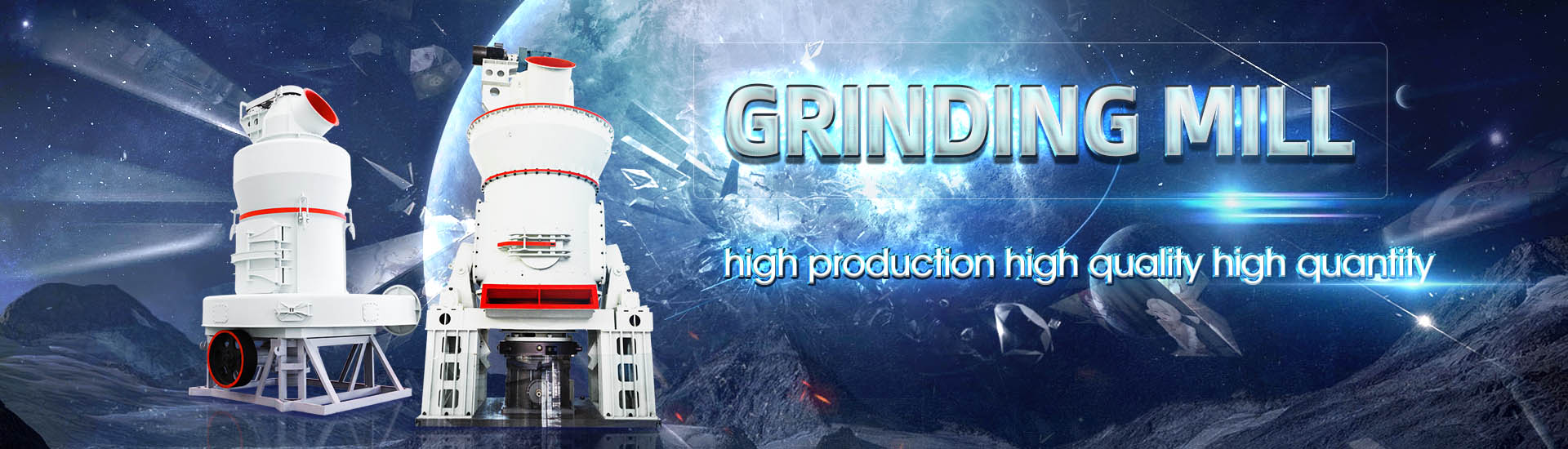
Ore mill graduation design
.jpg)
A Review of the Grinding Media in Ball Mills for Mineral
2023年10月27日 Grinding media play an important role in the comminution of mineral ores in these mills This work reviews the application of balls in mineral processing as a function of the This paper presents the structure of the latest version of the JKTech autogenous and semiautogenous (AG/SAG) mill specific energy model, which is an adaptation of that previously SAG Mill Design and Benchmarking Using Trends in the 2024年1月31日 When the feed size fluctuation is large, such as in a magnetite ore processing plant in the secondstage mill, the feed volume and feed size will be affected by the grade of the original ore Adding steel balls in the ceramic Enhancing the Grinding Efficiency of a Magnetite 2020年6月3日 Grinding mills are some of the most important equipment in mines, processing over a few thousand tons of ore every hour It is not uncommon to see these days that a single line of a grinding circuit consisting How grinding mill design changed over the last
.jpg)
Grinding in Ball Mills: Modeling and Process Control
Grinding in ball mills is an important technological process applied to reduce the size of particles which may have different nature and a wide diversity of physical, mechanical and chemical 2021年7月1日 The work uses the UFRJ mechanistic mill model and DEM to analyze the effect of several design and operating variables on the apparent breakage rates and breakage Predicting the effect of operating and design variables in fundamental to understand how ore textures influence the generation of ore particles and their properties This contribution outlines the processes used to generate and concentrate ore All About Particles: Modelling Ore Behaviour in Mineral 2021年1月11日 the correct power required to grind ore in a SAG mill, by developing ore hardness variability functions for the ore body to be mined This paper describes the next step Choosing a SAG Mill to Achieve Design Performance
.jpg)
Impact on Grinding Mill Design of Recent New Discoveries
2021年1月18日 Based on the 2009 CIM paper, the ratio of macro to micro grindability is an important key to achieving a reliable SAG mill design because that ratio reveals the best split 2023年4月23日 ciency include mill design, liner design, mill speed, charge ratio, and grinding media properties The authors also indi cated that circuit efficiency is determined by how well the power applied (PDF) Grinding Media in Ball MillsA ReviewWhite Paper created to illustrate path to NetZero Food Hub for GrowNYC New York Food HubORE Design + Technology2021年1月14日 energy required which in this case was to grind the ore represented by the samples, from a feed size F80 of 152 mm to 80% passing 17 mm, and a simple adjustment procedure in case the SAG product size needed to be adjusted Bond rod and ball mill work indices are readily converted to pinion energy for rod and ball mills but not for SAG parison of Ore Hardness Measurements for
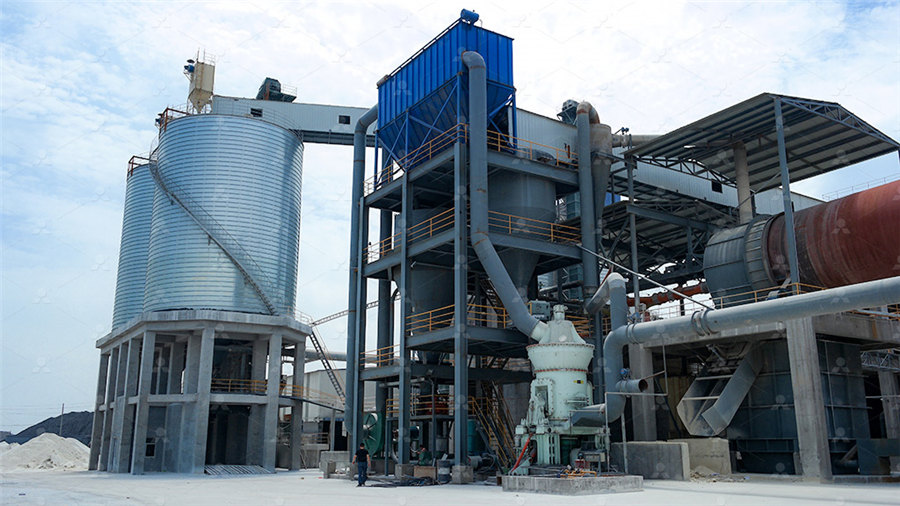
(PDF) A Review on Current Mill Liner Design and
2020年10月1日 These include mill power draft calculations, shell lifter design, lifter wear prediction, pulp lifter simulation and ore particle breakage in grinding mills The status of advancement in each of 2021年1月18日 the client’s ore and the mill design is specific to that ore By using these methods, two large areas for mistakes have been avoided First, the problem of designing for hardest ores has been eliminatedbecause a SAGDesign test identifies SAG hardness up to over 30 kWh/t Second, the use of calculation instead of simulation with other ores Impact on Grinding Mill Design of Recent New Discoveries2023年10月10日 The design of SAG mills can vary depending on various factors such as feed size, hardness, and desired throughput rate This flexibility makes them suitable for different types of ores and minerals found during copper mining operations The future of SAG mills in copper ore mining looks promising as advancements continue to be made in their Understanding the SAG Mill in Copper Ore Mining Processin the ability of design engineers to size circuits that meet project requirements (Staples et al, 2015) One of the recommendations in both Bailey et al (2009) and Staples et al (2015) was in the empirical Ore hardness testwork Mill total filling and ball load measurements Equipment design and operating variablesSAG Mill Design and Benchmarking Using Trends in the
.jpg)
Magnetite Iron Ore Design Case Study ResearchGate
2024年8月20日 Reducing Grinding Energy and Cost Magnetite Iron Ore Design Case Study A Jankovic and W Valery Metso Process Technology Innovation, PO Box 1028, Eagle Farm Qld, 4009, Australia2016年4月22日 In all ore dressing and milling processes, including flotation, cyanidation, gravity concentration, and amalgamation, it is necessary to crush and grind, often with rob mill ball mills, the ore in order to liberate the minerals In the chemical and process industries, grinding is an important step in preparing raw materials for subsequent treatmentBall Mill Rod Mill Design 911MetallurgistHowever, ore below the pay limit adds variation to the mill grade as increased mill throughput will be required to make up for the loss of gold, and that impacts on the recovery in the plant It is against these perspectives and findings of this study that the MCF should be seen as a method that identify the real problems underground and when Monitoring ore loss and dilution for minetomill integration 2021年1月14日 energy required which in this case was to grind the ore represented by the samples, from a feed size F80 of 152 mm to 80% passing 17 mm, and a simple adjustment procedure in case the SAG product size needed to be adjusted Bond rod and ball mill work indices are readily converted to pinion energy for rod and ball mills but not for SAG parison of Ore Hardness Measurements for
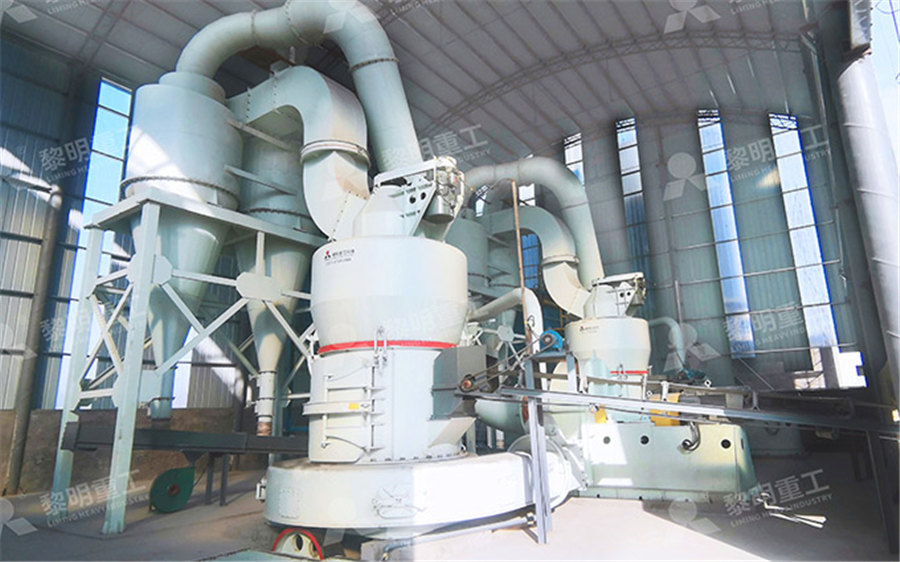
SAG Mill Grinding Circuit Design 911Metallurgist
2016年6月6日 Mill Control Schemes; Semi Autogenous Design Factors The design of large mills has become increasingly more complicated as the size has increased and there is little doubt that without sophisticated design procedures 2019年7月1日 Simulation of casting process: case study on the gating and feeding design for outlet diaphragms of iron ore ball mill July 2019 Heat and Mass Transfer 55(7):1959–1967(PDF) Simulation of casting process: case study 2021年3月23日 Milling is among the most energyconsuming technological stages of copper ore processing It is performed in mills, which are machines of high rotational massesEnergy Efficiency Analysis of Copper Ore Ball Mill Drive 2023年10月27日 The ball mill is a rotating cylindrical vessel with grinding media inside, which is responsible for breaking the ore particles Grinding media play an important role in the comminution of mineral ores in these mills This work reviews the application of balls in mineral processing as a function of the materials used to manufacture them and the mass loss, as A Review of the Grinding Media in Ball Mills for Mineral

Ecoefficient and costeffective process design for magnetite iron ore
2015年2月24日 Ecoefficient and costeffective process design for magnetite iron ore Currently, the mining industry is facing several issues related to energy consumption so the optimized use of energy is an everincreasing need with grinding were achieved over the first 8090 years of the last century by increasing the size and improving the design Attendance at graduation practice is mandatory for students to participate in the graduation ceremony Practice is typically scheduled the morning of Graduation in the Commons Students must make arrangements to attend and be present for the entire practice Practice will take 2 Graduation Information Gwinnett County Public Schools2018年9月24日 In this paper, the sand casting process was evaluated using ProCAST simulating software and practical experience for manufacturing of the high chromium stainless steel outlet diaphragms used in iron ore ball mill In the simulation practice, the effects of feeding and gating designs on the liquid flow, heat transfer and solidification phenomenon were Simulation of casting process: case study on the gating and 2020年12月1日 The application of ore sorting in the mining industry is one of the most promising recent technologies with the potential to cause step change in the way concentrators are designed Most typically, ore sorters are used to sort a given ore flow for grade, either to reject waste from the mill feed, or rescue ore from the waste pileSAG AND BALL MILL EFFECTS FROM ORE SORTING
.jpg)
ORE
info@oresign 1972 W 2425 S Woods Cross, UT 84087 ORE designs metal elements and systems for landscape architects and contractors Our work is engineered for flawless functionality and designed to captivate, for any site condition or design intent Learn More PreDesignedLargediameter autogenous and semiautogenous grinding mills represent the primary thrust of the expanding grinding technology In spite of initial difficulties, large autogenous and semiautogenous mills have reached an acceptable level of technology that provides the mineral engineer with a reliable, low cost means of ore comminutionA successful milling installation Semiautogenous mill liners: Designs, alloys, and maintenance procedures 2024年1月31日 Ceramic ball milling has demonstrated remarkable energysaving efficiency in industrial applications However, there is a pressing need to enhance the grinding efficiency for coarse particles This paper introduces a Enhancing the Grinding Efficiency of a Magnetite 2017年8月25日 These applications include orebody modelling and orereserve estimation; the design of optimum pits; the determination of optimal production schedules; the determination of optimal operating layouts; the determination of Usually local ore goes to the run of mill (ROM) pad or crusher or stockpile From there, the ore is blendedAPPLICATION OF OPTIMISATION TECHNIQUES IN OPEN
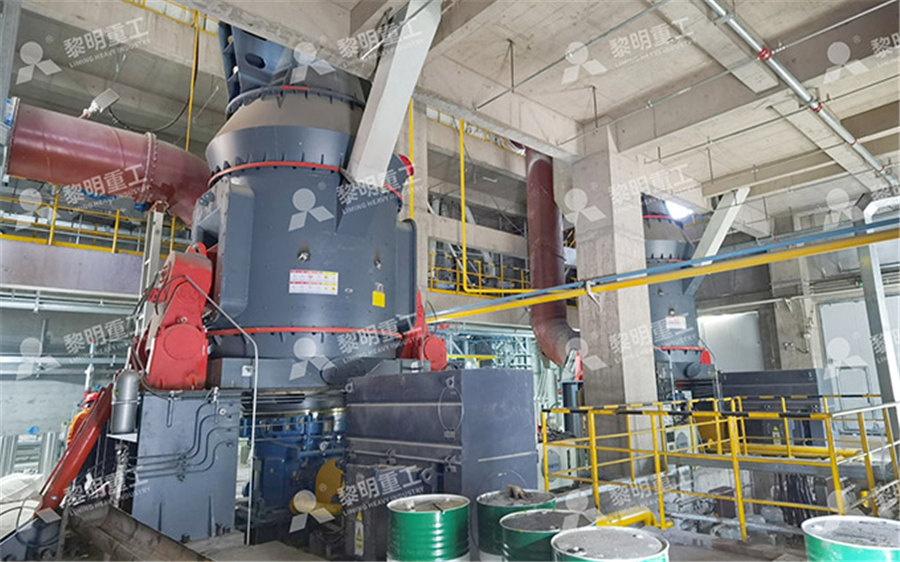
Underground Ore Loading Chutes; Ore Chute Design
2017年4月2日 To open it, the stop pin is withdrawn, and the pressure of the ore causes the door plate to swing outward at the bottom; the flow of the ore keeps it open until the loader, having reinserted the stop pin, strikes the under side of the projecting open gate depressing the inside half of the door until the flow of ore catches it and swings it shut 2021年5月8日 Drivers of grinding energy transfer to ore in ball mills • Charge density –charge shape and liner design • Charge surface area • Pulp density rheology • Media mass • Classifier efficiency How can we increase the grinding surface area? 1 Increase the grinding surface • Smaller ball media, or • Different media shape 2Rethinking Grinding Efficiency in Ball Mills RELO 2019年11月30日 The ultimate pit design for the iron ore mine was created in Surpac and is currently being used as a reference in the long term, medium term and shortterm planning The purpose of scheduling is to maximise the NPV while taking into considerations constraints such as mill throughput, tonnes that can be extracted per period, stockpile Mine Planning and Optimisation Techniques Applied in an Iron Ore 2015年4月15日 The samples can be taken from adits, pits, trenches, etc, in the ore body or they can be crushed drill cores While it is helpful in anticipating variations in feed rates to know the grindability of the various ore types in a deposit, for mill selection grindability tests should be run on composite samples representative of the blended mill feedWhat Ore Testing is Required For Mill Selection
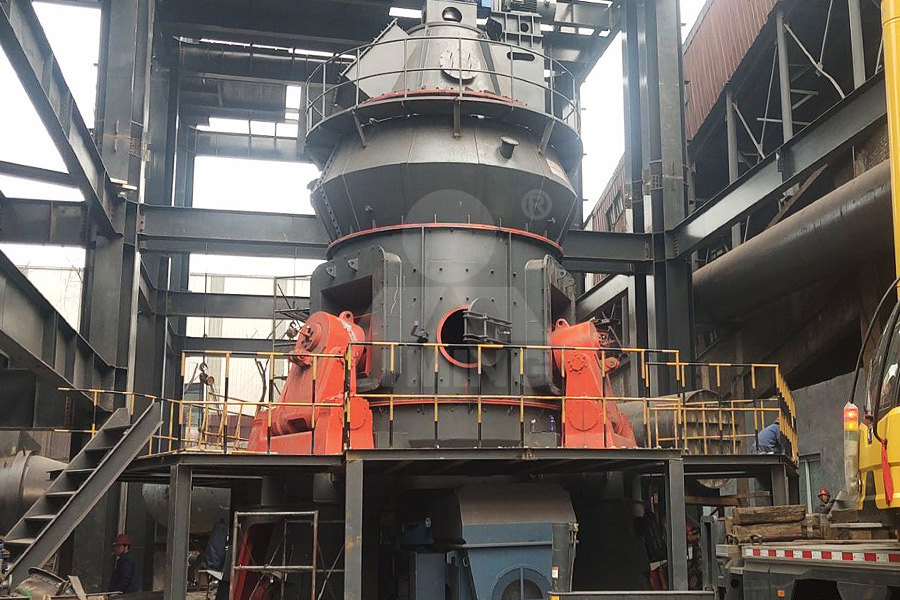
High efficiency ball mill grinding ResearchGate
2008年4月1日 The test material studied here is a gold ore ground in a closed ball mill circuit with hydrocyclone classification Several sampling campaigns were carried out aiming to produce mass balances and 2018年9月17日 development of a labora tory test to design vertical stirre d mills for iron ore REGRIND CIRCUITS MG Bergerman 1,* , D B Mazzinghy 2 , L C de R Machado 3 1DEVELOPMENT OF A LABORATORY TEST TO DESIGN VERTICAL STIRRED MILLS 2019年7月23日 Ball Mill Design Power Free download as PDF File (pdf), Text File (txt) or read online for free This document provides information about grinding mills, including standard sizes and dimensions of mills, descriptions of mill types and components, and methods for estimating mill power requirements The key details are mill dimensions and specifications for Ball Mill Design Power PDF Mill (Grinding) Iron Ore2023年4月23日 ciency include mill design, liner design, mill speed, charge ratio, and grinding media properties The authors also indi cated that circuit efficiency is determined by how well the power applied (PDF) Grinding Media in Ball MillsA Review
.jpg)
ORE Design + Technology
White Paper created to illustrate path to NetZero Food Hub for GrowNYC New York Food Hub2021年1月14日 energy required which in this case was to grind the ore represented by the samples, from a feed size F80 of 152 mm to 80% passing 17 mm, and a simple adjustment procedure in case the SAG product size needed to be adjusted Bond rod and ball mill work indices are readily converted to pinion energy for rod and ball mills but not for SAG parison of Ore Hardness Measurements for 2020年10月1日 These include mill power draft calculations, shell lifter design, lifter wear prediction, pulp lifter simulation and ore particle breakage in grinding mills The status of advancement in each of (PDF) A Review on Current Mill Liner Design and 2021年1月18日 the client’s ore and the mill design is specific to that ore By using these methods, two large areas for mistakes have been avoided First, the problem of designing for hardest ores has been eliminatedbecause a SAGDesign test identifies SAG hardness up to over 30 kWh/t Second, the use of calculation instead of simulation with other ores Impact on Grinding Mill Design of Recent New Discoveries
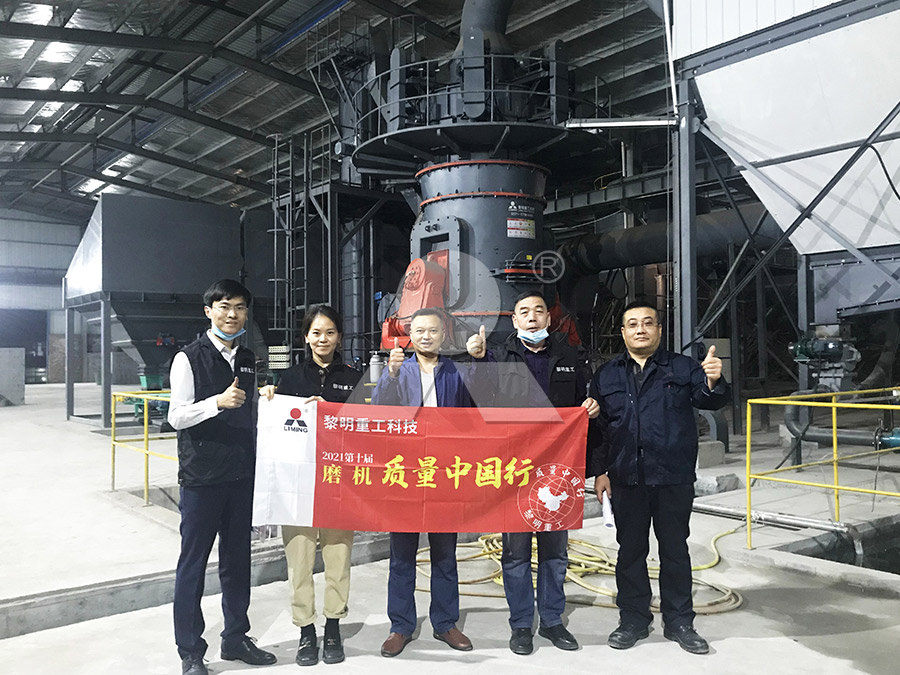
Understanding the SAG Mill in Copper Ore Mining Process
2023年10月10日 The design of SAG mills can vary depending on various factors such as feed size, hardness, and desired throughput rate This flexibility makes them suitable for different types of ores and minerals found during copper mining operations The future of SAG mills in copper ore mining looks promising as advancements continue to be made in their in the ability of design engineers to size circuits that meet project requirements (Staples et al, 2015) One of the recommendations in both Bailey et al (2009) and Staples et al (2015) was in the empirical Ore hardness testwork Mill total filling and ball load measurements Equipment design and operating variablesSAG Mill Design and Benchmarking Using Trends in the 2024年8月20日 Reducing Grinding Energy and Cost Magnetite Iron Ore Design Case Study A Jankovic and W Valery Metso Process Technology Innovation, PO Box 1028, Eagle Farm Qld, 4009, AustraliaMagnetite Iron Ore Design Case Study ResearchGate2016年4月22日 In all ore dressing and milling processes, including flotation, cyanidation, gravity concentration, and amalgamation, it is necessary to crush and grind, often with rob mill ball mills, the ore in order to liberate the minerals In the chemical and process industries, grinding is an important step in preparing raw materials for subsequent treatmentBall Mill Rod Mill Design 911Metallurgist

Monitoring ore loss and dilution for minetomill integration
However, ore below the pay limit adds variation to the mill grade as increased mill throughput will be required to make up for the loss of gold, and that impacts on the recovery in the plant It is against these perspectives and findings of this study that the MCF should be seen as a method that identify the real problems underground and when