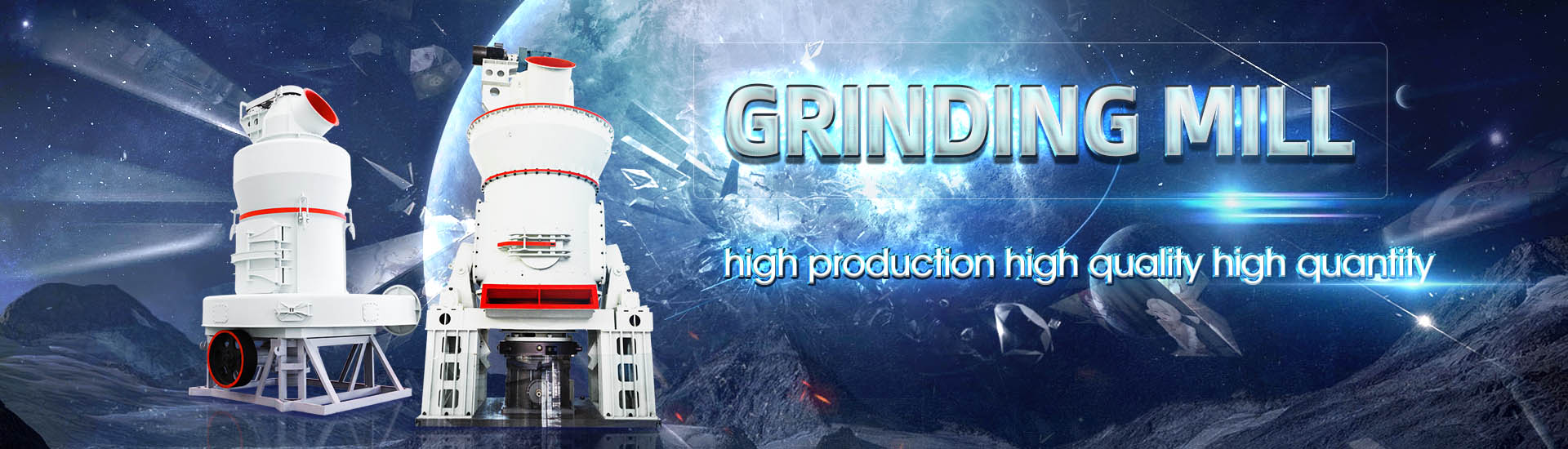
Silicon ore fine particle ore grinding machine
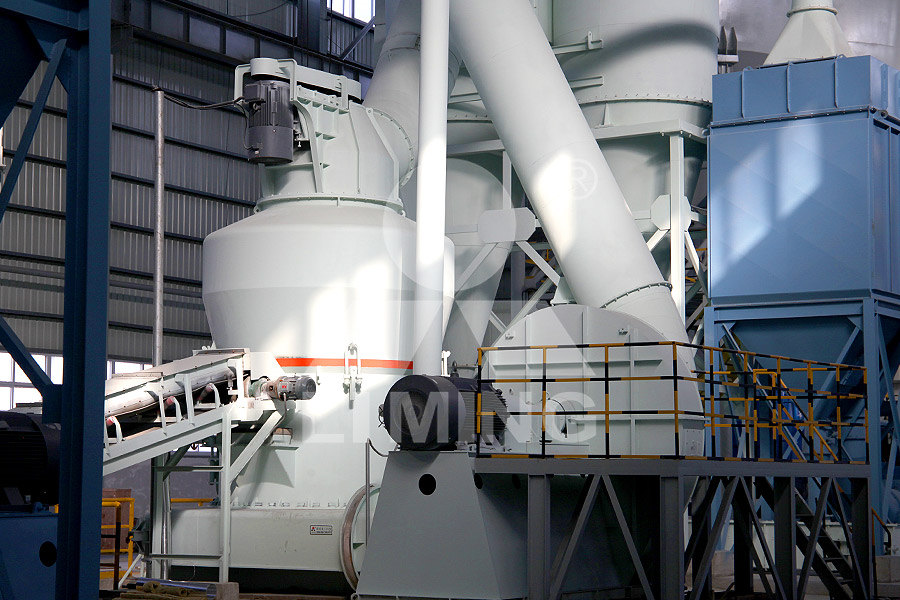
Fine grinding: How mill type affects particle shape characteristics
2017年9月1日 The objective of this work is to assess the influence of fine grinding in ball mills and stirred mills on valuable mineral liberation and particle shape characteristics of UG2 ore, a 3 天之前 The IsaMill™ is a largescale energy efficient continuous grinding technology specifically developed for rugged metalliferrous applications Glencore Technology supplies the IsaMill™ technology to mining operations around the Ultrafine Grinding and the IsaMill™ Technology2023年7月20日 According to the particle sizes of grinding products, the grinding process is divided into coarse grinding, medium grinding, fine grinding, microfine grinding, and ultrafine Ore Grinding SpringerLink2024年8月7日 Mineral processing involves key stages to extract valuable minerals from ores, including crushing to reduce ore size for further processing, grinding to further refine particle size and liberate minerals, classification to Mineral Processing Equipment for Mining Industry
.jpg)
Energy Use of Fine Grinding in Mineral Processing
2013年12月18日 Fine grinding, to P80 sizes as low as 7 μ m, is becoming increasingly important as mines treat ores with smaller liberation sizes This grinding is typically done using stirred mills such as the Isamill or Stirred The “M” Series fine grinders are designed to grind dry, freeflowing material down to 400 mesh with extremely tight particle size distribution This highly efficient machine ensures easy access to all internal areas and is perfect for heat Fine Grinders, Hammer Mills, and More for 2023年7月20日 Ultrafine grinding process is to produce ultrafine ore particles There is no unified standard for the size of ultrafine particles, but it is generally believed that the ultrafine Ultrafine Grinding Process SpringerLink2024年6月1日 High MRR is obtained by optimizing the characteristics of grindpolishing wheel Silicon is essential to the production of integrated circuits and optical components Grinding is Ultralow damage processing of silicon wafer with an
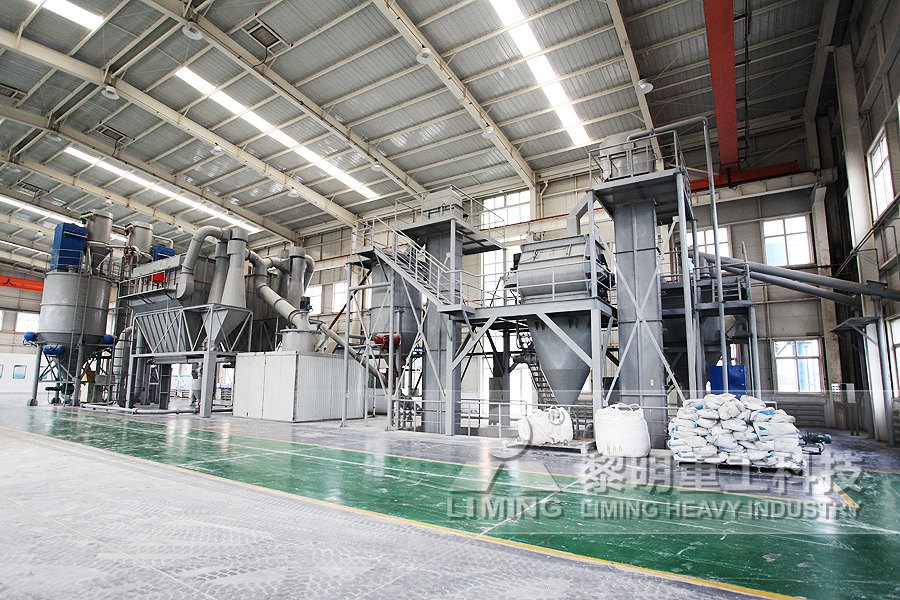
Evolution of grinding energy and particle size during dry ball
2020年10月1日 In this paper, we present a detailed investigation of the dry grinding of silica sand in an oscillatory ball mill We are interested in the evolution of specific surface area 2024年4月26日 Sintering, on the other hand, involves heating the fine iron ore particles to form a porous mass without the use of binders The sintered product, known as a sinter, is then crushed and screened to produce the desired Iron Ore Processing: From Extraction to 2017年3月20日 In this work, using highsilicon iron ore concentrates as raw material, the effect of highsilicon iron ore concentrates with different particle size on the oxidation behavior of pellets was studiedPhysicochemical Problems of Mineral Processing 2023年7月10日 The present literature review explores the energyefficient ultrafine grinding of particles using stirred mills The review provides an overview of the different techniques for size reduction and the impact of energy EnergyEfficient Advanced Ultrafine Grinding of
.jpg)
Effect of iron ore tailings as partial replacement to fine
2023年12月13日 After the beneficiation of iron ore, the waste is generated, which arise many environmental issues for both living and nonliving components Iron ore tailings are a byproduct of the mining and processing of iron ore, and their potential use as a replacement resource is the emphasis of this study The purpose of this research is to determine how well sand can stand 2020年5月15日 Figure 3 shows the particle size distribution for the ground ore blend The ultrafine generation through HPGR was remarkably higher than the ball mill, which is explained by a higher generation of surfaces within the microcracks reported at the BSA, especially in particle size range bellow 30 μmDevelopment of a Novel Grinding Process to Iron Ore2023年7月20日 Ore particles in metal mine whose size is below 400 mesh can be called ultrafine grinding particles Ultrafine particles are widely used in the military, metallurgy, chemical industry, electronics, computer, aerospace, pharmaceuticals, and other hightech fields Ultrafine particles can be produced with chemical and physical methods Chemical Ultrafine Grinding Process SpringerLink2023年8月24日 The optimization of ore blending technology in sintering is an effective method to improve the quality of sinter and efficient utilization of high silicon ore The main method of ore blending optimization is based on the basic process performance of iron ore at high temperature [6–8] For example, the assimilation and liquid fluidity of Optimization of iron ore blending based on replacing
.jpg)
Relationships between particle breakage characteristics and comminution
2021年4月1日 The present work investigates the response of four iron ore concentrates to different single particle breakage tests, pistonanddie tests, as well as experiments in a laboratory highpressure grinding roll and a ball mill, analysing the relationship between the different measures in light of the mineralogy and texture of the concentrates When iron ore is extracted from a mine, it must undergo several processing stages Six steps to process iron ore 1 Screening We recommend that you begin by screening the iron ore to separate fine particles below the crusher's CSS before the crushing stage A static screen is used to divert the fine particles for crushing WhatsApp: +86 fine particles of silicon ore crusher anmartbehuisingcoThe iron ore sample was crushed and pulverized using a crusher and grinder and then classified by size using sieving to produce various size fractions (45~250 μm) The chemical compositions of the iron ore sample with various sizes are shown in Table 1 The results of particle size distribution analysis are plotted in Figure 2Removal of Silicon, Aluminum and Phosphorus 2023年2月7日 plained by the fact that as the particle size decreases, the number of particles increases, and the number of contact points between balls and particles decreases Thus, the ratio of ball to particle decreases and the grinding rate decreases TABLE1 C HEMICAL ANALYSIS OF TALC SAMPLE Species % Species % SiO R 2 46329 P 2 O 5 0106Parameters affecting wet ultrafine grinding of talc ore
.jpg)
Comparative study on mineral dissemination
2022年12月7日 The disseminated particle size of fluorapatite, dolomite, and quartz in the ore is coarse, and the content of fine particle size is extremely little, indicating that the ore belongs to the type of 2017年3月4日 A typical type of fine grinder is the A rotating drum causes friction and attrit ion between steel rods and ore particles] arsenide, aluminium oxide, silicon carbon ate, zirconium (PDF) SIZE REDUCTION BY GRINDING METHODS 2024年9月1日 The average particle size of the raw ore powder measured with a particle size analyzer (Malvern, 2000) is 5694 μm, along with a specific surface area of 088 m 2 /g (Fig 1 b and Table 2) Scanning electron microscopy (SEM, Tescan Mira Lms, Czech Republic) and energy dispersive spectroscopy (EDS, Oxford) were conducted to elucidate the micro Improvement of mechanochemical leaching of zinc oxide ore 2020年10月1日 Several comminution laws have been proposed to link the consumed energy to a characteristic particle size of the powder The popular models are those of Rittinger [4], Bond [5] and Kick [6]While the Bond and Kick models are mostly employed for coarse and intermediate size grinding, the Rittinger model is better suited for fine comminution [7]This model assumes Evolution of grinding energy and particle size during dry ball
.jpg)
AutoSEM particle shape characterisation: Investigating fine grinding
2015年4月1日 Currently, studies utilising ComputerControlled SEMEDS routines to define the shape of coal dust particles primarily assess this by quantifying the aspect ratio of the particle [24,25,47]2016年7月7日 The recovery of gold by ore leaching is influenced by the size of the particles and the chemical environment The effect of particle size on the dissolution of gold is usually studied using mono Effect of Particle Size and Grinding Time on Gold Dissolution to clean the ore material surface from finedispersed particles of minerals and slime, as well as disintegrating ore aggregates fed to the magnetic separator The main tasks involve identifying regularities of influence of slurry pretreatment by highenergy ultrasound on properties of iron ore magnetic separation, determining regulations ofIncreasing efficiency of iron ore magnetic separation by Brief Introduction HGM Ultra fine grinding mill (also called micro powder mill, superfine powder grinding mill, ultra fine powder grinder) is designed by SBM RD department on the basis of multiple innovations and testing It has been proved by thousands of customers that our ultra fine powder grinder has outstanding features, stable quality, easy operation, and maintenanceUltra Fine Grinding Mill SBM Ultrafine Powder Technology
.jpg)
Nanobubbles effect on the mechanical flotation of phosphate ore fine
2017年5月8日 Froth flotation is one of the main methods for processing phosphate ores However, the flotation of fine particles, especially phosphate ores, has always been one of the fundamental problems2024年8月7日 After crushing, grinding refines ore into a fine powder to liberate valuable minerals Key types include Ball Mills, which grind ore using steel balls in a rotating cylinder; Rod Mills, which use long rods for a coarser grind; and Mineral Processing Equipment for Mining Industry2024年9月24日 The grade of the ore was improved from 5443% Fe to 6571% Fe However, significant μ amount of fine iron ore particles were lost during the processing of 150 μm size ore, because it is not very effective for particles less than 15 μm Thus, fine hematite and goethite particles are usually not recovered resulting in the loss ofOpen Access Recovery Improvement of Fine Iron Ore 2022年5月6日 In order to explore the reasonable ore blending of lowsilicon magnetite in sintering, it I necessary to realize the efficient utilization of lowsilicon ore, further reduce cost, and increase yield In this study, based on the high Study on Influencing Factors of High
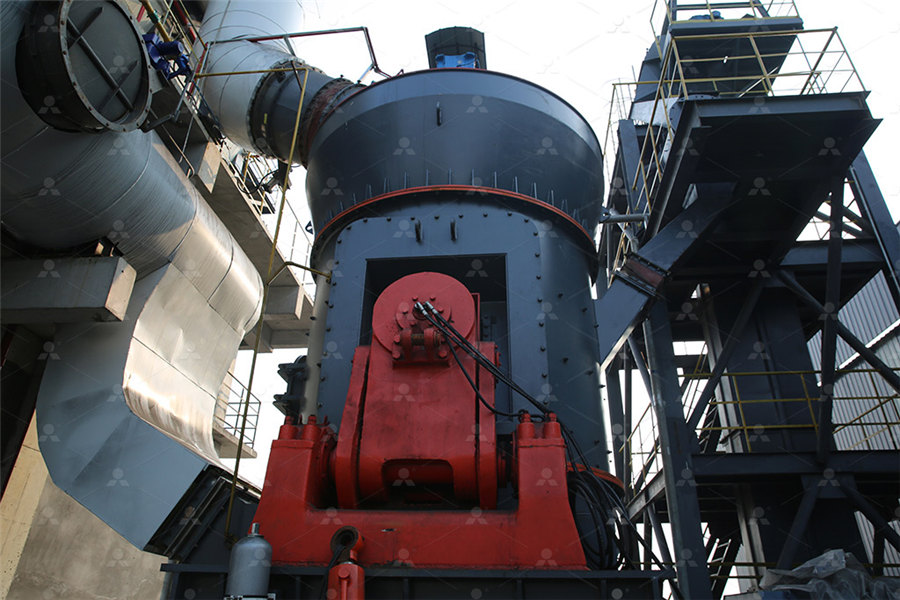
Ultra Fine Grinding A Practical Alternative to Oxidative
20 小时之前 the gold deportment and particle size may provide additional information Mineralogical scans such as QEMScan and MLA are able to give good data as to the mineral liberation and particle size of gold down to about 5µm Below this size, an alternative method such as secondary ion mass spectrometry (SIMS) should be used Ultra Fine Grinding at KCGMSBM ultrafine powder technology co,ltd Is China's excellent ore mill supplier Our main products include ultrafine vertical roller mill, ultrafine grinding mill, stone powder production equipment, Welcome to consult HGM series ring roller mill is a type of advanced grinding machine designed to produce fine to ultrafine powders for various SBM Ultrafine Powder Technology Industrial Grinding Mill, 2023年11月1日 Powder grinding technology was a method of reducing traditional powders to particles in the micrometer range, resulting in a significant increase in material surface area and reactivity [7]This technique had a notable impact on the physical, mechanical, and chemical properties of materials [8, 9]Mechanical grinding was an effective method for processing Mechanical grinding kinetics and particle packing novel 2021年2月17日 The return fine rate of sinter decreased from 2543 to 2464%, and the solid fuel consumption decreased from 448 to 439 kgce/t Download conference paper PDF Similar content being viewed by others So, the suitable matching mode of fuel particle size (d) and blending ore particle size (D) may be as follows: d/D = 047 ~ 054Particle Size Matching Mechanism of Blending Ore and Solid
.jpg)
Fine Grinding as Enabling Technology – The IsaMill
3 天之前 the particle But for a 9 micron particle this rim is sufficient for the mineral to disintegrate (Figure 2) • The mechanical activation impact the high energy intensity of fine creates a highly stressed surface, reducing the crystalline nature to amorphous phases (Figure 3)2020年5月28日 where F 80 is 80% feed particle size passing (μm), P 80 is 80% product particle size passing (μm), P i is the size of the mesh selected for the test, and Gpb is the grindability of the undersized product produced per mill revolution (g/rev) After grinding the iron ore samples X, Y, and Z in the BBM, it was recorded that P 80, BWI, and RT varied for each iron ore sample Investigation on Iron Ore Grinding based on Particle Size Distribution 2024年4月26日 Sintering, on the other hand, involves heating the fine iron ore particles to form a porous mass without the use of binders The sintered product, known as a sinter, is then crushed and screened to produce the desired Iron Ore Processing: From Extraction to 2017年3月20日 In this work, using highsilicon iron ore concentrates as raw material, the effect of highsilicon iron ore concentrates with different particle size on the oxidation behavior of pellets was studiedPhysicochemical Problems of Mineral Processing
.jpg)
EnergyEfficient Advanced Ultrafine Grinding of
2023年7月10日 The present literature review explores the energyefficient ultrafine grinding of particles using stirred mills The review provides an overview of the different techniques for size reduction and the impact of energy 2023年12月13日 After the beneficiation of iron ore, the waste is generated, which arise many environmental issues for both living and nonliving components Iron ore tailings are a byproduct of the mining and processing of iron ore, and their potential use as a replacement resource is the emphasis of this study The purpose of this research is to determine how well sand can stand Effect of iron ore tailings as partial replacement to fine 2020年5月15日 Figure 3 shows the particle size distribution for the ground ore blend The ultrafine generation through HPGR was remarkably higher than the ball mill, which is explained by a higher generation of surfaces within the microcracks reported at the BSA, especially in particle size range bellow 30 μmDevelopment of a Novel Grinding Process to Iron Ore2023年7月20日 Ore particles in metal mine whose size is below 400 mesh can be called ultrafine grinding particles Ultrafine particles are widely used in the military, metallurgy, chemical industry, electronics, computer, aerospace, pharmaceuticals, and other hightech fields Ultrafine particles can be produced with chemical and physical methods Chemical Ultrafine Grinding Process SpringerLink
制粉-10.25公众号.jpg)
Optimization of iron ore blending based on replacing
2023年8月24日 The optimization of ore blending technology in sintering is an effective method to improve the quality of sinter and efficient utilization of high silicon ore The main method of ore blending optimization is based on the basic process performance of iron ore at high temperature [6–8] For example, the assimilation and liquid fluidity of 2021年4月1日 The present work investigates the response of four iron ore concentrates to different single particle breakage tests, pistonanddie tests, as well as experiments in a laboratory highpressure grinding roll and a ball mill, analysing the relationship between the different measures in light of the mineralogy and texture of the concentrates Relationships between particle breakage characteristics and comminution When iron ore is extracted from a mine, it must undergo several processing stages Six steps to process iron ore 1 Screening We recommend that you begin by screening the iron ore to separate fine particles below the crusher's CSS before the crushing stage A static screen is used to divert the fine particles for crushing WhatsApp: +86 fine particles of silicon ore crusher anmartbehuisingcoThe iron ore sample was crushed and pulverized using a crusher and grinder and then classified by size using sieving to produce various size fractions (45~250 μm) The chemical compositions of the iron ore sample with various sizes are shown in Table 1 The results of particle size distribution analysis are plotted in Figure 2Removal of Silicon, Aluminum and Phosphorus